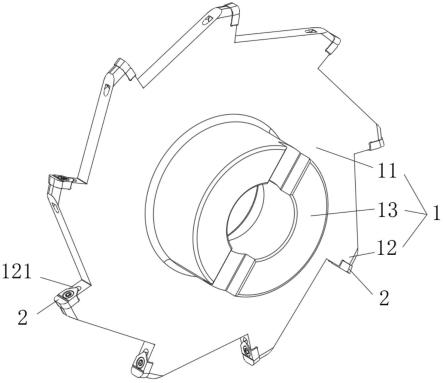
1.本实用新型涉及加工刀具的技术领域,具体是涉及一种窄槽大圆弧三面刃铣刀。
背景技术:2.人们的生产生活中所使用到的工具中很多都使用到了带窄槽的零部件,通过窄槽实现车削退刀、形成限位槽以及切断等操作,运用广泛,因此,提高窄槽的加工效率和使用性能成为了行业关注的重点。
3.目前,现有的零部件在加工窄槽时,一般通过切槽刀进行加工,导致其加工出来的窄槽的转角为直角结构,存在应力集中且易断裂的问题,另外,加工过程中通过单一的切槽刀进行加工,对该切槽刀的损耗较大,存在频繁更换刀具的问题,存在使用不便问题,加工效率低的问题,并且,现有切槽刀的刃宽较宽,加工时易造成刀刃损坏问题,同样影响刀具的使用寿命。
技术实现要素:4.针对现有技术中存在的上述问题,现旨在提供一种窄槽大圆弧三面刃铣刀,以设置带若干刀座的转盘,每一刀座上均设置有刀片,且刀片为三面刃和大圆弧转角结构,使得能通过多个刀片同时加工窄槽,减少了单一刀片的加工量,降低了单一刀片的损耗,避免了频繁更换刀片的问题,使用更方便,提高了加工效率,另外,加工得到的窄槽的转角的大圆弧结构,避免了应力集中以及易断裂的问题,保证了产品的使用性能,并且,刀片三面刃之间为大圆弧连接,使得刃宽较窄,从而避免了刃宽导致的刀刃易损坏问题,进一步延长了刀具的使用寿命。
5.具体技术方案如下:
6.一种窄槽大圆弧三面刃铣刀,具有这样的特征,包括:
7.转盘,转盘包括盘体和若干刀座,盘体为圆片结构,盘体的外侧边沿上以盘体的圆心为中心呈环形阵列分布有若干刀座,每一刀座上均具有刀片安装位,并且沿盘体的一周向方向上,每一刀座上的刀片安装位均朝向同一方向布置;
8.刀片,刀片设置于每一刀片安装位上,每一刀片的一端均具有三个刀刃面,三个刀刃面呈“[”字形分布,且相邻两刀刃面之间设置有圆弧角,且圆弧角直径与长度最短的一刀刃面的长度的比例为0.3-0.8。
[0009]
上述的一种窄槽大圆弧三面刃铣刀,其中,盘体的一侧且位于其圆心处设置有轴套,轴套与盘体同轴布置,且盘体、轴套以及刀座为一体式成型结构。
[0010]
上述的一种窄槽大圆弧三面刃铣刀,其中,每一刀座均呈三角形布置,刀座的一条边与盘体的盘沿固定连接,刀座的另一条边与盘体的径向呈倾斜布置,且倾斜方向为刀片安装位所朝向的方向,刀座的最后一条边沿盘体的切线方向布置。
[0011]
上述的一种窄槽大圆弧三面刃铣刀,其中,每一刀座上且位于其与盘体的径向呈倾斜布置的一条边所对应的面上设置有下沉槽,且下沉槽位于靠近沿盘体的切线方向布置
的一条边的一侧。
[0012]
上述的一种窄槽大圆弧三面刃铣刀,其中,刀座上且位于下沉槽的槽底开设有锁紧孔,锁紧孔贯穿至沿盘体的切线方向布置的一条边所对应的面,下沉槽和锁紧孔形成刀片安装位。
[0013]
上述的一种窄槽大圆弧三面刃铣刀,其中,下沉槽靠近盘体的一侧的槽壁为定位面,刀片背离其设置有刀刃面的一端抵靠于定位面上,且定位面呈“v”字形布置,下沉槽的定位面处且位于下沉槽的槽壁和槽底以及相邻槽壁之间的转角处均设置有过渡槽,且过渡槽均为圆弧形槽。
[0014]
上述的一种窄槽大圆弧三面刃铣刀,其中,刀片包括刃口部和固定部,刃口部和固定部为一体成型结构,三个刀刃面设置于刃口部上,并且,刃口部和固定部之间设置有内凹的弧形过渡面,并且刃口部连接弧形过渡面的一面倾斜向上翘起,形成三个刀刃面中处于中间位置的刀刃面,固定部上开设有一固定孔,且固定孔与锁紧孔通过锁紧螺丝连接。
[0015]
上述的一种窄槽大圆弧三面刃铣刀,其中,刃口部的下端面小于其上端面的面积,且其下端面朝向固定部一侧偏移。
[0016]
上述的一种窄槽大圆弧三面刃铣刀,其中,固定部背离刃口部的一侧呈与定位面配合的尖角突出布置,并且,固定部的尖角的最顶端设置有弧形的过渡角。
[0017]
上述的一种窄槽大圆弧三面刃铣刀,其中,轴套的中心孔为台阶孔,同时,轴套的一端的壁体上设置有限位缺口。
[0018]
上述技术方案的积极效果是:
[0019]
上述的窄槽大圆弧三面刃铣刀,通过设置带若干刀座的转盘,并且每一刀座上均设置有刀片,且刀片为三面刃结构,相邻两刀刃面之间设置有圆弧角,且圆弧角直径与长度最短的一刀刃面的长度的比例为0.3-0.8,使得相邻两刀刃面之间形成大圆弧转角,从而使得窄槽的加工是通过多个刀片同时进行,有效减少了单一刀片的加工量,降低了单一刀片的损耗,避免了频繁更换刀片的问题,使用更方便,提高了加工效率,并且能加工得到转角为的大圆弧结构的窄槽,有效避免了加工得到的产品应力集中以及易断裂的问题,保证了产品的使用性能,并且,刀片的三刀刃面之间通过大圆弧转角连接,可使得每一刃宽均较窄,从而避免了刃宽太宽导致的刀刃易损坏问题,进一步延长了刀具的使用寿命。
附图说明
[0020]
图1为本实用新型的一种窄槽大圆弧三面刃铣刀的实施例的结构图;
[0021]
图2为本实用新型一较佳实施例的转盘的一视角的结构图;
[0022]
图3为本实用新型一较佳实施例的转盘的另一视角的结构图;
[0023]
图4为本实用新型一较佳实施例的刀片的一视角的结构图;
[0024]
图5为本实用新型一较佳实施例的刀片的另一视角的结构图;
[0025]
图6为本实用新型一较佳实施例的刀片的又一视角的结构图。
[0026]
附图中:1、转盘;11、盘体;12、刀座;13、轴套;121、刀片安装位;131、限位缺口;1211、下沉槽;1212、锁紧孔;1213、定位面;1214、过渡槽;2、刀片;21、刃口部;22、固定部;23、弧形过渡面;211、刀刃面;212、圆弧角;221、固定孔;222、过渡角。
具体实施方式
[0027]
为了使本实用新型实现的技术手段、创作特征、达成目的与功效易于明白了解,以下实施例结合附图1至附图6对本实用新型提供的技术方案作具体阐述,但以下内容不作为本实用新型的限定。
[0028]
图1为本实用新型的一种窄槽大圆弧三面刃铣刀的实施例的结构图。如图1所示,本实施例提供的窄槽大圆弧三面刃铣刀包括:转盘1和若干刀片2。
[0029]
图2为本实用新型一较佳实施例的转盘的一视角的结构图;图3为本实用新型一较佳实施例的转盘的另一视角的结构图。如图1、图2以及图3所示,转盘1又包括盘体11和若干刀座12,此时,盘体11为圆片结构,使得盘体11的厚度较薄,从而适应窄槽的加工需求。同时,于盘体11的外侧边沿上以盘体11的圆心为中心呈环形阵列分布有若干刀座12,实现了若干刀座12在盘体11上的均匀分布,使得后续盘体11转动时能带动刀座12转动,从而使得工件上窄槽的加工是通过多个刀座12上的刀片2同时进行加工,有效减少了单一刀片2的加工量,降低了单一刀片2的损耗,避免了频繁更换刀片2的问题,使用更方便,提高了加工效率。并且,每一刀座12上均具有刀片安装位121,并且沿盘体11的一周向方向上,每一刀座12上的刀片安装位121均朝向同一方向布置,使得在盘体11沿其周向的一方向转动时,每一刀座12上的刀片安装位121均处于转动方向的前方,从而为后续刀片安装位121上的刀片2能对工件进行切削提供了条件。
[0030]
图4为本实用新型一较佳实施例的刀片的一视角的结构图;图5为本实用新型一较佳实施例的刀片的另一视角的结构图;图6为本实用新型一较佳实施例的刀片的又一视角的结构图。如图1、图4、图5以及图6所示,每一刀片安装位121上均设置有一刀片2,使得刀片2能跟随盘体11的转动而实现对工件的切削,实现对工件上窄槽的加工。并且,每一刀片2的一端均具有三个刀刃面211,三个刀刃面211呈“[”字形分布,使得三个刀刃面211能一一对应窄槽的槽底和两槽侧壁,实现对窄槽的一次性加工,保证了加工精度。并且,相邻两刀刃面211之间设置有圆弧角212,即相邻两刀刃面211之间的转角为圆弧角212,实现两者之间的圆滑过渡,并且,圆弧角212直径与长度最短的一刀刃面211的长度的比例为0.3-0.8,优选的,两者的比例为0.6或0.7,即在保留刀刃面211的情况下能增大相邻两刀刃面211之间的转角直径,形成大圆弧结构,既能使得加工得到的窄槽的转角为大圆弧结构,避免了加工得到的产品应力集中以及易断裂的问题,保证了产品的使用性能,并且,刀片2的三刀刃面211之间通过大圆弧结构连接,可使得每一刃宽均较窄,从而避免了刃宽太宽导致的刀刃易损坏问题,有效延长了刀具的使用寿命。
[0031]
更加具体的,转盘1的盘体11的一侧且位于其圆心处设置有轴套13,轴套13与盘体11同轴布置,此时,由于转盘1的厚度较薄,与转轴连接时其稳定性和可靠性均较低,通过在转盘1的圆心处同轴设置有轴套13,有效增大了后续与转轴的接触面积,提高了连接稳定性和可靠性。并且,盘体11、轴套13以及刀座12为一体式成型结构,使得转盘1的结构强度更高,承载能力更强,提高了加工时的安全性,结构设计更合理。
[0032]
更加具体的,每一刀座12均呈三角形布置,提高了刀座12本身结构的稳定性。此时,刀座12的一条边与盘体11的盘沿固定连接,刀座12的另一条边与盘体11的径向呈倾斜布置,并且,倾斜方向为刀片安装位121所朝向的方向,使得刀座12具有一条朝向盘体11的转动方向的前方倾斜的部位,为后续安装刀片2并且提高刀片2的支撑强度提供了条件,防
止了受力后发生形变的问题。另外,刀座12的最后一条边沿盘体11的切线方向布置,使得刀座12突出于盘体11外的一侧也能平滑过渡连接至盘体11的边沿上,避免了部位不平整导致的碰撞问题。
[0033]
更加具体的,每一刀座12上且位于其与盘体11的径向呈倾斜布置的一条边所对应的面上设置有下沉槽1211,即下沉槽1211位于盘体11转动方向的前方的一个面上,使得后续加工时,下沉槽1211能第一时间接触待加工的工件,并且,下沉槽1211位于靠近沿盘体11的切线方向布置的一条边的一侧,使得下沉槽1211处于刀座12的最外侧,进一步使得加工时下沉槽1211能第一时间接触待加工的工件,防止了盘体11等结构碰撞待加工的工件的问题。
[0034]
更加具体的,刀座12上且位于下沉槽1211的槽底开设有锁紧孔1212,通过锁紧孔1212为后续刀片2的安装提供了锁紧基础。同时,锁紧孔1212贯穿至沿盘体11的切线方向布置的一条边所对应的面,贯穿的锁紧孔1212相较于盲孔而言,加工更方便。并且,下沉槽1211和锁紧孔1212形成刀片安装位121,即通过下沉槽1211和锁紧孔1212实现了刀片2在刀座12上的安装。
[0035]
更加具体的,下沉槽1211靠近盘体11的一侧的槽壁为定位面1213,此时,刀片2背离其设置有刀刃面211的一端抵靠于定位面1213上,即通过定位面1213为刀片2在刀片安装位121上的安装提供了定位,保证了刀片2安装的稳定性和可靠性。另外,定位面1213呈“v”字形布置,可使得定位面1213形成夹角结构,实现多方位定位,进一步提高了定位效果。另外,下沉槽1211的定位面1213处且位于下沉槽1211的槽壁和槽底以及相邻槽壁之间的转角处均设置有过渡槽1214,且过渡槽1214均为圆弧形槽,可避免转角处为直角结构而无法加工清角的问题,并且,圆弧形槽的过渡槽1214可通过钻孔加工得到,加工更方便,结构设计更合理。
[0036]
更加具体的,刀片2又包括刃口部21和固定部22,此时,刃口部21和固定部22为一体成型结构,整体性更好,结构强度更高,且易于加工。另外,三个刀刃面211设置于刃口部21上,并且,刃口部21和固定部22之间设置有内凹的弧形过渡面23,实现了刃口部21和固定部22之间的圆滑过渡且也使得刃口部21的起始位置较低,为后续刃口部21上的刀刃面211倾斜翘起提供了条件。并且刃口部21连接弧形过渡面23的一面倾斜向上翘起,形成三个刀刃面211中处于中间位置的刀刃面211的刃口,使得刀片2的进刀方向为倾斜方向,方便了进刀,同时也改变了刀片2的刃口部21的受力方向,使用性能更好。另外,固定部22上开设有一固定孔221,且固定孔221与锁紧孔1212通过锁紧螺丝连接,即通过固定部22上的固定孔221实现了在下沉槽1211中的安装,安装更方便。
[0037]
更加具体的,刀片2的刃口部21的下端面小于其上端面的面积,此时,刃口部21的下端面朝向固定部22一侧偏移,从而使得刃口部21的三刀刃面211处的上端面和下端面出现错位而形成倾斜结构,既能保证切削角,又能防止刀片2除刃口外的其他地方接触待加工的工件,结构设计更合理。
[0038]
更加具体的,固定部22背离刃口部21的一侧呈与定位面1213配合的尖角突出布置,使得刀片2在安装于刀片安装位121中时,尖角能正好卡入至呈“v”字形布置的定位面1213中,满足多方位定位的需求。并且,固定部22的尖角的最顶端设置有弧形的过渡角222,不仅方便了加工,还使得刀片2上除了刀刃面211的刃口外的其他棱边能较为圆滑,安全性
更高。
[0039]
更加具体的,轴套13的中心孔为台阶孔,能通过台阶孔安装于驱动用的转轴上,实现定位,保证安装的稳定性。同时,轴套13的一端的壁体上设置有限位缺口131,限位缺口131内能安装与驱动用的转轴配合的限位销等结构,保证了轴套13和驱动用的转轴连接的可靠性,安全保障性更高。
[0040]
作为优选的实施方式,刀片2的材质为钛合金材质,硬度高,耐磨性好,使用寿命更长。
[0041]
本实施例提供的窄槽大圆弧三面刃铣刀,包括转盘1和刀片2;通过设置带有若干刀座12的转盘1,并于每一刀座12上均设置有刀片2,通过多个刀片2来同时加工窄槽,有效减少了单一刀片2的加工量,降低了单一刀片2的损耗,避免了频繁更换刀片2的问题,使用更方便,提高了加工效率,并且,每一刀片2均具有三个刀刃面211,且相邻两刀刃面211之间通过圆弧角212过渡,且圆弧角212直径与长度最短的一刀刃面211的长度的比例为0.3-0.8,使得相邻两刀刃面211之间形成大圆弧转角,不仅使得加工得到的窄槽的转角为大圆弧结构,避免了应力集中以及易断裂的问题,还能使得每一刀刃面211的刃宽较窄,有效避免了刃宽较宽导致的刀刃易损问题,延长了刀具的使用寿命。
[0042]
以上仅为本实用新型较佳的实施例,并非因此限制本实用新型的实施方式及保护范围,对于本领域技术人员而言,应当能够意识到凡运用本实用新型说明书及图示内容所作出的等同替换和显而易见的变化所得到的方案,均应当包含在本实用新型的保护范围内。