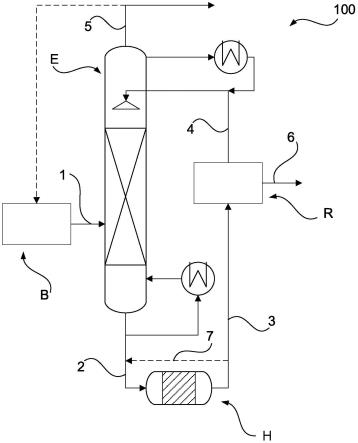
1.本发明涉及根据独立权利要求的前序部分的使用醛制备目标化合物的工艺和相应的设备。
2.产生本专利申请的项目受到欧盟horizon 2020研究和创新计划的第814557号资助协议的资助。
背景技术:3.由醛制备醇、特别是由丙醛制备丙醇基本上是已知的。例如,ullmann的《encyclopedia of industrial chemistry》2012版中的文章“propanols”描述了在110℃至150℃和0.14mpa至1.0mpa的压力下,在20:1的氢气与丙醛之比下进行的非均相气相工艺。当存在过量的氢气时发生还原,并且通过使气相循环通过外部热交换器或通过在内部冷却反应器来除去反应热。氢的效率大于90%,醛转化率高达99.9%,并且获得大于99%的醇产率。常用的商业催化剂包括负载在氧化铝或硅藻土上的cu、zn、ni和cr的组合。二丙醚、乙烷和丙酸丙酯被提及作为主要杂质。
4.文献中也给出了相应的液相工艺的细节。例如,这些反应在95-120℃的温度和3.5mpa的压力下进行。优选的催化剂通常是ni、cu、雷尼镍或用mo、mn和na增强的负载型ni催化剂。例如,在这些液相工艺中可以以99.9%的纯度生产1-丙醇。
5.丙醇纯化中的重要问题是从该工艺的产物混合物中除去水。如果如本发明的一个实施例中,丙醇脱水为丙烯,即如果丙醇仅用作由丙醇合成烯烃的中间体,则水也是该脱水步骤中的反应产物之一,因此不必预先进行水分离。丙烯和水的分离相对简单。然而,在这种情况下,除水以外的组分的分离通常也更困难,特别是如果这些其它组分具有比醛显著更低的沸点并且不能通过冷凝除去。
6.相应工艺中使用的醛可以例如使用氢甲酰化提供。典型的氢甲酰化工艺通常假定在工业规模上具有高烯烃含量的相对纯的进料流。因此,所述较低沸点的组分,例如二氧化碳、较低沸点的烃(尤其是甲烷)以及未反应的一氧化碳和氢气通常也以非显著量存在于产物流中。也可以加工纯度较低和/或稀释的进料流的烯烃的氢甲酰化的新工艺是已知的,例如由de102019119543、de102019119562和de102019119540已知。
7.一氧化碳和二氧化碳可以在开始描述的氢化过程中作为抑制剂,或者也可以导致不希望的副产物。
8.原则上,存在大量不同的用于将烃和相关化合物相互转化的工艺,其中一些作为示例在下面列出。
9.例如,通过氧化脱氢(odh,在乙烷的情况下也称为odhe)将烷烃转化为链长相当的烯烃是公知的。典型地,odh也形成链长当量的羧酸,即,在odhe情况下形成作为副产物的乙酸。乙烯也可以通过甲烷的氧化偶联(ocm)来制备。
10.通过脱氢(pdh)由丙烷制备丙烯也是已知的,并且代表了商业上可行和已建立的工艺。这同样适用于通过烯烃复分解由乙烯生产丙烯。该工艺需要2-丁烯作为起始产物。
11.最后,有所谓的甲烷到烯烃或甲烷到丙烯(mto,mtp)工艺,其中首先由甲烷生产合成气,然后将合成气转化为烯烃如乙烯和丙烯。相应的工艺可以基于甲烷进行操作,但也可以基于其它烃或含碳原料(如煤或生物质)进行操作。
12.丙烯的生产也详细描述于技术文献中,例如在ullmann的《encyclopedia of industrial chemistry》2012版的文章“propylene”中。丙烯通常通过烃原料的蒸汽裂化和炼油操作中的转化工艺来生产。在后一种工艺中,丙烯不一定以所需量形成,并且仅作为与其它化合物的混合物中的几种组分之一形成。其它生产丙烯的工艺也是已知的,但并不是在所有情况下(例如在效率和产率方面)都令人满意。
13.预测未来对丙烯的需求增加(“丙烯缺口”),这需要提供相应的选择性工艺。同时,必须减少或甚至防止二氧化碳排放。另一方面,大量甲烷可作为潜在的进料获得,其目前仅在非常有限的程度上再循环并且主要被焚烧。
14.如已经提及的,氢甲酰化(也称为羰基合成)是特别用于制备上述类型的羰基合成化合物的另一种技术。通常,乙烯或丙烯在氢甲酰化中反应,但也可使用高级烃,特别是具有六至十一个碳原子的烃。具有四和五个碳原子的烃的转化也是可能的,但不太重要。氢甲酰化,其中首先形成醛,随后可以进行氢化。在根据本发明的工艺的实施例中也是这种情况。通过这种氢化形成的醇随后可以进一步脱水成相应的烯烃。
15.在文献green et al,catal.lett.1992,13,341中,描述了一种由甲烷和空气生产丙醛的工艺。在所提出的工艺中,记录了相对于甲烷的通常低的产率。该工艺包括甲烷的氧化偶联(ocm)和甲烷部分氧化(pox)为氢和一氧化碳,随后进行氢甲酰化。目标产物是上述丙醛,其必须如此分离。限制来自于甲烷氧化偶联为乙烯,目前通常仅实现较低的转化率和有限的选择性。
16.刚刚提到的工艺中的氢甲酰基化反应在典型的催化剂上在115℃和1巴下在有机溶剂中进行。对(不期望的)副产物乙烷的选择性为约1%-4%,而据报道对丙醛的选择性达到超过95%,通常超过98%。在此没有进一步描述工艺步骤的广泛整合或作为副产物形成的大量二氧化碳的使用,尤其是在甲烷的氧化偶联中,因此与传统工艺相比存在缺点。因为在该工艺中使用部分氧化作为氧化偶联的下游步骤,即存在顺序的相互联系,所以在部分氧化中必须从氧化偶联中处理或以很高的费用分离大量的未反应的甲烷。
17.us 6,049,011a描述了在稀释物流中乙烯的氢甲酰化工艺。乙烯尤其可以由乙烷形成。除了丙醛之外,还可以生产丙烷作为目标产物。形成的醇也可进一步脱水成烯烃。然而,该出版物也没有公开用于分离较低沸点化合物的任何进一步的整合或有利的解决方案。
18.本发明旨在提供一种由醛制备目标产物(如醇或烯烃)的改进的工艺。
技术实现要素:19.在此背景下,本发明提出了一种具有独立权利要求的各个特征的使用醛制备目标化合物的工艺和相应的设备。本发明的优选实施例是从属权利要求和以下描述的内容。
20.根据本发明,醛作为合成目标化合物的起始化合物,可选地通过一种或多种中间体。醛可以通过也可以是本发明一部分的过程步骤提供。目标化合物特别可以是醇,它可以由醛形成,特别是通过氢化,但也可以是烯烃,烯烃反过来可以由这样的醇制备,特别是通
过脱水。因此,在后一种情况下,产生烯烃作为目标产物,醛经由醇作为中间体转化为烯烃。更一般地,在本发明的上下文中,目标产物表示由醛形成的醇或再由醇形成的化合物。因此,在下文中,当“醇”被提及时,它是目标产物或中间产物。
21.无论本发明的具体实施例如何,即,无论提供哪种目标产物,在本发明的上下文中,醛是在组分混合物中提供的,该组分混合物包含沸点低于醛的组分,特别是沸点低于0℃的组分。
22.根据本发明,使用萃取蒸馏从组分混合物形成富含醛和贫沸点低于醛的组分的(醇)合成进料,并进行反应以形成作为目标或中间产物的醇。根据本发明,至少部分醇由此用于形成萃取蒸馏中使用的夹带剂。形成目标产物的反应也可以是得到目标产物过程中的几个合成步骤之一。
23.在本发明的上下文中,醛和醇特别是具有相同链长的线性碳链的化合物,分别具有末端醛基和末端醇基。链长可以是2至20,特别是2至10,进一步特别是2、3、4、5、6或7。特别地,醛是丙醛,醇是1-丙醇。如果目标化合物是由醇形成的化合物而不是醇本身,目标化合物特别地可以是烯烃,特别地,在刚才解释的情况下是丙烯。然而,本发明不限于此,尽管下面的解释主要涉及这些化合物。
24.如果这里进一步提到“一种”醛被转化为“一种”醇,并可能进一步转化为“一种”烯烃,可以理解对应的工艺变体也可以包括几种相应化合物的处理。沸点低于醛的化合物特别可以是较轻的烃类,例如甲烷、乙烷或乙烯,以及沸点低于醛的非烃类,例如二氧化碳、一氧化碳、和氢气。特别地,所提到的化合物比液体形式的水沸点更低。
25.如上所述,本发明包括在含有沸点低于醛的组分的组分混合物中提供醛。具体地,如下文所述,甲烷的氧化脱氢和/或氧化偶联,各自然后进行氢甲酰化,可用于这方面,但也可使用提供适当组分混合物的任何合适的其他工艺。本发明不限于此,但本发明可以包括对应的工艺步骤,例如根据已经提及的de102019119543、de102019119562和de102019119540,作为所提出的工艺的一部分,并且特别有利地也适用于其中显著量的沸点低于醛的提及的组分包含在组分混合物中的工艺,例如适用于包括甲烷的氧化偶联步骤的工艺。
26.正如在开始时已经提到的,氧化脱氢基本上是从现有技术中原已知的工艺。在本发明的上下文中,已知的工艺概念可用于氧化脱氢。例如,在本发明的氧化脱氢中,公开了如文献cavani et al,catal.today 2007,127,113中公开的工艺。特别地,v、sr、mo、ni、nb、co、pt和/或ce和其他含金属的催化剂可以与硅酸盐、氧化铝、分子筛、膜和/或整体性载体结合使用。例如,对应金属的组合和/或氧化物,例如movtenb氧化物和ni与nb、cr和v的混合氧化物也可用于本发明中。例如,文献melzer et al,angew.chem.2016,128,9019;et al,chemcatchem 2013,5,3196;和meiswinkel,"oxidative dehydrogenation of short chain paraffins",dgmk-tagungsbericht 2017-2,isbn 978-3-941721-74-6,以及申请人的各种专利和专利申请。
27.在基本上所有的工艺变体中,氧化脱氢的典型副产物是相应的羧酸,即在乙烷氧化脱氢的情况下,是可能必须分离的乙酸,但可能代表另外的有价值的产物,并且通常以百分之几的含量存在(最高至低两位数百分比范围)。也形成低百分比范围的一氧化碳和二氧化碳。乙烷的氧化脱氢的典型产物混合物具有例如以下混合比例:
[0028][0029][0030]
相比之下,典型的甲烷的氧化偶联产物混合物具有如下混合物比例:
[0031][0032]
这些数字在每种情况下都是指产物混合物的干燥部分,取决于工艺,其可以含有水蒸气。其它组分可以痕量存在,即通常少于1%。这里应当提到的是,除非另外明确说明,否则本公开中描述的所有比例和数量比是指物质的量(在气体的情况下,其通常还对应于体积分数)。
[0033]
由于在本发明的优选实施例中使用甲烷的氧化偶联,因此在下面首先对其进行更详细地说明。文献中描述了甲烷的氧化偶联,例如j.a.kent(编)的《handbook of industrial chemistry and biotechnology》,卷2,第12版,springer,纽约,2012中j.d.idol等人的“natural gas”。然而,原则上,在本发明的范围内,加工其它气体混合物,即不是由氧化偶联提供的气体混合物,也可能的和有利的,如果这些气体混合物含有一种或多种含量显著的烯烃,例如超过10摩尔%、20摩尔%、30摩尔%、40摩尔%、或50摩尔%以及高至80摩尔%(作为单独或总和值)和同样在此数量范围内的一氧化碳。本发明在下面具体参考甲烷的氧化偶联和在氧化偶联中形成的乙烯进行描述,但并不意味着对此进行限制。
[0034]
根据目前的知识,甲烷的氧化偶联涉及甲烷与氧的催化气相反应,其中从两个甲烷分子的每个中分离出一个氢原子。氧气和甲烷在催化剂表面被活化。所得到的甲基首先反应形成乙烷分子。在反应过程中还形成水分子。然后在合适的甲烷与氧气的摩尔比、合适的反应温度、和选择合适的催化条件下,乙烷发生氧化脱氢得到乙烯,该乙烯是甲烷氧化偶联中的目标化合物。在该过程中,形成另一水分子。所用的氧在上述反应中通常完全转化。
[0035]
甲烷的氧化偶联的反应条件通常包括500℃至900℃的温度、0.5mpa至1mpa的压力和高空速。最近的发展也朝着使用较低温度的方向发展。该反应可以在固定床或流化床中
均相和多相催化进行。在甲烷的氧化偶联中,也可以形成具有多至六或八个碳原子的高级烃,但是焦点集中在乙烷或乙烯以及可能还有丙烷或丙烯。
[0036]
特别是由于甲烷分子中碳和氢之间的高结合能,甲烷氧化偶联的产率相对较低。通常,不超过10%至15%的所用甲烷被转化。此外,断裂这些键所需的相对苛刻的反应条件和温度也有利于甲基和其它中间体进一步氧化成一氧化碳和二氧化碳。特别地,在此使用氧气起到双重作用。因此,甲烷转化率取决于混合物中的氧浓度。副产物的形成与反应温度有关,因为甲烷、乙烷、和乙烯的完全氧化优选在高温下发生。
[0037]
尽管低产率和一氧化碳和二氧化碳的形成可以通过选择优化的催化剂和适合的反应条件而部分地抵消,但是在甲烷的氧化偶联过程中形成的气体混合物除了目标化合物(如乙烯)和可能的丙烯之外,还主要含有未反应的甲烷以及二氧化碳、一氧化碳和水。由于可能发生的任何非催化裂化反应,也可能存在相当大量的氢。在这里使用的术语中,这种气体混合物也称为甲烷氧化偶联的“产物混合物”,尽管它主要不包含所需产物,但也包含未反应的离析物甲烷和刚才解释的副产物。
[0038]
在甲烷的氧化偶合中,可以使用其中催化区之后是非催化区的反应器。从催化区流出的气体混合物被转移到非催化区,在那里它最初仍然以催化区中使用的相对高的温度存在。特别地,由于在甲烷氧化偶联过程中形成的水的存在,此处的反应条件类似于常规蒸汽裂化工艺的那些。因此,乙烷和高级煤油在此可以转化为烯烃。其它煤油也可加入非催化区,以使甲烷氧化偶联的余热可以特别有利的方式利用。
[0039]
在催化区下游的非催化区中的这种目标蒸汽裂化也称为“床后裂化”。术语“催化后蒸汽裂化”也将在下文中使用。当下文提及“使用”甲烷的氧化偶联形成或提供根据本发明使用的起始气体混合物的事实时,本说明书不应理解为仅必须使用氧化偶联本身来用于所述提供。相反,在提供起始气体混合物方面,还可以包括另外的工艺步骤,特别是催化后蒸汽裂化。
[0040]
在本发明的上下文中,例如在甲烷的氧化脱氢和/或氧化偶联中形成的烯烃可以与一氧化碳和氢气进行氢甲酰化以获得醛。
[0041]
氢甲酰化工艺也是现有技术中已知的。目前,rh基催化剂通常用于这些工艺中,如下面引用的文献中所述。旧的工艺也使用co基催化剂。
[0042]
例如,可以使用具有膦和/或亚磷酸酯配体的均相rh(i)基催化剂。这些可以是单齿或二齿配合物。80℃至150℃的反应温度和对应的催化剂通常用于丙醛的生产。在本发明的范围内,也可以使用现有技术中已知的所有工艺。
[0043]
氢甲酰化通常在氢气与一氧化碳的比例为1:1的条件下进行,但该比例通常可以为0.5:1至10:1。所用的rh基催化剂的rh含量可为0.01wt%至1.00wt%,配体可过量存在。更多细节描述于ullmann的《encyclopedia of industrial chemistry》2012版的文章“propanal”中。本发明不受上述工艺条件的限制。
[0044]
在另一种工艺中,例如在文献moulijn,makee&van diepen,chemical process technology,2012,235的“hydroformylation”一章中所述,对于rh基催化剂使用20巴至50巴的压力,对于co基催化剂使用70巴至200巴的压力。co似乎也与金属形式的氢甲酰化相关。其它金属或多或少是不重要的,特别是ru、mn和fe。上述工艺中使用的温度范围在370k至440k之间。
dehydration,"chemical engineering 120,2013,29。1-丙醇或2-丙醇脱水生成丙烯没有实用价值。然而,在无机酸催化剂存在下,在室温或更高温度下2-丙醇的脱水是最简单的。反应本身是吸热的和平衡受限的。低压和高温有利于高转化率。通常使用基于al2o3或sio2的非均相催化剂。通常,几种类型的酸催化剂是合适的,并且还可以使用例如分子筛和沸石。典型的温度是在200℃至250℃范围内用于乙醇脱水,或300℃至400℃范围内用于2-丙醇或丁醇脱水。由于平衡限制,通常将产物流分离(通过例如蒸馏分离烯烃产物以及至少部分水),并将含有未转化的醇的物流再循环到反应器入口。
[0053]
因此,在实施例中,本发明总体上提出了醛制备工艺的偶联,该工艺具体包括醛的制备和(至少)下游氢化,其中,氢化的醇产物或其一部分用于形成用于粗醛的萃取或萃取蒸馏的夹带剂,并相应地以这种方式循环。然而,一般说来,当所述工艺以外的工艺用于提供要对应处理的组分混合物时,醇产物也可用于在萃取蒸馏中形成夹带剂。使用“形成”夹带剂并不排除之前在其他地方使用相应的醇,例如如下所述作为吸收剂,因此夹带剂的组成不同。
[0054]
在本发明的上下文中,特别的优点尤其来自于以下事实:萃取蒸馏可以使用特别在氢化中形成的醇作为中间产物或目标产物来进行,并且剩余组分可以在萃取蒸馏中从醛生产工艺的产物混合物(“粗醛”)中分离,而不需要复杂的深冷分离步骤。特别地,不参与反应的组分,例如烷烃和二氧化碳,以及未完全反应的离析物,例如烯烃、一氧化碳和氢气,可以被携带并更容易地分离。特别地,未反应的反应物可以容易地以这种方式再循环,例如,并且再次用于反应进料中以生产醛。而且,在先前反应步骤中形成或未反应的氢气可以用于随后的氢化步骤。在此,也可以例如通过本身已知的分离步骤如变压吸附来分离和/或富集氢气。
[0055]
如上所述,在醛生产工艺中,特别是在氧化脱氢并随后氢甲酰化的形式中,在乙烷作为氧化脱氢的进料,羧酸特别可以作为进一步的副产物形成,特别是乙酸。来自提供用于氢甲酰化的进料流的工艺的这些和其它副产物和/或未反应的进料可以与反应水一起例如通过冷凝和/或水洗而相对容易地至少部分地与形成醛的步骤,特别是氢甲酰化的步骤的上游或下游的相应的进料或产物流分离。二氧化碳由于其极性同样可以相对容易地从相应的混合物中除去,由此可以使用已知的用于除去二氧化碳的工艺,特别是对应的洗涤(例如胺和/或碱洗)。不需要深冷分离,因此本发明的整个工艺,至少包括醛生产工艺,特别是氢甲酰化和萃取蒸馏不需要深冷分离步骤。
[0056]
由于在分离上游不需要干燥含醛的组分混合物,因此省略低温分离也是有利的。该优点同样适用于在分离上游从含醛的组分混合物中除去二氧化碳。在特定实施例中,可以提供干燥和/或二氧化碳去除,可能是部分的,但对于萃取蒸馏以及随后的氢化工艺不是绝对必要的。
[0057]
上述副产物和/或未反应或未完全反应的反应物的分离有利地完全非低温进行,因此在设备和能耗方面极其简单。这代表了本发明相对于现有技术的工艺的显著优点,现有技术的工艺通常需要在随后的工艺步骤中复杂地分离不期望的组分。使用该工艺内部的物流作为夹带剂还避免了将可能难以从产物混合物中分离的外来物质引入该工艺中。因此,这对产品纯度或工艺经济性具有有益的影响。
[0058]
术语“非低温”分离是指在高于0℃,特别是高于环境温度的温度水平下进行的分
离或分离步骤。然而,在任何情况下,本公开的上下文中的“非低温”还特别意味着不必使用c3和/或c2制冷剂,因此意味着至少高于-30℃,特别是高于-20℃的温度。
[0059]
与另外包含在组分混合物中的烯烃和/或烷烃相比,用于本发明的醛具有相对高的蒸气压,使得简单的蒸馏导致塔顶馏出物的对应的损失,或者蒸馏塔需要非常多的理论塔板。这样,设备复杂性和因此成本显著增加。在本发明中使用的最轻的醛丙醛的情况下尤其如此。尤其是在此,高比例的甲烷和/或乙烷由于相对接近的蒸气压和/或沸点而具有特别不利的影响。根据本发明,通过将分离设计为使用氢化中形成的醇作为萃取或夹带剂的萃取蒸馏来克服这一缺点。根据本发明,在分离步骤中仅损失非常少的醛,因为保持气态的大部分醛溶解在夹带剂中或进入底部液体中。
[0060]
通常,存在于组分混合物中的组分,例如也可根据本发明使用的组分,不能彼此无限混合。特别是,它很大程度上取决于是否出现与两种液相的溶解度间隙的设定条件。因此,合适的工艺条件的选择可受到严格限制。特别地,使用轻质醇,例如丙醇,即在本发明的上下文中作为产物或中间体形成的醇,在此再次具有有利的效果,因为然后可以将这些与水和烃二者混合。因此,通过使用本发明,可能的溶解度间隙显著减小或甚至避免。
[0061]
特别地,为了从沸点低于醛的组分中分离丙醛和丙醇,在传统蒸馏的情况下必须从这些组分中产生回流。这需要对应低的、主要是低温的头温度,这又引起混合间隙。此外,如已经解释的,在这样的低温下,通常需要二氧化碳和/或水的预先分离以防止固体沉积物(干冰/冰)的形成。这个缺点也通过使用本发明而克服。
[0062]
特别地,萃取蒸馏以这样的方式进行,使得包含在组分混合物中的醛的至少60%、70%、80%、90%、95%、99%或99.9%,但也可能包含水,被分离到塔底物流中,即被转移到在那里形成的液体馏分中,并且特别地可以被转移到随后的氢化中。
[0063]
萃取蒸馏有利地以这样的方式进行,使得至多40%、30%、20%、10%、5%、1%、或0.1%的沸点低于醛的组分被分离到塔底物流中,即被转移到在那里形成的液体馏分中。
[0064]
因此,塔底物流有利地主要由醛和作为夹带剂的醇以及可能的水组成,而萃取蒸馏的对应塔顶物流尤其由沸点低于醛的化合物组成,与醛以及可能包含在其中的水相比,该化合物在醇或夹带剂中的溶解度也较小。
[0065]
在这种情况下,应当注意的是,当水以低浓度存在时,其具有比纯水显著更高的蒸气压。这是由于以下事实,即纯水或至少高度浓缩水的蒸气压或相关沸点温度可归因于各个相邻水分子之间的强氢键。在低浓度下,仅有少数水分子彼此相邻,使得仅可形成少数氢键。在这种情况下,水组分的蒸汽压或沸点温度由分子量支配,导致相对低的沸点温度或蒸汽压。因此,取决于蒸馏进料的组成,存在于蒸馏进料中的水可以优先分离到塔顶物流中或优先分离到萃取蒸馏的塔底物流中。本发明通过根据本发明设计的萃取蒸馏避免了共沸物的形成。
[0066]
组分混合物中的氧化脱氢副产物,如果以这种方式形成,则通常是未反应的烷烃、二氧化碳和一氧化碳。在氧化偶联的情况下,由于通常低的转化率,未反应的甲烷通常尤其是组分混合物(连同二氧化碳和一氧化碳)的主要组分。这些化合物可以毫无问题地转移到随后的氢甲酰化中。一氧化碳在此可以与烯烃以及另外加入的一氧化碳一起反应,另外加入的一氧化碳可以例如源自干重整。烷烃通常在氢甲酰化中不反应。由于在氢甲酰化中形成的醛是具有较高沸点或不同极性的较重化合物,如上所述,它们可以在本发明的萃取蒸
馏中比较容易地并且非低温地与剩余的烷烃分离。
[0067]
在本发明的一个实施例中,通过氢化将醛转化为醇是特别有利的,因为氢甲酰化的产物混合物中含有的过量的氢可以用于此,这些氢已经存在于氢甲酰化上游的进料混合物中,并且可以经过氢甲酰化。因此,在本发明的范围内,特别是在基本已知类型的水煤气变换中,可以调节氢甲酰化进料混合物中氢和一氧化碳的含量。
[0068]
在根据本发明及其实施例的工艺中的任何合适的点,氢气可以进料,特别是在氢化的上游进料。因此,氢气可用于这种氢化。进料不必直接发生在加氢的上游;相反,氢气也可以通过加氢上游存在或进行的工艺或分离步骤进料。
[0069]
在本发明工艺的特别优选的实施例中,进一步提供了另外的吸收,其中使用由至少部分醇形成的吸收液体对萃取蒸馏的塔顶气体进行吸收,并获得液体馏分。以这种方式,实现了进一步改进的不期望的组分的消耗,同时具有较低的醛损失。在本发明的这个实施例中,在吸收中形成的液体馏分有利地至少部分用于形成萃取蒸馏的夹带剂。换句话说,在此首先将醇用作吸收剂,然后在已经部分负载的状态下,用作萃取蒸馏中的夹带剂。吸收剂和夹带剂相在此由于吸收中醇的负载而具有不同的组成。
[0070]
特别是,在醛的反应过程中形成的醇可以比较容易地从未反应的烷烃中分离出来。以这种方式,在这里也可以非低温地形成烷烃的循环流,并循环到例如氧化脱氢和/或氧化偶联。
[0071]
本发明还延伸到一种用于生产目标化合物的设备,关于该设备明确地参考对应的独立权利要求。对应的设备,其优选地被设置用于执行先前在各种实施例中解释的工艺,以同样的方式受益于先前已经提到的优点。
[0072]
下面的实施例,其目的在于有助于更好地理解一般说明,代表了本发明萃取蒸馏的各种有利的实施例(示例3和7a/b/c各自没有另外的吸收塔,示例4和8a/b/c各自具有另外的吸收塔)。示例2和6各自用作没有萃取和吸收的常规蒸馏的比较例。在每种情况下,压力设定为2.0mpa的压力水平。蒸馏或萃取蒸馏的理论塔板数由n(多级塔)给出,而吸收塔的塔板数n(吸收塔)仅在另外提供吸收塔时给出(示例4和8a/b/c)。
[0073]
示例1和5各自用于为后面的其他示例限定示例性输入流(也称为进料流)。
[0074]
在每种情况下,只列出烃类、丙醛、氢气、一氧化碳、和二氧化碳的质量流量(以kg/h为单位)或比例(以摩尔%为单位)。其他痕量成分,特别是水的比例不包括在内。
[0075]
实施例中的蒸馏每种都以底部(t_bottom)、顶部冷凝器(t_condenser)和流出的顶部物流(t_ovhd)的对应的温度水平为特征。温度t_feed表示来自示例1或5的进料流进入塔内的温度水平,温度t_propanol表示夹带剂丙醇进入塔内的温度水平。沸腾比值描述了沸腾后作为气体送回分离的液体和作为蒸馏塔底产物以液体形式除去的产物流的比率(分别以kg/h为单位)。
[0076]
此外,给出了来自示例1或5的进入各自蒸馏的进料流的对应质量流量和夹带剂丙醇的对应的质量流量。表flow ovhd[kg/h]和flow bottom[kg/h]指定了各自分离得到的顶部和底部流的比例组成。
[0077]
对于每一种蒸馏,计算了塔头和塔底流之间的丙醛分布作为相关的效率标准。因此:
[0078]
1.efficiency ovhd[split top:bottom,单位重量%]是顶部的丙醛与底部的丙
醛之比
[0079]
2.efficiency bottom[split bottom:top,单位重量%]是底部丙醛与顶部丙醛的之比
[0080]
即,efficiency bottom[split bottom:top,单位重量%]的值应尽可能接近100重量%,即在这种情况下丙醛完全转移至塔的底部物流中。对应地,efficiency ovhd[split top:bottom,单位重量%]的值应尽可能接近0重量%,即在这种情况下,顶部物流含有很少或不含丙醛。
[0081]
示例1-提供来自氢甲酰化工艺的进料流
[0082]
例如,将进料流a进料到氢甲酰化单元。在那里,乙烯发生了90%的转化,一氧化碳和氢气对应地按化学计量进行了转化。另外的副反应(例如乙烯加氢成乙烷和/或丙醛加氢成丙醇)在本示例中不发生,或者发生的量可以忽略不计。形成氢甲酰化反应的产物流b。
[0083]
表1:根据示例1的进料和产物流的组成。1
[0084][0085][0086]
示例2-无萃取和吸收的蒸馏(示例3和4的比较情况,不根据本发明)。
[0087]
将来自示例1的产物流b进料到该比较示例2中的蒸馏塔。确切数据见表2。
[0088]
示例3-无吸收塔的萃取蒸馏
[0089]
将来自示例1的产物流b进料到无吸收塔的萃取蒸馏中,该萃取蒸馏对应于图1所示并在下面更详细地描述的本发明的实施例。确切的数据和结果见表2。
[0090]
示例4-有吸收塔的萃取蒸馏
[0091]
将来自示例1的产物流b进料到图2所示的根据本发明实施例的并在下面进行更详细的说明的带有吸收塔的萃取蒸馏。
[0092]
显然,在所选择的条件下,与标准蒸馏(比较示例2)相比,有丙醇再循环的萃取蒸馏(示例3)已经显著减少了通过塔顶物流的丙醛损失。另外的吸收(示例4)然后导致底部物流中几乎定量的丙醛产率。
[0093]
表2:根据示例2、3和4的分离过程的比较2
[0094]
[0095][0096]
示例5
[0097]
在该示例中,提供物流c作为进料流,该进料流可以在根据本发明的工艺的一个实施例中进一步处理。这相当于在40℃下液相冷凝和分离后从物流b中剩下的气相部分。
[0098]
表3:根据示例5的物流的组成。3
[0099]
[0100][0101]
示例6-无萃取和吸收的蒸馏(实施例7和8的比较情况,不根据本发明)。
[0102]
将来自示例5的物流c进料到蒸馏塔。确切数据见表4。
[0103]
示例7a和7b-无吸收塔的萃取蒸馏
[0104]
将来自示例5的物流c进料到无吸收塔的萃取蒸馏中,该萃取蒸馏对应于图1所示并在下文中详细描述的本发明实施例。
[0105]
顶部冷凝器的温度是变化的(示例7a:30℃;示例7b:20℃)。确切的数据和结果见表4。
[0106]
示例8a、8b和8c-有吸收塔的萃取蒸馏
[0107]
根据图2所示的本发明的实施例,将来自示例5的物流c进料到带有吸收塔的萃取蒸馏。变化包括丙醇的回流(示例8a和8c:20kg/h;示例8b:15kg/h)和吸收塔中板的数量(示例8a:12;示例8b:10;示例8c:20)。顶部和底部馏分的温度水平由其他参数产生。确切的数据和结果见表4。
[0108]
在这些示例中,萃取蒸馏(示例7a和7b)已经导致efficiency ovhd值比参考例(示例6)提高多于4倍。另外的吸收(示例8a、8b和8c)再次导致塔底物流中接近定量的丙醛产量。
[0109]
表4:根据示例6、7a、7b和8a至8c的分离过程的比较4
[0110]
[0111]
[0112]
附图说明
[0113]
图1以高度简化的示意图示出了根据本发明的系统的有利设计。
[0114]
图2示出了根据本发明的系统的另一有利设计。
具体实施方式
[0115]
以下参考附图中所示系统的解释以类似的方式应用于对应的过程。为了清楚起见,在设备组件中执行的工艺骤用与各个对应设备组件相同的附图标记来表示。例如,如果说明书涉及被供给到设备组件的物质流,则这一方面应当理解为意味着在该工艺的一个实施例中,该物质流在该设备组件中经受对应的工艺步骤。另一方面,对于设备的实施例,这应理解为意味着提供例如管道形式的对应管线,在该管线中,物质流可被引导到设备组件中。这同样类似地适用于在一个工艺步骤中形成的物质流的情况,该物质流对应地从相关的设备组件中引出。
[0116]
图1所示的用于生产目标化合物6的设备100包括萃取蒸馏塔e、氢化反应器h和循环设备r。
[0117]
将组分混合物1进料到萃取蒸馏塔e中,并在那里至少部分分离,使得(醇)合成进料2作为底部产物形成,并形成塔顶产物5。组分混合物1尤其包含醛,例如丙醛。
[0118]
将夹带剂4进料到萃取蒸馏塔e中,该夹带剂含有或基本上由链长与组分混合物1中的醛相同的醇、特别是1-丙醇组成。例如,进料到萃取蒸馏塔e的头部的夹带剂4可以具有大于75%、80%、90%、95%或99%的1-丙醇含量,例如约95%的1-丙醇含量。
[0119]
在离开萃取蒸馏塔e的合成进料2中,醛相对于组分混合物1是富集的,而在组分混
合物1中含有的上述类型的其它组分,例如烯烃,特别是乙烯、一氧化碳、氢气和/或烷烃,特别是乙烷,在离开萃取蒸馏塔的合成进料2中相比组分混合物1是贫化的。合成进料2还含有较大比例的夹带剂4。
[0120]
根据组分混合物1的供应b的实施方式,组分混合物1可具有非常高的甲烷含量(例如,当使用甲烷的氧化偶联时),例30%至90%,但在其它实施方式中也可基本上不含甲烷(例如,当使用氧化脱氢时)。在该实施例中,可以进一步存在例如0.1%至10%的氢和5%至50%的丙醛。此外,其它易挥发组分例如二氧化碳、一氧化碳、丙烷、丙烯、乙烷和/或乙烯可以以可变的量存在,但是它们的比例限制为总共小于50%,特别是小于30%。如已经多次提到的,这些值是指组分混合物1的干燥(即无水)部分。然而,组分混合物1也可以含有水,特别是水饱和的。在氧化脱氢的情况下,所提及的其它易挥发组分的比例通常总共至多65%,特别是至多40%。
[0121]
萃取蒸馏塔e可以例如以这样的方式操作,即夹带剂4以相当于进料到萃取蒸馏塔e中的组分混合物1的质量流量的10%至50%、特别是15%至30%、例如约25%的质量流量进料。
[0122]
萃取蒸馏塔e的塔底蒸发器在50℃至300℃、特别是100℃至280℃、尤其是150℃至250℃、例如约170℃至190℃的温度范围内操作,而对应的塔顶冷凝器在-30℃至50℃、特别是在常温(根据din 1945-1)和45℃之间的温度范围内操作,但在任何情况下都是在非低温范围内,例如约20℃。
[0123]
有利地,萃取蒸馏塔e在0.5mpa至10mpa、尤其1mpa至5mpa、例如约1.5mpa至3.5mpa的压力下操作。
[0124]
萃取蒸馏塔e特别设计为具有内件的塔,其中有利的(理论或实际)塔板数为5至100,特别是10至50,例如20。
[0125]
在通过萃取蒸馏e之后,在该实施例中的塔底物流或(醇)合成进料2含有大于85%的包含在蒸馏进料1中的丙醛,而少于15%的所用丙醛经由对应的塔顶物流5从萃取蒸馏塔e中逸出,包含在塔底物流2中的上述高挥发性其它组分至多代表塔底物流2中的痕量杂质。它们的累积含量被限制在低两位数ppm范围内,例如低于20ppm。萃取剂4基本上完全进入塔底物流,特别是达到超过85%、90%、95%或99%的比例,使得其在塔底物流2中的比例为20%至90%,特别是30%至70%,例如约45%至55%。
[0126]
因此,塔顶物流5仅含有少量夹带剂4,但蒸馏进料1的易挥发组分以占绝大部分存在,特别是大于99%或大于99.9%。
[0127]
塔底物流2作为进料2在萃取蒸馏塔e的下游被送入氢化反应器h。除了进料2之外,氢气(图中未示出)也被送入氢化反应器。例如,可以使用吸附和/或膜法从萃取蒸馏塔e的塔顶物流5中分离出氢气。进料2中所含的醛(丙醛)与氢在氢化反应器h中反应形成对应的醇(1-丙醇)。通常,实现了大于85%、90%、95%、99%或99.9%的高至几乎完全的转化率,同时具有远远超过90%的高产物选择性。
[0128]
因此,离开氢化反应器的产物流3可以基本上由形成的醇组成,并且可能仍然具有少量未反应的醛和氢气。部分产物流3可以作为稀释流7再循环到氢化反应器h上游的(醇)合成进料2中,以允许更好地控制氢化反应器h中的工艺条件。可以利用稀释流7来降低待反应的醛的浓度。因此,可以调节待转化的醛的浓度,并且还可以影响反应器h中的主要温度。
[0129]
产物流3的另一部分被供给到循环设备r,在该循环设备r中发生产物流3的分流。产物流中所含的至少部分醇作为夹带剂4返回到萃取蒸馏塔e中,而另一部分产物流3作为目标化合物6从设备100中排出,可选地使用另外的反应器和/或纯化段。
[0130]
产物流3中可能含有的氢气可以与萃取剂一起循环到萃取蒸馏塔,在萃取蒸馏塔中,如上所述,大部分氢气通过在那里形成的塔顶物流5排出。产物流中含有的任何未反应的醛也可以与夹带剂4一起循环到萃取蒸馏塔e中,并因此循环到氢化反应器h上游的进料2中。
[0131]
图2所示的用于生产目标化合物6的系统200的组件基本上对应于已经结合图1详细描述的系统100的组件,因此系统200的对应的组件用与系统100的那些相同的附图标记表示,并且仅为了清楚起见不再重复描述。
[0132]
与设备100相比,图2所示的设备200还具有吸收塔a,萃取蒸馏塔e的塔顶物流5进料到吸收塔a的底部,吸收剂8进料到吸收塔a的顶部。原则上,吸收塔a的操作与萃取蒸馏塔e的操作相同,但两者的操作参数彼此不同。因此,在该示例中,吸收塔在20℃至60℃、特别是30℃至50℃、例如约40℃的塔底温度下操作。
[0133]
吸收塔的(理论或实际)板数可以在5和30之间,尤其在10和15之间,例如12。
[0134]
例如,吸收剂8也可以含有来自产物流3的醇。然而,在特定实施例中也可以设想使用不同的吸收剂8以使经由吸收塔塔顶物流9的产物损失最小化。吸收塔的液体塔底物流可以与萃取剂4和/或在萃取蒸馏塔e的塔顶冷凝器中形成的冷凝物流一起循环到萃取蒸馏塔e的顶部。
[0135]
由于所形成另外的分离阶段,蒸馏进料1中所含的醛被显著更有效地分离到萃取蒸馏塔的塔底物流中,使得吸收塔的塔顶物流9实际上不再含有醛,或者离开吸收塔的醛相比蒸馏进料1中所含的醛的比例为小于1%、1
‰
、100ppm或10ppm。因此,使用设备200的本发明工艺的总产率特别高,而没有牺牲选择性。
[0136]
这里应特别指出,吸收塔a不必直接位于萃取蒸馏塔e的顶部,如图2所示,尽管从工艺经济性的观点来看这是优选的布置。然而,例如空间填充要求可能需要不同的布置,以从该变型的优点中获益。
[0137]
还可以在设备100或200的萃取蒸馏塔e的上游设置冷凝器,其用于液化存在于蒸馏进料1中的大部分醛并将其单独地转移到氢化反应器中,使得萃取蒸馏塔e可以尺寸较小,因为必须处理较小总体积流量的蒸馏进料1。
[0138]
在任何情况下,提供供应单元b以提供氢化所需的醛h。如开始所述,例如,供应单元b可以包括一个或多个用于二氧化碳的干重整、用于甲烷的氧化偶联、用于乙烷的氧化脱氢和/或用于乙烯的氢甲酰化的反应器,以及用于纯化相应的物质流的相应分离设备。可选地,离开萃取蒸馏塔e和/或吸收塔a的一部分塔顶物流5、9可以再循环到供应单元b的一个或多个反应器,这又可以提高设备100、200的总效率。