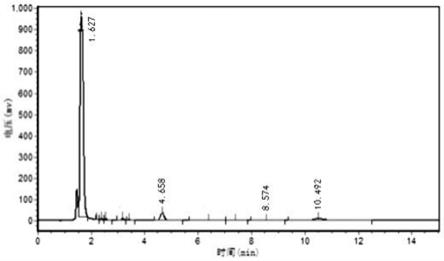
1.本发明属于橡塑助剂领域,具体涉及从抗氧剂168浓母液中回收2,4-二叔丁基苯酚的方法。
背景技术:2.在高分子材料中,加入抗氧剂,能够有效抑制或延缓聚合物的氧化降解的发生,从而使高分子材料的使用寿命得以延长。抗氧剂168(学名三[2.4-二叔丁基苯基]亚磷酸酯)为亚磷酸酯类辅助抗氧剂,具有耐高温,耐水解、不变色与不着色的特色功能,特别是当其与受阻酚类主抗氧剂配合使用,能够有效提高聚烯烃类树脂的加工稳定性、耐热稳定性、色泽改良性和耐候性,具有良好的协同效应,是亚磷酸酯类辅助抗氧剂的主流品种,广泛应用于各种聚烯烃的加工过程中,具有良好的发展前景。
[0003]
目前,抗氧剂168主要制备工艺是用2,4-二叔丁基苯酚和三氯化磷在反应溶剂及催化剂作用下进行酯化反应,反应混合物经过结晶、离心洗料及干燥而得。离心工序所得的滤液通常称为母液,母液中还包括未完全反应的2,4-二叔丁基苯酚及未完全反应成168的一取代物和二取代物等杂质,结晶母液通过蒸馏回收结晶溶剂,蒸馏出溶剂的残留物通常称为浓母液,从节约成本、减少环境污染考虑,需要从抗氧剂168浓母液中回收2,4-二叔丁基苯酚。
[0004]
现有技术多采用多次重结晶的方式回收2,4-二叔丁基苯酚,得到产物纯度低,需要进一步精馏使用,降低了收率,且大量结晶溶剂的使用后处理繁琐,污染环境。专利申请cn108484367a公开了一种从抗氧化剂168母液中回收2,4-二叔丁基苯酚的方法,但该方法需要低沸点溶剂石油醚多次萃取,操作过程繁琐,降低了2,4-二叔丁基苯酚的回收率,而且低沸点的有机溶剂带来了环境和安全上的隐患,另外在后续工序的使用中不能再直接使用。
技术实现要素:[0005]
为了解决以上问题,本发明提供一种从抗氧剂168浓母液中回收2,4-二叔丁基苯酚的方法,本方法操作简单且无副产品,降低能源消耗,同时杜绝了低沸点的有机溶剂对环境的污染,提高2,4-二叔丁基苯酚的收率,回收的2,4-二叔丁基苯酚纯度高,可直接用于抗氧剂168的生产,回收工艺中所用的溶剂甲苯、酸性水溶液可以进行反复使用。
[0006]
为了实现上述目的,本发明采用如下技术方案:一种从抗氧剂168浓母液中回收2,4-二叔丁基苯酚的方法,其特征在于:该方法包括以下步骤:
[0007]
(1)将抗氧剂168浓母液、溶剂甲苯、酸性水溶液按比例依次加入到反应器中,开启高速搅拌,给反应体系升温至回流,反应4-5小时,静置分层,将下层酸性水溶液分离去除得有机相ⅰ;
[0008]
(2)向步骤(1)有机相ⅰ中加入蒸馏水,升温至90℃水洗0.5-1h,再静置分层,将下层水溶液分离去除得有机相ⅱ;
[0009]
(3)将步骤(2)有机相ⅱ进行第一次减压蒸馏,馏出液为溶剂甲苯,去除溶剂甲苯得有机相ⅲ;
[0010]
(4)将步骤(3)有机相ⅲ进行到第二次减压蒸馏,馏出液即是2,4-二叔丁基苯酚。
[0011]
所述的溶剂甲苯加入量为抗氧剂168浓母液质量的0.5-2倍。
[0012]
所述的酸性水溶液加入量为抗氧剂168浓母液质量的1-2倍。
[0013]
所述的酸性水溶液为硫酸水溶液或盐酸水溶液,浓度为1wt%-4wt%。
[0014]
所述的回流反应温度为110-112℃。
[0015]
所述的蒸馏水量为抗氧剂168浓母液质量的2-3倍。
[0016]
所述的第一次减压蒸馏温度为110-140℃,真空度为-0.09mpa~-0.1mpa。
[0017]
所述的第二次减压蒸馏温度为150-220℃,真空度为-0.09mpa~-0.1mpa。
[0018]
本发明的抗氧剂168浓母液含有大量的抗氧剂168,2,4-二叔丁基苯酚,未反应完全的一取代物和二取代物,即二[2,4-二叔丁基苯基]氯代亚磷酸酯,[2,4-二叔丁基苯基]二氯代亚磷酸酯,上述物质易水解,因亚磷酸酯类抗氧剂分子结构中的三价磷元素具有一对未成键电子,表现为较强的亲核能力,磷原子体积较大,受电子离域作用影响能够被亲核试剂作用,因而在有水的情况下和水发生水解反应,特别是空间位阻效应较弱的烷基亚磷酸酯,水解活性较强,而在酸性溶液中,羰基氧原子先质子化,增加基团正电性,从而提高了受亲核试剂水进攻的能力。
[0019]
本发明具有以下有益效果:
[0020]
1、本发明利用抗氧剂168浓母液在酸性溶液中,残留的抗氧剂168、未反应完全的二[2,4-二叔丁基苯酚]氯代亚磷酸酯,[2,4-二叔丁基苯酚]二氯代亚磷酸酯充分水解生成2,4-二叔丁基苯酚,再通过减压蒸馏的方式回收溶剂和2,4-二叔丁基苯酚,减少了环境污染,提高了2,4-二叔丁基苯酚的收率,节约资源,降低生产成本。
[0021]
2、本发明简化生产操作过程,且无副产品,得到的2,4-二叔丁基苯酚纯度高,可直接用于抗氧剂168的生产,回收工艺所用的溶剂甲苯、酸性水溶液可以进行反复使用,杜绝了有机溶剂和废水对环境的污染。
[0022]
3、本发明最后蒸馏剩余极少量物料,可以同下一批次浓母液混合后继续进行反应,无副产品产生。
[0023]
4、本发明中所用的盐酸水溶液,酸度较高时(浓度高于4wt%),可以排入抗氧剂168生产车间合成的副产品盐酸中,不会造成浪费及污染。
附图说明
[0024]
图1为抗氧剂168浓母液液相色谱图。
[0025]
图2为本发明实施例1中得到的2,4-二叔丁基苯酚气相色谱图。
[0026]
图3为本发明实施例2中制得的抗氧剂168液相色谱图。
[0027]
图4为本发明回收2,4-二叔丁基苯酚方法的流程图。
具体实施方式
[0028]
下面结合具体实施例对本发明作进一步解说,所述是对本发明的解释而非限定。
[0029]
本发明采用的抗氧剂168浓母液经液相色谱检测,各组分质量百分比如图1所示,
含有抗氧剂168为2-7%,出峰时间为10.492min,2,4-二叔丁基苯酚85-90%,出峰时间为1.627min,[2.4-二叔丁基苯基]二氯代亚磷酸酯3-6%,出峰时间为4.658min,二[2.4-二叔丁基苯基]氯代亚磷酸酯0.5-2%,出峰时间为8.547min,其他杂质2-4%。
[0030]
实施例1
[0031]
向带有机械搅拌装置、温度计及回流冷凝器的反应瓶中,加入200g抗氧剂168浓母液及170g甲苯,搅拌使抗氧剂168浓母液完全溶于甲苯后,加入2wt%盐酸水溶液200g,升温至110℃,甲苯回流,保持反应体系的温度在110-112℃,高速搅拌反应4小时后停止搅拌,得到反应液静置分层,待油相和水相分开后将下层酸性水溶液分离去除,再加入400g水,升温至90℃,水洗0.5h,水洗结束后停止搅拌静置分层,待油相和水相分开后将下层水相分离去除。剩余油相物料进行蒸馏,前期常压蒸馏,温度升至110℃后开启真空,将真空度由-0.09mpa逐渐调至-0.1mpa,反应体系温度逐渐升至140℃,将甲苯脱除干净。然后进行二次蒸馏,真空度-0.09mpa逐渐调至-0.1mpa将2,4-二叔丁基苯酚蒸出,随着蒸馏的进行温度由150℃逐渐升高,最终温度升至220℃时停止蒸馏,瓶内剩余微量物料可加入到168浓母液中套用,继续进行水解反应。
[0032]
回收得到的2,4-二叔丁基苯酚,收率为96.1%,经气相色谱检测,谱图如图2所示,4.03min为2,4-二叔丁基苯酚的出峰时间,测得的2,4-二叔丁基苯酚含量为99.77%,其他测试结果见表1。
[0033]
实施例2
[0034]
用实施例1中回收的2,4-二叔丁基苯酚合成抗氧剂168。
[0035]
称取实施例1回收的2,4-二叔丁基苯酚68.8g及适量甲苯加入到四口烧瓶中,搅拌使2,4-二叔丁基苯酚溶于甲苯中,加入催化剂三乙胺,升温至40℃后,滴加15.4g三氯化磷,滴加过程中保持温度在40-50℃,滴加结束后维持温度在50-55℃,保温反应约1h,然后升温至回流,反应4.5h,结束反应。减压蒸馏回收反应溶剂甲苯,得到白色固体产物。再向反应瓶内加入适量甲苯及中和剂二正丁胺,升温至90℃,中和反应0.5h,热过滤,将盐过滤干净,再升温减压蒸馏甲苯,蒸净后加入150ml甲醇,升温至回流搅拌使物料完全分散,冷却至室温,过滤,得到白色粉末状的三(2,4-二叔丁基苯基)亚磷酸酯。
[0036]
反应制得的抗氧剂168经液相色谱检测,7.947min为抗氧剂168的出峰时间,测得的含量为99.78%,与抗氧剂168浓母液采用不同液相色谱仪,出峰时间不同,液相色谱图如图3所示。
[0037]
实施例3
[0038]
向带有机械搅拌装置、温度计及回流冷凝器的反应瓶中,加入200g抗氧剂168浓母液及100g甲苯,开启搅拌使抗氧剂168浓母液完全溶于甲苯后,加入含1wt%盐酸水溶液400g,升温至110℃,甲苯回流,保持反应体系的温度在110-112℃,高速搅拌反应5小时后停止搅拌,得到反应液静置分层,待油相和水相分开后将下层酸性水溶液分离去除,再加入600g水,升温至90℃,水洗1h,水洗结束后停止搅拌静置分层,待油相和水相分开后将下层水相分离去除。剩余油相物料进行蒸馏,前期常压蒸馏,温度升至110℃后开启真空,将真空由-0.09mpa逐渐调至-0.1mpa,反应体系温度逐渐升至140℃,将甲苯脱除干净。继续升温进行二次蒸馏,真空度-0.09mpa逐渐调至-0.1mpa将2,4-二叔丁基苯酚蒸出,随着蒸馏的进行温度由150℃逐渐升高,最终温度升至220℃时停止蒸馏,瓶内剩余微量物料,此物料可加入
到抗氧剂168浓母液中套用,继续进行水解反应。
[0039]
回收得到的2,4-二叔丁基苯酚,收率为92.3%,经气相色谱检测,2,4-二叔丁基苯酚含量为99.57%,采用实施例2的方法合成抗氧剂168,测试结果见表1。
[0040]
实施例4
[0041]
向带有机械搅拌装置、温度计及回流冷凝器的反应瓶中,加入170g抗氧剂168浓母液及340g甲苯,搅拌使母液完全溶于甲苯后,加入含4%盐酸的水溶液255g,升温至110℃,甲苯回流,保持反应体系的温度在110-112℃,高速搅拌回流反应4小时后停止搅拌,得到反应液静置分层,待油相和水相分开后将下层酸性水溶液分离去除;再加入500g水,升温至90℃,水洗0.5h,水洗结束后停止搅拌静置分层,待油相和水相分开后将下层水相分离去除。剩余油相物料蒸馏,前期常压蒸馏,温度升至110℃后开启真空,将真空度由-0.09mpa逐渐调至-0.1mpa,反应体系温度逐渐升至140℃,将甲苯脱除干净。继续升温进行二次减压蒸馏,真空度-0.09mpa逐渐调至-0.1mpa将2,4-二叔丁基苯酚蒸出,随着减压蒸馏的进行温度由150℃逐渐升高,最终温度升至220℃时停止蒸馏,瓶内剩余微量物料,此物料可加入到抗氧剂168浓母液中套用,继续进行水解反应。
[0042]
回收得到的2,4-二叔丁基苯酚,收率为95.5%,经气相色谱检测,含量为99.81%,采用实施例2的方法合成抗氧剂168,测试结果见表1。
[0043]
实施例5
[0044]
向带有机械搅拌装置、温度计及回流冷凝器的反应瓶中,加入170g抗氧剂168浓母液及170g甲苯,搅拌使母液完全溶于甲苯后,加入含2%硫酸水溶液300g,升温至110℃,甲苯回流,保持反应体系的温度在110-112℃,高速搅拌反应5小时后停止搅拌,得到反应液静置分层,待油相和水相分开后将下层酸性水溶液分离去除;再加入240g水,升温至90℃,水洗0.5h,水洗结束后停止搅拌静置分层,待油相和水相分开后将下层水相分离去除。剩余油相物料进行蒸馏,前期常压蒸馏,温度升至110℃后开启真空,将真空度由-0.09mpa逐渐调至-0.1mpa,反应体系温度逐渐升至140℃,将甲苯脱除干净。继续升温进行二次减压蒸馏,真空度-0.09mpa逐渐调至-0.1mpa将2,4-二叔丁基苯酚蒸出,随着减压蒸馏的进行温度由150℃逐渐升高,最终温度升至220℃时停止蒸馏,瓶内剩余微量物料,此物料可加入到抗氧剂168浓母液中套用,继续进行水解反应。
[0045]
蒸馏得到的2,4-二叔丁基苯酚,收率为96.4%,经气相色谱检测,含量为99.70%,采用实施例2的方法合成抗氧剂168,测试结果见表1。
[0046]
实施例6
[0047]
用车间生产精馏2,4-二叔丁基苯酚成品制备抗氧剂168。
[0048]
将生产车间精馏2,4-二叔丁基苯酚68.8g及适量甲苯加入到四口烧瓶中,搅拌使2,4-二叔丁基苯酚溶于甲苯中,加入催化剂三乙胺,升温至40℃后,滴加15.4g三氯化磷,滴加过程中保持温度在40-50℃,滴加结束后维持温度在50-55℃,保温反应约1h,然后升温至回流,反应4.5h,结束反应。减压蒸馏回收反应溶剂甲苯,得到白色固体产物。再向反应瓶内加入适量甲苯及中和剂二正丁胺,升温至90℃,中和0.5h,热过滤,将盐过滤干净,再升温减压蒸馏甲苯,蒸净后加入150ml甲醇,升温至回流搅拌使物料完全分散,冷却至室温,过滤,得到白色粉末状的抗氧剂168成品。制备的抗氧剂168成品经液相色谱检测,含量为99.79%。
[0049]
表1
[0050][0051][0052]
表1抗氧剂168的透光率采用分光光度计检测,从测试结果表1可以看出,本发明从抗氧剂168母液中回收的2,4-二叔丁基苯酚含量在99.57-99.81%之间,收率在92.3-96.4%之间,回收的2,4-二叔丁基苯酚主含量高,杂质少,且收率高,再合成的抗氧剂168含量在99.72-99.82%,成品各项指标均符合行业标准,通过实验参数的调整,回收反应的稳定性较高,与生产车间精制2,4-二叔丁基苯酚制得的抗氧剂168指标无差别。
[0053]
以上所述仅为本发明的优选实例而已,并不用于限制本发明,对于本领域的技术人员来说,本发明可以有各种更改和变化。凡对本发明所做的任何修改、等同替换、改进等,均应包含在本发明的保护范围之内。