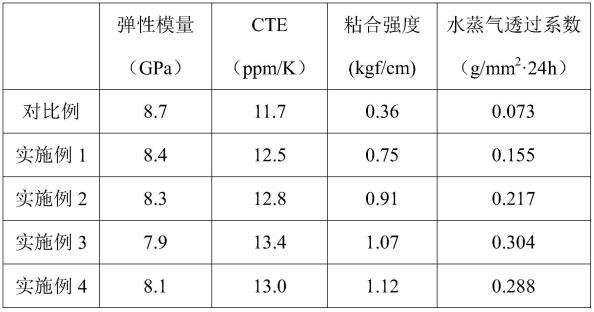
1.本发明涉及聚酰亚胺薄膜技术领域,尤其涉及一种具有改善的粘合力和透湿速率的聚酰亚胺薄膜及制备方法。
背景技术:2.由3,3',4,4'-联苯四甲酸二酐(s-bpda)和对苯二胺(pda)制备的聚酰胺酸,经流延成膜、亚胺化处理后可获得聚酰亚胺薄膜,该聚酰亚胺薄膜具有高的尺寸稳定性和优异的力学性能,被广泛用于集成电路领域。然而,由上述s-bpda/pda组分制备的聚酰亚胺薄膜的表面活性差、粘合力低,不利于与其他材料形成层压体;且上述聚酰亚胺薄膜的透湿速率也较低,用作电子部件的基板时,通过焊接处理时会形成高温状态,膜内部的水分气化,由此引发薄膜起泡或者剥离。
技术实现要素:3.基于背景技术存在的技术问题,本发明提出了一种具有改善的粘合力和透湿速率的聚酰亚胺薄膜及制备方法,该薄膜在具有优异的力学性能和高的尺寸稳定性的基础上,同时还具有很好的粘合强度和水蒸气透过系数。
4.本发明提出的一种具有改善的粘合力和透湿速率的聚酰亚胺薄膜,是由二元酐单体和二元胺单体经缩聚反应得到聚酰胺酸树脂,再经流延成膜、热酰亚胺化处理后得到的;所述二元酐单体包括3,3',4,4'-联苯四甲酸二酐和4,4'-联苯醚二酐,其摩尔百分比为70~99:1~30;所述二元胺单体包括对苯二胺和二氨基二苯醚,其摩尔百分比为70~99:1~30。
5.优选地,所述二氨基二苯醚选自3,4'-二氨基二苯醚、4,4'-二氨基二苯醚中的一种或其组合。
6.优选地,所述对苯二胺和二氨基二苯醚的摩尔百分比为80~95:5~20。
7.优选地,所述3,3',4,4'-联苯四甲酸二酐和4,4'-联苯醚二酐的摩尔百分比为80~95:5~20。
8.优选地,所述4,4'-联苯醚二酐和二氨基二苯醚的用量占所有单体总摩尔份数的5~30%。
9.上述所有单体,包括反应所用的二元酐单体和二元胺单体。
10.本发明还提出了上述具有改善的粘合力和透湿速率的聚酰亚胺薄膜的制备方法,包括以下步骤:
11.s1、保护气氛下,将对苯二胺和二氨基二苯醚加入到极性非质子溶剂中,搅拌溶解,得二胺溶液;
12.s2、向二胺溶液中分批加入3,3',4,4'-联苯四甲酸二酐和4,4'-联苯醚二酐,进行缩聚反应,制得聚酰胺酸树脂;
13.s3、将聚酰胺酸树脂流延成膜,再进行梯度热酰亚胺化处理,即得聚酰亚胺薄膜。
14.优选地,s1中,所述极性非质子溶剂选自n-甲基吡咯烷酮、n,n-二甲基甲酰胺、n,n-二甲基乙酰胺中的一种或一种以上。
15.优选地,s2中,缩聚反应的反应温度为20~30℃,反应时间为1~24h。
16.优选地,s3中,梯度热酰亚胺化处理的具体操作如下:100~130℃下保温5~10min、180~200℃下保温5~10min、230~250℃下保温5~10min、300~320℃下保温5~10min、400~420℃下保温5~10min。
17.与现有技术相比,本发明的有益效果主要体现在以下几个方面:
18.1.本发明通过引入联苯醚类单体—4,4'-联苯醚二酐和二氨基二苯醚,并调整联苯醚类单体用量来调节制备的聚酰胺酸树脂中柔性醚键含量,相较于传统以3,3',4,4'-联苯四甲酸二酐单体和对苯二胺单体缩聚制备聚酰胺酸树脂,本发明在大分子序列结构中引入柔性醚键,增加了分子链的柔顺性,使制备的聚酰亚胺薄膜粘合强度增大。
19.2.本发明通过原位聚合法,使联苯醚类单体与其他聚合单体均匀分散在溶剂中,通过调整反应单体的加料顺序,将二胺单体溶解到有机溶剂中,再将二酐分批加入,使得二胺和二酐充分混合均匀进行缩聚反应形成无规型聚合物,降低以3,3',4,4'-联苯四甲酸二酐单元和对苯二胺单元的聚合物分子链的紧密性和规整性,从而增加了分子链对水蒸气的透过率,提高薄膜的透湿速率。
20.3.本发明在保持原有s-bpda/pda组分制备的聚酰亚胺薄膜优异性能的基础上(优异的力学性能、高的尺寸稳定性),改善了薄膜的粘合强度和水蒸气透过系数的性能,薄膜粘合强度保持0.75kgf/cm以上,水蒸气透过系数保持0.155g/mm2·
24h以上,避免薄膜在高温焊接下产生发泡或剥落等现象,弥补了应用过程中的不足之处。
具体实施方式
21.下面,通过具体实施例对本发明的技术方案进行详细说明。
22.实施例1
23.s1、在氮气氛围下,在500ml反应瓶中添加12.31g的对苯二胺和1.22g的4,4'-二氨基二苯醚,然后加入200ml的n,n-二甲基乙酰胺作为溶剂,设定反应温度为25℃,均匀搅拌30min,确认单体溶解完之后,将33.50g的3,3',4,4'-联苯四甲酸二酐和1.86g的4,4'-联苯醚二酐分四次加入聚合反应瓶中,反应12h后,最终获得聚酰胺酸树脂。
24.s2、将聚酰胺酸树脂进行12h的真空消泡处理,然后在载体上成膜并干燥以制备凝胶膜。
25.s3、将凝胶膜梯度升温,进行热酰亚胺化反应:包括120℃下保温5min、180℃下保温5min、250℃下保温5min、320℃下保温5min、400℃下保温5min,最终形成聚酰亚胺薄膜。
26.实施例2
27.s1、在氮气氛围下,在500ml反应瓶中添加12.31g的对苯二胺和1.22g的3,4'-二氨基二苯醚,然后加入200ml的n,n-二甲基乙酰胺作为溶剂,设定反应温度为25℃,均匀搅拌30min,确认单体溶解完之后,将28.22g的3,3',4,4'-联苯四甲酸二酐和7.44g的4,4'-联苯醚二酐分四次加入聚合反应瓶中,反应12h后,最终获得聚酰胺酸树脂。
28.s2、将聚酰胺酸树脂进行12h的真空消泡处理,然后在载体上成膜并干燥以制备凝胶膜。
29.s3、将凝胶膜梯度升温,进行热酰亚胺化反应:包括120℃下保温5min、180℃下保温5min、250℃下保温5min、320℃下保温5min、400℃下保温5min,最终形成聚酰亚胺薄膜。
30.实施例3
31.s1、在氮气氛围下,在500ml反应瓶中添加10.39g的对苯二胺和4.80g的3,4'-二氨基二苯醚,然后加入200ml的n,n-二甲基乙酰胺作为溶剂,设定反应温度为25℃,均匀搅拌30min,确认单体溶解完之后,将24.71g的3,3',4,4'-联苯四甲酸二酐和11.16g的4,4'-联苯醚二酐分四次加入聚合反应瓶中,反应12h后,最终获得聚酰胺酸树脂。
32.s2、将聚酰胺酸树脂进行12h的真空消泡处理,然后在载体上成膜并干燥以制备凝胶膜。
33.s3、将凝胶膜梯度升温,进行热酰亚胺化反应:包括120℃下保温5min、180℃下保温5min、250℃下保温5min、320℃下保温5min、400℃下保温5min,最终形成聚酰亚胺薄膜。
34.实施例4
35.s1、在氮气氛围下,在500ml反应瓶中添加9.07g的对苯二胺和7.20g的4,4'-二氨基二苯醚,然后加入200ml的n,n-二甲基乙酰胺作为溶剂,设定反应温度为25℃,均匀搅拌30min,确认单体溶解完之后,将28.22g的3,3',4,4'-联苯四甲酸二酐和7.44g的4,4'-联苯醚二酐分四次加入聚合反应瓶中,反应12h后,最终获得聚酰胺酸树脂。
36.s2、将聚酰胺酸树脂进行12h的真空消泡处理,然后在载体上成膜并干燥以制备凝胶膜。
37.s3、将凝胶膜梯度升温,进行热酰亚胺化反应:包括120℃下保温5min、180℃下保温5min、250℃下保温5min、320℃下保温5min、400℃下保温5min,最终形成聚酰亚胺薄膜。
38.对比例
39.s1、在氮气氛围下,在500ml反应瓶中添加12.96g的对苯二胺,然后加入200ml的n,n-二甲基乙酰胺作为溶剂,设定反应温度为25℃,均匀搅拌30min,确认单体溶解完之后,将35.20g的3,3',4,4'-联苯四甲酸二酐分四次加入聚合反应瓶中,反应12h后,最终获得聚酰胺酸树脂。
40.s2、将聚酰胺酸树脂进行12h的真空消泡处理,然后在载体上成膜并干燥以制备凝胶膜。
41.s3、将凝胶膜梯度升温,进行热酰亚胺化反应:包括120℃下保温5min、180℃下保温5min、250℃下保温5min、320℃下保温5min、400℃下保温5min,最终形成聚酰亚胺薄膜。
42.对本发明实施例1-4和对比例制备的聚酰亚胺薄膜进行性能测试,具体检测性能及指标如下:
43.(a)评价薄膜力学性能:采用弹性模量来表征薄膜力学性能,按照gb/t 1040-2018进行测试;
44.(b)评价薄膜尺寸稳定性:采用线性热膨胀系数(cte)来表征薄膜尺寸稳定性,按照gb/t 1036-2008进行测试;
45.(c)评价薄膜粘合强度:按照gb/t 4851-2014进行测试;
46.(d)评价薄膜水蒸气透过系数:按照gb/t 26253-2010进行测试。
47.检测结果见表1。
48.表1实施例1-4和对比例中制备的聚酰亚胺薄膜的性能数据
[0049][0050]
依据上表性能测试结果,本技术提供的聚酰亚胺薄膜具有保持原有s-bpda/pda组成制备的聚酰亚胺薄膜优异的力学性能和高的尺寸稳定性,同时改善了聚酰亚胺薄膜的粘合力和透湿速率,粘合强度保持0.75kgf/cm以上,水蒸气透过系数保持0.155(g/mm2·
24h)以上,在集成电路领域具有重要应用。
[0051]
以上所述,仅为本发明较佳的具体实施方式,但本发明的保护范围并不局限于此,任何熟悉本技术领域的技术人员在本发明揭露的技术范围内,根据本发明的技术方案及其发明构思加以等同替换或改变,都应涵盖在本发明的保护范围之内。