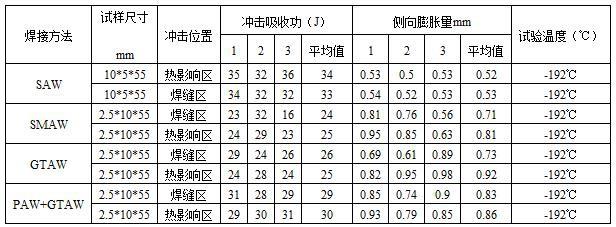
1.本发明涉及低温罐箱技术领域,具体涉及一种应变强化低温罐箱的罐体焊接方法。
背景技术:2.应变强化低温罐箱的罐体部分是罐箱中的重要组成部件,是核心部件,其作用是用来装载易燃、易爆及有毒危害介质。因为需要进行应变强化,所以对罐体的焊接接头质量比较普通焊接接头要求高,而且罐体的焊接质量和焊接效率决定了整个产品的质量和生产速度。目前罐体的环缝和纵缝主要使用埋弧焊、手把焊、氩弧焊等常用焊接方法,低温罐箱罐体是一种大直径筒体结构,焊接量较大,使用手把焊和氩弧焊焊接效率低、工期较长,且外观成型和焊缝一次合格率对焊工水平要求很高,易出现夹渣、气孔、未焊透等因人工操作出现的焊接缺陷,埋弧焊需要背面清根,而且由于应变强化技术下内罐体一般为s30408等材料,碳弧气刨清根需要考虑渗碳和打磨清根部位,工作量大且存在影响焊缝质量的风险,并且应变强化技术要求不允许增设人孔所以封闭环缝需单面焊双面成型且背面无法进行气体保护(要背面进行气体保护需整个罐体充满保护气体)故对此焊缝无法使用埋弧焊,手工焊存在上述弊端,焊缝合格率不稳定,而且封闭焊缝返修困难。除此之外这些常用焊接方法都存在需要坡口加工、焊层间清理,延长生产周期和增加焊接耗材使用,提高了生产成本的缺点。
3.paw+gtaw自动焊具有线能量低、能量集中、焊接变形小、单面焊双面成型、极少填充材料、焊接效率高、焊接接头性能好、一次合格率高、成型美观等优点,而且应变强化下的低温罐箱罐体厚度在3~8mm之内,使用paw+gtaw自动焊无需坡口加工和层间清理,施焊环境良好无污染避免后期为罐体内部后期脱脂清洗带来不必要的负担,所以此工艺完全适用于应变强化下的低温罐箱罐体的焊接。但是paw+gtaw自动焊缺乏合理的施焊准备和工艺参数,使得paw+gtaw自动焊在应变强化低温罐箱的生产中使用受到局限,因此,研制开发合理的焊接工艺对于应变强化下的低温罐箱制造是积极有利的。
技术实现要素:4.针对焊接质量差、效率低等技术问题,本发明提供一种应变强化低温罐箱的罐体焊接方法,提高了罐体焊接时的合格率,提高生产效率,进而降低成本。
5.本发明提供一种应变强化低温罐箱的罐体焊接方法,包括普通环缝及纵缝焊接、封闭环缝焊接;普通环缝及纵缝焊接包括如下步骤:s1、对各罐体筒节焊接坡口预处理;s2、将各罐体筒节吊运至组对台位进行组对、定位焊,然后吊运至焊接台位并将普通环缝及纵缝待焊缝位置调制至最底部;s3、依次采用paw+gtaw自动焊对普通环缝、纵缝焊接;
对普通环缝焊接时焊机位于罐体内部,焊机处的罐体外部设有紧贴罐体外表面的第一气体保护装置,第一气体保护装置可形成保护气体封闭空间并充填有保护气体,焊接时采用焊机及第一气体保护装置固定、罐体旋转的方式焊接;对纵缝焊接时焊机位于罐体内部,焊机处外部设有紧贴罐体外表面的第二气体保护装置,第二气体保护装置可形成保护气体封闭空间并充填有保护气体,焊接时采用焊机及第二气体保护装置同步纵向移动、罐体固定的方式焊接;封闭环缝焊接包括如下步骤:p1、对罐体筒节两端焊接坡口预处理;p2、用吊运设备将罐体封头吊运至组对台位进行组对、定位焊,定位焊时在坡口内侧焊接垫板;p3、采用gtaw自动焊在罐体外侧对封闭环缝焊接。
6.进一步的,步骤s1中坡口预处理的方法为:坡口为“i”型坡口,用不锈钢打磨工具对坡口及两侧20mm范围内修正和清理,清除坡口表面铁屑、油污、水分、挂渣及氧化皮。
7.进一步的,步骤s2中,组对的方法为:组对间隙≤1mm,坡口错边量≤1/4筒体厚度,错边量≤1mm,纵缝增加50mm
×
50mm等厚引弧板和熄弧板。
8.进一步的,步骤s2中,定位焊的方法为:采用氩弧焊点焊,间距为500~600mm,均匀分布,焊缝余高≤0.5mm。
9.进一步的,第一气体保护装置、第二气体保护装置均具有如下结构:包括顶部具有开口的盒体,盒体开口处连接有环形柔性密封带,环形柔性密封带上端与罐体外表面紧密贴合,盒体内设有气体导管,气体导管设有气孔,气体导管通过软管与外部保护气体供气装置连接。
10.进一步的,步骤s3中,paw+gtaw自动焊焊接参数为:paw焊接,电流极性为dcen,电流为170~190a,电压为24~248v,焊速为26~30cm/min,线能量为≤12.3kj/cm;gtaw焊接,焊材类型为er308l焊丝,焊材规格为φ1.0mm,电流极性为dcen,电流为190~210a,电压为12~15v,焊速为26~30cm/min,线能量为≤7.2kj/cm。
11.进一步的,步骤s3中,焊机及第二气体保护装置同步纵向移动的结构为:在罐体纵缝的正下方设有与纵缝平行的滑轨,第二气体保护装置可沿滑轨滑动,位于罐体内部的焊机与位于罐体外部的第二气体保护装置通过u型杆连接。
12.进一步的,步骤p1中,坡口预处理的方法为,坡口角度为10
°
~15
°
,无钝边,坡口间隙为3~4mm,底部加4mm同材质垫板,垫板与筒体间隙为0~0.3mm,垫板、坡口及两侧20mm范围内进行修正和清理。
13.进一步的,步骤p2中,组对的方法为,坡口错边量≤1/4筒体厚度,错边量≤1mm;定位焊的方法为,坡口内侧垫板与筒节采用氩弧焊点焊,间距为500~600mm,均匀分布,焊缝余高≤0.5mm。
14.进一步的,gtaw自动焊的焊接方法为,首先在焊缝处打底,再进行填充与盖面,引弧和熄弧部位重叠10-20mm;打底焊接参数为,焊材类型为er308l焊丝,焊材规格为φ1.0mm,电流极性为dcen,电流为170~190a,电压为12~14v,焊速为28~32cm/min,线能量为≤5.7kj/cm;填充与盖面焊接参数为,焊材类型为er308l焊丝,焊材规格为φ1.0mm,电流极性为dcen,电流为190~210a,电压为12~15v,焊速为26~30cm/min,线能量为≤7.2kj/cm。
15.本发明的有益效果在于:本发明采用paw+gtaw自动焊实现了应变强化下低温罐箱的罐体部分主体焊缝的自动化焊接,极大地降低成本和提高生产效率,本发明焊接工艺一次性焊接合格率达98.6%以上。
附图说明
16.为了更清楚地说明本发明实施例或现有技术中的技术方案,下面将对实施例或现有技术描述中所需要使用的附图作简单地介绍,显而易见地,对于本领域普通技术人员而言,在不付出创造性劳动的前提下,还可以根据这些附图获得其他的附图。
17.图1是本发明具体实施方式普通环缝焊接结构示意图。
18.图2是本发明具体实施方式纵缝焊接结构示意图。
19.图3是本发明具体实施方式第一、第二气体保护装置结构示意图。
20.图4是本发明具体实施方式气体导管结构示意图。
21.图中,1-高度可调式固定支撑,2-筒节,3-盒体,4-焊机,5-滑轨,6-气体导管,7-u型杆,8-软管,9-环形柔性密封带。
具体实施方式
22.为了使本技术领域的人员更好地理解本发明中的技术方案,下面将结合本发明实施例中的附图,对本发明实施例中的技术方案进行清楚、完整地描述,显然,所描述的实施例仅仅是本发明一部分实施例,而不是全部的实施例。基于本发明中的实施例,本领域普通技术人员在没有做出创造性劳动前提下所获得的所有其他实施例,都应当属于本发明保护的范围。
23.实施例1本实施例为2台应变强化45ft低温罐箱罐体焊接,罐体组成分为内罐体和外罐体,内外罐体材质为s30408,内罐体内径2275mm,长度13318mm,壁厚5.5mm,外罐体内径2418mm长度13466mm,壁厚4mm。内罐体由6节筒体和2个封头组成,其中普通环缝和纵缝各6条,封闭环缝1条,外罐体由7节筒体和2个封头组成,其中普通环缝8条,纵缝7条。
24.所述的应变强化低温罐箱的罐体焊接方法,包括普通环缝及纵缝焊接、封闭环缝焊接;普通环缝及纵缝焊接包括如下步骤:s1、对各罐体筒节2焊接坡口预处理,坡口预处理的方法为:坡口为“i”型坡口,用不锈钢打磨工具对坡口及两侧20mm范围内修正和清理,清除坡口表面铁屑、油污、水分、挂渣及氧化皮;s2、将各罐体筒节2吊运至组对台位进行组对、定位焊,组对的方法为:组对间隙≤1mm,坡口错边量≤1/4筒体厚度,错边量≤1mm,纵缝增加50mm
×
50mm等厚引弧板和熄弧板,定位焊的方法为:采用氩弧焊点焊,间距为500~600mm,均匀分布,焊缝余高≤0.5mm,然后吊运至焊接台位并将普通环缝及纵缝待焊缝位置调制至最底部;s3、依次采用paw+gtaw自动焊对普通环缝、纵缝焊接;如图1,对普通环缝焊接时焊机4位于罐体内部,焊机处的罐体外部设有紧贴罐体外表面的第一气体保护装置,第一气体保护装置设置于高度可调式固定支撑1上,如图3、4
所示,第一气体保护装置包括顶部具有开口的盒体3,盒体3开口处连接有环形柔性密封带9,环形柔性密封带9选用耐高温耐磨材料,如耐温橡胶等,环形柔性密封带9上端与罐体外表面紧密贴合,盒体3内设有气体导管6,气体导管6设有气孔,气体导管6通过软管8与外部保护气体供气装置连接,第一气体保护装置可形成保护气体封闭空间并充填有保护气体,保护气体为氩气,焊接时采用焊机4及第一气体保护装置固定、罐体旋转的方式焊接,罐体通过滚轮架旋转,图1中a处为焊接点;如图2,对纵缝焊接时焊机4位于罐体内部,焊机4处外部设有紧贴罐体外表面的第二气体保护装置,第二气体保护装置与第一气体保护装置结构相同,第二气体保护装置可形成保护气体封闭空间并充填有保护气体,保护气体为氩气,焊接时采用焊机4及第二气体保护装置同步纵向移动、罐体固定的方式焊接,焊机4及第二气体保护装置同步纵向移动的结构为:在罐体纵缝的正下方设有与纵缝平行的滑轨5,第二气体保护装置可沿滑轨5滑动,位于罐体内部的焊机4与位于罐体外部的第二气体保护装置通过u型杆7连接,通过u型杆7焊接伸缩臂水平移动带动焊机4及第二气体保护装置同步纵向移动,图2中b处为焊接点;步骤s3中,paw+gtaw自动焊焊接参数如表1所示,焊机4自带气体保护装置及第一、第二气体保护装置的气体流量见表2。
25.表1 paw+gtaw自动焊焊接参数表2 焊机自带气体保护装置及第一、第二气体保护装置的气体流量封闭环缝焊接包括如下步骤:p1、对罐体筒节两端焊接坡口预处理,坡口预处理的方法为,坡口角度为10
°
~15
°
,无钝边,坡口间隙为3~4mm,底部加4mm同材质垫板,垫板与筒体间隙为0~0.3mm,垫板、坡口及两侧20mm范围内进行修正和清理;p2、用吊运设备将罐体封头吊运至组对台位进行组对、定位焊,组对的方法为,坡口错边量≤1/4筒体厚度,错边量≤1mm;定位焊的方法为,坡口内侧垫板与筒节采用氩弧焊点焊,间距为500~600mm,均匀分布,焊缝余高≤0.5mm,定位焊时在坡口内侧焊接垫板;p3、采用gtaw自动焊在罐体外侧对封闭环缝焊接,gtaw自动焊的焊接方法为,首先在焊缝处打底,再进行填充与盖面,引弧和熄弧部位重叠10~20mm;步骤p3中,gtaw自动焊的焊接参数如表3所示,焊接时保护气体氩气流量为16-20l/min。
26.表3 gtaw自动焊的焊接参数
gtaw自动焊焊材类型焊材规格/mm电流极性电流/a电压/v焊速/cm/min线能量kj/cm打底er308lφ1.0dcen170-19012-1428-32≤5.7填充和盖面er308lφ1.0dcen190-21012-1526-30≤7.2
对比例
对比例上对实施例1中相同的2台应变强化45ft低温罐箱罐体进行焊接,所不同的是对比例分别采用传统的saw、smaw、gtaw焊接方法进行焊接。
27.对实施例1中paw+gtaw自动焊及对比例各焊接方法分别取样,按照nb/t47014进行冲击试样制作,按照gb/t229和nb/t47014进行冲击实验,以检测奥氏体不锈钢焊接接头焊接内部情况及相关的韧性能力,各个焊接接头数据如表4所示;按照nb/t47014进行拉伸试样制作,按照gb/t228进行拉伸实验,检测不同焊接方法对焊接接头的力学性能影响。实验得出各个焊接接头抗拉强度数据如表5所示;按照tcatsi 05001-2018进行弯曲试样制作,按照gb/t2653和nb/t47014进行弯曲实验,以检测奥氏体不锈钢焊接接头焊接内部情况及相关的塑性能力,各个焊接接头取面弯背弯各2个,数据如表6所示。
28.表4 实施例1及对比例各个焊接接头性能测试数据表5 实施例1及对比例各个焊接接头抗拉强度数据表6实施例1及对比例各个焊接接头弯曲实验结果由表4、5、6可以看出,本发明paw+gtaw自动焊的焊接接头性能在冲击试验、抗拉试验、弯曲性能优于saw、手工gtaw、smaw。
29.本发明通过以上焊接工艺(paw+gtaw自动焊)实现了应变强化下低温罐箱的罐体
部分所有主体焊缝的自动化焊接,极大地降低成本和提高生产效率,本发明焊接工艺只需一名焊机操作工就可完成全部焊接工作,而smaw、saw、手工gtaw至少需要2名焊接人员,在人员数量上有很大优势;而且焊接生产效率约是手工焊(smaw、gtaw)的4-5倍,约是swa的1倍;同时节约了加工坡口和碳弧气刨的工作时间,对于普通环纵缝基本无使用焊材,节约了焊材成本。
30.经过长时间生产实践中对焊缝合格量数据的统计,本发明所述的焊接工艺一次合格率高达98.6%以上。
31.尽管通过参考附图并结合优选实施例的方式对本发明进行了详细描述,但本发明并不限于此。在不脱离本发明的精神和实质的前提下,本领域普通技术人员可以对本发明的实施例进行各种等效的修改或替换,而这些修改或替换都应在本发明的涵盖范围内/任何熟悉本技术领域的技术人员在本发明揭露的技术范围内,可轻易想到变化或替换,都应涵盖在本发明的保护范围之内。