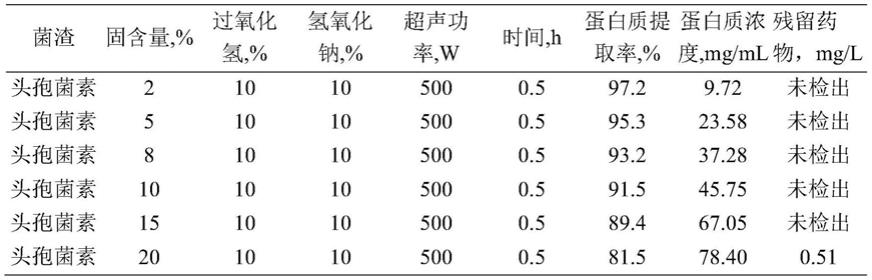
1.本发明涉及固体废弃物资源化利用领域,尤其是涉及一种利用生物医药发酵菌渣回收生物源蛋白的方法。
背景技术:2.生物发酵技术在医药行业应用广泛,菌渣是发酵行业最大的废弃物类别。据统计,我国每年生物医药发酵菌渣的产生量就达到150万吨。菌渣中含有丰富的单细胞蛋白,以干重计蛋白质含量可达42%~75%。国内外对于医药菌渣的无害化和资源化技术开展了大量深入的研究,目前生物医药菌渣资源化途径主要有能源化、原料化及肥料化途径,但在资源化应用过程中,其中丰富的蛋白组分大部分被降解,利用效率低,造成资源的浪费。生物医药发酵菌渣废弃物含有丰富的有机蛋白组分,可回收生物源蛋白,制备低成本、高纯度的生物源蛋白产品。
3.关于蛋白质物化法提取技术主要分为碱法提取和酸法提取,目前主要是是污水处理剩余污泥中蛋白质的提取,在专利cn109400671a“一种剩余污泥中提取微生物蛋白的方法”中介绍了碱性低温水解剩余污泥制备蛋白质,属于污泥处理技术领域,包括预处理单元、水解单元、固液分离单元、浓缩单元、树脂提取单元和收集单元。具体步骤如下:预处理加水调浆,在高温110~130℃条件下,ph值为8.5~11.5,处理4~6h后固液分离获得滤液,活性炭吸附后,滤液浓缩,浓缩后采用大孔阴离子交换树脂提取后洗脱,洗脱液再浓缩4-10倍,获得蛋白浓缩液。蛋白质水解提取率最高为63.58%,最终蛋白质回收率低,仅30%。
4.在专利cn106749506a“一种从土霉素菌渣中提取蛋白质的方法”中介绍了一种用酸/热联合法破碎消化土霉素菌渣提取蛋白质的方法。该方法包括以下步骤:土霉素菌渣搅匀均质预处理、酸-热联合处理土霉素菌渣、溶解性蛋白质提取液分离、等电点法沉淀蛋白质和蛋白质的分离。调节土霉素菌渣的含水率为94wt%,放入打浆机中搅拌5~10分钟;调节预处理后菌渣溶液的ph至2,搅拌均匀后放入恒温反应器,120℃条件下反应时间2h;提取液固液离心分离,去除残渣获得蛋白质提取液;调节提取液ph至6,反应沉淀时间5~10分钟;将沉淀后蛋白质提取液放入离心机分离后干燥沉淀物。土霉素菌渣中粗蛋白含量约45%,按照94%的含水率,获得6376.93mg/l的提取液,蛋白质溶出率小于30%,按照最大沉淀效率92.73%,回收率约为27%。
5.生物医药发酵菌渣与剩余污泥理化性质具有明显差别,且含有残留药物,目前提取难度极大。在现有技术中,对生物医药菌渣中蛋白质的提取缺少药物残留低、安全高效的技术。
技术实现要素:6.本发明的目的就是为了解决上述问题而提供一种利用生物医药发酵菌渣回收生物源蛋白的方法,本方法制备的生物源蛋白具有很高的回收率和蛋白纯度,且无药物残留,应用前景广阔,符合资源高效、环境友好的发展理念。
7.申请人发现生物医药发酵菌渣与剩余污泥理化性质具有明显差别,由于生物医药发酵菌渣中含有残留药物,蛋白质回收过程中残留药物的去除十分重要,而剩余污泥中的蛋白质提取不需要考虑抗生素问题。在高温条件下,蛋白质的水解损失严重,是造成回收率降低的重要原因。单一酸热和碱热条件对残留药物去除效果较差,在沉淀回收过程中,残留药物仍然会保留蛋白质产品中,存在安全风险。菌渣中蛋白质的提取需要通过过程控制,一方面降低回收的蛋白质产品的药物残留,另一方面提高蛋白质的回收率和纯度。
8.本发明的目的通过以下技术方案实现:
9.本技术方案的目的是保护一种利用生物医药发酵菌渣回收生物源蛋白的方法,本方法采用过氧化氢-碱法联合超声辅助技术,通过预处理、破壁处理、浓缩处理、分离及干燥回收生物源蛋白。包括以下步骤:
10.s1、调浆处理:取生物医药发酵菌渣加水调整固含量为至2~20%,搅拌至体系均匀;
11.s2、破壁处理:向调浆后的液体添加过氧化氢和碱,采用超声仪辅助破壁。
12.s3、浓缩处理:将破壁后的液体置于浓缩装置,浓缩至蛋白质浓度为80-120mg/ml;
13.s4、分离提纯:向浓缩液中加入酸作为沉淀剂,收集沉淀物,得到固体蛋白质;
14.s5、干燥回收:将回收的沉淀物进行低温冷冻干燥,得到生物源蛋白。
15.进一步地,s1中,所述生物医药发酵菌渣来自于生物医药发酵过程产生的菌丝体废弃物。
16.进一步地,s1中,所述菌丝体废弃物来自于头孢菌素、灰黄霉素、阿维菌素、林可霉素、泰乐菌素、硫酸安普霉素、阿卡波糖发酵中产生的菌丝体废弃物。
17.进一步地,s2中,所述过氧化氢为30wt%的双氧水,添加量为生物医药发酵菌渣投入质量的1%-30%。
18.进一步地,s2中,所述碱为固体粉末状的氢氧化钠、氢氧化钾、氧化钙中的一种或多种,优选为氢氧化钠。
19.进一步地,s2中,破壁处理时间为0.25h-2h。
20.进一步地,s2中,所述碱的用量为生物医药发酵菌渣投入质量的5%-30wt%。
21.进一步地,s3中,浓缩温度为60~80℃。选用市场上主流的低温减压浓缩装置实现。
22.进一步地,s4中,沉淀剂为硫酸、盐酸、柠檬酸、甲酸、三氯乙酸、磺基水杨酸的一种或多种,优选为磺基水杨酸。
23.进一步地,s4中,沉淀剂的加入量为菌渣添加量的2-20%。
24.与现有技术相比,本技术方案具有以下技术优势:
25.(1)本发明通过将生物发酵菌渣废弃物制备生物源蛋白,开发了生物发酵菌渣废弃物资源综合利用的途径,提升了产品经济价值。
26.(2)本发明采用超声氧化+碱法进行破壁处理,与酸/热法相比,能够极大的提高蛋白质提取效率和沉淀效率,蛋白质回收率高且纯度较高,蛋白质回收率大于85%,产品纯度大于800mg/g。
27.(3)本发明在回收提取过程中,能够有效去除生物医药发酵菌渣中残留药物,并减少残留药物共沉淀到蛋白质产物中,保证蛋白质产品的安全性,产品中药物残留小于1mg/
kg。
具体实施方式
28.下面结合具体实施例对本发明进行详细说明,但绝不是对本发明的限制。本技术方案中如未明确说明的制备手段、材料、结构或组成配比等特征,均视为现有技术中公开的常见技术特征。
29.若未特别指明,实施例中所用化学试剂均为常规在售试剂,实施例中所用的技术手段为本领域技术人员所熟知的常规手段。
30.实施例1
31.取生物医药发酵菌渣加水调整,配制2-20%的头孢菌素菌渣溶液,在转速180r/min条件下,搅拌均匀,加入以此过氧化氢10%,氢氧化钠10%(本技术方案中加入物料的百分量均为以菌渣投入质量作为基准,以各加入组分占菌渣投入质量表示),超声功率设置500w,打开超声仪和电动搅拌机,匀速搅拌下超声处理0.5h。过滤分离,测定提取液中的蛋白质浓度、计算蛋白质提取率以及提取液中的残留药物。由表1可以看出,随着固含量的增加,蛋白质浓度随之增加,蛋白质提取率随之减少。蛋白质提取率为可达到95%以上,在固含量2-15%范围内,残留药物能达到有效处理,经检测未检出。
32.表1不同固含量条件下蛋白质提取率、蛋白质浓度和残留药物
[0033][0034]
实施例2
[0035]
配制5%的头孢菌素菌渣溶液,在转速180r/min条件下,搅拌均匀,分别考察过氧化氢0-30%和氢氧化钠0-30%对蛋白质提取率、蛋白质浓度和残留药物去除效果的影响,超声功率设置500w,打开超声仪和电动搅拌机,匀速搅拌下超声处理0.5h。过滤分离,测定提取液中的蛋白质浓度、计算蛋白质提取率以及提取液中的残留药物。由表2可以看出,随着氢氧化钠添加量的增加,蛋白质提取率和浓度先增加后降低,添加过氧化氢和氢氧化钠处理残留药物明显低于单独过氧化氢处理和碱处理,提取率最高为96.9%,蛋白质浓度为24.23mg/ml,未检出残留药物。
[0036]
表2不同过氧化氢和氢氧化钠添加量下蛋白质提取率、蛋白质浓度和残留药物
[0037][0038]
实施例3
[0039]
配制5%的头孢菌素菌渣溶液,在转速180r/min条件下,搅拌均匀,考察超声功率200w-1000w和时间0.25h-2h条件下蛋白质提取率、蛋白质浓度和残留药物,打开超声仪和电动搅拌机,匀速搅拌下超声处理。过滤分离,测定提取液中的蛋白质浓度和计算蛋白质提取率。由表3可以看出,蛋白质提取率最高可达到98.6%,蛋白质浓度为24.65mg/ml,残留药物明显降低。
[0040]
表3不同超声功率和时间下的蛋白质提取率、蛋白质浓度和残留药物
[0041][0042]
实施例4
[0043]
通过实施例1-3筛选出的工艺条件,配制5%的头孢菌素、灰黄霉素、阿维菌素、林可霉素、泰乐菌素、硫酸安普霉素、阿卡波糖七类菌渣溶液,在转速180r/min条件下,搅拌均匀,加入过氧化氢10%,氢氧化钠10%,超声功率设置范围500w,打开超声仪和电动搅拌机,匀速搅拌下超声处理0.5h。过滤分离,测定提取液中的蛋白质浓度、计算蛋白质提取率和相应残留药物。由表4可以看出,七类菌渣蛋白质提取率均在95%以上,蛋白质浓度12.13mg/ml-24.65mg/ml,残留药物含量低,仅灰黄霉素和硫酸安普霉素的提取液有较低的药物检出。
[0044]
表4不同菌渣种类的蛋白质提取率、蛋白质浓度和残留药物
[0045][0046]
实施例5
[0047]
选择最优蛋白质浓度为24.65mg/ml的提取液,采用旋转蒸发仪,在75℃条件下,浓缩至蛋白质80-120mg/ml,分别加入2-20%的磺基水杨酸,静置40min后,过滤回收的固体物质通过低温冷冻干燥,即为蛋白质产品。并对产品中的蛋白质浓度和回收率进行测定,由表5可以看出,蛋白质纯度最高可到达881.3mg/g,总体回收率可达到90.5%以上。
[0048]
表5不同工艺回收蛋白质的纯度、蛋白质回收率和残留药物
[0049][0050]
实施例6
[0051]
进一步采用实施例5的最优方法对实施例4中7类菌渣提取液中蛋白质进行回收,采用旋转蒸发仪,在75℃条件下,浓缩至蛋白质80-120mg/ml,加入5%的磺基水杨酸,静置40min后,过滤回收的固体物质通过低温冷冻干燥,即为蛋白质产品。采用cn106749506a“一种从土霉素菌渣中提取蛋白质的方法”中提到的酸/热工艺对头孢菌素、灰黄霉素、阿维菌素、林可霉素、泰乐菌素、硫酸安普霉素、阿卡波糖发酵菌渣中蛋白质进行回收,并对回收的蛋白质产品进行检测。并对两类工艺回收的蛋白质产品进行纯度、回收率和残留药物的测定。采用本发明工艺提取的蛋白质产品经检测7类菌渣提取的蛋白质总体回收率均在87%以上,蛋白质纯度在820mg/g以上,明显优于对比工艺。产品相对更加安全,蛋白质中残留药物可达到1mg/kg以下或未检出。
[0052]
表6不同工艺提取的蛋白质产品数据
[0053][0054]
上述的对实施例的描述是为便于该技术领域的普通技术人员能理解和使用发明。熟悉本领域技术的人员显然可以容易地对这些实施例做出各种修改,并把在此说明的一般原理应用到其他实施例中而不必经过创造性的劳动。因此,本发明不限于上述实施例,本领域技术人员根据本发明的揭示,不脱离本发明范畴所做出的改进和修改都应该在本发明的保护范围之内。