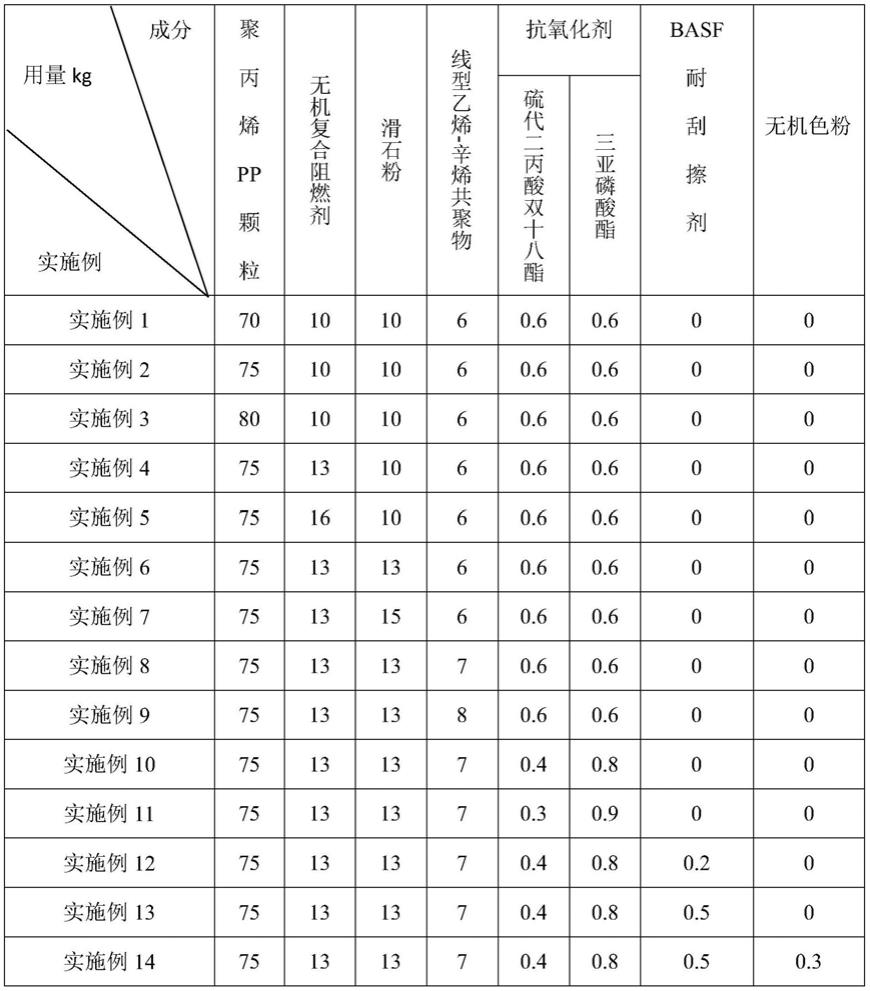
一种高模量汽车内饰阻燃pp材料及其制备方法
技术领域
1.本技术涉及汽车内饰材料的制备领域,更具体地说,它涉及一种高模量汽车内饰阻燃pp材料及其制备方法。
背景技术:2.汽车内饰主要是指汽车内部改装所用到的汽车产品,涉及到汽车内部的方方面面,比如汽车方向盘套、汽车坐垫、汽车脚垫、汽车香水、汽车挂件、内部摆件、收纳箱等。
3.汽车内饰件的阻燃要求,正在逐步严格。同时汽车内饰件的voc要求,已经是各汽车主机厂必须要解决的问题。汽车内饰件,如门板、立柱、穿线管、把手、顶棚、中控台等,多数以pp材料为主。pp材料的阻燃大多为含卤素阻燃体系,但其由于存在容易析出、气味大、容易老化等问题,不适合在汽车内饰件里使用;而氢氧化铝、氢氧化镁等无机阻燃剂化学稳定性好,不易挥发,毒性低或无毒,不产生腐蚀等有害气体,对环境友好,但是,一般需要高填充量才能产生好的阻燃效果。
4.针对上述中的相关技术,发明人认为氢氧化铝和氢氧化镁在用于汽车内饰pp材料的阻燃剂时存在阻燃效果差的缺点。
技术实现要素:5.为了解决氢氧化铝和氢氧化镁作为阻燃剂应用在汽车内饰pp材料时存在阻燃效果差的问题,本技术提供一种高模量汽车内饰阻燃pp材料及其制备方法。
6.本技术提供的一种高模量汽车内饰阻燃pp材料,采用如下的技术方案:
7.一种高模量汽车内饰阻燃pp材料,由包括以下重量份的原料制成:聚丙烯pp颗粒70-80份、无机复合阻燃剂10-16份、线型乙烯-辛烯共聚物6-8份、滑石粉10-15份和抗氧剂1.2份;
8.所述无机复合阻燃剂的制备方法如下:
9.将纳米氢氧化铝粉体搅拌并加热,将偶联剂加入纳米氢氧化铝粉体中,使纳米氢氧化铝充分偶联改性,得到改性纳米氢氧化铝;
10.将所得改性纳米氢氧化铝与微米氢氧化镁和硼酸锌按重量比为(1-5):(6-8):1混合搅拌均匀,制得无机复合阻燃剂。
11.通过采用上述技术方案,由于纳米氢氧化铝改性后具有优良的相容性且分解速度快;而微米氢氧化镁的表面极性大、分解速度慢,阻燃效果较好,但相容性差;两者复配后,改性纳米氢氧化铝可以迅速发挥效力,而微米氢氧化镁能持续较长时间发挥效力,速效与长效的结合,且在硼酸锌的辅助作用下,形成的无机复合阻燃剂具有高效且无烟的效果,因而提高了汽车内饰阻燃pp材料的阻燃性;
12.滑石粉作为一种无机填料,能够增加聚丙烯复合材料的刚性和韧性;线型乙烯-辛烯共聚物作为聚丙烯复合材料的增韧剂,以降低复合材料脆性和提高材料抗冲击性能;滑石粉和线型乙烯-辛烯共聚物两者在共同条件下提高了汽车内饰阻燃pp材料的力学性能,
使其具有高模量;
13.可选的,所述偶联剂的加入量为纳米氢氧化铝粉体重量的0.5-3%。
14.通过采用上述技术方案,优化了偶联剂的加入量,使得改性后的纳米氢氧化铝的分散度更好,有利于提高汽车内饰阻燃pp材料的阻燃性能和力学性能。
15.可选的,所述偶联剂包括二甲基硅油、线型聚二甲基硅氧烷和油酸钠的一种。
16.可选的,对所述纳米氢氧化铝粉体的加热温度为100-130℃。
17.通过采用上述技术方案,通过优化纳米氢氧化铝粉体的加热温度,使其与微米氢氧化镁和硼酸锌混合地更加均匀,从而提高无机复合阻燃剂的协同作用。
18.可选的,所述抗氧剂包括主抗氧剂和辅助抗氧剂,所述主抗氧剂为硫代二丙酸双十八酯,所述辅助抗氧剂为三亚磷酸酯,且硫代二丙酸双十八酯和三亚磷酸酯的重量比为1:(1-3)。
19.通过采用上述技术方案,硫代二丙酸双十八酯能有效防止聚丙烯在长期老化过程中的热氧化降解,同时与三亚磷酸酯并用具有协同效应,两者联合使用能有效提高汽车内饰pp材料的抗老化综合能力,可有效地延长汽车内饰阻燃pp材料的使用寿命。
20.可选的,所述原料中还包括0.2-0.5重量份的助剂。
21.通过采用上述技术方案,助剂与pp基材相容性较强、扩散速度较慢、极性较好,有利于提高汽车内饰阻燃pp材料的使用期限。
22.可选的,所述原料中还包括0.3-0.5重量份的无机色粉。
23.通过采用上述技术方案,在符合环保的要求下,添加无机色粉有利于提高汽车内饰阻燃pp材料所制成的产品的商业价值。
24.第二方面,本技术提供一种高模量汽车内饰阻燃pp材料的制备方法,采用如下的技术方案:
25.一种高模量汽车内饰阻燃pp材料的制备方法,包括以下步骤:
26.将相应重量的原料进行混合,形成混合料;
27.将所述混合料进行挤出、熔融、造粒得到母粒;
28.将所述母粒进行干燥处理,得到高模量汽车内饰pp阻燃材料。
29.通过采用上述技术方案,所制得的汽车内饰阻燃pp材料具有优良的阻燃性和高模量性,能较好的应用在汽车的内饰品上,并且汽车类饰品的力学性能达到了较大的提高,制备工艺简单,无需特殊设备,适合工业化生产。
30.可选的,采用搅拌的方式对所述原料进行混合,其中搅拌速度为300-400r/min,搅拌时间为5-10min。
31.可选的,所述母粒干燥过程中,干燥温度为85-90℃,干燥时间为2-3h。
32.通过采用上述技术方案,优化了搅拌速度、搅拌时间、干燥温度和干燥时间,有利于更好地制备汽车内饰pp阻燃材料。
33.综上所述,本技术具有以下有益效果:
34.1.由于本技术采用改性纳米氢氧化铝和微米氢氧化铝在硼酸锌的辅助下复合形成的无机复合阻燃剂属于无卤阻燃剂,由于它本身无毒,而且可以避免含卤阻燃高分子材料燃烧时产生的有毒烟雾,在充分发挥氢氧化铝和氢氧化镁的阻燃协同作用下,使得汽车内饰阻燃pp材料获得了优异的阻燃效果;
35.2.本技术在pp材料中添加滑石粉作为一种无机填料,不仅降低了pp材料的生产成本,而且能够增加聚丙烯复合材料的刚性和韧性;而线型乙烯-辛烯共聚物作为pp材料的增韧剂,降低了复合材料脆性和提高了抗冲击性能;滑石粉和线型乙烯-辛烯共聚物两者在共同条件下使得汽车内饰阻燃pp材料具有高模量性能和优异的抗冲击性能;
36.3、本技术中优选采用硫代二丙酸双十八酯作为主抗氧剂,三亚磷酸酯作为辅助抗氧剂,由于硫代二丙酸双十八酯和三亚磷酸酯具有协同效应,有效地延长了汽车内饰阻燃pp材料的使用期限。
具体实施方式
37.以下结合制备例和实施例对本技术作进一步详细说明。
38.制备例和实施例中所用的相关原材料中:
39.聚丙烯pp颗粒的型号为gb303hp;纳米氢氧化铝的平均粒径≤80nm;微米氢氧化镁的平均粒径为1-10μm;线型乙烯-辛烯共聚物的密度为0.88g/cm3,牌号为8137;滑石粉的平均粒径为0.1-2μm;硫代二丙酸双十八酯的牌号为123-28-4;三亚磷酸酯的牌号为kc-69;助剂选择basf耐刮擦剂。
40.制备例
41.制备例1
42.本制备例制备了一种无机复合阻燃剂,具体方法如下:
43.将100kg纳米氢氧化铝粉体置于高速搅拌机中,均匀搅拌并加热至100℃,采用喷雾法将0.5kg二甲基硅油加入纳米氢氧化铝粉体中,使纳米氢氧化铝充分偶联改性,制成改性纳米氢氧化铝;
44.将600kg的微米氢氧化镁和100kg硼酸锌加入上述改性纳米氢氧化铝中,搅拌均匀,制得无机复合阻燃剂。
45.制备例2
46.本制备例制备了一种无机复合阻燃剂,具体方法如下:
47.将300kg纳米氢氧化铝粉体置于高速搅拌机中,均匀搅拌并加热至115℃,采用喷雾法将4.5kg线型聚二甲基硅氧烷加入纳米氢氧化铝粉体中,使纳米氢氧化铝充分偶联改性,制成改性纳米氢氧化铝;
48.将700kg的微米氢氧化镁和100kg硼酸锌加入上述改性纳米氢氧化铝中,搅拌均匀,制得无机复合阻燃剂。
49.制备例3
50.将500kg纳米氢氧化铝粉体置于高速搅拌机中,均匀搅拌并加热至130℃,采用喷雾法将15kg油酸钠加入纳米氢氧化铝粉体中,使纳米氢氧化铝充分偶联改性,制成改性纳米氢氧化铝;
51.将800kg的微米氢氧化镁和100kg硼酸锌加入上述改性纳米氢氧化铝中,搅拌均匀,制得无机复合阻燃剂。
52.实施例
53.实施例1-15
54.如表1所述,实施例1-15的主要区别在于pp材料的原料配比不同。
55.以下以实施例1为例进行说明。本技术公开了一种高模量汽车内饰阻燃pp材料,其实施的具体配方为:聚丙烯pp颗粒70kg,无机复合阻燃剂10kg,线型乙烯-辛烯共聚物6kg,滑石粉10kg,硫代二丙十八酯0.6kg,和三亚磷酸酯0.6kg,其中无机复合阻燃剂采用制备例2所得。
56.实施例1高模量汽车内饰阻燃pp材料的制备方法如下:
57.按配方称取原料置于搅拌机中,在搅拌速度为300r/min的条件下,搅拌10min,使原料充分混合,形成混合料;
58.将上述混合料投入双螺杆挤出机,井熔融挤出后冷却造粒得到母粒,其中螺杆各区温度:一区、二区140-160℃,三区、四区180-200℃,五区、六区190-210℃,七区、八区和九区200-210℃,机头200-220℃;螺杆主机转速:220-350r/min;
59.将上述母粒进行干燥处理,得到高模量汽车内饰阻燃pp材料;其中干燥温度为85℃,干燥时间为3h。
60.表1实施例1-15中汽车内饰阻燃pp材料中各原料配比
[0061][0062][0063]
实施例16
[0064]
本实施例与实施例15不同的是,无机复合阻燃剂采用制备例1所得。
[0065]
实施例17
[0066]
本实施例与实施例15不同的是,无机复合阻燃剂采用制备例3所得。
[0067]
实施例18
[0068]
本实施例与实施例15不同的是,制备方法中,搅拌速度为400r/min,搅拌时间为5min;干燥温度为90℃,干燥时间为2min。
[0069]
对比例
[0070]
对比例1
[0071]
本对比例与实施例2不同之处在于,pp材料中阻燃剂完全为改性纳米氢氧化铝,且
其加入量为10kg。
[0072]
对比例2
[0073]
本对比例与实施例2不同之处在于,pp材料中阻燃剂完全为微米氢氧化镁,且其加入量为10kg。
[0074]
对比例3
[0075]
本对比例与实施例4不同之处在于,滑石粉的加入量为0kg。
[0076]
对比例4
[0077]
本对比例与实施例4不同之处在于,滑石粉的加入量为30kg。
[0078]
对比例5
[0079]
本对比例与实施例6的不同之处在于,线型乙烯-辛烯共聚物的加入量为0kg。
[0080]
对比例6
[0081]
本对比例与实施例6的不同之处在于,线型乙烯-辛烯共聚物的加入量为15kg。
[0082]
性能检测试验
[0083]
采用相同重量的由实施例1-18获得的汽车内饰阻燃pp材料作为试验样1-18,采用与试验样相同重量的由对比例1-6获得的汽车内饰阻燃pp材料作为对照样1-6。对试验样和对照样进行性能检测,结果如表2。
[0084]
一、力学性能
[0085]
力学性能试验在温度为25℃、湿度为50%的条件下进行,试验如下:
[0086]
根据gb/t 1040、1/2-2006,对相应的试验样、对照样进行拉伸屈服应力以及断裂拉伸应变测试,记录数据并分析,其中试样的形状和尺寸为1b型;
[0087]
根据gb/t 9341-2008,对相应的试验样、对照样进行弯曲模量测试,记录数据并分析,其中试样尺寸为80
×
10
×
4mm,试验速度为20mm/min;
[0088]
根据gb/t 1843-2008,对相应的试验样、对照样进行悬臂梁缺口冲击强度测试,记录数据并分析,其中试样尺寸为80
×
10
×
4mm,试样缺口为a型。
[0089]
二、阻燃性能
[0090]
根据gb/t 2406.2-2009,对相应的试验样、对照样进行jf-3型氧指数测试,记录数据并分析,其中试样尺寸为80
×6×
3mm。
[0091]
表2性能检测数据表
[0092][0093]
参照表2,结合实施例2、4、5和对比例1和2,可以看出,加入单一的改性纳米氢氧化铝和微米氢氧化镁的阻燃效果和力学性能均没有复合后的阻燃剂对汽车内饰pp材料的阻燃效果好和弯曲模量高;随着无机复合阻燃剂加入量的不断增加,汽车内饰pp材料的氧指数上升,阻燃性得以提高。
[0094]
参照表2,结合实施例4、6、7和对比例3和4,可以看出,随着填充物滑石粉的加入量的不断增加,材料的刚性和韧性越大,冲击强度越差。
[0095]
参照表2,结合实施例6、8、9和对比例5和6,可以看出,随着增韧剂线型乙烯-辛烯共聚物的不断加入,可有效改善试样的冲击强度;但是线型乙烯-辛烯共聚物的加入也会导致试样刚性和韧性的下降。
[0096]
参照表2,结合实施例1-3,可以看出,随着pp聚丙烯颗粒的不断加入,会提高试样的刚性和韧性,相应的试样的冲击强度会有所下降。
[0097]
参照表2,结合实施例8,10-15,可以看出,pp材料中抗氧化剂、basf耐刮擦剂以及无机色粉的加入,对试样的力学性能和阻燃性能影响不大。
[0098]
参照表2,结合实施例15-17,可以看出,在适当范围内改变改性纳米氢氧化铝、微米氢氧化镁和硼酸锌,三者之间的复配比、改性纳米氢氧化铝的搅拌温度以及偶联剂的种类和含量,所制备的无机复合阻燃剂均具有良好的阻燃效果;且制备例2所制备出的无机复合阻燃剂对试样的阻燃性能较优。
[0099]
参照表2,结合实施例15和18,可以看出,在适当范围内改变制备方法中的搅拌速度、搅拌时间、干燥温度和干燥时间,得到的试样均具有优异的力学性能和阻燃性。
[0100]
本具体实施例仅仅是对本技术的解释,其并不是对本技术的限制,本领域技术人员在阅读完本说明书后可以根据需要对本实施例做出没有创造性贡献的修改,但只要在本技术的权利要求范围内都受到专利法的保护。