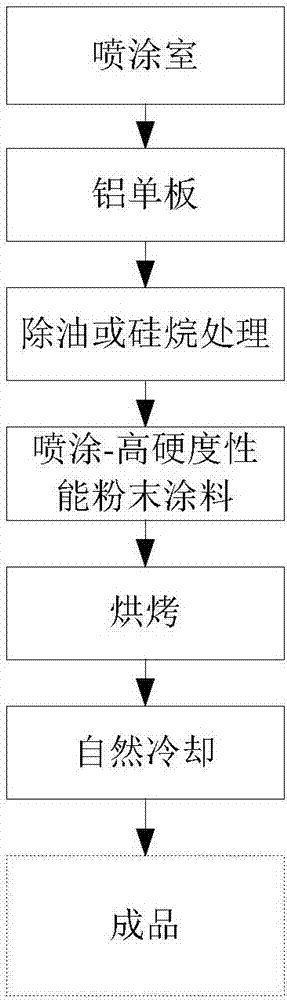
本发明属于涂料
技术领域:
,涉及一种高硬度粉末涂料、制备方法及其应用。
背景技术:
:体育器材、户外建筑幕墙、户外场所护栏板等户外物品的外观件长期暴露于户外环境中,容易受到外界的影响而造成刮擦,进而造成涂膜表面的擦伤,既影响外观件的美观,又容易造成涂层的破坏,进而对外观件的使用性能造成影响。传统粉末涂料覆盖外观件表面形成涂层,涂层采用一次喷涂、一次成膜的工艺制成,膜厚为60-120um,涂层对基材的粘结强度大、吸水率小、耐高温性能好、耐冲击、柔韧性好,但是存在硬度较低的缺陷。涂覆传统粉末涂料的涂层在使用过程中,因外力磨损或刮擦时会严重影响外观效果及使用寿命。尤其是,外观件的美感及使用寿命越来越受到重视,更加迫切需要克服该缺陷。有鉴于此,需要提供一种新型的高硬度粉末涂料,在保证涂层对于基材的附着力、耐高温性能、涂膜完整性的前提下,提高硬度性能,使其达到很好的耐刮擦效果。技术实现要素:为了克服上述现有技术存在的缺陷,本发明的第一个目的是提供一种高硬度粉末涂料,使涂料涂层的硬度性能好。本发明的另一个目的是提供一种所述高硬度粉末涂料的制备方法。本发明的再一个目的是提供一种所述高硬度粉末涂料用于外观件的用途。为了实现上述目的,本发明采用的技术方案如下:本发明的一个方面提供了一种高硬度粉末涂料,包括以下重量份的组分:所述聚氨酯树脂的玻璃化温度(tg)为45~55℃,优选50℃,本发明实施例中聚氨酯树脂为帝兴树脂(昆山)有限公司的uralacp1580。所述聚酯树脂的玻璃化温度(tg)为45~55℃,优选50℃,本发明实施例中聚酯树脂为帝兴树脂(昆山)有限公司的reafree17091。所述异氰酸脂二聚体的nco总量(异氰酸酯基团总质量)为15.2±0.5%,本发明实施例中异氰酸脂二聚体为赢创德固赛(evonikdegussa)的异氰酸酯二聚体b1530(粉末)。优选地,所述助剂包含以下重量份的组分:更优选地,所述流平剂优选5份。所述流平剂为宁波南海化学有限公司的glp599。所述安息香系统命名为2-羟基-1,2-二苯基乙酮,为宁波南海化学有限公司或南通精元药业有限公司的安息香。所述催化剂为上海恒祥化工材料有限公司的st-70聚氨脂催化剂。所述干燥剂为赢创德固赛(evonikdegussa)的氧化铝c(aerosilaluc)。所述抗划伤助剂为上海信立钛化工科技有限公司的mc-100(jtc305s),或南京天诗新材料科技有限公司的ptfe0101。所述颜料为钛白粉或炭黑中的至少一种,钛白粉使用杜邦化工有限公司的r902,所述炭黑使用赢创德固赛的fw200。所述填料为硫酸钡,为上海信立钛化工科技有限公司的on310,或者贵州鑫城矿业有限公司的w44hd。本发明的另一个方面提供了一种所述高硬度粉末涂料的制备方法,包括以下步骤:将20-25份聚氨酯树脂、5-10份聚酯树脂、25-30份异氰酸脂二聚体、5.5-7.5份助剂、1.4-7份颜料和25-38份填料混合均匀,熔融挤出,压片,冷却,然后依次进行粗破碎和磨细粉碎,筛分后获得所述高硬度粉末涂料。所述熔融挤出的温度为95-105℃。所述高硬度粉末涂料的粒径为25-80μm。本发明的再一个方面提供了一种所述高硬度粉末涂料用于外观件的用途,包括以下步骤:将外观件的表面处理,喷涂所述高硬度粉末涂料,然后烘烤、冷却,获得涂层进行性能测试。所述烘烤的温度为190-220℃,时间为10~20min,烘烤加热采用高频线圈、天然气炉、生物颗粒炉或柴油炉加热。所述外观件为铝单板外观件。由于采用了上述技术方案,本发明具有以下优点和有益效果:本发明的高硬度粉末涂料对于基材的硬度性能优秀,高硬度粉末涂料和基材的附着力达到最好,对于基材的粘结性能好、硬度性能好,具有很好的耐刮擦效果,避免了因涂层受外力刮擦而导致涂层的性能不良问题的发生;在应用到外观件时,可在现有户外粉末产品喷涂工艺基础上进行,不改变现场喷涂工艺;对本发明的高硬度粉末涂料的涂层进行硬度测试,结果表明该产品可以达到铅笔硬度4h(按gb/t63792006),涂层的硬度性能好。附图说明图1为本发明的高硬度粉末涂料的制备方法的流程示意图;以及图2为本发明的高硬度粉末涂料用于外观件的用途的流程示意图。具体实施方式为了更清楚地说明本发明,下面结合优选实施例对本发明做进一步的说明。本领域技术人员应当理解,下面所具体描述的内容是说明性的而非限制性的,不应以此限制本发明的保护范围。在通过以下实施例对本发明的目的予以阐明、解释的情形下,所述组合物的组分均以重量份为通用标准予以释明。在无特别说明的情况下,为简明起见,本发明实施例中所述的“份”与重量份具有相同的意义。在以下通过实施例对本发明进一步予以阐明的举例中,聚氨酯树脂的玻璃化温度为45~55℃,优选50℃,本发明实施例中聚氨酯树脂为帝兴树脂(昆山)有限公司的uralacp1580。在以下通过实施例对本发明进一步予以阐明的举例中,聚酯树脂的玻璃化温度为45~55℃,优选50℃,本发明实施例中聚酯树脂为帝兴树脂(昆山)有限公司的reafree17091。在以下通过实施例对本发明进一步予以阐明的举例中,异氰酸脂二聚体的nco总量(重量)为15.2±0.5%,本发明实施例中异氰酸脂二聚体为赢创德固赛(evonikdegussa)的异氰酸酯二聚体b1530(粉末)。在以下通过实施例对本发明进一步予以阐明的举例中,流平剂为宁波南海化学有限公司的glp599;安息香系统命名为2-羟基-1,2-二苯基乙酮,为宁波南海化学有限公司或南通精元药业有限公司的安息香;催化剂为上海恒祥化工材料有限公司的st-70聚氨脂催化剂;干燥剂为赢创德固赛(evonikdegussa)的氧化铝c(aerosilaluc);抗划伤助剂为上海信立钛化工科技有限公司的mc-100(jtc305s),或南京天诗新材料科技有限公司的ptfe0101。在以下通过实施例对本发明进一步予以阐明的举例中,填料为硫酸钡,为上海信立钛化工科技有限公司的on310,或者贵州鑫城矿业有限公司的w44hd。在以下通过实施例对本发明进一步予以阐明的举例中,颜料为钛白粉或炭黑中的至少一种,钛白粉使用杜邦化工有限公司的r902;炭黑使用赢创德固赛的fw200。在以下通过实施例对本发明进一步予以阐明的举例中,外观件为铝单板外观件,同时适用于其他户外铝件,铝单板外观件优选为户外体育场外观铝单板,高硬度粉末涂料适用于工作温度为-25℃-50℃的户外环境。实施例1一种高硬度粉末涂料,包括以下重量份的组分:如图1所示,图1为本发明的高硬度粉末涂料的制备方法的流程示意图。首先,按照所述高硬度粉末涂料组分的配方组成精确的称量原材料,在预混罐里经过高速旋转混合均匀(预混时间5-10分钟),然后把混合均匀的生料匀速放入双螺杆挤出机,在95-105℃条件下熔融挤出,经过冷却辊压成料片,料片在自然温度下冷却后,使用粉碎机对料片进行粗破碎,得到的物料冷却后使用粉碎机进行磨细粉碎,使用180目筛网进行筛分,180目筛网过筛的筛分自然冷却,最后得到粒径均匀(25-45μm)的所述高硬度粉末涂料。如图2所示,图2为本发明的高硬度粉末涂料用于外观件的用途的流程示意图。将铝单板进行除油(或进行其他前处理如硅烷处理),在无尘室进行喷涂,之后进入烘道进行烘烤,烘烤的温度为190-220℃,时间为10~20min,烘烤加热采用高频线圈加热;待涂层充分固化后自然冷却。涂料在铝单板的喷涂方式和正常铝单板喷涂方式一样,工艺数据如表1所示:表1如表2所示,表2为本发明的高硬度粉末涂料涂层的附着力测试和铅笔硬度结果。对涂层进行附着力测试,两层间可以100/100附着。对所述涂层进行硬度测试,最高可以达到铅笔硬度4h(按gb/t63792006),说明所述涂层硬度性能优异。表2测试内容测试结果测试结论附着力测试0级测试通过1h铅笔硬度测试没有塑性变形或内聚破坏测试通过2h铅笔硬度测试没有塑性变形或内聚破坏测试通过3h铅笔硬度测试没有塑性变形或内聚破坏测试通过4h铅笔硬度测试没有塑性变形或内聚破坏测试通过5h铅笔硬度测试有塑性变形测试不通过实施例2一种高硬度粉末涂料,包括以下重量份的组分:首先,按照所述高硬度粉末涂料组分的配方组成精确的称量原材料,在预混罐里经过高速旋转混合均匀(预混时间5-10分钟),然后把混合均匀的生料匀速放入双螺杆挤出机,在95-105℃条件下熔融挤出,经过冷却辊压成料片,料片在自然温度下冷却后,使用粉碎机对料片进行粗破碎,得到的物料冷却后使用粉碎机进行磨细粉碎,使用180目筛网进行筛分,180目筛网过筛的筛分自然冷却,最后得到粒径均匀(26-70μm)的所述高硬度粉末涂料。本实施例的高硬度粉末涂料用作外观件的用途,包括以下步骤:将铝单板进行除油(或进行其他前处理如硅烷处理),在无尘室进行喷涂,之后进入烘道进行烘烤,烘烤的温度为190-220℃,时间为10~20min,烘烤加热采用高频线圈加热;待涂层充分固化后自然冷却。对所述涂层进行硬度测试,最高可以达到铅笔硬度4h(按gb/t63792006),说明所述涂层硬度性能优异。实施例3一种高硬度粉末涂料,包括以下重量份的组分:首先,按照所述高硬度粉末涂料组分的配方组成精确的称量原材料,在预混罐里经过高速旋转混合均匀(预混时间5-10分钟),然后把混合均匀的生料匀速放入双螺杆挤出机,在95-105℃条件下熔融挤出,经过冷却辊压成料片,料片在自然温度下冷却后,使用粉碎机对料片进行粗破碎,得到的物料冷却后使用粉碎机进行磨细粉碎,使用180目筛网进行筛分,180目筛网过筛的筛分自然冷却,最后得到粒径均匀(26-70μm)的所述高硬度粉末涂料。本实施例的高硬度粉末涂料用作外观件的用途,包括以下步骤:将铝单板进行除油(或进行其他前处理如硅烷处理),在无尘室进行喷涂,之后进入烘道进行烘烤,烘烤的温度为190-220℃,时间为10~20min,烘烤加热采用高频线圈加热;待涂层充分固化后自然冷却。对涂层进行硬度测试,最高可以达到铅笔硬度4h(按gb/t63792006),说明所述涂层硬度性能优异。实施例4一种高硬度粉末涂料,包括以下重量份的组分:首先,按照所述高硬度粉末涂料组分的配方组成精确的称量原材料,在预混罐里经过高速旋转混合均匀(预混时间5-10分钟),然后把混合均匀的生料匀速放入双螺杆挤出机,在95-105℃条件下熔融挤出,经过冷却辊压成料片,料片在自然温度下冷却后,使用粉碎机对料片进行粗破碎,得到的物料冷却后使用粉碎机进行磨细粉碎,使用180目筛网进行筛分,180目筛网过筛的筛分自然冷却,最后得到粒径均匀(26-70μm)的所述高硬度粉末涂料。本实施例的高硬度粉末涂料用作外观件的用途,包括以下步骤:将铝单板进行除油(或进行其他前处理如硅烷处理),在无尘室进行喷涂,之后进入烘道进行烘烤,烘烤的温度为190-220℃,时间为10~20min,烘烤加热采用高频线圈加热;待涂层充分固化后自然冷却。对涂层进行硬度测试,最高可以达到铅笔硬度4h(按gb/t63792006),说明所述涂层硬度性能优异。实施例5一种高硬度粉末涂料,包括以下重量份的组分:首先,按照所述高硬度粉末涂料组分的配方组成精确的称量原材料,在预混罐里经过高速旋转混合均匀(预混时间5-10分钟),然后把混合均匀的生料匀速放入双螺杆挤出机,在95-105℃条件下熔融挤出,经过冷却辊压成料片,料片在自然温度下冷却后,使用粉碎机对料片进行粗破碎,得到的物料冷却后使用粉碎机进行磨细粉碎,使用180目筛网进行筛分,180目筛网过筛的筛分自然冷却,最后得到粒径均匀(26-70μm)的所述高硬度粉末涂料。本实施例的高硬度粉末涂料用作外观件的用途,包括以下步骤:将铝单板进行除油(或进行其他前处理如硅烷处理),在无尘室进行喷涂,之后进入烘道进行烘烤,烘烤的温度为190-220℃,时间为10~20min,烘烤加热采用高频线圈加热;待涂层充分固化后自然冷却。对涂层进行硬度测试,最高可以达到铅笔硬度4h(按gb/t63792006),说明所述涂层硬度性能优异。实施例6一种高硬度粉末涂料,包括以下重量份的组分:首先,按照所述高硬度粉末涂料组分的配方组成精确的称量原材料,在预混罐里经过高速旋转混合均匀(预混时间5-10分钟),然后把混合均匀的生料匀速放入双螺杆挤出机,在95-105℃条件下熔融挤出,经过冷却辊压成料片,料片在自然温度下冷却后,使用粉碎机对料片进行粗破碎,得到的物料冷却后使用粉碎机进行磨细粉碎,使用180目筛网进行筛分,180目筛网过筛的筛分自然冷却,最后得到粒径均匀(26-70μm)的所述高硬度粉末涂料。本实施例的高硬度粉末涂料用作外观件的用途,包括以下步骤:将铝单板进行除油(或进行其他前处理如硅烷处理),在无尘室进行喷涂,之后进入烘道进行烘烤,烘烤的温度为190-220℃,时间为10~20min,烘烤加热采用高频线圈加热;待涂层充分固化后自然冷却。对涂层进行硬度测试,最高可以达到铅笔硬度4h(按gb/t63792006),说明所述涂层硬度性能优异。本发明中如聚氨酯树脂用量在20份以下(19份或更低)或降低异氰酸脂二聚体到25份以下(24份或更低),会导致烘烤后涂层的硬度性能下降,不能满足铅笔硬度达到4h的要求,以上两组分的含量过高会导致成本增加。本发明通过选用合适的原料和原料配比,使得涂料涂层和基材的附着力达到最好,涂料对于基材的粘结性能好、硬度性能好。当各组份原料用量过少,则附着力和硬度性会受到影响,若过多成本会增加且影响其硬度性。本发明的高硬度粉末涂料对于基材的硬度性能优秀,高硬度粉末涂料和基材的附着力达到最好,对于基材的粘结性能好、硬度性能好,具有很好的耐刮擦效果,避免了因涂层受外力刮擦而导致涂层的性能不良问题的发生;在应用到外观件时,可在现有户外粉末产品喷涂工艺基础上进行,不改变现场喷涂工艺;对本发明的高硬度粉末涂料的涂层进行硬度测试,结果表明该产品可以达到铅笔硬度4h(按gb/t63792006),涂层的硬度性能好。显然,本发明的上述实施例仅仅是为清楚地说明本发明所作的举例,而并非是对本发明的实施方式的限定,对于所属领域的普通技术人员来说,在上述说明的基础上还可以做出其它不同形式的变化或变动,本发明所例举的实施例无法对所有的实施方式予以穷尽,凡是属于本发明的技术方案所引伸出的显而易见的变化或变动仍处于本发明的保护范围之列。在本发明中提及的所有文献都在本申请中引用作为参考,就如同一篇文献被单独引用为参考那样。当前第1页12