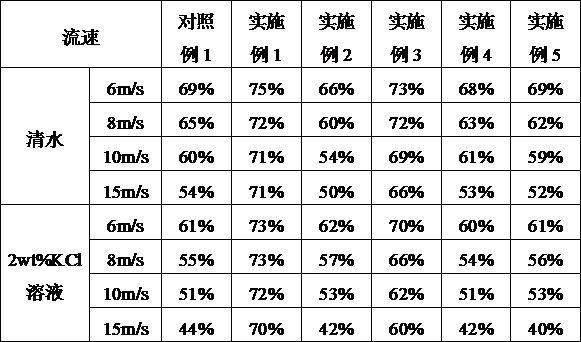
1.本发明涉及减阻剂技术领域,尤其涉及一种耐盐型压裂用减阻剂及其制备方法。
背景技术:2.随着我国石油与天然气消费量日益增长,油气自主供应能力不足,对外依存度持续提高,严重影响我国能源安全。非常规油气资源作为清洁能源的重要组成部分,是我国调整能源结构的一项重要内容。目前,非常规油气开采核心技术主要是滑溜水(减阻水)体积(缝网)压裂技术和水平井技术,其中滑溜水压裂液中的核心组分减阻剂是实现体积压裂改造的重要物质基础之一。压裂液由高压泵注增压后通过管柱高速泵入地层,但在高速泵注下,管内会出现严重的湍流摩阻增加现象。加入减阻剂不仅降低施工摩阻,改善裂缝复杂度,而且减少设备对水马力的要求,避免设备因作业过程中的高速冲击造成磨损。1948年toms无意中发现聚甲基丙烯酸甲酯能有效减小湍流的流动摩擦阻力。自此,国内外学者对高分子聚合物的流动特性、减阻效果和减阻机理等方面进行了深入的研究,并且将聚合物减阻剂成功应用于页岩储层压裂。页岩气作为一种储量丰富的非常规能源已经受到世界各国的广泛重视。作为一种新兴的非常规天然气,页岩气对于优化能源消费结构、缓解能源对外依存度具有重要意义。而滑溜水压裂技术是国内外页岩气开采的主要技术之一,减阻剂又是滑溜水压裂液的核心添加剂之一。聚丙烯酰胺类降阻剂具有成本低,易溶解等优势,目前是滑溜水减阻剂研究的重点。该类减阻剂的室内研究及现场应用已经取得了一定的进展。
3.可应用的减阻剂主要包括胍胶、黄原胶、田菁胶、纤维素等生物多糖类,聚氧乙烯及其衍生物类,聚丙烯酰胺及其衍生物等水溶性减阻剂类。生物基多糖和生物胶因为可生物降解的特点,在作为压裂减阻剂方面有其环境友好的优势,其主要代表就是水溶性的瓜尔胶和黄原胶。聚氧乙烯(peo)由于具有—ch2—ch2—o—重复单元结构,其分子链在空间上表现为螺旋结构,分子链柔顺性好,水溶性强,在理论上作为减阻剂非常具有优势,在早期是用作减阻机理研究的典型材料。表面活性剂因为其存在疏水链段,当浓度超过临界胶束浓度后,在水溶液中会聚集形成胶束,虽然单个表面活性剂分子相对分子质量不高,但形成胶束后不仅有较大相对分子质量,也有较大的立体空间结构,一般形成棒状结构,使得表面活性剂具有类似聚合物分子链的作用,但相比聚合物分子链,胶束链更短,所以更耐高速剪切,而单个表面活性剂因为分子链短小,无机盐对其影响程度更小,所以表面活性剂作为减阻剂有其特殊的优势。主要类型包括阴阳离子、非离子和两性离子表面活性剂四类减阻剂。高矿化度配液水质中对减阻剂的聚合物分子结构有严重的影响,宏观上主要表现为减阻水溶液黏度降低,减阻率显著降低,甚至某些减阻剂与高矿化度配液水不配伍,无法有效分散于水中。而微观上水中的无机盐金属离子对减阻剂聚合物分子的影响是多方面的共同作用,主要包括静电屏蔽,压缩聚合物表面水化膜双电层以及减小聚合物表面水化膜厚度作用。
4.减阻剂分子多为改性聚丙烯酰胺,其分子链上分布有水解电离的带负电的基团
(如-coo-),其在水溶液中由于电荷互斥力而使得聚合物分子链伸展性加强,但在高矿化度盐水中,大量的无机阴离子和阳离子分布在聚合物分子链周围,由于带电基团更容易吸引其相反电荷离子,导致带电基团被屏蔽,从而使得分子链上带电基团的电荷斥力的减弱,最终导致聚合物延展程度降低,卷曲程度增加。而卷曲的减阻剂分子链抑制湍流作用和弹性大幅度降低,减阻作用因此降低。在高含钙镁离子等高价金属离子的水溶液中,钙镁离子与聚合物分子链上某些基团具有特殊的连接作用,其中主要包括高价离子与羧酸根离子的架桥络合作用。钙镁离子与羧酸根离子在水溶液中存在一个溶积度值,当钙镁离子与羧酸根离子之积超过其溶积度值之后,高价金属离子开始与羧酸根产生络合作用,对钙镁离子而言,尤其是钙离子,两个羧酸根与钙离子连接成核,并且随着离子浓度增加,晶核不断增长。当不同聚合链的羧酸根与同一金属连接时,整个聚合缠绕结构得到加强。在水资源越来越紧张,环保要求日益凸显的情况下,利用浅层地表水、地层返排水等进行配液施工逐渐受到关注,但由于其高矿化度的特点,一般减阻剂很难在该条件下满足施工性能要求,故研制具备有较好耐盐性的减阻剂是未来减阻剂发展的重要方向之一。当暴露于高盐度盐水时,聚合物的减阻性能取决于单体类型、重复单体单元、分子结构、分子量和离子强度。目前主要通过接入功能单体降低聚合物对盐的敏感性,包括含有硫酸根基团的单体、含有环状结构基团的单体、含有疏水性基团的单体等等,这些基团的接入不仅能够改善其在盐水溶液中的减阻性能,而且可以提高共聚物的抗温和抗盐性能;或增加分子链的刚性,提高聚合物的热稳定性及抗剪切性。
5.专利cn112410013 b提供了一种悬浊液状减阻剂及其制备方法,按总质量为100%计,减阻剂由以下质量百分比的原料组分组成:水溶性高分子聚合物15~60wt%,表面活性剂0.3~2wt%,增稠剂0.5~5wt%,余量为油溶剂;减阻剂的粘度为5-20万cp;增稠剂选自聚苯乙烯-乙烯-丙烯、聚苯乙烯-乙烯-丁烯、聚乙烯、聚丙烯、聚脲、聚异戊二烯、聚丁二烯、聚二苯乙烯-乙烯-丙烯、聚(苯乙烯-丁二烯)、聚甲基丙烯酸酯、聚异丁烯、氢化(苯乙烯-异戊二烯)共聚物、脂肪醇中的一种或多种。该申请提供的悬浊液状减阻剂,针对特定用量以及分子量的聚丙酰胺粉,采用特定组成配比的增稠剂配合特定组成及配比的表面活性剂,使获得的最终减阻剂产品具有更好的减阻性、耐盐性以及储存稳定性。
6.专利cn113736443 a公开了一种压裂用低碳环保多功能型减阻剂及其制备方法,石油天然气领域,更具体的是涉及压裂用减阻剂领域,解决现有的减阻剂碳足迹较多,碳排放较大,不环保的问题,包括如下组分:稠化剂,分散介质,增稠剂,增稠助剂,湿润分散剂,助分散剂,分散介质为聚乙二醇-100、聚乙二醇-200、聚乙二醇-400中的一种或多种;绝大部分均为水溶性原材料,易降解易返排,不会对地层造成二次伤害,堵塞地层等问题,可以有效提高页岩气储层返排效率,提高产量;悬浮复配工艺仅涉及原材料的投放和搅拌,不涉及温控,碳足迹、碳排放单一;粉末型阴离子聚丙烯酰胺原材料配制为水溶液聚合,低温引发,反应温和,亦不涉及过多的碳足迹和碳排放。
7.目前所使用的聚丙烯酰胺类降阻剂有粉剂型和乳液型之分,业界普遍认为粉剂型产品聚合工艺简单,成本较低,一般产品溶解速度较慢,但是速溶型产品在一定条件下也可以实现在线混配。乳液型产品聚合工艺复杂,成本较高且不便运输,但是产品的溶解速度较快,较容易实现在线混配。然而,目前仍存在的一问题是聚丙烯酰胺大多是被制备成固体粉末状添加到压裂液中使用的,然而,粉状产品的溶解速度较慢,通常溶解时间为20~120min,
未溶解的聚合物会堵塞井筒或油藏,导致采油效率降低。乳液产品的使用更为广泛,因为乳液产品的溶解速度较快,溶解时间约为3~5min。然而,这类乳液产品预先添加了亲水表面活性剂,处于不稳定的相态,在有水的情况下会发生突然的相变。此外,不稳定的聚合物乳液产品在长时间的运输或储存过程中容易发生乳化。因此,应设计和制备一种新的聚丙烯酰胺类乳液作为减阻剂来应用到压裂中以平衡储存稳定性和溶解速度是十分必要的。
技术实现要素:8.有鉴于现有技术中的上述缺陷,本发明所要解决的技术问题是提供一种稳定性好,溶解快的聚丙烯酰胺类乳液减阻剂及其制备方法。
9.刺激反应型表面活性剂可以在外部刺激条件下发生特定的结构变化,使乳剂的相位反转或反乳化。在有些研究中将刺激反应型表面活性剂应用于o/w型乳剂,以制备疏水性聚合物,其中外部刺激被用来破坏聚合物乳剂的稳定性,导致疏水性聚合物乳胶颗粒的分离。然而,更广泛使用的亲水聚合物,如聚丙烯酰胺,却很少被如此使用。这可能是因为亲水聚合物不能通过反乳化从乳液中提纯。对于乳液型减阻剂来说,乳液纯化是没有必要的。聚合物减阻剂乳液可以在水中释放亲水聚合物,其溶解速度足以减少阻力。在本发明中,发明人制备了基于马来酸和二甲氨基-十八烷基乙酰胺的新型ph敏感复合表面活性剂,并用于构建ph敏感的w/o乳液,以便随后对聚丙烯酰胺基减阻剂进行反乳液聚合。由于没有添加亲水表面活性剂作为破乳剂,在ph值敏感复合表面活性剂基础上构建的聚丙烯酰胺基w/o乳液减阻剂显示出很高的稳定性,另外,这种对ph值敏感的聚合物乳液分别在ph值《6和》8时可立即产生相位倒置和破乳化。聚丙烯酰胺可达到快速释放使其在短时间内完全溶解并达到良好的减阻效果。因此,这种基于刺激反应的表面活性剂构建水溶性聚丙烯酰胺乳液减阻剂的方法为减阻剂的设计和生产提供了新的思路,有助于提高减阻剂效率。
10.本发明的技术方案:一种耐盐型压裂用减阻剂的制备方法,包括如下步骤:s1将十八烷胺与甜菜碱混合,氮气气氛下升温至70~90℃,再加入亚硫酰氯,30~60min内升温至150~170℃,继续加入氧化铝,在160~200℃下继续反应20~28h,反应结束后过滤,滤饼经丙酮、异丙醇洗涤后干燥得到二甲氨基-十八烷基乙酰胺;s2将马来酸和步骤s1中的二甲氨基-十八烷基乙酰胺混合,加水,升温至70~90℃下搅拌1~3h,得到马来酸/二甲氨基-十八烷基乙酰胺复合物;s3将丙烯酰胺、丙烯酸、2-丙烯酰胺-2-甲基丙磺酸加入到水中,加入步骤s2中的马来酸/二甲氨基-十八烷基乙酰胺复合物,搅拌,再加入1mol/l naoh水溶液调节ph至6~8,将液体石蜡加入到混合溶液中,在20~30℃下搅拌0.5~2h,得到聚合物乳液;s4将步骤s3得到的聚合物乳液注入氮气,在10~20℃下搅拌10~60min后,加入叔丁基过氧化氢和亚硫酸氢钠,以0.5~1℃/min的速度升温至30~50℃,继续搅拌2~4h进行聚合,反应结束后得到耐盐压裂液减阻剂。
11.优选的,所述步骤s1中十八烷胺与甜菜碱、亚硫酰氯、氧化铝的质量比为20~34:6~18:1~1.4:0.2~0.5。
12.优选的,所述步骤s2中马来酸与二甲氨基-十八烷基乙酰胺、水的质量比为5~15:35~45:5~10。
13.优选的,所述步骤s3中丙烯酰胺、丙烯酸、2-丙烯酰胺-2-甲基丙磺酸、水、马来酸/二甲氨基-十八烷基乙酰胺复合物、液体石蜡的质量比为5~10:1~2:3~5:60~80:1~3:40~60。
14.优选的,所述步骤s4中叔丁基过氧化氢和亚硫酸氢钠的质量比为0.5~1.5:0.5~1.5。
15.进一步的,所述耐盐型压裂用减阻剂的制备方法,包括如下步骤:s1将十八烷胺20~34重量份与甜菜碱6~18重量份混合,氮气气氛下升温至70~90℃,再加入亚硫酰氯1~1.4重量份,30~60min内升温至150~170℃,继续加入氧化铝0.2~0.5重量份,在160~200℃下继续反应20~28h,反应结束后过滤,滤饼经丙酮、异丙醇洗涤后干燥得到二甲氨基-十八烷基乙酰胺;s2将马来酸5~15重量份和步骤s1中的二甲氨基-十八烷基乙酰胺35~45重量份混合,再加入水5~10重量份,升温至70~90℃下搅拌1~3h,得到马来酸/二甲氨基-十八烷基乙酰胺复合物;s3将丙烯酰胺5~10重量份、丙烯酸1~2重量份、2-丙烯酰胺-2-甲基丙磺酸3~5重量份加入到60~80重量份水中,加入步骤s2中的马来酸/二甲氨基-十八烷基乙酰胺复合物1~3重量份,搅拌,再加入1mol/l naoh水溶液调节ph至6~8,再加入液体石蜡40~60重量份,在20~30℃下搅拌0.5~2h,得到聚合物乳液;s4将步骤s3得到的聚合物乳液注入氮气,在10~20℃、氮气气氛下搅拌10~60min后,加入叔丁基过氧化氢0.5~1.5重量份和亚硫酸氢钠0.5~1.5重量份,以0.5~1℃/min的速度升温至30~50℃,继续搅拌2~4h进行聚合,反应结束后得到耐盐压裂液减阻剂。
16.与现有技术相比,本发明的有益效果:(1)在本发明中,发明人制备了基于马来酸和二甲氨基-十八烷基乙酰胺的新型ph敏感复合表面活性剂,并用于构建ph敏感的w/o乳液,以便随后对聚丙烯酰胺基减阻剂进行反乳液聚合。由于没有添加亲水表面活性剂作为破乳剂,在ph值敏感复合表面活性剂基础上构建的聚丙烯酰胺基w/o乳液减阻剂显示出很高的稳定性;(2)该聚合物乳液可达到快速释放使其在短时间内完全溶解并达到良好的减阻效果,大大降低了阻塞管道的风险;(3)这种基于刺激反应的表面活性剂构建水溶性聚丙烯酰胺乳液减阻剂的方法为减阻剂的设计和生产提供了新的思路,有助于提高减阻剂效率。
具体实施方式
17.下面,通过具体实施例对本发明的技术方案进行详细说明,但是应该明确提出这些实施例用于举例说明,但是不解释为限制本发明的范围。
18.本发明实施例中部分原料的参数如下:聚丙酰胺粉末,mw=800~2500万,粒径:0.2~0.8mm,郑州市光洋环保技术有限公司。
19.液体石蜡,货号:585647,熔点:42℃,苏州筑信工业润滑油。
20.对照例1一种耐盐型压裂液减阻剂的制备方法,包括如下步骤:s1称取液体石蜡50g、黄原胶2g,在55℃充分搅拌使其完全溶解,得到混合物;s2将温度降低至45℃,向步骤s1得到的混合物中依次加入span60 1.25g 和
tween60 1.25 g,继续搅拌至完全溶解;s3保持温度45℃不变,向步骤s2中加入聚丙烯酰胺粉末13g、水70ml,搅拌3h,冷却至室温即获得耐盐压裂液减阻剂。
21.实施例1一种耐盐型压裂液减阻剂的制备方法,包括如下步骤:s1将十八烷胺27g与甜菜碱12g混合,氮气气氛下升温至80℃,再加入亚硫酰氯1.2g,45min内升温至160℃,继续加入氧化铝0.3g,在180℃下反应24h,反应结束后过滤,滤饼分别经丙酮、异丙醇洗涤后干燥得到二甲氨基-十八烷基乙酰胺;s2将马来酸10g和步骤s1得到的二甲氨基-十八烷基乙酰胺38g混合,再加入水8ml,升温至80℃下搅拌2h,得到马来酸/二甲氨基-十八烷基乙酰胺复合物;s3将丙烯酰胺7.5g、丙烯酸1.5g、2-丙烯酰胺-2-甲基丙磺酸4g加入到70ml水中,加入步骤s2得到的马来酸/二甲氨基-十八烷基乙酰胺复合物2.5g,搅拌,再加入1mol/l naoh水溶液调节ph至7,再加入液体石蜡50g,在25℃下搅拌1.5h,得到聚合物乳液;s4将步骤s3得到的聚合物乳液注入氮气,在15℃、氮气气氛下搅拌40min后,加入叔丁基过氧化氢1g、亚硫酸氢钠1g,以0.5℃/min的速度升温至40℃,继续搅拌3h进行聚合,反应结束后得到耐盐压裂液减阻剂。
22.实施例2一种耐盐型压裂液减阻剂的制备方法,包括如下步骤:s1称取液体石蜡50g、黄原胶2g,在55℃充分搅拌使其完全溶解,得到混合物;s2将温度降低至45℃,向步骤s1获得的混合物中加入聚丙烯酰胺粉末13g、水70ml,45℃下搅拌3h,冷却至室温即获得耐盐压裂液减阻剂。
23.实施例3一种耐盐型压裂液减阻剂的制备方法,包括如下步骤:s1将十八烷胺27g与甜菜碱12g混合,氮气气氛下升温至80℃,再加入亚硫酰氯1.2g,45min内升温至160℃,继续加入氧化铝0.3g,在180℃下继续反应24h,反应结束后过滤,滤饼分别经丙酮、异丙醇洗涤后干燥得到二甲氨基-十八烷基乙酰胺;s2将马来酸10g和步骤s1得到的二甲氨基-十八烷基乙酰胺38g混合,再加入水8ml,升温至80℃下搅拌2h,得到马来酸/二甲氨基-十八烷基乙酰胺复合物;s3将丙烯酰胺7.5g、丙烯酸1.5g、2-丙烯酰胺-2-甲基丙磺酸4g加入到70ml水中,加入步骤s2得到的马来酸/二甲氨基-十八烷基乙酰胺复合物2.5g,搅拌,再加入液体石蜡50g,在25℃下搅拌1.5h,得到聚合物乳液;s4将步骤s3得到的聚合物乳液注入氮气,在15℃、氮气气氛下搅拌40min后,加入叔丁基过氧化氢1g、亚硫酸氢钠1g,以0.5℃/min的速度升温至40℃,继续搅拌3h进行聚合,反应结束后得到耐盐压裂液减阻剂。
24.实施例4一种耐盐型压裂液减阻剂的制备方法,包括如下步骤:s1称取液体石蜡50g、羧甲基纤维素2g,在55℃充分搅拌使其完全溶解,得到混合物;s2将温度降低至45℃,向步骤s1得到的混合物中依次加入span60 1.25g和
tween60 1.25g,继续搅拌至完全溶解;s3保持温度45℃不变,向步骤s2中加入聚丙烯酰胺粉末13g、水70ml,搅拌3h,冷却至室温即获得耐盐压裂液减阻剂。
25.实施例5一种耐盐型压裂液减阻剂的制备方法,包括如下步骤:s1称取液体石蜡50g、聚乙烯2g,在55℃充分搅拌使其完全溶解,得到混合物;s2将温度降低至45℃,向步骤s1得到的混合物中依次加入span60 1.25g和tween60 1.25g,继续搅拌至完全溶解;s3保持温度45℃不变,向步骤s2中加入聚丙烯酰胺粉末13g、水70ml,搅拌3h,冷却至室温即获得耐盐压裂液减阻剂。
26.测试例1对对照例及实施例制备的减阻剂进行减阻测试,分别在清水和2wt%的kcl溶液中进行减阻测试,25℃下,分别将上述减阻剂配成0.05wt%水溶液加入到溶解罐中,溶液由泵输送流出,经转子流量计进入试验段。用转子流量计计量流量,流量大小由变频器控制,测定溶液通过试验段的压降。测试圆管直径为0.635cm,测试管段长度为3m,管径为10mm,减阻率(dr,%)按下式计算:dr=δp0-δp/δp0×
100%,其中p0为一定流速下清水或2wt% kcl水溶液流经测试管段时产生的压降,单位为pa;δp为同一流速下减阻剂溶液流经测试管段时产生的压降,单位为pa。具体测试结果见表1。
27.表1减阻性能测试结果表从减阻性能测试可以看出,对照例及实施例在清水中的减阻性能均表现较佳,而在盐型溶液中对照例1及实施例2、实施例4、实施例5的减阻性能则较差,这可能是由于实施例1及实施例3中在制备聚合物乳液时添加了含有磺酸根基团的单体,与羧酸根相比,磺酸根被认为能够与水形成更强的氢键从而提高了在溶液中的稳定性,而且磺酸根的亲水性更强,增加了共聚物的水溶性。另外磺酸基团的引入还可以提高共聚物抗盐性能,不仅如此,所制备的基于马来酸和二甲氨基-十八烷基乙酰胺的新型ph敏感复合表面活性剂能够帮助
提升乳液减阻剂的稳定性,同时聚丙烯酰胺可达到快速释放使其在短时间内完全溶解并达到良好的减阻效果,因此,不论是在清水条件还是盐溶液条件下均能表现出良好的减阻性能。
28.测试例2取实施例以及对照例中所制备的减阻剂,配制0.1wt%的水溶液,取聚丙酰胺粉末配制0.1wt%的水溶液作为空白对照,分别观察它们在水中溶解所需要的时间并进行记录,测试结果如表2所示。
29.表2溶解性测试反相聚合物乳液是分散相为聚合物乳液颗粒的w/o型乳液,实施例1中反相聚合物乳液在水中的快速溶解是由于聚合物乳液的ph刺激,导致聚合物乳液颗粒在水中的释放。虽然聚合物乳液颗粒可以释放到水中并在酸碱刺激下快速溶解,但快速释放和溶解机理不同。由于聚合物的分子大小比水分子大得多,当将粉末聚合物加入水中时,水分子会进入聚合物颗粒,聚合物会经历溶胀然后溶解的过程,这大大降低了溶解速率。相比之下,乳液聚合物由于与水的接触面积较大,溶解时间要短得多。对于常规的乳液聚合物,在使用前添加一种倒置表面活性剂来调节乳化剂的hlb值,使乳液更亲水,以分散在水中,如对照例1、实施例4、实施例5,可以加快溶解速率。然而,相转移剂的加入难以控制,导致聚合物乳液产品的性能不稳定。实施例1中通过添加碱来加速聚合物在水中的释放,导致聚合物乳液的相分离或反转,从而使得溶解加快,因此相比实施例3溶解速率更快。溶解速率的加快对于提升减阻性能是十分有利的,并且可以大大降低阻塞管道的风险。
30.测试例3对对照例及实施例所制备的减阻剂进行稳定型测试,称取相同质量的减阻剂20g在常温(室温25℃)下静置30天,观察是否出现肉眼可观察到的乳液分层现象,具体测试结果见表3.表3减阻剂稳定性测试结果表
从稳定性测试可以看到,聚丙烯酰胺乳液的稳定可以通过添加增稠剂及表面活性剂来实现,采用合适的表面活性剂,能够促使聚丙烯酰胺粉末在体系更稳定从而不出现分层,一旦出现分层减阻剂将很难再发挥出良好的减阻性,而普通表面活性剂的加入往往只能维持一段时间的稳定,这是远远不够的,而在实施例1中制备了基于马来酸和二甲氨基-十八烷基乙酰胺的新型ph敏感复合表面活性剂,并用于构建ph敏感的w/o聚合物乳液,以便随后对聚丙烯酰胺基减阻剂进行反乳液聚合。由于没有添加亲水表面活性剂作为破乳剂,在ph值敏感的复合表面活性剂基础上构建的聚丙烯酰胺基w/o乳液减阻剂显示出很高的稳定性,即使静置30天也未出现分层现象,这对于维持减阻剂的减阻性能来说是十分重要的。实施例1和3的稳定型结果表现不同可能是由于实施例3中没有加入naoh调节ph,这对于形成的聚合物乳液的状态有着较大影响,因此稳定性不如实施例1。这种基于ph敏感的w/o聚合物乳液能够根据ph来对自身状态进行调整,从而具有更好的稳定性。