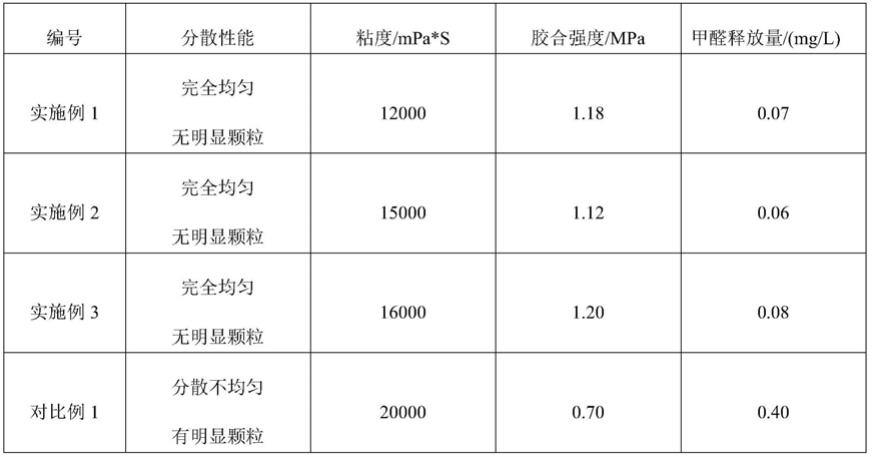
1.本发明具体涉及一种原料组合物、增粘剂及其制备方法、应用、调和胶。
背景技术:2.2019年,全国人造板工业用甲醛胶黏剂消耗量为1518万吨(固体含量100%),约占木材工业用胶黏剂消耗量85.6%。胶黏剂的种类有很多种,主要包括白乳胶、淀粉胶黏剂、水玻璃、酚醛树脂胶黏剂、脲醛树脂胶黏剂、聚乙烯醇胶黏剂等。其中,酚醛树脂胶黏剂由于其胶接强度高,耐热、耐老化、耐水、耐化学介质、耐霉菌、耐沸水等性能好,以及尺寸稳定性好、电绝缘性能优良等特性,广泛应用于胶合板的制造,木材与塑料、橡胶和金属的粘结,以及汽车和飞机工业中。
3.纸浆造纸行业是我国污染较重的行业之一,每年产量大量的废弃物,如腐浆、浆渣、树皮、药剂废液、草末、制浆废液等,这些废弃物没有很好的处理方式,大多采用焚烧处理。但是焚烧仅实现了废弃物热值的回收利用,且焚烧过程中很容易产生新的污染,没有真正实现造纸废弃物的综合利用,仅是作为废弃物的处理方式。
4.将造纸废弃物用作胶黏剂的增粘剂,现有技术有一些研究。例如中国专利文献cn111704873a公开了一种脲醛树脂添加剂及其制备方法,其将造纸废弃物代替面粉用于脲醛树脂胶黏剂的增粘剂,既降低了成本又提高了胶合板的胶合强度、降低了甲醛释放量。但是其利用造纸废弃物制得的增粘剂只适用于酸性环境的脲醛树脂,应用于酚醛树脂或生物基无醛胶等碱性树脂中会出现分散效果差、流动性差、黏度不均匀和结块等现象,严重影响涂胶机的涂胶过程,同时胶合强度有待进一步提高,甲醛释放量有待进一步降低。
技术实现要素:5.本发明解决的技术问题在于克服了现有技术中造纸废弃物制得的胶黏剂增粘剂用于碱性树脂中会出现分散效果差、流动性差、黏度不均匀和结块等现象,严重影响涂胶机的涂胶过程,以及胶合强度低、甲醛释放量高的缺陷,提供了一种原料组合物、增粘剂及其制备方法、调和胶。本发明的增粘剂在碱性胶黏剂中分散性好,能与碱性胶黏剂完全混合均匀、无明显颗粒,便于涂胶;同时,所得调和胶的胶合强度明显提高、甲醛释放量明显降低。
6.本发明采用以下技术方案解决上述技术问题:
7.本发明提供了一种原料组合物,其包括如下重量份数的各组分:造纸废弃物100~150份,交联剂1~30份,碱性催化剂1~6份和溶剂200~500份。
8.本发明中,所述造纸废弃物可为本领域常规,较佳地为腐浆干粉、浆渣干粉、造纸废弃木皮干粉、药剂废液干粉、草末干粉和造纸废液干粉中的一种或多种,更佳地为造纸废弃木皮干粉、草末干粉或制浆废液干粉。本发明中,所述交联剂可为本领域常规的能与所述造纸废弃物发生聚合反应的化合物,较佳地为乌洛托品、甲醛、聚乙烯醇、亚硫酸钠、亚硫酸氢钠和亚硫酸钠中的一种或多种,更佳地为亚硫酸钠和聚乙烯醇的混合物、亚硫酸氢钠和甲醛的混合物或乌洛托品和亚硫酸钠的混合物。
9.其中,当所述交联剂为亚硫酸钠和聚乙烯醇的混合物时,所述亚硫酸钠和所述聚乙烯醇的质量比可为本领域常规,较佳地为1:(0.3~3),例如1:0.5、1:1或1:2。
10.其中,当所述交联剂为亚硫酸氢钠和甲醛的混合物时,所述亚硫酸氢钠和所述甲醛的质量比可为本领域常规,较佳地为100:(30~50),例如100:37。
11.其中,当所述交联剂为乌洛托品和亚硫酸钠的混合物时,所述乌洛托品和所述亚硫酸钠的质量比可为本领域常规,较佳地为1:(0.3~3),例如1:0.5、1:1或1:2。
12.其中,当所述交联剂为甲醛时,所述交联剂一般以甲醛溶液的形式添加。所述甲醛溶液的质量浓度可为本领域常规,较佳地为(30~50)%,例如37%。
13.本发明中,所述碱性催化剂可为本领域常规的碱性化合物,较佳地为强碱,更佳地为氢氧化钠、氢氧化钾和氢氧化钡中的一种或多种。
14.本发明中,所述溶剂可为本领域常规的能溶解所述造纸废弃物、所述交联剂和所述碱性催化剂的溶剂即可,较佳地为水。
15.本发明中,所述交联剂较佳地为10~20份,更佳地为10~15份,例如13.7份。
16.本发明中,所述碱性催化剂较佳地为2~4份,例如3份。
17.本发明中,所述溶剂较佳地为250~400份,例如300份。
18.本发明中,所述原料组合物较佳地包括所述造纸废弃物100~150份、所述交联剂10~15份、所述碱性催化剂2~3份和所述溶剂250~400份。
19.本发明某一较佳实施例中,所述原料组合物包括造纸废弃木皮干粉100份、亚硫酸钠5份、聚乙烯醇5份、氢氧化钾2份和水250份。
20.本发明某一较佳实施例中,所述原料组合物包括草末干粉150份、水300g、亚硫酸氢钠10份、甲醛3.7份和氢氧化钠2份。
21.本发明某一较佳实施例中,所述原料组合物包括造纸废液干粉100份、水400份、乌洛托品5份、亚硫酸钠5份和氢氧化钡3份。
22.本发明还提供一种增粘剂的制备方法,其包括如下步骤:如上所述的原料组合物进行反应,即得;所述反应的温度为80~120℃,所述反应的时间为50~120min。
23.本发明中,所述反应的温度较佳地为85~95℃,例如90℃。
24.本发明中,所述反应的时间较佳地为60~90min,例如80min。
25.本发明的某一较佳实施例中,所述反应的温度为85℃,所述反应的时间为60min。
26.本发明的某一较佳实施例中,所述反应的温度为90℃,所述反应的时间为90min。
27.本发明的某一较佳实施例中,所述反应的温度为70℃,所述反应的时间为80min。
28.本发明中,较佳地,所述造纸废弃物和所述溶剂的混合物先预热至40~80℃,与所述交联剂和所述碱性催化剂混合,再加热至所述反应的温度。
29.本发明中,所述反应较佳地还包括搅拌。
30.其中,所述搅拌的转速可为本领域常规,较佳地为150~300r/min。
31.本发明中,所述反应结束后,较佳地还包括干燥步骤。
32.其中,所述干燥可采用本领域常规的方法进行,较佳地为喷雾干燥。
33.其中,所述干燥前物料的温度可为本领域常规,较佳地为30~50℃,更佳地为40~45℃。
34.本发明还提供一种由上述制备方法制得的增粘剂。
35.本发明还提供一种如上所述的增粘剂在调和胶中的应用。
36.本发明还提供一种调和胶,其包括如上所述的增粘剂和碱性胶黏剂。
37.本发明中,所述碱性胶黏剂可为本领域常规,较佳地为酚醛树脂或生物基胶黏剂胶。
38.其中,所述生物基胶黏剂较佳地为木质素基木材胶黏剂。
39.本发明中,所述增粘剂与所述碱性胶黏剂的质量比较佳地为(25~50):100,更佳地为30:100,其中,所述碱性胶黏剂的质量为湿重。
40.本发明还提供一种如上所述的调和胶的制备方法,其包括如下步骤:所述增粘剂和所述碱性胶黏剂进行混合即可。
41.本发明中,所述混合可采用本领域常规的方法进行,一般地在搅拌器中进行搅拌即可。
42.其中,所述搅拌器可为本领域常规,较佳地为高速搅拌器。
43.其中,所述搅拌的转速可为本领域常规,较佳地为100~150r/min,例如120r/min。
44.其中,所述搅拌的时间可为本领域常规,一般不小于20min,较佳地为25~60min,例如30min。
45.在符合本领域常识的基础上,上述各优选条件,可任意组合,即得本发明各较佳实例。
46.本发明还提供一种胶合板,其包括如上所述的调和胶和单板。
47.本发明中,所述调和胶在所述单板的上胶量为350~450g/m2。
48.本发明中,所述单板的制备方法可为本领域常规,一般地可为木段旋切而成或由木方刨切而成。
49.本发明中,所述单板的数目可为本领域常规,较佳地为奇数,更佳地为3或5。
50.本发明中,所述单板的材质可为本领域常规,较佳地为杨木、松木或桉木。
51.本发明所用试剂和原料均市售可得。
52.本发明的积极进步效果在于:
53.(1)本发明的增粘剂可以替代面粉作为增粘剂应用到胶黏剂中,既实现了生物质资源的高效利用,同时降低了胶料的成本;
54.(2)本发明的增粘剂能在碱性胶黏剂中有良好的分散性能,实现混合均匀,无明显颗粒,便于施胶;
55.(3)本发明的胶料能明显提升胶合强度,增粘剂添加比例为30%时,酚醛树脂胶合板的强度可均大于1.12mpa,甚至高达1.20mpa;木质素基木材胶黏剂胶合板的强度可均大于1.16mpa,甚至高达1.23mpa;
56.(4)本发明的胶料能明显降低甲醛释放量,增粘剂添加比例为30%时,本发明的酚醛树脂胶合板的甲醛释放量可均小于0.08mg/l,甚至低至0.06mg/l,木质素基木材胶黏剂胶合板的甲醛释放量可均小于0.04mg/l。
具体实施方式
57.下面通过实施例的方式进一步说明本发明,但并不因此将本发明限制在所述的实施例范围之中。下列实施例中未注明具体条件的实验方法,按照常规方法和条件,或按照商
品说明书选择。
58.实施例1~3所用的造纸废弃木皮干粉、草末干粉和造纸废液干粉均由济宁比奥新材料有限公司提供。
59.实施例1
60.原料组合物:造纸废弃木皮干粉100g,去离子水250g,亚硫酸钠5g,聚乙烯醇5g,氢氧化钾2g。
61.增粘剂的制备步骤如下:
62.1)造纸废弃木皮干粉100g、去离子水250g加入釜底升温至50℃,加入交联剂亚硫酸钠5g,聚乙烯醇5g,氢氧化钾2g升温至85℃,保温60min。
63.2)降温至40℃,经喷雾干燥后制得增粘剂。
64.实施例2
65.原料组合物:草末干粉150g,去离子水300g,亚硫酸氢钠10g,甲醛(37%)10g,氢氧化钠2g。
66.增粘剂制备步骤如下:
67.1)将草末干粉150g、去离子水300g加入釜底升温至60℃,加入交联剂亚硫酸氢钠10g,甲醛(37%)10g,氢氧化钠2g升温至90℃,保温90min;
68.2)降温至40℃,经喷雾干燥后制得增粘剂。
69.实施例3
70.原料组合物:造纸废液干粉100g,去离子水400g,乌洛托品5g,亚硫酸钠5g,氢氧化钡3g。
71.增粘剂制备步骤如下:
72.1)将造纸废液干粉100g、去离子水400g加入釜底升温至70℃,加入交联剂乌洛托品5g,亚硫酸钠5g,氢氧化钡3g升温至95℃,保温80min。
73.2)降温至45℃,经喷雾干燥后制得增粘剂。
74.对比例1
75.按照中国专利文献cn111704873a公开的实施例2制备对比例所用的脲醛树脂增粘剂。具体步骤如下:
76.1)将制浆废液干粉100g、去离子水300g加入釜底升温至65℃,加入交联剂亚硫酸钠10g,甲醛3.7g,升温至90℃,保温70min;
77.2)降温至80℃,加入甲酸0.6g,升温至95℃,保温10min;
78.3)二次降温至40℃,加入甲酸0.4g,经喷雾干燥后制得对比例产品。
79.效果实施例1
80.实施例1~3和对比例1所得的增粘剂分别与酚醛树脂按质量比30:100的比例在高速搅拌器中以120r/min的转速搅拌30min进行混合,混合均匀后得调和胶。以杨木板作为单板,调和胶的上胶量为350g/m2,制成五层胶合板。采用gb 9846.12
‑
1988《胶合板胶合强度的测定》的方法测定12个胶合板样品的强度,取平均值作为胶合强度;采用gb18580
‑
2017《室内装饰装修材料人造板及其制品中甲醛释放量》的方法测定胶合板样品的甲醛释放量,结果如表1所示。
81.效果实施例2
82.将效果实施例1的酚醛树脂改为木质素基木材胶黏剂,其他均与效果实施例1相同,结果如表2所示。
83.表1酚醛树脂胶合板指标检测结果
[0084][0085]
表2木质素基木材胶黏剂胶合板指标检测结果
[0086][0087][0088]
从表1和表2的测试结果可以看出:本发明制得的增粘剂添加到酚醛树脂和木质素基木材胶黏剂中能实现混合完全均匀,无明显颗粒,分散性能明显优于对比例所得增粘剂。
[0089]
本发明的增粘剂与酚醛树脂或木质素基木材胶黏剂混合后制作的胶合板的强度有明显提升。在增粘剂添加比例为30%时,酚醛树脂胶合板的强度均大于1.12mpa,实施例3高达1.20mpa,对比例1仅为0.7mpa;木质素基木材胶黏剂胶合板的强度均大于1.16mpa,实施例3高达1.23mpa,对比例1仅为0.86mpa。
[0090]
本发明的增粘剂还能明显降低胶合板的甲醛释放量。在增粘剂添加比例为30%时,本发明的酚醛树脂胶合板的甲醛释放量可均小于0.08mg/l,对比例1的酚醛树脂胶合板的甲醛释放量为0.40mg/l;木质素基木材胶黏剂胶合板的甲醛释放量可均小于0.04mg/l,
对比例的木质素基木材胶黏剂胶合板的甲醛释放量为0.09mg/l。
[0091]
综上,本发明制得的增粘剂既达到生物质资源高效利用的目的,并且生产的胶合板胶合强度高、甲醛释放量低,在酚醛树脂或木质素基木材胶黏剂中分散性能良好,便于施胶。