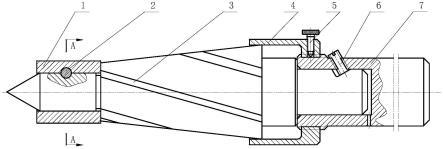
1.本实用新型属于工艺装备设计及制造技术领域,涉及一种机夹硬质合金锥度铰刀,便于提高被加工锥孔的质量,降低刀具制造成本。
背景技术:2.在机械加工领域,整体合金锥度铰刀的应用范围还是很广泛的,但是,在制造整体合金锥度铰刀的过程中,数控磨刀机开槽时,由于砂轮的直径的影响,前导部分会被砂轮磨削出和刀具齿形一样的沟槽,严重破坏前引导部分,从而对前导的引导功能造成影响,严重时起不到引导的作用,最终影响被加工产品锥孔的质量。目前,从制造整体合金锥度铰刀来讲,还无法避免。
3.另外,在使用整体合金锥度铰刀时,使用者通常只凭工作经验及技能手法控制铰刀的进给深度,有时稍有不慎,往往造成锥孔被加工大的情况,从而严重影响着产品的质量。目前,在整体合金锥度铰刀上增加限位装置的情况还不曾出现。
4.并且,由于整体硬质合金价格较贵,且由于其材料的特殊性,普通机加手段很难实现高效加工,因此制造成本也相对较高。目前有许多刀具厂家采用尾柄焊接的形式来节省成本,但由于焊接水平的不同,有些刀具在使用过程中往往会在焊口处断裂,存在一定的安全隐患。尾柄采用机械装夹形式的情况还不多见。
技术实现要素:5.为了解决上述问题,本实用新型提供了一种机夹硬质合金锥度铰刀。采用增加合金工具钢材料的导向套的结构,前引导能够保证完好的引导性能,避免了数控磨刀机开槽时前导部分会被砂轮磨削出沟槽的情况;带有可调整的限位套,从而避免因进给深度过大而造成锥孔超差的现象;采用机械装夹形式的合金工具钢材质的尾柄,不但大幅降低成本,还弥补了焊接结构的不足。
6.本实用新型的技术方案:
7.一种机夹硬质合金锥度铰刀,所述铰刀包括合金工具钢导向套1、圆柱销2、铰刀主体3、限位套4、紧定螺钉5、侧固螺钉6和合金工具钢尾柄7。
8.所述的铰刀主体3包括带顶尖的圆柱形前导部分、锥形的刃部、圆柱形的台阶外圆和圆柱形的尾部,其中刃部左端头部的外径大于前导部分,刃部尾端的外径大于台阶外圆,尾部的外径小于台阶外圆并制有一斜窝;所述的合金工具钢导向套1与铰刀主体3的前导部分的圆柱段配合方式为过盈配合,合金工具钢导向套1外径略大于刃部左端头部的外径,用于保证完好的引导性能;所述的圆柱销2压入合金工具钢导向套1和铰刀主体3配制的孔中,来固定合金工具钢导向套1和铰刀主体3,该孔的轴与合金工具钢导向套1的轴垂直;所述的合金工具钢尾柄7左端制有圆孔,其与铰刀主体3的尾部配合方式为过盈配合,合金工具钢尾柄7左端孔的孔底处有排气孔,便于合金工具钢尾柄7与铰刀主体3的装配,合金工具钢尾柄7左端外壁制有螺纹;所述的限位套4为中空阶梯轴结构,其左侧大径段内径与铰刀主体3
刃部尾端的外径配合,右侧小径段内制螺纹与合金工具钢尾柄7螺纹连接,在使用时限位套4可以通过旋转来进行轴向移动,控制铰刀主体3的进给深度;所述的紧定螺钉5安装在限位套4小径段外壁的通孔内,起固定限位套4的作用;所述的合金工具钢尾柄7侧壁制有一斜螺纹孔,侧固螺钉6拧入该斜螺纹孔,且拧紧时其端面顶在铰刀主体3尾部的斜窝处,用于紧固合金工具钢尾柄7与铰刀主体3。
9.一种机夹硬质合金锥度铰刀的制作过程如下:
10.先根据铰刀主体3的长度两端适当加长,线切整体合金棒成单件,两端磨反顶尖,然后以反顶尖为基准,在合金外圆磨床上磨铰刀主体3的台阶外圆和尾部外圆,磨削铰刀主体3的斜窝,然后线切去右端反顶尖,其余部分先不加工;车合金工具钢尾柄7外圆留精加工余量,车左端孔,制安装侧固螺钉6的螺纹孔,其余部分先不加工;调整铰刀主体3的斜窝与合金工具钢尾柄7上紧定螺钉孔的位置相对应,并将合金工具钢尾柄7左端孔与铰刀主体3尾部压合装配,拧紧侧固螺钉6;车合金工具钢尾柄7的螺纹,并制右端中心孔作为制造过程中的定位基准,卸下侧固螺钉6;然后在外圆磨床上磨削合金工具钢尾柄7外圆,再重新装上并拧紧侧固螺钉6;在合金外圆磨床上磨削铰刀主体3的前导部分达到与合金工具钢导向套1的配合要求;磨铰刀主体3的刃部锥度外圆;在数控磨刀机上装夹合金工具钢尾柄7,磨削铰刀主体3的刃部;合金工具钢导向套1压入铰刀主体3的前导部分前,在圆柱销2装配位置需要有线切割用的穿丝孔,将合金工具钢导向套1压入铰刀主体3的前导部分;在线切割机床上切圆柱销2的装配孔;压入圆柱销2,且要求紧压合;卸下侧固螺钉6,从合金工具钢尾柄7的右端装入限位套4,与合金工具钢尾柄7的螺纹部分装配;在侧固螺钉6的螺纹部分涂上防松胶,重新安装并拧紧;在限位套4外圆上的螺纹孔处,拧入紧定螺钉5,无需拧紧。
11.使用时,根据被加工产品的锥孔尺寸,旋转限位套4调整其位置,调整好后,拧紧紧定螺钉5;用手风钻装夹合金工具钢尾柄7;然后将合金工具钢导向套1穿入被加工产品的导向孔内;启动手风钻开始进给,铰刀主体3的刃部切削被加工产品的锥孔;当限位套4的左端面与被加工产品接触时,无法继续进给,加工完成,继续进行下一个锥孔的加工。
12.本实用新型的有益效果:
13.本实用新型在使用过程中,有效地保证了前引导部分的导向功能,提高了刀具使用的稳定性;且准确地控制了铰刀的进给深度,避免了因进给过大造成被加工锥孔超差的现象,保证产品质量的同时,也大幅提高加工效率。本实用新型采用机械装夹形式的合金工具钢材质的尾柄,不但大幅降低成本,还弥补了焊接结构的不足。
附图说明
14.图1为本实用新型提供的铰刀的结构示意图。
15.图2为本实用新型提供的铰刀的a-a剖视图。
16.图3为本实用新型提供的铰刀主体各部分结构说明图。
17.图中:1合金工具钢导向套;2圆柱销;3铰刀主体;4限位套;5紧定螺钉;6侧固螺钉;7合金工具钢尾柄。
具体实施方式
18.以下结合附图和技术方案,进一步说明本实用新型的具体实施方式。
19.实施例
20.如图1至图3所示,一种机夹硬质合金锥度铰刀,所述铰刀包括合金工具钢导向套1、圆柱销2、铰刀主体3、限位套4、紧定螺钉5、侧固螺钉6和合金工具钢尾柄7。
21.所述的铰刀主体3包括带顶尖的圆柱形前导部分、锥形的刃部、圆柱形的台阶外圆和圆柱形的尾部,其中刃部左端头部的外径大于前导部分,刃部尾端的外径大于台阶外圆,尾部的外径小于台阶外圆并制有一斜窝;所述的合金工具钢导向套1与铰刀主体3的前导部分的圆柱段配合方式为过盈配合,合金工具钢导向套1外径略大于刃部左端头部的外径,用于保证完好的引导性能;所述的圆柱销2压入合金工具钢导向套1和铰刀主体3配制的孔中,来固定合金工具钢导向套1和铰刀主体3,该孔的轴与合金工具钢导向套1的轴垂直;所述的合金工具钢尾柄7左端制有圆孔,其与铰刀主体3的尾部配合方式为过盈配合,合金工具钢尾柄7左端孔的孔底处有排气孔,便于合金工具钢尾柄7与铰刀主体3的装配,合金工具钢尾柄7左端外壁制有螺纹;所述的限位套4为中空阶梯轴结构,其左侧大径段内径与铰刀主体3刃部尾端的外径配合,右侧小径段内制螺纹与合金工具钢尾柄7螺纹连接,在使用时限位套4可以通过旋转来进行轴向移动,控制铰刀主体3的进给深度;所述的紧定螺钉5安装在限位套4小径段外壁的通孔内,起固定限位套4的作用;所述的合金工具钢尾柄7侧壁制有一斜螺纹孔,侧固螺钉6拧入该斜螺纹孔,且拧紧时其端面顶在铰刀主体3尾部的斜窝处,用于紧固合金工具钢尾柄7与铰刀主体3。
22.一种机夹硬质合金锥度铰刀的制作过程如下:
23.先根据铰刀主体3的长度两端适当加长,线切整体合金棒成单件,两端磨反顶尖,然后以反顶尖为基准,在合金外圆磨床上磨铰刀主体3的台阶外圆和尾部外圆,磨削铰刀主体3的斜窝,然后线切去右端反顶尖,其余部分先不加工;车合金工具钢尾柄7外圆留精加工余量,车左端孔,制安装侧固螺钉6的螺纹孔,其余部分先不加工;调整铰刀主体3的斜窝与合金工具钢尾柄7上紧定螺钉孔的位置相对应,并将合金工具钢尾柄7左端孔与铰刀主体3尾部压合装配,拧紧侧固螺钉6;车合金工具钢尾柄7的螺纹,并制右端中心孔作为制造过程中的定位基准,卸下侧固螺钉6;然后在外圆磨床上磨削合金工具钢尾柄7外圆,再重新装上并拧紧侧固螺钉6;在合金外圆磨床上磨削铰刀主体3的前导部分达到与合金工具钢导向套1的配合要求;磨铰刀主体3的刃部锥度外圆;在数控磨刀机上装夹合金工具钢尾柄7,磨削铰刀主体3的刃部;合金工具钢导向套1压入铰刀主体3的前导部分前,在圆柱销2装配位置需要有线切割用的穿丝孔,将合金工具钢导向套1压入铰刀主体3的前导部分;在线切割机床上切圆柱销2的装配孔;压入圆柱销2,且要求紧压合;卸下侧固螺钉6,从合金工具钢尾柄7的右端装入限位套4,与合金工具钢尾柄7的螺纹部分装配;在侧固螺钉6的螺纹部分涂上防松胶,重新安装并拧紧;在限位套4外圆上的螺纹孔处,拧入紧定螺钉5,无需拧紧。
24.使用时,根据被加工产品的锥孔尺寸,旋转限位套4调整其位置,调整好后,拧紧紧定螺钉5;用手风钻装夹合金工具钢尾柄7;然后将合金工具钢导向套1穿入被加工产品的导向孔内;启动手风钻开始进给,铰刀主体3的刃部切削被加工产品的锥孔;当限位套4的左端面与被加工产品接触时,无法继续进给,加工完成,继续进行下一个锥孔的加工。
25.以上所述实施例仅表达本实用新型的实施方式,但并不能因此而理解为对本实用新型专利的范围的限制,应当指出,对于本领域的技术人员来说,在不脱离本实用新型构思的前提下,还可以做出若干变形和改进,这些均属于本实用新型的保护范围。