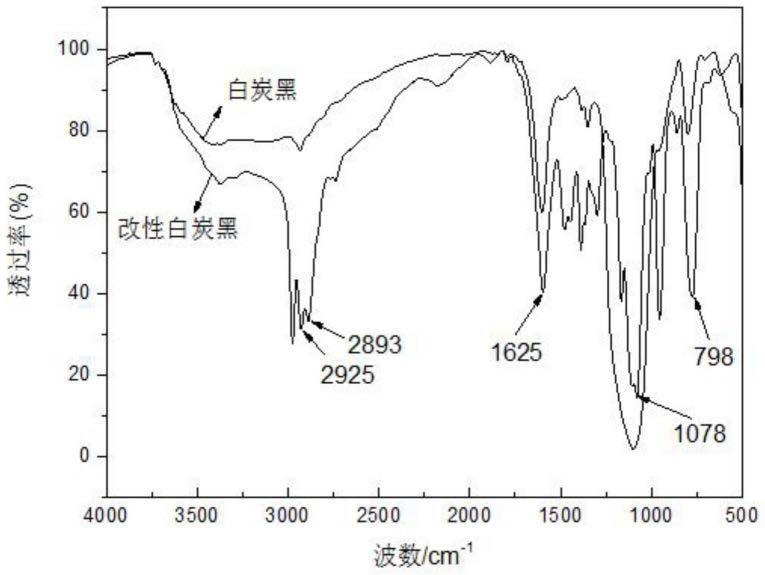
1.本发明涉及一种丁腈橡胶的制备方法,具体涉及一种低压缩形变高力学性能的丁腈橡胶及制备方法。
背景技术:2.丁腈橡胶(nbr)是目前用量最大的一种特殊合成橡胶,其耐油性极好、耐磨性较高、耐热性较好、粘接力强,但其耐臭氧性差、高温下易变形、力学性能较低,因此想要大量广泛的使用nbr还需要对其进行改性才能达到日常使用要求。现阶段国内外对nbr的需求旺盛,通过改性提高nbr的性能是大势所趋,但是国外的一些垄断技术扼制了国内nbr发展的命脉。目前国内很多研究学者通过改性橡胶的填料来提高橡胶的性能,不限于用不同的填料如炭黑、白炭黑、碳纳米管、氧化石墨烯纳米颗粒等去改性,但现有改性方法皆存在一些问题,例如:炭黑环境污染较严重;仅用白炭黑做填料,补强效果不明显;改性碳纳米管氧化石墨烯等方法成本较高,不易普及;一些低成本、易实施且补强效果明显的改性,如丁腈橡胶与pvc共混进行改性等技术,已经被国外所垄断。因此,探究新的改性放大意义重大。
技术实现要素:3.基于上述现有技术所存在的不足之处,本发明的目的在于提供一种nbr的制备方法,旨在制备出具有高力学性能以及低压缩变形的nbr。
4.本发明为实现目的,采用如下技术方案:
5.一种低压缩形变高力学性能的丁腈橡胶,其特点在于:所述丁腈橡胶是在丁腈橡胶生胶中加入复合填料后进行硫化获得;所述复合填料由改性白炭黑与改性石墨烯组成;所述改性白炭黑是利用3-氨丙基三乙氧基硅烷改性的白炭黑;所述改性石墨烯是利用3-氨丙基三乙氧基硅烷改性的表面包覆环氧树脂的石墨烯。
6.进一步地,所述复合填料中,改性石墨烯在橡胶硫化压力下的体积百分比为1.5~2.5%。改性石墨烯在橡胶硫化压力下的体积百分比确定方法为:将质量为m的改性石墨烯装入长方体容器中,施加橡胶硫化压力,记录其体积v,从而计算获得改性石墨烯在橡胶硫化压力下的密度ρ=m/v;改性白炭黑与白炭黑原料的密度相同,其在橡胶硫化压力下的密度已知(购买时,该参数会给出)。根据二者在橡胶硫化压力下的密度以及二者的质量,可换算获得改性石墨烯在橡胶硫化压力下的体积百分比。
7.进一步地,所述复合填料占所述丁腈橡胶生胶质量的35~40%。
8.本发明所述低压缩形变高力学性能的丁腈橡胶的制备方法,包括如下步骤:
9.步骤1、改性白炭黑的制备
10.称取38~42质量份的白炭黑置于烧杯中,加入2~5质量份的3-氨丙基三乙氧基硅烷(kh550)和250~300质量份的去离子水,盖保鲜膜进行密封,然后超声分散均匀;超声结束后,将所得溶液磁力搅拌1~3h,100~105℃真空干燥20~24h,研磨,继续在100~105℃真空干燥至水份完全挥发(当挥发后总质量与原料白炭黑和3-氨丙基三乙氧基硅烷总质量
的差值在
±
3质量份时,可视为水份完全挥发),得到改性白炭黑;
11.步骤2、改性石墨烯的制备
12.将10~50质量份的环氧树脂与2~10质量份的石墨烯放入烧杯中,加入110~130质量份的乙醇和0.5~2质量份的甲基六氢苯酐固化剂,电动搅拌下,先加热升温至65~70℃,再保温3~4h,使环氧树脂在石墨烯表面包覆生长,过滤、用去离子水洗涤、80~90℃烘干后,获得表面包覆环氧树脂的石墨烯;
13.在10~25质量份的表面包覆环氧树脂的石墨烯中加入2~5质量份的3-氨丙基三乙氧基硅烷(kh550),再加入130~200质量份的去离子水,盖保鲜膜进行密封,然后超声分散均匀;超声结束后,将所得溶液磁力搅拌1~3h,100~105℃真空干燥20~24h,得到改性石墨烯;
14.按照复合填料中改性石墨烯在橡胶硫化压力下的体积百分比为1.5~2.5%确定所需改性石墨烯的用量;
15.步骤3、丁腈橡胶的制备
16.将步骤1所制备的全部改性白炭黑和步骤2所制备的所需量的改性石墨烯作为复合填料加入到丁腈橡胶生胶中,经硫化即获得成品丁腈橡胶,具体方法为:
17.步骤31、分别称取98~102质量份的nbr生胶、0.8~1.2质量份的硬脂酸(sa)、2.8~3.2质量份的氧化锌(zno)、1.3~1.7质量份的防老剂(rd)、1.3~1.7质量份的促进剂(ns)和1.3~1.7质量份的硫磺(s)。
18.步骤32、先用nbr生胶洗辊,去除双辊中残留的废胶和小料,待双辊清洗干净后,调整辊间距,将98~102质量份的nbr生胶放入双辊之间,打开开炼机电源进行生胶的开炼,待生胶粘辊后依次加入sa、zno和rd,待小料混炼均匀后再少量多次地加入改性白炭黑以及改性石墨烯作为复合填料进行开炼共混,待复合填料混炼均匀后,再依次向开炼中的生胶加入ns和s,打三角包多次后薄通出片;
19.步骤33、将所制得的胶置于室温条件下干燥24h后,用利用橡胶加工分析仪(rpa8000)对混炼胶的硫化特性进行测试,测试模式为mdr、温度为160℃、频率1hz、应变0.5deg,可以得到硫化时间(tc90)。
20.根据硫化时长利用平板硫化仪进行硫化后置于室温24h后便可得到目标胶。
21.作为优选,所述丁腈橡胶生胶中的丙烯腈含量为30%~35%。
22.与已有技术相比,本发明的有益效果体现在:
23.1、本发明利用偶联剂上的部分官能基团与白炭黑表面的羟基发生化学反应从而改变白炭黑表面的基团结构和分布,将石墨烯表面包裹环氧树脂并利用硅烷偶联剂改善石墨烯与环氧树脂之间的接合性和相容性,从而提高复合填料与橡胶基体的相容性以及复合填料自身的分散性,经实验结果验证本发明所制备的丁腈橡胶具有低压缩形变高力学性能的特点。
24.2、本发明采用填料通过非共价作用和nbr大分子链增强了相互作用,使得由改性白炭黑与改性石墨烯组成的复合填料加入丁腈橡胶后,可显著提升橡胶的力学性能,同时提升其在高温压变后的回复性能,且橡胶在拉伸测试过程中最大应力和最大断裂伸长率均有显著的提升,经过高温热压后其永久压缩变形率得到显著的下降。
附图说明
25.图1为实施例1所用白炭黑和所得改性白炭黑的ftir图。
26.图2中a、b、c、d、e、f分别为实施例1及对比例1、2、3、4、5所得橡胶样品的断面sem图。
27.图3为实施例1及对比例1、2、3、4、5所制得的橡胶样品在150℃、70h条件下测得的永久压缩变形率图。
28.图4为实施例1及对比例1、2、3、4、5所制得的橡胶样品进行力学性能测试的最大应力性能图。
29.图5为实施例1及对比例1、2、3、4、5所制得的橡胶进行力学性能测试的最大应变性能图。
具体实施方式
30.下面对本发明的实施例作详细说明,本实施例在以本发明技术方案为前提下进行实施,给出了详细的实施方式和具体的操作过程,但本发明的保护范围不限于下述的实施例。
31.下述实施例中,力学性能是根据行业标准gb/t528-2009进行测试,将样品按照国标法裁剪为标准样品后,用万能拉伸机的夹具夹住样品的两端,并测得拉伸前的厚度、长度与宽度,准备好后清零并校准机器然后点击启动按钮,万能拉伸机拉断样品后便可得到应力应变曲线。
32.下述实施例中,压缩变形根据国标gb/t1683-2018,制备高度12.5mm、直径30.0mm的样品,在压缩永久变形模具上进行测试,测试条件为150℃
×
70h,测试结束后取出样品停放1h,测试样品高度,根据式(1)计算压缩永久变形率k(%):
[0033][0034]
式(1)中:h0为橡胶原始高度,单位(mm);h1为橡胶压缩后的高度,单位(mm);hs为模具中限制器的高度,单位(mm)。
[0035]
实施例1
[0036]
本实施例按如下步骤制备低压缩形变高力学性能的丁腈橡胶:
[0037]
步骤1、改性白炭黑的制备
[0038]
称取40质量份的白炭黑置于500ml烧杯中,加入2质量份的3-氨丙基三乙氧基硅烷和300质量份的去离子水,盖保鲜膜进行密封,然后超声分散均匀;超声结束后,将所得溶液磁力搅拌2h,105℃真空干燥24h,研磨,继续在105℃真空干燥至水份完全挥发,得到改性白炭黑。
[0039]
步骤2、改性石墨烯的制备
[0040]
将50质量份的环氧树脂与10质量份的石墨烯放入200ml烧杯中,加入130质量份的乙醇和1.5质量份的甲基六氢苯酐固化剂,电动搅拌下,先加热升温至70℃,再保温3h,使环氧树脂在石墨烯表面包覆生长,过滤、用去离子水洗涤、85℃烘干后,获得表面包覆环氧树脂的石墨烯。
[0041]
在25质量份的表面包覆环氧树脂的石墨烯中加入2质量份的3-氨丙基三乙氧基硅
烷,再加入150质量份的去离子水,盖保鲜膜进行密封,然后超声分散均匀;超声结束后,将所得溶液磁力搅拌1h,105℃真空干燥24h,得到改性石墨烯;
[0042]
将5质量份的改性石墨烯装入长方体容器中,施加橡胶硫化压力10mpa,记录其体积v,从而计算获得改性石墨烯在橡胶硫化压力下的密度ρ=m/v;记录步骤1所得改性白炭黑的总体积,按照复合填料中改性石墨烯在橡胶硫化压力10mpa下的体积百分比为2%确定所需改性石墨烯的质量。
[0043]
步骤3、丁腈橡胶的制备
[0044]
步骤31、分别称取100质量份的nbr生胶(丙烯腈含量为30%)、1.0质量份的硬脂酸(sa)、3.0质量份的氧化锌(zno)、1.5质量份的防老剂(rd)、1.5质量份的促进剂(ns)和1.5质量份的硫磺(s)。
[0045]
步骤32、先用nbr生胶洗辊,去除双辊中残留的废胶和小料,待双辊清洗干净后,调整辊间距,将100质量份的nbr生胶放入双辊之间,打开开炼机电源进行生胶的开炼,待生胶粘辊后依次加入sa、zno和rd,待小料混炼均匀后再少量多次地加入步骤1所制备的全部改性白炭黑以及步骤2所制备的所需量的石墨烯作为复合填料进行开炼共混,待复合填料混炼均匀后,再依次向开炼中的生胶加入ns和s,打三角包多次后薄通出片,得到待硫化的胶。
[0046]
步骤33、将步骤32所制得的胶置于室温条件下干燥24h后,用利用橡胶加工分析仪(rpa8000)对混炼胶的硫化特性进行测试,测试模式为mdr、温度为160℃、频率1hz、应变0.5deg,可以得到硫化时间(tc90)。
[0047]
根据硫化时长564秒,在10mpa压力下利用平板硫化仪进行硫化后置于室温24h后便可得到目标胶。
[0048]
对比例1
[0049]
本对比例按照实施例1步骤3的方法制备丁腈橡胶,区别在于所用填料仅为40质量份的白炭黑。
[0050]
对比例2
[0051]
本对比例按照实施例1步骤3的方法制备丁腈橡胶,区别在于所用填料仅为按步骤1改性后的白炭黑,不加石墨烯。
[0052]
对比例3
[0053]
本对比例按照实施例1步骤3的方法制备丁腈橡胶,区别在于所用复合填料为40质量份未改性的白炭黑和未改性的石墨烯(复合填料中石墨烯在橡胶硫化压力10mpa下的体积百分比为2%)。
[0054]
对比例4
[0055]
本对比例按照实施例1步骤3的方法制备丁腈橡胶,区别在于所用填料仅为按步骤1改性后的白炭黑和未改性的石墨烯(复合填料中石墨烯在橡胶硫化压力10mpa下的体积百分比为2%)。
[0056]
对比例5
[0057]
本对比例按照实施例1步骤3的方法制备丁腈橡胶,区别在于所用填料仅为按步骤1改性后的白炭黑和未包覆环氧树脂仅通过3-氨丙基三乙氧基硅烷改性的石墨烯(复合填料中石墨烯在橡胶硫化压力10mpa下的体积百分比为2%)。
[0058]
图1中可以看出3-氨丙基三乙氧基硅烷对白炭黑表面改性后,在1625cm-1
归属于
sio2表面的oh伸缩振动吸收峰,1078cm-1
和798cm-1
波数所对应的峰为si-o-si的反对称伸缩对称吸收峰和弯曲振动伸缩峰,且弯曲振动伸缩峰较未改性有明显增强。此外在波数为2893cm-1
、2925cm-1
处出现甲基和亚甲基的c-h伸缩振动峰,该峰归属于kh550上的-ch2的吸收峰,以上说明kh550成功接枝到sio2表面。
[0059]
将各实施例与对比例所得橡胶样品在液氮下进行脆断,利用s-4800型扫描电子显微镜对橡胶的断面形貌进行分析。图2中a、b、c、d、e、f分别为实施例1及对比例1、2、3、4、5所得橡胶样品的断面sem图。图2a可以看出经过kh550改性后的白炭黑再混入一定体积经过kh550改性后的表面包裹环氧树脂的石墨烯作为混合填料后,两种填料nbr基质中能够实现良好的分散,增加了填料与丁腈胶之间的界面相容性,限制了应变下的橡胶分子的相对位移,橡胶的力学性能的得到显著提高,且压缩永久变形性能最好。图2b可以看出未用3-氨丙基三乙氧基硅烷去处理白炭黑时,将纯白炭黑作为填料制得的混合胶其白炭黑团聚情况比较严重,而且是多层堆积,尺寸较大,分布不均匀,团聚的白炭黑没有被橡胶包裹住,导致结合胶含量少,橡胶间的相互作用力低,这也是影响nbr橡胶力学性能的主要原因,从而导致橡胶的力学性能下降,压缩形变性能变差。从图2c中可以看出经过kh550改性后,白炭黑分散比较均匀,很少出现团聚,放大两千倍时其断面依旧很规整,力学性能和压缩形变得到提升但不是最佳。图2d可以看出当用未经kh550改性的纯白炭黑与纯石墨烯做复合填料时,其断面具有较多团聚的复合填料,且复合填料的分散性变差,因此力学性能和压缩形变性能都会变差。图2e可以看出用kh550改性后的白炭黑可以在生胶中均匀分布,但是未经过kh550改性后的石墨烯则在断面中出现团聚现象,由于填料之间的作用力远小于填料与橡胶基体间的作用力,团聚的石墨烯会在橡胶的拉伸和压缩测试中使其结果均变差。图2f可以看出经过kh550改性后的白炭黑与石墨烯复合填料能够在橡胶集体中分布均匀,但由于没有环氧树脂与石墨烯和橡胶基体间的作用力因此其拉伸与压缩结果相对于实施例1较差。
[0060]
图3为实施例1及对比例1、2、3、4、5所制得的橡胶样品在150℃、70h条件下测得的永久压缩变形率,从图中可以看出:经过高温热压,实施例1所制的nbr(以改性白炭黑+改性且包覆石墨烯作为填料)的压缩变形率为12.32%,对比例1所制得的nbr(以纯白炭黑作为填料)压缩变形率为40.82%,对比例2所制得的nbr(以改性白炭黑作为填料)的压缩变形率降低到24.41%,对比例3所制得的nbr(以纯白炭黑+纯石墨烯作为填料)的压缩变形率为29.45%,对比例4所制得的nbr(以改性白炭黑+纯石墨烯作为填料)的压缩变形率降低到22.17%,而对比例5所制得的nbr(以改性白炭黑+改性但未包覆的石墨烯作为填料)的压缩永久变形率为20.16%。实施例1所制得的nbr压缩永久变形率与对比例相比,显著降低。
[0061]
图4为实施例1及对比例1、2、3、4、5所制得的橡胶样品进行力学性能测试的最大应力性能图,由图可以看出:对比例1所制得的nbr最大应力为15.68mpa,对比例2所制得的nbr最大应力为19.63mpa,对比例3所制得的nbr最大应力为20.52mpa,对比例4、5所制得的nbr最大应力分别为21.48mpa、24.64mpa。而实施例1所制得的nbr最大应力为31.45mpa,相比对比例显著提升。
[0062]
图5为实施例1及对比例1、2、3、4、5所制得的橡胶进行力学性能测试的最大应变性能图,由图可以看出:对比例1所制得的nbr最大应变为1180%,对比例2所制得的nbr最大应变为1402%,对比例3所制得的nbr最大应变为1450%,对比例4、5所制得的nbr最大应变分
别为1490%、1510%。而实施例1所制得的nbr最大应变为1680%,相比对比例显著提升。
[0063]
以上所述仅为本发明的较佳实施例而已,并不用以限制本发明,凡在本发明的精神和原则之内所作的任何修改、等同替换和改进等,均应包含在本发明的保护范围之内。