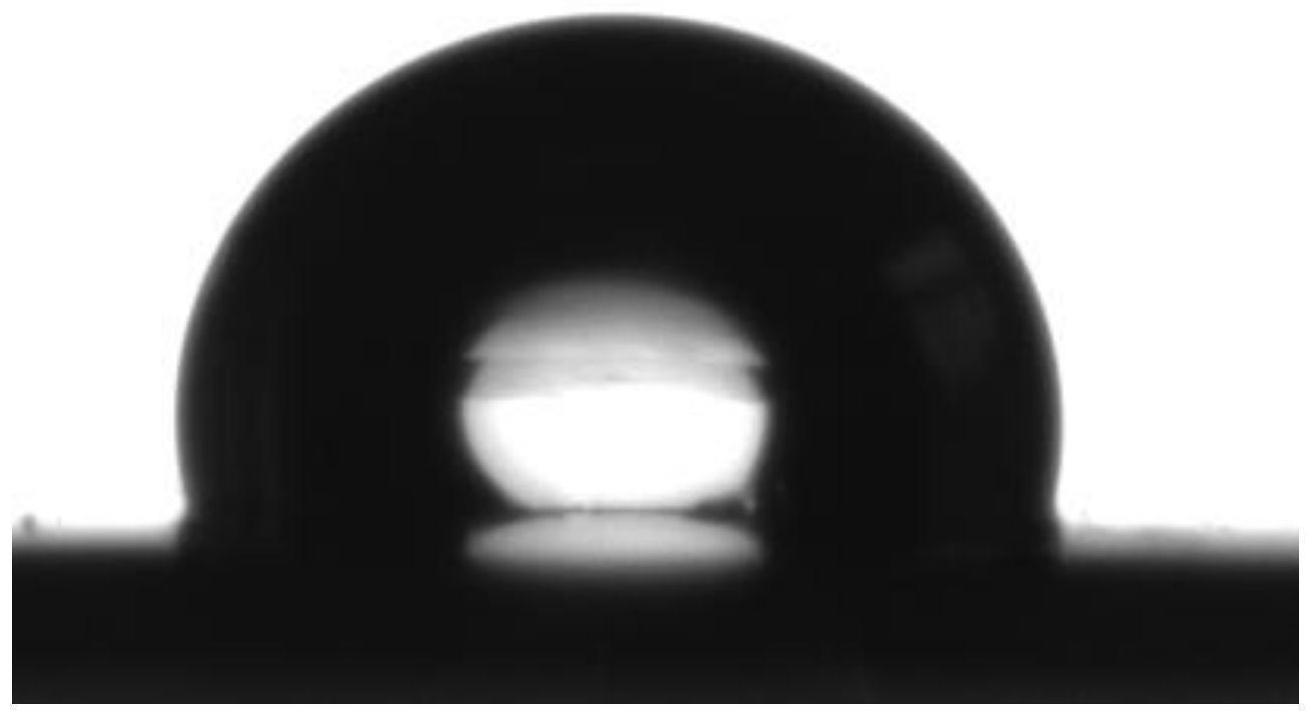
1.本发明属于高分子材料技术领域,具体涉及一种高强、自感应超支化粘结材料及其绿色制备方法以及应用。
背景技术:2.粘结材料在工程领域具有非常重要的地位,如何提高粘结材料与被粘物之间的界面结合强度是各方关注的重要课题。通过化学交联提高界面结合强度是一种通用方法,然而化学交联后一旦出现缺陷将对界面结合强度造成致命损伤,因此对工艺要求严格,且对粘结材料的回收带来挑战。在线性分子中引入极性基团或添加含有极性基团的填料,可以有效解决上述问题,但线性分子间容易发生滑移,界面结合强度较弱。更重要地,现有粘结材料在制备和使用过程中多选用有机溶剂作为稀释剂,对环境造成一定污染。部分在水相中制备得到的粘结材料则只能用于干燥环境,大大限制了其使用范围。此外,现有粘结材料只能被动粘结,而无法主动检测所承受的应力状态,导致其服役状态和瞬时强度无法实时输出。
技术实现要素:3.有鉴于此,本发明要解决的技术问题在于提供一种高强、自感应超支化粘结材料及其绿色制备方法以及应用,本发明提供的超支化粘结材料不仅具有高粘结强度,还可以对界面处所承受的应力进行自感应,实时更新服役状态,其制备和使用过程无需有机溶剂,在干燥环境和潮湿环境中均可使用且可回收,对碳中和和环境保护具有非常重要的意义。
4.本发明提供了一种高强、自感应超支化粘结材料的制备方法,包括以下步骤:
5.a)将二伯胺类单体和双丙烯酰胺类单体溶解于甲醇水溶液中,进行反应,得到超支化粘结材料内核;
6.b)将所述超支化粘结材料内核与甲基丙烯酰氧乙基三甲基氯化铵进行反应,得到端部离子化的超支化结构材料;
7.c)将所述端部离子化的超支化结构材料与水溶性有机离子盐进行离子置换,得到超支化粘结材料。
8.优选的,所述二伯胺类单体选自聚醚胺d2000、聚醚胺d400、聚醚胺d230、乙二胺、1,3-丙二胺、1,4-丁二胺、1,6-已二胺、1,8-辛二胺、萘乙二胺、月桂胺二亚丙基二胺、4,7,10-三氧-1,13-十三烷二胺、四甲基乙二胺、n,n
’‑
二甲基乙二胺、n,n
’‑
二叔丁基乙二胺、n,n
’‑
二异丙基乙二胺、芴二胺、n,n
’‑
二胺乙基-1,3-丙二胺、2,2
’‑
二吡啶-6,6
’‑
二胺、十二烷二胺中任意一种或多种任意比例的混合物。
9.优选的,所述双丙烯酰胺类单体选自n,n
’‑
亚甲基双丙烯酰胺、双丙烯酰胺、n,n
’‑
(1,2-二羟基乙烯)双丙烯酰胺、酒石酸双丙烯酰胺、n,n
’‑
乙烯基双丙烯酰胺、六亚甲基双丙烯酰胺中任意一种或多种任意比例的混合物。
10.优选的,所述二伯胺类单体与双丙烯酰胺类单体的摩尔比为1:0.5~4;
11.所述甲基丙烯酰氧乙基三甲基氯化铵与所述二伯胺类单体的摩尔比为2:0.4~4;
12.所述水溶性有机离子盐与所述甲基丙烯酰氧乙基三甲基氯化铵的摩尔比例为1:0.2~2。
13.优选的,步骤a)的反应温度为10~50℃,时间12~48h。
14.优选的,所述水溶性有机离子盐选自双三氟甲烷磺酰亚胺锂盐、双三氟甲烷磺酰亚胺钠盐、双三氟甲烷磺酰亚胺钾盐、双三氟甲烷磺酰亚胺镁盐、双三氟甲烷磺酰亚胺钙盐、双三氟甲烷磺酰亚胺锌盐、三氟甲磺酸锂盐、三氟甲磺酸钠盐、磷酸二氢锂、六氟磷酸锂、四氟硼酸锂中的一种或多种。
15.优选的,所述甲醇水溶液中,水与甲醇的体积比为2~10:1~5。
16.本发明还提供了一种上述制备方法制备得到的高强、自感应超支化粘结材料。
17.本发明还提供了一种上述高强、自感应超支化粘结材料在作为粘结剂中的应用。
18.优选的,所述粘结剂用于粘结玻璃、金属、塑料或陶瓷。
19.与现有技术相比,本发明提供了一种高强、自感应超支化粘结材料的制备方法,包括以下步骤:a)将二伯胺类单体和双丙烯酰胺类单体溶解于甲醇水溶液中,进行反应,得到超支化粘结材料内核;b)将所述超支化粘结材料内核与甲基丙烯酰氧乙基三甲基氯化铵进行反应,得到端部离子化的超支化结构材料;c)将所述端部离子化的超支化结构材料与水溶性有机离子盐进行离子置换,得到超支化粘结材料。本发明的制备方法利用离子键、氢键等非共价键协同作用赋予该超支化结构材料高强、高粘和自感应性能,对包括玻璃、金属、塑料、陶瓷等多种材料在内被粘物均表现出良好粘结能力,拉伸强度可达5mpa以上。本发明的端部离子化超分子结构材料,从水环境中反应制备得到,制备过程绿色环保无污染,对环境保护和碳中和具有非常重要的意义。且本发明的高强、自感应超支化粘结材料在干燥环境和潮湿环境中均表现出良好的粘结能力。本发明的端部离子化超分子结构材料可以探测感知不同类型的应力状态,包括正应力、剪切应力等,且均表现出灵敏的感应能力,压力响应时间在100毫秒以内,实现了粘结材料的自感应功能。另外,通过改变超支化结构内核中二伯胺和双丙烯酰胺类单体的用量可以实现超支化粘结材料性能的有效控制。
附图说明
20.图1为实施例2与水的接触角照片;
21.图2为实施例7与水的接触角照片;
22.图3为实施例8与水的接触角照片;
23.图4为对比例1与水的接触角照片;
24.图5为对比例2与水的接触角照片;
25.图6为实施例1的傅里叶红外曲线;
26.图7为实施例3的傅里叶红外曲线;
27.图8为实施例6的傅里叶红外曲线;
28.图9为实施例2的热失重曲线;
29.图10为实施例4的热失重曲线;
30.图11为实施例2粘结不同材质时的剪切强度曲线;
31.图12为实施例4粘结不同材质时的剪切强度曲线;
32.图13为实施例6粘结不同材质时的剪切强度曲线;
33.图14为实施例2承受正应力时的自感应曲线;
34.图15为实施例4承受剪切应力时的自感应曲线。
具体实施方式
35.本发明提供了一种高强、自感应超支化粘结材料的制备方法,包括以下步骤:
36.a)将二伯胺类单体和双丙烯酰胺类单体溶解于甲醇水溶液中,进行反应,得到超支化粘结材料内核;
37.b)将所述超支化粘结材料内核与甲基丙烯酰氧乙基三甲基氯化铵进行反应,得到端部离子化的超支化结构材料;
38.c)将所述端部离子化的超支化结构材料与水溶性有机离子盐进行离子置换,得到超支化粘结材料。
39.本发明首先将二伯胺类单体和双丙烯酰胺类单体溶解于甲醇水溶液中混合搅拌,进行迈克尔加成反应,得到超支化粘结材料内核;
40.其中,所述二伯胺类单体选自聚醚胺d2000、聚醚胺d400、聚醚胺d230、乙二胺、1,3-丙二胺、1,4-丁二胺、1,6-已二胺、1,8-辛二胺、萘乙二胺、月桂胺二亚丙基二胺、4,7,10-三氧-1,13-十三烷二胺、四甲基乙二胺、n,n
’‑
二甲基乙二胺、n,n
’‑
二叔丁基乙二胺、n,n
’‑
二异丙基乙二胺、芴二胺、n,n
’‑
二胺乙基-1,3-丙二胺、2,2
’‑
二吡啶-6,6
’‑
二胺、十二烷二胺中任意一种或多种任意比例的混合物。
41.所述双丙烯酰胺类单体选自n,n
’‑
亚甲基双丙烯酰胺、双丙烯酰胺、n,n
’‑
(1,2-二羟基乙烯)双丙烯酰胺、酒石酸双丙烯酰胺、n,n
’‑
乙烯基双丙烯酰胺、六亚甲基双丙烯酰胺中任意一种或多种任意比例的混合物。
42.所述二伯胺类单体与双丙烯酰胺类单体的摩尔比为1:0.5~4,优选为1:0.5、1:1、1:2、1:3、1:4,或1:0.5~4之间的任意值。
43.所述反应温度为10~50℃,优选为10、20、30、40、50,或10~50℃之间的任意值,时间12~48h,优选为12、18、24、36、48,或12~48h之间的任意值。
44.所述甲醇水溶液中,水与甲醇的体积比为2~10:1~5,优选为2:5、1:1、3:1、5:1、10:1,或2~10:1~5之间的任意值。
45.得到超支化粘结材料内核后,将所述超支化粘结材料内核与甲基丙烯酰氧乙基三甲基氯化铵进行反应,得到端部离子化的超支化结构材料。
46.其中,所述甲基丙烯酰氧乙基三甲基氯化铵与所述二伯胺类单体的摩尔比为2:0.4~4,优选为2:0.4、2:1、2:2、2:3、2:4,或2:0.4~4之间的任意值。
47.所述反应的温度为10~50℃,优选为10、20、30、40、50,或10~50℃之间的任意值,时间12~48h,优选为12、18、24、36、48,或12~48h之间的任意值。
48.接着,将所述端部离子化的超支化结构材料与水溶性有机离子盐进行离子置换,得到超支化粘结材料。
49.具体的,将水溶性有机离子盐加入至上述反应得到的端部离子化的超支化结构材料溶液中,保持室温条件进行搅拌,直至有沉淀析出。然后将所述沉淀收集后,进行洗涤干
燥,得到超支化粘结材料。
50.其中,所述洗涤用去离子水洗涤3次以上,每次洗涤时间12~24h。
51.所述水溶性有机离子盐与所述甲基丙烯酰氧乙基三甲基氯化铵的摩尔比例为1:0.2~2,优选为1:0.2、1:0.5、1:1、1:1.5、1:2,或1:0.2~2之间的任意值。
52.本发明还提供了一种上述制备方法制备得到的高强、自感应超支化粘结材料。其中,所述超支化粘结材料不仅展现出典型的粘结剂特征,拉伸强度可达5mpa以上,还能表现出优异的自感应能力,压力响应时间在100毫秒以内,对多种形式的应力均可展现出良好的自感应能力。
53.本发明还提供了一种上述高强、自感应超支化粘结材料在作为粘结剂中的应用。
54.其中,所述粘结剂用于粘结玻璃、金属、塑料或陶瓷。
55.本发明中,基于多种非共价键作用力构筑具有高强、自感应超支化结构粘结材料,采用二伯胺和双丙烯酰胺类单体通过迈克尔加成反应获得超支化结构,采用甲基丙烯酰氧乙基三甲基氯化铵继续通过迈克尔加成反应获得离子化超支化结构,随后采用双三氟甲烷磺酰亚胺金属离子盐通过置换获得具有疏水特性的离子型超支化材料。所述方法主要基于动态可逆的离子键和氢键制备高强粘结材料,实现了超支化材料的高强、高粘和自感应能力。
56.本发明的制备方法通过迈克尔加成反应、离子置换反应制备了基于离子键、氢键等非共价键的高强、自感应粘结材料,其表现出优异的力学强度、粘结性能和自感应性能。其中,迈克尔加成反应和离子置换反应均在水环境中进行,绿色环保无公害释放。基于迈克尔加成反应,通过调控超支化分子结构,实现了基于树枝状分子结构的内核制备和端部离子化制备,各超支化分子间通过离子键和氢键等非共价键相互作用,赋予材料高强、高粘特性。端部离子化特征赋予材料灵敏的压力感应特性,无需加入其他任何形式的导电性物质,即可在不同的应力环境中表现出相应的电信号,实现了自感应功能。
57.因此,控制二伯胺和双丙烯酰胺类单体的种类、数量以及水溶性有机金属离子盐的类别等,可以实现对材料性能的有效调控。
58.与现有技术相比,本发明的有益效果是:
59.1)本发明的离子键与氢键的协同耦合作用赋予超支化结构材料高强的界面结合能力,对包括玻璃、金属、塑料、陶瓷等多种材料在内被粘物均表现出良好粘结能力,拉伸强度可达5mpa以上。
60.2)本发明的端部离子化超分子结构材料,从水环境中反应制备得到,制备过程绿色环保无污染,对环境保护和碳中和具有非常重要的意义。且本发明的高强、自感应超支化粘结材料在干燥环境和潮湿环境中均表现出良好的粘结能力。
61.3)本发明的端部离子化超分子结构材料可以探测感知不同类型的应力状态,包括正应力、剪切应力等,且均表现出灵敏的感应能力,压力响应时间在100毫秒以内,实现了粘结材料的自感应功能。
62.为了进一步理解本发明,下面结合实施例对本发明提供的高强、自感应超支化粘结材料及其绿色制备方法以及应用进行说明,本发明的保护范围不受以下实施例的限制。
63.测试方法
64.采用动态接触角测量仪(dcat21)对相关超支化材料与水的接触角进行测量,每个
样品选不同区域测量五次,去平均值。
65.采用傅里叶红外光谱(nicolet 6700)对相关超支化材料的分子结构进行表征,选用分辨率为4cm-1
,扫描次数为32次。
66.采用德国耐驰公司tga2019f1对相关样品的热失重性能进行测试,测试温度为50-700℃,升温速率为20℃/min。
67.采用美特斯台式电子万能试验机(2kn)对相关样品的力学行为进行测试,其中,用lap shear强度表示粘结强度,即将相关超支化粘结材料涂敷于被粘结物表面,将两片被粘结物错位粘结,测试时分别夹住被粘物两端,从而获得力(f)-位移(δl)曲线。可根据如下公式计算得到相应的应力(σ)-位移曲线:
[0068][0069]
其中,f为力,a为粘结面积。
[0070]
采用keithley 6514对相关超支化粘结材料的自感应能力进行测量,选用电阻模式,记录承载不同压力时的电阻变化(δr)。
[0071]
实施例1
[0072]
s1.将d230和n,n
’‑
亚甲基双丙烯酰胺分别完全溶解于水/甲醇混合液中,随后将二者混合搅拌,搅拌温度30℃,搅拌时间24h;
[0073]
s2.按照设定比例将甲基丙烯酰氧乙基三甲基氯化铵加入上述s1溶液中,在相同温度继续保持搅拌24h;
[0074]
s3.按照设定比例将双三氟甲烷磺酰亚胺锂盐加入上述s2溶液中,保持室温条件继续搅拌至有沉淀析出;
[0075]
s4.将上述沉淀收集,并用去离子水洗涤3次以上,每次洗涤时间24h,随后干燥即可得到高强、自感应超支化粘结材料。
[0076]
其中,s1中所述d230与n,n
’‑
亚甲基双丙烯酰胺的摩尔比为1:1。
[0077]
其中,s1中所述水/甲醇的质量比为3:1。
[0078]
其中,s2中所述甲基丙烯酰氧乙基三甲基氯化铵与s1中d230的摩尔比为1:1.2。
[0079]
其中,s3中所述双三氟甲烷磺酰亚胺锂盐与s2中甲基丙烯酰氧乙基三甲基氯化铵的摩尔比例为1.2:1。
[0080]
参见图6,图6为实施例1的傅里叶红外曲线。
[0081]
实施例2
[0082]
s1.将d230和n,n
’‑
亚甲基双丙烯酰胺分别完全溶解于水/甲醇混合液中,随后将二者混合搅拌,搅拌温度30℃,搅拌时间24h;
[0083]
s2.按照设定比例将甲基丙烯酰氧乙基三甲基氯化铵加入上述s1溶液中,在相同温度继续保持搅拌24h;
[0084]
s3.按照设定比例将双三氟甲烷磺酰亚胺锂盐加入上述s2溶液中,保持室温条件继续搅拌至有沉淀析出;
[0085]
s4.将上述沉淀收集,并用去离子水洗涤3次以上,每次洗涤时间24h,随后干燥即可得到高强、自感应超支化粘结材料。
[0086]
其中,s1中所述d230与n,n
’‑
亚甲基双丙烯酰胺的摩尔比为1:0.9。
[0087]
其中,s1中所述水/甲醇的质量比为3:1。
[0088]
其中,s2中所述甲基丙烯酰氧乙基三甲基氯化铵与s1中d230的摩尔比为1:1.2。
[0089]
其中,s3中所述双三氟甲烷磺酰亚胺锂盐与s2中甲基丙烯酰氧乙基三甲基氯化铵的摩尔比例为1.2:1。
[0090]
参见图1,图1为实施例2制备的粘结剂与水的接触角照片。由图1可知,经双三氟甲烷磺酰亚胺锂盐置换后,实施例2与水的接触角为106
°
,表现出明显的疏水特性。
[0091]
参见图9,图9为实施例2的热失重曲线。由图9可知,实施例2在自然环境中达到平衡状态后,含水量低于1%,与其疏水特性相印证,且粘结剂开始降解温度大于200℃,可见在室温环境中具有良好的热稳定性。
[0092]
参见图11,图11为实施例2粘结不同材质时的剪切强度曲线。由图11可知,当施加剪切力后,粘结处能够发生一定的形变,展现出明显的非脆性断裂行为,表明实施例2具有优异的韧性,且与铁片、不锈钢,甚至有机玻璃粘结时,均表现出较高的粘结强度。
[0093]
参见图14,图14为实施例2承受应力时的自感应曲线。由图14可知,当承受不同的压力时,该超支化粘结材料表现出灵敏的电阻变化特性,可以用来检测所承受的压力状态。图中峰1、5、6、7的持续时间为2s,峰2、3、4、8的持续时间为1s。也可以将不同持续时间所产生的电信号与摩斯密码符号一一对应,即图中所示信号所对应的字母分别为“n”、“i”、“m”、“t”、“e”。
[0094]
实施例3
[0095]
s1.将d230和n,n
’‑
亚甲基双丙烯酰胺分别完全溶解于水/甲醇混合液中,随后将二者混合搅拌,搅拌温度30℃,搅拌时间24h;
[0096]
s2.按照设定比例将甲基丙烯酰氧乙基三甲基氯化铵加入上述s1溶液中,在相同温度继续保持搅拌24h;
[0097]
s3.按照设定比例将双三氟甲烷磺酰亚胺锂盐加入上述s2溶液中,保持室温条件继续搅拌至有沉淀析出;
[0098]
s4.将上述沉淀收集,并用去离子水洗涤3次以上,每次洗涤时间24h,随后干燥即可得到高强、自感应超支化粘结材料。
[0099]
其中,s1中所述d230与n,n
’‑
亚甲基双丙烯酰胺的摩尔比为1:0.85。
[0100]
其中,s1中所述水/甲醇的质量比为3:1。
[0101]
其中,s2中所述甲基丙烯酰氧乙基三甲基氯化铵与s1中d230的摩尔比为1:1.2。
[0102]
其中,s3中所述双三氟甲烷磺酰亚胺锂盐与s2中甲基丙烯酰氧乙基三甲基氯化铵的摩尔比例为1:1。
[0103]
参见图7,图7为实施例3的傅里叶红外曲线。
[0104]
实施例4
[0105]
s1.将d230和n,n
’‑
乙烯基双丙烯酰胺分别完全溶解于水/甲醇混合液中,随后将二者混合搅拌,搅拌温度30℃,搅拌时间24h;
[0106]
s2.按照设定比例将甲基丙烯酰氧乙基三甲基氯化铵加入上述s1溶液中,在相同温度继续保持搅拌24h;
[0107]
s3.按照设定比例将双三氟甲烷磺酰亚胺锂盐加入上述s2溶液中,保持室温条件继续搅拌至有沉淀析出;
[0108]
s4.将上述沉淀收集,并用去离子水洗涤3次以上,每次洗涤时间24h,随后干燥即可得到高强、自感应超支化粘结材料。
[0109]
其中,s1中所述d230与n,n
’‑
乙烯基双丙烯酰胺的摩尔比为1:0.8。
[0110]
其中,s1中所述水/甲醇的质量比为3:1。
[0111]
其中,s2中所述甲基丙烯酰氧乙基三甲基氯化铵与s1中d230的摩尔比为1:1.2。
[0112]
其中,s3中所述双三氟甲烷磺酰亚胺锂盐与s2中甲基丙烯酰氧乙基三甲基氯化铵的摩尔比例为1.5:1。
[0113]
参见图10,图10为实施例4的热失重曲线。由图10可知,实施例4在自然环境中达到平衡状态后,含水量低于1%,与其疏水特性相印证,且粘结材料开始降解温度大于200℃,可见在室温环境中具有良好的热稳定性。
[0114]
参见图12,图12为实施例4粘结不同材质时的剪切强度曲线。由图12可知,当施加剪切力后,粘结处能够发生一定的形变,展现出明显的非脆性断裂行为,表明实施例4具有优异的韧性,且与铁片、不锈钢,甚至有机玻璃粘结时,均表现出优异的粘结强度,其中与铁片的粘结强度可高达12mpa。
[0115]
参见图15,图15为实施例4承受剪切应力时的自感应曲线。由图15可知,当承受剪切压力时,该超支化粘结材料表现出灵敏的电阻变化特性,可以用来检测所承受的压力状态。如图中所示,施加剪切应力时,电阻增加,卸载剪切应力时,电阻减小,最后恢复至原位。
[0116]
实施例5
[0117]
s1.将1,8-辛二胺和n,n
’‑
乙烯基双丙烯酰胺分别完全溶解于水/甲醇混合液中,随后将二者混合搅拌,搅拌温度30℃,搅拌时间24h;
[0118]
s2.按照设定比例将甲基丙烯酰氧乙基三甲基氯化铵加入上述s1溶液中,在相同温度继续保持搅拌24h;
[0119]
s3.按照设定比例将双三氟甲烷磺酰亚胺锂盐加入上述s2溶液中,保持室温条件继续搅拌至有沉淀析出;
[0120]
s4.将上述沉淀收集,并用去离子水洗涤3次以上,每次洗涤时间24h,随后干燥即可得到高强、自感应超支化粘结材料。
[0121]
其中,s1中所述1,8-辛二胺与n,n
’‑
乙烯基双丙烯酰胺的摩尔比为1:1。
[0122]
其中,s1中所述水/甲醇的质量比为3:1。
[0123]
其中,s2中所述甲基丙烯酰氧乙基三甲基氯化铵与s1中d230的摩尔比为1:1.2。
[0124]
其中,s3中所述双三氟甲烷磺酰亚胺锂盐与s2中甲基丙烯酰氧乙基三甲基氯化铵的摩尔比例为1:1.5。
[0125]
实施例6
[0126]
s1.将d400和n,n
’‑
乙烯基双丙烯酰胺分别完全溶解于水/甲醇混合液中,随后将二者混合搅拌,搅拌温度30℃,搅拌时间24h;
[0127]
s2.按照设定比例将甲基丙烯酰氧乙基三甲基氯化铵加入上述s1溶液中,在相同温度继续保持搅拌24h;
[0128]
s3.按照设定比例将双三氟甲烷磺酰亚胺锂盐加入上述s2溶液中,保持室温条件继续搅拌至有沉淀析出;
[0129]
s4.将上述沉淀收集,并用去离子水洗涤3次以上,每次洗涤时间24h,随后干燥即
可得到高强、自感应超支化粘结材料。
[0130]
其中,s1中所述d400与n,n
’‑
乙烯基双丙烯酰胺的摩尔比为1:0.9。
[0131]
其中,s1中所述水/甲醇的质量比为3:1。
[0132]
其中,s2中所述甲基丙烯酰氧乙基三甲基氯化铵与s1中d400的摩尔比为1:1.2。
[0133]
其中,s3中所述双三氟甲烷磺酰亚胺锂盐与s2中甲基丙烯酰氧乙基三甲基氯化铵的摩尔比例为1:1.5。
[0134]
参见图8,图8为实施例6的傅里叶红外曲线。
[0135]
参见图13,图13为实施例6粘结不同材质时的剪切强度曲线。由图13可知,当施加剪切力后,粘结处能够发生一定的形变,展现出明显的非脆性断裂行为,但与铁片、不锈钢、有机玻璃粘结时,其粘结强度低于实施例2和实施例4。
[0136]
实施例7
[0137]
s1.将n,n
’‑
二甲基乙二胺和n,n
’‑
乙烯基双丙烯酰胺分别完全溶解于水/甲醇混合液中,随后将二者混合搅拌,搅拌温度30℃,搅拌时间24h;
[0138]
s2.按照设定比例将甲基丙烯酰氧乙基三甲基氯化铵加入上述s1溶液中,在相同温度继续保持搅拌24h;
[0139]
s3.按照设定比例将双三氟甲烷磺酰亚胺锌盐加入上述s2溶液中,保持室温条件继续搅拌至有沉淀析出;
[0140]
s4.将上述沉淀收集,并用去离子水洗涤3次以上,每次洗涤时间24h,随后干燥即可得到高强、自感应超支化粘结材料。
[0141]
其中,s1中所述n,n
’‑
二甲基乙二胺与n,n
’‑
乙烯基双丙烯酰胺的摩尔比为1:0.9。
[0142]
其中,s1中所述水/甲醇的质量比为3:1。
[0143]
其中,s2中所述甲基丙烯酰氧乙基三甲基氯化铵与s1中n,n
’‑
二甲基乙二胺的摩尔比为1:1.2。
[0144]
其中,s3中所述双三氟甲烷磺酰亚胺锌盐与s2中甲基丙烯酰氧乙基三甲基氯化铵的摩尔比例为1:1.5。
[0145]
参见图2,图2为实施例7与水的接触角照片。由图2可知,经双三氟甲烷磺酰亚胺锌盐置换后,实施例7与水的接触角为105
°
,表现出明显的疏水特性。
[0146]
实施例8
[0147]
s1.将n,n
’‑
二甲基乙二胺和n,n
’‑
乙烯基双丙烯酰胺分别完全溶解于水/甲醇混合液中,随后将二者混合搅拌,搅拌温度30℃,搅拌时间24h;
[0148]
s2.按照设定比例将甲基丙烯酰氧乙基三甲基氯化铵加入上述s1溶液中,在相同温度继续保持搅拌24h;
[0149]
s3.按照设定比例将双三氟甲烷磺酰亚胺钙盐加入上述s2溶液中,保持室温条件继续搅拌至有沉淀析出;
[0150]
s4.将上述沉淀收集,并用去离子水洗涤3次以上,每次洗涤时间24h,随后干燥即可得到高强、自感应超支化粘结材料。
[0151]
其中,s1中所述n,n
’‑
二甲基乙二胺与n,n
’‑
乙烯基双丙烯酰胺的摩尔比为1:0.9。
[0152]
其中,s1中所述水/甲醇的质量比为3:1。
[0153]
其中,s2中所述甲基丙烯酰氧乙基三甲基氯化铵与s1中n,n
’‑
二甲基乙二胺的摩
尔比为1:1.2。
[0154]
其中,s3中所述双三氟甲烷磺酰亚胺钙盐与s2中甲基丙烯酰氧乙基三甲基氯化铵的摩尔比例为1:1.5。
[0155]
参见图3,图3为实施例8与水的接触角照片。由图3可知,经双三氟甲烷磺酰亚胺钙盐置换后,实施例8与水的接触角为102
°
,表现出明显的疏水特性。
[0156]
对比例1
[0157]
s1.将d230和n,n
’‑
亚甲基双丙烯酰胺分别完全溶解于水/甲醇混合液中,随后将二者混合搅拌,搅拌温度30℃,搅拌时间24h;
[0158]
s2.将上述溶液缓慢滴加至丙酮溶液中,待有沉淀析出,并用去离子水洗涤3次以上,每次洗涤时间24h,随后干燥。
[0159]
其中,s1中所述d230与n,n
’‑
亚甲基双丙烯酰胺的摩尔比为1:0.9。
[0160]
其中,s1中所述水/甲醇的质量比为3:1。
[0161]
参见图4,图4为对比例1与水的接触角照片。由图4可知,对比例1与水的接触角小于50
°
,表现出明显的亲水性。
[0162]
对比例2
[0163]
s1.将d230和n,n
’‑
亚甲基双丙烯酰胺分别完全溶解于水/甲醇混合液中,随后将二者混合搅拌,搅拌温度30℃,搅拌时间24h;
[0164]
s2.按照设定比例将甲基丙烯酰氧乙基三甲基氯化铵加入上述s1溶液中,在相同温度继续保持搅拌24h;
[0165]
s3.将上述溶液缓慢滴加至丙酮溶液中,待有沉淀析出,并用去离子水洗涤3次以上,每次洗涤时间24h,随后干燥。
[0166]
其中,s1中所述d230与n,n
’‑
亚甲基双丙烯酰胺的摩尔比为1:0.9。
[0167]
其中,s1中所述水/甲醇的质量比为3:1。
[0168]
其中,s2中所述甲基丙烯酰氧乙基三甲基氯化铵与s1中d230的摩尔比为1:1.2。
[0169]
参见图5,图5为对比例2与水的接触角照片。由图5可知,未经水溶性有机离子盐置换的对比例2,与水的接触角约为60
°
,表现出明显的亲水特性。因此,对比例1和对比例2不能适用于潮湿和其他含水环境。
[0170]
以上所述仅是本发明的优选实施方式,应当指出,对于本技术领域的普通技术人员来说,在不脱离本发明原理的前提下,还可以做出若干改进和润饰,这些改进和润饰也应视为本发明的保护范围。