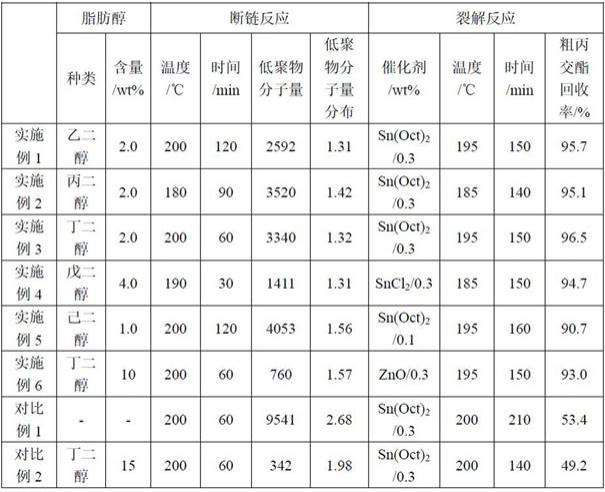
1.本发明涉及一种从聚乳酸废弃物直接回收丙交酯的方法,属聚酯废弃物材料回收技术领域。
背景技术:2.随着不可降解商超购物袋、一次性餐具的限制使用,作为完全可降解的绿色高分子材料的聚乳酸及其衍生物将会日益替代石油基材料的使用。而随着聚乳酸的广泛使用,必将产生大量的废旧聚乳酸。因此,开发废旧聚乳酸回收利用技术具有重要意义。
3.目前,研究较多的回收方法是将聚乳酸材料在催化剂作用下得到有价值的乳酸或乳酸酯。例如,cn 108821972 b在聚乳酸废料中加入固体碱催化剂和有机醇试剂,然后在温度50~180℃醇解0.5~5小时,反应后冷却至室温,过滤或离心;蒸馏回收醇,减压蒸馏得到相应的乳酸烷基酯产物。强碱作为催化剂,会导致大量的废水排放问题。cn 107382718 b以cao/mcf型介孔碱性分子筛为催化剂、以甲醇为反应物降解聚乳酸,反应结束后,经过滤、蒸馏等操作回收乳酸甲酯产品。cn 109942419 a公开了一种以固载化离子液体[tespmim][oac]-zn(oac)2/sba-15为催化剂醇解废聚乳酸材料回收乳酸甲酯的方法。由于聚乳酸在甲醇中难以溶解,使其醇解反应需要在高温、高压或大量的传统酸或碱催化条件下进行。因此,cn 106083566 b提供了一种聚乳酸废弃物的回收方法,将聚乳酸废弃物加热溶解在丙交酯中,再加入水进行反应后,得到反应混合物;然后将上述步骤得到的产物与钙源混合反应后得到乳酸钙。cn 111973929 b提供了一种无溶剂催化降解聚乳酸的方法,将聚乳酸和金属加氢催化剂置于200~300℃反应釜中,主要产物为乳酸乙酯、丙酸乙酯、乙醇和丙酸仲丁酯。
[0004]
目前,关于废旧聚乳酸直接得到其原始聚合单体丙交酯的报道较少。cn 102746270 b将聚乳酸熔体在180~250℃和催化剂存在的条件下,进行断链反应;将断链之后的聚乳酸熔体发生解聚反应,生成粗丙交酯。然而,该方法存在以下两个问题:(1)聚乳酸熔体主要在水分子的作用下降低分子量,反应慢,耗时长;(2)丙交酯回收率不高,经济收益不理想。
[0005]
本发明针对背景技术中所指出的问题及现有技术存在的不足,发明人通过大量的实验研究,开发出了一种有效回收废旧聚乳酸的方法,即利用适量脂肪醇促使聚乳酸分子量降低,进而裂解得到粗丙交酯,本发明方法简单、快速、条件温和,可高效回收粗丙交酯,粗丙交酯中l-丙交酯占比高于95%,可有效实现废旧聚乳酸资源的高价值回收利用。
技术实现要素:[0006]
为了解决上述技术问题,本发明提供了一种由聚乳酸废弃物的回收制备丙交酯的方法,本发明提出的在脂肪醇存在下聚乳酸废弃物的断链反应,可加速断链反应,抑制副反应发生,降低断链反应温度,聚乳酸低聚物的分子量分布窄,提高粗丙交酯回收率,且所得粗丙交酯中内消旋、乳酸、乳酸二聚体含量均较低,回收方法工艺简单、条件温和、安全环
保、适合规模化工业生产。
[0007]
本发明的具体技术方案为:一种由聚乳酸废弃物的回收制备丙交酯的方法,包括以下步骤:(1)聚乳酸废弃物的断链反应:向反应器中加入聚乳酸废弃物与适量的脂肪醇,在加热搅拌条件下进行聚乳酸废弃物的断链反应,制备聚乳酸低聚物;其中断链反应温度为180~220℃,制得的低聚物分子量为400~5000。
[0008]
在步骤(1)中本发明使用脂肪醇加入量远低于现有专利中以甲醇、乙醇等作为溶剂对聚乳酸废弃物进行醇解生成乳酸酯类化合物,能更为有效地提高断链反应速率,同时抑制副反应的发生(如乳酸酯类化合物的生产),所得乳酸低聚物的分子量分布更为均一,使后续反应得到的粗丙交酯回收率提高,内消旋、乳酸、乳酸二聚体含量均较低。
[0009]
(2)聚乳酸低聚物的裂解反应:向步骤(1)制备的聚乳酸低聚物中加入裂解催化剂,经充分混合后进行减压蒸馏操作,聚乳酸低聚物不断裂解,收集得到粗丙交酯。其中裂解温度为170~200℃,真空度为0.1~10kpa。
[0010]
(3)粗丙交酯的提纯:将所述粗丙交酯溶解于有机溶剂中,冷却结晶,抽滤得到丙交酯;重复上述操作多次,真空干燥得到高纯度丙交酯。
[0011]
作为优选,聚乳酸废弃物为聚左旋乳酸、聚右旋乳酸或聚消旋乳酸,所述的聚乳酸废弃物为聚乳酸均聚物、共聚物或共混物。
[0012]
作为优选,聚乳酸废弃物中聚乳酸的数均分子量为103~107g/mol,聚乳酸的重量含量为20%~100%。
[0013]
作为优选,步骤(1)中,所述脂肪醇为乙二醇、丙二醇、丁二醇、戊二醇、己二醇或其组合,特别优选为丁二醇;作为优选,所述脂肪醇与聚乳酸废弃物的重量比为1.0%~8.0%。脂肪醇重量过高,则易引发副反应,生产乳酸酯类化合物,导致丙交酯产率降低;脂肪醇重量过低,则断链反应速率降低,反应时间增大,更优选为2.0%~5.0%。
[0014]
作为优选,步骤(1)中,所述反应温度为180~220℃,更优选为180~200℃;,反应时间为1~3h。
[0015]
作为优选,步骤(1)中,所述聚乳酸低聚物的分子量为400~5000,更优选为500~2000。
[0016]
作为优选,步骤(2)中,所述裂解催化剂为辛酸亚锡、氯化亚锡或氧化锌;所述裂解催化剂与聚乳酸低聚物的重量比为1:10000~1:100,更优选为1:3000~1:800。
[0017]
作为优选,步骤(2)中,所述裂解温度为170~200℃,更优选为180~195℃;真空度为0.1~10 kpa,更优选为0.2~1 kpa。
[0018]
作为优选,步骤(3)中,所述有机溶剂为无水乙醇、乙酸乙酯、二氯甲烷、异丙醇、甲苯或其组合。
[0019]
与现有技术对比,本发明的有益效果是:(1)通过向聚乳酸废弃物中加入脂肪醇,有利于加速断链反应得到聚乳酸低聚物,
减少副反应的发生,降低断链反应温度,聚乳酸低聚物分子量分布更为均一;另外,脂肪醇在裂解反应可起到协同催化的作用,进一步降低裂解反应温度,缩短反应时间,从而大幅降低生产能耗。
[0020]
(2)脂肪醇的加入提高了丙交酯回收率(>95%),且得到的粗丙交酯中内消旋、乳酸、乳酸二聚体含量均较低,进一步提纯得到高化学纯度(>99.9%)、高光学纯度(>99.9%)的高纯度丙交酯,可直接二次利用。
[0021]
(3)与传统的聚乳酸回收得到乳酸酯类化合物相比,无需使用大量溶剂或固体碱催化剂,仅采用少量脂肪醇作为催化剂和酯交换剂,由聚乳酸废弃物直接获得丙交酯单体,实现单体-聚合物-单体的循环,使自然资源得到充分利用,有助于减少环境污染。
[0022]
(4)本发明是聚乳酸材料化学回收方法的一种,方法简单、快速,减少工业步骤,加强生产效率,降低工业成本,适用于各种聚乳酸、聚乳酸共聚物及其共混物废弃物的回收利用,符合可持续发展原则。
具体实施方式
[0023]
以下,结合实施列对本发明优选的方式进行具体说明,但不以任何方式限制本发明。
[0024]
实施例1(1)脂肪醇存在下聚乳酸废弃物的断链反应:向反应器中加入聚乳酸废弃物与乙二醇(2.0 wt%),在加热搅拌条件下进行聚乳酸废弃物的断链反应,制备聚乳酸低聚物;其中断链反应温度为200℃,反应时间为120min,制得的低聚物分子量为2592。
[0025]
(2)聚乳酸低聚物的裂解反应:向步骤(1)制备的聚乳酸低聚物中加入裂解催化剂sn(oct)2(0.3 wt%),经充分混合后进行减压蒸馏操作,乳酸低聚物不断裂解,收集得到丙交酯。其中裂解温度为195℃,真空度为0.5 kpa。
[0026]
(3)将所述粗丙交酯溶解于乙酸乙酯中,冷却结晶,抽滤得到丙交酯;重复上述操作多次,真空干燥得到高纯丙交酯。
[0027]
实施例2(1)脂肪醇存在下聚乳酸废弃物的断链反应:向反应器中加入聚乳酸废弃物与丙二醇(2.0 wt%),在加热搅拌条件下进行聚乳酸废弃物的断链反应,制备聚乳酸低聚物;其中断链反应温度为180℃,反应时间为90min,制得的低聚物分子量为3520。
[0028]
(2)聚乳酸低聚物的裂解反应:向步骤(1)制备的聚乳酸低聚物中加入裂解催化剂sn(oct)2(0.3 wt%),经充分混合后进行减压蒸馏操作,乳酸低聚物不断裂解,收集得到丙交酯。其中裂解温度为185℃,真空度为0.5 kpa。
[0029]
(3)将所述粗丙交酯溶解于乙酸乙酯中,冷却结晶,抽滤得到丙交酯;重复上述操作多次,真空干燥得到高纯丙交酯。
[0030]
实施例3
(1)脂肪醇存在下聚乳酸废弃物的断链反应:向反应器中加入聚乳酸废弃物与丁二醇(2.0 wt%),在加热搅拌条件下进行聚乳酸废弃物的断链反应,制备聚乳酸低聚物;其中断链反应温度为200℃,反应时间为60min,制得的低聚物分子量为3340。
[0031]
(2)聚乳酸低聚物的裂解反应:向步骤(1)制备的聚乳酸低聚物中加入裂解催化剂sn(oct)2(0.3 wt%),经充分混合后进行减压蒸馏操作,乳酸低聚物不断裂解,收集得到丙交酯。其中裂解温度为195℃,真空度为0.5 kpa。
[0032]
(3)将所述粗丙交酯溶解于甲苯中,冷却结晶,抽滤得到丙交酯;重复上述操作多次,真空干燥得到高纯丙交酯。
[0033]
实施例4(1)脂肪醇存在下聚乳酸废弃物的断链反应:向反应器中加入聚乳酸废弃物与戊二醇(4.0 wt%),在加热搅拌条件下进行聚乳酸废弃物的断链反应,制备聚乳酸低聚物;其中断链反应温度为190℃,反应时间为30min,制得的低聚物分子量为1411。
[0034]
(2)聚乳酸低聚物的裂解反应:向步骤(1)制备的聚乳酸低聚物中加入裂解催化剂sncl2(0.3 wt%),经充分混合后进行减压蒸馏操作,乳酸低聚物不断裂解,收集得到丙交酯。其中裂解温度为185℃,真空度为0.5 kpa。
[0035]
(3)将所述粗丙交酯溶解于二氯甲烷中,冷却结晶,抽滤得到丙交酯;重复上述操作多次,真空干燥得到高纯丙交酯。
[0036]
实施例5(1)脂肪醇存在下聚乳酸废弃物的断链反应:向反应器中加入聚乳酸废弃物与己二醇(1.0 wt%),在加热搅拌条件下进行聚乳酸废弃物的断链反应,制备聚乳酸低聚物;其中断链反应温度为200℃,反应时间为120min,制得的低聚物分子量为4053。
[0037]
(2)聚乳酸低聚物的裂解反应:向步骤(1)制备的聚乳酸低聚物中加入裂解催化剂sn(oct)2(0.1 wt%),经充分混合后进行减压蒸馏操作,乳酸低聚物不断裂解,收集得到丙交酯。其中裂解温度为195℃,真空度为0.5 kpa。
[0038]
(3)将所述粗丙交酯溶解于无水乙醇中,冷却结晶,抽滤得到丙交酯;重复上述操作多次,真空干燥得到高纯丙交酯。
[0039]
实施例6(1)脂肪醇存在下聚乳酸废弃物的断链反应:向反应器中加入聚乳酸废弃物与己二醇(10.0 wt%),在加热搅拌条件下进行聚乳酸废弃物的断链反应,制备聚乳酸低聚物;其中断链反应温度为200℃,反应时间为60min,制得的低聚物分子量为760。
[0040]
(2)聚乳酸低聚物的裂解反应:向步骤(1)制备的聚乳酸低聚物中加入裂解催化剂zno(0.3 wt%),经充分混合后
进行减压蒸馏操作,乳酸低聚物不断裂解,收集得到丙交酯。其中裂解温度为195℃,真空度为0.5 kpa。
[0041]
(3)将所述粗丙交酯溶解于异丙醚中,冷却结晶,抽滤得到丙交酯;重复上述操作多次,真空干燥得到高纯丙交酯。
[0042]
对比例1(1)聚乳酸废弃物的断链反应:向反应器中加入聚乳酸废弃物,在加热搅拌条件下进行聚乳酸废弃物的断链反应,制备聚乳酸低聚物;其中断链反应温度为200℃,反应时间为60min,制得的低聚物分子量为9541。
[0043]
(2)聚乳酸低聚物的裂解反应:向步骤(1)制备的聚乳酸低聚物中加入裂解催化剂sn(oct)2(0.3 wt%),经充分混合后进行减压蒸馏操作,乳酸低聚物不断裂解,收集得到丙交酯。其中裂解温度为200℃,真空度为0.5 kpa。
[0044]
(3)将所述粗丙交酯溶解于无水乙醇中,冷却结晶,抽滤得到丙交酯;重复上述操作多次,真空干燥得到高纯丙交酯。
[0045]
对比例2(1)聚乳酸废弃物的断链反应:向反应器中加入聚乳酸废弃物与丁二醇(15.0 wt%),在加热搅拌条件下进行聚乳酸废弃物的断链反应,制备聚乳酸低聚物;其中断链反应温度为200℃,反应时间为60min,制得的低聚物分子量为342。
[0046]
(2)聚乳酸低聚物的裂解反应:向步骤(1)制备的聚乳酸低聚物中加入裂解催化剂sn(oct)2(0.3 wt%),经充分混合后进行减压蒸馏操作,乳酸低聚物不断裂解,收集得到丙交酯。其中裂解温度为200℃,真空度为0.5 kpa。
[0047]
(3)将所述粗丙交酯溶解于乙酸乙酯中,冷却结晶,抽滤得到丙交酯;重复上述操作多次,真空干燥得到高纯丙交酯。
[0048]
分别记录实施例1~6以及对比例1~2的反应条件与制得的丙交酯性能,得出结果如表1和2所述:表1 l-丙交酯的制备条件
ꢀ
表2 粗l-丙交酯的表征结果如上述表格所示,本发明实施例1~6中使用脂肪醇存在下的断链反应后裂解制得的粗丙交酯回收率较高,粗丙交酯中内消旋、乳酸、乳酸二聚体含量低。其中,实施例3中粗丙交酯回收率最高,达到96.5%,内消旋丙交酯含量为0.27%,乳酸含量0.19%,乳酸二聚体含量1.14%,与相同条件下无脂肪醇存在时的回收率高。由对比例1与实施例3的数据比较,控制断链反应时间60min,通过向聚乳酸废弃物中加入脂肪醇后,脂肪醇的存在可有效抑制副反应的发生,相同条件下聚乳酸低聚物的分子量显著降低,使最终丙交酯回收率提高,且粗丙交酯中l-丙交酯含量增加。脂肪醇在裂解反应过程中可起到协同催化的作用,进一步缩短裂解反应时间和裂解温度,相较于对比例1,解聚反应时间由210min减少到150min,从而大幅降低生产能耗。对比例2中使用15%的丁二醇,丙交酯产率与纯度远远低于其他实施例,主要是由于过量的醇存在易发生副反应,影响粗丙交酯产率与化学纯度。
[0049]
本发明中所用原料、设备,若无特别说明,均为本领域的常用原料、设备;本发明中所用方法,若无特别说明,均为本领域的常规方法。
[0050]
以上所述,仅是本发明的较佳实施例,并非对本发明作任何限制,凡是根据本发明技术实质对以上实施例所作的任何简单修改、变更以及等效变换,均仍属于本发明技术方案的保护范围。