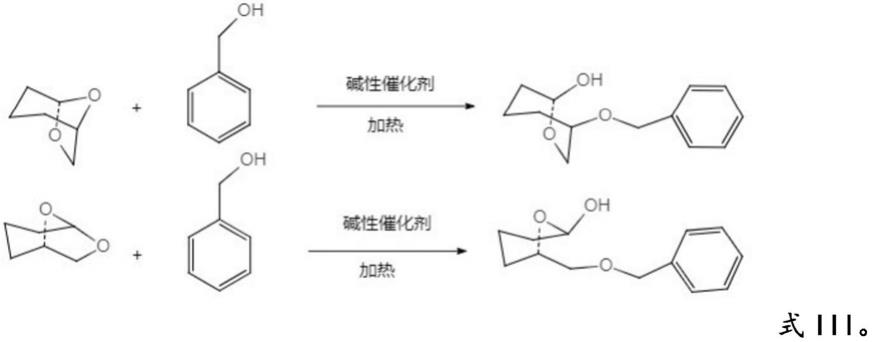
1.本发明涉及生产有机硅烷的副产物的处理方法,尤其涉及一种烯丙基缩水甘油醚异构体混合物的处理方法及应用。
背景技术:2.目前合成γ
‑
(2,3
‑
环氧丙氧基)丙基三甲氧基硅烷的产量越来越高,很多有机硅厂家采用烯丙基缩水甘油醚与三甲氧基氢硅烷加成的工艺合成γ
‑
(2,3
‑
环氧丙氧基)丙基三甲氧基硅烷。该合成工艺中,在铂催化剂的作用下,原料烯丙基缩水甘油醚很容易异构化,生成两种不同结构的烯丙基缩水甘油醚异构体(2,6
‑
氧桥氧杂环庚烷)。这两种异构体混合物的副产物处理也一直困扰着很多有机硅厂家。
3.烯丙基缩水甘油醚异构体在铂催化剂的作用下,烯丙基缩水甘油醚自身发生异构化,碳碳双键打开形成醚键。目前对烯丙基缩水甘油醚两种异构体混合物的副产物都是当废弃物处理,既浪费资源也污染环境。且在目前的公开报道中,还未涉及到副产物烯丙基缩水甘油醚异构体混合物的综合处理问题。
技术实现要素:4.为了克服现有技术不足,本发明的目的是提供一种可处理γ
‑
(2,3
‑
环氧丙氧基)丙基三甲氧基硅烷副产物的烯丙基缩水甘油醚异构体混合物的处理方法及应用。
5.本发明提供一种烯丙基缩水甘油醚异构体混合物的处理方法,将烯丙基缩水甘油醚异构体混合物与苯甲醇按质量比1~3∶1进行投料,再加入碱性催化剂,然后升温至60℃~100℃,保温反应4~8小时,反应结束,通过精馏除去杂质,得到含有6
‑
(苄基氧基)氧杂环庚
‑2‑
醇两种异构体的混合物;所述烯丙基缩水甘油醚异构体混合物由以下分子式i的化合物和分子式ii的化合物按任意比例混合而成:
[0006][0007]
本发明中,所述烯丙基缩水甘油醚异构体混合物与苯甲醇的反应分子式如下式iii所示:
[0008][0009]
本发明通过烯丙基缩水甘油醚的两种异构体(2,6
‑
氧桥氧杂环庚烷)混合物,与苯甲醇在碱性催化剂的作用下,发生开环反应,再经过精馏提纯,得到与两种原料异构体对应的两种不同的醚的混合物(6
‑
(苄基氧基)氧杂环庚
‑2‑
醇两种异构体的混合物)。
[0010]
进一步,所述烯丙基缩水甘油醚异构体混合物为γ
‑
(2,3)环氧丙氧基丙基三甲氧基硅烷合成时得到的副产物,所述烯丙基缩水甘油醚异构体混合物由分子式i的化合物和分子式ii的化合物按任意比例混合而成。所述分子式i的化合物和分子式ii的化合物的总含量为副产物质量的92%以上。由于本发明的所述烯丙基缩水甘油醚异构体混合物为γ
‑
(2,3)环氧丙氧基丙基三甲氧基硅烷合成时得到的副产物,因此,本发明的处理方法可实现对γ
‑
(2,3)环氧丙氧基丙基三甲氧基硅烷合成副产物的有效处理,解决了现有γ
‑
(2,3)环氧丙氧基丙基三甲氧基硅烷合成过程中副产物污染环境的问题,及副产物处理成本高的问题。
[0011]
优选的,所述烯丙基缩水甘油醚异构体混合物与苯甲醇的质量比2∶1。
[0012]
进一步,所述碱性催化剂为季胺化合物或叔胺化合物中的一种或两种的混合物。采用季胺化合物或叔胺化合物可以催化烯丙基缩水甘油醚异构体中的氧杂环开环,且碱性适中,不会过度催化,导致烯丙基缩水甘油醚异构体开环后爆聚。
[0013]
优选的,所述碱性催化剂为四甲基氢氧化铵或三乙胺中的一种或两种的混合物。采用这两种催化剂,不仅催化效果适中,且在后处理中较易除去,四甲基氢氧化铵在120℃可直接分解,三乙胺沸点较低,可以在精馏操作中去除。
[0014]
进一步,所述碱性催化剂的投量为烯丙基缩水甘油醚异构体混合物和苯甲醇投量质量总和的1
‰
~1%。优选的,所述碱性催化剂的投量为烯丙基缩水甘油醚异构体混合物和苯甲醇投量质量总和的5
‰
。
[0015]
优选的,所述反应温度为80℃。
[0016]
本发明还公开了上述处理方法所得产物的应用,所述处理方法得到的产物为6
‑
(苄基氧基)氧杂环庚
‑2‑
醇两种异构体的混合物应用为环氧树脂稀释剂。
[0017]
现有技术中采用苯甲醇作为环氧树脂做增塑剂,但由于苯甲醇中存在活性羟基,催化活性较高,导致环氧树脂与固化剂反应速率过快,不宜施工使用。本发明处理方法得到的6
‑
(苄基氧基)氧杂环庚
‑2‑
醇两种异构体的混合物,由于每种6
‑
(苄基氧基)氧杂环庚
‑2‑
醇异构体中含有两个醚键,与环氧树脂有更好的相容性。同时,由于6
‑
(苄基氧基)氧杂环庚
‑2‑
醇异构体中也存在羟基,但是其羟基的反应活性没有苯甲醇高。因此,本发明处理方
法得到的6
‑
(苄基氧基)氧杂环庚
‑2‑
醇两种异构体的混合物作为环氧树脂的稀释剂使用时,可控制固化时间在10
‑
15分钟左右,相对苯甲醇适当地延长了固化时间,方便施工控制;同时固化时间又不会过长,从而影响固化效率。因此,本发明制备得到的6
‑
(苄基氧基)氧杂环庚
‑2‑
醇两种异构体的混合物非常适合作为环氧树脂稀释剂在施工过程使用。
[0018]
本发明的有益效果为:本发明的处理方法可实现对γ
‑
(2,3)环氧丙氧基丙基三甲氧基硅烷合成副产物的有效处理,解决了现有γ
‑
(2,3)环氧丙氧基丙基三甲氧基硅烷合成副产物污染环境,及处理成本高的问题。因此,本发明的处理方法具有环保、降低γ
‑
(2,3)环氧丙氧基丙基三甲氧基硅烷合成成本等优点。
[0019]
同时,本发明的处理方法得到的6
‑
(苄基氧基)氧杂环庚
‑2‑
醇两种异构体的混合物可作为环氧树脂稀释剂,应用于施工中,实现资源的合理利用。
具体实施方式
[0020]
实施例1
[0021]
准确称取烯丙基缩水甘油醚两种异构体混合物100g,50g苯甲醇,0.75g三乙胺催化剂,投入带搅拌器、温度计和球型冷凝管的三口烧瓶中,升温搅拌至80℃,保温反应6小时左右,取样分析,得到的粗品中,6
‑
(苄基氧基)氧杂环庚
‑2‑
醇两种异构体的混合物含量可以达到70%(有两个峰,异构体)。将得到的粗品进行精馏处理,得到6
‑
(苄基氧基)氧杂环庚
‑2‑
醇两种异构体的混合物,含量达到90%左右,其中含有5%左右的苯甲醇。
[0022]
其中,所述烯丙基缩水甘油醚异构体混合物由以下分子式i的化合物和分子式ii的化合物按任意比例混合而成:
[0023][0024]
实施例2
[0025]
准确称取烯丙基缩水甘油醚两种异构体混合物100g,50g苯甲醇,0.75g四甲基氢氧化铵催化剂,投入带搅拌器、温度计和球型冷凝管的三口烧瓶中,升温搅拌至80℃,保温反应6小时左右,取样分析,得到的粗品中,6
‑
(苄基氧基)氧杂环庚
‑2‑
醇两种异构体的混合物含量达到71%(有两个峰,异构体)。将得到的粗品进行精馏处理,得到6
‑
(苄基氧基)氧杂环庚
‑2‑
醇两种异构体的混合物含量达到91%左右,其中含有4.5%左右的苯甲醇。
[0026]
实施例3
[0027]
准确称取烯丙基缩水甘油醚两种异构体混合物50g,50g苯甲醇,0.05g四甲基氢氧化铵催化剂,投入带搅拌器、温度计和球型冷凝管的三口烧瓶中,升温搅拌至100℃,保温反应4小时左右,取样分析,得到的粗品中,6
‑
(苄基氧基)氧杂环庚
‑2‑
醇两种异构体的混合物含量可以达到73%(有两个峰,异构体)。将得到的粗品进行精馏处理,得到6
‑
(苄基氧基)氧杂环庚
‑2‑
醇两种异构体的混合物含量达到90.2%左右,其中含有5.5%左右的苯甲醇。
[0028]
实施例4
[0029]
准确称取烯丙基缩水甘油醚两种异构体混合物100g,50g苯甲醇,1.5g四甲基氢氧化铵催化剂,投入带搅拌器、温度计和球型冷凝管的三口烧瓶中,升温搅拌至60℃,保温反应8小时左右,取样分析,得到的粗品中,6
‑
(苄基氧基)氧杂环庚
‑2‑
醇两种异构体的混合物
含量可以达到70.0%(有两个峰,异构体)。将得到的粗品进行精馏处理,得到6
‑
(苄基氧基)氧杂环庚
‑2‑
醇两种异构体的混合物含量达到90%左右,其中含有4.1%左右的苯甲醇。
[0030]
实施例5
[0031]
准确称取烯丙基缩水甘油醚两种异构体混合物150g,50g苯甲醇,1.0g四甲基氢氧化铵催化剂,投入带搅拌器、温度计和球型冷凝管的三口烧瓶中,升温搅拌至80℃,保温反应6小时左右,取样分析,得到的粗品中,6
‑
(苄基氧基)氧杂环庚
‑2‑
醇两种异构体的混合物含量可以达到70.5%(有两个峰,异构体)。将得到的粗品进行精馏处理,得到6
‑
(苄基氧基)氧杂环庚
‑2‑
醇两种异构体的混合物含量达到91%左右,其中含有4.3%左右的苯甲醇。
[0032]
实施例6
[0033]
凝胶现象是指树脂固化过程中树脂失去原有的流动性,表明树脂线性和支链结构转变为体型结构的开始。树脂从配好至凝胶这段时间称为树脂的适用期,根据不同的需要和条件,控制一定的适用期是树脂施工工艺中的重要问题。
[0034]
称取100g环氧树脂,加入20g实施例1中得到的6
‑
(苄基氧基)氧杂环庚
‑2‑
醇两种异构体的混合物,使用10.74g三乙烯四胺固化剂,搅拌均匀后,在80摄氏度下进行固化反应,其固化时间为10min。
[0035]
实施例7
[0036]
称取100g环氧树脂,加入20g实施例2中得到的6
‑
(苄基氧基)氧杂环庚
‑2‑
醇两种异构体的混合物,使用10.74g三乙烯四胺固化剂,搅拌均匀后,在80摄氏度下进行固化反应,其固化时间为12min。
[0037]
实施例8
[0038]
称取100g环氧树脂,加入20g实施例4中得到的6
‑
(苄基氧基)氧杂环庚
‑2‑
醇两种异构体的混合物,使用22.5g低分子量聚酰胺固化剂,搅拌均匀后,在80摄氏度下进行固化反应,其固化时间为13min。
[0039]
实施例9
[0040]
称取100g环氧树脂,加入20g实施例5中得到的6
‑
(苄基氧基)氧杂环庚
‑2‑
醇两种异构体的混合物,使用22.5g低分子量聚酰胺固化剂,搅拌均匀后,在80摄氏度下进行固化反应,其固化时间为11min。
[0041]
实施例10
[0042]
称取100g环氧树脂,加入20g实施例3中得到的6
‑
(苄基氧基)氧杂环庚
‑2‑
醇两种异构体的混合物,使用10.74g三乙烯四胺固化剂,搅拌均匀后,在80摄氏度下进行固化反应,其固化时间为13min。
[0043]
实施例11
[0044]
称取100g环氧树脂,加入20g苯甲醇,使用10.74g三乙烯四胺固化剂,搅拌均匀后,在80摄氏度下进行固化反应,其固化时间为3min。
[0045]
实施例12
[0046]
称取100g环氧树脂,加入20g苯甲醇,使用22.5g低分子量聚酰胺固化剂,搅拌均匀后,在80摄氏度下进行固化反应,其固化时间为4min。
[0047]
根据上述实施例可以看出,实施例11和实施例12采用苯甲醇作为环氧树脂的稀释剂,固化时间为3
‑
4分钟,固化速度过快,不利于固化过程的控制。采用本发明实施例1
‑
5处
理方法得到的6
‑
(苄基氧基)氧杂环庚
‑2‑
醇两种异构体的混合物,对应采用6
‑
10的应用方法,作为环氧树脂的稀释剂,固化时间为10
‑
13分钟,固化速度适中,方便固化过程的控制,适合用于施工使用。
[0048]
需要说明的是,尽管在本文中已经对上述各实施例进行了描述,但并非因此限制本发明的专利保护范围。因此,基于本发明的创新理念,对本文所述实施例进行的变更和修改,或利用本发明说明书内容所作的等效结构或等效流程变换,直接或间接地将以上技术方案运用在其他相关的技术领域,均包括在本发明的专利保护范围之内。