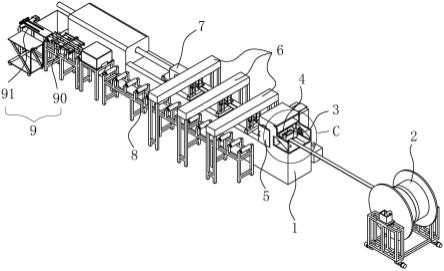
1.本实用新型涉及铜排生产设备技术领域,尤其涉及一种生产铜排的全自动液压拉拔机。
背景技术:2.现有用于铜排加工的液压拉拔机,将卷在上料辊待挤压拉拔的原材料经过模具,在液压拉拔机构的带动下形成目标的形状和尺寸,为了保证表面的光滑不磨损,在进入挤压模具前先在原材料的表面的喷淋润滑液,对所得铜排的表面进行保护;所得铜排经过拉拔后切断得到一定长度的铜排,转移后进一步进行切割为更短的规格,再人工分拣下料,整个生产加工属于开放式的结构,存在以下问题:喷淋液的利用效率低;切割过程高温碎屑飞溅,不利于碎屑收集的同时威胁工作人员的人身健康;经切割的铜排还具有较高的余温,人工上下料不方便,且容易烫伤。
技术实现要素:3.本实用新型的目的在于提供一种全自动液压拉拔机,本实用新型构建半闭合的生产空间,减少对外部环境的影响,提高自动化生产性能和安全性。
4.为解决此技术问题,本实用新型的技术方案是:一种全自动液压拉拔机,沿着铜排加工的上料方向依次包括上料辊以及安装于机架的润滑液喷淋装置、挤压成型组件和液压拉拔组件,在挤压成型组件和液压拉拔组件之间还设置有将成型的铜排切割分段的切割组件;还包括将切割分段后的铜排夹持移位至传动组件下料的自动下料组件;沿着下料的方向还包括自动分拣组件,自动分拣组件将自动下料组件上的铜排分别向着自动下料组件的左右两侧推动分拣下料。
5.优选的,所述润滑液喷淋装置包括喷淋单元、供液单元以及回收单元,所述喷淋单元管道连接供液单元,所述供液单元与回收单元管道连接形成润滑液的循环;所述喷淋单元包括喷淋件,所述喷淋件分布于铜排的上下两侧且中部连接于供液单元;所述回收单元包括收集盒,收集盒和与收集盒分体设置的回流件,所述收集盒下方设有过滤网,所述回流件朝向所述过滤网用于收集经过过滤网的润滑液的开口端;所述过滤网和所述回流件的开口端之间留有间距;所述收集盒和所述喷淋单元通过移位组件同步移动或者定位。
6.上述设置中,收集盒围绕着的喷淋单元形成半封闭状态设置,期间阻隔了飞溅的润滑液,促使润滑液集中于收集盒内,避免外部环境对润滑液的污染;集中后的润滑液经过过滤网的过滤流入回流件内,其中减少润滑液掺杂其他物质,提高使用寿命。
7.优选的,所述切割组件包括安装于机架密封壳体,所述壳体内装有相对待切割铜排相对移动的刀具,所述刀具通过水平移动组件在水平方向往复移动;与所述刀具处于相对铜排两侧的所述壳体处设有一相对壳体发生水平方向移动打开或者关闭壳体的移门;所述移门安装于连接件上,通过连接件沿着水平方向设有的安装轴相连接形成水平方向往复移动;所述壳体下部设有一向着远离铜排方向内凹的收集部。
8.上述设置中,在切割的最大外围处设置了半封闭状态的罩壳,相对人工操作方向设置了有一移动门,为了便于设备在出现故障时进形检修及更换挤压模具;当移门关上时形成了一个封闭状态的加工空间,阻隔在切割过程中高温碎屑的飞溅,同时飞溅的碎屑自动落入收集部内,从而减少对外部环境的影响,节省清理时间。
9.优选的,所述自动分拣组件包括移动路径定位机构和分拣机构;所述移动路径定位机构包括沿着已切割铜排移动路径设置的两竖直设置的挡板,所述两挡板之间形成铜排的移动路径;所述两挡板通过距离调节结构相对移动;所述分拣机构在铜排的移动路径两侧往复移动。
10.上述设置中,铜排向着下料方向移动经过移动路径定位机构的两挡板之间设定的位置以及定位方向,依次排序移动至分拣机构内,分拣机构垂直于铜排移动路径往复移动,将已在分拣机构内的铜排进行推动至合格或者不合格放置区,其中避免人员对切割后还是具有较高温度的铜排直接接触,提高分拣效率。
11.优选的,在相对所述挤压成型组件有一将成型铜排待夹持的所述液压拉拔组件;所述液压拉拔组件包括两夹板,通过两夹板将已整形后的铜排进行夹持且沿着机架水平方向移动形成拉拔,在相对两夹板的四周各设有一滑轮,所述滑轮沿着机架水平方向设置;所述滑轮与机架导轨之间相配合形成所述液压拉拔组件滑动导向并进行往复移动。
12.上述设置中,铜排在挤压模具挤压整形的同时经过拉拔机构的夹持拉拔,两者相互配合操作下,有助于铜排形成目标的形状和尺寸。
13.优选的,在所述切割组件和所述液压拉拔组件之间还设置有将成型切割分段后的铜排夹持移位的自动下料组件;所述自动下料组件包括夹持机构,所述夹持机构在铜排的上端设有固定的第一夹持板,相应的铜排下端设有相对第一夹持板的第二夹持板,通过第二夹持板向着第一夹持板移动时,将已存在两者之间的铜排进行夹持及固定;所述夹持机构通过链轮传动在垂直于移动路径方向进行往复移动,将已夹持的铜排移位到传动组件;所述自动下料组件具有多个,且横向一字排列于机架和传动组件上方。
14.上述设置中,自动下料组件排列在垂直于铜排移动路径上方,已切割成型的铜排需要多组自动下料组件同时进行夹持和移动,再传递到下一工位,实现工位之间自动流转,有效的提高自动化生产性能。
15.优选的,所述传动组件安装在与所述机架水平方向的一侧,还与机架竖直方向之间设有间距;所述传动组件由多个滚筒和架子组成,将已放置的铜排通过电机驱动滚筒向着下料方向传送。
16.上述设置中,铜排自动经过传动组件传送至下一工位,该设置实现工位之间的自动化流转。
17.综上所述,与现有技术相比,本实用新型具有以下有益效果:
18.本实用新型中,铜排依次通过润滑液喷淋装置、挤压成型组件、液压拉拔组件、切割组件、传动组件、自动下料组件和自动分拣组件形成一个工位之间自动流转生产线,其中对喷淋后整形、切割分段以及下料后分拣构建了半封闭加工环境,减少了对人工及外部的影响,从而提升生产线的自动化和安全性能。
附图说明
19.图1是本实用新型涉及的一种全自动液压拉拔机的结构示意图;
20.图2是本实用新型的润滑液喷淋装置的c局部示意图;
21.图3是本实用新型的润滑液喷淋装置局部结构图;
22.图4是本实用新型的润滑液喷淋装置中的d局部示意图;
23.图5是本实用新型的切割组件的密封壳体结构图;
24.图6是本实用新型的切割组件结构图;
25.图7是本实用新型涉及的一种全自动液压拉拔机的结构示意图;
26.图8是本实用新型的夹持下料流向的e局部结构示意图;
27.图9是本实用新型的自动分拣组件f局部结构示意图;
28.图中标号为:
29.1、机架;11、机架导轨;2、上料辊;3、润滑液喷淋装置;31、喷淋单元;311、喷淋件;32、供液单元;33、回收单元;331、收集盒;332、回流件;333、过滤网;34、移位组件;4、挤压成型组件;5、切割组件;51、壳体;52、水平移动组件;521、刀具;53、移门;531、安装轴;532、连接件;54、收集部;6、自动下料组件;61、夹持机构;611、第一夹持板;612、第二夹持板;7、液压拉拔组件;71、两夹板;72、滑轮;8、传动组件;81、滚筒;82、架子;9、自动分拣组件;90、路径定位机构;901、调节结构;9011、挡板;91、分拣机构。
具体实施方式
30.为了更好的理解本实用新型技术内容,下面提供具体实施例,并结合附图对本实用新型做进一步说明。
31.如图1至图7所示,一种全自动液压拉拔机,沿着铜排加工的上料方向依次包括上料辊2以及安装于机架1的润滑液喷淋装置3、挤压成型组件4和液压拉拔组件7,在挤压成型组件4和液压拉拔组件7之间还设置有将成型的铜排切割分段的切割组件5;还包括将切割分段后的铜排夹持移位至传动组件8下料的自动下料组件6;沿着下料的方向还包括自动分拣组件9,自动分拣组件9将自动下料组件6上的铜排分别向着自动下料组件6的左右两侧推动分拣下料。
32.进一步的,如图2、3、4所示,润滑液喷淋装置3包括喷淋单元31、供液单元32以及回收单元33,喷淋单元31管道连接供液单元,供液单元32与回收单元33管道连接形成润滑液的循环;喷淋单元31包括喷淋件311,喷淋件311分布于铜排的上下两侧且中部连接于供液单元32;回收单元33包括收集盒331,收集盒331和与收集盒分体设置回流件332,收集盒331下方设有过滤网333,回流件332朝向过滤网333用于收集经过过滤网333的润滑液的开口端;过滤网333和回流件332的开口端之间留有间距;收集盒331和喷淋单元31通过移位组件34同步移动或者定位。收集盒331围绕着喷淋单元31形成半封闭状态设置,期间阻隔了飞溅的润滑液,促使润滑液集中于收集盒331内,避免外部环境对润滑液的污染;集中后的润滑液经过过滤网333的过滤流入回流件332内,其中减少润滑液掺杂其他物质,提高使用寿命。
33.进一步的,如图5、6所示,切割组件5包括安装于机架密封壳体51,壳体51内装有相对待切割铜排相对移动的刀具521,刀具521通过水平移动组件52在水平方向往复移动;与刀具521处于相对铜排两侧的壳体51处设有一相对壳体51发生水平方向移动打开或者关闭
壳体的移门53;移门53安装于连接件532上,通过连接件532沿着水平方向设有的安装轴531相连接形成水平方向往复移动。当移门53关闭并工作时,切割组件5工位呈现封闭状态,使得在切割过程中挡住了高温碎屑的飞溅,从而减少对外部环境的影响;在壳体51下部设有一向着远离铜排方向内凹的收集部54,通过壳体51和移门53四周围合促使在切割时产出的碎屑能够有效落入收集部54内,从而节省人工清理时间。
34.进一步的,如图9所示,自动分拣组件9包括移动路径定位机构90和分拣机构91;移动路径定位机构90包括沿着已切割铜排移动路径设置的两竖直设置的挡板9011,两挡板9011之间形成铜排的移动路径;两挡板9011通过距离调节结构901相对移动;分拣机构91在铜排的移动路径两侧往复移动。铜排向着下料方向移动经过移动路径定位机构90的两挡板9011之间设定的位置以及定位方向,依次排序移动至分拣机构91内,分拣机构91垂直于铜排移动路径往复移动,将已在分拣机构91内的铜排进行推动至合格或者不合格放置区,其中避免人员对切割后还是具有较高温度的铜排直接接触,提高分拣效率。
35.进一步的,如图8所示,在相对挤压成型组件4有一将成型铜排待夹持的液压拉拔组件7;液压拉拔组件7包括两夹板71,通过两夹板71将已整形后的铜排进行夹持,且沿着机架1水平方向移动形成拉拔,在相对两夹板的四周各设有一滑轮72,滑轮72沿着机架1水平方向设置;滑轮72与机架导轨11之间相配合形成液压拉拔组件7的滑动导向并进行往复移动。铜排在挤压模具挤压整形的同时经过液压拉拔组件7的夹持拉拔,两者相互配合操作下,有助于铜排形成目标的形状和尺寸。
36.进一步的,如图8所示,在切割组件5和液压拉拔组件7之间还设置有将成型切割分段后的铜排夹持移位的自动下料组件6;自动下料组件6包括夹持机构61,夹持机构61在铜排的上端设有固定的第一夹持板611,相应的铜排下端设有相对第一夹持板611的第二夹持板612,通过气缸制动使第二夹持板612向着第一夹持板611移动时,将已存在两者之间的铜排进行夹持及固定后;夹持机构61通过链轮传动在垂直于移动路径方向进行往复移动,将已夹持的铜排移位到传动组件8;自动下料组件6具有多个,且横向一字排列于机架1和传动组件8上方。自动下料组件6排列在垂直于铜排移动路径上方,已切割成型的铜排需要多组自动下料组件6同时进行夹持和移动,再传递到下一工位,实现工位之间自动流转,有效的提高自动化生产性能。
37.进一步的,如图8所示,传动组件8安装在与机架1水平方向的一侧,还与机架1竖直方向之间设有间距,传动组件8由多个滚筒81和架子82组成,将已放置的铜排通过电机驱动滚筒81向着下料方向传送。铜排自动经过传动组件8传送至下一工位,该设置实现工位之间的自动化流转。
38.生产工作时,沿着铜排加工的上料方向,随着上料辊2滚动先经过酸洗槽进行对铜排表面酸洗处理,在酸洗铜排表面的污渍后,穿过预整形组件,通过润滑液喷淋装置3对铜排的上下两端面进行均匀的喷洒,对所得的铜排表面进行保护,使得铜排经过挤压成型组件4对铜排整形后同时在液压拉拔组件7的带动下形成目标的形状和尺寸,在拉拔到一定长度尺寸后,自动下料组件6将待切割的铜排夹持,此时切割组件5对铜排进行切割分段,液压拉拔组件7松开夹持后,自动下料组件6经过电机驱动将铜排移动至传动组件8上,松开夹持后,传动组件8上的电机驱动滚筒81向着下料方向转动到成品切割分段处进行自动切割,依次通过移动路径定位机构90设置的两竖直的挡板9011之间形成铜排的移动路径,将铜排移
动至分拣机构91内,最后垂直于移动路径的分拣机构91向着两侧来回推动合格或者不合格的铜排。
39.文中所描述的具体实施例仅仅是对本实用新型精神作举例说明。本实用新型所属技术领域的技术人员可以对所描述的具体实施例做各种各样的修改或补充或采用类似的方式替代,但并不会偏离本实用新型的精神或者超越所附权利要求书所定义的范围。