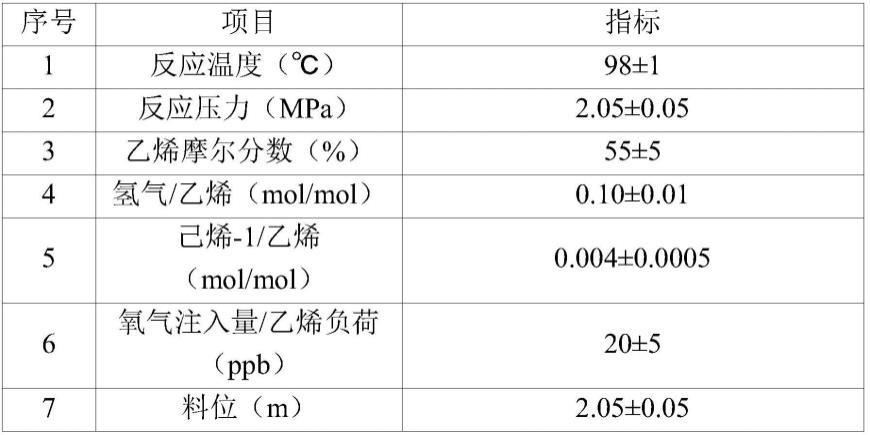
1.本发明涉及气相法流化床乙烯聚合技术领域,尤其涉及一种气相法聚乙烯铬系列不同催化剂之间的切换方法。
背景技术:2.气相聚乙烯生产技术是以流化床为中心的气固相聚合技术。在流化床反应器中,所有原料(乙烯、共聚单体、氢气等)以气体形式与处于流化床中固相状态的催化剂相接触,在催化剂表面形成聚乙烯分子,终成颗粒。其反应条件温和,设备简单,三废很少,具有简单、灵活、稳定、经济、安全等特点。但也具有气相法的种种缺陷,如产品切换易产生大量过渡料,生产效率低等。
3.zl200780011189.2提供了在聚合过程中在各聚合物等级之间进行切换的方法,该聚合过程包括在彼此串联连接的至少第一反应器和第二反应器中聚合至少一种单体,其中在切换期间进入第一反应器中的单体进料保持基本上恒定。该发明权利要求中所述聚合反应器是环流反应器,不适用于气相流化床反应器聚合技术。
4.us 7,629,422 b2提供了聚合催化剂系统之间过渡的过程,包括使用ziegler-natta催化剂系统和铬基催化剂系统在烯烃聚合反应体系之间过渡的过程。所设想的实施例包括在烯烃聚合反应器中从第一催化剂过渡到第二催化剂的方法,包括:在反应器中添加从一氧化碳、二氧化碳或其组合中选择的失活剂(da);在反应器中添加辅助催化剂吸附剂(caa),包括从二氧化硅、氧化铝或其组合中选择的无机氧化物;其中,所述第一催化剂包括至少一个常规ziegler-natta催化剂和一个辅助催化剂,其中第二催化剂包括至少一个铬基催化剂,其中所述反应器为气相流化床反应器,且所述caa基本上不含过渡金属。在另一个实施例中,设想了在烯烃聚合反应器中从第一催化剂过渡到第二催化剂的方法,包括:添加过渡助剂(taa),其中从烷氧化胺、烷氧基化酰胺或其组合中选择taa,其中第一催化剂包括至少一个ziegler-natta催化剂,该催化剂包括催化剂、辅佐催化剂和选择性载体,第二催化剂包括至少一个铬基催化剂。该发明涉及气相聚乙烯工艺两个不同体系催化剂之间的切换,不适用于同系列两种催化剂之间的切换。
5.zl201210402797.9提供了一种气相法聚乙烯钛系与铬系催化剂切换工艺。该工艺先利用终止剂co2终止聚乙烯钛系催化剂的反应,再进行氮气置换,氮气置换完成时,向反应器中注入钛系催化剂及其助催化剂的消除剂h2o进行反应,最后调整反应器组分后,投入铬系催化剂建立反应,整个催化剂切换过程不用更换种子床。该工艺操作简单、易于实施,不仅减少了停车时间,而且增加了产量。同样,该发明涉及气相聚乙烯工艺两个不同体系催化剂之间的切换,不适用于同系列两种催化剂之间的切换。
技术实现要素:6.针对现有技术中的上述缺陷,本发明的目的在于提供一种高效、平稳的气相法聚乙烯铬系列不同催化剂之间的切换方法,该方法不仅工艺操作易于实施,而且切换用时短、
切换过程平稳、细粉含量少,同时减少因关键设备堵塞造成的装置停车次数,节省了大量的能耗、物耗。
7.为此,本发明提供一种气相法聚乙烯铬系列不同催化剂之间的切换方法,包括以下步骤:
8.(1)停止第一种铬系催化剂进料,同时停止氧气注入;
9.(2)按照排料间隔设定排料程序,将气相反应器的床层料位降低至不低于聚合反应工况条件下可操作的床层最低流化高度;
10.(3)按照第二种铬系催化剂的工艺控制条件调整气相反应器的工艺条件,第二种铬系催化剂与第一种铬系催化剂不同;
11.(4)开始按照≤正常消耗量的1/2加入第二种铬系催化剂,当建立反应后,开始注入氧气,氧气注入量根据乙烯负荷进行调整,然后逐渐增加第二种铬系催化剂进料量和氧气注入量,直至控制乙烯负荷达100%;
12.(5)在切换过程中,观察气相反应器表征流化状态的工艺参数,及时调整与流化状态相关的工艺条件;
13.(6)根据第二种铬系催化剂的工艺控制条件和聚合产品指标对氢气/乙烯摩尔比值、共聚单体/乙烯摩尔比值、氧气注入量进行微调;当聚合产品指标进行检测合格后,切换过程平稳结束。
14.本发明所述的气相法聚乙烯铬系列不同催化剂之间的切换方法,步骤(3)中,优选的是,所述工艺条件包括反应温度、反应压力、乙烯摩尔分数、氢气/乙烯摩尔比值、共聚单体/乙烯摩尔比值。
15.本发明所述的气相法聚乙烯铬系列不同催化剂之间的切换方法,步骤(5)中,优选的是,所述表征流化状态的工艺参数包括气相反应器的压差分布、温度分布、静电变化,所述与流化状态相关的工艺条件包括流化气速、停留时间、催化剂进料量、乙烯负荷。
16.本发明所述的气相法聚乙烯铬系列不同催化剂之间的切换方法,步骤(1)中,优选的是,所述第一种铬系催化剂是有机铬催化剂或无机铬催化剂,所述第一种铬系催化剂的聚合反应工艺条件为:反应温度60~140℃,反应压力0.7~3.0mpa,乙烯摩尔分数10~80%,氢气/乙烯摩尔比值≤0.8,共聚单体α-烯烃,共聚单体/乙烯摩尔比值≤0.5。
17.其中,对于铬系列催化剂,温度用于调节聚合产品的熔融指数,随温度升高,熔融指数增大;共聚单体用于调节聚合产品的密度,随共聚单体含量增加,密度降低。
18.本发明所述的气相法聚乙烯铬系列不同催化剂之间的切换方法,步骤(2)中,优选的是,所述排料间隔为30s/次、60s/次、100s/次、300s/次或1000s/次,所述床层料位的水平高度降低至聚合反应工况条件下正常床层料位的水平高度的70%~100%,进一步优选的,聚合反应工况条件下正常床层料位的水平高度为流化床反应器直筒段高度的1~1.3倍。若床层料位降至低于聚合反应工况条件下可操作的床层最低流化高度,会造成流化状态的紊乱,影响装置持续运转。
19.本发明所述的气相法聚乙烯铬系列不同催化剂之间的切换方法,步骤(3)中,优选的是,所述第二种铬系催化剂是有机铬催化剂或无机铬催化剂,所述第二种铬系催化剂的聚合反应工艺条件为:反应温度60~140℃,反应压力0.7~3.0mpa,乙烯摩尔分数10~80%,氢气/乙烯摩尔比值≤0.8,共聚单体α-烯烃,共聚单体/乙烯摩尔比值≤0.5。
20.本发明所述的气相法聚乙烯铬系列不同催化剂之间的切换方法,其中优选的是,所述有机铬催化剂为负载型催化剂,由硅胶负载有机硅烷铬酸酯形成;所述无机铬催化剂由载体、活性组分和助催化剂组成,所述载体为无机氧化物,所述活性组分为氧化铬,所述助催化剂为烷基铝或有机硼。
21.本发明所述的气相法聚乙烯铬系列不同催化剂之间的切换方法,其中优选的是,所述有机硅烷铬酸酯为双三苯基硅烷铬酸酯。
22.本发明所述的气相法聚乙烯铬系列不同催化剂之间的切换方法,其中优选的是,所述α-烯烃包括丁烯-1、己烯-1中的至少一种。
23.本发明所述的气相法聚乙烯铬系列不同催化剂之间的切换方法,步骤(4)中,优选的是,所述第二种铬系催化剂开始时的加入量为正常消耗量的1/3~1/2。切换过程中,第一种铬系催化剂的残留反应依然存在,一方面可以加快第二种铬系催化剂的引发时间,但更重要的另一方面是对第二种铬系催化剂建立平衡反应形成干扰,所以第二种铬系催化剂在开始加入时,最优加入量应为正常消耗量的1/3~1/2,然后在逐渐增加催化剂加入量至正常消耗量,否则可能会导致细粉含量的增加,结块的产生,甚至停车。
24.本发明所述的气相法聚乙烯铬系列不同催化剂之间的切换方法,步骤(5)中,优选的是,所述流化气速的调整范围为0.5~0.7m/s,所述停留时间的调整范围在1~5h。流化气速和停留时间是气相反应器流化状态平稳控制的重要参数;及时调整流化气速,气相流化床反应器中的聚乙烯颗粒能够进行充分的分散和合理的分布,流化床反应器中不存在死区,流化状态才能更加适合聚合反应的进行;及时调整停留时间,为了保持流化床反应器床层重量,合理控制床层置换时间。只有对流化气速和停留时间进行及时的调整,才能保证流化状态的平稳控制和切换过程的顺利进行。
25.本发明所述的气相法聚乙烯铬系列不同催化剂之间的切换方法,步骤(6)中,优选的是,所述聚合产品指标包括聚乙烯的密度、熔融指数、堆密度、粉料粒径分布中的至少一种。通过密度、熔融指数、堆密度、聚合物粉料粒径分布等产品指标的定时分析,可以对切换过程中流化状态及进度进行准确的判断,以便进行及时的调整,保证切换过程的顺利进行。
26.具体的,在聚乙烯聚合过程中,对于聚乙烯催化剂,反应温度、反应压力、反应器中乙烯摩尔分数、氢气/乙烯摩尔比值、共聚单体/乙烯摩尔比值、流化气速、床层料位、停留时间、催化剂进料量、乙烯负荷等都是该催化剂聚合生产过程中的工艺控制条件,只有控制这些工艺条件达到最佳,聚合反应状态才能保持平稳运行,而两种不同的聚乙烯催化剂在表观物性、活性、聚合工艺控制条件等各方面存在差异。
27.具体的,气相聚乙烯两种催化剂之间的工艺切换过程,是终止第一种催化剂的聚合反应平稳状态,建立第二种催化剂的聚合反应平稳状态。在切换过程中,第一种催化剂进料停止后,仍会有残留催化剂进行反应;在加入第二种催化剂后,也需要一段引发时间,才能建立反应。对于不同系列聚乙烯催化剂之间,例如钛系与铬系之间、钛系与茂金属之间等互为影响,不能共存,需要通过注入终止剂、失活剂等手段终止第一种催化剂的聚合反应,然后通过反应控制,尽快构建第二种催化剂的聚合反应平稳状态。但是,终止剂、失活剂等能立即终止第一种催化剂的聚合反应,同时也能抑制第二种催化剂进入聚合反应器后建立反应,所以在不同系列催化剂之间的切换时间长,步骤繁琐,过程复杂。对于同系列聚乙烯催化剂之间,例如同为钛系之间、同为铬系之间,能够共存,不需要彻底终止第一种催化剂
的聚合反应,即可加入第二种催化剂。
28.特别针对铬系催化剂,因为其引发时间长,所以第一种催化剂残留反应的存在,能够加快第二种催化剂建立反应的引发时间,但同时第一种催化剂残留反应的时间过长,也会对第二种催化剂建立聚合反应平衡状态形成干扰。尤其铬系催化剂在停止进料后的残留反应持续时间很长,甚至需要将当前聚合反应器中的床层进行完全置换,才能消除第一种催化剂对第二种催化剂的影响。举例来说,对于50kg/h的聚乙烯中试装置,在正常聚合反应状态下(即乙烯为满负荷),将聚合反应器中的床层完全置换,需要6-8h;若在两种铬系催化剂的切换过程中,乙烯达不到满负荷,将聚合反应器中的床层完全置换,时间远大于6-8h;所以在切换过程中,可通过加快排料,将聚合反应器床层料位降低至不低于聚合反应工况条件下可操作的床层最低流化高度,尽快减弱第一种催化剂对第二种催化剂的影响。
29.进一步地,对于铬系催化剂,反应温度、反应压力、反应器中乙烯摩尔分数、氢气/乙烯摩尔比值、共聚单体/乙烯摩尔比值、流化气速、床层料位、停留时间、催化剂进料量、氧气注入量、乙烯负荷等都是该催化剂聚合评价过程中的工艺控制条件,其中敏感工艺控制条件为氧气注入量,氧气是铬系催化剂的活性抑制剂,氧气注入量越多,催化剂活性抑制越明显;同时氧气注入是调控聚合产品熔融指数的重要工艺条件。在铬系两种催化剂之间的切换过程中,关键步骤为:(1)尽快减弱第一种催化剂的残留反应,弱化第一种催化剂对第二种催化剂的干扰;(2)选择第二种催化剂加入聚合反应器的时机,加快第二种催化剂建立反应的时间;(3)切换过程中流化状态的即时监测及调整,保证切换过程的平稳控制。
30.在以往的切换过程中,切换过程控制不够精细、明确,切换关键控制点模糊,尤其是第二种催化剂的加入时间和加入量掌握不好,切换过程中流化状态控制不平稳等诸多因素,造成切换时间过长,流化状态紊乱、细粉含量(乙烯聚合物中粒径≤0.125mm的粉料比重)增加而造成循环气压缩机、循环气换热器、反应器分布板等堵塞,从而导致整个聚合装置停车,需要重新换床重新开车,不仅影响聚合装置催化剂评价试验,同时造成大量的物耗、能耗。
31.因此,本发明所采用的具体的技术方案是:
32.(1)停止第一种铬系催化剂进料,同时停止氧气注入。在铬系催化剂的气相聚合反应中,氧气是调控聚合产品熔融指数的重要工艺条件,同时也是催化剂活性抑制剂。在停止第一种铬系催化剂进料后,如果不停止氧气注入,残留在聚合反应器中的第一种催化剂会加快失活,但同时会对第二种铬系催化剂加入聚合反应器后建立反应起到抑制作用,延长第二种铬系催化剂建立反应的引发时间,所以停止第一种铬系催化剂进料的同时,停止氧气注入。聚合反应器中残留的催化剂仍在进行反应,但是逐渐减弱;残留的第一铬系催化剂反应有助于加快第二种铬系催化剂加入聚合反应器后的反应建立时间,加快两种铬系催化剂的切换时间。
33.(2)按照时间间隔设定排料程序,将床层料位降低至不低于聚合反应工况条件下可操作的床层最低流化高度。通过缩短排料设定程序的时间间隔,单位时间内的排料次数增多,会加快排料过程,短时间内将床层料位降低至不低于聚合反应工况条件下可操作的床层最低流化高度;通过加快排料,可将粉料中夹带的残留催化剂的大部分排出聚合反应器,尽快减弱第一种铬系催化剂在聚合反应器中的残留反应,弱化第一种铬系催化剂对第二种铬系催化剂建立聚合反应平衡状态的干扰。
34.(3)按照第二种铬系催化剂的工艺控制条件,依次调整气相反应器中反应温度、反应压力、乙烯摩尔分数、氢气/乙烯摩尔比值、共聚单体/乙烯摩尔比值等工艺条件。在第一种铬系催化剂残留反应的存在下,即可对气相反应器中反应温度、反应压力、乙烯摩尔分数、氢气/乙烯摩尔比值、共聚单体/乙烯摩尔比值等工艺条件进行调整,尽快构建第二种气相催化剂建立反应的工艺控制条件。其中反应温度、反应压力、乙烯摩尔分数是首要工艺控制条件;切换过程中,反应温度、反应压力、乙烯摩尔分数都达到第二种气相催化剂的工艺控制要求,即可往聚合反应器加入第二种气相催化剂。所以反应温度、反应压力、乙烯摩尔分数等工艺控制条件的快速调整,会加快第二种气相催化剂的加入时间,同时会加快第二种气相催化剂聚合反应平稳状态的调整时间,加快两种铬系催化剂的切换时间。
35.(4)开始按照≤正常消耗量的1/2加入第二种催化剂;当建立反应后,开始注入氧气,氧气注入量根据乙烯负荷进行调整;然后逐渐增加第二种催化剂进料量和氧气注入量,直至控制乙烯负荷达100%。床层料位的降低,减弱第一种气相催化剂在聚合反应器中的残留反应,弱化了聚合反应器中第一种气相催化剂的残留反应对第二种气相催化剂建立聚合反应平衡状态的干扰;气相反应器中反应温度、反应压力、乙烯摩尔分数等工艺条件的调整到位,使得第二种气相催化剂加入聚合反应器具备了条件。但在切换过程中,为防止细粉含量增加,结片产生,所以在开始加入时,按照≤正常消耗量的1/2加入第二种气相催化剂。当建立反应以后,开始注入氧气,氧气注入量根据乙烯负荷进行调整;为了切换过程的平稳过渡,逐渐增加第二种气相催化剂进料量和氧气注入量,直至控制乙烯负荷达100%。
36.(5)在切换过程中,观察反应器压差分布、温度分布、静电变化等表征流化状态的工艺参数,及时调整流化气速、停留时间、催化剂进料量、乙烯负荷等工艺条件。反应器压差分布、温度分布、静电变化等是表征流化状态的工艺参数,是判断切换过程平稳过渡的重要依据。根据气相反应器压差分布、温度分布、静电等工艺参数的变化趋势,可及时对流化气速、停留时间、催化剂进料量、乙烯负荷等工艺条件进行调整。及时调整流化气速,是为了保持气相反应器流化状态的平稳过渡;调整停留时间,是为了减少反应器中细粉含量的滞留。
37.(6)根据第二种铬系催化剂的工艺控制条件和聚合产品指标对氢气/乙烯摩尔比值、共聚单体/乙烯摩尔比值、氧气注入量进行微调。当聚合产品指标进行检测合格后,切换过程平稳结束。在加入第二种铬系催化剂建立反应后,逐渐增加第二种铬系催化剂进料量和氧气注入量,直至控制乙烯负荷达100%的过程中,反应器压差分布、温度分布、静电变化等表征流化状态的工艺参数变化趋势平稳,说明切换过程顺利过渡,第一种铬系催化剂的聚合工艺状态已过渡为第二种铬系催化剂的聚合工艺状态;只需要根据第二种铬系催化剂的工艺控制条件和聚合产品指标对氢气/乙烯摩尔比值、共聚单体/乙烯摩尔比值、氧气注入量进行微调,至密度、熔融指数、堆密度、聚合物粉料粒径分布等产品指标合格,转入正常生产。
38.本发明提供的气相法聚乙烯铬系列不同催化剂之间的切换方法,第一,在停止第一种铬系催化剂进料后,设定时间排料,将床层料位降低,加快排料,是为了尽快减弱第一种铬系催化剂的残留反应,弱化第一种铬系催化剂对第二种铬系催化剂建立聚合反应平衡状态的干扰;第二,在反应器中反应温度、反应压力、乙烯摩尔分数等首要工艺控制条件已经调整到位、以及第一种铬系催化剂残留反应尚存在的条件下,加入第二种铬系催化剂,是为了促进第二种铬系催化剂加入聚合反应器后快速建立反应,加快两种催化剂不同聚合工
艺条件的调整速度,缩短两种催化剂聚合工艺之间的切换时间;第三,在切换过程中,观察反应器压差分布、温度分布、静电变化等表征流化状态的工艺参数,及时调整流化气速、停留时间、催化剂进料量、乙烯负荷等工艺条件,是为了保持气相反应器流化状态的平稳过渡,减少反应器中细粉含量的滞留,避免造成循环气压缩机、循环气换热器、反应器分布板等堵塞,从而导致整个聚合装置停车。
具体实施方式
39.以下对本发明的实施例作详细说明:本实施例在以本发明技术方案为前提下进行实施,给出了详细的实施方式和过程,但本发明的保护范围不限于下述的实施例,下列实施例中未注明具体条件的实验方法,通常按照常规条件。
40.以下结合在50kg/h气相法聚乙烯试验装置进行的实施例对本发明进一步描述。
41.实施例1
42.第一种铬系催化剂是硅胶负载的硅烷铬酸酯催化剂,催化剂中,硅烷铬酸酯的含量为1.83wt%,余量为硅胶,活性为2000~3000g pe/g cat,生产工艺条件如表1所示:
43.表1
[0044][0045]
第二种铬系催化剂是负载在硅胶载体上的cro3型催化剂,催化剂中,cro3的含量为2.0%,余量为载体,活性为20000~30000 g pe/g cat,生产工艺条件如表2所示:
[0046]
表2
[0047][0048]
两种铬系催化剂聚合工艺切换方法,具体实施步骤为:
[0049]
(1)停止第一种铬系催化剂进料,停止氧气注入,同时停止己烯-1进料;
[0050]
(2)按照60s/次时间间隔设定排料程序,将床层料位降低至正常控制料位的90%,降至1.845m;
[0051]
(3)开始逐步提高反应温度至103℃,升压至2.25mpa,降低反应器中乙烯摩尔分数至40%;同时根据氢气/乙烯摩尔比值的在线色谱分析结果,调整氢气进料量,逐渐控制氢气/乙烯摩尔比值由0.10mol/mol降至0.09mol/mol;开始丁烯-1进料,并根据丁烯-1/乙烯摩尔比值的在线色谱分析结果,调整丁烯-1进料量,控制丁烯-1/乙烯摩尔比值由0mol/mol升至0.012mol/mol;
[0052]
(4)开始按照0.8g/h加入第二种铬系催化剂;当建立反应后,开始注入氧气,根据氧气注入量/乙烯负荷比值的在线分析结果,调整氧气注入量,控制氧气注入量/乙烯负荷比值由20ppb升至50ppb;然后逐渐增加第二种铬系催化剂进料量至1.8g/h,氧气注入量至2.8mg/h,控制乙烯负荷为100%(乙烯进料量为50kg/h);
[0053]
(5)切换过程中,观察反应器压差分布、温度分布、静电变化等表征流化状态的工艺参数变化情况,流化气速由0.60m/s调整为0.59m/s,停留时间维持在2.5~3h;
[0054]
(6)根据第二种铬系催化剂的工艺控制条件和聚合产品指标对氢气/乙烯摩尔比值、丁烯-1/乙烯摩尔比值、氧气注入量进行微调。当聚合产品指标进行检测合格后,切换过程平稳结束。
[0055]
由第一种催化剂的聚合工艺成功切换至第二种催化剂的聚合工艺,切换时间为6h,切换过程平稳,细粉含量保持在≤6%。
[0056]
对比例1
[0057]
两种铬系催化剂聚合工艺切换方法,与实施例1的步骤中的不同之处:
[0058]
(1)第一种铬系催化剂停止进料后,未进行排料操作,第一种铬系催化剂残留反应的存在时间过长对第二种催化剂进入反应器后建立聚合反应平衡状态形成干扰;
[0059]
(2)切换过程中对乙烯负荷、流化气速、停留时间没有进行关注和及时的调整,易导致细粉含量的增加和结片的产生。
[0060]
整个切换过程,时间为19h,细粉含量持续升高至21%,导致循环气压缩机、循环气
换热器、反应器分布板等堵塞,整个聚合装置停车,需要重新换床重新开车。
[0061]
实施例2
[0062]
第一种铬系催化剂是负载在硅胶载体上钛改性的cro3型催化剂,催化剂中,cro3的含量为2.03wt%,钛含量以氧化钛计为3.75wt%,余量为载体,活性为40000~50000g pe/g cat,生产工艺条件如表3所示:
[0063]
表3
[0064][0065]
第二种铬系催化剂是铬系催化剂是硅胶负载的硅烷铬酸酯催化剂,催化剂中,硅烷铬酸酯的含量为1.95%,余量为硅胶,活性为3000~5000g pe/g cat,生产工艺条件如表4所示:
[0066]
表4
[0067][0068]
两种铬系催化剂聚合工艺切换方法,具体实施步骤为:
[0069]
(1)停止第一种铬系催化剂进料,停止氧气注入;
[0070]
(2)按照90s/次时间间隔设定排料程序,将床层料位降低至正常控制料位的88%,降至1.80m;
[0071]
(3)开始逐步降低反应温度至98℃,提高反应器中乙烯摩尔分数至55%,根据氢
气/乙烯摩尔比值的在线色谱分析结果,调整氢气进料量,逐渐控制氢气/乙烯摩尔比值由0.09mol/mol升至0.10mol/mol;根据丁烯-1/乙烯摩尔比值的在线色谱分析结果,调整丁烯-1进料量,控制丁烯-1/乙烯摩尔比值由0.012mol/mol降至0.004mol/mol;
[0072]
(4)开始按照6g/h加入第二种铬系催化剂;当建立反应后,开始注入氧气,根据氧气注入量/乙烯负荷比值的在线分析结果,调整氧气注入量,控制氧气注入量/乙烯负荷比值由50ppb降至20ppb;然后逐渐增加第二种铬系催化剂进料量至12g/h,氧气注入量至1.14mg/h,控制乙烯负荷为100%(乙烯进料量为50kg/h);
[0073]
(5)切换过程中,观察气相反应器压差分布、温度分布、静电变化等表征流化状态的工艺参数变化情况,流化气速由0.58m/s调整为0.61m/s,停留时间维持在2~2.5h;
[0074]
(6)根据第二种铬系催化剂的工艺控制条件和聚合产品指标对氢气/乙烯摩尔比值、丁烯-1/乙烯摩尔比值、氧气注入量进行微调。当聚合产品指标进行检测合格后,切换过程平稳结束。
[0075]
由第一种催化剂的聚合工艺成功切换至第二种催化剂的聚合工艺,切换时间为5.5h,切换过程平稳,细粉含量保持在≤6.4%。
[0076]
对比例2
[0077]
两种铬系催化剂聚合工艺切换方法,与实施例2步骤中的不同之处:
[0078]
(1)第一种催化剂停止进料后,未进行排料操作,第一种催化剂残留反应的存在时间过长对第二种催化剂进入反应器后建立聚合反应平衡状态形成干扰;
[0079]
(2)切换过程中对乙烯负荷、流化气速、停留时间没有进行关注和及时的调整,易导致细粉含量的增加和结片的产生。
[0080]
整个切换过程,时间为21h,细粉含量持续升高至23%,导致循环气压缩机、循环气换热器、反应器分布板等堵塞,整个聚合装置停车,需要重新换床重新开车。
[0081]
实施例3
[0082]
第一种铬系催化剂是负载在硅胶载体上的cro3型催化剂,催化剂中,cro3的含量为1.86wt%,活性为10000~15000g pe/g cat,生产工艺条件如表5所示:
[0083]
表5
[0084][0085]
第二种铬系催化剂是负载在硅胶载体上的钛改性cro3型催化剂,钛含量以氧化钛
计为5.78wt%,cro3的含量为1.68wt%,活性为12000~18000g pe/g cat,生产工艺条件如表6所示:
[0086]
表6
[0087][0088][0089]
两种铬系催化剂聚合工艺切换方法,具体实施步骤为:
[0090]
(1)停止第一种铬系催化剂进料,停止氧气注入;
[0091]
(2)按照100s/次时间排料设定排料程序,将床层料位降低至正常控制料位的92%,降至1.89m;
[0092]
(3)开始逐步提高反应温度至98℃,提高反应器中乙烯摩尔分数至55%,根据氢气/乙烯摩尔比值的在线色谱分析结果,调整氢气进料量,逐渐控制氢气/乙烯摩尔比值由0.11mol/mol降至0.10mol/mol;根据己烯-1/乙烯摩尔比值的在线色谱分析结果,调整己烯-1进料量,控制己烯-1/乙烯摩尔比值由0.02mol/mol升至0.1mol/mol;
[0093]
(4)开始按照1.4g/h加入第二种铬系催化剂;当建立反应后,开始注入氧气,根据氧气注入量/乙烯负荷比值的在线分析结果,调整氧气注入量,控制氧气注入量/乙烯负荷比值由50ppb降至40ppb;然后逐渐增加第二种铬系催化剂进料量至3.5g/h,氧气注入量至1.72mg/h,控制乙烯负荷为100%(乙烯进料量为50kg/h);
[0094]
(5)切换过程中,观察气相反应器压差分布、温度分布、静电变化等表征流化状态的工艺参数变化情况,流化气速由0.60m/s调整为0.61m/s,停留时间维持在1.5~2.5h;
[0095]
(6)根据第二种铬系催化剂的工艺控制条件和聚合产品指标对氢气/乙烯摩尔比值、己烯-1/乙烯摩尔比值、氧气注入量进行微调。当聚合产品指标进行检测合格后,切换过程平稳结束。
[0096]
由第一种催化剂的聚合工艺成功切换至第二种催化剂的聚合工艺,切换时间为5h,切换过程平稳,细粉含量保持在≤5.8%。
[0097]
对比例3
[0098]
两种铬系催化剂聚合工艺切换方法,与实施3的步骤中的不同之处:
[0099]
(1)第一种催化剂停止进料后,未进行排料操作,第一种催化剂残留反应的存在时间过长对第二种催化剂进入反应器后建立聚合反应平衡状态形成干扰;
[0100]
(2)第二种催化剂开始就已正常消耗量加入聚合反应器,易造成流化状态紊乱,细粉增加、结片产生;
[0101]
(3)切换过程中对乙烯负荷、流化气速、停留时间没有进行关注和及时的调整,易导致细粉含量的增加和结片的产生。
[0102]
整个切换过程,时间为18h,细粉含量持续升高至19%,导致循环气压缩机、循环气换热器、反应器分布板等堵塞,整个聚合装置停车,需要重新换床重新开车。
[0103]
由以上实施例和对比例的对比可知,本发明提供的气相法聚乙烯铬系列不同催化剂之间的切换方法,第一,在停止第一种催化剂进料后,设定时间排料,将床层料位降低,加快排料,是为了尽快减弱第一种催化剂的残留反应,弱化第一种催化剂对第二种催化剂建立聚合反应平衡状态的干扰;第二,在反应器中反应温度、反应压力、乙烯摩尔分数等首要工艺控制条件已经调整到位、以及第一种催化剂残留反应尚存在的条件下,加入第二种催化剂,是为了促进第二种催化剂加入聚合反应器后快速建立反应,加快两种催化剂不同聚合工艺条件的调整速度,缩短两种催化剂聚合工艺之间的切换时间;第三,在切换过程中,观察反应器压差分布、温度分布、静电变化等表征流化状态的工艺参数,及时调整流化气速、停留时间、催化剂进料量、乙烯负荷等工艺条件,是为了保持气相反应器流化状态的平稳过渡,减少反应器中细粉含量的滞留,避免造成循环气压缩机、循环气换热器、反应器分布板等堵塞,从而导致整个聚合装置停车。
[0104]
当然,本发明还可有其它多种实施例,在不背离本发明精神及其实质的情况下,熟悉本领域的技术人员可根据本发明作出各种相应的改变和变形,但这些相应的改变和变形都应属于本发明的保护范围。