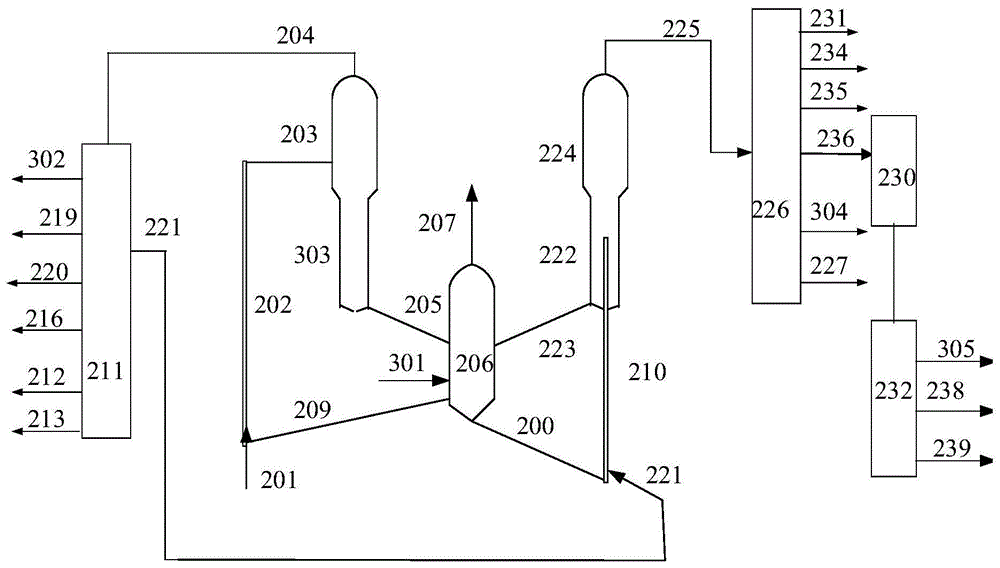
本发明涉及一种石油原料生产化工原料的方法和装置,更具体地说,涉及一种重质油生产乙烯、丙烯和芳烃的方法和装置。技术背景乙烯,丙烯和btx芳烃做为大宗基础化工原料,需求一直在每年增长。催化裂化作为加工重油生产汽油的装置也副产大量的丙烯,是丙烯市场的主要补充来源。其中使用较多择型分子筛(zsm-5)作为活性中心的深度催化裂化(如dcc工艺)可以大量生产丙烯并副产一定的丙烯和btx芳烃。目前该类工艺一般采用蜡油或加氢蜡油,并掺入少量渣油,或石蜡基常压渣油作为原料。富含烯烃的液化气制丙烯技术是以附加值较低的液化气为原料,在催化剂的作用下液化气中的碳四烯烃裂解反应生成高附加值的丙烯、乙烯和高辛烷值的富芳烃汽油组分,如在dcc家族技术中就有将c4烯烃返回催化裂解装置循环再裂解生成乙烯、丙烯。同时到2020年,全国范围内将推广乙醇汽油,至此醚化c4或醚化轻汽油产品将限制加入成品汽油中,大量c4醚化装置会闲置,c4烯烃的再加工利用又受到关注。cn1034586a公开了一种催化裂化生产低碳烯烃的方法,采用汽油、煤油、柴油、减压蜡油、渣油及混合物为原料,该方法使用y型分子筛和含磷zsm-5分子筛作为活性中心;采用流化床或提升管反应器;操作条件为压力120kpa~400kpa,反应温度480-680℃,停留时间0.1-6秒,剂油比4-20,雾化水蒸汽占原料重量1%~50%。该方法尽管对催化剂进行改性,与cn104878存在相似问题,即反应温度高,甲烷副产品较多,且产生大量无法使用的碳四和柴油。cn1056595a公开了一种采用多段进料低生产碳烯烃的方法。该方法采用从乙烷到渣油为原料,使用含碱土金属型分子筛作为活性中心;采用提升管反应器;操作条件为压力130kpa~400kpa,反应温度600-900℃,停留时间0.1-6秒以及剂油比5-100,按照不同裂解难度从高到低多段进料裂化。该方法尽管解决了碳四等副产品问题,但对于加工性质差的原料,也存在甲烷和焦炭副产品较多的问题,cn1065963a公开了一种多段进料生产低碳烯烃的方法,该方法以汽油、减压蜡油、渣油为原料,使用y型分子筛和zsm-5分子筛作为活性中心;采用提升管反应器+流化床反应器;操作条件为压力130kpa~400kpa,反应温度500-600℃,提升管停留时间1-5秒,流化床空速0.2-20hr-1以及剂油比6-15,雾化水蒸汽占原料重量1%~60%,其中减压蜡油和渣油的混合物进入提升管反应器底部,汽油组分进入流化床反应器,提升管反应器和流化床反应器串联。该方法无法解决甲烷,碳四和柴油副产品较多的问题。cn102337148a公开了一种富含碳四到碳八汽油为原料生产低碳烯烃的方法。该方法使用该方法使用y型分子筛和zsm-5分子筛作为活性中心;采用提升管反应器+流化床反应器;操作条件为压力150kpa~300kpa,反应温度480-680℃,提升管停留时间1-5秒,流化床空速0.2-30hr-1以及剂油比8-40。该方法尽管进行了碳四到碳八烯烃循环利用,无法解决烷烃组分的积累。cn101362961a公开了一种以馏分160℃-270℃烃类为原料生产低碳烯烃和芳烃的方法,该方法使用该方法使用y型分子筛和zsm-5分子筛作为活性中心;采用提升管反应器或流化床反应器;操作条件为压力100kpa~1000kpa,反应温度450-750℃,空速1-150hr-1以及剂油比1-150。该方法解决了部分柴油的出路。cn101747928a公开了一种以减压蜡油、渣油为原料生产低碳烯烃和芳烃的方法。该方法使用该方法使用y型分子筛和zsm-5分子筛作为活性中心;采用提升管反应器或流化床反应器;原料反应器和将c4烯烃-250℃产物循环反应器共用一个再生器。该方法随人解决了部分柴油的出路,但无法解决了烷烃组分和多环芳烃组分的积累问题。cn1667089a公开了一种生产低碳烯烃的方法,该方法以汽油、煤油、柴油、减压蜡油、渣油及混合物为原料,先对原料和循环物流进行加氢处理,再将这些物流进入催化裂解反应器。其中气体循环物为乙烷,丙烷和碳四。液体循环进料物为c5~c6,重汽油芳烃抽余油,lco,hco和油浆。该方法虽然解决了大部分副产品的出路,但无法解决烷烃组分和多环芳烃组分的积累问题。cn101747928a公开了一种生产低碳烯烃和芳烃的方法,该方法以减压蜡油、渣油为原料,将催化裂解和蒸汽裂解结合。该方法将催化裂解的产物经分离后c2到汽油的烷烃进入蒸汽裂解反应器,将丁烯,回炼油和油浆返回催化裂解反应器。通过芳烃抽提工艺生产芳烃。该方法虽然解决了解决了烷烃组分和多环芳烃组分的积累问题。但分离c4以上各组分的烯烃和烷烃,能耗很高,得不偿失。由于碳四烷烃反应速度明显慢于碳四烯烃的反应速度,造成在提升管反应器中混合碳四反应过程中碳四烯烃转化率较高,而碳四烷烃转化率极低。现有技术的碳四组分循环反应过程中,碳四组分中不仅保留了未反应碳四烷烃同时原料油产生的烷烃也不断在循环物流中累积。造成的问题是如果不提高碳四循环比例,则由于碳四中烯烃含量减少而降低丙烯产率。如提高碳四循环比例,则大幅增加能耗。技术实现要素:本发明要解决的技术问题之一是解决现有技术中烃油制备低碳烯烃过程中的烷烃组分积累的问题,提出一种降低烷烃组分积累,高产品收率的重质油生产乙烯、丙烯和芳烃的方法。本发明要解决的技术问题之二是提供一种重质油生产乙烯、丙烯和芳烃的催化转化装置。本发明提供的一种重质油生产丙烯、乙烯和芳烃的方法,包括:(1)重质油原料进入第一反应器,与再生器来的第一股催化剂在接触反应,反应得到的油气和催化剂混合物经气固分离,分离出的待生催化剂去再生器烧焦再生并升温;分离出的反应油气经第一分离系统分离出干气、液化气、汽油、柴油和油浆,进一步分离出乙烯、丙烯、芳烃和第一碳四组分;(2)第一碳四组分单独或与外来的碳四组分引入第二反应器,与再生器来的第二股再生催化剂接触反应,反应得到的油气和催化剂混合物经气固分离,分离出的待生催化剂去再生器烧焦炭再生并升温;分离出的油气经第二分离系统分离出干气、液化气、汽油和柴油,进一步分离出乙烯、丙烯和第二碳四组分;(3)第二碳四组分进入芳构化反应器,与芳构化催化剂接触反应,反应产物经第三分离系统分离出干气、液化气和富含芳烃的汽油,进一步分离出乙烯、丙烯和芳烃产品。本发明提供的重质油生产丙烯、乙烯和芳烃的催化转化装置,用于上述的重质油生产丙烯、乙烯和芳烃的方法,包括:(1)依次连通的第一反应器、气固分离设备和第一分离系统;(2)依次连通的第二反应器、气固分离设备和第二油气分离系统;(3)依次连通的芳构化反应器及第三分离系统;(4)再生器,所述的再生器的再生催化剂斜管分别与第一反应器和第二反应器底部连通,所述的再生器的待生催化剂斜管与所述的气固分离设备的固体颗粒出口连通;其中,所述的第一分离系统的c4出口与第二反应器原料进口连通,所述的第二油气分离系统的c4出口与芳构化反应器连通。本发明提供的重质油生产丙烯、乙烯和芳烃的方法和催化转化装置的有益效果:本发明提供的方法以重质油为原料生产丙烯,乙烯和芳烃,可以最大量生产乙烯,丙烯和芳烃。本方法解决了碳四循环烷烃累积的问题,除了大幅度增加乙烯,丙烯和芳烃产率,同时也大幅降低了碳四循环的能耗和操作费用;本方法降低催化裂化装置的满足热平衡所需的焦炭产率;还可以降低芳构化装置的取热负荷,降低芳构化装置的能耗。附图说明图1为本发明提供的重质油生产丙烯、乙烯和芳烃的方法的流程示意图。图2为本发明提供的重质油生产丙烯、乙烯和芳烃的方法油气分离过程的流程示意图。图3为对比例1、2中重质油生产乙烯、丙烯的方法的流程示意图。其中:202-第一反应器;203、224-沉降器;303、222-汽提器;206-再生器;211-第一分离系统;226-第二分离系统;230-芳构化反应器;232-第三分离系统,其他为管线。具体实施方式以下具体说明本发明的具体实施方式:一种重质油生产丙烯、乙烯和芳烃的方法,包括:(1)重质油原料进入第一反应器,与再生器来的第一股催化剂接触反应,反应得到的油气和催化剂混合物经气固分离,分离出的待生催化剂去再生器烧焦再生并升温;分离出的反应油气经第一分离系统分离出干气、液化气、汽油、柴油和油浆,进一步分离出乙烯、丙烯、芳烃和第一碳四组分;(2)第一碳四组分单独或与外来的碳四组分一起引入第二反应器,与再生器来的第二股再生催化剂接触反应,反应得到的油气和催化剂混合物经气固分离,分离出的待生催化剂去再生器烧焦炭再生并升温;分离出的油气经第二分离系统分离出干气、液化气、汽油和柴油,进一步分离出乙烯、丙烯和第二碳四组分;(3)第二碳四组分进入芳构化反应器,与芳构化催化剂接触反应,反应产物经第三分离系统分离出干气、液化气和富含芳烃的汽油,进一步分离出乙烯、丙烯和芳烃产品。本发明提供的方法中,所述的催化裂化原料为选自蜡油、常压渣油、减压渣油、焦化蜡油、脱沥青油、糠醛精制抽余油、煤液化油、油砂油、页岩油、经过f-t合成得到的馏分油和动植物油中一种或几种的混合物。也可以是其它碳数大于16的有机化合物或烃类。所述的催化剂为催化裂化催化剂,含有mfi结构分子筛、y型分子筛、粘土和粘结剂,以所述催化剂的总重量计,mfi结构分子筛的含量为105~60重量%,优选为3010~50重量%,y型分子筛的含量为1~40重量%,优选为1~230重量%,粘土的含量为10~70重量%,优选为15~45重量%,粘结剂的含量为105~40重量%,优选为205~35重量%。所述的第一反应器为提升管反应器、湍流床反应器和快速床反应器中的一种或以上几种组合的反应器。第一反应器的操作条件为:平均温度为500℃~700℃,反应压力0.15mpa~0.5mpa,反应空速为2~600h-1。所述的第一反应器中的催化剂和油气分离采用本领域均知的旋风气固分离器,沉降器等。所述的再生器为本领域的各种形式的再生器,其使用空气或空气混合富氧气体与待生催化剂上的焦炭反应,烧掉待生催化剂上的焦炭以恢复待生催化剂的活性(称为再生催化剂),并且将催化剂温度升高到600℃到760℃,以便返回反应器为反应带来热量和催化介质。所述的第一分离系统,可以采用分馏塔,精馏塔,吸收塔,解吸塔中的一种或多种组合。所述的第二反应器为提升管反应器、湍流床反应器和快速床反应器中的一种或以上几种组合的反应器。第二反应器的操作条件为:平均温度为550℃~700℃,反应压力0.15mpa~0.5mpa,反应空速为2~600h-1。所述的第二反应器催化剂和油气分离采用本领域均知的旋风气固分离器,沉降器等,分离出的吸附有油气的待生催化剂经汽提器汽提。所述的第一碳四组分含有c4烯烃和c4烷烃,其烯烃含量大于20wt%;所述的第二碳四组分含有c4烯烃和c4烷烃,其烯烃含量大于40wt%;优选地,所述的外来的碳四组分中的烯烃含量大于20wt%。本发明提供的重质烃油多产低碳烯烃的方法中,所述的第一反应器和所述的第二反应器单独设置沉降器和汽提器,并且单独设置分离系统。所述的第二分离系统,可以采用分馏塔,精馏塔,吸收塔,解吸塔中的一种或多种组合。所述的芳构化反应器,第二碳四组分在芳构化反应器中进行芳构化反应,生成干气、液化气和富含芳烃的汽油馏分,其中,所述的芳烃为c6到c10单环芳烃。所述的芳构化反应器的操作条件为:反应温度为350~450℃,反应压力为0.20mpa~2.0mpa,反应空速为0.2~2h-1。所述的芳构化反应器采用芳构化催化剂,含有分子筛、金属活性组分和耐热无机氧化物载体,所述的金属活性组分选自稀土元素、vib、viii、iib、viib族元素的一种或几种,所述的耐热无机氧化物优选氧化硅和氧化铝。所述的第三分离系统,可以采用分馏塔,精馏塔,吸收塔,解吸塔中的一种或多种组合。下面结合附图对本方法进行说明,但并不因此而限制本发明。附图1为重质油生产丙烯、乙烯和芳烃的方法的流程示意图。如附图1所示,重质油原料经预热后经管线201进入第一反应器202与经管线209来自再生器206的热再生催化催化剂接触反应,所述的第一反应器为提升管反应器。反应油气和催化剂混合物进入沉降器203,沉降器203内设置有气固分离设备,在沉降器203内油气和催化剂分离,分离后带炭的催化剂经汽提段303由经管线205进入再生器206烧焦再生。在再生器206内经管线301来的空气烧掉催化剂上焦炭以恢复活性,然后经管线209进入第一反应器202底部循环参与反应。分离出的油气经管线204进入第一分离系统,经第一分离系统分离得到干气302,丙烯219,丙烷220,产品汽油216,产品柴油212和油浆213。所述的第一分离系统包括分馏塔、后吸收稳定系统和气体分离装置。第一碳四组分221进入第二反应器210与经管线200来与再生器206热的再生催化催化剂接触,生成的油气和催化剂进入沉降器224,沉降器224内设置气固分离设备,在沉降器224内油气和催化剂分离,分离后带炭的催化剂经汽提段222由经管线223进入再生器206烧焦再生恢复活性,然后经管线200进入反应器210底部循环参与反应。分离出的油气经管线225进入第二分离系统,分离出干气231、丙烯234,丙烷235、第二碳四组分236、汽油304、柴油227,所述的第一分离系统包括分馏塔、后吸收稳定系统和气体分离装置。第二碳四组分236进入芳构化反应器237,与芳构化催化剂接触进行芳构化反应。其产品经分离后得到富含芳烃的汽油239,干气305和液化气238。附图2为本发明提供的重质油生产丙烯、乙烯和芳烃的方法油气分离过程的流程示意图。如附图2所示,第一反应器的沉降器中分离出的油气经管线204进入第一分离系统的分馏塔211,分馏塔211中部抽出产品柴油212,底部抽出产品油浆213,分馏塔211塔顶得到的汽油以下产物经管线214进入第一分离系统的后吸收稳定系统215,稳定系统分离出的产品汽油216,干气302和液化气217,液化气217进入气体分离装置218分离出丙烯219,丙烷220和第一碳四组分221。第二反应器的沉降器分离出的油气经管线225进入第二分离系统的分馏塔226,分馏塔226底部抽出产品柴油227,分馏塔226塔顶得到的汽油以下产物经管线229进入第二分离系统的后吸收稳定系统230,稳定系统230分离出的产品汽油304,干气231和液化气232,液化气232进入气分装置233分离出丙烯234,丙烷235和第二碳四组分236。以下通过实施例和对比例说明本发明提供的重质油生产乙烯、丙烯和芳烃的方法的效果,但并不因此而限制本发明。对比例和实施例中,使用的重质油原料a为加氢渣油,取自中国石油化工股份有限公司石家庄炼油厂;重质油原料b为直馏蜡油,取自中国石油化工股份有限公司燕山分公司。重质油原料a、b的性质见表1。使用的催化剂为中国石油化工股份有限公司催化剂分公司生产的dmmc-1催化剂。其性质见表2。对比例1-2对比例1-2采用如附图2所示的重质油催化裂化生产乙烯、丙烯的工艺方法的流程示意图,如附图2所示:重质油原料经预热后经管线101进入催化裂化提升管主反应器102与经管线109来自再生器106热的再生催化催化剂接触,生成的油气和催化剂进入沉降器103,在沉降器103内油气和催化剂分离,分离后带炭的催化剂经汽提器402汽提后由经管线105进入再生器106烧焦。在再生器106内经管线108来的空气烧掉催化剂上焦炭以恢复活性,然后经管线109进入反应器102底部循环参与反应。分离出的油气经管线104进入分馏塔111,分馏塔111中部抽出产品柴油112,底部抽出产品油浆113。分馏塔111塔顶得到的汽油以下产物经管线114进入后吸收稳定系统115,稳定系统分离出的干气401、液化气117和汽油116,液化气117进入气分装置118分离出丙烯119,丙烷120和碳四组分121。碳四组分121进入催化裂化提升管副反应器110与经管线100来与再生器106热的再生催化催化剂接触,生成的油气和催化剂进入在沉降器103,所述的催化裂化提升管副反应器110与所述的催化裂化提升管主反应器102共用同一沉降器和再生器。对比例1-2的各反应操作条件见表3,产品收率见表4。实施例1-2实施例1-2采用如附图1所示的反应流程,具体地,(1)重质油原料进入第一反应器,与再生器来的第一股催化剂接触反应,反应得到的油气和催化剂混合物经气固分离,分离出的待生催化剂去再生器烧焦再生并升温;分离出的反应油气经第一分离系统分离出干气、丙烯、丙烷、第一碳四组分、汽油、柴油和油浆;(2)第一碳四组分单独与再生器来的第二股再生催化剂接触反应,反应得到的油气和催化剂混合物经气固分离,分离出的待生催化剂去再生器烧焦炭再生并升温;分离出的油气经第二分离系统分离出干气、液化气、汽油、柴油和油浆,进一步分离出乙烯和丙烯产品和第二碳四组分;(3)第二碳四组分进入碳四芳构化反应器,与芳构化催化剂接触反应,反应产物经第三分离系统分离出干气、液化气和富含芳烃的汽油,进一步分离出乙烯、丙烯和芳烃产品。实施例1-2的各反应操作条件见表3,产品收率见表4。由表4中的结果可以看出,采用重质油原料a的情况下,与对比例1相比,本发明提供的方法实施例1的碳四进料/原料减少了0.11,乙烯产率增加了0.63个百分点,丙烯产率增加了1.38个百分点,芳烃(btx)产率增加了1.67个百分点。采用重质油原料b的情况下,与对比例2相比,本发明提供的方法实施例2的碳四进料/原料减少了0.21,乙烯产率增加了1.20个百分点,丙烯产率增加了1.72个百分点,芳烃(btx)产率增加了3.84个百分点。表1表2表3各反应器操作条件项目对比例1实施例1对比例2实施例2原料油原料a原料a原料b原料b第一反应器催化剂dmcc-1dmcc-1dmcc-1dmcc-1反应压力/mpa0.20.20.280.28反应温度/℃555555620620再生器温度/℃690690710710剂油比10101515反应空速/h-1141455雾化蒸汽/%25251515第二反应器碳四进料/原料油0.250.140.400.19反应压力mpa0.20.20.280.28反应温度/℃600600640640再生器温度/℃690690710710剂油比881212反应空速/h-1505088雾化蒸汽/%10102525芳构化反应器条件:反应温度/℃450460反应压力/mpa11.2反应空速/h-111.2表4产品收率对比例1实施例1对比例2实施例2产品收率,wt%h2-c213.6914.5216.1117.35c3-c422.9321.3139.2536.86c5+汽油29.4430.1826.8927.85柴油16.3016.328.688.72重油5.705.712.182.21焦炭11.9411.966.897.01乙烯8.008.6310.6711.87丙烯19.0520.4330.2631.98btx9.3511.027.5011.34当前第1页12