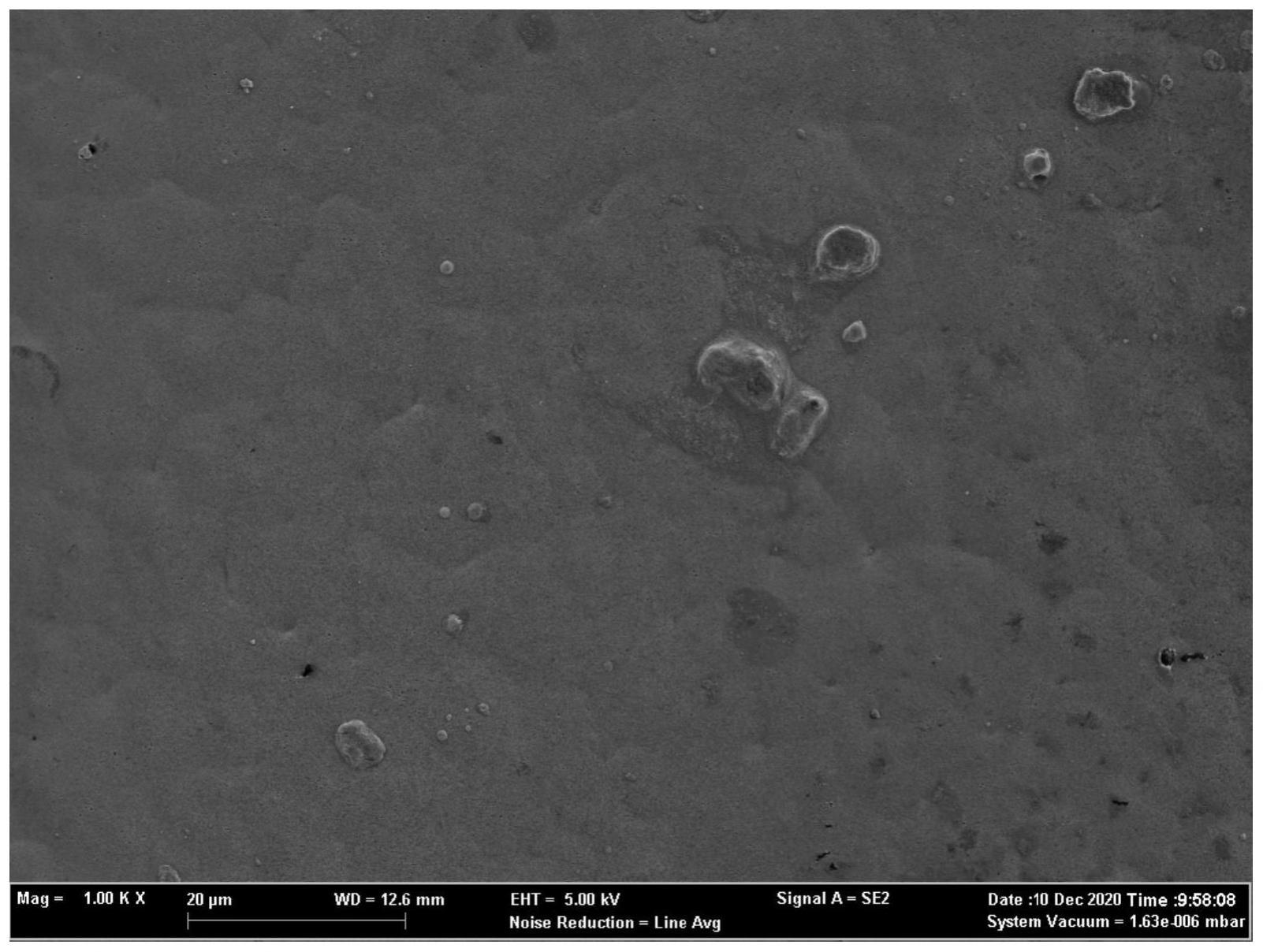
1.本发明属于电介质材料领域,具体涉及一种全有机复合材料薄膜及其制备方法和应用。
背景技术:2.近年来,随着电子电气工业的高性能需求和电子能源系统的不断发展,拥有纳米级充放电速率的、优异柔韧性和可加工性的、出色绝缘性能的金属化有机电介质薄膜电容器受到了广泛的关注和研究。目前,商用的双轴拉伸聚丙烯电容器(bopp)的能量密度通常低于3j/cm3,这限制了薄膜电容器在电气设备小型化要求下的应用。
3.目前,为提高薄膜电容器的能量密度,通常将具有高介电常数的陶瓷粒子或者导电粒子添加到聚合物基体中,聚合物基电介质复合材料的制备方法主要是溶液共混或者熔融共混法。
4.例如mojtaba rahimabady等人在“dielectric behaviors and high energy density of nanocomposites with core
‑
shell batio3@tio
2 in poly(vinylidene fluoride
‑
hexafluoropropylene”(《journal of materials chemistry c》,2013,15,16242)中将氧化钛(tio2)包覆的钛酸钡(batio3)添加到铁电聚合物(p(vdf
‑
hfp))基体内制备成复合材料。随着钛酸钡填料的添加,该复合材料的介电常数可以达到110,能量密度可以达到12.2j/cm3,但是复合材料的介电损耗会因为无机填料的添加而增加,这容易造成电容器充放电效率的降低。
5.又例如kuo han等人在“suppression of energy dissipation and enhancement of breakdown strength in ferroelectric polymer
‑
graphene percolative composites”(《journal of materials chemistry c》,2013,1,7034)一文中以铁电聚合物(p(vdf
‑
ctfe))为基体,以氧化硅包覆的石墨烯为无机分散相,采用溶液刮涂法制备了聚合物基介电复合材料。该复合材料中,当石墨烯填料为1.5vol%时,复合材料的介电常数在1000赫兹时可以达到65,但是击穿场强会随着导电填料的增加而显著降低。
6.但是目前报道的聚合物基电介质复合材料,无法满足高击穿强度、高能量密度、优异的力学性能、制备工艺简单等要求。因此,如何提高聚合物基电介质材料的绝缘性能与储能特性,并优化聚合物基复合材料的制备工艺,成为亟需解决的问题。
技术实现要素:7.本发明旨在至少在一定程度上解决相关技术中的技术问题之一。为此,本发明的一个目的在于提出一种全有机复合材料薄膜及其制备方法和应用。本发明以聚合物为基体,以有机填料为分散相,得到的全有机复合材料薄膜具有介电损耗较低、击穿强度较高、放电能量密度高、物理机械性能良好、电气绝缘性能高、制备工艺简单适合工业生产和工程应用等优点。
8.在本发明的一个方面,本发明提出了一种全有机复合材料薄膜,根据本发明的实
施例,所述全有机复合材料薄膜包括:聚合物基体和有机填料,所述聚合物基体为聚偏二氟乙烯
‑
co
‑
六氟丙烯,所述有机填料为甲基丙烯酸甲酯、丁二烯和苯乙烯的三元共聚物。
9.根据本发明实施例全有机复合材料薄膜,本发明以聚合物为基体,以有机填料为分散相,得到的全有机的聚合物基电介质复合材料薄膜具有介电损耗较低、击穿强度较高、放电能量密度高、物理机械性能良好、电气绝缘性能高、制备工艺简单适合工业生产和工程应用等优点。另外,本发明的全有机复合材料薄膜的制备原料易于获取,适合大批量生产。而现有的以无机陶瓷为填料的聚合物基电介质复合材料无法兼顾介电常数和绝缘性能,并且不适于大规模的工业化制备。
10.另外,根据本发明上述实施例全有机复合材料薄膜还可以具有如下附加的技术特征:
11.在本发明的一些实施例中,基于所述复合材料薄膜的总体积,所述聚合物基体的体积分数为90
‑
98%,所述有机填料的体积分数为2
‑
10%。
12.在本发明的一些实施例中,所述有机填料的粒径为1
‑
2μm。
13.在本发明的一些实施例中,所述复合材料薄膜的厚度为7
‑
12微米。
14.在本发明的再一个方面,本发明提出了一种制备上述全有机复合材料薄膜的方法。根据本发明的实施例,所述方法包括:
15.(1)将有机填料、聚合物基体和溶剂混合,搅拌,以便得到混合溶液;
16.(2)采用溶液刮涂的方法,将所述混合溶液旋涂于基板上,干燥,以便得到全有机复合材料薄膜。
17.根据本发明实施例的制备上述全有机复合材料薄膜的方法,本发明通过以聚合物为基体,以有机填料为分散相,采用溶液刮涂技术,制备得到的全有机的聚合物基电介质复合材料薄膜具有介电损耗较低、击穿强度较高、放电能量密度高、物理机械性能良好、电气绝缘性能高、制备工艺简单适合工业生产和工程应用等优点。另外,本发明的全有机复合材料薄膜的制备原料易于获取,制备工艺简单易行,适合大批量生产。而现有的以无机陶瓷为填料的聚合物基电介质复合材料无法兼顾介电常数和绝缘性能,并且不适于大规模的工业化制备。
18.另外,根据本发明上述实施例的制备上述全有机复合材料薄膜的方法还可以具有如下附加的技术特征:
19.在本发明的一些实施例中,步骤(1)包括:
20.(1
‑
1)将有机填料与第一溶剂混合,搅拌,超声,以便得到有机填料的分散液;
21.(1
‑
2)将聚合物基体与第二溶剂混合,搅拌,以便得到聚合物基体的溶液;
22.(1
‑
3)将所述有机填料的分散液与所述聚合物基体的溶液混合,搅拌,以便得到混合溶液。
23.在本发明的一些实施例中,在步骤(1
‑
1)中,所述有机填料与所述第一溶剂的体积比为1:(100
‑
500)。
24.在本发明的一些实施例中,在步骤(1
‑
1)中,所述第一溶剂选自n,n
‑
二甲基甲酰胺和n,n
‑
二甲基乙酰胺中的至少之一。
25.在本发明的一些实施例中,在步骤(1
‑
1)中,所述搅拌为45℃
‑
55℃下搅拌30
‑
60min。
26.在本发明的一些实施例中,所述超声的时间为30
‑
60min。
27.在本发明的一些实施例中,在步骤(1
‑
2)中,所述聚合物基体与所述第二溶剂的体积比为1:(10
‑
20)。
28.在本发明的一些实施例中,在步骤(1
‑
2)中,所述搅拌为45℃
‑
55℃下搅拌55
‑
65min。
29.在本发明的一些实施例中,在步骤(1
‑
2)中,所述第二溶剂选自n,n
‑
二甲基甲酰胺和n,n
‑
二甲基乙酰胺中的至少之一。
30.在本发明的一些实施例中,在步骤(1
‑
3)中,所述搅拌为45℃
‑
55℃下搅拌5
‑
6h。
31.在本发明的一些实施例中,在步骤(2)中,所述基板为玻璃基板。
32.在本发明的一些实施例中,在步骤(2)中,所述干燥为将旋涂后的基板置于电热恒温鼓风干燥箱中,在65
‑
75℃下恒温11
‑
13h。
33.在本发明的第三个方面,本发明提出一种电容器。根据本发明的实施例,所述电容器是采用以上实施例所述全有机复合材料薄膜或者以上实施例所述方法制备得到的全有机复合材料薄膜制备得到的。由此,所述电容器具有介电损耗较低、击穿强度较高、放电能量密度高、物理机械性能良好、电气绝缘性能高等优点。
34.本发明的附加方面和优点将在下面的描述中部分给出,部分将从下面的描述中变得明显,或通过本发明的实践了解到。
附图说明
35.本发明的上述和/或附加的方面和优点从结合下面附图对实施例的描述中将变得明显和容易理解,其中:
36.图1为实施例1制备得到的复合材料薄膜的断面电子显微镜(sem)照片。
37.图2为实施例1、2、3、4、5制备的复合材料薄膜室温下的介电常数与频率的关系图。
38.图3为实施例1、2、3、4、5制备的复合材料薄膜室温下的介电损耗与频率的关系图。
39.图4为实施例1、2、3、4、5制备的复合材料薄膜室温下的击穿强度与外加电场的关系图。
40.图5为实施例1、2、3、4、5制备的复合材料薄膜室温下的放电能量密度与外加电场的关系图。
具体实施方式
41.下面详细描述本发明的实施例,所述实施例的示例在附图中示出,其中自始至终相同或类似的标号表示相同或类似的元件或具有相同或类似功能的元件。下面通过参考附图描述的实施例是示例性的,旨在用于解释本发明,而不能理解为对本发明的限制。
42.在本发明的一个方面,本发明提出了一种全有机复合材料薄膜,根据本发明的实施例,所述全有机复合材料薄膜包括:聚合物基体和有机填料,所述聚合物基体为聚偏二氟乙烯
‑
co
‑
六氟丙烯p(vdf
‑
hfp),所述有机填料为甲基丙烯酸甲酯、丁二烯和苯乙烯的三元共聚物mbs。发明人发现,p(vdf
‑
hfp)作为聚合物基体,具有较高的介电常数,有利于提高薄膜电容器储存的能量密度,而添加mbs会使得复合材料的击穿强度和能量密度得到提高;且上述偏二氟乙烯
‑
co
‑
六氟丙烯与上述甲基丙烯酸甲酯、丁二烯和苯乙烯的三元共聚物的分
子链之间存在相互缠结,形成类似交联结构的共混聚合物,从而有利于提高全有机复合材料薄膜的击穿强度。由此,本发明以聚合物为基体,以有机填料为分散相,得到的全有机的聚合物基电介质复合材料薄膜具有介电损耗较低、击穿强度较高、放电能量密度高、物理机械性能良好、电气绝缘性能高、制备工艺简单适合工业生产和工程应用等优点。另外,本发明的全有机复合材料薄膜的制备原料易于获取,适合大批量生产。而现有的以无机陶瓷为填料的聚合物基电介质复合材料无法兼顾介电常数和绝缘性能,并且不适于大规模的工业化制备。
43.根据本发明的一个具体实施例,基于所述复合材料薄膜的总体积,所述聚合物基体的体积分数为90
‑
98%,所述有机填料的体积分数为2
‑
10%,发明人发现,如果有机填料的含量过少,会造成不能有效提高复合材料的击穿强度和能量密度;如果有机填料的含量过多,会造成会引入缺陷,反而会降低复合材料的击穿强度。
44.根据本发明的再一个具体实施例,所述有机填料的粒径为1
‑
2μm,由此,该粒径范围下,有机填料在基体中的相容性和分散性较好。发明人发现,如果有机填料的粒径过大,容易使得填料与基体之间产生缺陷;如果其粒径过小,则容易导致填料发生团聚,不利于填料在基体中的分散。
45.在本发明的实施例中,所述复合材料薄膜的具体厚度并不受特别限制,本领域人员可根据实际情况随意选择,作为一种优选的方案,所述复合材料薄膜的厚度为7
‑
12微米,由此满足实际生产需求。
46.在本发明的再一个方面,本发明提出了一种制备上述全有机复合材料薄膜的方法。根据本发明的实施例,所述方法包括:
47.s100:将有机填料、聚合物基体和溶剂混合,搅拌
48.在该步骤中,将有机填料、聚合物基体和溶剂混合,搅拌,以便得到混合溶液。在本发明的实施例中,将有机填料、聚合物基体和溶剂混合的具体方式并不受特别限制,例如可以将有机填料和聚合物基体分别溶解于溶剂,再将二者混合,也可以将有机填料和聚合物基体同时加入溶剂中混合。
49.根据本发明的又一个具体实施例,步骤s100包括如下步骤:
50.s110:将有机填料与第一溶剂混合,搅拌,超声
51.在该步骤中,将有机填料与第一溶剂混合,搅拌,超声,以便得到有机填料的分散液。
52.根据本发明的又一个具体实施例,所述有机填料与所述第一溶剂的体积比为1:(100
‑
500),由此,能够将有机填料充分地溶解在第一溶剂中。
53.在本发明的实施例中,所述第一溶剂的具体种类并不受特别限制,本领域人员可根据实际情况随意选择,作为一种优选的方案,所述第一溶剂选自n,n
‑
二甲基甲酰胺dmf和n,n
‑
二甲基乙酰胺dmac中的至少之一。
54.根据本发明的又一个具体实施例,所述搅拌为45℃
‑
55℃下搅拌30
‑
60min,由此,更好地将有机填料充分地溶解在第一溶剂中,形成分散溶液。
55.根据本发明的又一个具体实施例,所述超声的时间为30
‑
60min,由此,更好地将有机填料充分地溶解在第一溶剂中,形成分散溶液。
56.s120:将聚合物基体与第二溶剂混合,搅拌
57.在该步骤中,将聚合物基体与第二溶剂混合,搅拌,以便得到聚合物基体的溶液。
58.根据本发明的又一个具体实施例,所述聚合物基体与所述第二溶剂的体积比为1:(10
‑
20),由此,能够将聚合物基体充分地溶解在第二溶剂中。
59.在本发明的实施例中,所述第二溶剂的具体种类并不受特别限制,本领域人员可根据实际情况随意选择,作为一种优选的方案,所述第二溶剂选自n,n
‑
二甲基甲酰胺dmf和n,n
‑
二甲基乙酰胺dmac中的至少之一。
60.根据本发明的又一个具体实施例,所述搅拌为45℃
‑
55℃下搅拌55
‑
65min,由此,更好地将聚合物基体充分地溶解在第二溶剂中。
61.s130:将所述有机填料的分散液与所述聚合物基体的溶液混合,搅拌
62.在该步骤中,将所述有机填料的分散液与所述聚合物基体的溶液混合,搅拌,以便得到混合溶液。
63.根据本发明的又一个具体实施例,所述搅拌为45℃
‑
55℃下搅拌5
‑
6h,由此,更好地将有机填料的分散液与聚合物基体的溶液充分混合,形成混合溶液。
64.s200:采用溶液刮涂的方法,将所述混合溶液旋涂于基板上,干燥
65.在该步骤中,采用溶液刮涂的方法,将所述混合溶液旋涂于基板上,干燥,以便得到全有机复合材料薄膜。作为一个具体示例,将混合溶液倒在干净的玻璃基板上,采用溶液刮涂的方法,用刮刀制成相应厚度的薄膜。
66.根据本发明的又一个具体实施例,将薄膜放入电热恒温鼓风干燥箱中,在65
‑
75℃下恒温11
‑
13h,得到全有机的复合材料薄膜。
67.根据本发明实施例的制备上述全有机复合材料薄膜的方法,本发明通过以聚合物为基体,以有机填料为分散相,采用溶液刮涂技术,制备得到的全有机的聚合物基电介质复合材料薄膜具有介电损耗较低、击穿强度较高、放电能量密度高、物理机械性能良好、电气绝缘性能高、制备工艺简单适合工业生产和工程应用等优点。另外,本发明的全有机复合材料薄膜的制备原料易于获取,制备工艺简单易行,适合大批量生产。而现有的以无机陶瓷为填料的聚合物基电介质复合材料无法兼顾介电常数和绝缘性能,并且不适于大规模的工业化制备。
68.在本发明的第三个方面,本发明提出一种电容器。根据本发明的实施例,所述电容器是采用以上实施例所述全有机复合材料薄膜或者以上实施例所述方法制备得到的全有机复合材料薄膜制备得到的。由此,所述电容器具有介电损耗较低、击穿强度较高、放电能量密度高、物理机械性能良好、电气绝缘性能高等优点。
69.下面详细描述本发明的实施例,需要说明的是下面描述的实施例是示例性的,仅用于解释本发明,而不能理解为对本发明的限制。另外,如果没有明确说明,在下面的实施例中所采用的所有试剂均为市场上可以购得的,或者可以按照本文或已知的方法合成的,对于没有列出的反应条件,也均为本领域技术人员容易获得的。
70.实施例1
71.将0.0063g粒径为1
‑
2μm的mbs加入10ml dmf中,在50℃磁力搅拌30min后,再以400w的功率超声震荡30min,得到mbs的分散液;将0.5g p(vdf
‑
hfp)加入10ml dmf中,于50℃搅拌60min,得到p(vdf
‑
hfp)溶液;将二者混合后,于50℃下磁力搅拌5小时,得到混合溶液;而后采用溶液刮涂技术在玻璃板上涂覆薄膜,并于70℃下恒温12小时,得到mbs的体积
分数为2%,厚度为8μm的薄膜。如图1所示,该图中的颗粒状物质是mbs填料,从图1中可以看出,填料与基体之间没有产生团聚、微孔等缺陷,由此说明mbs填料在p(vdf
‑
hfp)基体内分散均匀。室温下的不同频率条件下的介电常数、介电损耗以及不同电场条件下的击穿场强、放电能量密度分别如图2、3、4、5中的曲线1。其中,图2、3、4、5中的曲线0表示纯p(vdf
‑
hfp)的性能。
72.实施例2
73.将0.0129g粒径为1
‑
2μm的mbs加入10ml dmf中,在50℃磁力搅拌30min后,再以400w的功率超声震荡30min,得到mbs的分散液;将0.5g p(vdf
‑
hfp)加入10ml dmf中,于50℃搅拌60min,得到p(vdf
‑
hfp)溶液;将二者混合后,于50℃下磁力搅拌5小时,得到混合溶液;而后采用溶液刮涂技术在玻璃板上涂覆薄膜,并于70℃下恒温12小时,得到mbs的体积分数为4%,厚度为8μm的薄膜。室温下的不同频率条件下的介电常数、介电损耗以及不同电场条件下的击穿场强、放电能量密度分别如图2、3、4、5中的曲线2。
74.实施例3
75.将0.0197g粒径为1
‑
2μm的mbs加入10ml dmf中,在50℃磁力搅拌30min后,再以400w的功率超声震荡30min,得到mbs的分散液;将0.5g p(vdf
‑
hfp)加入10ml dmf中,于50℃搅拌60min,得到p(vdf
‑
hfp)溶液;将二者混合后,于50℃下磁力搅拌5小时,得到混合溶液;而后采用溶液刮涂技术在玻璃板上涂覆薄膜,并于70℃下恒温12小时,得到mbs的体积分数为6%,厚度为9μm的薄膜。室温下的不同频率条件下的介电常数、介电损耗以及不同电场条件下的击穿场强、放电能量密度分别如图2、3、4、5中的曲线3。
76.实施例4
77.将0.0269g粒径为1
‑
2μm的mbs加入10ml dmf中,在50℃磁力搅拌30min后,再以400w的功率超声震荡30min,得到mbs的分散液;将0.5g p(vdf
‑
hfp)加入10ml dmf中,于50℃搅拌60min,得到p(vdf
‑
hfp)溶液;将二者混合后,于50℃下磁力搅拌5小时,得到混合溶液;而后采用溶液刮涂技术在玻璃板上涂覆薄膜,并于70℃下恒温12小时,得到mbs的体积分数为8%,厚度为9μm的薄膜。室温下的不同频率条件下的介电常数、介电损耗以及不同电场条件下的击穿场强、放电能量密度分别如图2、3、4、5中的曲线4。如图5所示,当mbs含量为8vo%时,复合薄膜材料的放电能量密度最大,能达到12.33j/cm3。
78.实施例5
79.将0.0343g粒径为1
‑
2μm的mbs加入10ml dmf中,在50℃磁力搅拌30min后,再以400w的功率超声震荡30min,得到mbs的分散液;将0.5g p(vdf
‑
hfp)加入10ml dmf中,于50℃搅拌60min,得到p(vdf
‑
hfp)溶液;将二者混合后,于50℃下磁力搅拌5小时,得到混合溶液;而后采用溶液刮涂技术在玻璃板上涂覆薄膜,并于70℃下恒温12小时,得到mbs的体积分数为10%,厚度为10μm的薄膜。室温下的不同频率条件下的介电常数、介电损耗以及不同电场条件下的击穿场强、放电能量密度分别如图2、3、4、5中的曲线5。如图2、3所示,随着复合材料的介电常数和介电损耗随着mbs的添加而逐渐降低,当mbs体积分数为10vol%时,复合材料表现出最低的介电常数和介电损耗。
80.从图2
‑
5中可以看出,本发明得到的全有机复合材料薄膜具有介电常数较低、介电损耗较低、击穿强度较高、放电能量密度高等优点。
81.在本说明书的描述中,参考术语“一个实施例”、“一些实施例”、“示例”、“具体示
例”、或“一些示例”等的描述意指结合该实施例或示例描述的具体特征、结构、材料或者特点包含于本发明的至少一个实施例或示例中。在本说明书中,对上述术语的示意性表述不必须针对的是相同的实施例或示例。而且,描述的具体特征、结构、材料或者特点可以在任一个或多个实施例或示例中以合适的方式结合。此外,在不相互矛盾的情况下,本领域的技术人员可以将本说明书中描述的不同实施例或示例以及不同实施例或示例的特征进行结合和组合。
82.尽管上面已经示出和描述了本发明的实施例,可以理解的是,上述实施例是示例性的,不能理解为对本发明的限制,本领域的普通技术人员在本发明的范围内可以对上述实施例进行变化、修改、替换和变型。