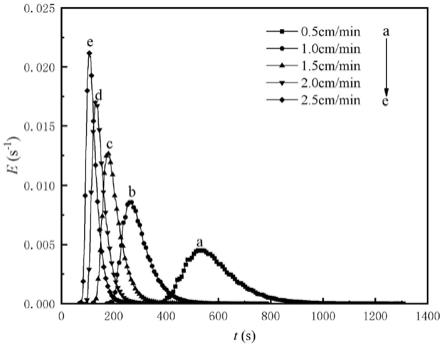
1.本发明属于生化分离领域,具体涉及一种规模化制备整体晶胶柱的方法。
背景技术:2.晶胶是采用低温冷冻和结晶致孔法制备得到的具有发达孔隙结构的聚合物材料,具有较好的渗透性、较高的比表面积、较强的机械强度和弹性,这些特性可以显著提高其传质性能,且生物相容性好,易于保存和循环使用。在层析分离生物大分子方面具有显著优势,近年来成为生化分离领域的研究热点。
3.晶胶制备过程采用溶剂结晶成型后占位得到多孔结构,同时反应物在有限空间进行聚合反应生成交联聚合物。但是,目前多用单根小尺寸小容量的玻璃柱作为载体模具制备晶胶介质,制备出来的晶胶体积都较小,对生物料液的处理量远未能达到工业化生产水平。
4.受限于结晶致孔温度的要求,对规模化制备晶胶的研究较少。因此,研发规模化制备技术,优化操作条件,降低成本,实现大规模生产,在生化分离领域具有十分重要的意义。
技术实现要素:5.针对现有技术存在的上述技术问题,本发明的目的在于提供一种规模化制备整体晶胶柱的方法,本发明在分离式多孔反应器内通过低温冷冻结晶致孔实现晶胶柱的批量化制备,制备方法安全高效,制得的晶胶柱性能稳定。本发明提供的方法,是对晶胶关键制备步骤的放大,所得晶胶柱外形均一、内部孔隙分布均匀、机械强度及稳定性好、传质能力佳,具有制备过程简单、安全高效、操作灵活等优点。
6.所述的一种规模化制备整体晶胶柱的方法,其特征在于,采用分离式多孔反应器进行规模化制备整体晶胶柱,分离式多孔反应器包括反应槽和多孔板,多孔板上均布有若干相同的孔位,多孔板可拆卸分离的沉浸于反应槽内,以便于后期晶胶柱的脱模取出;将用于制备晶胶柱的反应液加入至分离式多孔反应器内,反应液进入多孔板的孔位中,然后通过低温冷冻结晶致孔实现多孔板上整体晶胶柱的批量化制备。
7.所述的一种规模化制备整体晶胶柱的方法,其特征在于,所述反应槽和多孔板均为不锈钢材质。
8.所述的一种规模化制备整体晶胶柱的方法,其特征在于,所述的制备方法包括以下步骤:
9.1)将分离式多孔反应器置于冷冻槽中,于-2~-10℃温度下预冷1~1.5h;
10.2)以水作为溶剂,依次加入反应单体、交联剂、引发剂和加速剂,在冰浴下混匀得混合溶液,即得用于制备晶胶柱的反应液;
11.3)将步骤2)所得反应液加入至分离式多孔反应器内,反应液进入多孔板的孔位中,采用阶段式降温法,进行冷冻聚合反应;
12.4)步骤3)反应结束后将多孔板从反应槽中取出,自然解冻后,将多孔板的孔位中
的晶胶柱脱模取出,用纯水对晶胶柱进行浸泡冲洗处理以去除未反应的物质后,得到所述批量化制备的晶胶柱。
13.所述的一种规模化制备整体晶胶柱的方法,其特征在于,步骤2)中反应单体为甲基丙烯酸羟乙酯、甲基丙烯酸丁酯和甲基丙烯酸缩水甘油酯中的至少一种,交联剂为聚乙二醇二丙烯酸酯、亚甲基双丙烯酰胺中的至少一种,所述引发剂为过硫酸铵,加速剂为四甲基乙二胺。
14.所述的一种规模化制备整体晶胶柱的方法,其特征在于,所述反应单体、交联剂、引发剂和加速剂的投料质量比为1:0.05~0.2:0.003~0.01:0.003~0.01,优选为1:0.1~0.13:0.005~0.006:0.005~0.006。
15.所述的一种规模化制备整体晶胶柱的方法,其特征在于,步骤3)中采用阶段式降温法的具体过程为:进行阶段式降温,温度变化过程为-5℃~-10℃~-15℃~-20℃四个阶段温度,除-20℃之外的其余各阶段温度下反应时间20~40min,上一阶段温度反应结束后于3~10min内降温至下一阶段温度,当温度到达-20℃后,继续冷冻20~25h。所述步骤3)中,在低温聚合反应过程会有反应热产生,通过阶段式降温,确保各反应阶段多孔反应器各部分温度分布均匀。
16.所述的一种规模化制备整体晶胶柱的方法,其特征在于,所述多孔板上的孔位为空心腔柱,其直径为5~20mm、高度为15~20mm,多孔板上的孔位数量为180~240。
17.所述的一种规模化制备整体晶胶柱的方法,其特征在于,步骤4)制备的晶胶柱为多孔网状结构,晶胶柱的高度为2~15mm、直径为5~20mm,晶胶柱孔隙的孔径为200~1000μm,孔隙率为80~92%,外形均一、孔隙分布均匀、具有较高稳定性及良好的传质能力。
18.与现有技术相比,本发明的有益技术效果在于:
19.1.本发明设计的分离式多孔反应器由反应槽和多孔板两部分组成,反应槽设计可避免冷冻剂与反应物直接接触;多孔板沉浸于反应槽内,可拆卸分离,便于晶胶柱的脱模取出。多孔板中孔径尺寸和孔数可根据制备需要设计,可同步实现不同数量和尺寸晶胶柱的批量化制备。
20.2.本发明设计的分离式多孔反应器以不锈钢为材质,成本低、导热性好,耐腐蚀可在极端环境下使用,对制冷设备要求低,能耗低。
21.3.本发明的规模化制备方法,具有制备过程简单、操作方便、灵活性大等优点。所得晶胶柱直径为5~20mm,高度为2~15mm,孔隙率可达80~92%,渗透率为4.455
×
10-12
~7.289
×
10-12
m2,按相同的制备方法制备得到同类型普通小尺寸单根整体晶胶柱的孔隙率为82~90%,渗透率为1.964
×
10-12
~ 9.18
×
10-12
m2,两者相比,本发明制备的晶胶柱性能更优。
附图说明
22.图1a为本发明的分离式多孔反应器的整体结构示意图;
23.图1b为反应槽的结构示意图;
24.图1c为多孔板的结构示意图;
25.图2为本发明实施例1制备的晶胶柱的扫描电镜图片。
26.图3为本发明实施例1制备的晶胶柱测试的压降与流量的关系图。
27.图4为本发明实施例1制备的晶胶柱测试的不同流速的停留时间分布曲线。
28.图5为本发明实施例2制备的晶胶柱的扫描电镜图片。
29.图6为本发明实施例2制备的晶胶柱测试的压降与流量的关系图。
30.图7为本发明实施例2制备的晶胶柱测试的不同流速的停留时间分布曲线。
31.图8为本发明实施例3制备的晶胶柱扫描电镜图片。
32.图9为本发明实施例3制备的晶胶柱测试的压降与流量的关系图。
33.图10为本发明实施例3制备的晶胶柱测试的不同流速的停留时间分布曲线。
34.图11为本发明实施例4制备的晶胶柱扫描电镜图片。
35.图12为本发明实施例4制备的晶胶柱测试的压降与流量的关系图。
36.图13为本发明实施例4制备的晶胶柱测试的不同流速的停留时间分布曲线。
具体实施方式
37.下面结合具体实施例对本发明作进一步说明,但本发明的保护范围并不限于此。
38.实施例1
39.分离式多孔反应器的整体结构如图1a所示,分离式多孔反应器由反应槽和多孔板组成,反应槽和多孔板的结构分别如图1b和图1c所示。多孔板上均布有若干相同的孔位,多孔板可拆卸分离的沉浸于反应槽内,以便于后期晶胶柱的脱模取出。其中,多孔板上的孔位为空心腔柱,其直径为15mm、高度为 15mm,多孔板上的孔位数量为200。
40.首先,将分离式多孔反应器在低温恒温槽内于-5℃条件下预冷1h;称取 13.8g甲基丙烯酸羟乙酯、4.1g聚乙二醇二丙烯酸酯、20g聚甲基丙烯酸丁酯纳凝胶和161.6g纯水配置成单体溶液,放在冰水浴中预冷搅拌混匀;随后依次加入0.2g过硫酸铵和0.2g四甲基乙二胺,迅速搅拌均匀得到反应液,再将反应液移入分离式多孔反应器的多孔板的直径15mm、高度15mm的孔位中,每个孔位加入0.53ml反应液;采用阶段式降温法,温度变化过程为-5℃~
ꢀ‑
10℃~-15℃~-20℃,除-20℃之外的其余各阶段温度下反应时间均为30 min(即是在-5℃、-10℃和-15℃三个阶段温度下均是保温反应30min),上一阶段温度反应结束后于5min内降温至下一阶段温度,温度到达-20℃后,继续冷冻22h,随后自然解冻,脱模取出后用纯水多次浸泡冲洗除去未反应的物质,得到批量的直径15mm、高度3mm的晶胶柱,保存备用。
41.将所得直径15mm、高度3mm晶胶柱填充至内径15mm的层析柱内,填充数量20个至柱高6cm,测试晶胶柱的基础性能。
42.通过称重法测定晶胶柱的孔隙率,具体操作步骤为:截取层析柱的晶胶柱部分并浸入超纯水使其吸水饱和,再往量筒里装一定量的超纯水(密度为ρw),并记录此时体积为v1,吸饱和的晶胶放入量筒中记录体积v2,吸水饱和的晶胶质量为mw,将晶胶的非结合水用滤纸挤压吸干记录质量ms。孔隙率计算公式如下:
[0043][0044]
通过测定单位时间内流经床柱的流体流量和对应的压降利用达西方程进行计算晶胶柱的渗透率。方法如下:将晶胶柱与不同高度的水柱连通,维持水柱的高度不变,测量晶胶柱出口的流量再将水柱高度转换为压差,根据达西定律,对所得流量-压差进行线性回
归。
[0045]
渗透率kw计算公式如下:
[0046][0047]qw
为流体流量(m3/s),μw为超纯水的粘度(pa
·
s),l为晶胶柱的长度 (m),
△
pw为压降(pa),a为晶胶柱的截面积(m2)。
[0048]
停留时间分布通过脉冲示踪法测定。实验方法为:首先用20mmol/lph 7.2 的磷酸盐缓冲液平衡晶胶柱,随后用含有3%(v/v)丙酮的20mmol/lph 7.2 的pbs缓冲液为示踪剂,通过六通进样阀将含有150μl丙酮的溶液流过晶胶,用280nm波长紫外检测仪在线检测,得到了停留时间分布图像,其中e为分布密度函数,t为时间。
[0049]
图2~图4分别为本发明实施例1制备的晶胶柱的扫描电镜图片,压降与流量的关系图片和不同流速下的停留时间分布图片。由扫描电镜图可知,制备的晶胶柱有丰富的相互联通的孔隙结构,测定的孔隙率为87.4%~88.1%,渗透率为1.434
×
10-12
~2.179
×
10-12
m2,传质性能良好。
[0050]
按照实施例1晶胶柱的制备过程,当冷冻聚合反应是直接在低温下进行时,即直接降到最低温-20℃下反应24h,反应结果显示:聚合反应不太均匀,最终晶胶柱的孔隙率不理想(平均孔隙率在80%以下),弹性比较差。
[0051]
实施例2
[0052]
分离式多孔反应器的多孔板上的孔位为空心腔柱,其直径为15mm、高度为15mm,多孔板上的孔位数量为200。
[0053]
首先,将分离式多孔反应器在低温恒温槽内于-5℃条件下预冷1.5h;称取13.8g甲基丙烯酸羟乙酯、4.1g聚乙二醇二丙烯酸酯、20g聚甲基丙烯酸丁酯纳凝胶和161.6g纯水配置成单体溶液,放在冰水浴中预冷搅拌混匀;随后依次加入0.2g过硫酸铵和0.2g四甲基乙二胺,迅速搅拌均匀得到反应液,再将反应液移入分离式多孔反应器的多孔板的孔位中,每个孔位加入1.24ml 反应液;采用阶段式降温法进行冷冻聚合反应(阶段式降温法的具体操作步骤重复实施例1中)后,自然解冻,脱模取出后用纯水多次浸泡冲洗除去未反应的物质,得到批量的直径15mm、高度7mm的晶胶柱,保存备用。
[0054]
将所得直径15mm、高度7mm晶胶柱填充至内径15mm的层析柱内,填充数量9个至柱高6.3cm,测试晶胶柱的基础性能。
[0055]
测试方法如实施例1所示。
[0056]
图5~图7分别为本发明实施例2制备的晶胶柱的扫描电镜图片,压降与流量的关系图片和不同流速下的停留时间分布图片。由扫描电镜图可知,制备的晶胶柱有丰富的相互联通的孔隙结构,测定的孔隙率为84.1%~86.8%,渗透率为1.897
×
10-12
~2.434
×
10-12
m2,传质性能良好。
[0057]
实施例3
[0058]
分离式多孔反应器的多孔板上的孔位为空心腔柱,其直径为10mm、高度为15mm,多孔板上的孔位数量为200。
[0059]
首先,将分离式多孔反应器在低温恒温槽内于-5℃条件下预冷1h;称取13.8 g甲基丙烯酸羟乙酯、4.1g聚乙二醇二丙烯酸酯、20g聚甲基丙烯酸丁酯纳凝胶和161.6g纯水配
置成单体溶液,放在冰水浴中预冷搅拌混匀;随后依次加入0.2g过硫酸铵和0.2g四甲基乙二胺,迅速搅拌均匀得到反应液,再将反应液移入分离式多孔反应器的多孔板的直径10mm、高度15mm的孔位中,每个孔位加入0.79ml反应液;采用阶段式降温法进行冷冻聚合反应(阶段式降温法的具体操作步骤重复实施例1中)后,自然解冻,脱模取出后用纯水多次浸泡冲洗除去未反应的物质,得到批量的直径10mm、高度10mm的晶胶柱,保存备用。
[0060]
将所得直径10mm、高度10mm晶胶柱填充至内径10mm的层析柱内,填充数量6个至柱高6cm,测试晶胶柱的基础性能。
[0061]
测试方法如实施例1所示。
[0062]
图8~图10分别为本发明实施例3制备的晶胶柱的扫描电镜图片,压降与流量的关系图片和不同流速下的停留时间分布图片。由扫描电镜图可知,制备的晶胶柱有丰富的相互联通的孔隙结构,测定的孔隙率为89.4%~91.6%,渗透率为4.134
×
10-12
~6.579
×
10-12
m2,传质性能良好。
[0063]
实施例4
[0064]
分离式多孔反应器的多孔板上的孔位为空心腔柱,其直径为10mm、高度为15mm,多孔板上的孔位数量为200。
[0065]
首先,将分离式多孔反应器在低温恒温槽内于-5℃条件下预冷1.5h;称取13.8g甲基丙烯酸羟乙酯、4.1g聚乙二醇二丙烯酸酯、20g聚甲基丙烯酸丁酯纳凝胶和161.6g纯水配置成单体溶液,放在冰水浴中预冷搅拌混匀;随后依次加入0.2g过硫酸铵和0.2g四甲基乙二胺,迅速搅拌均匀得到反应液,再将反应液移入分离式多孔反应器的多孔板的直径10mm、高度15mm的孔位中,每个孔位加入1.2ml反应液;采用阶段式降温法进行冷冻聚合反应(阶段式降温法的具体操作步骤重复实施例1中)后,自然解冻,脱模取出后用纯水多次浸泡冲洗除去未反应的物质,得到批量的直径10mm、高度15mm的晶胶柱,保存备用。
[0066]
将所得直径10mm、高度15mm晶胶柱填充至内径10mm的层析柱内,填充数量4个至柱高6cm,测试晶胶柱的基础性能。
[0067]
测试方法如实施例1所示。
[0068]
图11~图13分别为本发明实施例4制备的晶胶柱的扫描电镜图片,压降与流量的关系图片和不同流速下的停留时间分布图片。由扫描电镜图可知,制备的晶胶柱有丰富相互联通的孔隙结构,测定的孔隙率为85.8%~87.6%,渗透率为3.289
×
10-12
~3.827
×
10-12
m2,传质性能良好。
[0069]
本说明书所述的内容仅仅是对发明构思实现形式的列举,本发明的保护范围不应当被视为仅限于实施例所陈述的具体形式。