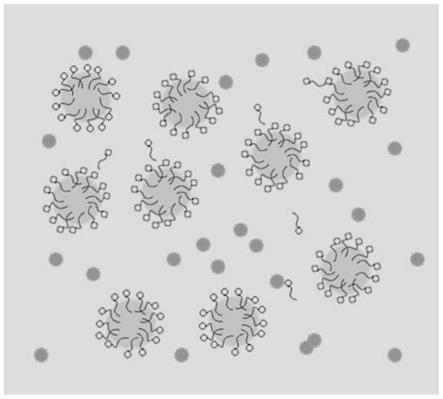
1.本发明涉及一种基于压力差渗入工件微小孔隙内部,发生厌氧聚合反应封堵工件孔隙的渗透密封胶,尤其是含功能型丙烯酸酯单体和其他助剂组成的循环回收复用型厌氧渗透密封胶。
背景技术:2.目前,常见的渗透密封胶为较低粘度的液态功能型丙烯酸酯单体混合物,依靠专用设备产生的压力差渗入金属铸件微小缺陷的内部,通过加热手段引发丙烯酸酯在微小孔隙内部的聚合固化,达到封堵工件缺陷的目的。渗透密封胶渗入工件微小孔隙内部的同时,会粘附于工件表面、型腔、螺纹孔等处,需在引发聚合固化前将这部分粘附的渗透密封胶用水清洗干净,防止其在固化后形成残留物,破坏工件表面,影响工件装配。为使渗透密封胶发生聚合反应,需将工件整体没入热水中,长时间加热,以使工件内部达到相当的温度,引发内部的渗透密封胶聚合。
3.目前将工件表面渗透密封胶清洗后的废水,含有大量有机污染物,cod严重超标,需要经过特殊处理后才能进行排放,造成污水处理成本的上升与环保达标排放的压力。同时,工件表面沾附的渗透密封胶未渗入工件微缺陷内部发挥作用即被洗去,形成渗透密封胶本身的浪费。
4.常规的渗透密封胶在固化过程中,需使用90℃左右热水对工件进行均匀加热较长时间,以使工件内部达到较高温度,引发内部渗透密封胶的聚合反应。在此阶段,工件表面受到连续加热,易发生变色、氧化、腐蚀等现象,严重影响工件表面质量,需要投入缓蚀剂进行对抗,工艺控制难度大,生产成本高。固化环节为保持水温,消耗大量能源,同时存在高温安全隐患。固化过程中易有部分密封胶受热膨胀,溢出微孔缺陷外,造成表面残留与缺陷内填充不足。
技术实现要素:5.本发明所要解决的技术问题:目前常见的渗透密封胶需要在真空-压力渗透环节结束后,用水清洗去除表面、型腔、盲孔、螺纹孔内的残余密封胶,避免其固化后形成残余物,破坏工件使用价值。清洗后产生了大量含有渗透密封胶的有机物废水,需要通过专门处理才能达到排放标准,形成了巨大的环保压力和污水处理成本,也造成了渗透密封胶的浪费。固化环节则需采用90左右℃热水浸没工件进行加温,工件表面长时间与高温热水接触,易出现氧化、变色、腐蚀现象,影响工件外观;为维持热水温度需持续加热,消耗大量能源,同时存在高温安全隐患。
6.为解决上述技术问题,本发明提供以下的技术方案:
7.一种循环回收复用型厌氧渗透密封胶组合物,包括密封胶主剂、分离剂和表面封闭剂;
8.在密封胶主剂的清洗过程中,所述分离剂在搅拌条件下使得密封胶主剂乳化,在
搅拌后的静置条件下破乳分离密封胶,分离后的密封胶直接回收复用;
9.在密封胶主剂的水浴固化过程中,所述表面封闭剂引发铸件微孔密封胶外表层的厌氧固化过程,形成“胶皮”状结构,彻底隔绝微孔内的密封胶与外界有氧环境,微孔内的密封胶在隔绝氧气后自发、持续地进行厌氧固化;
10.所述密封胶主剂和表面封闭剂内分置有厌氧引发组分,在无表面封闭剂时,所述密封胶主剂在分离剂作用下完成乳化过程,不发生固化;仅在同时存在表面封闭剂和密封胶主剂时,所述密封胶主剂发生厌氧固化。
11.优选地,所述密封胶主剂是由单官能度丙烯酸酯单体、双官能度的丙烯酸酯单体、反应型乳化剂、引发剂、阻聚剂在常温下均匀混合得到,各组分的配比如下:
[0012][0013]
优选地,所述单官能度丙烯酸酯为选自丙烯酸的碳数10至18的烷基酯,如丙烯酸月桂酯、甲基丙烯酸月桂酯、甲基丙烯酸异癸酯、丙烯酸十八醇酯、甲基丙烯酸十八醇酯、丙烯酸十三醇酯、甲基丙烯酸十三醇酯的一种或几种;
[0014]
所述多官能度丙烯酸酯为二丙烯酸多缩乙二醇酯、1,6己二醇二丙烯酸酯、2-甲基-1,3-丙二醇二丙烯酸酯、1,4-丁二醇二丙烯酸酯中的一种或几种;
[0015]
所述反应型乳化剂为改性烷基酚聚氧乙烯醚、脂肪酸聚氧乙烯酯、聚氧乙烯山梨糖醇酐单油酸酯、聚乙二醇单辛基苯基醚、蓖麻油聚氧乙烯醚中的一种或几种;
[0016]
所述引发剂为过氧化二苯甲酰、过氧化苯甲酰叔丁酯、过氧化甲乙酮、过氧化氢异丙苯中的一种或几种;
[0017]
所述阻聚剂为对苯二酚、苯醌、萘醌、蒽醌、2,6-二丁基对甲苯酚、苦味酸、4-甲氧基苯酚、萘醌、吩噻嗪、2,6-二叔丁基苯酚、2,5-二特丁基对苯二酚、2,5-二叔丁基-1,4-苯醌、2,6-二叔丁基-4-乙基苯醌中的一种或几种。
[0018]
优选地,所述分离剂是由阳离子型亲电吸附剂、反应型乳化剂、破乳剂、水混合得到,各组分的配比如下:
[0019]
[0020]
优选地,所述阳离子亲电吸附剂为十二烷基二甲基苄基氯化铵、十六酸酰胺丙基三甲基氯化铵、脂肪胺聚氧乙烯醚甲基氯化铵、丙烯酸二乙氨基乙酯氯化铵、原油酸酰胺季铵盐中的一种或几种;
[0021]
所述反应型乳化剂为改性烷基酚聚氧乙烯醚、脂肪酸聚氧乙烯酯、聚氧乙烯山梨糖醇酐单油酸酯、聚乙二醇单辛基苯基醚、蓖麻油聚氧乙烯醚中的一种或几种;
[0022]
所述破乳剂为聚氧乙烯聚氧丙烯十八醇醚、阳离子聚丙烯酰胺、聚合氯化铝中的一种或几种;
[0023]
所述水为电导率不大于10μs/cm的去离子水。
[0024]
优选地,所述表面封闭剂由水、水溶性引发剂、促进剂混合得到,各组分配比如下:
[0025][0026]
优选地,所述水溶性引发剂为过氧化氢、过硫酸铵、过硫酸钾、过硫酸钠、过硫酸氢钾中的一种或几种;所述促进剂为邻苯甲酰磺酰亚胺钠盐、二茂铁、三乙酰丙酮铝中的一种或几种;所述水为电导率不大于10μs/cm的去离子水。
[0027]
本发明获得的有益效果:
[0028]
本发明提供了一种以组分总密度低于水的丙烯酸酯型渗透密封胶,并配合使用过氧化物引发体系改变其固化反应发生条件。其被水清洗后,可在配用分离剂的辅助下,重新从水中分离,利用密度差漂浮于水表面形成胶层,使水中密封胶减少,水可循环清洗复用,大大减少了有机物污水排放量,并且渗透密封胶仍保持其原有性能,可循环复用,从污水处理量和渗透密封胶消耗量两方面极大地节省了成本,并减轻了环保压力。厌氧型渗透密封胶可在含有封闭促进剂的30-40℃热水中快速发生表面封闭,随后在工件孔隙内部形成厌氧环境,发生厌氧自固化,不需另行加温即可使固化反应完成,工件内部微孔隙被封堵,解决了工件受高温加热后的变色、氧化、腐蚀问题,节约了加温能耗,不产生高温热源,使生产工艺简化,生产安全性提高。同时没有密封胶受热膨胀溢出,造成损失的风险。
附图说明
[0029]
图1和图2为阳离子亲电吸附剂对乳化作用的影响示意图。
[0030]
其中,大圆形为密封胶有机相乳化液滴,蝌蚪形为乳化剂分子,小圆形为阳离子亲电吸附剂分子。
[0031]
图3为分离剂的组分变化对乳化后分层的影响。
具体实施方式
[0032]
下面通过对实施例的描述,对本发明的具体实施方式作进一步详细的说明,以帮助本领域的技术人员对本发明的发明构思、技术方案有更完整、准确和深入的理解。
[0033]
实施例1:本发明由主剂、配用分离剂、配用表面封闭剂三部分组成,其中主剂部分
使用方式如同常规的渗透密封胶,经过真空-压力浸渗、离心脱液、水清洗、热水固化环节,起密封工件内部微孔隙作用。配用分离剂部分在清洗环境加入清洗水中,待清洗环节完成后静置清洗水,配用分离剂即与主剂产生可逆电化学反应,使主剂中反应型乳化剂效果下降,造成破乳分层现象,达到循环回收的效果。表面封闭剂在固化环节加入30-40℃热水中,使工件孔隙内浅表层渗透密封胶主剂快速固化,孔隙内部形成厌氧环境,满足厌氧自固化反应要求。
[0034]
主剂部分是由单官能度丙烯酸酯单体、双官能度的丙烯酸酯单体、反应型乳化剂、引发剂、阻聚剂在常温下均匀混合得到。其组成份数如下(以下各种配比均以重量份计):
[0035]
表1主剂的组成成分及配比
[0036][0037]
将上述原料按配比加入搅拌釜中,混合30-60min,即得循环回收复用型渗透密封胶主剂部分。
[0038]
上述所指单官能度丙烯酸酯,为选自丙烯酸的碳数10至18的烷基酯,如丙烯酸月桂酯、甲基丙烯酸月桂酯、甲基丙烯酸异癸酯、丙烯酸十八醇酯、甲基丙烯酸十八醇酯、丙烯酸十三醇酯、甲基丙烯酸十三醇酯的一种或几种。
[0039]
上述所指多官能度丙烯酸酯,为二丙烯酸多缩乙二醇酯、1,6己二醇二丙烯酸酯、2-甲基-1,3-丙二醇二丙烯酸酯、1,4-丁二醇二丙烯酸酯中的一种或几种。
[0040]
上述所指反应型乳化剂,为改性烷基酚聚氧乙烯醚、脂肪酸聚氧乙烯酯、聚氧乙烯山梨糖醇酐单油酸酯(tw-80)、聚乙二醇单辛基苯基醚(op-10)、蓖麻油聚氧乙烯醚(el-40)中的一种或几种。
[0041]
上述所指引发剂,为过氧化二苯甲酰、过氧化苯甲酰叔丁酯、过氧化甲乙酮、过氧化氢异丙苯中的一种或几种。
[0042]
上述所指阻聚剂,为对苯二酚、苯醌、萘醌、蒽醌、2,6-二丁基对甲苯酚、苦味酸、4-甲氧基苯酚、萘醌、吩噻嗪、2,6-二叔丁基苯酚、2,5-二特丁基对苯二酚、2,5-二叔丁基-1,4-苯醌、2,6-二叔丁基-4-乙基苯醌中的一种或几种。
[0043]
配用分离剂部分是由阳离子型亲电吸附剂、反应型乳化剂、破乳剂、水混合得到。其组成份数如下:
[0044]
表2配用分离剂的组成成分及配比
[0045][0046]
将上述原料按配比加入搅拌釜中,混合30-60min,即得循环回收复用型渗透密封胶配用分离剂部分。
[0047]
上述所指阳离子亲电吸附剂,为十二烷基二甲基苄基氯化铵、十六酸酰胺丙基三甲基氯化铵、脂肪胺聚氧乙烯醚甲基氯化铵、丙烯酸二乙氨基乙酯氯化铵、原油酸酰胺季铵盐中的一种或几种。
[0048]
上述所指反应型乳化剂,为改性烷基酚聚氧乙烯醚、脂肪酸聚氧乙烯酯、聚氧乙烯山梨糖醇酐单油酸酯(tw-80)、聚乙二醇单辛基苯基醚(op-10)、蓖麻油聚氧乙烯醚(el-40)中的一种或几种。
[0049]
上述所指破乳剂,为聚氧乙烯聚氧丙烯十八醇醚、阳离子聚丙烯酰胺、聚合氯化铝中的一种或几种
[0050]
上述所指水为电导率不大于10μs/cm的去离子水。
[0051]
本发明中配用分离剂的工作原理:
[0052]
分离回收过程中的难点:渗透密封胶在施胶过程中,需将金属铸件整体浸没入液态密封胶中,通过真空—加压方式使液态密封胶渗入铸件微孔隙内部。在此期间不可避免地,会有大量密封胶沾附于铸件的型腔、内壁、螺纹孔等区域,需要用水清洗以免影响后续工序进行。一般的丙烯酸酯单体在水中相容性很差,呈油态,用水清洗基本不能洗脱。目前常用的方式为加入两亲性的乳化剂(表面活性剂)成分,在机械搅拌的作用下,有机相的密封胶能够在水相中受乳化剂分子包裹,形成悬浮的微滴,从而增加有机相与水相的相容性。但经过此种方法处理后,形成的有机相-水相混合乳液(对分离工艺而言)相当稳定与顽固,难于短时间内破坏体系的稳态,分离工艺存在相当困难。
[0053]
针对上述分离回收过程中的难点,本发明提出的解决方式:在于使用一类阳离子亲电吸附剂。此种吸附剂为一类有微弱乳化性能的阳离子表面活性剂,在水中分散后,与其他表面活性剂的极性端发生亲电吸附,聚集在乳化剂包裹的微滴外侧,又因其分子具有正电性,在亲电吸附发生过程中,吸附于同一微滴外侧的阳离子又发生同电性互斥,从微滴表面分离,牵连结合的乳化剂分子同步分离,减少了微滴外侧的乳化剂分子数量,使内部有机相与外部水相直接接触,因密度差的作用,发生相分离。如图1所示刚加入阳离子亲电吸附剂时并未影响乳化剂正常工作,机械搅拌下有机相液滴受乳化剂分子作用,在水相中分散形成微滴,相容性增加。图2所示搅拌后静置过程中亲电吸附剂与乳化剂分子极性端发生亲电吸附,多个吸附剂分子间发生同电性互斥,导致微滴表面撕裂,发生破乳分相。
[0054]
以此方式,一方面保证了在清洗过程中,机械搅拌作用下,乳化剂分子可以发挥正常效用,另一方面加入分离剂后进入静置状态,阳离子亲电吸附剂能以一定的速率与乳化剂分子结合,达到撕裂微滴表面,促成有机相与水相的分离。
[0055]
分离剂体系中破乳剂的作用,在于加速整个分离过程的速度。因密封胶主剂体系中选用的乳化剂hlb值较高,与水相容性较好,破乳剂不能直接破坏被包裹的微滴,不能独立起分离作用。但在与阳离子吸附剂协同作用下,破乳剂可以很好地限制微滴的重新形成,使整个有机相-水相的分离过程不可逆,明显增加单位时间内有机相的析出速度。
[0056]
向200g水中投入20g密封胶,16g分离剂,分离剂由35重量份阳离子亲电吸附剂、25重量份反应型乳化剂、30重量份份水与指定重量份数的破乳剂组成,分离剂中所含破乳剂的占比依次增加,在机械乳化分散机上,以2000r/min的转速,乳化10min,静置30min后观察分层情况:
[0057]
表3分离剂中破乳剂占比对于整体分层效果的影响
[0058][0059]
表3数据表明破乳剂的有无/数量对分层速度的显著影响,破乳剂数量的增加,可使单位时间内析出的浸渗密封胶增加,不讨论阳离子吸附剂,因其为分离原理的基础,在前部已作描述。
[0060]
图3中从左至右:b1-b5试样,明显可见分层速度不同。
[0061]
由于分层过程为利用有机相与水相的互不相容性,因此分离出的密封胶含水率很少(不足2%),与新制密封胶相当,性能不发生衰减,可以经检测合格后回收继续使用,显著减少了密封胶的使用量。清洗水不需排放,在分离密封胶后可继续循环使用,避免了污水排放。在实际客户现场试生产时,获得的有益效果如下:
[0062]
表4本发明在实际应用中的有益效果
[0063][0064]
对密封金属铸件工序来说,成本减少显著。
[0065]
配用表面封闭剂部分,为水、水溶性引发剂、促进剂混合得到。其组成份数如下:
[0066]
表5配用表面封闭剂的组成成分及配比
[0067][0068]
将上述原料按配比加入搅拌釜中,混合30-60min,即得表面封闭剂。
[0069]
上述所指水溶性引发剂,为过氧化氢、过硫酸铵、过硫酸钾、过硫酸钠、过硫酸氢钾中的一种或几种。
[0070]
上述所指促进剂,为邻苯甲酰磺酰亚胺钠盐、二茂铁、三乙酰丙酮铝中的一种或几种。
[0071]
上述所指水为电导率不大于10μs/cm的去离子水。
[0072]
本发明中配用表面封闭剂的工作原理:
[0073]
现有丙烯酸酯基渗透密封胶的固化机理为:自由基聚合反应,传统上引发聚合反应的方式为加热引发(烘箱/水浴环境),利用偶氮类引发剂低温下稳定、高温下快速分解形成自由基的原理促成固化反应的进行,通常需要达到90℃以上的温度。高温加热带来的主要问题有:1.反应能耗高;2.对铝合金、铸铁等材质的铸件表面有氧化腐蚀作用,需要额外加入缓蚀剂进行防护,工艺影响因素多;3.少数工件内微孔中填充的密封胶,在加热过程中、固化之前,因受热体积膨胀,溢出微孔外,形成表面残留与孔内填充不足,降低了施胶合格率。
[0074]
为解决上述问题可将丙烯酸酯基渗透密封胶转换为厌氧固化模式。厌氧固化的原理为:厌氧引发剂在常态下持续发生极轻微的分解,产生自由基,在与氧气接触的情况下,优先被氧自由基捕捉湮灭,维持体系的稳定;在与氧气隔绝的条件下,引发剂分解出的自由基则持续增加,与单体发生加成反应,最终使反应放热足以维持反应自身的进行,发生自加速效应,完成聚合过程。
[0075]
渗透密封胶采用厌氧体系,难点在于生产过程中将铸件浸没入密封胶并抽真空使密封胶渗入微孔缺陷内部的环节,有引发意外的厌氧聚合的风险。解决方法在于将厌氧固化过程与引发剂/引发体系的添加分为a、b两个部分。
[0076]
a部分:为油溶性良好的有机过氧化物,预加入密封胶主剂中,并与阻聚剂并用,控制其反应活性。即为主剂中的引发剂。
[0077]
b部分:为水溶性良好的无机过氧化物,与相应促进剂一起,配制为表面封闭剂。即为水溶性引发剂。
[0078]
实际使用时,将金属铸件放入密封胶内,因密封胶本体内a部分反应活性较低,并与阻聚剂并用,在短时间的抽真空工艺中能够维持稳定,不发生意外的厌氧聚合。在完成离心脱液、清洗等工序后,将铸件放入由b部分配置的水基工作溶液中,在水中一方面形成厌氧环境,并受一定温度作用(30-40℃),一方面其中的水溶引发剂与促进剂会引发铸件微孔密封胶外表层的厌氧固化过程,形成“胶皮”状结构,对微孔内的密封胶与外界氧气环境彻底隔绝(即表面封闭),在后续过程中自发、持续地进行厌氧固化。
[0079]
将厌氧引发组分分别置于a、b部分的做法,也能保持清洗、回收过程中,水中单体微滴、分离出的有机相的稳定,防止回收过程中出现意外固化。
[0080]
综上所述,本发明通过配用分离剂破坏渗透密封胶主剂从工件表面洗脱后在清洗水中形成的乳液,并通过配方控制主剂总密度小于水,使主剂能自行从水中分离形成两相,达到清洗水中渗透密封胶含量减少,清洗水与渗透密封胶均可循环使用的效果,同时不影响渗透密封胶原有的清洗性和对工件的密封有效性。
[0081]
通过主剂内部过氧化物引发体系,配合在30-40℃热水中使用表面封闭剂,使工件孔隙内浅表层渗透密封胶主剂快速固化,孔隙内部形成厌氧环境,满足厌氧自固化反应要求。不需要使用高温热水浸没工件并长时间加热,避免了工件表面受高温影响出现变色、氧化、腐蚀问题,节约了加温能耗,不产生高温热源,使生产工艺简化,生产安全性提高,同时
避免密封胶固化过程中因受热膨胀形成的溢出损失。
[0082]
以上实施例仅为说明本发明的技术思想,不能以此限定本发明的保护范围,凡是按照本发明提出的技术思想,在技术方案基础上所做的任何改动,均落入本发明保护范围之内;本发明未涉及的技术均可通过现有技术加以实现。