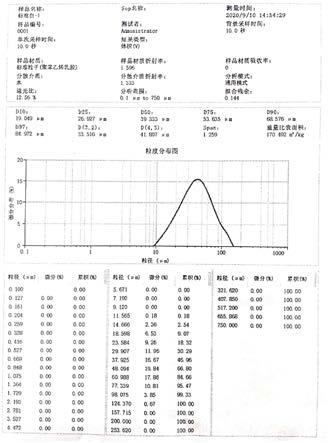
1.本发明涉及一种热固性粉末涂料,具体涉及一种不含尘的热固性粉末涂料及制备方法。
背景技术:2.热固性粉末涂料因其voc零排放,被认为最环保的涂料之一。现今相关部门都非常支持 热固性粉末涂料的发展,推行建设部门铝合金门窗指定采用热固性粉末涂料、环保涂料免消 费税等,特别现今国家大力提倡油漆改粉末(油改粉)。
3.但是热固性粉末涂料也有环保弊端,其会产生大量的粉尘,热固性粉末涂料含有大量粉 尘(pm2.5,pm10)颗粒物。现有技术针对该问题采用的的方法都是过滤、集尘、增加个人防 护,但是效果均不理想。
4.因此,需要对现有技术进行改进。
技术实现要素:5.本发明要解决的技术问题是提供一种高效的不含尘的热固性粉末涂料及制备方法。
6.为解决上述技术问题,本发明提供一种不含尘的热固性粉末涂料,按重量份数计包括以 下组分:
7.树脂50
‑
60份、偶联剂0.5
‑
1.5份、固化剂4
‑
5份、颜料10
‑
20份、助剂6
‑
8份和填料15
‑
20 份。
8.作为对本发明不含尘的热固性粉末涂料的改进:
9.所述树脂采用端羟基不饱和聚酯树脂;
10.所述偶联剂采用硅烷偶联剂;
11.所述固化剂选自异氰尿酸三缩水甘油酯、多元苯甲酸缩水甘油酯中的一种或多种;
12.所述颜料为造粒碳黑;
13.所述助剂为流平剂、脱气剂、松散剂、抗氧化剂、消泡剂中的一种或几种以上混合;
14.所述填料为硬酯酸。
15.作为对本发明不含尘的热固性粉末涂料的改进:
16.树脂为55份,偶联剂为1份,固化剂4.5份,助剂为7份,颜料为15份,填料为17.5 份。
17.作为对本发明不含尘的热固性粉末涂料的改进:
18.所述树脂的粒径为10微米以上;
19.所述偶联剂为液体;
20.所述固化剂的粒径为10微米以上;
21.所述助剂的粒径为10微米以上;
22.所述颜料的粒径为10微米以上;
23.所述硬酯酸的粒径为10微米以上。
24.本发明还提供一种不含尘的热固性粉末涂料制备方法,包括以下步骤:
25.步骤1)、配料,按配方配料;
26.步骤2)、研磨,调节磨粉喂料速度,磨盘转速,出料速度;
27.步骤3)、旋风分离时,加大离心力,去除大部分细尘;
28.步骤4)、超声波振动筛,把剩余的小部分的漏网细尘筛选出去;
29.步骤5)、激光粒度分析仪检测是否合格。
30.作为对本发明不含尘的热固性粉末涂料制备方法的改进:
31.步骤2)包括:
32.2.1)、用变频控制喂料,缓慢均匀进料,变频控制在22
‑
27赫兹之间;
33.2.2)、磨盘速度用变频控制,变频控制在45赫兹;
34.2.3)、加快出料速度,变频控制在18
‑
20赫兹之间。
35.作为对本发明不含尘的热固性粉末涂料制备方法的改进:
36.在步骤4)中:
37.超声波振动筛,筛孔大小为大于等于12微米,如果有细粉从过筛后通道筛出来了,需要 继续调大步骤3)中的旋风分离的离心力,直至过筛后通道没有细粉出来。
38.作为对本发明不含尘的热固性粉末涂料制备方法的改进在步骤5)中:
39.激光粒度分析仪检测得到实测粒径分布,如果粒径小于10微米的颗粒含量高于0.01%, 则判定为含尘,不合格;如果粒径小于10微米的颗粒含量小于等于0.01%,则判定为不含尘, 合格。
40.本发明不含尘的热固性粉末涂料及制备方法的技术优势为:
41.本发明不含尘的热固性粉末涂料,虽然只拿掉了不到10%的超细部分(10微米以下)适 当的改变了颗粒韧性,但是,很多性能都有显著或根本改变;具体为:
42.1)、大大降低了设备acm磨的损耗,磨粉时最耗能、最消耗磨盘磨柱的不是大颗粒, 而是反复磨的最小颗粒;
43.2)、在确保大小颗粒更集中的同时,产品的一致性得到了非常明显的提高,特别是热固 性粉末涂料喷涂使用的时候,基本上没有类似于现有技术那种会掉下来的(回收粉);
44.3)、减少了集尘设备的清洁,因为本发明不含尘的热固性粉末涂料没有尘,在使用过程, 不需要像以前那样天天打扫后道集尘设备;
45.4)、高压静电喷涂可以用在死角上了,之前因为法拉第效应,带正电荷的粉末颗粒会在 死角造成(静电屏蔽),无尘粉,现有技术一直没办法解决。现在发现,采用本发明不含尘 的热固性粉末涂料,可以有效避免静电屏蔽,同样重量粉末中,带电颗粒只有现有热固性粉 末涂料的1/3,所以本发明有效解决了死角静电屏蔽;
46.5)、以前粉末涂料制备行业生产过程会制造大量灰尘,后续在涂料过程也会有大量有害 粉尘。采用本发明不含尘的热固性粉末涂料,即没有pm2.5,也没有了pm10,彻底解决了粉 尘污染的问题。
附图说明
47.下面结合附图对本发明的具体实施方式作进一步详细说明。
48.图1是现有技术热固性粉末涂料的效果示意图;
49.图2是本发明不含尘的热固性粉末涂料的效果示意图。
具体实施方式
50.下面结合具体实施例对本发明进行进一步描述,但本发明的保护范围并不仅限于此。
51.实施例1、不含尘的热固性粉末涂料,针对现有的技术缺点,设想从源头解决问题,让 粉末涂料不含尘,就是最细颗粒大于10微米(pm2.5=0,pm10=0)。
52.首先在配方上,减少细颗粒物的用量,少用或不用碳酸钙、研磨颜料、超细蜡和细碳黑 等细颗粒原料,而是用包裹性填料、颗粒性碳黑、聚合蜡、包裹性更好的树脂。
53.本发明不含尘的热固性粉末涂料,包括树脂、偶联剂、固化剂、颜料(可含细)、助剂 (可含细)、填料(可不含细)。
54.树脂采用端羟基不饱和聚酯树脂;
55.偶联剂采用硅烷偶联剂;
56.固化剂选自异氰尿酸三缩水甘油酯、多元苯甲酸缩水甘油酯中的一种或多种;
57.颜料为造粒碳黑;
58.助剂为流平剂、脱气剂、松散剂、抗氧化剂、消泡剂中的一种或几种以上混合;
59.填料为硬酯酸。
60.颜料和助剂均可以选择尘料和粗料,优选粗料效果更佳。
61.填料采用是细(尘)料,需要采用包裹性无尘料。
62.具体成分为(重量份数):
[0063][0064]
研磨后分级筛分,针对产生的少量10微米以下细颗粒,使用多次分离,加大离心力,增 加旋风分离强度,用高目数超声波筛网过筛等等,让成品不含小于10微米的细颗粒。并用激 光粒度仪检测保证其质量。
[0065]
本发明的制备方法包括以下步骤:
[0066]
步骤1)、配料,按配方配料;
[0067]
步骤2)、研磨时,降低研磨分级速度;
[0068]
研磨时,需要调节磨粉喂料速度,磨盘转速,出料速度。
[0069]
2.1)、用变频控制喂料,做到缓慢,均匀进料,变频控制在22
‑
27赫兹之间比较合
适。
[0070]
2.2)、磨盘速度也用变频控制,控制在45赫兹最佳。
[0071]
2.3)、出料(分级)一定要降低,也就是出料速度必须要快,不能在磨室内有残料,出 料速度过慢,会造成研磨时磨盘和待磨料接触时间不稳定,待分离细粉含量会忽高忽低,影 响后续处理。一般设置在18到20赫兹之间就够了。研磨后的物料,未后续分离处理前,粒 径分布已经相当稳定,10微米以下含量已经小于万分之5了。
[0072]
步骤3)、旋风分离时,加大离心力,把大部分细尘甩出去;
[0073]
旋风分离,是使用离心力,把微小颗粒去除掉的过程。为了获得最佳的微粉颗粒去除效 果,通过加大离心风机口开关,降低旋风分离长径比,加大中央细粉通道管,降低底部成品 出口密封性,加大了离心力。使得入口速度从2米每秒,增加到3米每秒,细粉抽离处从2 米每秒,增加到2.5米每秒,使得超细粉抽净率,从79%提高到99%+。
[0074]
步骤4)、超声波振动筛,把剩余的小部分(几乎没有)的漏网细尘筛选出去;
[0075]
超声波振动筛,筛孔大小为大于等于12微米,主要作用是质量保证和检验,如果有细粉 从过筛后通道筛出来了,说明还有漏网之鱼,离心力还不够大,需要继续调大旋风分离的离 心力,直至过筛后通道没有细粉出来。
[0076]
步骤5)、激光粒度分析仪,检测,确保真正无尘。
[0077]
激光粒度分析仪检测得到实测粒径分布,如果粒径小于10微米的颗粒含量高于0.01%(最 低能测出值万分之一),则判定为含尘,不合格;如果粒径小于10微米的颗粒含量小于等于 0.01%(最低能测出值万分之一),则判定为不含尘,合格。
[0078]
最后,还需要注意的是,以上列举的仅是本发明的若干个具体实施例。显然,本发明不 限于以上实施例,还可以有许多变形。本领域的普通技术人员能从本发明公开的内容直接导 出或联想到的所有变形,均应认为是本发明的保护范围。