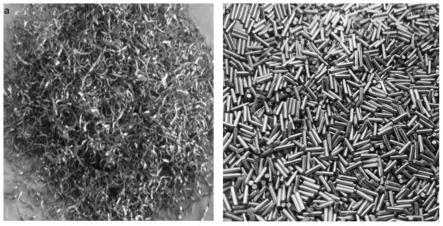
1.本发明涉及核动力技术领域化学计量学技术领域,具体涉及一种铪标准物质及其制备方法。
背景技术:2.铪具有较高的热中子吸收截面,在轻水、氦气、液态钠等介质中具有良好的耐腐蚀性能,并且有适中的力学性能和满意的焊接加工性能,是核反应堆控制棒和保护装置的首选材料。
3.碳、氢、氧、氮是金属及其合金材料中经常伴生的元素,它们的含量直接影响金属及其合金材料的性能。在铪材中碳、氢、氧、氮都属于间歇相元素,在达到一定浓度前,仅以间隙形式填充到金属晶格的节点中间,使晶格对称性稍有扭曲,从而影响材料物理和化学性能,甚至会给反应堆的运行带来不安全因素,必须严格控制碳、氢、氧、氮的质量分数。
4.金属的元素标准物质具有确定了的足够均匀的元素含量标称值,作为一种实物量具,是分析化学必不可少的用于校准测量设备、评价分析方法、考核分析人员技术水平和测量材料元素含量的计量标准。在产品的生产过程和质量控制过程中起着不可或缺的作用。
5.因核级铪材用途敏感性问题,国际上对铪标准物质实行技术封锁,也禁止相应标准物质出售。目前国内没有铪标准物质的生产及销售,各铪材生产及使用单位均采用ti、zr等同族元素标准物质替代。这就导致铪材元素分析检测时常存在一定程度的偏差,有时甚至差异明显,形成不易评判的质量异议。
6.为解决上述分析检测存在的问题,突破国际上的技术封锁,本发明专利提出一种铪标准物质及其制备方法,可以实现铪材碳、氢、氧、氮标准物质制造、评价、定值及保存,促进建立我国自有评价体系,提升铪材检测水平。
技术实现要素:7.本发明专利要解决的技术问题是目前国内普遍使用ti、zr等同族元素标准物质替代铪标准物质,导致分析检测结果出现偏差。本发明的目的是提供一种铪中碳、氢、氧、氮标准物质及其制备方法,突破国际技术封锁,实现更准确地校准铪材分析设备、评价铪材分析方法,为铪材碳、氢、氧、氮元素分析提供质量评判标准。
8.本发明通过下述技术方案实现:
9.本发明的第一个目的在于提供一种铪标准物质的制备方法,一种铪标准物质的制备方法,其特征在于,包括:
10.以晶条铪为原材料,进行熔炼处理,得到铪铸锭;
11.对得到的铪铸锭进行加工处理,得到碳屑状样块、氢颗粒样块、氧颗粒样块、氮颗粒样块;
12.晶条铪中碳含量为30~70μg/g,氢含量为10~40μg/g,氧含量为20~200μg/g,氮含量为5~40μg/g;
13.碳屑状样块中碳含量为10~50μg/g,氢颗粒样块中氢含量为5-30μg/g,氧颗粒样块中氧含量为100~300μg/g,氮颗粒样块中氮含量为10~60μg/g。
14.在一可选的实施例中,还包括:
15.对原材料、铸锭进行元素成分检验,以获取熔炼过程中的铪铸锭中标准元素的含量变化及分布均匀性;
16.对得到的样块进行均匀性初检,以确定多组检测样块中标准元素含量的粗略差异性;
17.对得到的样块进行均匀性评估,以确定最小包装单元的样块组内和组间不存在显著性差异;
18.对得到的样块进行定值检验,以获取铪中标准物质元素的含量标称值。
19.在一可选的实施例中,所述晶条铪表面无氧化、鼓包、沾污及明显疏松,外观长晶一致性良好,沿长度方向挠度不大于30毫米;且所述晶条铪的碳、氢含量高于标准物质的目标值,氮、氧含量低于标准物质的目标值。
20.在一可选的实施例中,所述熔炼处理为对所述晶条铪进行熔炼、切割,所述熔炼与切割交替进行,且在熔炼处理开始时以熔炼开始、在熔炼处理结束时以熔炼结束;
21.熔炼时炉内真空漏率小于等于0.05pa/min,熔炼功率为2~3kw,熔炼时间为0.5~1h,每次熔炼后形成直径尺寸维度均匀一致的铪铸锭;
22.每次熔炼完成后,对得到的铪铸锭进行去头尾、扒皮各2mm后,切割成多等分,对多个铪块进行位置交叉、首尾翻转以重新排列组合,再进行下一步熔炼,通过物理“搅拌”达到成分元素均质化。
23.在一可选的实施例中,在熔炼处理过程中,通过渗石墨、掺入高碳含量的晶条铪的增碳方式提高碳的含量,通过提高熔炼功率、加入低碳含量的晶条铪原材料降低碳的含量。
24.在一可选的实施例中,在造粒过程或造粒后对氧、氢、氮元素的含量进行控制。
25.在一可选的实施例中,所述元素成分检验以高频感应熔融-红外吸收法测定碳含量,以脉冲加热-红外法测定氧含量,以脉冲加热-热导法测定氮、氢含量;
26.在熔炼处理过程中每次熔炼结束后进行元素成分检验。
27.在一可选的实施例中,在熔炼处理过程中,对每次熔炼后的铪铸锭进行元素成分检验,至标准元素的含量极差不大于根据标准元素含量目标值确定的最大允许要求时,停止熔炼。
28.在一可选的实施例中,加工处理得到碳屑状样块的过程为:对熔炼处理后得到的铪铸锭进行扒皮后,以固定方向、0.15~0.2mm的给进量进行机械加工,剩余直径为初始直径10%~20%的芯体不加工,制备得到碳屑状样块。
29.在一可选的实施例中,加工处理得到氢、氧、氮颗粒样块的过程为:对熔炼处理后得到的铪铸锭进行扒皮后,通过热挤压、直线度校正、酸洗、锯端、热轧、直线度校正、锯端、热拉拔、磨制抛光、截断造粒、除油清洗、酸洗、超声纯化清洗、风干过程,制备氢、氧、氮颗粒状样块。
30.在一可选的实施例中,所述均匀性检验采用单因素方差分析方法判断组内和组间检测结果的显著性差异,以判断所得样块是否均匀。
31.在一可选的实施例中,所述标准物质元素的含量标称值为各检测单位检测结果的
平均值;
32.所述定值检验的过程中还包括对测量结果的不确定度进行评定。
33.本发明的第二个目的在于提供一种铪标准物质,采用上述的方法制备得到。
34.本发明与现有技术相比,具有如下的优点和有益效果:
35.本发明实施例提供的一种铪标准物质的制备方法,能够制备得到铪中碳、氢、氧、氮标准物质,为铪中其它元素的标准物质的制备提供技术借鉴,解决目前采用ti、zr等同族元素标准物质替代铪标准物质而产生的铪材分析检测结果出现偏差的问题,实现更准确地校准铪材分析设备、评价铪材分析方法、人员技术水平,为铪材碳、氢、氧、氮元素分析提供质量评判标准。
附图说明
36.此处所说明的附图用来提供对本发明实施例的进一步理解,构成本技术的一部分,并不构成对本发明实施例的限定。在附图中:
37.图1为本发明实施例提供的一种铪标准物质的包装图。
38.图2为本发明实施例提供的一种铪标准物质的实物状态图(图2a为碳屑状样块、图2b为氢、氧、氮颗粒状样块)。
39.图3为本发明实施例提供的一种铪标准物质在制备过程中得到的铪铸锭的切割示意图。
40.图4为本发明实施例提供的一种铪标准物质在制备过程中得到的铪铸锭的切割实物图。
41.图5为本发明实施例提供的一种铪标准物质在制备过程中对氢、氧、氮颗粒状样块的铪热拉拔丝实物图。
具体实施方式
42.为使本发明的目的、技术方案和优点更加清楚明白,下面结合实施例和附图,对本发明作进一步的详细说明,本发明的示意性实施方式及其说明仅用于解释本发明,并不作为对本发明的限定。
43.为了解决目前国内使用ti、zr等同族元素标准物质替代铪标准物质而产生分析检测结果出现偏差的问题,实现更准确地校准铪材分析设备、评价铪材分析方法,为铪材碳、氢、氧、氮元素分析提供质量评判标准,本发明实施例提供了一种铪标准物质的制备方法,具体为:
44.以晶条铪为原材料,经过熔炼处理、成分检验、加工处理、均匀性检验、定值检验、包装得到碳屑状样块和氢、氧、氮颗粒样块,以该屑状样块和颗粒样块作为标准物质,可用于碳、氢、氧、氮分析仪校准及铪材产品中碳、氢、氧、氮的检测。
45.所述晶条铪,是指于表面不得有氧化、鼓包、沾污及明显的疏松,外观长晶一致性良好,沿长度方向挠度不大于30毫米。
46.所述晶条铪,是指其碳、氢含量应略高于标准物质的目标值,其氮、氧含量应略低于标准物质的目标值。优选地,晶条铪中碳含量为30~70μg/g,氢含量为10~40μg/g,氧含量为20~200μg/g,氮含量为5~40μg/g。
47.制备得到的碳屑状样块中碳含量为10~50μg/g,氢颗粒样块中氢含量为5-30μg/g,氧颗粒样块中氧含量为100~300μg/g,氮颗粒样块中氮含量为10~60μg/g。
48.所述熔炼处理,是指通过一次熔炼、一次切割、二次熔炼完成,或通过一次熔炼、一次切割、二次熔炼、二次切割、三次熔炼完成,或通过多次切割、多次熔炼完成;熔炼与切割交替进行,每次熔炼完成后,对得到的铪铸锭进行去头尾、扒皮各2mm后,切割成多等分;且第一次熔炼一定要使晶条铪快速成铪锭,以尽可能降低成分的损失,并快速形成直径尺寸维度的均匀性和一致性;熔炼处理时应控制熔炼功率、熔炼时间和熔炼气氛,以控制碳、氢的损失和氧、氮的增加;熔炼设备可以采用但不限于用真空电子束炉、感应炉、电弧(自耗或非自耗)炉等。在熔炼处理时,应控制熔炼功率、熔炼时间和熔炼气氛,以控制碳、氢的损失和氧、氮的增加。优选地,熔炼时控制炉内真空漏率小于等于0.05pa/min,熔炼功率为2~3kw,熔炼时间为0.5~1h。
49.在熔炼过程中,当元素含量需要控制时,应通过合适的手段加以控制。如对于碳元素的控制来说,当含量偏低时,应通过渗石墨、熔炼高含量晶条铪等手段进行增碳,当含量偏高时,应通过加入新的低含量晶条铪的方式进行控制。对于氧、氢、氮元素的控制来说,一般在热轧、热拉拔、酸洗等造粒过程进行控制,或在造粒后进行专门的增量或减量控制。
50.熔炼过程中的切割是指沿一定方向(如长度或径向)对铪铸锭进行多等分,其目的是将得到的多等分铪块进行位置交叉、首尾翻转等操作,重新排列组合后进行下一步熔炼,通过物理“搅拌”的手段促使成分元素均质化。
51.所述成分检验,是指通过高频感应熔融-红外吸收法测定碳含量,通过脉冲加热-红外法测定氧含量,通过脉冲加热-热导法测定氮、氢含量。在原材料领料后、二次熔炼后、三次熔炼后及多次熔炼后均进行成分检验,通过极差、标准偏差等统计学方法初步判断元素分布的均匀性,当标准元素的含量极差不大于根据标准元素含量目标值确定的最大允许要求时,停止熔炼。
52.成分检验过程中,对每一支晶条铪、铪铸锭扒皮后,分别在可能造成碳、氢、氧、氮的分布不均匀的位置进行取样,比如在表面和芯体、端面和中部,以检验元素分布的均匀性。
53.所述加工处理,是指对铪铸锭扒皮后,按照固定的方向(顺时针或逆时针)、一定的给进量(一般为零点几毫米,应根据碳含量的高低和均匀性水平确定)进行机械加工,剩余一定直径的芯体不加工,如当剩余芯体的直径为初始直径10%~20%时,停止加工,制备碳屑状样块。
54.加工处理具体过程是指:对铪铸锭扒皮后,通过热挤压、直线度校正、精整处理、酸洗、锯端、热轧、直线度校正、精整处理、锯端、热拉拔、磨制抛光、截断造粒、除油清洗、酸洗、超声纯化清洗、风干等过程,制备氢、氧、氮颗粒状样块。
55.本发明实施例制备得到的碳屑状样块,应根据车屑过程中的直径变化,分数份或数十份分别收集于洁净的容器中,其份数应根据碳含量目标值高低制定,以备用于均匀性检验。
56.制备得到的氢、氧、氮颗粒状样块,应以一定的长度或一定的重量为单位,分数份或数十份分别收集于洁净的容器中,其份数应根据氢、氧、氮含量目标值高低制定,以备用于均匀性检验。
57.所述均匀性检验,是选取精密度及灵敏度不低于定值方法的测量方法,在重复性条件下进行均匀性检验。在每一份样块的容器中随机取样,其取样量应根据碳、氢、氧、氮含量目标值高低制定。将随机取出的样块均分成若干份(至少2份),并随机混合编组,按相同方法进行检验。各组内各检测结果及各组平均值之间的检测结果极差,应不大于根据元素含量目标值确定的最大允许要求。
58.所述定值检验,是指选取现行检测方法中准确度、精密度及灵敏度较高的测量方法,在重复性条件下进行定值检验。是指将全部容器内的样块混合均匀后,包装成若干份最小单位,在若干份最小单位中随机抽取数份(一般不低于6份)进行检验,其份数应根据若干最小单位的数量、元素含量目标值及统计学规律进行确定;是将随机抽取的数份(一般不低于6份)每一份均分为若干份(至少2份),分别送至若干家(至少2家)检测单位,用相同方法进行检验,各家单位间各份的检测结果,应不大于根据元素含量目标值确定的最大允许要求;对各家单位全部的检验结果进行统计学筛选后的检验结果的平均值,作为该批铪标准物质的元素含量标称值。对铪标准物质的元素含量标称值应给出测量结果的不确定度。
59.所述包装,是指具有较好封闭性的不含氯元素的塑料或玻璃瓶,在外包装上粘贴打印信息标签,包含标准物质名称、标称值、不确定度、生产单位、生产日期等有关信息,并在标准物质质量保证书上详细标注制备过程简介、存放条件、有效期、检验印鉴、执行标准等有关信息。
60.以下以制备一种表1所述的铪中碳、氢、氧、氮标准物质各1kg为例对本发明进行详细说明。
61.表1目标铪标准物质
62.元素外观形状目标值范围,μg/gc屑状10-50h颗粒状ф1.5mm
×
(5~10)mm5-30o颗粒状ф1.5mm
×
(5~10)mm100-300n颗粒状ф1.5mm
×
(5~10)mm10-60
63.第一步:原材料的选取。
64.选取表面没有氧化、鼓包、沾污及明显的疏松,外观长晶一致性良好,粗细较均匀,沿长度方向挠度不大于30毫米的晶条铪作为原材料,备用。每一支晶条铪均进行取样,对原材料中的各元素含量进行检测,用高频感应熔融-红外吸收法测定碳含量,通过脉冲加热-红外法测定氧含量,通过脉冲加热-热导法测定氮、氢含量,并其测量结果应满足表2所述。然后,预估熔炼、扒皮、检验等工艺过程的损耗约50%,各精选2kg晶条铪(碳多0.4kg)作为原材料。
65.表2晶条铪原材料元素含量
66.元素目标值,μg/gc30-70h10-40o50-200n5-40
67.第二步:熔炼处理。
68.在yhj-600真空氩弧焊箱中,将2kg晶条铪制备成宽度、高度、长度适当的捆绑电极,将捆绑好的电极装进氩弧焊箱中进行焊接。去除捆绑铁丝,将电极放入300kw真空电子束炉中,调节电炉真空度至设备要求,在熔炼过程持续关注真空度,确保漏率不大于0.05pa/min。调节电炉功率,使功率和熔速合理配合,控制液面高度和熔池饱满程度,减少冷隔、气孔、缩颈等熔炼缺陷,使电极形成直径尺寸维度均匀一致的的铸锭。
69.熔炼完成后,对铪铸锭进行去头尾、扒皮各2mm,对截面进行四等分(图3),沿长度方向进行切割得到四块铪扇形柱(图4)。然后,将得到的四块铪扇形柱其中两块进行位置交叉(1与4、2与3),另外两块进行首尾翻转,重新排列组合后进行下一步熔炼,以均匀化成分元素。
70.按照上述方法,再次制备电极、再次熔炼得到新的铪铸锭。
71.第三步:取样检测。
72.对铪铸锭进行去头尾、扒皮各2mm,然后分别在两端面1/2半径处及沿长度方向均分两个点,共四个点进行取样检测。四个点取样检测其元素含量极差,应不大于表3确定的最大允许要求。
73.超过极差最大允许要求的,应重复“第二步熔炼处理”并按本步骤再次取样检测,直至满足表3给出的要求。
74.表3极差最大允许要求
[0075][0076]
第四步,样块的加工。
[0077]
碳屑状样块的加工:取样检验满足表3要求后,从右端面开始向左,以0.15mm~0.2mm的给进量对铪铸锭进行机械加工,剩余6mm直径的芯体不加工,制备碳屑状样块,并根据车屑过程中的直径变化(表4),分4份分别收集于洁净的容器中。
[0078]
表4车屑直径变化分组办法
[0079]
序号沿直径方向到表面的距离(扒皮后表面为0mm),mm10-525-10310-15415-20
[0080]
氧、氮、氢颗粒状样块的加工:通过热挤压、直线度校正、酸洗、锯端、热轧、直线度校正、锯端、热拉拔(图5)、磨制抛光、截断造粒、除油清洗、酸洗、超声纯化清洗、风干等过程,制备氢、氧、氮颗粒状样块(图2b)。造好的粒,按重量每0.25kg为一份,共四份分别收集于洁净的容器中。
[0081]
第五步,均匀性初检。
[0082]
在每一份样块的容器中随机选取10g样品,用高频感应熔融-红外吸收法测定碳含量,通过脉冲加热-红外法测定氧含量,通过脉冲加热-热导法测定氮、氢含量,每一份样品独立分析3次,测量结果见表5。
[0083]
表5均匀性初检结果
[0084][0085]
由各份三次测量结果的平均值之间的极差初步判断样块的均匀性,平均值之间的极差不得大于表3所述的要求。以氧标准物质为例,4份样块测量结果的平均值之间的极差为0.0019%,满足表3规定的,氧含量为0.0100%~0.0200%时,极差最大不得超过0.0020%的要求,可以认为样品是比较均匀的。
[0086]
第六步,均匀性评估。
[0087]
将通过均匀性初检的全部容器内的样块混合均匀,包装成100份10g每份的小瓶(最小单位),开展均匀性评估。
[0088]
通过单因素方差分析方法(f检验法)判断组内和组间检测结果的显著性差异,评估样块的均匀性。设组数为m,每组重复测量次数为ni(i=1,2,3
…
,m),总数据个数为n,每组平均值为全部数据平均值为每组平均值对全部数据平均值的差方和为q1、自由度为f1、组间方差为s
12
,组内数据之间的差方和为q2、自由度为f2、组内方差为s
22
,方差统计量为f。根据方差分析方法,可得
[0089]
组间差方和为:
[0090][0091]
组内差方和为:
[0092][0093]
组间自由度为:
[0094]
f1=m-1
[0095]
组内自由度为:
[0096]
f2=n-m
[0097]
组间方差为:
[0098][0099]
组内方差为:
[0100][0101]
则,得统计量f为
[0102][0103]
以碳为例加以说明。在100份最小单位中随机抽取10份(即10组),每组测量3次,用相同方法测量,其测量结果见表6。
[0104]
表6碳均匀性测量结果
[0105][0106][0107]
由表6得,q1=1.59
×
10-9
,q2=1.53
×
10-9
,f1=9,f2=20;则s
12
=1.76
×
10-10
,s
22
=7.67
×
10-11
;得统计量f=2.30。
[0108]
设置信度为95%,则显著性水平为α=0.05,查fa分布临界值表得,f
0.05
[f1,f2]=f
0.05
[9,20]=2.39>f=2.30,满足f<f
0.05
,说明该组数据没有明显差异,可以认为碳屑状
样块是均匀的。
[0109]
第六步,定值检验。
[0110]
在100份小瓶中随机抽取8份,随机送至4家检测单位,每家单位检测2份,每份检测2次,每个实验室提供4个数据。用高频感应熔融-红外吸收法测定碳含量,通过脉冲加热-红外法测定氧含量,通过脉冲加热-热导法测定氮、氢含量。
[0111]
将各家单位全部的检验结果进行统计学筛选(包括组内可疑值剔除、组间等精度判定、合并数据正态性检验)后,将各家单位的平均值再求平均值,得到的总平均值即为该批铪标准物质的元素含量标称值。根据不确定度评定规则,考虑称量、标准曲线、重复测量、样品均匀性等环节引入的不确定度,对测量结果的不确定度进行评定,对铪标准物质的元素含量标称值给出测量结果的不确定度(表7)。
[0112]
表7铪标准物质标称值及不确定度
[0113]
元素标称值,%扩展不确定度(k=2),%c0.00170.0002h0.00280.0005o0.01620.0024n0.00110.0004
[0114]
第七步,包装。
[0115]
用具有较好封闭性的不含氯元素的塑料或玻璃瓶包装定值结束后剩下的最小单位,并在瓶子外表面装上粘贴打印信息标签,包含标准物质名称、重量、标称值、不确定度、生产单位、生产日期等有关信息,并在标准物质质量保证书上详细标注制备过程简介、存放条件、有效期、检验印鉴、执行标准等有关信息。包装图如图1中所示。
[0116]
本专利申请中,未提及的过程、方法均为现有技术或通过现有技术可以得到。
[0117]
本发明实施例提供的制备方法能够制备得到铪中碳、氢、氧、氮标准物质,为铪中其它元素的标准物质的制备提供技术借鉴,解决目前采用ti、zr等同族元素标准物质替代产生铪材分析检测结果出现偏差的问题,实现更准确地校准铪材分析设备、评价铪材分析方法、人员技术水平。通过本发明实施例的标准物质,为铪材碳、氢、氧、氮元素分析提供质量评判标准,为我国铪材生产检测技术的改进提供技术支持,为相关产品的质量控制和稳定性提供技术支撑。
[0118]
以上所述的具体实施方式,对本发明的目的、技术方案和有益效果进行了进一步详细说明,所应理解的是,以上所述仅为本发明的具体实施方式而已,并不用于限定本发明的保护范围,凡在本发明的精神和原则之内,所做的任何修改、等同替换、改进等,均应包含在本发明的保护范围之内。