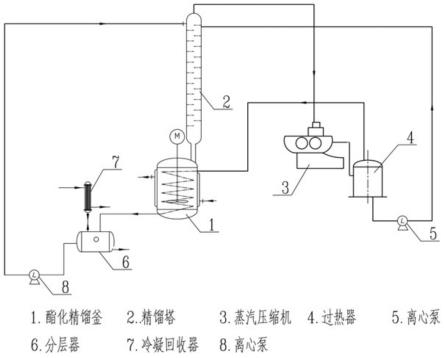
1.本发明涉及维生素b6的合成,具体涉及其中间体4-甲基-5-乙氧基噁唑酸乙酯的制备方法。
背景技术:2.维生素b6(vitamin b6)又称吡哆素,其包括吡哆醇、吡哆醛及吡哆胺,在体内以磷酸酯的形式存在,是一种水溶性维生素,遇光或碱易破坏,不耐高温。吡哆醇耐热,吡哆醛和吡哆胺不耐高温。市场上,维生素b6主要以盐酸吡哆醇形式出售。
[0003][0004]
维生素b6为人体内某些辅酶的组成成分,参与多种代谢反应,尤其是和氨基酸代谢有密切关系。临床上应用维生素b6制剂防治妊娠呕吐和放射病呕吐。同时可以用于治疗动脉硬化、秃头、胆固醇过高、膀胱炎、低血糖症、精神障碍、肌肉失调、神经障碍、怀孕初期的呕吐、超体重、手术后呕吐、对太阳光敏感等。近些年还发现了维生素b6可以抢救异烟肼中毒、治疗贫血、治疗白细胞减少症、治疗智力发育迟滞、治疗口腔溃疡、治疗动脉硬化及血栓栓塞性疾病、回乳、治疗帕金森综合征等。
[0005]
工业上通常采用化学合成法生产维生素b6,主要有吡啶酮法、噁唑法和其他微生物法。
[0006]“吡啶酮法”是以氯乙酸为起始原料,经酯化、取代、环合等反应合成维生素b6的方法,1936年首次合成维生素b6,并证明了与天然提取物具有相同的化学结构和生物活性,此后,世界各国积极开展维生素b6合成研究,从而促进了维生素b6工业的快速发展。
[0007]
20世纪60年代,firestone ra等在学者研究成果的基础上,以n-甲酰丙氨酸乙酯为起始物,经环合得到关键中间体4-甲基-5-乙氧基噁唑,然后与亲双烯体进行diels- alder反应,再经转化处理后得到维生素b6。这一合成路线具有原料易得、收率高等优点,该方法后来被简称为“噁唑法”。“噁唑法”应用于生产后显著降低了生产成本,从而导致维生素b6售价大幅下降。
[0008]
与“吡啶酮法”相比,“噁唑法”有了很大进步,但也存在一定不足。例如噁唑中间体合成过程中用到有毒溶剂苯和强腐蚀性的三氯氧磷,维生素b6粗品精制工艺较为复杂等。
[0009]
在噁唑法生产维生素b6过程中,有两个重要的中间体化合物:n-乙氧草酰丙氨酸乙酯和4-甲基-5-乙氧基噁唑酸乙酯。
[0010]
4-甲基-5-乙氧基噁唑酸乙酯的反应过程一般是将n-乙氧草酰丙氨酸乙酯进行环合反应,在反应容器内加入n-乙氧草酰丙氨酸乙酯、三氯氧磷和三乙基胺进行反应制备得到4-甲基
ꢀ‑
5-乙氧基噁唑酸乙酯。该制备步骤中,文献(中国医药工业杂志,2004,35(1),第1-2页) 报道的产率为76.5%。
80℃~100℃,保温反应0.5-4小时;反应完毕,将反应液降温至50℃~60℃,加入水;下层水用甲苯洗涤,甲苯层与上层物料混合,回收甲苯,蒸馏底物即得4-甲基-5-乙氧基-噁唑酸乙酯。
[0021]
如上所述的一种4-甲基-5-乙氧基噁唑酸乙酯的制备方法,其特征在于:在反应容器中加入n-乙氧草酰基丙氨酸乙酯200-230重量份,三乙胺450-520重量份,甲苯,冷却至-5℃~0℃;将固体光气110-130重量份溶于甲苯中,然后将混合液滴加至反应容器中,滴加过程中控制温度在6℃以下,滴加结束后,待反应容器内温度冷却至室温,保温搅拌;然后滴加 20-30重量份三氯氧磷,滴加结束后缓慢升温至40℃-60℃,反应4小时,然后升温至 80℃~100℃,保温反应1小时;反应完毕,将反应液降温至50℃~60℃,加入水;下层水用甲苯洗涤,甲苯层与上层物料混合,回收甲苯,蒸馏底物即得4-甲基-5-乙氧基-噁唑酸乙酯。
[0022]
如上所述的一种4-甲基-5-乙氧基噁唑酸乙酯的制备方法,其特征在于:在2l的反应釜中加入n-乙氧草酰基丙氨酸乙酯230g,三乙胺520g,甲苯400ml,冷却至-5℃~0℃;将固体光气110g溶于300ml甲苯中,然后将混合液滴加至反应釜中,滴加过程中控制温度在6℃以下,滴加结束后,待反应釜内温度冷却至室温,保温搅拌2h;然后滴加30g三氯氧磷,滴加结束后缓慢升温至40℃-60℃,反应4小时,然后升温至80℃~100℃,保温反应1小时;反应完毕,将反应液降温至50℃~60℃,加入水500ml;下层水用400ml甲苯洗涤2次,甲苯层与上层物料混合,在80℃~100℃/真空0.1kpa~3kpa条件下回收甲苯,蒸馏底物即得4
‑ꢀ
甲基-5-乙氧基-噁唑酸乙酯。
[0023]
本发明还提供了一种n-乙氧草酰丙氨酸乙酯的制备方法,本发明通过大量实验和创新性的研究发现,通过无水乙醇和甲苯的使用,可以成功将毒性较大的苯替换为毒性较低的溶剂,通过蒸汽压缩机的使用,使得蒸汽可以二次循环使用,使得能耗大大降低,实现了节能环保。
[0024]
本合成工艺采用甲苯进行酯化精馏带水,但由于甲苯和苯物化性质的差异,延长了反应时间,增加了能耗,为此,为降低生产能耗、缩短反应时间,本发明进行了多种尝试,最终发现了通过无水乙醇以及甲苯的使用,可以替换苯,并且保证收率不降低。通过蒸汽压缩机的使用,使得蒸汽可以二次循环使用,使得能耗大大降低,实现了节能环保。并且提供了一种全新的制备n-乙氧草酰丙氨酸乙酯的反应体系。
[0025]
本发明提供了一种n-乙氧草酰丙氨酸乙酯的反应体系(或反应设备),该体系包括:反应容器、精馏塔、分水器和蒸汽压缩机;加热所述反应容器使得蒸汽进入精馏塔内;汽相自精馏塔顶部进入蒸汽压缩机,蒸汽压缩机通过将热蒸汽压缩,使汽体温度升高,并将压缩后的蒸汽输入反应容器中,冷凝后的溶剂进入分水器中连续分出水层,甲苯层经泵泵入塔内。
[0026]
优选的,所述反应容器为酯化精馏釜。
[0027]
优选的,反应体系还包括过热器,蒸汽压缩机通过将热蒸汽压缩,使汽体温度升高,然后经过过热器输送至反应容器中。
[0028]
优选的,反应体系还包括离心泵,蒸汽压缩机通过将热蒸汽压缩,使汽体温度升高,然后经过过热器和离心泵,将蒸汽输入反应容器中。
[0029]
优选的,所述分水器为分层器,分层器上端设置有冷凝回收器;冷凝后的溶剂进入分层器中连续分出水层,甲苯层经泵泵入塔内。
[0030]
优选的在分水器之后设置离心泵,甲苯层经离心泵后,泵入塔内。
[0031]
最优选的,反应体系包括:反应容器1、精馏塔2、蒸汽压缩机3、过热器4、离心泵5、分层器6、冷凝回收器7和离心泵8。
[0032]
在反应容器1上端设置精馏塔2,汽相自精馏塔2顶部进入蒸汽压缩机3,蒸汽压缩机 3通过将热蒸汽压缩,使汽体温度升高,然后经过过热器4和离心泵5,将蒸汽输入反应容器中。在反应容器1下端设置分层器6,分层器6上设置有冷凝回收器7,冷凝后的溶剂进入分层器6中连续分出水层,甲苯层经离心泵8泵入塔内。
[0033]
所述反应容器优选为酯化精馏釜。
[0034]
本发明提供了一种n-乙氧草酰丙氨酸乙酯的制备方法,其特征在于:将20-50质量份 l-丙氨酸、30-80质量份草酸、无水乙醇分别加至混合容器中,升温至90℃~100℃加热溶解,然后将溶解液转至酯化精馏釜内,加入甲苯,草酸二乙酯50-100质量份,加热升温进行反应,汽相自精馏塔顶部进入蒸汽压缩机,蒸汽压缩机通过将热蒸汽压缩,使汽体温度升高,并将压缩后的蒸汽输入反应容器中,冷凝后的溶剂进入分水器中连续分出水层,甲苯层经泵泵入流入塔内;当反应进行到20-60小时,再次向酯化精馏釜内加入甲苯及乙醇进行反应精馏,至分水器基本无水析出、酯化精馏釜内物料水分小于0.1%时,停止反应;常压蒸去甲苯、乙醇;真空减压蒸除草酸二乙酯,即得n-乙氧草酰丙氨酸乙酯;
[0035]
所述制备方法使用的反应体系包括:反应容器、精馏塔、分水器和蒸汽压缩机;加热所述反应容器使得蒸汽进入精馏塔内;汽相自精馏塔顶部进入蒸汽压缩机,蒸汽压缩机通过将热蒸汽压缩,使汽体温度升高,并将压缩后的蒸汽输入反应容器中,冷凝后的溶剂进入分水器中连续分出水层,甲苯层经泵泵入塔内。
[0036]
优选的,所述反应容器为酯化精馏釜。
[0037]
优选的,反应体系还包括过热器,蒸汽压缩机通过将热蒸汽压缩,使汽体温度升高,然后经过过热器输送至反应容器中。
[0038]
优选的,反应体系还包括离心泵,蒸汽压缩机通过将热蒸汽压缩,使汽体温度升高,然后经过过热器和离心泵,将蒸汽输入反应容器中。
[0039]
优选的,所述分水器为分层器,分层器上端设置有冷凝回收器;冷凝后的溶剂进入分层器中连续分出水层,甲苯层经泵泵入塔内。
[0040]
优选的在分水器之后设置离心泵,甲苯层经离心泵后,泵入塔内。
[0041]
最优选的,反应体系包括:反应容器1、精馏塔2、蒸汽压缩机3、过热器4、离心泵5、分层器6、冷凝回收器7和离心泵8。
[0042]
在反应容器1上端设置精馏塔2,汽相自精馏塔2顶部进入蒸汽压缩机3,蒸汽压缩机3通过将热蒸汽压缩,使汽体温度升高,然后经过过热器4和离心泵5,将蒸汽输入反应容器中。在反应容器1下端设置分层器6,分层器6上设置有冷凝回收器7,冷凝后的溶剂进入分层器6中连续分出水层,甲苯层经离心泵8泵入塔内。
[0043]
所述反应容器优选为酯化精馏釜。
[0044]
如上所述的一种n-乙氧草酰丙氨酸乙酯的制备方法,其特征在于:所述制备方法使用的反应体系包括:酯化精馏釜1、精馏塔2、蒸汽压缩机3、过热器4、离心泵5、分层器6、冷凝回收器7和离心泵8;在酯化精馏釜1上端设置精馏塔2,汽相自精馏塔2顶部进入蒸汽压缩机3,蒸汽压缩机3通过将热蒸汽压缩,使汽体温度升高,然后经过过热器4和离心泵5,将蒸
汽输入反应容器中;在酯化精馏釜1下端设置分层器6,分层器6上设置有冷凝回收器7,冷凝后的溶剂进入分层器6中连续分出水层,甲苯层经离心泵8泵入塔内。
[0045]
如上所述的一种n-乙氧草酰丙氨酸乙酯的制备方法,其特征在于:将35质量份l-丙氨酸、58质量份草酸、无水乙醇分别加至混合容器中,升温至90℃~100℃加热溶解,然后将溶解液转至酯化精馏釜内,加入甲苯,草酸二乙酯65质量份,加热升温进行反应,汽相自精馏塔顶部进入蒸汽压缩机,蒸汽压缩机通过将热蒸汽压缩,使汽体温度升高,并将压缩后的蒸汽输入反应容器中,冷凝后的溶剂进入分水器中连续分出水层,甲苯层经泵泵入塔内;当反应进行到40小时,再次向酯化精馏釜内加入甲苯及乙醇进行反应精馏,至分水器基本无水析出、酯化精馏釜内物料水分小于0.1%时,停止反应;常压蒸去甲苯、乙醇;100℃~130℃ /10~200pa真空减压蒸除草酸二乙酯,即得n-乙氧草酰丙氨酸乙酯。
[0046]
如上所述的一种n-乙氧草酰丙氨酸乙酯的制备方法,其特征在于:将35千克l-丙氨酸、 58千克草酸、60升无水乙醇分别加至混合容器中,升温至90℃~100℃加热溶解,然后将溶解液转至酯化精馏釜内,加入甲苯50升,草酸二乙酯65千克,加热升温进行反应,汽相自精馏塔顶部进入蒸汽压缩机,蒸汽压缩机通过将热蒸汽压缩,使汽体温度升高,并将压缩后的蒸汽输入反应容器中,冷凝后的溶剂进入分水器中连续分出水层,甲苯层经泵泵入塔内;当反应进行到40小时,再次向酯化精馏釜内加入20升甲苯及30升乙醇进行反应精馏,至分水器基本无水析出、酯化精馏釜内物料水分小于0.1%时,停止反应;常压蒸去甲苯、乙醇;100℃~130℃/10~200pa真空减压蒸除草酸二乙酯,即得n-乙氧草酰丙氨酸乙酯。
[0047]
本发明实现了苯的成功替换,实现了环保节能的效果。
[0048]
本发明还涉及一种4-甲基-5-乙氧基噁唑酸乙酯的制备方法,其包括上述的n-乙氧草酰丙氨酸乙酯制备方法,和上述的4-甲基-5-乙氧基噁唑酸乙酯的制备方法。即以上述的n-乙氧草酰丙氨酸乙酯制备方法制备的n-乙氧草酰丙氨酸乙酯为原料,进一步按照上述的方法制备4-甲基-5-乙氧基噁唑酸乙酯。
[0049]
本发明中成功改进了现有技术中的n-乙氧草酰丙氨酸乙酯和一种4-甲基-5-乙氧基噁唑酸乙酯的制备方法;使得制备得到的n-乙氧草酰丙氨酸乙酯直接作为底物参与4-甲基-5-乙氧基噁唑酸乙酯的合成中。两个步骤紧密衔接,解决了维生素b6合成中两个关键中间体的合成,使得工艺步骤简单、不使用有毒的苯、大大降低了三氯氧磷的使用量,提高了中间体的收率,整个制备工艺环保节能无污染。三氯氧磷用量可以减少2/3,收率大幅提高,反应过程更温和。水层用甲苯萃取,可以使用萃取塔连续萃取,可以结合工程上的优化,应用于规模化工业量产中。
附图说明
[0050]
图1:反应设备示意图
[0051]
1为酯化精馏釜2为精馏塔3为蒸汽压缩机4为过热器5为离心泵6为分层器7为冷凝回收器8为离心泵。
具体实施方式
[0052]
实施例1:
[0053]
将35kgl-丙氨酸、58kg工业草酸、40l 95%乙醇分别加至混合容器中,升温至80℃
加热溶解,然后将溶解液转至酯化精馏釜内,加入苯30l,草酸二乙酯65kg,加热升温进行反应,自精馏塔顶部分水器中连续分出水层,苯层流入塔内。当反应进行到40小时,再次向酯化精馏釜内加入10l苯及20l 95%乙醇进行反应精馏,至分水器基本无水析出、酯化精馏釜内物料水分小于0.1%时,停止反应。常压蒸去苯、醇;100℃~130℃/10~200pa真空减压蒸除草酸二乙酯,即得n-乙氧草酰丙氨酸乙酯,收率91%。
[0054]
实施例2:
[0055]
将35kg l-丙氨酸、58kg工业草酸、40l 95%乙醇分别加至混合容器中,升温至80℃加热溶解,然后将溶解液转至酯化精馏釜内,加入甲苯30l,草酸二乙酯65kg,加热升温进行反应,自精馏塔顶部分水器中连续分出水层,甲苯层流入塔内。当反应进行到40小时,再次向酯化精馏釜内加入10l甲苯及20l 95%乙醇进行反应精馏,至分水器基本无水析出、酯化精馏釜内物料水分小于0.1%时,停止反应。常压蒸去甲苯、乙醇;100℃~130℃/10~200pa 真空减压蒸除草酸二乙酯,即得n-乙氧草酰丙氨酸乙酯,收率89%。
[0056]
由于甲苯毒性比苯低很多,对员工和环境危害较小。在实施例2中将溶剂换做甲苯后,发现产率有所下降,而且与实施例1相比耗能明显增加,能耗提升了26%。因此,需要筛选保证产率且降低能耗的方法。
[0057]
实施例3:
[0058]
将35kg l-丙氨酸、58kg草酸、60l无水乙醇分别加至混合容器中,升温至90℃~100℃加热溶解,然后将溶解液转至酯化精馏釜内,加入甲苯50l,草酸二乙酯65kg,加热升温进行反应,自精馏塔顶部分水器中连续分出水层,甲苯层流入塔内。当反应进行到40小时,再次向酯化精馏釜内加入20l甲苯及30l乙醇进行反应精馏,至分水器基本无水析出、三口容器内物料水分小于0.1%时,停止反应。常压蒸去甲苯、醇;100℃~130℃/10~200pa真空减压蒸除草酸二乙酯,即得n-乙氧草酰丙氨酸乙酯,收率92%。
[0059]
通过实验发现,通过使用无水乙醇,且加大无水乙醇和甲苯的使用量,可以使得反应的产率保持在90%以上。但是与实施例1相比,能耗仍然增加了33%。
[0060]
实施例4:
[0061]
将35kg l-丙氨酸、58kg草酸、60升无水乙醇分别加至混合容器中,升温至90℃~100℃加热溶解,然后将溶解液转至酯化精馏釜内,加入甲苯50l,草酸二乙酯65kg,加热升温进行反应。在酯化精馏釜1上端设置精馏塔2,汽相自精馏塔2顶部进入蒸汽压缩机3,蒸汽压缩机3通过将热蒸汽压缩,使汽体温度升高,然后经过过热器4和离心泵5,将蒸汽输入反应容器中。在酯化精馏釜1下端设置分层器6,分层器6上设置有冷凝回收器7,冷凝后的溶剂进入分层器6中连续分出水层,甲苯层经离心泵8泵入塔内。当反应进行到40小时,再次向酯化精馏釜内加入20l甲苯及30l乙醇进行反应精馏,至分水器基本无水析出、酯化精馏釜物料水分小于0.1%时,停止反应。常压蒸去甲苯、醇;100℃~130℃/10~200pa 真空减压蒸除草酸二乙酯,即得n-乙氧草酰丙氨酸乙酯,收率93%。通过蒸汽压缩机将蒸汽二次利用,使得与实施例1相比,产率没有下降,反而能耗下降了21%。
[0062]
因此,确定制备n-乙氧草酰丙氨酸乙酯的制备方法中,只把苯替换为甲苯,会使产率和能耗增加。虽然使用无水乙醇和增加甲苯的使用量,会使产率有所提升,但是同时又使得能耗增加。通过二次利用热气,将精馏塔进入分水器的残余蒸汽通过热气压缩机进行压缩,循环使用,极大降低了能耗。因此,通过本发明中组合使用,使得成功将苯替换为毒性更
低的甲苯,且能耗降低,实现了节能、环保。
[0063]
实施例54-甲基-5-乙氧基噁唑酸乙酯的制备
[0064]
在2l的反应釜中加入n-乙氧草酰基丙氨酸乙酯230g,三乙胺520g,甲苯400ml,冷却至-5℃~0℃。将固体光气110g溶于300ml甲苯中,然后将混合液滴加至反应釜中,滴加过程中控制温度在6℃以下,滴加结束后,待反应釜内温度冷却至室温,保温搅拌2h。然后滴加30g三氯氧磷,滴加结束后缓慢升温至40℃-60℃,反应4小时,然后升温至80℃~100℃,保温反应1小时。反应完毕,将反应液降温至50℃~60℃,加入水500ml。下层水用400ml 甲苯洗涤2次,甲苯层与上层物料混合,在80℃~100℃/真空0.1kpa~3kpa条件下回收甲苯,蒸馏底物即得4-甲基-5-乙氧基-噁唑酸乙酯,收率96%,含量95%。
[0065]
本发明采用三氯氧磷+三光气的复合环合剂,大大降低三氯氧磷使用量,同时反应收率由低于80%提高至90%以上,其优势体现在生产成本下降,含磷废水降低。三氯氧磷用量可以减少2/3,收率大幅提高,反应过程更温和。水层用甲苯萃取,可以使用萃取塔连续萃取,可以结合工程上的优化,应用于规模化工业量产中。
[0066]
以上描述是本发明的一般性描述。根据情况或实际需要,可进行形式的变化和等值的替代,虽然本文采用特定的术语,但这些术语意在描述,而不是为了限制的目的。本领域技术人员可以对本发明作各种改动或修改,这些等价形式同样落于本技术所附权利要求书所限定的范围之内。