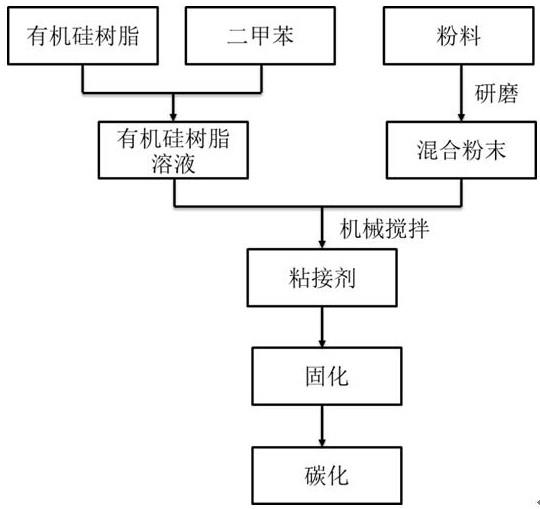
1.本发明属于碳/碳复合材料技术领域,具体涉及一种碳纤维增强碳基(c
f
/c)复合材料粘接修复方法。
背景技术:2.碳/碳复合材料具有密度低、热容高、热变形量小、抗烧蚀性能好、室温及高温力学性能优异等特点,广泛应用于先进刹车系统,热防护系统,航天飞机及火箭发动机等高温部位。然而由于c
f
/c复合材料制备周期长,成本高,且工艺复杂,因而对出现破损或已经到达使用寿命的c
f
/c复合材料构件进行修复再利用十分必要。传统修复技术(铆接、焊接或机械连接)容易对材料本身造成损伤,导致材料强度降低,同时所用修复材料重量大,造成有效载荷下降。粘接剂粘接作为一种将同质或异质物体表面连接在一起的技术,具有应力分布连续,重量轻等特点,可以有效避免传统机械连接方法所存在问题,是一种十分有效的c
f
/c复合材料修复方法。
3.c
f
/c复合材料的高温应用领域,决定了粘接剂除了具有良好的耐热性能和韧性以满足结构粘接性能要求外,还要具有优异的热传导率以满足传热要求。目前已开发出的c
f
/c复合材料用粘接剂主要分为有机和无机两种。有机粘接剂经高温热处理后形成碳粘结层或硅粘接层,在室温及低温条件下具有较高的结合强度,但由于其为单相结构,存在一定的局限性,断裂韧性低,抗热震性差。无机胶粘剂可以与c
f
/c基体反应形成具有较高结合强度的碳化物结合层,耐温性能优异,但陶瓷层与c
f
/c复合材料之间的热膨胀系数和弹性模量存在很大的不匹配,在制备温度冷却过程中会产生残余应力,导致粘接强度降低。另外,对于两种粘接剂的导热性能也鲜有报道。因此现有粘接剂很难满足c
f
/c复合材料的粘接修复需求。
技术实现要素:4.针对现有技术缺陷,本发明的目的是提供一种碳纤维增强碳基复合材料粘接修复方法及所使用的粘接剂及其制备方法,采用本发明修复的碳纤维增强碳基复合材料从室温到1800℃均具有较高的力学强度,导热性能不低于修复前材料,力学性能与修复前材料基本相同。
5.上述目的可以通过以下技术方案实现:
6.第一方面,本发明提供了一种碳纤维增强碳基复合材料粘接修复方法,包括以下步骤:
7.(1)粘接剂的配置:
8.室温25℃条件下,首先将10~15wt.%的金刚石粉末、12~15wt.%的氧化锌粉末、6~12wt.%的铜粉、10~15wt.%的钛粉、32~37wt.%的低熔点玻璃粉加入到研钵中混合研磨30分钟制成混合粉末;
9.将上述混合粉末与20~25wt.%的有机硅树脂溶液同时加入到容器(烧杯)中机械搅拌1小时,完成粘接剂的配置;所述有机硅树脂溶液由有机硅树脂与二甲苯搅拌混合制成,黏度为65~100cps;
10.(2)粘接剂的固化:
11.将上述配置好的粘接剂均匀涂抹在待修复材料的两个粘接面表面,然后将两个表面进行贴合,之后将其在大气环境下通过控制施加在材料表面压力的大小,控制胶层厚度在0.08~0.3μm,之后将其放入鼓风烘箱中以5℃/小时的速率升温至250℃后保温2小时完成粘接剂的固化,整个固化期间通过给材料施加压力将胶层厚度控制在0.08μm~0.3μm;
12.(3)粘接剂的碳化:
13.将固化后的材料放入高温真空设备中,在
‑
0.1mpa的真空环境下以100℃/小时的速率升温至1200℃后保温2小时完成粘接剂的碳化。
14.所述步骤(1)中金刚石粉末粒度为460~650目;氧化锌粉末粒度为270~325目;铜粉目数为200~325目;钛粉目数为200~325目;低熔点玻璃粉目数为1500~3000目,熔点为700~750℃。
15.所述有机硅树脂为聚甲基苯基硅氧烷;所述二甲苯的纯度为分析纯。
16.第二方面,本发明提供了一种高导热耐高温粘接剂,所述粘接剂由以下方法制成:
17.室温25℃条件下,首先将10~15wt.%的金刚石粉末、12~15wt.%的氧化锌粉末、6~12wt.%的铜粉、10~15wt.%的钛粉、32~37wt.%的低熔点玻璃粉加入到研钵中混合研磨30分钟制成混合粉末;
18.将上述混合粉末与20~25wt.%的有机硅树脂溶液同时加入到容器(烧杯)中机械搅拌1小时,完成粘接剂的配置;所述有机硅树脂溶液由有机硅树脂与二甲苯搅拌混合制成,黏度为65~100cps。
19.所述金刚石粉末粒度为460~650目;氧化锌粉末粒度为270~325目;铜粉目数为200~325目;钛粉目数为200~325目;低熔点玻璃粉目数为1500~3000目,熔点为700~750℃。
20.所述有机硅树脂为聚甲基苯基硅氧烷;所述二甲苯的纯度为分析纯。
21.本发明的粘接剂具有优异的室温及高温粘接强度和耐热震性能,并且粘接修复后的材料室温导热系数高于22.31w/(m
·
k),在c
f
/c复合材料领域内具有广泛的实用价值和应用前景。
22.第三方面,本发明提供了一种高导热耐高温粘接剂的制备方法,包括如下步骤:
23.室温25℃条件下,首先将10~15wt.%的金刚石粉末、12~15wt.%的氧化锌粉末、6~12wt.%的铜粉、10~15wt.%的钛粉、32~37wt.%的低熔点玻璃粉加入到研钵中混合研磨30分钟制成混合粉末;
24.将上述混合粉末与20~25wt.%的有机硅树脂溶液同时加入到容器(烧杯)中机械搅拌1小时,完成粘接剂的配置;所述有机硅树脂溶液由有机硅树脂与二甲苯搅拌混合制成,黏度为65~100cps。
25.所述金刚石粉末粒度为460~650目;氧化锌粉末粒度为270~325目;铜粉目数为200~325目;钛粉目数为200~325目;低熔点玻璃粉目数为1500~3000目,熔点为700~750℃。
26.所述有机硅树脂为聚甲基苯基硅氧烷;所述二甲苯的纯度为分析纯。
27.第四方面,本发明提供了上述高导热耐高温粘接剂在碳纤维增强碳基复合材料修复中的应用。
28.本发明的高导热耐高温粘接剂的优点和积极效果在于其不仅具有良好的室温和高温粘接强度,同时还拥有优异的导热性能,具体表现在:
29.1)采用本发明粘接修复后的种碳纤维增强碳基(c
f
/c)复合材料室温粘接强度为11.6~13.0mpa,失效模式为本体断裂;
30.2)采用本发明粘接后的c
f
/c复合材料分别在300℃、700℃、1100℃以及1500℃下累积处理50小时后,胶层处没有发现孔隙和裂纹等缺陷,其粘接强度为11.6~13.0mpa,相比室温粘接强度无衰减,失效模式仍为本体材料断裂;
31.3)采用本发明粘接后的c
f
/c复合材料在1800℃下累积处理20小时后粘接样品没有裂开,其粘接强度为6.8~7.5mpa,说明该粘接剂具有优异的耐热性能;
32.4)采用本发明粘接后的c
f
/c复合材料在室温(25℃)、700℃和1000℃下的导热系数分别为22.31~25.35w/(m
·
k)、20.86~21.56w/(m
·
k)和17.68~19.15w/(m
·
k),与c
f
/c复合材料的导热系数相当。
附图说明
33.图1是本发明粘接修复方法的流程图。
具体实施方式
34.下面结合附图和实施例对本发明做进一步说明。
35.实施例1:
36.本实施例提供一种碳纤维增强碳基复合材料粘接修复方法,包括以下步骤:
37.(1)室温25℃条件下,首先将10wt.%的金刚石粉末,12wt.%的氧化锌粉末,10wt.%的铜粉,15wt.的钛粉和33wt.%的低熔点玻璃粉加入到研钵中研磨30分钟制成混合粉末,然后将有机硅树脂与适量二甲苯搅拌混合,制成黏度为80cps的有机硅树脂溶液,最后将20wt.%的有机硅树脂溶液与混合粉末同时加入到烧杯中机械搅拌1小时。其中金刚石粉末粒度为460目;氧化锌粉末粒度为325目;铜粉目数为325目;钛粉目数为325目;低熔点玻璃粉目数为1500~3000目,熔点为700~750℃;有机硅树脂为聚甲基苯基硅氧烷;二甲苯纯度为分析纯。
38.(2)将粘接剂均匀涂抹在两个粘接面表面,然后将两个表面进行贴合,之后将其在大气环境下通过控制施加在材料表面压力的大小,控制胶层厚度为0.12μm,之后将其放入鼓风烘箱中以5℃/小时的速率升温至250℃后保温2小时。
39.(3)将固化后的材料放入高温真空设备中,在
‑
0.1mpa的真空环境下以100℃/小时的速率升温至1200℃后保温2小时。
40.采用实施例1粘接修复后的c
f
/c复合材料:
41.室温粘接强度为12.5mpa,失效模式为c
f
/c复合材料本体断裂;
42.在300℃、700℃、1100℃以及1500℃下累积处理50小时后,胶层处没有发现孔隙和裂纹等缺陷,其粘接强度为12.6mpa,相比室温粘接强度无衰减,失效模式仍为本体材料断
裂;
43.在1800℃下累积处理20小时后粘接样品没有裂开,其粘接强度为7.2mpa,具有优异的耐热性能;
44.在室温(25℃)、700℃和1000℃下的导热系数分别为23.54w/(m
·
k)、21.23w/(m
·
k)和18.56w/(m
·
k),与c
f
/c复合材料的导热系数相当。
45.以上粘接性能的测试方法如下:
46.室温粘接强度:通过在万能电子试验机上采用“短梁法”测试试样的剪切性能来衡量的;
47.耐热性能:将粘接好的试样放入管式炉内,在氩气保护气氛下于测试温度点保温相应的时间,然后将其冷却到室温进行粘接性能测试;
48.导热系数:将粘接好的试样放入德国耐驰公司生产的lfa427ht型激光导热仪中,在真空环境下测得其导热系数。
49.实施例2:
50.本实施例提供一种碳纤维增强碳基复合材料粘接修复方法,包括以下步骤:
51.(1)室温25℃条件下,首先将10wt.%的金刚石粉末,10wt.%的氧化锌粉末,10wt.%的铜粉,10wt.的钛粉和35wt.%的低熔点玻璃粉加入到研钵中研磨30分钟制成混合粉末,然后将有机硅树脂与适量二甲苯搅拌混合,制成黏度为100cps的有机硅树脂溶液,最后将25wt.%的有机硅树脂溶液与混合粉末同时加入到烧杯中机械搅拌1小时,完成粘接剂的配置。其中金刚石粉末粒度为460目;氧化锌粉末粒度为325目;铜粉目数为325目;钛粉目数为325目;低熔点玻璃粉目数为1500目;有机硅树脂为聚甲基苯基硅氧烷;二甲苯纯度为分析纯。
52.(2)将粘接剂均匀涂抹在两个粘接面表面,然后将两个表面进行贴合,之后将其在大气环境下通过控制施加在材料表面压力的大小,控制胶层厚度为0.15μm,之后将其放入鼓风烘箱中以5℃/小时的速率升温至250℃后保温2小时。
53.(3)将固化后的材料放入高温真空设备中,在
‑
0.1mpa的真空环境下以100℃/小时的速率升温至1200℃后保温2小时完成粘接剂的碳化。
54.采用实施例2粘接修复后的c
f
/c复合材料:
55.室温粘接强度为13.0mpa,失效模式为c
f
/c复合材料本体断裂;
56.在300℃、700℃、1100℃以及1500℃下累积处理50小时后,胶层处没有发现孔隙和裂纹等缺陷,其粘接强度为13.0mpa,相比室温粘接强度无衰减,失效模式仍为本体材料断裂;
57.在1800℃下累积处理20小时后粘接样品没有裂开,其粘接强度为7.1mpa,具有优异的耐热性能;
58.在室温(25℃)、700℃和1000℃下的导热系数分别为22.31w/(m
·
k)、20.97w/(m
·
k)和17.90w/(m
·
k),与c
f
/c复合材料的导热系数相当。
59.以上粘接性能的测试方法与实施例1相同。
60.实施例3:
61.本实施例提供一种碳纤维增强碳基复合材料粘接修复方法,包括以下步骤:
62.(1)室温25℃条件下,首先将13wt.%的金刚石粉末,12wt.%的氧化锌粉末,
8wt.%的铜粉,10wt.%的钛粉和32wt.%的低熔点玻璃粉加入到研钵中研磨30分钟制成混合粉末,然后将有机硅树脂与适量二甲苯搅拌混合,制成黏度为85cps的有机硅树脂溶液,最后将25wt.%的有机硅树脂溶液与混合粉末同时加入到烧杯中机械搅拌1小时,完成粘接剂的配置。其中金刚石粉末粒度为650目;氧化锌粉末粒度为270目;铜粉目数为200目;钛粉目数为325目;低熔点玻璃粉目数为1500目;有机硅树脂为聚甲基苯基硅氧烷;二甲苯纯度为分析纯。
63.(2)将粘接剂均匀涂抹在两个粘接面表面,然后将两个表面进行贴合,之后将其在大气环境下通过控制施加在材料表面压力的大小,控制胶层厚度为0.08μm,之后将其放入鼓风烘箱中以5℃/小时的速率升温至250℃后保温2小时。
64.(3)将固化后的材料放入高温真空设备中,在
‑
0.1mpa的真空环境下以100℃/小时的速率升温至1200℃后保温2小时。
65.采用实施例3粘接修复后的c
f
/c复合材料:
66.室温粘接强度为12.9mpa,失效模式为c
f
/c复合材料本体断裂;
67.在300℃、700℃、1100℃以及1500℃下累积处理50小时后,胶层处没有发现孔隙和裂纹等缺陷,其粘接强度为12.9mpa,相比室温粘接强度无衰减,失效模式仍为本体材料断裂;
68.在1800℃下累积处理20小时后粘接样品没有裂开,其粘接强度为7.1mpa,具有优异的耐热性能;
69.在室温(25℃)、700℃和1000℃下的导热系数分别为24.68w/(m
·
k)、21.12w/(m
·
k)和19.03w/(m
·
k),与c
f
/c复合材料的导热系数相当。
70.以上粘接性能的测试方法与实施例1相同。