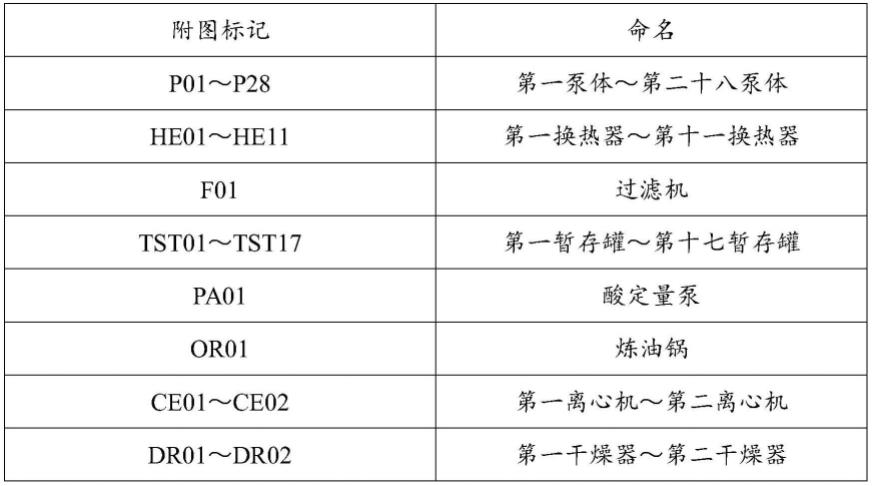
1.本发明涉及油脂精深加工设备技术领域,特别是涉及一种阿魏酸甲酯、植物甾醇、脂肪酸及脂肪酸甲酯的联产系统及工艺。
背景技术:2.米糠油是稻谷加工过程中产生的米糠经压榨或浸出制取的油脂,米糠中含有活性较高的脂肪酶,使甘油三酯水解成游离脂肪酸和甘油或甘一/甘二酯,导致米糠极易酸败,米糠毛油的酸价普遍较高,绝大部分在16~40mgkoh/g,有的甚至高达50~60mgkoh/g。此外,米糠毛油的色泽较深,脱色难度大,加工成国标一级米糠油非常困难。我国的米糠油产品多为国标四级油,售价普遍不高,采用的加工工艺多为物理精炼,炼耗大约是酸价的1.2倍,利润空间有限。
3.阿魏酸甲酯作为一种新型的日化原料,主要用作美白剂和防晒剂,其安全性也已经得到了美国fda的认可,在一些国际知名品牌中已经有应用。有文献报道,以甲醇和阿魏酸为原料,强酸性阳离子交换树脂为催化剂,直接酯化合成阿魏酸甲酯;但大规模的工业化生产尚未见闻。
4.工业上生产植物甾醇的原料主要是植物油脱臭馏出物、植物油沥青、塔尔油沥青、塔尔油。目前国际上约70%以上的商品植物甾醇来源于脱臭馏出物。目前常见的方法有:有机溶剂提取、化学法、吸附法、酶法和超临界co2萃取法等。
5.用于提取植物甾醇的常用有机溶剂包括氯仿-甲醇,氯仿-甲醇-水,正己烷,二氯甲烷,丙酮等。用有机溶剂提取植物甾醇的优点是不需要特殊仪器,是最为常用,简便,易于实施的一种提取方法,普通实验室皆可操作。缺点是溶剂消耗量大,部分提取剂毒性较大,安全性较差。
6.吸附法是根据吸附剂对不同组分吸附的选择性差异将植物甾醇分离出来的方法,提取的植物甾醇纯度较高,但是洗脱时间过长,溶剂消耗量大。
7.化学法主要是利用化学反应制备甾醇的各种衍生物,增加各种甾醇的物理性差异,再用物理法分离的方法,包括络合法、皂化法等。络合法是利用甾醇和有机酸、卤素、卤素碱土金属盐等的络合性,甾醇络合后的溶解度产生较大差异达到分离提取的效果。该法得到的植物甾醇纯度和回收率较高,但是溶剂回收困难,生产成本较大。皂化法是利用酯在碱的作用下水解生成羧酸盐和醇,再获取所要提取的有机物,但该法原料的利用率、产品的纯度和收率低。
8.酶法是使用酶对酯化过程进行催化,从而提高植物甾醇的纯度及回收率方法,但酶的价格高使用寿命短。
9.超临界co2萃取法是通过选择操作条件,在溶解度较高的脂肪酸、甘油三酯被萃取后,将留在萃取器中的植物甾醇再进行分离纯化,或者直接用制得的植物甾醇制品进入此分离系统进行分离,但设备复杂且费用高。
10.目前,在我国制备生物柴油的主要原料是各种废弃动植物油脂以及油脂精炼过程中的副产物,如餐厨垃圾油、地沟油、煎炸废油、酸化油、脂肪酸脱臭馏出物等。
11.生物柴油的生产方法目前普遍采用酸或碱催化方法。所用的酸性催化剂通常是硫酸、磷酸、盐酸和有机磺酸等,其中浓硫酸因价格便宜、资源丰富,而成为最常用的酸性催化剂;所用的碱性催化剂一般首选naoh、koh和甲醇钠。
12.液体碱催化法由于具有反应温度低、速度快、收率高、对设备腐蚀小等特点,但由于其能与原料油中的游离脂肪酸发生皂化反应,皂的存在会使反应产物发生乳化现象,造成后续分离困难,因此,对原料油的酸值和水分含量要求严格。液体酸催化法对原料要求比较低,但是反应产率低,设备腐蚀严重。
13.基于以上原因,在生物柴油的工业化生产中,普遍采用酸催化剂,而在设备选型上,通常采用搪瓷反应釜作为酯化或酯交换反应的核心设备,采用常规的塔式或釜式减压蒸馏生产精制生物柴油。常规的塔式减压蒸馏温度为220~230℃,减压蒸馏过程中需要回流比来平衡,夹带现象难以避免,会导致产品的酸值、游离甘油及总甘油三个项目的指标超标;在长时间蒸馏过程中,粗甲酯中的不饱和脂肪酸碳碳双键之间会发生聚合反应,导致植物沥青的生成,从而使产品得率大幅下降。在生产过程中,酯化或酯交换反应结束后,需中和酸或碱性催化剂,并进行水洗以除去中和产物,不可避免的会产生大量工业废水,给企业增加废水处理的成本。
14.此外,目前工业上生产的生物柴油是不同碳数脂肪酸甲酯的混合物,产品只能作为生物柴油售卖,附加值普遍不高。
技术实现要素:15.本发明的目的是提供一种阿魏酸甲酯、植物甾醇、脂肪酸及脂肪酸甲酯的联产系统及工艺,用于实现米糠油的深加工,提升产品的附加值。
16.为实现上述目的,本发明提供了如下方案:
17.本发明公开了一种阿魏酸甲酯、植物甾醇、脂肪酸及脂肪酸甲酯的联产系统,包括:
18.脂肪酸提取系统,所述脂肪酸提取系统包括第一蒸馏单元,所述第一蒸馏单元用于将脱胶干燥米糠原料油蒸馏分离得到第一轻组分物质和第一重组分物质;所述第一轻组分物质包括脂肪酸,所述第一重组分物质包括脱酸米糠油;
19.醇解系统,所述醇解系统包括依次相连的醇解单元、第二分离单元和第二干燥单元,所述醇解单元与所述第一蒸馏单元相连,用于使所述第一重组分物质进行醇解反应,所述第二分离单元用于将所述醇解反应的产物离心分离得到粗生物柴油和副产品,所述第二干燥单元用于将所述粗生物柴油脱甲醇得到脱甲醇粗生物柴油;
20.阿魏酸甲酯提取系统,所述阿魏酸甲酯提取系统包括第二蒸馏单元,所述第二蒸馏单元与所述第二干燥单元相连,用于将所述脱甲醇粗生物柴油蒸馏分离得到第二轻组分物质和第二重组分物质;所述第二轻组分物质包括阿魏酸甲酯,所述第二重组分物质包括粗生物柴油;
21.脂肪酸甲酯提取系统,所述脂肪酸甲酯提取系统包括第三蒸馏单元,所述第三蒸馏单元与所述第二蒸馏单元相连,用于将所述第二重组分物质蒸馏分离得到第三轻组分物
质和第三重组分物质;所述第三轻组分物质包括脂肪酸甲酯,所述第三重组分物质包括粗植物甾醇;
22.植物甾醇提取系统,所述植物甾醇提取系统包括第四蒸馏单元,所述第四蒸馏单元与所述第三蒸馏单元相连,用于将所述第三重组分物质蒸馏分离得到第四轻组分物质和第四重组分物质;所述第四轻组分物质包括植物甾醇,所述第四重组分物质包括米糠蜡。
23.优选地,还包括用于将米糠原料油处理得到脱胶干燥米糠原料油的前处理系统;所述前处理系统包括依次相连的除杂单元、脱胶单元、第一分离单元和第一干燥单元;所述除杂单元用于接收所述米糠原料油并对所述米糠原料油中的杂质进行过滤;所述脱胶单元用于将除杂后的所述米糠原料油进行精炼脱胶,以分离出胶质;第一分离单元用于将所述脱胶单元得到的产物进行离心分离,以得到脱胶米糠原料油和所述胶质;所述第一干燥单元用于对所述脱胶米糠原料油进行干燥处理,以得到脱胶干燥米糠原料油;所述第一干燥单元与所述第一蒸馏单元相连,以将得到的所述脱胶干燥米糠原料油输送至所述第一蒸馏单元。
24.优选地,所述除杂单元包括依次相连的第六换热器、过滤机和第一暂存罐;所述第六换热器的入口用于接收所述米糠原料油,所述第六换热器的出口与所述过滤机的入口相连;所述过滤机的出口与所述第一暂存罐的入口相连,以将过滤处理后的所述米糠原料油暂存在所述第一暂存罐内;
25.所述脱胶单元包括酸定量泵和炼油锅;所述炼油锅的入口与所述第一暂存罐的出口相连,以接收过滤处理后的所述米糠原料油;所述酸定量泵与所述炼油锅相连,以向所述炼油锅内泵送所述米糠原料油的脱胶反应所需的酸性辅料;
26.所述第一分离单元包括第七换热器、第一离心机和第二暂存罐;所述第七换热器的入口与所述炼油锅的出口相连,以接收所述炼油锅的精炼脱胶产物;所述第一离心机的入口与所述第七换热器的出口相连,以将所述精炼脱胶产物离心分离,得到所述脱胶米糠原料油和所述胶质;所述第二暂存罐的入口与所述第一离心机的出口相连,以对所述脱胶米糠原料油暂时储存;
27.所述第一干燥单元包括第八换热器、第一干燥器和第一真空泵,所述第八换热器的入口与所述第二暂存罐的出口相连,以接收所述脱胶米糠原料油;所述第一干燥器的入口与所述第八换热器的出口相连,以对所述脱胶米糠原料油进行干燥处理,得到所述脱胶干燥米糠原料油;所述第一真空泵的入口与所述第一干燥器的出口相连,以将所述脱胶干燥米糠原料油向所述第一干燥器的出口泵送。
28.优选地,还包括第一精制系统,所述第一精制系统包括第五蒸馏单元,所述第五蒸馏单元与所述第三蒸馏单元相连,以将所述第三轻组分物质蒸馏分离得到第五轻组分物质和第五重组分物质;所述第五轻组分物质包括棕榈酸甲酯、油酸甲酯、亚油酸甲酯的混合物,所述第五重组分物质包括硬脂酸甲酯。
29.优选地,还包括第二精制系统,所述第二精制系统包括第六蒸馏单元,所述第六蒸馏单元与所述第五蒸馏单元相连,以将所述第五轻组分物质蒸馏分离得到第六轻组分物质和第六重组分物质;所述第六轻组分物质包括棕榈酸甲酯,所述第六重组分物质包括油酸甲酯、亚油酸甲酯的混合物。
30.优选地,所述第五蒸馏单元包括第四换热器、第五短程蒸馏器、第五重组分罐、第
五轻组分罐、第九冷阱、第十冷阱和第七真空泵;所述第四换热器的入口用于接收所述第三轻组分物质,所述第四换热器的出口与所述第五短程蒸馏器的入口相连;所述第五短程蒸馏器的重组分出口与所述第五重组分罐相连,以将所述第五重组分物质注入所述第五重组分罐内;所述第五短程蒸馏器的轻组分出口与所述第五轻组分罐相连,以将所述第五轻组分物质注入所述第五轻组分罐内;所述第五短程蒸馏器的抽真空口与所述第九冷阱、所述第十冷阱、所述第七真空泵串联相连,以通过所述第七真空泵对所述第五短程蒸馏器抽真空,通过所述第九冷阱与所述第十冷阱捕集来自所述第五短程蒸馏器的可凝性气体组分;和/或
31.所述第六蒸馏单元包括第五换热器、第六短程蒸馏器、第六重组分罐、第六轻组分罐、第十一冷阱、第十二冷阱和第八真空泵;所述第五换热器的入口用于接收所述第五轻组分物质,所述第五换热器的出口与所述第六短程蒸馏器的入口相连;所述第六短程蒸馏器的重组分出口与所述第六重组分罐相连,以将所述第六重组分物质注入所述第六重组分罐内;所述第六短程蒸馏器的轻组分出口与所述第六轻组分罐相连,以将所述第六轻组分物质注入所述第六轻组分罐内;所述第六短程蒸馏器的抽真空口与所述第十一冷阱、所述第十二冷阱、所述第八真空泵串联相连,以通过所述第八真空泵对所述第六短程蒸馏器抽真空,通过所述第十一冷阱与所述第十二冷阱捕集来自所述第六短程蒸馏器的可凝性气体组分。
32.优选地,所述第一蒸馏单元包括第九换热器、第一短程蒸馏器、第一重组分罐、第一轻组分罐、第一冷阱、第二冷阱和第二真空泵;所述第九换热器的入口用于接收所述脱胶干燥米糠原料油,所述第九换热器的出口与所述第一短程蒸馏器的入口相连;所述第一短程蒸馏器的重组分出口与所述第一重组分罐相连,以将所述第一重组分物质注入所述第一重组分罐内;所述第一短程蒸馏器的轻组分出口与所述第一轻组分罐相连,以将所述第一轻组分物质注入所述第一轻组分罐内;所述第一短程蒸馏器的抽真空口与所述第一冷阱、所述第二冷阱、所述第二真空泵串联相连,以通过所述第二真空泵对所述第一短程蒸馏器抽真空,通过所述第一冷阱与所述第二冷阱捕集来自所述第一短程蒸馏器的可凝性气体组分;和/或
33.所述第二蒸馏单元包括第一换热器、第二短程蒸馏器、第二重组分罐、第二轻组分罐、第三冷阱、第四冷阱和第四真空泵;所述第一换热器的入口用于接收所述脱甲醇粗生物柴油,所述第一换热器的出口与所述第二短程蒸馏器的入口相连;所述第二短程蒸馏器的重组分出口与所述第二重组分罐相连,以将所述第二重组分物质注入所述第二重组分罐内;所述第二短程蒸馏器的轻组分出口与所述第二轻组分罐相连,以将所述第二轻组分物质注入所述第二轻组分罐内;所述第二短程蒸馏器的抽真空口与所述第三冷阱、所述第四冷阱、所述第四真空泵依次串联相连,以通过所述第四真空泵对所述第二短程蒸馏器抽真空,通过所述第三冷阱与所述第四冷阱捕集来自所述第二短程蒸馏器的可凝性气体组分;和/或
34.所述第三蒸馏单元包括第二换热器、第三短程蒸馏器、第三重组分罐、第三轻组分罐、第五冷阱、第六冷阱和第五真空泵;所述第二换热器的入口用于接收所述第二重组分物质,所述第二换热器的出口与所述第三短程蒸馏器的入口相连;所述第三短程蒸馏器的重组分出口与所述第三重组分罐相连,以将所述第三重组分物质注入所述第三重组分罐内;
所述第三短程蒸馏器的轻组分出口与所述第三轻组分罐相连,以将所述第三轻组分物质注入所述第三轻组分罐内;所述第三短程蒸馏器的抽真空口与所述第五冷阱、所述第六冷阱、所述第五真空泵依次串联相连,以通过所述第五真空泵对所述第三短程蒸馏器抽真空,通过所述第五冷阱与所述第六冷阱捕集来自所述第三短程蒸馏器的可凝性气体组分;和/或
35.所述第四蒸馏单元包括第三换热器、第四短程蒸馏器、第四重组分罐、第四轻组分罐、第七冷阱、第八冷阱和第六真空泵;所述第三换热器的入口用于接收所述第三重组分物质,所述第三换热器的出口与所述第四短程蒸馏器的入口相连;所述第四短程蒸馏器的重组分出口与所述第四重组分罐相连,以将所述第四重组分物质注入所述第四重组分罐内;所述第四短程蒸馏器的轻组分出口与所述第四轻组分罐相连,以将所述第四轻组分物质注入所述第四轻组分罐内;所述第四短程蒸馏器的抽真空口与所述第七冷阱、所述第八冷阱、所述第六真空泵依次串联相连,以通过所述第六真空泵对所述第四短程蒸馏器抽真空,通过所述第七冷阱与所述第八冷阱捕集来自所述第四短程蒸馏器的可凝性气体组分。
36.优选地,所述醇解单元包括甲醇定量泵、醇解釜、第一冷凝器、催化剂添加口和辅料添加口;所述醇解釜的入口与所述第一蒸馏单元相连,以接收所述第一重组分物质;所述甲醇定量泵与所述醇解釜相连,以向所述醇解釜内泵送甲醇;所述第一冷凝器与所述醇解釜相连,以对所述醇解釜排出的气体进行冷凝处理;所述催化剂添加口与所述醇解釜相连,以向所述醇解釜内添加醇解反应所需的催化剂;所述辅料添加口与所述醇解釜相连,以向所述醇解釜内添加醇解反应所需的辅料;
37.所述第二分离单元包括第十换热器、第二离心机、第三暂存罐、甲醇回收釜、第二冷凝器、捕集器和第九真空泵;所述第十换热器的入口与所述醇解釜的出口相连,以接收所述醇解反应得到的粗生物柴油和副产品;所述第二离心机的入口与所述第十换热器的出口相连,以将所述粗生物柴油与所述副产品进行离心分离;所述第三暂存罐的入口与所述第二离心机的出口相连,以暂时储存所述粗生物柴油;所述甲醇回收釜与所述第三暂存罐的出口相连,以接收所述粗生物柴油;所述第二冷凝器与所述甲醇回收釜相连,以对所述甲醇回收釜排出的气体进行冷凝处理;所述捕集器与所述第二冷凝器相连,以捕集来自所述甲醇回收釜的可凝性气体组分;所述第九真空泵与所述捕集器相连,以将所述甲醇回收釜内的气体向外泵出;
38.所述第二干燥单元包括第十一换热器、第二干燥器和第三真空泵,所述第十一换热器的入口与所述甲醇回收釜的出口相连,以接收去除甲醇后的所述粗生物柴油;所述第二干燥器的入口与所述第十一换热器的出口相连,以对所述粗生物柴油进行脱甲醇处理,得到脱甲醇粗生物柴油;所述第三真空泵的入口与所述第二干燥器的出口相连,以将所述脱甲醇粗生物柴油向所述第二干燥器的出口泵送。
39.本发明还公开了一种阿魏酸甲酯、植物甾醇、脂肪酸及脂肪酸甲酯的联产工艺,包括如下步骤:
40.s1、将脱胶干燥米糠原料油在50~300pa、170~210℃条件下,蒸馏分离得到第一轻组分物质和第一重组分物质,所述第一轻组分物质包括脂肪酸,所述第一重组分物质包括脱酸米糠油;
41.s2、使所述第一重组分物质进行醇解反应,将所述醇解反应的产物离心分离得到粗生物柴油和副产品,将所述粗生物柴油在50~300pa、30~70℃条件下,脱甲醇得到脱甲
醇粗生物柴油;
42.s3、将所述脱甲醇粗生物柴油在0~100pa、120~160℃条件下,蒸馏分离得到第二轻组分物质和第二重组分物质,所述第二轻组分物质包括阿魏酸甲酯,所述第二重组分物质包括粗生物柴油;
43.s4、将所述第二重组分物质在0~50pa、150~180℃条件下,蒸馏分离得到第三轻组分物质和第三重组分物质,所述第三轻组分物质包括脂肪酸甲酯,所述第三重组分物质包括粗植物甾醇;
44.s5、将所述第三重组分物质在0~30pa、190~220℃条件下,蒸馏分离得到第四轻组分物质和第四重组分物质;所述第四轻组分物质包括植物甾醇,所述第四重组分物质包括米糠蜡。
45.优选地,在步骤s1之前还包括前处理步骤,所述前处理步骤包括:对所述米糠原料油中的杂质进行过滤;将除杂后的所述米糠原料油进行精炼脱胶,以分离出胶质;将精炼脱胶产物进行离心分离,以得到脱胶米糠原料油和所述胶质;对所述脱胶米糠原料油在0~300pa、80~120℃条件下,进行干燥处理,以得到脱胶干燥米糠原料油;
46.在步骤s4之后还包括精制步骤,所述精制步骤包括:将所述第三轻组分物质在0~50pa、160~170℃条件下,蒸馏分离得到第五轻组分物质和第五重组分物质;将所述第五轻组分物质在0~50pa、150~165℃条件下,蒸馏分离得到第六轻组分物质和第六重组分物质;所述第五轻组分物质包括棕榈酸甲酯、油酸甲酯、亚油酸甲酯的混合物,所述第五重组分物质包括硬脂酸甲酯;所述第六轻组分物质包括棕榈酸甲酯,所述第六重组分物质包括油酸甲酯、亚油酸甲酯的混合物。
47.本发明相对于现有技术取得了以下技术效果:
48.1、显著提升米糠油的价值,为企业创造效益。
49.(1)本发明的联产系统可联产阿魏酸甲酯、植物甾醇、脂肪酸和脂肪酸甲酯,产品种类多样,附加值高。
50.(2)本发明的优选方案通过对中间产物精制的方式,能实现棕榈酸甲酯、油酸甲酯、亚油酸甲酯和硬脂酸甲酯从混合脂肪酸甲酯中的精准分离,显著提高企业效益。
51.2、生物柴油的品质更优、得率更高。
52.(1)在生物柴油提纯及精制过程中可有效避免夹带现象,从而保证“酸值、含皂量、游离甘油及总甘油”几项指标满足bd100要求。
53.(2)本发明的优选方案采用短程蒸馏方式,可有效防止物料的聚合,避免植物沥青的生成,从而提高产品得率。
54.3、降低生产能耗,节约生产成本。
55.本发明的优选方案采用短程蒸馏方式,在相同真空度条件下,短程蒸馏的温度更低。比如提取脂肪酸甲酯时,短程蒸馏的温度最高为160~170℃,较之常规塔式减压蒸馏温度为220~230℃,分离温度更低,并且蒸馏分离的时间更短(一般在十秒左右)。
56.4、环境友好。
57.(1)本发明的优选方案采用短程蒸馏方式,短程蒸馏不需要直接蒸汽,从而避免了水污染和大气污染。
58.(2)整套联产设备及联产工艺无废水排放,环境友好。
附图说明
59.为了更清楚地说明本发明实施例或现有技术中的技术方案,下面将对实施例中所需要使用的附图作简单地介绍,显而易见地,下面描述中的附图仅仅是本发明的一些实施例,对于本领域普通技术人员来讲,在不付出创造性劳动的前提下,还可以根据这些附图获得其他的附图。
60.图1为脂肪酸提取系统主体部分结构示意图;
61.图2为醇解系统主体部分结构示意图;
62.图3为阿魏酸甲酯提取系统主体部分结构示意图;
63.图4为脂肪酸甲酯提取系统主体部分结构示意图;
64.图5为植物甾醇提取系统主体部分结构示意图;
65.图6为第一精制系统主体部分结构示意图;
66.图7为第二精制系统主体部分结构示意图;
67.图8为前处理系统主体部分结构示意图;
68.附图标记说明:
69.附图标记说明详见表1。
70.表1附图标记说明
71.72.具体实施方式
73.下面将结合本发明实施例中的附图,对本发明实施例中的技术方案进行清楚、完整地描述,显然,所描述的实施例仅仅是本发明一部分实施例,而不是全部的实施例。基于本发明中的实施例,本领域普通技术人员在没有做出创造性劳动前提下所获得的所有其他实施例,都属于本发明保护的范围。
74.本发明的目的是提供一种阿魏酸甲酯、植物甾醇、脂肪酸及脂肪酸甲酯的联产系统及工艺,用于实现米糠油的深加工,提升产品的附加值。
75.为使本发明的上述目的、特征和优点能够更加明显易懂,下面结合附图和具体实施例对本发明作进一步详细的说明。
76.参照图1~图5,本实施例提供一种阿魏酸甲酯、植物甾醇、脂肪酸及脂肪酸甲酯的联产系统(以下简称为联产系统),包括脂肪酸提取系统100、醇解系统200、阿魏酸甲酯提取系统300、脂肪酸甲酯提取系统400和植物甾醇提取系统500。
77.其中,脂肪酸提取系统100包括第一蒸馏单元,第一蒸馏单元用于将脱胶干燥米糠原料油蒸馏分离得到第一轻组分物质和第一重组分物质。第一轻组分物质包括脂肪酸,第一重组分物质包括脱酸米糠油。米糠毛油的酸价普遍较高,绝大部分在16~40mgkoh/g(约占米糠油重量的8~20%),有的甚至高达50~60mgkoh/g(约占米糠油重量的25~30%)。因此,第一蒸馏单元提取的脂肪酸纯度高,可作为化工原料直接外售。此外,由于采用的是物理提取方法,提取过程中的油脂损耗很低,较之油脂精炼中的常规物理脱酸工艺,除能明显降低能耗和生产成本外,还提高了企业的经济效益。
78.醇解系统200包括依次相连的醇解单元、第二分离单元和第二干燥单元,醇解单元与第一蒸馏单元相连,用于使第一重组分物质进行醇解反应,第二分离单元用于将醇解反应的产物离心分离得到粗生物柴油和副产品,第二干燥单元用于将粗生物柴油脱甲醇得到脱甲醇粗生物柴油。
79.阿魏酸甲酯提取系统300包括第二蒸馏单元,第二蒸馏单元与第二干燥单元相连,用于将脱甲醇粗生物柴油蒸馏分离得到第二轻组分物质和第二重组分物质。第二轻组分物质包括阿魏酸甲酯,第二重组分物质包括粗生物柴油。阿魏酸甲酯具有抗氧化的作用,能防止或延缓食品成分的氧化变质,用量一般在0.0025~0.1%。此外,阿魏酸甲酯还具有美白、消炎等功效,用于皮肤化妆品中,可使皮肤具有绢质感。
80.脂肪酸甲酯提取系统400包括第三蒸馏单元,第三蒸馏单元与第二蒸馏单元相连,用于将第二重组分物质蒸馏分离得到第三轻组分物质和第三重组分物质。第三轻组分物质包括脂肪酸甲酯,第三重组分物质包括粗植物甾醇。
81.植物甾醇提取系统500包括第四蒸馏单元,第四蒸馏单元与第三蒸馏单元相连,用于将第三重组分物质蒸馏分离得到第四轻组分物质和第四重组分物质。第四轻组分物质包括植物甾醇,第四重组分物质包括米糠蜡。植物甾醇可以分为4-无甲基甾醇、4-单甲基甾醇和4,4-双甲基甾醇三大类,主要有谷甾醇、菜油甾醇和豆甾醇,其他还包括燕麦甾醇、菠菜甾醇、钝叶大戟甾醇、芦竹甾醇、环木菠萝烯醇和24-亚甲基环木菠萝醇等。植物油中普遍含有甾醇,以米糠油、小麦胚芽油及玉米胚芽油中甾醇含量较高,绝大部分油品中无甲基甾醇占总甾醇的70%以上。甾醇分类表详见表2。
82.表2甾醇分类表
[0083][0084]
几种常见植物油中植物甾醇总含量见表3。
[0085]
表3常见植物油中总甾醇含量
[0086]
油脂名称甾醇含量(%)油脂名称甾醇含量(%)大豆油0.15~0.38橄榄油0.11~0.31菜籽油0.35~0.51葵花籽油0.35~0.75米糠油0.75~1.80茶油0.10~0.60玉米油0.58~1.50小麦胚芽油1.30~2.60棕榈油0.03~0.26芝麻油0.17~0.30
[0087]
植物甾醇与胆固醇结构相似,其结构特点使之具有竞争性地阻碍小肠吸收胆固醇,使胆固醇排出体外的作用,因而有降低血液中胆固醇水平、预防心血管疾病的功效。大量国内外研究表明,补充植物甾醇能够显著降低血液中总胆固醇和低密度脂蛋白胆固醇的含量,同时对高血脂症也有辅助治疗效果。2000年9月,美国食品与药品监督管理局(fda)正式批准植物甾醇和植物甾醇酯可以作为食品增补剂来使用,并可以使用“有益健康”标签。2007年11月,植物甾醇在我国又被评为“新资源食品”,2010年又通过了国家新法规下的新资源食品认证。
[0088]
植物甾醇具有良好的抗氧化性,可用作食品添加剂,也可作为动物生长剂原料,促进动物生长,增进动物健康。
[0089]
此外,植物甾醇具有较强的皮肤渗透性和促进皮脂分泌、保持润湿和柔软的生理特性,使甾醇在化妆品中呈有柔软剂作用。
[0090]
第四蒸馏单元自米糠原料油中提取的植物甾醇,纯度高、色泽好,能显著提高米糠原料油的附加值,增加企业的经济效益。
[0091]
综上,该联产系统以米糠油为原料,可以进行阿魏酸甲酯、植物甾醇、脂肪酸及脂肪酸甲酯的提取,从而显著提升产品的附加值。
[0092]
进一步的,本实施例的联产系统还包括用于将米糠原料油处理得到脱胶干燥米糠原料油的前处理系统800,该前处理系统800得到的脱胶干燥米糠原料油供脂肪酸提取系统100使用。前处理系统800包括依次相连的除杂单元、脱胶单元、第一分离单元和第一干燥单元。除杂单元用于接收米糠原料油并对米糠原料油中的杂质进行过滤。脱胶单元用于将除
杂后的米糠原料油进行精炼脱胶,以分离出胶质。第一分离单元用于将脱胶单元得到的产物进行离心分离,以得到脱胶米糠原料油和胶质。第一干燥单元用于对脱胶米糠原料油进行干燥处理,以得到脱胶干燥米糠原料油。第一干燥单元与第一蒸馏单元相连,以将得到的脱胶干燥米糠原料油输送至第一蒸馏单元。
[0093]
具体的,参照图8,本实施例中,除杂单元包括依次相连的第六换热器he06、过滤机f01和第一暂存罐tst01。第六换热器he06的入口用于接收的米糠原料油,第六换热器he06的出口与过滤机f01的入口相连。过滤机f01的出口与第一暂存罐tst01的入口相连,以将过滤处理后的米糠原料油暂存在第一暂存罐tst01内。脱胶单元包括酸定量泵pa01和炼油锅or01。炼油锅or01的入口与第一暂存罐tst01的出口相连,以接收过滤处理后的米糠原料油。酸定量泵pa01与炼油锅or01相连,以向炼油锅or01内泵送米糠原料油的脱胶反应所需的酸性辅料(草酸的水溶液、磷酸、柠檬酸等)。第一分离单元包括第七换热器he07、第一离心机ce01和第二暂存罐tst02。第七换热器he07的入口与炼油锅or01的出口相连,以接收炼油锅or01的精炼脱胶产物。第一离心机ce01的入口与第七换热器he07的出口相连,以将精炼脱胶产物离心分离,得到脱胶米糠原料油和胶质(胶质主要为磷脂,可直接外售)。第二暂存罐tst02的入口与第一离心机ce01的出口相连,以对脱胶米糠原料油暂时储存。第一干燥单元包括第八换热器he08、第一干燥器dr01和第一真空泵vp01,第八换热器he08的入口与第二暂存罐tst02的出口相连,以接收脱胶米糠原料油。第一干燥器dr01的入口与第八换热器he08的出口相连,以对脱胶米糠原料油进行干燥处理,得到脱胶干燥米糠原料油。第一真空泵vp01的入口与第一干燥器dr01的出口相连,以将脱胶干燥米糠原料油向第一干燥器dr01的出口泵送。
[0094]
参照图8,前处理系统800使用时,米糠原料油经第一泵体p01泵出后,通过第六换热器he06升温到适宜温度后进入过滤机f01,完成过滤后,进入第一暂存罐tst01中。第一暂存罐tst01中的米糠原料油经第二泵体p02泵入炼油锅or01中,与经酸定量泵pa01泵入的酸在炼油锅or01中进行脱胶反应。反应后的物料经第三泵体p03泵出炼油锅or01,通过第七换热器he07升温到适宜温度后进入第一离心机ce01进行离心分离,分离得到的脱胶米糠原料油进入第二暂存罐tst02中。脱胶米糠原料油经第四泵体p04泵出第二暂存罐tst02,通过第八换热器he08升温到适宜温度后进入第一干燥器dr01中。在第一真空泵vp01提供的真空条件下,水分及小分子挥发物被除去,干燥后的脱胶米糠原料油经第五泵体p05泵入第四暂存罐tst04中。
[0095]
为了进一步提高产品附加值,本实施例的联产系统还包括第一精制系统600。第一精制系统600包括第五蒸馏单元,第五蒸馏单元与第三蒸馏单元相连,以将第三轻组分物质(即脂肪酸甲酯)蒸馏分离得到第五轻组分物质和第五重组分物质。第五轻组分物质包括棕榈酸甲酯、油酸甲酯、亚油酸甲酯的混合物,第五重组分物质包括硬脂酸甲酯。
[0096]
参照图6,本实施例中,第五蒸馏单元包括第四换热器he04、第五短程蒸馏器sd05、第五重组分罐rc05、第五轻组分罐lc05、第九冷阱ct09、第十冷阱ct10和第七真空泵vp07。第四换热器he04的入口用于接收第三轻组分物质,第四换热器he04的出口与第五短程蒸馏器sd05的入口相连。第五短程蒸馏器sd05的重组分出口与第五重组分罐rc05相连,以将第五重组分物质注入第五重组分罐rc05内。第五短程蒸馏器sd05的轻组分出口与第五轻组分罐lc05相连,以将第五轻组分物质注入第五轻组分罐lc05内。第五短程蒸馏器sd05的抽真
空口与第九冷阱ct09、第十冷阱ct10、第七真空泵vp07串联相连,以通过第七真空泵vp07对第五短程蒸馏器sd05抽真空,通过第九冷阱ct09与第十冷阱ct10捕集来自第五短程蒸馏器sd05的可凝性气体组分。
[0097]
参照图6,第五蒸馏单元使用时,第三轻组分物质经第二十三泵体p23泵入第四换热器he04,升温到适宜温度后进入第五短程蒸馏器sd05中,在第七真空泵vp07提供的真空条件下,区分得到第五轻组分物质和第五重组分物质。第五轻组分物质流入第五轻组分罐lc05中,而后经第二十四泵体p24泵入第十四暂存罐tst14中。第五重组分物质流入第五重组分罐rc05中,而后经第二十五泵体p25泵入第十五暂存罐tst15中。
[0098]
参照图7,为了进一步提高产品附加值,本实施例的联产系统还包括第二精制系统700。第二精制系统700包括第六蒸馏单元,第六蒸馏单元与第五蒸馏单元相连,以将第五轻组分物质蒸馏分离得到第六轻组分物质和第六重组分物质。第六轻组分物质包括棕榈酸甲酯,第六重组分物质包括油酸甲酯、亚油酸甲酯的混合物。
[0099]
参照图7,本实施例中,第六蒸馏单元包括第五换热器he05、第六短程蒸馏器sd06、第六重组分罐rc06、第六轻组分罐lc06、第十一冷阱ct11、第十二冷阱ct12和第八真空泵vp08。第五换热器he05的入口用于接收第五轻组分物质,第五换热器he05的出口与第六短程蒸馏器sd06的入口相连。第六短程蒸馏器sd06的重组分出口与第六重组分罐rc06相连,以将第六重组分物质注入第六重组分罐rc06内。第六短程蒸馏器sd06的轻组分出口与第六轻组分罐lc06相连,以将第六轻组分物质注入第六轻组分罐lc06内。第六短程蒸馏器sd06的抽真空口与第十一冷阱ct11、第十二冷阱ct12、第八真空泵vp08串联相连,以通过第八真空泵vp08对第六短程蒸馏器sd06抽真空,通过第十一冷阱ct11与第十二冷阱ct12捕集来自第六短程蒸馏器sd06的可凝性气体组分。
[0100]
参照图7,第六蒸馏单元使用时,第五轻组分物质经第二十六泵体p26泵出第十四暂存罐tst14,通过第五换热器he05升温到适宜温度后进入第六短程蒸馏器sd06中,在第八真空泵vp08提供的真空条件下,区分得到第六轻组分物质和第六重组分物质。第六轻组分物质流入第六轻组分罐lc06中,而后经第二十七泵体p27泵入第十六暂存罐tst16中。第六重组分物质流入第六重组分罐rc06中,而后经第二十八泵体p28泵入第十七暂存罐tst17中。
[0101]
参照图1,本实施例中,第一蒸馏单元包括第九换热器he09、第一短程蒸馏器sd01、第一重组分罐rc01、第一轻组分罐lc01、第一冷阱ct01、第二冷阱ct02和第二真空泵vp02。第九换热器he09的入口用于接收脱胶干燥米糠原料油,第九换热器he09的出口与第一短程蒸馏器sd01的入口相连。第一短程蒸馏器sd01的重组分出口与第一重组分罐rc01相连,以将第一重组分物质注入第一重组分罐rc01内。第一短程蒸馏器sd01的轻组分出口与第一轻组分罐lc01相连,以将第一轻组分物质注入第一轻组分罐lc01内。第一短程蒸馏器sd01的抽真空口与第一冷阱ct01、第二冷阱ct02、第二真空泵vp02串联相连,以通过第二真空泵vp02对第一短程蒸馏器sd01抽真空,通过第一冷阱ct01与第二冷阱ct02捕集来自第一短程蒸馏器sd01的可凝性气体组分。
[0102]
参照图1,第一蒸馏单元使用时,脱胶干燥米糠原料油经第六泵体p06泵出第四暂存罐tst04,通过第九换热器he09升温到适宜温度后进入第一短程蒸馏器sd01中,在第二真空泵vp02提供的真空条件下,区分得到第一轻组分物质和第一重组分物质。第一轻组分物
质流入第一轻组分罐lc01中,而后经第七泵体p07泵入第五暂存罐tst05。第一重组分物质流入第一重组分罐rc01中,而后经第八泵体p08泵入第六暂存罐tst06中,准备进入醇解系统200。
[0103]
参照图3,本实施例中,第二蒸馏单元包括第一换热器he01、第二短程蒸馏器sd02、第二重组分罐rc02、第二轻组分罐lc02、第三冷阱ct03、第四冷阱ct04和第四真空泵vp04。第一换热器he01的入口用于接收脱甲醇粗生物柴油,第一换热器he01的出口与第二短程蒸馏器sd02的入口相连。第二短程蒸馏器sd02的重组分出口与第二重组分罐rc02相连,以将第二重组分物质注入第二重组分罐rc02内。第二短程蒸馏器sd02的轻组分出口与第二轻组分罐lc02相连,以将第二轻组分物质注入第二轻组分罐lc02内。第二短程蒸馏器sd02的抽真空口与第三冷阱ct03、第四冷阱ct04、第四真空泵vp04依次串联相连,以通过第四真空泵vp04对第二短程蒸馏器sd02抽真空,通过第三冷阱ct03与第四冷阱ct04捕集来自第二短程蒸馏器sd02的可凝性气体组分。
[0104]
参照图3,第二蒸馏单元使用时,脱甲醇粗生物柴油经第十四泵体p14泵入第一换热器he01,通过第一换热器he01升温到适宜温度后进入第二短程蒸馏器sd02中,在第四真空泵vp04提供的真空条件下,区分得到第二轻组分物质和第二重组分物质。第二轻组分物质流入第二轻组分罐lc02中,而后经第十五泵体p15泵入第八暂存罐tst08中。第二重组分物质流入第二重组分罐rc02中,而后经第十六泵体p16泵入第九暂存罐tst09中。
[0105]
参照图4,本实施例中,第三蒸馏单元包括第二换热器he02、第三短程蒸馏器sd03、第三重组分罐rc03、第三轻组分罐lc03、第五冷阱ct05、第六冷阱ct06和第五真空泵vp05。第二换热器he02的入口用于接收第二重组分物质,第二换热器he02的出口与第三短程蒸馏器sd03的入口相连。第三短程蒸馏器sd03的重组分出口与第三重组分罐rc03相连,以将第三重组分物质注入第三重组分罐rc03内。第三短程蒸馏器sd03的轻组分出口与第三轻组分罐lc03相连,以将第三轻组分物质注入第三轻组分罐lc03内。第三短程蒸馏器sd03的抽真空口与第五冷阱ct05、第六冷阱ct06、第五真空泵vp05依次串联相连,以通过第五真空泵vp05对第三短程蒸馏器sd03抽真空,通过第五冷阱ct05与第六冷阱ct06捕集来自第三短程蒸馏器sd03的可凝性气体组分。
[0106]
参照图4,第三蒸馏单元使用时,第二重组分物质经第十七泵体p17泵出第九暂存罐tst09,通过第二换热器he02升温到适宜温度后进入第三短程蒸馏器sd03中,在第五真空泵vp05提供的真空条件下,区分得到第三轻组分物质和第三重组分物质。第三轻组分物质流入第三轻组分罐lc03中,而后经第十八泵体p18泵入第十暂存罐tst10中。第三重组分物质流入第三重组分罐rc03中,而后经第十九泵体p19泵入第十一暂存罐tst11中。
[0107]
参照图5,本实施例中,第四蒸馏单元包括第三换热器he03、第四短程蒸馏器sd04、第四重组分罐rc04、第四轻组分罐lc04、第七冷阱ct07、第八冷阱ct08和第六真空泵vp06。第三换热器he03的入口用于接收第三重组分物质,第三换热器he03的出口与第四短程蒸馏器sd04的入口相连。第四短程蒸馏器sd04的重组分出口与第四重组分罐rc04相连,以将第四重组分物质注入第四重组分罐rc04内。第四短程蒸馏器sd04的轻组分出口与第四轻组分罐lc04相连,以将第四轻组分物质注入第四轻组分罐lc04内。第四短程蒸馏器sd04的抽真空口与第七冷阱ct07、第八冷阱ct08、第六真空泵vp06依次串联相连,以通过第六真空泵vp06对第四短程蒸馏器sd04抽真空,通过第七冷阱ct07与第八冷阱ct08捕集来自第四短程
蒸馏器sd04的可凝性气体组分。
[0108]
参照图5,第四蒸馏单元使用时,第三重组分物质经第二十泵体p20泵出第十一暂存罐tst11,通过第三换热器he03升温到适宜温度后进入第四短程蒸馏器sd04中,在第六真空泵vp06提供的真空条件下,区分得到第四轻组分物质和第四重组分物质。第四轻组分物质流入第四轻组分罐lc04中,而后经第二十一泵体p21泵入第十二暂存罐tst12中。第四重组分物质流入第四重组分罐rc04中,而后经第二十二泵体p22泵入第十三暂存罐tst13中。
[0109]
参照图2,本实施例中,醇解单元包括甲醇定量泵pm01、醇解釜e01、第一冷凝器co01、催化剂添加口ca01和辅料添加口a01。醇解釜e01的入口与第一蒸馏单元相连,以接收第一重组分物质。甲醇定量泵pm01与醇解釜e01相连,以向醇解釜e01内泵送甲醇。第一冷凝器co01与醇解釜e01相连,以对醇解釜e01排出的气体进行冷凝处理。催化剂添加口ca01与醇解釜e01相连,以向醇解釜e01内添加醇解反应所需的催化剂。辅料添加口a01与醇解釜e01相连,以向醇解釜e01内添加醇解反应所需的辅料。
[0110]
第二分离单元包括第十换热器he10、第二离心机ce02、第三暂存罐tst03、甲醇回收釜mr01、第二冷凝器co02、捕集器cat01和第九真空泵vp09。第十换热器he10的入口与醇解釜e01的出口相连,以接收醇解反应得到的粗生物柴油和副产品。第二离心机ce02的入口与第十换热器he10的出口相连,以将粗生物柴油与副产品进行离心分离。第三暂存罐tst03的入口与第二离心机ce02的出口相连,以暂时储存粗生物柴油。甲醇回收釜mr01与第三暂存罐tst03的出口相连,以接收粗生物柴油。第二冷凝器co02与甲醇回收釜mr01相连,以对甲醇回收釜mr01排出的气体进行冷凝处理。捕集器cat01与第二冷凝器co02相连,以捕集来自甲醇回收釜mr01的可凝性气体组分。第九真空泵vp09与捕集器cat01相连,以将甲醇回收釜mr01内的气体向外泵出。
[0111]
第二干燥单元包括第十一换热器he11、第二干燥器dr02和第三真空泵vp03,第十一换热器he11的入口与甲醇回收釜mr01的出口相连,以接收去除甲醇后的粗生物柴油。第二干燥器dr02的入口与第十一换热器he11的出口相连,以对粗生物柴油进行脱甲醇处理,得到脱甲醇粗生物柴油。第三真空泵vp03的入口与第二干燥器dr02的出口相连,以将脱甲醇粗生物柴油向第二干燥器dr02的出口泵送。
[0112]
参照图2,醇解单元使用时,第六暂存罐tst06中的第一重组分物质经第九泵体p09泵入醇解釜e01中,与经甲醇定量泵pm01泵入的甲醇在醇解釜e01中混合,在经由催化剂添加口ca01添加的催化剂的作用下发生醇解反应。反应后的物料经第十泵体p10泵出醇解釜e01,通过第十换热器he10升温到适宜温度后进入第二离心机ce02进行分离,分离得到的粗生物柴油进入第三暂存罐tst03中,副产品主要为甘油,可直接外售。第三暂存罐tst03中的粗生物柴油经第十一泵体p11泵入甲醇回收釜mr01中,在第九真空泵vp09提供的真空条件下,气化的甲醇经第二冷凝器co02冷凝后变为液体,流入甲醇罐mt01中,以备进一步精馏处理。甲醇回收完毕后,粗生物柴油经第十二泵体p12泵出甲醇回收釜mr01,通过第十一换热器he11升温到适宜温度后进入第二干燥器dr02中,在第三真空泵vp03提供的真空条件下,水分及小分子挥发物被除去,干燥好的粗生物柴油经第十三泵体p13泵入第七暂存罐tst07中。
[0113]
第一冷凝器co01设置于醇解釜e01的顶部,其起到将醇解反应过程中的甲醇蒸汽冷凝为液体、回流到醇解釜e01内部的作用,可减少醇解过程中的甲醇损耗。
[0114]
辅料添加口a01设置于醇解釜e01的顶部,可根据物料的性质及反应进程的不同灵活把握需添加的辅料种类及数量,确保醇解反应的效果及产品生物柴油的性能。
[0115]
捕集器cat01设置在第九真空泵vp09和第二冷凝器co02之间,它能有效的捕集未被第二冷凝器co02冷凝的甲醇蒸汽,保证体系的真空度。
[0116]
需要说明的是,本实施例中多处使用了蒸馏单元。本领域技术人员可以理解的是,蒸馏单元的类型有多种,只要能够实现蒸馏功能即可。由于短程蒸馏能够防止物料的聚合,避免植物沥青的生成,同时能够降低能耗,本实施例采用短程蒸馏的方式。
[0117]
参照图1~图5,本实施例还提供一种阿魏酸甲酯、植物甾醇、脂肪酸及脂肪酸甲酯的联产工艺,包括如下步骤:
[0118]
s1、将脱胶干燥米糠原料油在50~300pa、170~210℃条件下,蒸馏分离得到第一轻组分物质和第一重组分物质,第一轻组分物质包括脂肪酸。
[0119]
s2、使第一重组分物质进行醇解反应,将醇解反应的产物离心分离得到粗生物柴油和副产品,将粗生物柴油在50~300pa、30~70℃条件下,脱甲醇得到脱甲醇粗生物柴油。
[0120]
s3、将脱甲醇粗生物柴油在0~100pa、120~160℃条件下,蒸馏分离得到第二轻组分物质和第二重组分物质,第二轻组分物质包括阿魏酸甲酯。
[0121]
s4、将第二重组分物质在0~50pa、150~180℃条件下,蒸馏分离得到第三轻组分物质和第三重组分物质,第三轻组分物质包括脂肪酸甲酯。
[0122]
s5、将第三重组分物质在0~30pa、190~220℃条件下,蒸馏分离得到第四轻组分物质和第四重组分物质。第四轻组分物质包括植物甾醇。
[0123]
参照图8,作为一种优选技术方案,在步骤s1之前还包括前处理步骤,前处理步骤包括:对米糠原料油中的杂质进行过滤。将除杂后的米糠原料油进行精炼脱胶,以分离出胶质。将精炼脱胶产物进行离心分离,以得到脱胶米糠原料油和胶质。对脱胶米糠原料油在0~300pa、80~120℃条件下,进行干燥处理,以得到脱胶干燥米糠原料油。
[0124]
参照图6~图7,作为一种优选技术方案,在步骤s4之后还包括精制步骤,精制步骤包括:将第三轻组分物质在0~50pa、160~170℃条件下,蒸馏分离得到第五轻组分物质和第五重组分物质。将第五轻组分物质在0~50pa、150~165℃条件下,蒸馏分离得到第六轻组分物质和第六重组分物质。
[0125]
本说明书中应用了具体个例对本发明的原理及实施方式进行了阐述,以上实施例的说明只是用于帮助理解本发明的方法及其核心思想;同时,对于本领域的一般技术人员,依据本发明的思想,在具体实施方式及应用范围上均会有改变之处。综上所述,本说明书内容不应理解为对本发明的限制。