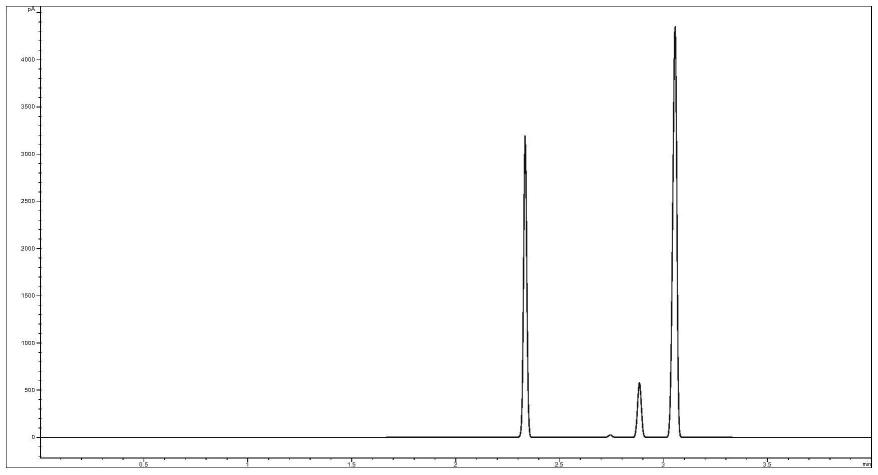
1.本发明涉及半导体技术领域,特别涉及一种提高硅粉利用率制备正硅酸乙酯的方法。
背景技术:2.随着半导体工艺的不断发展,用作栅氧电介质、器件隔离和金属导电层间绝缘介质的二氧化硅氧化膜的要求在不断提升。高纯正硅酸乙酯作为化学气相沉积法制备二氧化硅氧化膜的主要原料,因其优良的工艺使用稳定性、出色的沉积速率和使用安全性,正在被广泛使用。
3.目前正硅酸乙酯的制备的方法有很多,但主流的工业化路线只有两条,即四氯化硅间接法和硅粉直接法。我国大多数厂家均采用四氯化硅间接法,即用乙醇和四氯化硅反应制备正硅酸乙酯的方法,该法在合成正硅酸乙酯的过程中每生成1摩尔的正硅酸乙酯就会带来4摩尔的盐酸(hcl),大量盐酸存在的正硅酸乙酯生产体系,不仅会产生不完全反应的氯代正硅酸酯,使得成品正硅酸乙酯中携带大量的氯离子,限制其在半导体工艺中的应用。还会使得体系对水分很敏感,因为盐酸极易促使正硅酸乙酯发生聚合反应,使得成品正硅酸乙酯中聚合物含量的增加。此外,盐酸还会腐蚀设备和污染环境、损害健康。其中公开号为cn109748931a公布了一种通过四氯化硅间接法改良制备高纯正硅酸乙酯的方法,介绍了通过吸附和分段精馏分别对正硅酸乙酯进行提纯,并实现对副产盐酸的提纯。但此法设备投入大,对粗品正硅酸乙酯和盐酸分离工艺要求高,对不完全反应的氯代正硅酸乙酯管控困难,同时吸附树脂的能力不利于大规模连续化生产。
4.而通过硅粉和乙醇合成正硅酸乙酯,即硅粉直接法。过程中无有害气体排放,且无盐酸的催化大大减少了副反应的产生,正硅酸乙酯中的氯离子含量也极低。但是硅粉直接法存在硅粉利用率偏低的问题,因为在反应的中后期由于硅粉中杂质的累积和无水乙醇和硅粉本身反应活性限制导致反应无法进行。虽然可以通过不停引入碱金属盐催化反应进行,但是这样不仅会导致催化剂用量增加,还会加剧釜残的产生量,无形中增加成本。公开号为cn108640943a公布了一种硅粉直接法生产正硅酸乙酯的方法,分别介绍了合成催化剂和一锅法反应,但催化剂合成过程繁琐,实现困难。一锅法很难实现大规模的生产。
技术实现要素:5.本发明的目的是提供一种提高硅粉利用率制备正硅酸乙酯的方法,解决上述现有技术问题中的一个或者多个。
6.本发明提供的一种提高硅粉利用率制备正硅酸乙酯的方法,包括以下步骤:
7.将a组分、无水乙醇、甲醇与b组分混合,制得正硅酸乙酯。
8.具体地,a组分至少包括硅粉一种组分,b组分至少包括一种催化剂。
9.在某些实施方案中,甲醇和无水乙醇中水分小于500ppm。
10.所述a组分由硅粉和第一溶液混合,制成硅粉浆。
11.具体地,所述第一溶液选自正硅酸乙酯,所述正硅酸乙酯添加量与所述硅粉质量比为0.3~1:1。
12.其中:硅粉为市售工业级硅微粉,该工业级硅微粉中硅含量>99%,平均粒径为45μm~200μm;正硅酸乙酯为硅粉直接法合成的正硅酸乙酯,因其较其他正硅酸乙酯具有更低的氯离子含量和杂质,避免杂质引入影响效果的判定。
13.所述a组分经过超声预处理10min~20min,维持搅拌30min~60min。工业级硅微粉在生产和储存中,其表面会吸附杂质甚至被氧化而形成惰性保护层,这些惰性保护层会阻碍与乙醇的酯化反应,导致硅粉的利用率下降。通过超声预处理的方式,可以有效的剥离惰性保护层,实现工业级硅微粉表面光洁,使得硅单质可以直接与乙醇反应,提高硅粉的利用率。必要的充分搅拌可以进一步有效的促进工业级硅微粉在第一溶液中均匀分散,减少因硅粉颗粒团聚导致反应的活性降低。
14.所述b组分由催化剂和第一溶液混合制得;所述催化剂包括第一催化剂和第二催化剂,所述第一催化剂选自有机碱,所述有机碱选自甲醇盐、乙醇盐、叔丁醇盐和乙醇胺、二乙醇胺或三乙醇胺;所述第二催化剂选自甲基苯基硅油、十二烷基苯、联苯或二甘醇;所述第一溶液选自工业级正硅酸乙酯。
15.具体地,正硅酸乙酯为为硅粉直接法合成的正硅酸乙酯,优选的正硅酸乙酯中乙醇含量<5%。
16.所述第一催化剂的加入量占硅粉质量的1%~20%,所述第二催化剂的加入量占硅粉质量的1%~2%。
17.在某些实施方案中,包括以下步骤:
18.s1、将a组分、无水乙醇和甲醇以连续滴加方式加入b组分中进行酯化反应,生成物通过气液分离,得到(ch3o)nsi(oc2h5)
4-n
(粗品硅酸酯)。
19.以及
20.s2、分离提纯,得到si(oc2h5)4(成品正硅酸乙酯)。
21.具体地,气液分离包括:首先,气液混合物通过初级冷凝器,控制温度10℃-20℃;其次通过低温冷凝器,控制温度-10℃~-5℃;分离出氢气,得到粗品硅酸酯。
22.[步骤s1]
[0023]
a1、预先将a组分质量的1%~10%加入至b组分中活化,活化时间10-20min。硅粉与无水乙醇的反应需要较高的温度,采用部分硅粉在所述b组分中的沉积,可以有效的发挥b组分中催化剂的效能,使得开始阶段反应容易被激活。较传统一锅法而言,初始反应硅粉的量远低于一锅法硅粉量,可以有效控制反应开始阶段的活性,避免剧烈酯化反应产生的高温高压。
[0024]
a2、控制反应温度130~150℃,同时滴加a组分和第一无水乙醇,控制所述第一无水乙醇摩尔量与所述a组分中硅粉摩尔量之比为3~4。硅粉的过量可以确保无水乙醇及时转化为正硅酸乙酯,避免过量无水乙醇未及时反应导致粗品正硅酸乙酯中乙醇含量偏高。少量硅粉在b组分的缓慢累积,可以增加反应体系温度平稳的能力,减少因溶剂蒸出带来的温度波动。同时,累积的硅粉在体系内的反应热可以维持酯化反应的持续进行,不需要额外辅助加热。
[0025]
a3、a组分滴加结束后,控制反应温度为150~160℃,同时滴加第二无水乙醇和甲
醇,控制所述第二无水乙醇摩尔量与所述甲醇摩尔量之比为1~9:1。
[0026]
具体地,硅粉浆加完,b组分中会留有未完全反应的硅粉、与乙醇反应活性差的硅粉和杂质富集导致活性下降的硅粉,这些都是导致硅粉利用率不足的原因。与乙醇相比,甲醇与硅粉反应需要的反应温度更低,甲醇更容易与硅粉发生酯化反应,此时通过引入甲醇参与反应,残余硅粉可以不需要增加额外催化剂,即可与甲醇反应转化为含甲氧基硅酸酯。并且随着b组分中无水乙醇和甲醇的浓度的增加,体系中的杂质得已稀释,也可以进一步反应残余的硅粉,大大的提高硅粉的利用率。
[0027]
在某些实施方案中,滴加所述无水乙醇和甲醇总量和滴加所述a组分中硅粉摩尔量之比为5~7。
[0028]
[步骤s2]
[0029]
将所述粗品正硅酸乙酯通过酯交换和蒸馏,除去反应中的溶剂和含甲氧基硅酸酯,得到成品正硅酸乙酯。
[0030]
具体地:
[0031]
b1、在粗品正硅酸乙酯中加入第一催化剂,第一催化剂加入量占粗品正硅酸乙酯质量的0.3%~1%。所述第一催化剂优选甲醇钠、甲醇钾、乙醇钠或乙醇钾中一种。
[0032]
b2、控制蒸馏釜温为120℃~170℃,连续向釜中添加第三无水乙醇,蒸馏取出轻组分。在蒸馏中,含甲氧基硅酸酯与无水乙醇发生酯交换反应,含甲氧基硅酸酯转换为正硅酸乙酯和甲醇。酯交换反应虽然为可逆反应,但是因低沸点的甲醇在蒸馏体系会被优先蒸出,从而使得粗品正硅酸乙酯容易得到提纯。
[0033]
其中,所述轻组分主要为甲醇和无水乙醇及极少量的硅酸酯的混合物,该混合物可以作为原料进入所述步骤s1中重新参与酯化反应,从而实现甲醇和无水乙醇的回收再利用,使得在粗品正硅酸乙酯的分离提纯中几乎无额外副产物。
[0034]
b3、控制蒸馏釜温为170℃~180℃,收集塔顶168℃~169℃馏份,得到纯品正硅酸乙酯。
[0035]
有益效果:本发明提供一种提高硅粉利用率制备正硅酸乙酯的方法能够实现更高的硅粉转化率,同时反应可控,适合连续化大规模生产。具体为:
[0036]
(1)本发明通过酯化反应将所述a组分和无水乙醇和甲醇通过滴加方式加入所述b组分中,较其他硅粉直接法制备正硅酸乙酯相比,反应可控,工艺安全性更高,连续的滴加方式更利于大规模连续化生产;
[0037]
(2)本发明对硅粉浆进行超声预处理的方式,可以有效的去除硅粉表面的惰性保护层,提高硅粉的利用率;
[0038]
(3)本发明采用甲醇参与硅粉的酯化反应,在不添加额外催化剂的同时,大大促进残余硅粉的反应,进一步提高硅粉利用率;
[0039]
(4)本发明通过分离提纯的同时进行酯交换反应,可以实现对甲醇的回收再利用。
附图说明
[0040]
图1是实施案例1粗品硅酸酯gc图谱;
[0041]
图2是实施案例2粗品硅酸酯gc图谱;
[0042]
图3是实施案例3粗品硅酸酯gc图谱;
[0043]
图4是实施案例4粗品硅酸酯gc图谱;
[0044]
图5是实施案例1成品正硅酸乙酯gc图谱;
[0045]
图6是实施案例4成品正硅酸乙酯gc图谱。
具体实施方式
[0046]
下面通过实施方式对本发明进行进一步详细的说明。
[0047]
硅粉转化率估算方法:称取5g合成反应釜釜残和20g无水乙醇混合,混合物用定量滤纸过滤,滤除残留的醇和催化剂,不溶物在150℃烘箱中干燥1h后,取出放入干燥器内冷却后称重。按以下公式计算硅粉转化率:
[0048][0049]
m1‑‑
称取釜残重量,g;
[0050]
m2—过滤烘干后釜残重量,g;
[0051]
m3—合成反应釜釜残总重量,g;
[0052]
m4—投料硅粉总重量,g。
[0053]
实施案例1:
[0054]
s1、将800g硅粉(硅含量99.2%,50μm)和400g工业级正硅酸乙酯混合搅拌均匀制得硅粉浆,将硅粉浆经过超声预处理15min,充分搅拌30min后,得到a组分;在配有加热、搅拌和滴加口以及出料口的合成反应釜中加入50g甲醇钠、10g甲基苯基硅油、200g工业级正硅酸乙酯,搅拌均匀,得到b组分;将50ga组分加入b组分中活化10min后,升温并控制釜温135℃,分别以15g/min滴加a组分、49.3g/min滴加第一无水乙醇,直至a组分滴加结束;a组分滴加结束后,控制釜温150℃,分别以3.5g/min滴加甲醇和45.7g/min滴加第二无水乙醇,反应残余硅粉,51.7min后停止反应。生成物通过低温冷却,分离出氢气,得到粗品硅酸酯,取合成反应釜釜残进行硅粉转化率测试。
[0055]
s2、取以上s1所获得的粗品硅酸酯7000g转移至配有精馏塔的蒸馏反应釜中,分别加入35g甲醇钠和289g的第三无水乙醇进行蒸馏。控制釜温130℃以上,取出轻组分甲醇等,控制釜温175℃左右,收集塔顶168℃~169℃馏份,得到成品正硅酸乙酯4392g。
[0056]
经gc检测成品正硅酸乙酯含量99.3%,氯离子含量2.6ppb。
[0057]
实施案例2:
[0058]
s1、将800g硅粉(硅含量99.2%,50μm)和400g工业级正硅酸乙酯混合搅拌均匀制得硅粉浆,将硅粉浆经过超声预处理15min,充分搅拌30min后,得到a组分;在配有加热、搅拌和滴加口以及出料口的合成反应釜中加入50g乙醇钠、10g二甘醇、200g工业级正硅酸乙酯,搅拌均匀,得到b组分;将50ga组分加入b组分中活化10min后,升温并控制釜温135℃,分别以15g/min滴加a组分、49.3g/min滴加第一无水乙醇,直至a组分滴加结束;a组分滴加结束后,控制釜温150℃,分别以7.3g/min滴加甲醇和42g/min滴加第二无水乙醇,反应残余硅粉,50min后停止反应。生成物通过低温冷却,分离出氢气,得到粗品硅酸酯,取合成反应釜釜残进行硅粉转化率测试。
[0059]
s2、取以上s1所获得的粗品硅酸酯7000g转移至配有精馏塔的蒸馏反应釜中,分别
加入35g甲醇钠和578g第三无水乙醇进行蒸馏。控制釜温130℃以上,取出轻组分甲醇等,控制釜温175℃左右,收集塔顶168℃~169℃馏份,得到成品正硅酸乙酯4627g。
[0060]
经gc检测成品正硅酸乙酯含量99.2%,氯离子含量3.0ppb。
[0061]
实施案例3:
[0062]
s1、将800g硅粉(硅含量99.2%,50μm)和400g工业级正硅酸乙酯混合搅拌均匀制得硅粉浆,将硅粉浆经过超声预处理15min,充分搅拌30min后,得到a组分;在配有加热、搅拌和滴加口以及出料口的合成反应釜中加入50g叔丁醇钾、10g十二烷基苯、200g工业级正硅酸乙酯,搅拌均匀,得到b组分;将50ga组分加入b组分中活化10min后,升温并控制釜温135℃,分别以15g/min滴加a组分、49.3g/min滴加第一无水乙醇,直至a组分滴加结束;a组分滴加结束后,控制釜温150℃,分别以11.3g/min滴加甲醇和38g/min滴加第二无水乙醇,反应残余硅粉,48.4min后停止反应。生成物通过低温冷却,分离出氢气,得到粗品硅酸酯,取合成反应釜釜残进行硅粉转化率测试。
[0063]
s2、取以上s1所获得的粗品硅酸酯7000g转移至配有精馏塔的蒸馏反应釜中,分别加入35g甲醇钠和867.1g的第三无水乙醇进行蒸馏。控制釜温130℃以上,取出轻组分甲醇等,控制釜温175℃左右,收集塔顶168℃~169℃馏份,得到成品正硅酸乙酯4908g。
[0064]
经gc检测成品正硅酸乙酯含量99.2%,氯离子含量2.5ppb。
[0065]
实施案例4:
[0066]
s1、将800g硅粉(硅含量99.2%,50μm)和400g工业级正硅酸乙酯混合搅拌均匀制得硅粉浆,将硅粉浆经过超声预处理15min,充分搅拌30min后,得到a组分;在配有加热、搅拌和滴加口以及出料口的合成反应釜中加入50g三乙醇胺、10g联苯、200g工业级正硅酸乙酯,搅拌均匀,得到b组分;将50ga组分加入b组分中活化10min后,升温并控制釜温135℃,分别以15g/min滴加a组分、49.3g/min滴加第一无水乙醇,直至a组分滴加结束;a组分滴加结束后,控制釜温150℃,分别以15.6g/min滴加甲醇和33.7g/min滴加第二无水乙醇,反应残余硅粉,46.8min后停止反应。生成物通过低温冷却,分离出氢气,得到粗品硅酸酯,取合成反应釜釜残进行硅粉转化率测试。
[0067]
s2、取以上s1所获得的粗品硅酸酯7000g转移至配有精馏塔的蒸馏反应釜中,分别加入35g甲醇钠和1156.1g的第三无水乙醇进行蒸馏。控制釜温130℃以上,取出轻组分甲醇等,控制釜温175℃左右,收集塔顶168℃~169℃馏份,得到成品正硅酸乙酯5031g。
[0068]
经gc检测成品正硅酸乙酯含量99.1%,氯离子含量2.7ppb。
[0069]
实施案例5:
[0070]
s1、将800g硅粉(硅含量99.2%,50μm)和400g工业级正硅酸乙酯混合搅拌均匀制得硅粉浆(硅粉浆不进行超声预处理的方式),得到a组分;在配有加热、搅拌和滴加口以及出料口的合成反应釜中加入50g三乙醇胺、10g联苯、200g工业级正硅酸乙酯,搅拌均匀,得到b组分;将50ga组分加入b组分中活化10min后,升温并控制釜温135℃,分别以15g/min滴加a组分、49.3g/min滴加第一无水乙醇,直至a组分滴加结束;a组分滴加结束后,控制釜温150℃,分别以15.6g/min滴加甲醇和33.7g/min滴加第二无水乙醇,反应残余硅粉,46.8min后停止反应。生成物通过低温冷却,分离出氢气,得到粗品硅酸酯,取合成反应釜釜残进行硅粉转化率测试。
[0071]
s2、取以上s1所获得的粗品硅酸酯7000g转移至配有精馏塔的蒸馏反应釜中,分别
加入35g甲醇钠和289g的第三无水乙醇进行蒸馏。控制釜温130℃以上,取出轻组分甲醇等,控制釜温175℃左右,收集塔顶168℃~169℃馏份,得到成品正硅酸乙酯4813g。
[0072]
经gc检测成品正硅酸乙酯含量99.3%,氯离子含量3.0ppb。
[0073]
对比案例1:
[0074]
模拟一锅法:
[0075]
s1、将800g硅粉(硅含量99.2%,50μm)、600g工业级正硅酸乙酯和50g甲醇钠、10g甲基苯基硅油混合搅拌均匀制得硅粉浆;在配有加热、搅拌和滴加口以及出料口的合成反应釜中加入以上制得硅粉浆;升温并控制釜温140℃,以49.3g/min滴加无水乙醇,129.9min后停止反应(无水乙醇用量等同于实施案例1步骤s1中的用量)。生成物通过低温冷却,分离出氢气,得到粗品硅酸酯,取合成反应釜釜残进行硅粉转化率测试。
[0076]
s2、取以上s1所获得的粗品硅酸酯7000g转移至配有精馏塔的蒸馏反应釜中进行蒸馏。控制釜温130℃以上,取出轻组分乙醇等,控制釜温175℃左右,收集塔顶168℃~169℃馏份,得到成品正硅酸乙酯3520g。
[0077]
经gc检测成品正硅酸乙酯含量99.2%,氯离子含量2.5ppb。
[0078]
对比案例2:
[0079]
s1、将800g硅粉(硅含量99.2%,50μm)和400g工业级正硅酸乙酯混合搅拌均匀制得硅粉浆,得到a组分;在配有加热、搅拌和滴加口以及出料口的合成反应釜中加入50g甲醇钠、10g甲基苯基硅油、200g工业级正硅酸乙酯,搅拌均匀,得到b组分;将50ga组分加入b组分中活化10min后,升温并控制釜温135℃,分别以15g/min滴加a组分、49.3g/min滴加第一无水乙醇,直至a组分滴加结束;a组分滴加结束后,控制釜温150℃,以49.3g/min滴加第二无水乙醇,反应残余硅粉,53.3min后停止反应。生成物通过低温冷却,分离出氢气,得到粗品硅酸酯,取合成反应釜釜残进行硅粉转化率测试。
[0080]
s2、取以上s1所获得的粗品硅酸酯7000g转移至配有精馏塔的蒸馏反应釜中进行蒸馏。控制釜温130℃以上,取出轻组分乙醇等,控制釜温175℃左右,收集塔顶168℃~169℃馏份,得到成品正硅酸乙酯4020g。
[0081]
经gc检测成品正硅酸乙酯含量99.3%,氯离子含量2.3ppb。
[0082]
[表1]实施案例1-5和对比案例1-2主要参数和硅粉转化率统计表
[0083]
名称实施案例1实施案例2实施案例3实施案例4实施案例5对比案例1对比案例2硅粉(g)800800800800800800800第一催化剂(g)50505050505050第二催化剂(g)10101010101010a组分滴加速度(g/min)1515151515015a组分是否超声是是是是否否否第一无水乙醇滴加速度(g/min)49.349.349.349.349.3049.3甲醇滴加速度(g/min)3.57.311.315.615.600第二无水乙醇滴加速度(g/min)45.7423833.733.749.349.3滴加时间(min)51.75048.446.846.8129.953.3硅粉转化率(%)80.585.892.29591.355.368.1
[0084]
表1中实施案例1-4和对比案例2结果表明:在同等条件下,随着甲醇用量的增加,可以有效的反应釜内残余硅粉,大幅提升硅粉的利用率,硅粉利用率最高可达95%。
[0085]
表1中实施案例4和实施案例5结果表明:在物料完全相同的条件下,经过超声预处
理方式处理后的硅粉浆,其硅粉利用率高于未采用超声预处理的硅粉浆。说明采用超声预处理的方式能够剥离硅粉惰性保护层,提高硅粉活性,从而提升硅粉的利用率。
[0086]
表1中对比案例1和对比案例2结果表明:对比案例1一锅法由于受限于催化剂的用量,其硅粉的利用率最低;而对比案例2通过连续滴加的方式,有利于其硅粉利用率的提升,但是因其未采用超声预处理的方式和无甲醇的参与,整体的硅粉利用率也是偏低的。进一步从反面证明了,通过超声预处理的方式和甲醇参与反应的方式可以有效的提高硅粉的利用率。
[0087]
综上所述:本发明提供一种提高硅粉利用率制备正硅酸乙酯的方法能够实现更高的硅粉转化率,同时反应可控,适合连续化大规模生产。具体为:一方面,通过对硅粉进行超声预处理的方式,可以提高硅粉的反应活性,提高利用率;另一方面,通过在无水乙醇中引入更易与硅粉反应的甲醇,甲醇可以作为辅助催化促进中后期反应的进行,从而减少碱金属盐的用量,进一步提高硅粉的转化率。此外,用无水乙醇参与提纯,不仅可以提高正硅酸乙酯的含量,还可以实现对甲醇的回收再利用,避免大量额外杂质的产生。同时,采取连续滴加的方式,易于对反应的控制,具有更好的工艺安全性,有利于大规模工业化生产。
[0088]
以上表述仅为本发明的优选方式,应当指出,对本领域的普通技术人员来说,在不脱离本发明创造构思的前提下,还可以做出若干变形和改进,这些也应视为发明的保护范围之内。