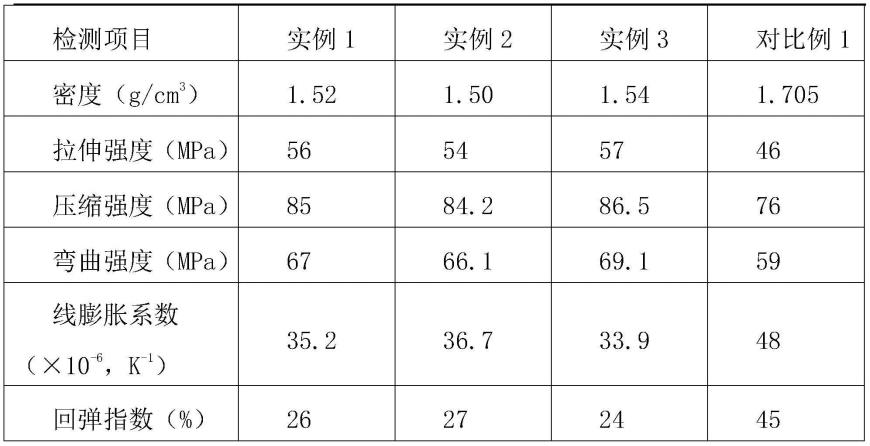
1.本发明涉及航空零部件生产制作领域,具体涉及一种航空连接件成型模具板材及制备方法。
背景技术:2.飞机蒙皮之间、蒙皮与内部结构件之间是通过连接件来实现两者的紧连接。连接件多为90
°
、60
°
折弯件,宽度尺寸100mm左右,连接件尺寸精度直接决定了飞机两块零件的连接精度,因此,对连接件尺寸精度要求非常高。该连接件成型工艺为:铝板或金属板放置于液压成型模具中,通过辊压设备成型折弯件,再将折弯件放置在精细成型模具上,通过手工敲击零件表面,使零件各处贴合模具,得到满足要求的连接件。要求精细成型模具具备强度高、回弹性小、硬度高等特性。传统精细成型模具采用金属材料和环氧复合材料加工而成,金属材料制备的精细成型模具性能均满足使用要求,但硬度较高,容易在零件上形成划痕,对飞机而言是致命的。且工装加工周期长,易生锈,保养难度大。环氧复合材料,硬度低于金属,手工敲击不易划伤零件,但敲击时模具材料回弹系数过大,造成需要反复多次敲击,才能达到零件尺寸要求。
技术实现要素:3.本发明针对现有技术的不足,提出一种材料强度高,材料回弹系数低、且加工性能优良的环境友好型国产复合板材,满足航空飞机连接件制造模具使用要求,缩短连接件手工精细成型时间,减轻工人劳动强度的航空连接件成型模具板材及制备方法,具体技术方案如下:
4.1、一种航空连接件成型模具板材,其特征在于:包括主剂聚酯多元醇、固化剂甲苯-2,4-二异氰酸酯及其预聚物、填料复合型氧化铝和助剂a消泡剂。
5.2、根据权利要求1所述航空连接件成型模具板材,其特征在于:所述主剂聚酯多元醇的质量份数为0.95-1.05份、固化剂甲苯-2,4-二异氰酸酯及其预聚物的质量份数为1.4-1.7份、填料复合型氧化铝的质量份数为1.9-2.3份、助剂a消泡剂添加比例为总量的0.5%~1%。
6.3、根据权利要求1或者2所述航空连接件成型模具板材的制备方法,其特征在于,具体步骤为:
7.步骤一:模具处理,清理模具表面,再加热至170℃-190℃,表面喷涂脱模剂;
8.步骤二:将模具放入烤箱内,40-50℃下预热1-2h,备用;
9.步骤三:将主剂置于40-50℃下预烘1-2h,降低主剂的粘度,复合氧化铝置于80-100℃下预烘1-2h,去除原材料中的水分;
10.步骤四:真空搅拌设备设定温度40-50℃,按照比例将主剂倒入真空搅拌设备中进行搅拌;预烘后的复合氧化铝经过震动筛过滤分散,吸入吸附塔从真空搅拌设备上端进入真空搅拌设备,两者搅拌均匀,搅拌设备中真空度控制在-0.06mpa~-0.08mpa,真空搅拌设
备搅拌时间不低于2-3h,目测混合料无结团、白点,按比例加入固化剂和助剂a,持续保持温度和真空度,搅拌时间介于30min~50min,确保混合料搅拌均匀,粘度不大于3000mpa2s,无分层等现象;
11.步骤五:将搅拌均匀的混合料恢复常压状态,打开烘箱,将混合料缓慢倒入方形模具中,在40-50℃温度下静置1-2h,随后升温至70-90℃,在该温度下保持20-24h。
12.步骤六:固化时间结束后,降温至40-50℃,脱模,取出零件。
13.本发明的有益效果为:本聚氨酯复合材料是由柔性链段(软段)和刚性链段(硬段)交替组成的嵌段共聚物,其中,软段为主剂聚酯多元醇,主要贡献复合材料的弹性和低温性能,采用分子结构设计的方法,通过调整主剂中聚酯的相对分子质量,可以制备出不同性能要求低回弹减震弹性体,对复合材料回弹性有一定的影响。酯基空间位阻比醚基的大,分子链段柔顺性差,链段活动受到限制,因此酯基多元醇制备的聚氨酯回弹性低于聚醚多元醇型。硬段为tdi异氰酸酯,直接影响着聚氨酯弹性体的回弹性能、刚度和强度。tdi异氰酸酯的异构体结构对称性和规整性差,使得软段和硬段的微相分离程度小,主链上大分子链段柔顺性较差,从而使得该聚氨酯体系的回弹性低。填料为复合氧化铝,粒度小,聚氨酯对其包裹较好,硬度相对较高,添加到聚氨酯体系中,也减低了体系回弹性。
14.成型工艺方面,通过添加消泡剂,降低了体系内部孔隙,提高致密性;填料高温预烘,除去水分,有效避免固化剂与水反应生成胺和二氧化碳,提升体系的致密性;填料经振动筛过滤分散,缩短搅拌时间,提高搅拌均匀性;搅拌操作全部在真空下进行,有效隔绝空气,均可提升体系的致密性。
15.最终采用本发明配方以及制备方法生产出的模具板材,材料的密度降低,拉伸强度、弯曲强度等显著提高,回弹指数显著降低,具备较好的强度及低回弹性能,以此满足航空飞机零件连接件的手工成型操作。
具体实施方式
16.下面对本发明的较佳实施例进行详细阐述,以使本发明的优点和特征能更易于被本领域技术人员理解,从而对本发明的保护范围做出更为清楚明确的界定。
17.实例一:
18.本实例主剂采用聚醚多元醇,牌号sw-72a,液态,粘度不大于5000mpa
·
s,固化剂为mdi异氰酸酯牌号sw-72b,液态,粘度不大于600mpa
·
s,填料为复合氧化铝,牌号sw-716a,粉状,d50为15-40μm,助剂为消泡剂zj-1,液态,半透明液体,粘度800-1500mpa
·
s,各组分质量份数为:主剂1.0份,固化剂1.6份,填料2.1份,助剂0.8%。
19.a、模具处理
20.模具选不锈钢金属模具,加热至180℃,表面喷涂脱模剂2遍,均匀擦拭,不能有脱模剂留痕等。浇注前,经脱模剂处理好的模具放入烘箱内,50℃下预热1.5h,备用。
21.b、浇注及固化
22.预烘:将主剂置于45℃下预烘1.5h,降低主剂的粘度;复合氧化铝置于90℃下预烘1.5h,去除原材料中的水分。
23.预混合:真空搅拌设备设定温度45℃,按照比例将主剂倒入真空搅拌设备中进行搅拌;预烘后的复合氧化铝经过震动筛过滤分散,吸入吸附塔从真空搅拌设备上端进入真
空搅拌设备,两者搅拌均匀,搅拌设备中真空度控制在-0.07mpampa,真空搅拌设备搅拌时间不低于2.5h,目测混合料无结团、白点。
24.按比例缓慢加入固化剂和助剂a,持续保持温度和真空度,搅拌时间40min,确保混合料搅拌均匀,粘度不大于3000mpa2s,无分层等现象。
25.浇注及固化:将搅拌均匀的混合料恢复常压状态,打开烘箱,将混合料缓慢倒入方形模具中,在40℃温度下静置1.5h,随后升温80℃,在该温度下保持22h。固化时间结束后,降温至50℃,脱模,取出零件。可进行后续加工处理。
26.实例二:
27.本实例主剂采用聚醚多元醇(sw-72a),固化剂为mdi异氰酸酯(sw-72b),填料为复合氧化铝(sw-716a),助剂为消泡剂(zj-1),各组分质量份数为:主剂0.95份,固化剂1.4份,填料2.3份,助剂0.5%。
28.a、模具处理
29.模具选不锈钢金属模具,加热至180℃,表面喷涂脱模剂2遍,均匀擦拭,不能有脱模剂留痕等。浇注前,经脱模剂处理好的模具放入烘箱内,45℃下预热1h,备用。
30.b、浇注及固化
31.预烘:将主剂置于40℃下预烘1h,降低主剂的粘度;复合氧化铝置于100℃下预烘2h,去除原材料中的水分。
32.预混合:真空搅拌设备设定温度40℃,按照比例将主剂倒入真空搅拌设备中进行搅拌;预烘后的复合氧化铝经过震动筛过滤分散,吸入吸附塔从真空搅拌设备上端进入真空搅拌设备,两者搅拌均匀,搅拌设备中真空度控制在-0.06mpampa,真空搅拌设备搅拌时间不低于2h,目测混合料无结团、白点。
33.按比例缓慢加入固化剂和助剂a,持续保持温度和真空度,搅拌时间40min,确保混合料搅拌均匀,粘度不大于3000mpa2s,无分层等现象。
34.浇注及固化:将搅拌均匀的混合料恢复常压状态,打开烘箱,将混合料缓慢倒入方形模具中,在40℃温度下静置1h,随后升温70℃,在该温度下保持20h。固化时间结束后,降温至40℃,脱模,取出零件。可进行后续加工处理。
35.实施例三:
36.本实例主剂采用聚醚多元醇(sw-72a),固化剂为mdi异氰酸酯(sw-72b),填料为复合氧化铝(sw-716a),助剂为消泡剂(zj-1),各组分质量份数为:主剂1.05份,固化剂1.7份,填料1.9份,助剂1%。
37.a、模具处理
38.模具选不锈钢金属模具,加热至180℃,表面喷涂脱模剂2遍,均匀擦拭,不能有脱模剂留痕等。浇注前,经脱模剂处理好的模具放入烘箱内,50℃下预热2h,备用。
39.b、浇注及固化
40.预烘:将主剂置于50℃下预烘2h,降低主剂的粘度;复合氧化铝置于80℃下预烘1h,去除原材料中的水分。
41.预混合:真空搅拌设备设定温度40℃,按照比例将主剂倒入真空搅拌设备中进行搅拌;预烘后的复合氧化铝经过震动筛过滤分散,吸入吸附塔从真空搅拌设备上端进入真空搅拌设备,两者搅拌均匀,搅拌设备中真空度控制在-0.08mpampa,真空搅拌设备搅拌时
间不低于3h,目测混合料无结团、白点。
42.按比例缓慢加入固化剂和助剂a,持续保持温度和真空度,搅拌时间50min,确保混合料搅拌均匀,粘度不大于3000mpa2s,无分层等现象。
43.浇注及固化:将搅拌均匀的混合料恢复常压状态,打开烘箱,将混合料缓慢倒入方形模具中,在40℃温度下静置2h,随后升温90℃,在该温度下保持24h。固化时间结束后,降温至50℃,脱模,取出零件。可进行后续加工处理。
44.性能测试:
45.对实施例1-3所得连接件模具材料的密度、压缩强度、弯曲强度、拉伸器强度、线膨胀系数、回弹指数等性能进行检测,验证其性能。同时,与采用不锈钢材质和环氧树脂复合材料制成的模具相关性能进行对比。
46.(1)密度测量:按照astm d792第5条进行测试,测试温度23
±
2℃,测试5个试样,取平均值;
47.(2)拉伸强度:按照gb/t 1040.1-2008中第9条进行测试,测试温度23
±
2℃,拉伸速率5mm/min,测试5个试样,取平均值;
48.(3)弯曲强度:按照gb/t 9341-2008中第8条进行测试,测试温度23
±
2℃,弯曲速率2mm/min,测试5个试样,取平均值;
49.(4)压缩强度:按照gb/t 1041-2008中第9条进行测试,测试温度23
±
2℃,压缩速率5mm/min,测试5个试样,取平均值;
50.(5)线膨胀系数:按照astm d696-2016中第9条进行测试,温度范围25~80℃,压缩速率测试5个试样,取平均值;
51.(6)回弹指数:回弹试验是一项力学性能试验,回弹试验习惯上称为冲击弹性试验,是检验应用最广泛的动态试验方法。其试验结果用回弹性或回弹率表示。回弹性的定义是受冲击的试样在产生形变恢复原形的过程中,输出能与输入能的比值。回弹性是检测力学性能指标之一,是反映柔顺材料的弹性大小。按gb/t 1681—2009中第5条进行测试,温度范围:10~40℃,测试5个试样,取平均值。
52.3个实例材料测试结果如下表所示:
[0053][0054]
从表中可以看出,对比环氧树脂基复合材料对比例1,实例1-3采用新型复合材料
浇注配方及成型工艺,材料的密度降低,拉伸强度、弯曲强度等显著提高,回弹指数显著降低,具备较好的强度及低回弹性能。本发明中,在复合氧化铝填料中添加了一些低回弹性填料,与主剂和固化剂有机结合,形成了本发明中连接件用成型模具特有的高强度、低回弹性等优异性能,以此满足航空飞机零件连接件的手工成型操作。