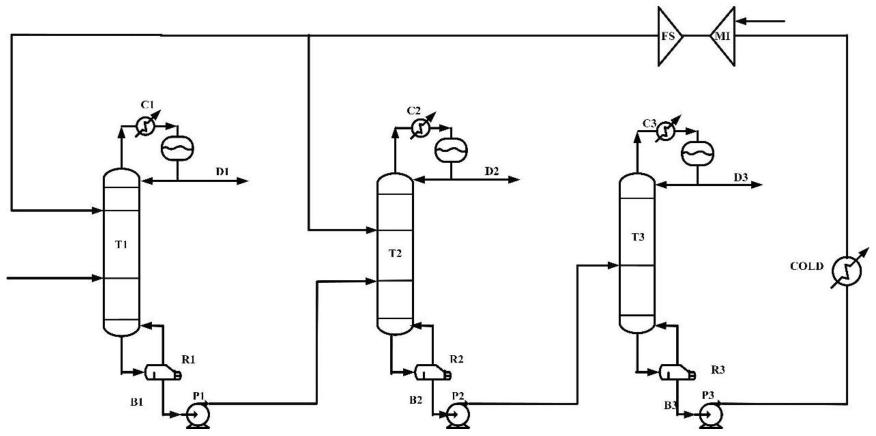
一种萃取变压精馏分离乙酸乙酯-乙醇-丁酮混合物的方法
【技术领域】
1.本发明属于化工分离纯化领域,具体涉及一种萃取变压精馏分离乙酸乙酯-乙醇-丁酮混合物的方法,进一步说,是涉及一种以二甲基亚砜作为萃取剂采用萃取变压精馏分离乙酸乙酯-乙醇-丁酮混合物的方法。
背景技术:2.乙酸乙酯、乙醇、丁酮是日常生活中常见的化学物质。乙酸乙酯是应用最广的脂肪酸酯之一,是一种快干性溶剂,具有优异的溶解能力,是极好的工业溶剂,也可用于柱层析的洗脱剂,在纺织工业中可用作清洗剂,在食品工业中可作为特殊改性酒精的香味萃取剂,还用作制药过程和有机酸的萃取剂。乙醇是重要的有机溶剂,广泛用于医药、涂料、卫生用品、化妆品、油脂等各个方面,占乙醇总耗量的50%左右。乙醇是重要的基本化工原料,并衍生出医药、染料、涂料、香料、合成橡胶、洗涤剂、农药等产品的许多中间体。丁酮主要用作溶剂,如用于润滑油脱蜡、涂料工业及多种树脂溶剂、植物油的萃取过程及精制过程的共沸精馏,其优点是溶解性强,挥发性比丙酮低,属中沸点酮类溶剂。在丁烷氧化生产乙酸过程中,易产生含乙酸乙酯-乙醇-丁酮的废液,而乙醇、乙酸乙酯是非常重要的有机溶剂和有机合成助剂。常压下,由于乙醇/乙酸乙酯、乙醇/丁酮、乙酸乙酯/丁酮能形成共沸物,这增加了分离难度。
3.本发明采用萃取变压精馏装置实现了乙酸乙酯-乙醇-丁酮混合物高纯度分离回收,以二甲基亚砜为萃取剂,利用二甲基亚砜和压力对乙醇/乙酸乙酯、乙醇/丁酮、乙酸乙酯/丁酮共沸物的相对挥发度影响大的特性实现分离。分离后的乙酸乙酯、乙醇、丁酮的纯度均高达99.9%以上,并且可以实现萃取剂高纯度回收再利用,大大降低了分离成本,该方法能耗低、设备少且工艺简单。
技术实现要素:4.[要解决的技术问题]
[0005]
本发明的另一个目的是提供使用所述装置萃取变压精馏分离乙酸乙酯-乙醇-丁酮混合物的方法。
[0006]
本发明的目的是提供一种二甲基亚砜萃取变压精馏分离乙酸乙酯-乙醇-丁酮混合物的装置。
[0007]
本发明的另一个目的是提供二甲基亚砜在萃取变压精馏分离乙酸乙酯-乙醇-丁酮混合物中作为萃取剂的用途。
[0008]
[技术方案]
[0009]
本发明是通过下述技术方案实现的。
[0010]
一种萃取变压精馏分离乙酸乙酯-乙醇-丁酮混合物的方法,其特征在于实现该方法的装置主要包括以下部分:精馏塔1(t1)、精馏塔2(t2)、精馏塔3(t3)、冷凝器1(d1)、冷凝器2(d2)、冷凝器3(d3)、再沸器1(r1)、再沸器2(r2)、再沸器3(r3)、冷却器(cold)、混合器
(mi)、分离器(fs)、离心泵(p1)、离心泵(p2);其中精馏塔1(t1)底部物流经过离心泵(p1)进入精馏塔2(t2),在精馏塔1(t1)塔顶物流采出高纯度产品乙酸乙酯;精馏塔2(t2)底部物流经过离心泵(p1)进入精馏塔3(t3),在精馏塔2(t2)塔顶物流采出高纯度产品乙醇,在精馏塔3(t3)塔顶物流采出高纯度产品丁酮;精馏塔3(t3)底部流出的高纯度萃取剂经过离心泵(p2)、冷却器(cold)、混合器(mi)和分离器(fs)循环回用于萃取塔;
[0011]
该分离方法主要包括以下步骤:
[0012]
(1)乙酸乙酯-乙醇-丁酮混合物从精馏塔(t1)的底部进入,萃取剂从精馏塔1(t1)的顶部进入,经有效接触分离后,在精馏塔1(t1)塔顶物流采出高纯度产品乙酸乙酯,萃余相中丁酮-乙醇-萃取剂混合物从精馏塔1(t1)塔底经离心泵(p1)进入精馏塔2(t2);
[0013]
(2)丁酮-乙醇-萃取剂混合物从精馏塔2(t2)的底部进入,萃取剂从精馏塔2(t2)的顶部进入,经有效接触分离后,在精馏塔2(t2)塔顶物流采出高纯度产品乙醇,萃余相中丁酮-萃取剂混合物从精馏塔2(t2)塔底进入精馏塔3(t3);
[0014]
(3)丁酮-萃取剂混合物从精馏塔3(t3)的底部进入,经有效接触分离后,在精馏塔3(t3)塔顶物流采出高纯度产品丁酮,高纯度萃取剂从精馏塔3(t3)塔底流出,经过离心泵(p2)、冷却器(cold)、混合器(mi)和分离器(fs)进入精馏塔(t1)循环使用;
[0015]
所述萃取剂为二甲基亚砜。
[0016]
根据本发明的另一优选实施方式,其特征在于:精馏塔1(t1)塔板数为70-75块,压力为0.4-0.5atm,温度为50~130℃;精馏塔2(t2)塔板数为105-110块,压力为5-6atm,温度为120~250℃;精馏塔3(t3)塔板数为25~30块,温度为70~200℃。
[0017]
根据本发明的另一优选实施方式,其特征在于:所述萃取剂为二甲基亚砜。
[0018]
根据本发明的另一优选实施方式,其特征在于:所述萃取剂与乙酸乙酯-乙醇-丁酮混合物的进料流量摩尔比为2.8~2.9。
[0019]
根据本发明的另一优选实施方式,其特征在于:所述的乙酸乙酯-乙醇-丁酮混合物中,乙酸乙酯摩尔分数为20%,乙醇摩尔分数为33%,丁酮摩尔分数为47%。
[0020]
根据本发明的另一优选实施方式,其特征在于:精馏塔1(t1)塔顶回收的乙酸乙酯纯度高于99.9%,收率高于99.9%;精馏塔2(t2)塔顶回收的乙醇纯度高于99.9%,收率高于99.9%;精馏塔3(t3)塔顶回收的丁酮纯度高于99.9%,收率高于99.9%。
[0021]
[有益效果]
[0022]
本发明与现有技术相比,主要有以下有益效果:
[0023]
(1)采用该方法分离乙酸乙酯-乙醇-丁酮混合物,得到高纯度的乙酸乙酯、乙醇、丁酮,解决了乙酸乙酯-乙醇-丁酮混合物难以分离的问题。
[0024]
(2)该方法具有工艺简单,投资设备少,分离后乙酸乙酯、乙醇、丁酮的纯度高等优点,所采用的萃取剂二甲基亚砜易于回收、化学热稳定性好、绿色无污染。
[0025]
(3)该方法中采用的萃取剂二甲基亚砜几乎不挥发,减少了萃取剂的损失,避免了乙酸乙酯、乙醇、丁酮的二次污染,此外,萃取剂易于回收利用,降低了分离成本。
【附图说明】
[0026]
图1是本发明萃取变压精馏分离乙酸乙酯-乙醇-丁酮混合物的工艺流程图。
[0027]
图中,t1-精馏塔、t2-精馏塔、t3-精馏塔;b1-塔底物流;b2-塔底物流;b3-塔底物
流;cold-冷却器;c1-冷却器;c2-冷却器;c3-冷却器;d1-冷凝器;d2-冷凝器;d3-冷凝器;r1-再沸器;r2-再沸器;r3-再沸器;fs-分离器;mi-混合器;p1-离心泵、p2-离心泵;p3-离心泵。
【具体实施方式】
[0028]
实施例1:
[0029]
进料流量为100kmol/h,进料中含乙酸乙酯20%,乙醇33%,丁酮47%(摩尔分数),精馏塔1(t1)理论板数为71块,压力为0.5atm,乙酸乙酯-乙醇-丁酮混合物从精馏塔1(t1)的底部进入,萃取剂从精馏塔1(t1)的顶部进入,萃取剂为二甲基亚砜,流量为200kmol/h;丁酮-乙醇-萃取剂混合物从精馏塔2(t2)的底部进入,萃取剂从精馏塔2(t2)的顶部进入,精馏塔2(t2)理论板数为108块,压力为5.5atm,萃取剂为二甲基亚砜,流量为90kg/h(萃取剂与乙酸乙酯-乙醇-丁酮混合物的进料流量摩尔比为2.9)。丁酮-萃取剂混合物从精馏塔3(t3)的底部进入。精馏塔3(t3)理论板数为26块,精馏塔的操作压力为常压,分离后乙酸乙酯的纯度为99.97%,收率为100%,乙醇的纯度为99.93%,收率为99.92%,丁酮的纯度为99.98%,收率为99.99%。
[0030]
实施例2:
[0031]
进料流量为100kmol/h,进料中含乙酸乙酯20%,乙醇33%,丁酮47%(摩尔分数),精馏塔1(t1)理论板数为73块,压力为0.45atm,乙酸乙酯-乙醇-丁酮混合物从精馏塔1(t1)的底部进入,萃取剂从精馏塔1(t1)的顶部进入,萃取剂为二甲基亚砜,流量为190kmol/h;丁酮-乙醇-萃取剂混合物从精馏塔2(t2)的底部进入,萃取剂从精馏塔2(t2)的顶部进入,精馏塔2(t2)理论板数为107块,压力为5.4atm,萃取剂为二甲基亚砜,流量为90kg/h(萃取剂与乙酸乙酯-乙醇-丁酮混合物的进料流量摩尔比为2.8)。丁酮-萃取剂混合物从精馏塔3(t3)的底部进入。精馏塔3(t3)理论板数为27块,精馏塔的操作压力为常压,分离后乙酸乙酯的纯度为99.98%,收率为100%,乙醇的纯度为99.95%,收率为99.94%,丁酮的纯度为99.98%,收率为99.99%。
[0032]
实施例3:
[0033]
进料流量为100kmol/h,进料中含乙酸乙酯20%,乙醇33%,丁酮47%(摩尔分数),精馏塔1(t1)理论板数为74块,压力为0.48atm,乙酸乙酯-乙醇-丁酮混合物从精馏塔1(t1)的底部进入,萃取剂从精馏塔1(t1)的顶部进入,萃取剂为二甲基亚砜,流量为200kmol/h;丁酮-乙醇-萃取剂混合物从精馏塔2(t2)的底部进入,萃取剂从精馏塔2(t2)的顶部进入,精馏塔2(t2)理论板数为110块,压力为6atm,萃取剂为二甲基亚砜,流量为80kg/h(萃取剂与乙酸乙酯-乙醇-丁酮混合物的进料流量摩尔比为2.8)。丁酮-萃取剂混合物从精馏塔3(t3)的底部进入。精馏塔3(t3)理论板数为29块,精馏塔的操作压力为常压,分离后乙酸乙酯的纯度为99.99%,收率为100%,乙醇的纯度为99.96%,收率为99.96%,丁酮的纯度为99.98%,收率为99.99%。