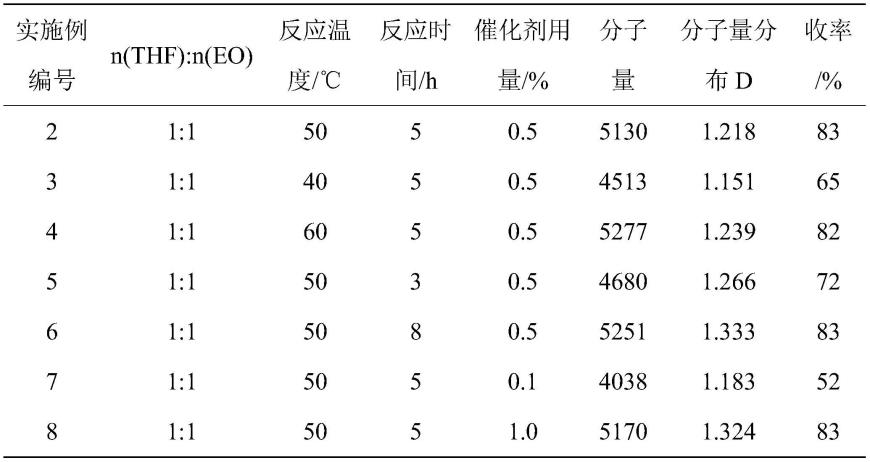
1.本发明涉及一种离子液体催化剂及其催化合成四氢呋喃环氧乙烷共聚醚的方法,更具体的说本发明涉及以催化剂催化得到四氢呋喃环氧乙烷共聚醚的方法,属于有机聚醚领域。
背景技术:2.四氢呋喃环氧乙烷共聚醚是以环氧乙烷(eo)、四氢呋喃(thf)为原料,在催化剂作用下共聚制得的线型聚合物,其主链由亚甲基(-ch2)和醚键(-o-)组成,具有良好的柔顺性。根据资料显示:四氢呋喃的均聚物或环氧乙烷的均聚物都易结晶,但对共聚醚来说由于两种单体的共聚破坏了高分子链结构的规整性,所以它不易结晶。常温下为液态稳定,在使用时不会产生微小裂纹。因此,可用作硝酸酯增塑的聚醚nepe等火箭推进剂重要粘合剂。用四氢呋喃环氧乙烷共聚醚还可以合成共聚醚型氨酯制品,因为耐磨性好、涂层硬度大、附着力好、耐候性好、耐化学品性好,在家具涂料、地板漆、汽车防腐、交通道路用漆等方面应用广泛。
3.四氢呋喃环氧乙烷开环聚合是一个典型的酸催化反应,其中催化剂是整个聚合反应的核心。目前,传统的聚合催化剂通常为质子酸如发烟硫酸、高氯酸等。由于此类催化剂在使用中存在很多缺点,如催化剂无法回收、产生大量废液、对设备腐蚀性大、环境污染严重等,因此使用受到限制。综上,有必要进一步开发四氢呋喃环氧乙烷共聚醚新的绿色环保制备工艺来解决前述的这些问题。
技术实现要素:4.鉴于此,本发明的目的是提供一种离子液体催化剂及其催化合成四氢呋喃环氧乙烷共聚醚的方法,该方法是以离子液体作为催化剂,催化效果佳,成功获得分子量在4000-6000的窄分布(d《1.4)产品,产率达83%,且具有不腐蚀设备、三废量少、绿色环保等优点。
5.为了实现上述目的,本发明提供一种离子液体催化剂及其催化合成四氢呋喃环氧乙烷共聚醚的方法。采用的技术方案如下:
6.第一方面,本发明提供一种离子液催化剂的制备方法,包括以下步骤:
7.步骤1,将3-氯丙基三乙氧基硅烷、1-甲基咪唑和nh4bf4按摩尔比1:(0.9~1.3):(0.9~1.3)备好;
8.步骤2,在n2保护下,油浴升温至110~130℃,将备好的3-氯丙基三乙氧基硅烷和1-甲基咪唑磁力搅拌回流反应22~26h,反应后冷却,真空干燥6~8h得到黄色粘稠液体中间体,记为[mim]cl;
[0009]
步骤3,将步骤2得到的[mim]cl和备好的nh4bf4溶于甲苯溶剂中,抽真空,通氮气保护,搅拌反应46~50h后,得到白色沉淀nh4cl和滤液;
[0010]
步骤4,向滤液中加入10~20%滤液总质量的中性a12o3,搅拌1.5~2.5h后滤去
a12o3,在60~70℃下,旋转蒸发除去甲苯溶剂,真空干燥8~12h得离子液体催化剂[mim]bf4。
[0011]
优选地,3-氯丙基三乙氧基硅烷、1-甲基咪唑和nh4bf4摩尔比为1:1:1。
[0012]
进一步地,所述甲苯溶剂加入量与[mim]cl投入量比例为(40~60)ml:0.1mol。
[0013]
第二方面,本发明提供一种离子液体催化剂,采用上述方法制得。
[0014]
第三方面,本发明提供一种离子催化剂催化合成四氢呋喃环氧乙烷共聚醚的方法,包括以下步骤:
[0015]
步骤1,准备原料四氢呋喃、环氧乙烷,引发剂二元醇及离子液体催化剂[mim]bf4;
[0016]
步骤2,将备好的四氢呋喃、引发剂二元醇和离子液体[mim]bf4加入高压釜中,通氮气置换3次,搅拌加热至40~60℃,加入备好的环氧乙烷,聚合反应3~8h,降温冷却,加去离子水萃取3次除去催化剂,干燥得到产品。
[0017]
进一步地,所述引发剂二元醇为乙二醇、丙二醇或丁二醇。
[0018]
进一步地,四氢呋喃和环氧乙烷的摩尔比为1:1。
[0019]
进一步地,引发剂加入量为所述原料总质量的1%。
[0020]
进一步地,所述离子液体催化剂[mim]bf4的加入量为所述原料总质量的0.1~1.0%。
[0021]
优选地,所述离子液体催化剂[mim]bf4的加入量为所述原料总质量的0.5%。
[0022]
优选地,所述聚合反应温度为50℃;反应时间为5h。
[0023]
本发明提供了一种四氢呋喃环氧乙烷共聚醚的制备方法,提出以离子液体作为催化剂,以二元醇为引发剂,在无溶剂条件下,促使四氢呋喃与环氧乙烷发生本体聚合制备四氢呋喃环氧乙烷共聚醚。结果表明,本发明的有益效果为:离子液体催化效果佳,成功获得分子量在4000-6000的窄分布(d《1.4)四氢呋喃环氧乙烷共聚醚产品,产率最高可达83%,有不腐蚀设备,三废量少、环境污染小、绿色环保等优点。
具体实施方式
[0024]
下面将结合本发明中的实施例,对本发明中的技术方案进行清楚、完整地描述。显然,所描述的实施例仅仅是本发明一部分实施例,而不是全部的实施例。基于本发明中的实施例,本领域普通技术人员在没有做出创造性劳动前提下所获得的所有其他实施例,都属于本发明保护的范围。
[0025]
实施例1
[0026]
在n2保护下,油浴升温至120℃,将0.5mol 3-氯丙基三乙氧基硅烷和0.5mol1-甲基咪唑磁力搅拌回流反应24h,反应后冷却,真空干燥7h得到黄色粘稠液体中间体,记为[mim]cl,取0.1mol的[mim]c进行以下反应;将0.1mol的[mim]cl溶于50ml甲苯溶剂中,再加入0.1mol nh4bf4,抽真空,通氮气保护,搅拌反应48h后,得到白色沉淀nh4cl和滤液;向滤液中加入15%滤液总质量的中性a12o3,搅拌2h后滤去a12o3,在65℃下,旋转蒸发除去甲苯溶剂,真空干燥10h得离子液体催化剂[mim]bf4。
[0027]
实施例2
[0028]
常温条件下,向高压釜中投入14g引发剂1,2丙二醇、7.0g实施例1制备的离子液体催化剂[mim]bf4、865g四氢呋喃,通氮气置换3次,搅拌加热至50℃时,缓慢通入529g环氧乙
烷,聚合反应5h后,降温冷却并脱气30min;加去离子水萃取3次除去催化剂,干燥得到四氢呋喃环氧乙烷共聚醚产品。结果如表1所示。
[0029]
实施例3
[0030]
常温条件下,向高压釜中投入14g引发剂1,2丙二醇、7.0g实施例1制备的离子液体催化剂[mim]bf4、865g四氢呋喃,通氮气置换3次,搅拌加热至40℃时,缓慢通入529g环氧乙烷,聚合反应5h后,降温冷却并脱气30min;加去离子水萃取3次除去催化剂,干燥得到四氢呋喃环氧乙烷共聚醚产品。结果如表1所示。
[0031]
实施例4
[0032]
常温条件下,向高压釜中投入14g引发剂1,2丙二醇、7.0g实施例1制备的离子液体催化剂[mim]bf4、865g四氢呋喃,通氮气置换3次,搅拌加热至60℃时,缓慢通入529g环氧乙烷,聚合反应5h后,降温冷却并脱气30min;加去离子水萃取3次除去催化剂,干燥得到四氢呋喃环氧乙烷共聚醚产品。结果如表1所示。
[0033]
实施例5
[0034]
常温条件下,向高压釜中投入14g引发剂1,2丙二醇、7.0g实施例1制备的离子液体催化剂[mim]bf4、865g四氢呋喃,通氮气置换3次,搅拌加热至50℃时,缓慢通入529g环氧乙烷,聚合反应3h后,降温冷却并脱气30min;加去离子水萃取3次除去催化剂,干燥得到四氢呋喃环氧乙烷共聚醚产品。结果如表1所示。
[0035]
实施例6
[0036]
常温条件下,向高压釜中投入14g引发剂1,2丙二醇、7.0g实施例1制备的离子液体催化剂[mim]bf4、865g四氢呋喃,通氮气置换3次,搅拌加热至50℃时,缓慢通入529g环氧乙烷,聚合反应8h后,降温冷却并脱气30min;加去离子水萃取3次除去催化剂,干燥得到四氢呋喃环氧乙烷共聚醚产品。结果如表1所示。
[0037]
实施例7
[0038]
常温条件下,向高压釜中投入14g引发剂1,2丙二醇、1.4g实施例1制备的离子液体催化剂[mim]bf4、865g四氢呋喃,通氮气置换3次,搅拌加热至50℃时,缓慢通入529g环氧乙烷,聚合反应5h后,降温冷却并脱气30min;加去离子水萃取3次除去催化剂,干燥得到四氢呋喃环氧乙烷共聚醚产品结果如表1所示。
[0039]
实施例8
[0040]
常温条件下,向高压釜中投入14g引发剂1,2丙二醇、14g实施例1制备的离子液体催化剂[mim]bf4、865g四氢呋喃,通氮气置换3次,搅拌加热至50℃时,缓慢通入529g环氧乙烷,聚合反应5h后,降温冷却并脱气30min;加去离子水萃取3次除去催化剂,干燥得到四氢呋喃环氧乙烷共聚醚产品。结果如表1所示。
[0041]
性能测试
[0042]
对实施例2~8制备的四氢呋喃环氧乙烷共聚醚进行性能测试,所得的性能指标结果见表1。其中,采用美国wyatt公司的dawneos型凝胶渗透色谱-多角度激光散射联用仪测定聚合物分子量(mn)及分子量分布(mw/mn),测试条件为以hplc级thf作为流动相,色谱柱为50nm,测试温度为25℃,流速为0.5ml/min。
[0043]
表1实施例2~8所制得的四氢呋喃环氧乙烷共聚醚性能指标
[0044][0045]
由表1的结果可以看出,以离子液体为催化剂可制得中等分子量(4000-6000)四氢呋喃环氧乙烷共聚醚,对比实施例2和实施例7可知,离子液体催化效果佳;对比实施例2-6可知,当四氢呋喃和环氧乙烷质量比为1:1时,在50℃下反应5h获得的共聚醚的实际相对分子质量与设计相对分子质量(5000)最接近,分子量分布《1.4,产率最高可达83%。
[0046]
以上所述仅是本发明的优选实施方式,应当指出,对于本技术领域的普通技术人员来说,在不脱离本发明原理的前提下,还可以做出若干改进和润饰,这些改进和润饰也应视为本发明的保护范围。