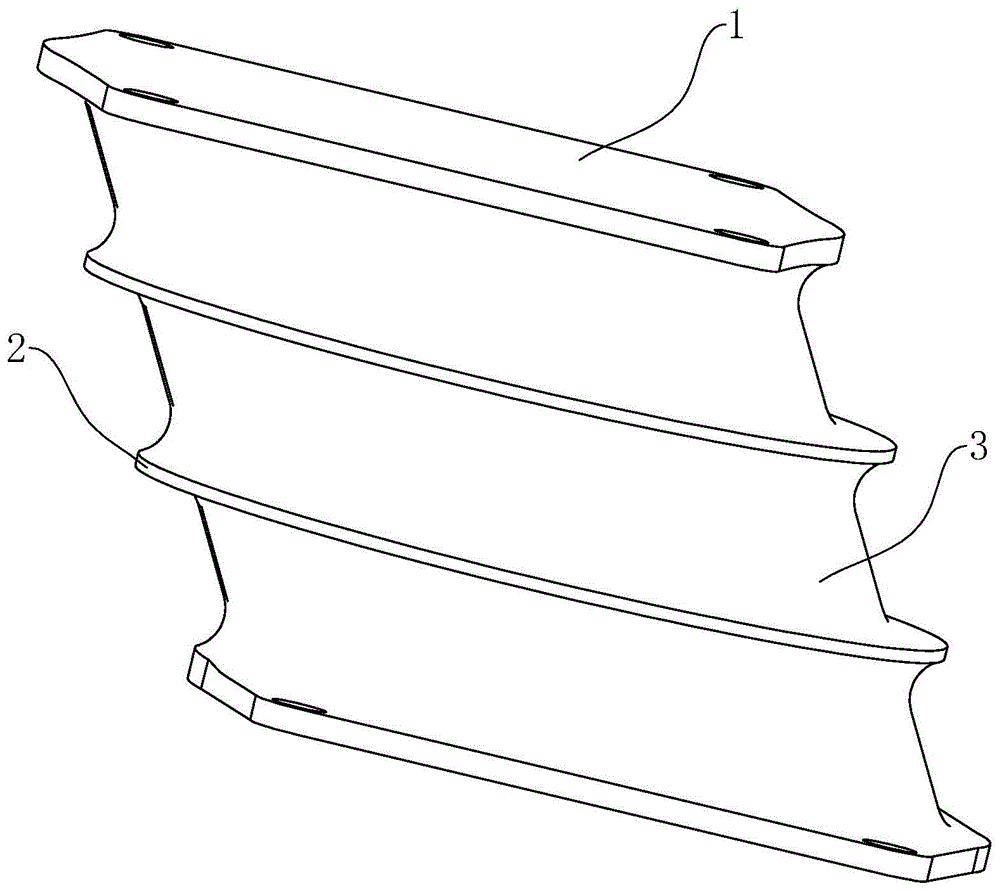
本申请涉及聚氨酯的
技术领域:
,尤其是涉及一种聚氨酯弹性材料以及采用该材料的聚氨酯弹性件。
背景技术:
:聚氨酯又称为聚氨基甲酸酯,由于其具有优良的耐磨性、耐油性和可设计性,且其软硬度可调;故在越来越多的领域得到应用。其中高弹性聚氨酯是聚氨酯应用的一个重要方面。目前,相关技术中,聚氨酯材料通过预聚体合成以及扩链反应而得到,其较高的弹性可通过原料的组分配比的调整而实现;聚氨酯的断裂伸长率可达到650%,回弹率可达到35%;可用于各种减震件上。针对上述中的相关技术,发明人认为相关技术中的聚氨酯材料尽管具有不错的弹性,但是对于如重型货车等要求较高领域的减震缓冲,还是存在一定不足。技术实现要素:针对相关技术存在的不足,为了提高聚氨酯材料的弹性,本申请提供了一种聚氨酯弹性材料以及采用该材料的聚氨酯弹性件。第一方面,本申请提供的一种聚氨酯弹性材料,采用如下技术方案:聚氨酯弹性材料,采用以下方法制得:(1)称取聚合物多元醇和二异氰酸酯并分别进行真空脱水;(2)在氮气保护下将脱水后的二异氰酸酯滴加到脱水后的聚合物多元醇中,之后加入催化剂;加热进行预聚反应得到预聚物;(3)称取苯乙烯-丁二烯-苯乙烯嵌段共聚物以及硅橡胶,真空脱水后与预聚物混合;(4)称取小分子二元醇、邻苯二甲酸酯,真空脱水后滴加到预聚物中并搅拌;之后注入模具中成型后硫化得到成品。通过采用上述技术方案,具有较高弹性的聚氨酯材料被制得;其中,苯乙烯-丁二烯-苯乙烯嵌段共聚物以及硅橡胶,可以和体系其他材料相配伍,有利于提高所制得的聚氨酯材料的弹性;小分子二元醇能够使扩链反应更加平稳,从而使扩链反应更加充分,进而提高了所制得的聚氨酯材料的性能;邻苯二甲酸酯作为增塑剂,可以提高所制得的聚氨酯材料的弹性。可选的,所述步骤(1)中,聚合物多元醇为聚醚多元醇;二异氰酸酯为二甲基联苯基二异氰酸酯、对苯二异氰酸酯或异佛尔酮二异氰酸酯。通过采用上述技术方案,聚醚多元醇相比于聚酯多元醇,更利于提高所制得的聚氨酯材料的弹性;而二甲基联苯基二异氰酸酯、对苯二异氰酸酯、异佛尔酮二异氰酸酯均能很好的参与聚氨酯的合成,保证聚氨酯材料的合成顺利完成。可选的,所述步骤(1)中,称取聚合物多元醇100质量份和二异氰酸酯90-130质量份,对两者分别加热并在110-120℃的条件下分别进行真空脱水。通过采用上述技术方案,通过加热更利于聚合物多元醇和二异氰酸酯脱水。可选的,所述步骤(2)中,预聚反应的温度控制在70-90℃。通过采用上述技术方案,能使聚氨酯材料顺利合成,并保证其具有较好的性能;而预聚温度较低,会使反应体系表观粘度变大,从而影响了反应进程;预聚温度过高时,体系过于活泼,会使-nco基团迅速反应并生成的-nhco-,而有一部分-nhco-又进一步与未反应的-nco反应生成脲,从而使-nco含量明显低于理论值,进而影响了聚氨酯材料的合成。可选的,所述步骤(3)中,还称取乙烯基弹性体、聚乙烯蜡以及抗氧化剂。通过采用上述技术方案,乙烯基弹性体有利于提高聚氨酯材料的弹性;聚乙烯蜡有利于提高反应中各组分的相容性,从而有利于聚氨酯合成的顺利进行。可选的,所述步骤(3)中,称取苯乙烯-丁二烯-苯乙烯嵌段共聚物10-22质量份、硅橡胶10-15质量份、乙烯基弹性体3-8质量份、聚乙烯蜡2-8质量份以及抗氧化剂0.2-0.6质量份,真空脱水后加入预聚物中混合。通过采用上述技术方案,通过各辅助原料的配伍,能够赋予最终合成的聚氨酯材料更好的性能。可选的,所述步骤(4)中,称取小分子二元醇20-35质量份及邻苯二甲酸酯8-12质量份滴加到预聚物中,同时抽真空脱去气泡。通过采用上述技术方案,为聚氨酯平稳合成创造了条件,并赋予聚氨酯材料较好的弹性。可选的,所述步骤(4)中,模具温度控制在90-110℃、硫化温度控制在120-130℃。通过采用上述技术方案,模具温度的合理控制,有助于聚氨酯合成反应的顺利进行,且有助于提高聚氨酯材料的性能。第二方面,本申请提供的一种采用上述聚氨酯弹性材料的聚氨酯弹性件,采用如下技术方案:采用上述聚氨酯弹性材料的聚氨酯弹性件,包括端板、中间加强板以及聚氨酯块;所述端板设置两块且上下平行设置;所述中间加强板设置于两端板之间,且与端板平行设置;所述聚氨酯块设置多个,且均为倾斜设置的圆柱体,聚氨酯块至少有一端的端面与中间加强板连接,另一端端面与端板或中间加强板连接。通过采用上述技术方案,聚氨酯块具有良好的弹性,可以起到缓冲减震的作用,使聚氨酯弹性件具有良好的弹性和缓冲能力。中间加强板可起到加强的作用,便于聚氨酯弹性件整体压缩后材料的流动。聚氨酯块呈倾斜圆柱体的设置,使整个聚氨酯弹性件呈倾斜设置的柱体;在实际使用中,通过两个聚氨酯弹性件相互配合,呈v字形安装,有助于更好的缓解冲击,不至于受到过大的横向力使橡胶弹性件本身受损。可选的,所述包括端板和中间加强板均采用聚氨酯弹性材料包裹。通过采用上述技术方案,可使整个聚氨酯弹性件具有更好的弹性和缓冲能力。综上所述,本申请至少包括以下有益技术效果之一:1.本申请所制得的聚氨酯弹性材料具有良好的弹性和不错的力学强度,其拉伸强度在42mpa以上,断裂伸长率在730%以上、回弹率在43%以上。2.本申请通过苯乙烯-丁二烯-苯乙烯嵌段共聚物以及硅橡胶的加入,能够提高所制得的聚氨酯材料的弹性。3.本申请通过小分子二元醇的加入使扩链反应更加平稳,从而使扩链反应更加充分,进而提高了所制得的聚氨酯材料的性能;邻苯二甲酸酯作为增塑剂,可以提高所制得的聚氨酯材料的弹性。4.本申请的聚氨酯弹性件具有良好的弹性和缓冲能力。附图说明图1是本申请实施例1的聚氨酯弹性件的立体示意图。附图标记说明:1、端板;2、中间加强板;3、聚氨酯块。具体实施方式以下结合附图对本申请作进一步详细说明。实施例中所用的原材料中:四氢呋喃醚二醇购自济南朋多商贸有限公司,分子量为950-1050,羟值为107-117mgkoh/g,酸值<0.005mgkoh/g。聚氧化丙烯二醇购自南通润洲化工有限公司,分子量为1000,羟值为102-125mgkoh/g,酸值≤0.5mgkoh/g。聚乙二醇购自上海链集化工有限公司,分子量为900-1100,羟值为102-125mgkoh/g。对苯二异氰酸酯购自湖北信康医药化工有限公司,密度为1.17g/cm3。3,3'-二甲基联苯基-4,4-二异氰酸酯购自广州昊毅新材料科技股份有限公司,密度为1.20g/cm3。异佛尔酮二异氰酸酯购自康迪斯化工(湖北)有限公司,nco基含量≥37.5%。苯乙烯-丁二烯-苯乙烯嵌段共聚物购自苏州陶氏进出口有限公司,密度0.87g/cm3。硅橡胶购自济南海澜化工有限公司,107型。乙烯辛烯共聚物购自东莞市樟木头恒泰塑胶原料经营部,其总苯乙烯含量为30-45wt%。邻苯二甲酸二异癸酯购自南通润丰石油化工有限公司。邻苯二甲酸二甲氧基乙酯购自杭州潜阳科技股份有限公司。实施例1本申请实施例公开了一种聚氨酯弹性材料,其采用以下方法制得:(1)称取聚四氢呋喃二醇100kg和对苯二异氰酸酯100kg;分别对两者加热到115℃,之后分别在相对真空度为-0.09mpa的条件下真空脱水1.5h。其中,脱水的目的在于:由于二异氰酸酯会与水发生反应,而使预聚物反应体系的粘度变大,而反应体系粘度变大不利于反应物之间的充分接触,从而影响了聚氨酯材料的顺利合成,进而影响了聚氨酯材料的性能。(2)在氮气保护下将脱水后的对苯二异氰酸酯滴加到脱水后的聚四氢呋喃二醇中,滴加控制在2h完成;之后加入作为催化剂的二月桂酸二丁基锡0.2kg;之后加热到85℃,保温3h进行预聚反应得到预聚物。其中,氮气保护的目的与脱水目的类似,为了减少二异氰酸酯与空气中的湿气发生反应而影响到聚氨酯材料的性能。同时将二异氰酸酯采用分批的方式(滴加)加入到聚合物多元醇中,可以使二异氰酸酯和聚合物多元醇由足够的反应时间,使反应更充分,有利于提高最终产物聚氨酯的性能。(3)称取苯乙烯-丁二烯-苯乙烯嵌段共聚物20kg、硅橡胶12kg、乙烯辛烯共聚物5kg、聚乙烯蜡6kg以及抗氧化剂10100.5kg,在40℃的温度下将上述材料混合均匀得到辅助料;之后将辅助料在温度为100℃、相对真空度为-0.09mpa的条件下真空脱水1h;将脱水后的辅助料加入预聚物中混合均匀。其中,苯乙烯-丁二烯-苯乙烯嵌段共聚物为一种苯乙烯类热塑性弹性体,其加入可以提高聚氨酯材料的弹性。硅橡胶不仅具有良好的弹性且还具有较好的耐低温性和耐高温性,将其复合在聚氨酯材料中,能够改善聚氨酯材料的性能。同时,乙烯辛烯共聚物为一种乙烯基弹性体,具有良好的柔软性和韧性,对于提高聚氨酯材料的弹性有积极影响;聚乙烯蜡用于提高各原料组分之间的相容性,有利于聚氨酯合成的顺利进行。(4)称取1,4-丁二醇25kg及邻苯二甲酸二异癸酯9kg混合并在温度为100℃、相对真空度为-0.09mpa的条件下真空脱水0.6h;之后滴加到温度为90℃,混合有辅助料的预聚物中并采用1000r/m的转速快速搅拌均匀,控制滴加时间为15min;同时抽真空以脱去气泡(相对真空度控制在-0.09mpa);滴加完成后将混合物注入100℃的模具中成型20min;之后脱模,在125℃下硫化5h得到成品。其中,1,4-丁二醇为一种小分子二元醇,其作为扩链剂扩链速度较慢,但是反应更加平稳,有利于聚氨酯的链段更加有序的排列,能够提高聚氨酯材料的性能;且相比于相关技术中通常采用的刚性较强的3,3'-二氯-4,4'-二氨基二苯基甲烷,1,4-丁二醇更有利于提高聚氨酯材料的弹性。邻苯二甲酸二异癸酯为一种增塑剂,可以延长聚氨酯制备时的固化时间,降低其硬度,提高聚氨酯材料的弹性。采用分批滴加扩链剂(1,4-丁二醇)到预聚体的方式,使反应更加平稳,有利于各组分充分接触反应,形成硬链段与硬链段及软链段与软链段之间较为有序的排列,从而提高聚氨酯材料的性能。本申请实施例还公开了一种采用上述聚氨酯弹性材料的聚氨酯弹性件。参照图1,一种聚氨酯弹性件,可用于汽车上的缓冲减震,其包括端板1、中间加强板2以及聚氨酯块3。聚氨酯块3采用上述聚氨酯弹性材料制成;端板1和中间加强板2均为铁板,且均外包了2-3mm的聚氨酯。参照图1,端板1具有两块且上下平行设置,中间加强板2也具有两块(可根据实际情况增减)并设置于两端板1之间。每块中间加强板2均与端板1平行设置,并且两块中间加强板2在端板1之间的空间里上下均匀分布。在端板1与中间加强板2之间以及两块中间加强板2之间均连接有聚氨酯块3;连接方式可采用聚氨酯软化后粘接或者在模具中通过熔融的聚氨酯浇筑而一体成型。另外,在端板1与聚氨酯块3、中间加强板2与聚氨酯块3的连接处利用聚氨酯材料设置弧形连接部,以减少应力集中。在聚氨酯弹性件中,聚氨酯块3由于具有良好的弹性,起到缓冲减震的作用;中间加强板2起到加强的作用,便于聚氨酯弹性件整体压缩后材料的流动。端板1起到连接板的作用。另外,参照图1,聚氨酯块3为倾斜设置的圆柱体;并且,位于端板1与中间加强板2之间的聚氨酯块3的一端的端面连接在中间加强板2的中心处,另一端端面与端板1的中心相连接;同时位于两块中间加强板2之间的聚氨酯块3,其两端端面分别连接在对应的中间加强板2的中心处;从而,使整个聚氨酯弹性件呈倾斜设置的柱体;在实际使用中,需两个聚氨酯弹性件配合使用;两块聚氨酯弹性件呈v字形安装,有助于更好的缓解冲击,不至于受到过大的横向力使橡胶弹性件本身受损。实施例2本申请实施例公开了一种聚氨酯弹性材料,其采用以下方法制得:(1)称取聚四氢呋喃二醇100kg和3,3'-二甲基联苯基-4,4-二异氰酸酯90kg;分别对两者加热到120℃,之后分别在相对真空度为-0.09mpa的条件下真空脱水1h。(2)在氮气保护下将脱水后的3,3'-二甲基联苯基-4,4-二异氰酸酯滴加到脱水后的聚四氢呋喃二醇中,滴加控制在1.5h完成;之后加入作为催化剂的二月桂酸二丁基锡0.1kg;之后加热到90℃,保温2h进行预聚反应得到预聚物。(3)称取苯乙烯-丁二烯-苯乙烯嵌段共聚物22kg、硅橡胶10kg、乙烯辛烯共聚物3kg、聚乙烯蜡8kg以及抗氧化剂10100.6kg,在40℃的温度下将上述材料混合均匀得到辅助料;之后将辅助料在温度为100℃、相对真空度为-0.09mpa的条件下真空脱水1.5h;将脱水后的辅助料加入预聚物中混合均匀。(4)称取1,4-丁二醇20kg及邻苯二甲酸二甲氧基乙酯8kg混合并在温度为100℃、相对真空度为-0.09mpa的条件下真空脱水1h;之后滴加到温度为90℃,混合有辅助料的预聚物中并采用1200r/m的转速快速搅拌均匀,控制滴加时间为10min;同时抽真空以脱去气泡(相对真空度控制在-0.09mpa);滴加完成后将混合物注入90℃的模具中成型30min;之后脱模,在130℃下硫化4h得到成品。本申请实施例还公开了一种采用上述聚氨酯弹性材料的聚氨酯弹性件,其结构与实施例1相同。实施例3本申请实施例公开了一种聚氨酯弹性材料,其采用以下方法制得:(1)称取聚四氢呋喃二醇100kg和异佛尔酮二异氰酸酯130kg;分别对两者加热到110℃,之后分别在相对真空度为-0.09mpa的条件下真空脱水2h。(2)在氮气保护下将脱水后的异佛尔酮二异氰酸酯滴加到脱水后的聚四氢呋喃二醇中,滴加控制在2.5h完成;之后加入作为催化剂的二月桂酸二丁基锡0.5kg;之后加热到75℃,保温4h进行预聚反应得到预聚物。(3)称取苯乙烯-丁二烯-苯乙烯嵌段共聚物10kg、硅橡胶15kg、乙烯辛烯共聚物8kg、聚乙烯蜡3kg以及抗氧化剂10100.2kg,在35℃的温度下将上述材料混合均匀得到辅助料;之后将辅助料在温度为100℃、相对真空度为-0.09mpa的条件下真空脱水1h;将脱水后的辅助料加入预聚物中混合均匀。(4)称取1,4-丁二醇35kg及邻苯二甲酸二甲氧基乙酯12kg混合并在温度为100℃、相对真空度为-0.09mpa的条件下真空脱水0.6h;之后滴加到温度为90℃,混合有辅助料的预聚物中并采用1500r/m的转速快速搅拌均匀,控制滴加时间为8min;同时抽真空以脱去气泡(相对真空度控制在-0.09mpa);滴加完成后将混合物注入110℃的模具中成型15min;之后脱模,在125℃下硫化5h得到成品。本申请实施例还公开了一种采用上述聚氨酯弹性材料的聚氨酯弹性件,其结构与实施例1相同。实施例4本申请实施例公开了一种聚氨酯弹性材料,其采用以下方法制得:(1)称取聚氧化丙烯二醇100kg和对苯二异氰酸酯100kg;分别对两者加热到115℃,之后分别在相对真空度为-0.09mpa的条件下真空脱水2h。(2)在氮气保护下将脱水后的对苯二异氰酸酯滴加到脱水后的聚氧化丙烯二醇中,滴加控制在2h完成;之后加入作为催化剂的二月桂酸二丁基锡0.2kg;之后加热到70℃,保温5h进行预聚反应得到预聚物。(3)称取苯乙烯-丁二烯-苯乙烯嵌段共聚物15kg、硅橡胶12kg、乙烯辛烯共聚物7kg、聚乙烯蜡6kg以及抗氧化剂10100.6kg,在35℃的温度下将上述材料混合均匀得到辅助料;之后将辅助料在温度为105℃、相对真空度为-0.09mpa的条件下真空脱水1h;将脱水后的辅助料加入预聚物中混合均匀。(4)称取1,4-丁二醇25kg及邻苯二甲酸二异癸酯9kg混合并在温度为105℃、相对真空度为-0.09mpa的条件下真空脱水0.6h;之后滴加到温度为95℃,混合有辅助料的预聚物中并采用1500r/m的转速快速搅拌均匀,控制滴加时间为10min;同时抽真空以脱去气泡(相对真空度控制在-0.09mpa);滴加完成后将混合物注入90℃的模具中成型35min;之后脱模,在120℃下硫化6h得到成品。本申请实施例还公开了一种采用上述聚氨酯弹性材料的聚氨酯弹性件,其结构与实施例1相同。实施例5本申请实施例公开了一种聚氨酯弹性材料,其采用以下方法制得:(1)称取聚氧化丙烯二醇100kg和3,3'-二甲基联苯基-4,4-二异氰酸酯120kg;分别对两者加热到110℃,之后分别在相对真空度为-0.09mpa的条件下真空脱水3h。(2)在氮气保护下将脱水后的3,3'-二甲基联苯基-4,4-二异氰酸酯滴加到脱水后的聚氧化丙烯二醇中,滴加控制在2.5h完成;之后加入作为催化剂的三乙烯二胺0.4kg;之后加热到80℃,保温4h进行预聚反应得到预聚物。(3)称取苯乙烯-丁二烯-苯乙烯嵌段共聚物18kg、硅橡胶12kg、乙烯辛烯共聚物4kg、聚乙烯蜡4kg以及抗氧化剂10100.3kg,在35℃的温度下将上述材料混合均匀得到辅助料;之后将辅助料在温度为105℃、相对真空度为-0.09mpa的条件下真空脱水1h;将脱水后的辅助料加入预聚物中混合均匀。(4)称取1,4-丁二醇30kg及邻苯二甲酸二异癸酯11kg混合并在温度为105℃、相对真空度为-0.09mpa的条件下真空脱水0.6h;之后滴加到温度为95℃,混合有辅助料的预聚物中并采用1200r/m的转速快速搅拌均匀,控制滴加时间为12min;同时抽真空以脱去气泡(相对真空度控制在-0.09mpa);滴加完成后将混合物注入100℃的模具中成型25min;之后脱模,在120℃下硫化6h得到成品。本申请实施例还公开了一种采用上述聚氨酯弹性材料的聚氨酯弹性件,其结构与实施例1相同。实施例6本申请实施例公开了一种聚氨酯弹性材料,其采用以下方法制得:(1)称取聚乙二醇100kg和异佛尔酮二异氰酸酯90kg;分别对两者加热到120℃,之后分别在相对真空度为-0.09mpa的条件下真空脱水1.5h。(2)在氮气保护下将脱水后的异佛尔酮二异氰酸酯滴加到脱水后的聚乙二醇中,滴加控制在1.5h完成;之后加入作为催化剂的三乙烯二胺0.1kg;之后加热到85℃,保温2h进行预聚反应得到预聚物。(3)称取苯乙烯-丁二烯-苯乙烯嵌段共聚物12kg、硅橡胶15kg、乙烯辛烯共聚物7kg、聚乙烯蜡8kg以及抗氧化剂10100.6kg,在45℃的温度下将上述材料混合均匀得到辅助料;之后将辅助料在温度为110℃、相对真空度为-0.09mpa的条件下真空脱水0.5h;将脱水后的辅助料加入预聚物中混合均匀。(4)称取1,4-丁二醇21kg及邻苯二甲酸二甲氧基乙酯8kg混合并在温度为110℃、相对真空度为-0.09mpa的条件下真空脱水0.3h;之后滴加到温度为100℃,混合有辅助料的预聚物中并采用1000r/m的转速快速搅拌均匀,控制滴加时间为18min;同时抽真空以脱去气泡(相对真空度控制在-0.09mpa);滴加完成后将混合物注入110℃的模具中成型15min;之后脱模,在130℃下硫化4h得到成品。本申请实施例还公开了一种采用上述聚氨酯弹性材料的聚氨酯弹性件,其结构与实施例1相同。实施例7本申请实施例公开了一种聚氨酯弹性材料,其采用以下方法制得:(1)称取聚乙二醇100kg和对苯二异氰酸酯110kg;分别对两者加热到110℃,之后分别在相对真空度为-0.09mpa的条件下真空脱水3.5h。(2)在氮气保护下将脱水后的对苯二异氰酸酯滴加到脱水后的聚乙二醇中,滴加控制在2h完成;之后加入作为催化剂的三乙烯二胺0.3kg;之后加热到90℃,保温1h进行预聚反应得到预聚物。(3)称取苯乙烯-丁二烯-苯乙烯嵌段共聚物16kg、硅橡胶12kg、乙烯辛烯共聚物7kg、聚乙烯蜡5kg以及抗氧化剂10100.4kg,在45℃的温度下将上述材料混合均匀得到辅助料;之后将辅助料在温度为110℃、相对真空度为-0.09mpa的条件下真空脱水1h;将脱水后的辅助料加入预聚物中混合均匀。(4)称取1,4-丁二醇28kg及邻苯二甲酸二甲氧基乙酯10kg混合并在温度为110℃、相对真空度为-0.09mpa的条件下真空脱水0.6h;之后滴加到温度为100℃,混合有辅助料的预聚物中并采用1200r/m的转速快速搅拌均匀,控制滴加时间为15min;同时抽真空以脱去气泡(相对真空度控制在-0.09mpa);滴加完成后将混合物注入100℃的模具中成型18min;之后脱模,在125℃下硫化5h得到成品。本申请实施例还公开了一种采用上述聚氨酯弹性材料的聚氨酯弹性件,其结构与实施例1相同。实施例8本实施例与实施例1基本相同,不同之处在于:在步骤(2)中,预聚反应的温度控制在60℃。实施例9本实施例与实施例1基本相同,不同之处在于:在步骤(2)中,预聚反应的温度控制在70℃。实施例10本实施例与实施例1基本相同,不同之处在于:在步骤(2)中,预聚反应的温度控制在100℃。实施例11本实施例与实施例1基本相同,不同之处在于:在步骤(3)中,不加入乙烯辛烯共聚物。实施例12本实施例与实施例1基本相同,不同之处在于:在步骤(3)中,不加入聚乙烯蜡。实施例13本实施例与实施例1基本相同,不同之处在于:在步骤(4)中,模具温度控制在75℃。实施例14本实施例与实施例1基本相同,不同之处在于:在步骤(4)中,模具温度控制在90℃。实施例15本实施例与实施例1基本相同,不同之处在于:在步骤(4)中,模具温度控制在110℃。实施例16本实施例与实施例1基本相同,不同之处在于:在步骤(4)中,模具温度控制在125℃。对比例1本对比例与实施例1基本相同,不同之处在于:不对各原料进行脱水处理。具体为:(1)称取聚四氢呋喃二醇100kg和对苯二异氰酸酯100kg。(2)在氮气保护下将对苯二异氰酸酯滴加到聚四氢呋喃二醇中;之后加入作为催化剂的二月桂酸二丁基锡0.2kg;之后加热到85℃,保温3h进行预聚反应得到预聚物。(3)称取苯乙烯-丁二烯-苯乙烯嵌段共聚物20kg、硅橡胶12kg、乙烯辛烯共聚物5kg、聚乙烯蜡6kg以及抗氧化剂10100.5kg,在40℃的温度下将上述材料混合均匀得到辅助料;将辅助料加入预聚物中混合均匀。(4)称取1,4-丁二醇25kg及邻苯二甲酸二异癸酯9kg混合;之后滴加到温度为90℃,混合有辅助料的预聚物中并采用1000r/m的转速快速搅拌均匀,控制滴加时间为15min;同时抽真空以脱去气泡(相对真空度控制在-0.09mpa);滴加完成后将混合物注入100℃的模具中成型20min;之后脱模,在125℃下硫化5h得到成品。对比例2本对比例与实施例1基本相同,不同之处在于:在将苯二异氰酸酯滴加到聚四氢呋喃二醇中时不进行氮气保护。对比例3本对比例与实施例1基本相同,不同之处在于:对苯二异氰酸酯加入聚四氢呋喃二醇中的方式由滴加改为一次性加入。具体为:(1)称取聚四氢呋喃二醇100kg和对苯二异氰酸酯100kg;分别对两者加热到115℃,之后分别在相对真空度为-0.09mpa的条件下真空脱水1.5h。(2)在氮气保护下将脱水后的对苯二异氰酸酯直接加入脱水后的聚四氢呋喃二醇中,滴加控制在2h完成;之后加入作为催化剂的二月桂酸二丁基锡0.2kg;之后加热到85℃,保温3h进行预聚反应得到预聚物。(3)称取苯乙烯-丁二烯-苯乙烯嵌段共聚物20kg、硅橡胶12kg、乙烯辛烯共聚物5kg、聚乙烯蜡6kg以及抗氧化剂10100.5kg,在40℃的温度下将上述材料混合均匀得到辅助料;之后将辅助料在温度为100℃、相对真空度为-0.09mpa的条件下真空脱水1h;将脱水后的辅助料加入预聚物中混合均匀。(4)称取1,4-丁二醇25kg及邻苯二甲酸二异癸酯9kg混合并在温度为100℃、相对真空度为-0.09mpa的条件下真空脱水0.6h;之后滴加到温度为90℃,混合有辅助料的预聚物中并采用1000r/m的转速快速搅拌均匀,控制滴加时间为15min;同时抽真空以脱去气泡(相对真空度控制在-0.09mpa);滴加完成后将混合物注入100℃的模具中成型20min;之后脱模,在125℃下硫化5h得到成品。对比例4本对比例与实施例1基本相同,不同之处在于:步骤(3)中不加入苯乙烯-丁二烯-苯乙烯嵌段共聚物。对比例5本对比例与实施例1基本相同,不同之处在于:步骤(3)中不加入硅橡胶。对比例6本对比例与实施例1基本相同,不同之处在于:步骤(4)中采用等量的3,3'-二氯-4,4'-二氨基二苯基甲烷代替1,4-丁二醇。对比例7本对比例与实施例1基本相同,不同之处在于:步骤(4)中不加入邻苯二甲酸二异癸酯。力学性能测试:将实施例1-16以及对比例1-7所提供的聚氨酯材料进行性能测试。1、拉伸强度测试:参照标准:gb/t528;试样采用哑铃状(1型);夹具移动速度500mm/min;实验时温度为25℃。2、断裂伸长率测试:参照标准:gb/t528;试样采用哑铃状(1型);夹具移动速度500mm/min;实验时温度为25℃。3、回弹率测试:参照标准:gb/t1681;试样厚度为12mm,直径为29mm;冲头直径12.45mm;检测温度为25℃。检测结果如表1:表1实施例1-16及对比例1-7的聚氨酯材料的力学性能检测编号拉伸强度/mpa断裂伸长率/%回弹率/%实施例14878048实施例24775045实施例34673043实施例44573044实施例54275046实施例64575045实施例74376047实施例84070040实施例94575043实施例104473042实施例114971041实施例124576045实施例134071041实施例144575044实施例154474042实施例164173042对比例13666036对比例23867037对比例33869039对比例44562032对比例54763032对比例63867037对比例74666036参见表1,实施例1-7考察了不同原料配方下所制得的聚氨酯材料的力学性能。通过上述检测结果可以发现:实施例1-7中所制得的聚氨酯材料的拉伸强度均在42mpa以上,断裂伸长率均在730%以上、回弹率均在43%以上,表现出良好的弹性;同时也有不错的力学强度。实施例1、实施例8-10考察了不同的预聚反应温度对于聚氨酯材料力学性能的影响;对比结果可知:当预聚反应温度较低(60℃,实施例8)或者过高(100℃,实施例10)时,所制得的聚氨酯材料的各项力学性能均相对略微逊色;这是由于预聚温度较低时,反应体系表观粘度大,流动性差,从而影响了反应进程;而预聚温度过高时,体系活泼,-nco基团迅速反应,生成的-nhco-有一部分又进一步与未反应的-nco反应生成脲,从而使-nco含量明显低于理论值,进而影响了聚氨酯材料的合成。实施例11考察了乙烯辛烯共聚物的加入对于聚氨酯材料弹性的影响;与实施例1相比:没添加乙烯辛烯共聚物的实施例11所得到的聚氨酯材料的弹性相对较差,表明乙烯辛烯共聚物的加入有助于提高聚氨酯材料的弹性。实施例12考察了聚乙烯蜡的加入对于聚氨酯复合材料力学性能的影响;对比实施例1:实施例12的聚氨酯材料的各项力学性能均更差;这是由于聚乙烯蜡的加入,可以提高各原料组分之间的相容性,有利于聚氨酯合成的顺利进行,从而提高了聚氨酯材料的性能。实施例1、实施例13-16考察了模具温度对于聚氨酯材料性能的影响;通过检测结果可知:当模具温度过低(75℃,实施例13)或者过高(125℃,实施例16),都会影响到聚氨酯材料的合成进程,从而影响到其性能。对比例1考察了不对原料进行脱水对最终聚氨酯材料性能的影响;由检测结果可以发现:不对原料进行脱水所制得的聚氨酯材料的各项力学性能均有明显下降。对比例2考察了在将苯二异氰酸酯滴加到聚四氢呋喃二醇中时不进行氮气保护对最终聚氨酯材料性能的影响;与对比例1的结果类似:不进行氮气保护操作所制得的聚氨酯材料的各项力学性能均有下降。对比例3考察了苯二异氰酸酯加入聚四氢呋喃二醇的方式对所制得的聚氨酯材料的性能的影响;对比实施例1可知:由于一次性将苯二异氰酸酯加入聚四氢呋喃二醇,使得反应剧烈进行,从而影响了反应的充分性,最终降低了所得聚氨酯材料的性能。对比例4考察了苯乙烯-丁二烯-苯乙烯嵌段共聚物的加入对于聚氨酯材料弹性的影响;结果表明:不加入苯乙烯-丁二烯-苯乙烯嵌段共聚物所得到的聚氨酯材料的弹性有明显下降。对比例5考察了硅橡胶的加入对于聚氨酯材料弹性的影响;结果与对比例4类似:不加入硅橡胶所得到的聚氨酯材料的弹性明显相对较差。对比例6考察了1,4-丁二醇的加入对于聚氨酯材料性能的影响;结果表明:与实施例1相比,没有使用1,4-丁二醇的对比例6所得到的聚氨酯材料的各项力学性能相对较差;这是由于1,4-丁二醇作为扩链剂能使扩链反应更加平稳,反应更充分。对比例7考察了邻苯二甲酸二异癸酯的加入对于聚氨酯材料弹性的影响;参看结果并与实施例1相比较可发现:没加邻苯二甲酸二异癸酯所制得的聚氨酯材料的弹性更差,说明邻苯二甲酸二异癸酯的加入有利于提高聚氨酯材料的弹性。以上均为本申请的较佳实施例,并非依此限制本申请的保护范围,故:凡依本申请的结构、形状、原理所做的等效变化,均应涵盖于本申请的保护范围之内。当前第1页12