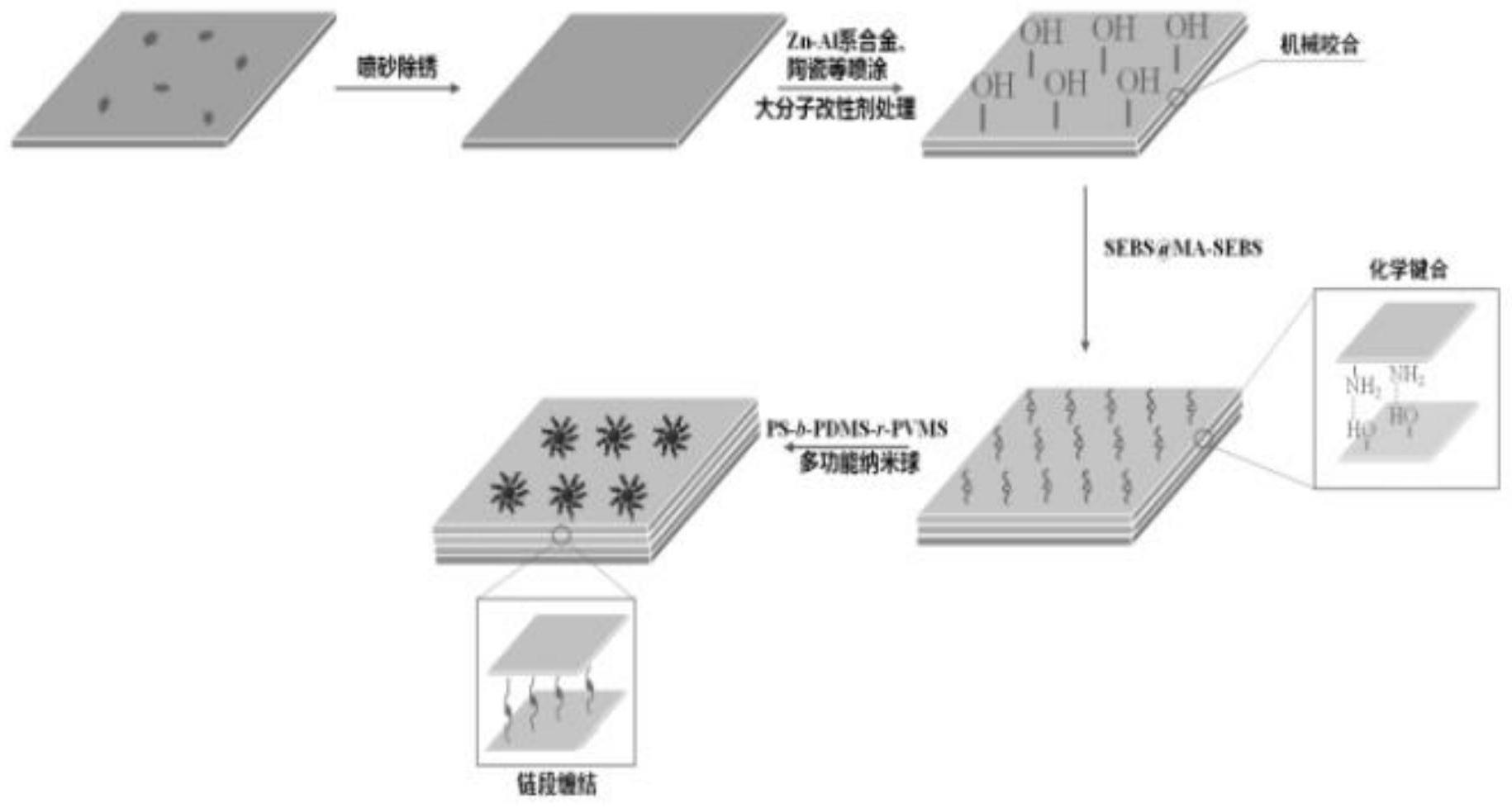
1.本发明涉及防腐材料制备技术领域,尤其是涉及一种海洋抗污防腐涂层及其喷涂工艺。
背景技术:2.海洋生物在装备表面的淤积过程一般可分为四个阶段:基材浸入海水数分钟后表面即形成为微生物生长繁殖提供营养物质的调节膜,数小时内沉积于调节膜的细菌和藻类等微生物分泌胞外聚合物形成细菌生物膜,几天内细菌和藻类等微生物快速生长为孢子或原生物、数月内孢子和原生物生长为藻类等大型淤积生物。基于海洋生物的淤积过程和影响因素所研制的海洋防污材料,可以概略的将涂层材料划分为杀生型、自抛型、抗淤积型、淤积释放型。
3.舰船水线区和水下部位是腐蚀最容易发生且最严重的部位,其腐蚀类型主要包括:化学腐蚀、电化学腐蚀、空泡腐蚀及海洋生物腐蚀。而保护舰船免受腐蚀的方法有许多,例如耐蚀材料选择、涂层保护、牺牲阳极保护、外加电源保护等等,其中涂层保护是船体材料保护中最主要的措施之一。
4.下面提供一种基于涂层保护的金属件涂层以及喷涂工艺,改工艺施工方便、易于维护、操作简单,结合机械咬合
‑
化学键合
‑
物理缠结的共同作用使得涂装效果以及整体的结构强度得到有效提高,满足船只的实用需求。
技术实现要素:5.所以,本发明的目的是提供一种新型的船体涂层结构以及喷涂工艺,帮助提高现有船只结构部件的抗污耐腐蚀性能。
6.本发明通过以下技术方案来实现上述目的:一种海洋抗污防腐涂层:包括金属
‑
陶瓷基础层、sebs结构层以及ps
‑
b
‑
pdms
‑
r
‑
pvms/mnps@laf活性层;
7.金属
‑
陶瓷基础层:所述金属
‑
陶瓷基础层以锌铝
‑
陶瓷复合合金丝材为金属基板,将zn
‑
al系合金为主要成分,以tio2、sio2、稀土氧化物为辅助成分,喷涂至所述基板上,得到金属
‑
陶瓷基础层;
8.sebs结构层:在所述金属
‑
陶瓷基础层表面上涂覆大分子偶联剂,所述金属陶瓷基础层表面的
‑
oh与大分子偶联剂一端的硅羟基有机结合,大分子偶联剂另一端的环氧基团和氨基与所述金属
‑
陶瓷基础层中的马来酸酐化的sebs键合,得到sebs结构层;
9.ps
‑
b
‑
pdms
‑
r
‑
pvms/mnps@laf活性层:以ps
‑
b
‑
pdms
‑
r
‑
pvms嵌段聚合物为基体、以~100nm、单分散mnps@laf纳米微球为添加剂制成的复合材料,将嵌段聚合物ps
‑
b
‑
pdms
‑
r
‑
pvms溶解于乙酸乙酯中,与吸附了小分子的feco/明胶纳米球均匀混合,其涂覆在sebs结构层涂层上,得到ps
‑
b
‑
pdms
‑
r
‑
pvms/mnps@laf活性层;
10.通过在所述金属
‑
陶瓷基础层上设置所述sebs结构层,并于所述sebs结构层的基础上设置所述ps
‑
b
‑
pdms
‑
r
‑
pvms/mnps@laf活性层的方式,得到抗污防腐涂层。
11.一种海洋抗污防腐涂层的喷涂工艺:
12.步骤一:以基板为基础,将基板进行净化及喷砂处理;处理后的表面清洁度达sa3,粗糙度达到rz25
‑
100μm;
13.喷砂工艺参数为:
14.磨料选择铸铁砂,粒径为0.5mm~1.5mm,磨料要求有棱角、清洁、干燥、没有油污;
15.喷射处理所有的压缩空气经过冷却装置及油水分离器处理,以保证压缩空气的干燥、无油、压缩空气压力为0.7mpa;
16.喷嘴到基体金属表面保持100mm~300mm的距离;
17.喷射方向与基体金属表面法线的夹角控制在15~30
°
范围;
18.表面预处理后,用干燥、无油的压缩空气清除浮尘和碎屑,清理后的表面不得用手触摸。
19.步骤二:在步骤一处理好后的基板表面等离子喷涂zn
‑
al系合金,然后再将cr2o3、al2o3、tio2、sio2和稀土氧化物为陶瓷层原料,比例为2:3:2:1:2,等离子喷涂至金属层上,得到带有金属
‑
陶瓷基础层的基板;
20.步骤三:以乙酸乙酯作为溶剂,配制浓度比为1:1:2的sebs(氢化苯乙烯
‑
丁二烯嵌段共聚物)、ma
‑
sebs(马来酸酐化sebs)和大分子偶联剂(c8h22o3n2si)的混合溶液,然后在步骤二处理好的基板表面采用增压泵将涂料增至高压(压160
‑
280kg/cm2)喷涂50μm,大分子偶联剂上的硅羟基与金属
‑
陶瓷基础层表面的
‑
oh有机结合、环氧基团和氨基与金属
‑
陶瓷基础层中的马来酸酐化的sebs键合,使得sebs生长于金属
‑
陶瓷材料表面,得到sebs结构层;
21.步骤四:配置溶解有嵌段聚合物ps
‑
b
‑
pdms
‑
r
‑
pvms的乙酸乙酯溶液,乙酸乙酯溶液浓度为10mol/l,将配置好的乙酸乙酯溶液与吸附了小分子的feco/明胶纳米球均匀混合,然后涂覆在步骤三处理好的基板表面厚度为30μm,完成整体喷涂。
22.进一步的,所述金属
‑
陶瓷基础层以锌铝
‑
陶瓷复合合金丝材为金属基板,对所述基板进行净化、喷砂处理,以zn
‑
ni系合金为金属层材料,以cr2o3、al2o3、tio2、sio2和稀土氧化物为陶瓷层原料,将所述金属层材料电弧喷涂至所述基板表面后再电弧喷涂陶瓷层原料,得到金属层、陶瓷层双层基础层。
23.进一步的,所述zn
‑
ni余量为20%~35%,所述cr2o3、al2o3、tio2、sio2和稀土氧化物的质量比为2:3:2:1:2。
24.本发明的有益效果在于:在船体钢铁或铝基体上采用大功率超音速电弧喷涂zn
‑
al系金属
‑
陶瓷合金丝材或铝锌包覆多种陶瓷形成的复合粉末芯丝形成的牢固结合防腐涂层作基础,再在喷涂层层状结构的特有的粗糙表面涂覆与之适应匹配,相容性好的低表面能涂料,获得结合强度高,耐腐、抗污、抗冲刷效果一体化的涂层结构,涂层材料易实现工业化制备,前处理、复合涂层制备技术成型配套,可实现船台与现场的再制造与快速修复。
附图说明
25.图1是涂层结构示意图;
26.图2是基础涂层截面;
27.图3是涂层截面;
具体实施方式
28.下面将结合本发明实施例中的附图,对本发明实施例中的技术方案进行清楚、完整地描述,显然,所描述的实施例仅仅是本发明一部分实施例,而不是全部的实施例。基于本发明中的实施例,本领域普通技术人员在没有做出创造性劳动前提下所获得的所有其他实施例,都属于本发明保护的范围。
29.在本发明的描述中,需要理解的是,术语“纵向”、“横向”、“长度”、“宽度”、“厚度”、“上”、“下”、“前”、“后”、“左”、“右”、“竖直”、“水平”、“顶”、“底”、“内”、“外”等指示的方位或位置关系为基于附图所示的方位或位置关系,仅是为了便于描述本发明和简化描述,而不是指示或暗示所指的装置或元件必须具有特定的方位、以特定的方位构造和操作,因此不能理解为对本发明的限制。
30.结合图1
‑
图3所示的下面将结合本发明中的实施例,对本发明实施例中的技术方案进行清楚、完整地描述,显然,所描述的实施例仅仅是本发明一部分实施例,而不是全部的实施例。基于本发明中的实施例,本领域普通技术人员在没有做出创造性劳动前提下所获得的所有其他实施例,都属于本发明保护的范围。
31.实施例一:
32.本发明提供的一种海洋抗污防腐涂层,包括金属
‑
陶瓷基础层、sebs结构层以及ps
‑
b
‑
pdms
‑
r
‑
pvms/mnps@laf活性层,将船体金属板进行常规的净化、喷砂处理,将金属
‑
陶瓷材料喷涂于金属基材表面;采用大分子改性剂对金属
‑
陶瓷材料进行喷涂处理,使其与金属
‑
陶瓷中的sio2、tio2等的化学键合,并与酸酐化的sebs化合,使sebs生长于金属
‑
陶瓷材料表面;最后通过链段缠结与浓度扩散作用,将ps
‑
b
‑
pdms
‑
r
‑
pvms/mnps@laf活性层构筑于涂层表面。
33.金属
‑
陶瓷基础层:基础层以锌铝
‑
陶瓷复合合金丝材为金属基板,将zn
‑
al系合金为主要成分,以tio2、sio2、稀土氧化物为辅助成分,喷涂至基板上,得到金属
‑
陶瓷基础层,;
34.sebs结构层:在基础层表面上涂覆大分子偶联剂,金属陶瓷基础层表面的
‑
oh与大分子偶联剂一端的硅羟基有机结合,大分子偶联剂另一端的环氧基团和氨基与金属
‑
陶瓷基础层中的马来酸酐化的sebs键合,得到sebs结构层;
35.ps
‑
b
‑
pdms
‑
r
‑
pvms/mnps@laf活性层:以ps
‑
b
‑
pdms
‑
r
‑
pvms嵌段聚合物为基体、以~100nm、单分散mnps@laf纳米微球为添加剂制成的复合材料,将嵌段聚合物ps
‑
b
‑
pdms
‑
r
‑
pvms溶解于乙酸乙酯中,与吸附了小分子的feco/明胶纳米球均匀混合,其涂覆在结构层涂层上,得到ps
‑
b
‑
pdms
‑
r
‑
pvms/mnps@laf活性层;
36.通过在基础层上设置结构层,并于结构层的基础上设置活性层的方式,得到抗污防腐涂层。
37.一种海洋抗污防腐涂层的喷涂工艺:
38.步骤一:以基板为基础,将基板进行净化及喷砂处理;处理后的表面清洁度达sa3,粗糙度达到rz25
‑
100μm。
39.喷砂工艺参数
40.磨料选择铸铁砂,粒径为0.5mm~1.5mm,磨料要求有棱角、清洁、干燥、没有油污;
41.喷射处理所有的压缩空气经过冷却装置及油水分离器处理,以保证压缩空气的干
燥、无油、压缩空气压力为0.7mpa;
42.喷嘴到基体金属表面保持100mm~300mm的距离;
43.喷射方向与基体金属表面法线的夹角控制在15~30
°
范围;
44.表面预处理后,用干燥、无油的压缩空气清除浮尘和碎屑,清理后的表面不得用手触摸。
45.步骤二:在步骤一处理好后的基板表面等离子喷涂zn
‑
al系合金,然后再将cr2o3、al2o3、tio2、sio2和稀土氧化物为陶瓷层原料,比例为2:3:2:1:2,等离子喷涂至金属层上,得到带有金属
‑
陶瓷基础层的基板;
46.步骤三:以乙酸乙酯作为溶剂,配制浓度比为1:1:2的sebs(氢化苯乙烯
‑
丁二烯嵌段共聚物)、ma
‑
sebs(马来酸酐化sebs)和大分子偶联剂(c8h22o3n2si)的混合溶液,然后在步骤二处理好的基板表面采用增压泵将涂料增至高压(压160
‑
280kg/cm2)喷涂50μm,大分子偶联剂上的硅羟基与金属
‑
陶瓷基础层表面的
‑
oh有机结合、环氧基团和氨基与金属
‑
陶瓷基础层中的马来酸酐化的sebs键合,使得sebs生长于金属
‑
陶瓷材料表面,得到sebs结构层;
47.步骤四:配置溶解有嵌段聚合物ps
‑
b
‑
pdms
‑
r
‑
pvms的乙酸乙酯溶液,乙酸乙酯溶液浓度为10mol/l,将配置好的乙酸乙酯溶液与吸附了小分子的feco/明胶纳米球均匀混合,然后涂覆在步骤三处理好的基板表面厚度为30μm,完成整体喷涂。
48.其中,具体喷涂参数为:金属层喷涂参数:工作电流400,ar气流量0.55l/min,n2气流量0.3l/min,h2气流量0.15l/min,合金粉送粉速率80g/min,喷涂厚度150μm;
49.陶瓷层喷涂参数:工作电流500,ar气流量0.55l/min,n2气流量0.3l/min,h2气流量0.25l/min,合金粉送粉速率75g/min,喷涂厚度120μm。
50.金属
‑
陶瓷基础层以锌铝
‑
陶瓷复合合金丝材为金属基板,对基板进行净化、喷砂处理,以zn
‑
ni系合金为金属层材料,以cr2o3、al2o3、tio2、sio2和稀土氧化物为陶瓷层原料,将金属层材料电弧喷涂至基板表面后再电弧喷涂陶瓷层原料,得到金属层、陶瓷层双层基础层。
51.zn
‑
ni余量为20%~35%,cr2o3、al2o3、tio2、sio2和稀土氧化物的质量比为2:3:2:1:2。
52.实施例二:
53.一种海洋抗污防腐涂层的喷涂工艺:
54.步骤一:以基板为基础,将基板进行净化及喷砂处理;处理后的表面清洁度达sa3,粗糙度达到rz25
‑
100μm。
55.喷砂工艺参数
56.磨料选择铸铁砂,粒径为0.5mm,磨料要求有棱角、清洁、干燥、没有油污;
57.喷射处理所有的压缩空气经过冷却装置及油水分离器处理,以保证压缩空气的干燥、无油、压缩空气压力为0.7mpa;
58.喷嘴到基体金属表面保持100mm的距离;
59.喷射方向与基体金属表面法线的夹角控制在15范围;
60.表面预处理后,用干燥、无油的压缩空气清除浮尘和碎屑,清理后的表面不得用手触摸。
61.步骤二:在步骤一处理好后的基板表面等离子喷涂zn
‑
al系合金,然后再将cr2o3、al2o3、tio2、sio2和稀土氧化物为陶瓷层原料,比例为2:3:2:1:2,等离子喷涂至金属层上,得到带有金属
‑
陶瓷基础层的基板;
62.步骤三:以乙酸乙酯作为溶剂,配制浓度比为1:1:2的sebs(氢化苯乙烯
‑
丁二烯嵌段共聚物)、ma
‑
sebs(马来酸酐化sebs)和大分子偶联剂(c8h22o3n2si)的混合溶液,然后在步骤二处理好的基板表面采用增压泵将涂料增至高压(压160
‑
280kg/cm2)喷涂60μm,大分子偶联剂上的硅羟基与金属
‑
陶瓷基础层表面的
‑
oh有机结合、环氧基团和氨基与金属
‑
陶瓷基础层中的马来酸酐化的sebs键合,使得sebs生长于金属
‑
陶瓷材料表面,得到sebs结构层;
63.步骤四:配置溶解有嵌段聚合物ps
‑
b
‑
pdms
‑
r
‑
pvms的乙酸乙酯溶液,乙酸乙酯溶液浓度为10mol/l,将配置好的乙酸乙酯溶液与吸附了小分子的feco/明胶纳米球均匀混合,然后涂覆在步骤三处理好的基板表面厚度为35μm,完成整体喷涂。
64.其中,具体喷涂参数为:金属层喷涂参数:工作电流400,ar气流量0.55l/min,n2气流量0.3l/min,h2气流量0.15l/min,合金粉送粉速率80g/min,喷涂厚度150μm;
65.陶瓷层喷涂参数:工作电流500,ar气流量0.55l/min,n2气流量0.3l/min,h2气流量0.25l/min,合金粉送粉速率75g/min,喷涂厚度120μm。
66.金属
‑
陶瓷基础层以锌铝
‑
陶瓷复合合金丝材为金属基板,对基板进行净化、喷砂处理,以zn
‑
ni系合金为金属层材料,以cr2o3、al2o3、tio2、sio2和稀土氧化物为陶瓷层原料,将金属层材料电弧喷涂至基板表面后再电弧喷涂陶瓷层原料,得到金属层、陶瓷层双层基础层。
67.zn
‑
ni余量为20%~35%,cr2o3、al2o3、tio2、sio2和稀土氧化物的质量比为2:3:2:1:2。
68.实施例三:
69.一种海洋抗污防腐涂层的喷涂工艺:
70.步骤一:以基板为基础,将基板进行净化及喷砂处理;处理后的表面清洁度达sa3,粗糙度达到rz25
‑
100μm。
71.喷砂工艺参数
72.磨料选择铸铁砂,粒径为1mm,磨料要求有棱角、清洁、干燥、没有油污;
73.喷射处理所有的压缩空气经过冷却装置及油水分离器处理,以保证压缩空气的干燥、无油、压缩空气压力为0.7mpa;
74.喷嘴到基体金属表面保持200mm的距离;
75.喷射方向与基体金属表面法线的夹角控制在15范围;
76.表面预处理后,用干燥、无油的压缩空气清除浮尘和碎屑,清理后的表面不得用手触摸。
77.步骤二:在步骤一处理好后的基板表面等离子喷涂zn
‑
al系合金,然后再将cr2o3、al2o3、tio2、sio2和稀土氧化物为陶瓷层原料,比例为2:3:2:1:2,等离子喷涂至金属层上,得到带有金属
‑
陶瓷基础层的基板;
78.步骤三:以乙酸乙酯作为溶剂,配制浓度比为1:1:2的sebs(氢化苯乙烯
‑
丁二烯嵌段共聚物)、ma
‑
sebs(马来酸酐化sebs)和大分子偶联剂(c8h22o3n2si)的混合溶液,然后在
步骤二处理好的基板表面采用增压泵将涂料增至高压(压160
‑
280kg/cm2)喷涂50μm,大分子偶联剂上的硅羟基与金属
‑
陶瓷基础层表面的
‑
oh有机结合、环氧基团和氨基与金属
‑
陶瓷基础层中的马来酸酐化的sebs键合,使得sebs生长于金属
‑
陶瓷材料表面,得到sebs结构层;
79.步骤四:配置溶解有嵌段聚合物ps
‑
b
‑
pdms
‑
r
‑
pvms的乙酸乙酯溶液,乙酸乙酯溶液浓度为10mol/l,将配置好的乙酸乙酯溶液与吸附了小分子的feco/明胶纳米球均匀混合,然后涂覆在步骤三处理好的基板表面厚度为30μm,完成整体喷涂。
80.其中,具体喷涂参数为:金属层喷涂参数:工作电流400,ar气流量0.55l/min,n2气流量0.3l/min,h2气流量0.15l/min,合金粉送粉速率80g/min,喷涂厚度150μm;
81.陶瓷层喷涂参数:工作电流500,ar气流量0.55l/min,n2气流量0.3l/min,h2气流量0.25l/min,合金粉送粉速率75g/min,喷涂厚度120μm。
82.金属
‑
陶瓷基础层以锌铝
‑
陶瓷复合合金丝材为金属基板,对基板进行净化、喷砂处理,以zn
‑
ni系合金为金属层材料,以cr2o3、al2o3、tio2、sio2和稀土氧化物为陶瓷层原料,将金属层材料电弧喷涂至基板表面后再电弧喷涂陶瓷层原料,得到金属层、陶瓷层双层基础层。
83.zn
‑
ni余量为20%~35%,cr2o3、al2o3、tio2、sio2和稀土氧化物的质量比为2:3:2:1:2。
84.对于本领域技术人员而言,显然本发明不限于上述示范性实施例的细节,而且在不背离本发明的精神或基本特征的情况下,能够以其他的具体形式实现本发明。因此,无论从哪一点来看,均应将实施例看作是示范性的,而且是非限制性的,本发明的范围由所附权利要求而不是上述说明限定,因此旨在将落在权利要求的等同要件的含义和范围内的所有变化囊括在本发明内。不应将权利要求中的任何附图标记视为限制所涉及的权利要求。
85.此外,应当理解,虽然本说明书按照实施方式加以描述,但并非每个实施方式仅包含一个独立的技术方案,说明书的这种叙述方式仅仅是为清楚起见,本领域技术人员应当将说明书作为一个整体,各实施例中的技术方案也可以经适当组合,形成本领域技术人员可以理解的其他实施方式。