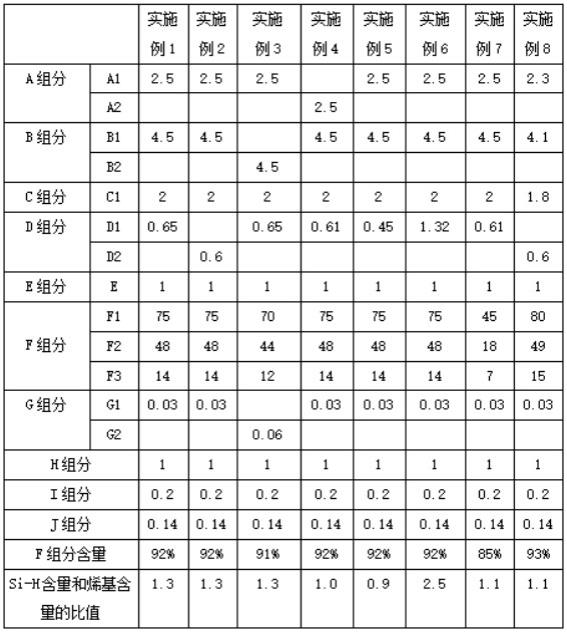
1.本技术涉及半导体器件封装技术领域,具体涉及一种含硅的热界面材料、其制备方法及芯片封装结构。
背景技术:2.在本领域,诸如大集成电路或集成电路芯片等电子器件被广泛认为是在使用期间产生热量导致与之相关的性能下降,各种散热技术已被用作解决这一问题的手段。例如,将冷却构件设置在发热构件附近,且冷却构件和发热构件密切接触,从而将热量传递出去。在这种情况下,如果发热构件和冷却构件间存在间隙,则会插入导热性低的空气,降低传热效率。热界面材料是涂敷于发热构件和冷却构件间,用来填充发热构件和冷却构件间的空气间隙,以此来提高传热效率。
3.对于热界面材料,为提高其导热性,往往需要加入大量的导热填料,这又导致热界面材料在热固化后的断裂伸长率降低。断裂伸长率的降低使热界面材料失去灵活性,当热界面材料填充发热构件和冷却构件间的间隙时,热界面材料难以完全贴合,则会在发热构件和/或冷却构件与热界面材料间存在新的空气间隙,影响传热效率。
技术实现要素:4.本技术的目的是提供一种含硅的热界面材料、其制备方法及芯片封装结构,该含硅的热界面材料可显著改善断裂伸长率,当涂敷与发热构件和冷却构件间时可确保完全贴合。
5.为达到上述目的,本技术实施例一方面提供一种含硅的热界面材料,其原材料包括烯基硅油、含氢硅油、导热填料、催化剂、润湿剂和附着力促进剂;所述烯基硅油由20~50wt.%的双端烯基硅油、30~76wt.%的侧烯基硅油、4~25wt.%的端侧烯基硅油复配,且其中双端烯基硅油和侧烯基硅油共计75~96wt.%;以及所述含氢硅油由10~60wt.%的侧氢硅油和40~90wt.%的端氢硅油复配;所述双端烯基硅油选自由含2个乙烯基的基团对硅氧烷链的两端封端得到;所述侧烯基硅油选自由含乙烯基的烃基连接到硅氧烷链侧端得到;所述端侧烯基硅油选自由含乙烯基的烃基连接到硅氧烷链侧端以及至少一终端得到。
6.在一些具体实施方式中,含2个乙烯基的基团选自三羟甲基亚丙基三丙烯酸酯基或三羟甲基亚丙基三烯丙醚基。
7.在一些具体实施方式中,含乙烯基的烃基选自乙烯基。
8.在一些具体实施方式中,含氢硅油由31~57wt.%的侧氢硅油和43~69wt.%的端氢硅油复配。
9.在一些具体实施方式中,含氢硅油中si-h键基团的摩尔量是所述烯基硅油中烯基基团的0.9~2.5倍,优选为0.9~1.3倍,进一步优选为0.9~1.1倍。
10.在一些具体实施方式中,催化剂选自铂基金属催化剂或胶囊型催化剂;当催化剂选自铂基金属催化剂,所述热界面材料还包括抑制剂。
11.本技术实施例另一方面提供上述热界面材料的制备方法:将烯基硅油、导热填料和润湿剂按配比混合,加热到110~160℃温度下搅拌0.5~5h;冷却至室温,再加入含氢硅油、催化剂和附着力促进剂,于室温搅拌0.1~4h;经真空脱泡得热界面材料。
12.本技术实施例再一方面提供一种芯片封装结构:包括芯片,用于给芯片散热的散热构件,以及涂敷于芯片与散热构件间的热界面层,所述热界面层由上述热界面材料经硫化交联而成。
13.和现有技术相比,本技术具有如下特点和技术效果:本技术中含硅的热界面材料的断裂伸长率得到显著改善,具有优异的断裂伸长率、拉伸强度、si附着力、触变性以及可施工时间长等优势,当将其用于在芯片的发热构件和冷却构件间形成热界面层,可确保完全贴合,从而改善导热效率。
具体实施方式
14.为了使本技术的目的、技术方案及有益效果更加清楚明白,以下结合实施例,对本技术进行进一步详细说明。
15.本技术实施例提供的一种含硅的热界面材料,其原料包括烯基硅油、含氢硅油、导热填料、催化剂、润湿剂和附着力促进剂,其中,烯基硅油由双端烯基硅油、侧烯基硅油、端侧烯基硅油复配,含氢硅油由侧氢硅油和端氢硅油复配。
16.一、烯基硅油粘度为0.1~60pa
·
s的各种烯基硅油的复配混合物可使材料体系具有优良的触变性和工艺粘度,并能使硫化产物具有优良的物理性能。分子量较小的组分可降低材料体系的粘度,提高硫化产物的交联密度,使其具有较高的强度和硬度;而分子量大的组分可使硫化产物具有高弹性和较大的伸长率。
17.材料体系的弹性除与粘度有关外,还与烯基的含量以及烯基在硅氧烷链中的位置有关。本技术实施例中烯基硅油由双端烯基硅油(a)、侧烯基硅油(b)、端侧烯基硅油(c)复配。其中,双端烯基硅油是烯基对硅氧烷链的两终端进行封端,每个分子均含4个烯基;侧烯基硅油是烯基接到硅氧烷链侧端;端侧烯基硅油是烯基接到硅氧烷链的侧端和至少一终端。通过调整双端烯基硅油(a)、侧烯基硅油(b)、端侧烯基硅油(c)的配比,可调整固化产物的硬度和弹性。以双端烯基硅油(a)、侧烯基硅油(b)、端侧烯基硅油(c)总质量为100份算,双端烯基硅油(a)、侧烯基硅油(b)、端侧烯基硅油(c)的用量分别为20~50份、30~76份、4~25份,且其中双端烯基硅油(a)和侧烯基硅油(b)的用量合计75~96份,优选为28份、50份、22份。
18.(1)双端烯基硅油(a):双端烯基硅油(a)由含2个乙烯基的基团对硅氧烷链的两端进行封端得到,其结构式表示如下:
ꢀꢀꢀꢀꢀꢀꢀꢀꢀꢀꢀꢀꢀꢀꢀꢀꢀꢀꢀ
(ⅰ)结构式(ⅰ)中:ra分别独立地选自碳数1~20的烷基或芳香基,优选为甲基或苯基;
ra1分别独立地选自含2个乙烯基的基团,优选三羟甲基亚丙基三丙烯酸酯基或三羟甲基亚丙基三烯丙醚基;h为独立的整数,取值范围10~50000。
19.本技术实施例中,双端烯基硅油(a)的粘度优选为0.01~10pa
·
s。
20.三羟甲基亚丙基三丙烯酸酯基的结构式见式(ⅱ),其可由三羟甲基亚丙基三丙烯酸酯中的一乙烯基与氢硅键发生加成反应得到:
ꢀꢀꢀꢀꢀꢀꢀꢀꢀꢀꢀꢀꢀ
(ⅱ)三羟甲基亚丙基三烯丙醚基的结构式见式(ⅲ),其可由三羟甲基亚丙基三烯丙醚中的一乙烯基与氢硅键发生加成反应得到:
ꢀꢀꢀꢀꢀꢀꢀꢀꢀꢀꢀꢀꢀ
(ⅲ)本技术实施例中,三羟甲基亚丙基三丙烯酸酯基或三羟甲基亚丙基三烯丙醚基封端的聚硅氧烷采用如下方法合成:使三羟甲基丙烷三丙烯酸酯或季戊四醇三烯丙基醚与端氢硅油在卡斯特催化剂的催化作用下发生氢硅化反应,得到三羟甲基亚丙基三丙烯酸酯基或三羟甲基亚丙基三烯丙醚基封端的聚硅氧烷。
21.(2)侧烯基硅油(b):侧烯基硅油(b)由含乙烯基的基团连接到硅氧烷链侧端得到,其结构式表示如下:
ꢀꢀꢀꢀꢀꢀꢀꢀꢀꢀꢀꢀꢀꢀꢀ
(ⅳ)结构式(ⅳ)中:rb分别独立地选自碳数1~20的烷基或芳香基,优选为甲基或乙基;rb1独立地选自含乙烯基的烃基,优选乙烯基;i和j均为独立的整数,i的取值范围为3~100,j的取值范围为10~1000。侧烯基硅油(b)中,所有含乙烯基的基团均接于si-o-si链的
侧链。
22.本技术实施例中,侧烯基硅油的粘度优选为0.05~20pa
·
s,乙烯基含量优选为0.75~1.21%。
23.(3)端侧烯基硅油(c):端侧烯基硅油(c)由含乙烯基的烃基连接到硅氧烷链侧端以及至少一终端得到,其结构式表示如下:
ꢀꢀꢀꢀꢀꢀꢀꢀꢀꢀꢀꢀꢀꢀꢀ
(
ⅴ
)结构式(
ⅴ
)中:rc分别独立地选自碳数1~20的烷基或芳香基,优选甲基或乙基;rc1独立地选自烃基,且两个rc1中至少一个选自含碳碳双键的烃基,该烃基优选乙烯基;rc2独立地选自含碳碳双键的烃基,优选乙烯基;k和l为独立的整数,k的取值范围为0~100,l的取值范围为10~1000。
24.端侧烯基硅油(c)中,含碳碳双键的烃基连接于si-o-si链的侧链,同时也连接于si-o-si链的至少一个终端。
25.本技术实施例中,端侧烯基硅油的粘度优选为0.05~20pa
·
s,乙烯基含量优选为1.25%。
26.二、含氢硅油含氢硅油在加成型液体硅橡胶中用作交联剂,粘度为0.002~0.3pa
·
s,即低粘度的线型氢硅油。含氢硅油分子中直接与硅原子相连接的活性氢原子与烯基在高温下催化发生加成反应,使生胶硫化,形成交联结构固化成硅橡胶。
27.本技术实施例中,含氢硅油由侧氢硅油(d)和端氢硅油(e)复配,其中,侧氢硅油(d)是si-o-si链的侧链连接si-h键,也可以是si-o-si链的侧链和至少一个终端同时连接si-h键;端氢硅油是仅si-o-si链的两终端连接si-h键,即si-h键对si-o-si链的两端进行封端。侧氢硅油(d)硫化的硅橡胶具有较高交联度,而端氢硅油(e)硫化的硅橡胶交联度较低。将两者复配使用可调节硅橡胶的硬度和弹性。优选地,侧氢硅油(d)和端氢硅油(e)中si-h键活性基团的摩尔量是烯基硅油中烯基活性基团的0.9~2.5倍,优选为0.9~1.3倍,进一步优选为0.9~1.1倍。其中,端氢硅油加入较少则起不到柔软性作用,加入过多会导致硅橡胶拉伸强度降低。本技术实施例中,以侧氢硅油(d)和端氢硅油(e)总质量为100份算,侧氢硅油(d)和端氢硅油(e)的用量分别为10~60份、40~90份,优选为31~57份、43~69份,进一步优选为31~39份、61~69份。
28.侧氢硅油(d)的结构表示如下:
ꢀꢀꢀꢀꢀꢀꢀꢀꢀꢀꢀꢀꢀꢀꢀꢀ
(ⅵ)结构式(ⅵ)中,rd分别独立地选自饱和脂肪烃基,优选为甲基;rd1分别独立地选自饱和脂肪烃基或h,当rd1选自饱和脂肪烃基时,则优选为甲基;m和n分别独立地为3~100的整数。侧氢硅油中含氢量为0.1~1%,优选为0.1~0.2%,进一步优选为0.13~0.19%,粘度
为0.002~0.3pa
·
s。
29.侧氢硅油作为交联剂,其分子中与硅原子相连接的活性氢原子与烯基硅油中的乙烯基团在高温下催化发生加成反应,使生胶硫化,从而形成交联结构固化成硅橡胶,具有良好的机械强度。
30.端氢硅油(e)的化学式如下:
ꢀꢀꢀꢀꢀꢀꢀꢀꢀꢀꢀꢀꢀꢀꢀꢀꢀꢀꢀꢀꢀꢀ
(ⅶ)结构式(ⅶ)中,re分别独立地选自饱和脂肪烃基,优选为甲基;o为非0整数,优选为30~200的整数。端氢硅油中含氢量为0.01~0.2%,优选为0.06~0.08%。
31.端氢硅油将烯基硅油中的乙烯基端链接起来,增大了硅链的长度和韧性,在保证材料体系拉伸强度的同时,还可有效改善材料体系的断裂伸长率和柔软性。
32.本领域技术人员可以理解,本技术中端氢硅油、侧氢硅油可以分别是不同重复单元数的聚合物的混合物。例如在一些实施例中,所述端氢硅油可为o为30、m为100以及m为30~200间其他数值的聚合物的混合物。
33.三、导热填料(f)导热填料可选金属、金属氧化物、金属氢氧化物、金属氮化物、金属碳化物、碳同素异形体等常见导热填料中的一种或多种的复合。金属导热填料进一步可选铝粉、铜粉、铁粉、镍粉、金粉、金属硅粉、铟粉、镓粉等,金属氧化物导热填料进一步可选氧化铝粉、氧化锌粉等,金属氮化物导热填料进一步可选氮化铝粉、氮化硼粉等,碳同素异形体导热填料进一步可选金刚石粉、碳粉、石墨烯粉等。另外,优选导热系数为8w/mk或以上的导热填料。这是因为,如果导热填料的导热系数为8w/mk或以上,则热界面材料本身的导热系数也会变大。
34.综合考虑导热性和实用性,本技术实施例导热填料优选铝粉、氧化铝粉、氧化锌粉中的一种或多种的组合,进一步优选为铝粉和/或氧化锌粉。导热填料的平均粒径优选为0.1~100μm,进一步优选为0.8~20μm;当平均粒径大于1μm时,所得到的导热硅胶组合物可获得良好的延展性,成为润滑脂;当平均粒径小于100μm时,导热硅胶组合物的耐热性变大,且热性能恶化的可能性很小。需要说明的是,本技术中平均粒径由激光粒度仪(欧美克)测定,为基于体积的平均粒径。导热填料颗粒的形状可为任何形状,例如球形。在热界面材料组合物中,导热填料的质量百分数为85~93%,优选为91~93%。
35.四、催化剂(g)催化剂用来促进烯基与si-h键活性基团间的加成反应,可以选自铂基金属催化剂或胶囊型催化剂,也可以选择其他常规的加成反应催化剂。铂基金属催化剂为公知的加成反应催化剂,可列举出包括铂、铂黑色、氯铂酸、铂烯烃配合物、铂醇配合物和铂配位化合物。可单独使用一种铂基金属催化剂,或多种铂基金属催化剂联合使用。优选的,铂基金属催化剂选自卡斯特催化剂(cas号:81032-58-8)或胶囊型催化剂。所述卡斯特催化剂中pt(铂)含量为2wt.%。
36.当选择铂族金属系催化剂时,同时还需配合添加抑制剂,抑制剂用来让催化剂的效果减缓。胶囊型催化剂是使用树脂将铂族金属系催化剂(例如卡斯特催化剂)封在胶囊中,使用时通过加热使胶囊破裂,催化剂进入体系固化。囊型催化剂中pt含量为优选为
1wt.%。当选择胶囊型催化剂时,则无需添加抑制剂。催化剂的加入量为催化剂量,即促进加成反应和固化组合物所需的有效量,优选为pt的最终浓度为0.1~1000ppm,更优选为5~100ppm,此处pt浓度指元素pt在本技术最终所合成热界面材料中的含量。
37.五、润湿剂(h)润湿剂包覆于导热填料表面的成分,用来降低导热填料与烯基硅油、含氢硅油的表面张力,降低粘度,并促进导热填料的高填充。在热界面材料组合物中,如果润湿剂用量小于0.1%,则产品几乎不能表现出足够的润湿性;如果润湿剂用量大于15%,则产品会表现出牙膏状,从而破坏施工性。本技术实施例中润湿剂用量为0.60~1.5%,优选为0.60~0.75%,进一步优选为0.64~0.67%。
38.本技术实施例中润湿剂选自可水解的有机聚硅氧烷,其通用结构式如下:
ꢀꢀꢀꢀꢀꢀꢀꢀꢀꢀꢀꢀꢀꢀꢀꢀꢀꢀꢀ
(
ⅷ
)结构式(
ⅷ
)中,rh独立地为碳原子数1~10的二价碳基,rh1独立地为碳原子数1~10的二价碳基,rh和rh1相同或不同;p为非0整数,优选为5~100,进一步优选为10~60。当p小于5,由硅胶成分产生的溢油量变得严重,可靠性恶化;当p大于100,导电填料的润湿性降低。
39.rh、rh1进一步为线性烷基、支链烷基、环状烷基、芳基、芳烷基和卤化烷基。线性烷基可列举出甲基、乙基、丙基、己基、辛基和十烷基。支链烷基可列举出异丙基、异丁基、叔丁基和2-乙基己基。环烷基可列举出环戊基、环己基。芳基可列举出苯基。rh1优选为甲基或苯基。
40.六、附着力促进剂(i)附着力促进剂包括含可水解的甲氧基、乙氧基等活性基团的附着力促进剂。在产品固化过程中,这些活性基团可发生水解、交联反应,从而增强产品在铜,硅等材料表面的附着力,使产品具有较高的稳定性耐用性。在热界面材料组合物中,当附着力促进剂用量小于0.05%时,不能起到有效提高附着力的效果;而当附着力促进剂用量大于2%,不会再提高附着力,而造成原材料浪费。本技术实施例中,附着力促进剂的用量为0.1~0.3%,优选为0.13~0.24%,进一步优选为0.13~0.14%。
41.本技术实施例中附着力促进剂选自氢硅型附着力促进剂,其为含1~7个氢硅基团及3个(与硅原子相连的)甲氧基或乙氧基的化合物。氢硅型附着力促进剂优选三甲氧基氢硅烷(cas号:2487-90-3)。
42.七、抑制剂(j)当催化剂选择铂基金属系催化剂时,同时还需配合添加抑制剂,抑制剂可让催化剂的催化效果减缓。若不加入催化剂,产品会在室温下出现固化,导致难以保存。铂基金属系催化剂和抑制剂配合使用,增加了产品的保存性能。本实施例中抑制剂选自含不饱和炔烃基的化合物,所述含不饱和炔烃基的化合物可以选自但不限于1-乙炔基环己醇(cas号:78-27-3)、3-甲基-1-丁炔-3-醇、3-苯基-1-丁炔-3-醇、3-丙基-1-丁炔-3-醇、3-辛基-1-丁炔-3-醇或1-二甲氢硅氧基-1-乙炔基-环己烷中的一种或几种,优选为1-乙炔基环己醇。本技术实施例中,抑制剂用量为0.01~1%,优选为0.09~0.17%,进一步优选为0.09~0.1%。
43.八、其他组分除了上述组分(a)~(j),本技术实施例热界面材料还可以包含常规的抗氧化剂,以防止添加固化型硅树脂组合物恶化。此外,粘附促进剂、脱模剂、着色剂、阻燃剂(耐热增强剂)、抗沉淀剂、嗜硫剂等可根据需要添加。
44.下面将提供本技术的实施例和对比例,实施例和对比例中的原材料具体如下:a1:三羟甲基亚丙基三丙烯酸酯基封端的聚硅氧烷,聚合度200,粘度0.8pa
·
s;a2:三羟甲基亚丙基三丙烯醚基封端的聚硅氧烷,聚合度200,粘度0.3pa
·
s;b1:侧烯基硅油,粘度0.2pa
·
s,乙烯基含量1.21wt.%;b2:侧烯基硅油,粘度2pa
·
s,乙烯基含量0.75wt.%;b1和b2均选自浙江润禾有机硅材料有限公司的侧烯基硅油;c:端侧烯基硅油,采用浙江润禾有机硅材料有限公司的端侧乙烯基硅油,粘度0.2pa
·
s,乙烯基含量1.25wt.%;d1:侧氢硅油,粘度0.03~0.04pa
·
s,含氢量0.13~0.14wt.%,采用浙江润禾有机硅材料有限公司的侧氢硅油rh-h57(主要成分:聚二甲基甲基氢硅氧烷);d2:侧氢硅油,粘度0.06~0.08pa
·
s,含氢量0.17~0.19wt.%,采用浙江润禾有机硅材料有限公司的侧氢硅油rh-h33(主要成分:聚二甲基甲基氢硅氧烷);e:端氢硅油,粘度0.03~0.05pa
·
s,含氢量0.06~0.08wt.%,采用浙江润禾有机硅材料有限公司的端氢硅油rh-dh07(主要成分:氢封端聚二甲基硅氧烷);f1:球形铝粉,平均粒径20μm;f2:球形铝粉,平均粒径为5μm;f3:纳米氧化锌,平均粒径0.8μm;g1:卡斯特催化剂,有效成分浓度2%;g2:胶囊催化剂,有效成分浓度1%;h:润湿剂结构式为,其中q平均值30;i:附着力促进剂选自三甲氧基氢硅烷,cas号:2487-90-3;j:抑制剂,选自1-乙炔-1-环己醇。
45.本实施例中,a1和a2自制,其中,a1的合成方法为:在配有通氮气、搅拌器、温度计以及回流冷凝装置的四口烧瓶中,按照摩尔比3.3:1.0(即c=c键:si-h键)取26.96g三羟甲基丙烷三丙烯酸酯(cas号:15625-89-5,厂家:深圳飞扬化工有限公司)和592g的端氢硅油(采用浙江润禾rh-h518,氢含量0.17~0.19wt.%,聚合度约200),将26.96g三羟甲基丙烷三丙烯酸酯和0.309g卡斯特催化剂(cas号:81032-58-8,厂家:广州市矽友新材料有限公司,有效pt含量20000ppm),将三羟甲基丙烷三丙烯酸酯和卡斯特催化剂加入四口烧瓶,将温度升至95℃,用蠕动泵将592g的端氢硅油加入反应体系中,加入过程约6h。经继续反应6h后,减压蒸去低沸物得到约619g的三羟甲基亚丙基三丙烯酸酯基封端的聚硅氧烷。
46.a2的合成方法为:在配有通氮气、搅拌器、温度计以及回流冷凝装置的四口烧瓶中,按照摩尔比3.3:
1.0(即c=c键:si-h键)取20.48g季戊四醇三烯丙基醚(cas号:1471-17-6,厂家:深圳飞扬化工有限公司)和592g的端氢硅油(采用浙江润禾rh-h518,氢含量0.17~0.19wt.%,聚合度约200),将20.48g季戊四醇三烯丙基醚和0.304g卡斯特催化剂(cas号:81032-58-8,厂家:广州市矽友新材料有限公司,有效pt含量20000ppm),将季戊四醇三烯丙基醚和卡斯特催化剂加入四口烧瓶,将温度升至90℃,用蠕动泵将592g的端氢硅油加入反应体系中,加入过程约6h。经继续反应6h后,减压蒸去低沸物得到约610g的三羟甲基亚丙基三丙烯醚基封端的聚硅氧烷。
47.本技术实施例中热界面材料的制备方法如下:将烯基硅油、导热填料和润湿剂按配比添加到行星搅拌机,加热到110~160℃搅拌0.5~5h;冷却至室温,再加入含氢硅油、催化剂、附着力促进剂和抑制剂,继续室温搅拌0.1~4h;最后经真空脱泡得到产品。本技术实施例中,在导热填料加入前,对导热填料进行加热干燥,即将导热填料置于110℃烘箱内加热干燥2h。
48.采用如下方法测定实施例和对比例产品的各项性能。
49.粘度:在室温(25℃)下采用粘度计测定。导热率:将产品平整地涂抹在两个长3cm、宽2cm、厚5mm的槽中,固化后用热线法在室温下测定导热率。硬度:测定邵氏硬度。断裂伸长率和拉伸强度:按照标准hg/t2580-94进行测定。si附着力;按照标准gb11211-89进行测定。室温可施工时间:将产品在室温放置7天(但实施例3产品在室温中放置了1个月),隔预设时间测定其粘度,具体地,头3天,每隔12h测定一次粘度,对实施例3产品每隔2天测定一次粘度,若粘度变化率小于50%(粘度变化率是指相对初始粘度的变化率),视为可施工状态;否则为不可施工状态。
50.实施例和对比例的配方分别见表1和表3,相应的性能数据分别见表2和表4,从表中可以看出,实施例产品具有断裂伸长率高,附着力好,拉伸强度高,触变性好,可施工时间长等有益效果。
51.表1 实施例1-8的配方
表2 实施例1-8的性能数据
表3 对比例1-6的配方表4 对比例1-6的性能数据从表1~4可以发现,实施例1~8的产品具有优异的导热率以及具有更长的断裂伸长率;从实施例3可以看出,相比铂基金属催化剂,胶囊型催化剂可极大增加产品的室温可施工时间;从实施例6可以看出,当si-h键基团的含量偏高时,会降低断裂伸长率,当含氢硅油中si-h键基团的摩尔量为烯基硅油中烯基基团的0.9~1.1倍,会获得明显更优异的断裂伸长率。对比例1~2中,未添加a组分,产品硬度偏高,断裂伸长率低。对比例3~4中未添加e
组分,产品断裂伸长率低。对比例5中,未添加润湿剂,样品成膏状,无法成胶。对比例6中,含氢硅油用量偏多,产品硬度偏高,断裂伸长率低。
52.由于本技术热界面胶具有高伸长率和高导热性,特别适合链接芯片中的发热件和冷却件,避免两者在使用过程开裂,始终可保持较高的导热能力。
53.上述实施例仅是为了清楚地说明所做的实施例,而并非对实施方式的限制。对于所属领域的普通技术人员来说,在上述说明的基础上还可以做出其他不同形式的变化或者变动,这里无需也无法对所有的实施方式予以穷举,因此所引申的显而易见的变化或变动仍处于本发明创造的保护范围之内。