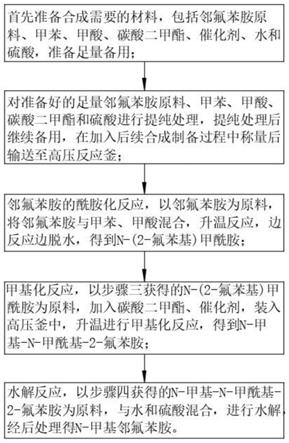
一种一锅法合成n
‑
甲基邻氟苯胺的方法
技术领域
1.本发明属于n
‑
甲基邻氟苯胺合成技术领域,更具体地说,尤其涉及一种一锅法合成n
‑
甲基邻氟苯胺的方法。
背景技术:2.n
‑
甲基邻氟苯胺属于含氟类n
‑
烷基芳胺,是一种非常重要的有机原料和精细化工中间体,广泛应用于燃料、塑料、医药和农药等领域,随着染料和橡胶工业的不断发展,农药、医药的用量液不断增加;一锅法,one
‑
potreaction是一种非常具有前景的有机合成方法,一锅法反应中的多步反应可以从相对简单易得的原料出发,不经中间体的分离,直接获得结构复杂的分子,这样的反应显然经济上和环境友好上较为有利。
3.n
‑
甲基邻氟苯胺的需求量迅速增长,与其相应的合成开发也备受关注,具体而言n
‑
甲基邻氟苯胺的合成方法有很多种,根据不同的反应路线,如下:
4.1、以邻氟苯胺为原料,与碳酸二甲基发生甲基化反应制得n
‑
甲基邻氟苯胺的方法。但是由于碳酸二甲酯属于甲基化比较容易的一种原料,实际上部分(84%)生成了二甲基取代的n,n
‑
二甲基邻氟苯胺,目标产物n
‑
甲基邻氟苯胺只有5%左右;
5.2、以邻氟苯胺为起始原料,在正丁基锂催化作用下,四氢呋喃为溶剂,与硫酸二甲酯发生甲基化反应制得n
‑
甲基邻氟苯胺的方法。该方法需要较低温
‑
78℃下进行,条件较为苛刻,硫酸二甲酯为第6.1类a级有机剧毒品,且正丁基锂使用需要无水无氧,安全隐患较大;
6.3、以邻氟苯胺为起始原料,以dmf为溶剂,在氢化钠催化作用下,邻氟苯胺与碘甲烷发生甲基化反应制得。该方法使用氢化钠,同样很不安全,且碘甲烷价格昂贵,原料成本居高不下,工业化应用较难,因此我们需要提出一种一锅法合成n
‑
甲基邻氟苯胺的方法。
技术实现要素:7.本发明的目的是为了解决现有技术中存在的缺点,而提出的一种一锅法合成n
‑
甲基邻氟苯胺的方法。
8.为实现上述目的,本发明提供如下技术方案:一种一锅法合成n
‑
甲基邻氟苯胺的方法,包括如下步骤:
9.步骤一、首先准备合成需要的材料,包括邻氟苯胺原料、甲苯、甲酸、碳酸二甲酯、催化剂、水和硫酸,准备足量备用;
10.步骤二、对准备好的足量邻氟苯胺原料、甲苯、甲酸、碳酸二甲酯和硫酸进行提纯处理,提纯处理后继续备用,在加入后续合成制备过程中称量后输送至高压反应釜;
11.步骤三、邻氟苯胺的酰胺化反应,以邻氟苯胺为原料,将邻氟苯胺与甲苯、甲酸混合,升温反应,边反应边脱水,得到n
‑
(2
‑
氟苯基)甲酰胺;
12.步骤四、甲基化反应,以步骤三获得的n
‑
(2
‑
氟苯基)甲酰胺为原料,加入碳酸二甲酯、催化剂,装入高压釜中,升温进行甲基化反应,得到n
‑
甲基
‑
n
‑
甲酰基
‑2‑
氟苯胺;
13.步骤五、水解反应,以步骤四获得的n
‑
甲基
‑
n
‑
甲酰基
‑2‑
氟苯胺为原料,与水和硫酸混合,进行水解,经后处理得n
‑
甲基邻氟苯胺。
14.优选的,所述的邻氟苯胺与甲酸的摩尔比为1:1.0~1.5,优选为1:1.3~1.5;所述的邻氟苯胺与甲苯的质量比为1:3.0~4.0,优选为1:3.5~4.0。
15.优选的,步骤五中,脱水的起始温度为88℃,持续升温至106℃~109℃,保温脱水,总脱水时间为5.5~7.5h。
16.优选的,酰胺化反应结束后,反应液降温至26~29℃,水洗涤至ph为6~7,分层,有机相减压蒸除甲苯,得到n
‑
(2
‑
氟苯基)甲酰胺。
17.优选的,步骤三中,酰胺化反应结束后,反应液降温至25~30℃,水洗涤至ph为6~7,分层,有机相减压蒸除甲苯,得到n
‑
(2
‑
氟苯基)甲酰胺。
18.优选的,步骤四中,所述的甲基化反应温度为120℃~140℃,反应压力为0.4~0.6mpa;所述n
‑
(2
‑
氟苯基)甲酰胺与碳酸二甲酯的摩尔比为1:3.0~5.0,优选为1:4.0~4.5。
19.优选的,步骤五中,以h2so4计,所述的n
‑
甲基
‑
n
‑
甲酰基
‑2‑
氟苯胺与硫酸的摩尔比为1:1.0~2.0,硫酸的含量为15%~20%;优选的,所述的n
‑
甲基
‑
n
‑
甲酰基
‑2‑
氟苯胺与硫酸的摩尔比为1:1.3~1.5,硫酸的含量为12%~15%。
20.优选的,步骤五的水解反应结束后,反应液降温至25~30℃,滴加10%氢氧化钠溶液调节ph为7~8,静置,分层,负压收集85~90℃(20mmhg)馏分,即为n
‑
甲基邻氟苯胺。
21.优选的,所述高压反应釜设置为磁力传动的带有聚四氟乙烯内衬的工业高压反应釜,所述高压反应釜包括电机减速机、磁力传动装置、封头、筒体、夹套与搅拌器。
22.优选的,所述高压反应釜的规格:容量500l
‑
5000l、转速为10
‑
800转/分钟、加热功率为0.9kw
‑
9kw、内部设计压力大于22mpa、内部最高反应温度大于350摄氏度。
23.本发明的技术效果和优点:本发明提供的一种一锅法合成n
‑
甲基邻氟苯胺的方法,与现有技术相比;
24.本发明通过邻氟苯胺的酰胺化反应,以邻氟苯胺为原料,将邻氟苯胺与甲苯、甲酸混合,升温反应,边反应边脱水,得到n
‑
(2
‑
氟苯基)甲酰胺;以获得的n
‑
(2
‑
氟苯基)甲酰胺为原料,加入碳酸二甲酯、催化剂,装入高压釜中,升温进行甲基化反应,得到n
‑
甲基
‑
n
‑
甲酰基
‑2‑
氟苯胺;以获得的n
‑
甲基
‑
n
‑
甲酰基
‑2‑
氟苯胺为原料,与水和硫酸混合,进行水解,经后处理得n
‑
甲基邻氟苯胺;同时对本反应所需的邻氟苯胺原料、甲苯、甲酸、碳酸二甲酯、催化剂、水和硫酸等原料进行预先提纯,从而保证后续一锅法合成n
‑
甲基邻氟苯胺的合成效率,本发明原料易得,原料成本较低,反应条件温和,方法绿色、安全,总收率高达90%,具有较大的工业化应用前景。
附图说明
25.图1为本发明一锅法合成n
‑
甲基邻氟苯胺的方法的方法流程图。
具体实施方式
26.为了使本发明的目的、技术方案及优点更加清楚明白,以下结合具体实施例,对本发明进行进一步详细说明。应当理解,此处所描述的具体实施例仅仅用以解释本发明,并不
用于限定本发明。基于本发明中的实施例,本领域普通技术人员在没有做出创造性劳动前提下所获得的所有其他实施例,都属于本发明保护的范围。
27.实施例一
28.一种一锅法合成n
‑
甲基邻氟苯胺的方法,包括如下步骤:
29.步骤一、首先准备合成需要的材料,包括邻氟苯胺原料、甲苯、甲酸、碳酸二甲酯、催化剂、水和硫酸,准备足量备用;
30.步骤二、对准备好的足量邻氟苯胺原料、甲苯、甲酸、碳酸二甲酯和硫酸进行提纯处理,提纯处理后继续备用,在加入后续合成制备过程中称量后输送至高压反应釜;
31.步骤三、邻氟苯胺的酰胺化反应,以邻氟苯胺为原料,将邻氟苯胺与甲苯、甲酸混合,升温反应,边反应边脱水,得到n
‑
(2
‑
氟苯基)甲酰胺;
32.步骤四、甲基化反应,以步骤三获得的n
‑
(2
‑
氟苯基)甲酰胺为原料,加入碳酸二甲酯、催化剂,装入高压釜中,升温进行甲基化反应,得到n
‑
甲基
‑
n
‑
甲酰基
‑2‑
氟苯胺;
33.步骤五、水解反应,以步骤四获得的n
‑
甲基
‑
n
‑
甲酰基
‑2‑
氟苯胺为原料,与水和硫酸混合,进行水解,经后处理得n
‑
甲基邻氟苯胺。
34.本发明通过邻氟苯胺的酰胺化反应,以邻氟苯胺为原料,将邻氟苯胺与甲苯、甲酸混合,升温反应,边反应边脱水,得到n
‑
(2
‑
氟苯基)甲酰胺;以获得的n
‑
(2
‑
氟苯基)甲酰胺为原料,加入碳酸二甲酯、催化剂,装入高压釜中,升温进行甲基化反应,得到n
‑
甲基
‑
n
‑
甲酰基
‑2‑
氟苯胺;以获得的n
‑
甲基
‑
n
‑
甲酰基
‑2‑
氟苯胺为原料,与水和硫酸混合,进行水解,经后处理得n
‑
甲基邻氟苯胺;同时对本反应所需的邻氟苯胺原料、甲苯、甲酸、碳酸二甲酯、催化剂、水和硫酸等原料进行预先提纯,从而保证后续一锅法合成n
‑
甲基邻氟苯胺的合成效率,本发明原料易得,原料成本较低,反应条件温和,方法绿色、安全,总收率高达90%,具有较大的工业化应用前景。
35.所述的邻氟苯胺与甲酸的摩尔比为1:1.0,优选为1:1.3;所述的邻氟苯胺与甲苯的质量比为1:3.0,优选为1:3.5;步骤五中,脱水的起始温度为88℃,持续升温至106℃,保温脱水,总脱水时间为5.5h;酰胺化反应结束后,反应液降温至26℃,水洗涤至ph为6,分层,有机相减压蒸除甲苯,得到n
‑
(2
‑
氟苯基)甲酰胺。
36.步骤三中,酰胺化反应结束后,反应液降温至25℃,水洗涤至ph为6,分层,有机相减压蒸除甲苯,得到n
‑
(2
‑
氟苯基)甲酰胺;步骤四中,所述的甲基化反应温度为120℃,反应压力为0.4mpa;所述n
‑
(2
‑
氟苯基)甲酰胺与碳酸二甲酯的摩尔比为1:3.0,优选为1:4.0。
37.步骤五中,以h2so4计,所述的n
‑
甲基
‑
n
‑
甲酰基
‑2‑
氟苯胺与硫酸的摩尔比为1:1.0,硫酸的含量为15%;所述的n
‑
甲基
‑
n
‑
甲酰基
‑2‑
氟苯胺与硫酸的摩尔比为1:1.3,硫酸的含量为12%;步骤五的水解反应结束后,反应液降温至25℃,滴加10%氢氧化钠溶液调节ph为7,静置,分层,负压收集85(20mmhg)馏分,即为n
‑
甲基邻氟苯胺。
38.所述高压反应釜设置为磁力传动的带有聚四氟乙烯内衬的工业高压反应釜,所述高压反应釜包括电机减速机、磁力传动装置、封头、筒体、夹套与搅拌器;所述高压反应釜的规格:容量500l
‑
5000l、转速为10
‑
800转/分钟、加热功率为0.9kw
‑
9kw、内部设计压力大于22mpa、内部最高反应温度大于350摄氏度,反应釜的材质为304、316l不锈钢;
39.本反应釜还配备有控温仪,控温仪实时显示转速、温度、工作时间、加热电压等,调节加热电压,温度及转速,标配pid;自动温度调节表,可自动恒温,可配套电机电流表,压力
数显表及上微机软件。控温仪的工作环境为:环境温度0
‑
50℃,相对湿度30
‑
85%,周围介质中不含导电尘埃及腐蚀气体。该反应釜的关键部件磁力耦合传动器是一种利用永磁材料进行耦合传动的传动装置,改变了传统机械密封和填料密封的那种通过轴套或填料密封搅拌轴的动密封结构为静密封结构,反应釜内介质完全处于由反应釜釜体与密封罩体构成的密封腔内,彻底解决了填料密封和机械密封因动密封而造成的无法克服的泄露问题,使反应介质绝无任何泄露和污染。
40.实施例二
41.与实施例一不同的是,所述的邻氟苯胺与甲酸的摩尔比为1:1.25,优选为1:1.3~1.5;所述的邻氟苯胺与甲苯的质量比为1:3.5,优选为1:3.75;步骤五中,脱水的起始温度为88℃,持续升温至107℃,保温脱水,总脱水时间为6h;酰胺化反应结束后,反应液降温至26~29℃,水洗涤至ph为6.5,分层,有机相减压蒸除甲苯,得到n
‑
(2
‑
氟苯基)甲酰胺。
42.步骤三中,酰胺化反应结束后,反应液降温至27℃,水洗涤至ph为6.5,分层,有机相减压蒸除甲苯,得到n
‑
(2
‑
氟苯基)甲酰胺;步骤四中,所述的甲基化反应温度为130℃,反应压力为0.5mpa;所述n
‑
(2
‑
氟苯基)甲酰胺与碳酸二甲酯的摩尔比为1:4.0,优选为1:4.25。
43.步骤五中,以h2so4计,所述的n
‑
甲基
‑
n
‑
甲酰基
‑2‑
氟苯胺与硫酸的摩尔比为1:1.5,硫酸的含量为17.5%;所述的n
‑
甲基
‑
n
‑
甲酰基
‑2‑
氟苯胺与硫酸的摩尔比为1:1.4,硫酸的含量为13.5%;步骤五的水解反应结束后,反应液降温至27.5℃,滴加10%氢氧化钠溶液调节ph为7.5,静置,分层,负压收集87.5℃(20mmhg)馏分,即为n
‑
甲基邻氟苯胺。
44.实施例三
45.与实施例一不同的是,所述的邻氟苯胺与甲酸的摩尔比为1:1.5,优选为1:1.5;所述的邻氟苯胺与甲苯的质量比为1:4.0,优选为1:4.0;步骤五中,脱水的起始温度为88℃,持续升温至109℃,保温脱水,总脱水时间为7.5h;酰胺化反应结束后,反应液降温至29℃,水洗涤至ph为7,分层,有机相减压蒸除甲苯,得到n
‑
(2
‑
氟苯基)甲酰胺。
46.步骤三中,酰胺化反应结束后,反应液降温至25~30℃,水洗涤至ph为7,分层,有机相减压蒸除甲苯,得到n
‑
(2
‑
氟苯基)甲酰胺;步骤四中,所述的甲基化反应温度为140℃,反应压力为0.6mpa;所述n
‑
(2
‑
氟苯基)甲酰胺与碳酸二甲酯的摩尔比为1:5.0,优选为1:4.5。
47.步骤五中,以h2so4计,所述的n
‑
甲基
‑
n
‑
甲酰基
‑2‑
氟苯胺与硫酸的摩尔比为1:2.0,硫酸的含量为20%;所述的n
‑
甲基
‑
n
‑
甲酰基
‑2‑
氟苯胺与硫酸的摩尔比为1:1.5,硫酸的含量为15%;步骤五的水解反应结束后,反应液降温至0℃,滴加10%氢氧化钠溶液调节ph为8,静置,分层,负压收集90℃(20mmhg)馏分,即为n
‑
甲基邻氟苯胺。
48.最后应说明的是:以上所述仅为本发明的优选实施例而已,并不用于限制本发明,尽管参照前述实施例对本发明进行了详细的说明,对于本领域的技术人员来说,其依然可以对前述各实施例所记载的技术方案进行修改,或者对其中部分技术特征进行等同替换,凡在本发明的精神和原则之内,所作的任何修改、等同替换、改进等,均应包含在本发明的保护范围之内。
49.步骤1中,还包括将所述吹扫料流和苯酚水进料料流引导至酚水分离单元,和分离废水料流、苯酚料流和回收的丙酮料流。
50.步骤1中,所述进料料流包含基于所述进料料流的总重量计97至99.5重量%,或98至99.5重量%的丙酮;所述进料料流包含基于所述进料料流的总重量计100至500ppm,或200至300ppm的甲醇。
51.实施例2
52.与实施例1不同的是,步骤3中,将计量好的丙酮缩氨基乙内酰脲40kg、甲醇钠180kg加入反应罐内,然后关闭进料阀门,开冷凝器、蒸汽、搅拌升温控制罐内温度在70℃,保温回流45分钟,使罐内丙酮缩氨基乙内酰脲全部溶解,开始加氯乙酸甲酯50kg,加毕,保温反应40分钟,关闭蒸汽阀门,打开夹套冷凝水阀门降温至50℃,开始滴加浓度为30%的盐酸65kg至ph=6,开蒸汽阀门,升温脱出水和反应生产的甲醇,先常压后减压蒸发至干,开夹套冷凝水降温至40℃以下,加入丙酮100kg,开动搅拌,升温到固体分散后,保温60分钟,保温结束,降温至50℃以下,放料甩滤,液相为丙酮缩氨基
‑1‑
氨基乙内酰脲溶液,将丙酮缩氨基
‑1‑
氨基乙内酰脲投入另一反应罐,加盐酸50kg,至ph=2保温回流60分钟,先常压后减压脱出水和反应生产的丙酮至干,得盐酸
‑1‑
氨基乙内酰脲。
53.最后应说明的是:以上所述仅为本发明的优选实施例而已,并不用于限制本发明,尽管参照前述实施例对本发明进行了详细的说明,对于本领域的技术人员来说,其依然可以对前述各实施例所记载的技术方案进行修改,或者对其中部分技术特征进行等同替换,凡在本发明的精神和原则之内,所作的任何修改、等同替换、改进等,均应包含在本发明的保护范围之内。