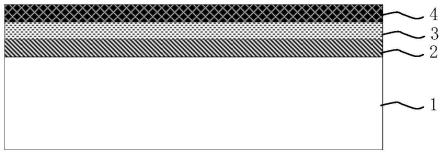
1.本发明涉及一种胶带及其制备方法,尤其涉及一种可发光的热贴合型胶带及其制备方法。
背景技术:2.随着社会的不断进步与发展,汽车已进入千家万户。随着汽车的普及,人们对于高品质、个性化的汽车外观及设计要求日益增多,且夜间行车也已成为人们的日常生活。怎样在夜幕下凸显汽车的个性化以及具有安全警示性作用的问题也以成为现今亟待解决的难题。
3.现有的汽车用发光胶带以电力发光源和荧光色的压敏胶带为主,荧光色压敏胶带身不具备发光能力,通过其他光照进行反射从而达到夜间发光的效果,但这种反射光的形式一旦在没有光束的照射下就会失效,对于在无光照的条件下行走的人起不到警示作用。而电力发光源需要进行插电或充电处理,对于设备要求高的同时不环保。
4.此外,现有胶带采用压敏胶粘结方式,由于压敏胶带本身不具备长时间的耐候性能,因此荧光色压敏胶带的寿命较短,且容易出现脱落情况。
技术实现要素:5.本发明所要解决的技术问题是提供一种可发光的热贴合型胶带及其制备方法,用于汽车、高铁等车身,夜间发光可起到装饰、夜间安全警示的作用。
6.本发明为解决上述技术问题而采用的技术方案是提供一种可发光的热贴合型胶带,包括热贴合型复合膜、发光型涂层、保护涂层和保护膜。
7.上述的可发光的热贴合型胶带,其中,所述的热贴合型复合膜为pp与pe多层复合膜,所述的热贴合型复合膜厚度为50-100微米,软化点为170-190摄氏度。
8.上述的可发光的热贴合型胶带,其中,所述的发光型涂层为蓄光型水性涂层,蓄光时间大于6h,干膜厚度20-40微米。
9.上述的可发光的热贴合型胶带,其中,所述的保护涂层由水性丙烯酸树脂合成,其干膜厚度15-25微米,硬度大于1h。
10.上述的可发光的热贴合型胶带,其中,所述保护膜为耐高温静电吸附膜,其软化点大于150摄氏度。
11.上述的可发光的热贴合型胶带,其中,所述发光型涂层包含如下组分:主体树脂、润湿剂、水、消泡剂、流平剂、增稠剂以及发光颜料。
12.上述的可发光的热贴合型胶带,其中,所述的主体树脂为水基型丙烯酸酯和聚氨酯的混合物;各组分按重量份数配比如下:
13.丙烯酸酯
ꢀꢀꢀꢀꢀꢀ
10-15份;
14.聚氨酯
ꢀꢀꢀꢀꢀꢀꢀꢀ
16-20份;
15.发光颜料
ꢀꢀꢀꢀꢀꢀ
15-20份。
16.上述的可发光的热贴合型胶带,其中,所述的流平剂为改性丙烯酸共聚物,所述的增稠剂为改型聚丙烯酸类增稠剂及缔合型聚氨酯类增稠剂的混合物,所述的发光颜料为稀土激活碱土金属发光材料。
17.上述的可发光的热贴合型胶带,其中,所述稀土激活碱土金属发光材料的粒径为20-40微米。
18.本发明为解决上述技术问题还提供一种上述的可发光的热贴合型胶带的制备方法,其中,包括如下步骤:s1)将主体树脂加入到反应釜中搅拌,加入离子水润湿剂、消泡剂、流平剂混合,加入发光材料进行搅拌,加入增稠剂增稠,边搅拌边加入,过滤形成发光型涂层;s2)在热贴合复合膜上涂布所述发光型涂层,热固后涂布保护涂层;s3)加热烘干后保护涂层面与保护膜贴合。
19.本发明对比现有技术有如下的有益效果:本发明提供的可发光的热贴合型胶带及其制备方法,用于汽车车身的装饰作用,其所具有的蓄光自发光功能,在光照条件下具有装饰作用,在黑暗条件下具有安全警示作用;热贴合的粘结形式较之传统的胶水粘结形式更稳固环保。
附图说明
20.图1为本发明可发光的热贴合型胶带结构示意图;
21.图2为本发明的热贴合型胶带中的发光型涂层制备流程图。
22.图中:
23.1热贴合型复合膜
ꢀꢀꢀꢀꢀꢀꢀꢀꢀꢀꢀ
2发光型涂层
ꢀꢀꢀꢀꢀꢀꢀ
3保护涂层
24.4保护膜
具体实施方式
25.下面结合附图和实施例对本发明作进一步的描述。
26.图1为本发明可发光的热贴合型胶带结构示意图。
27.请参见图1,本发明提供的可发光的热贴合型胶带,包括热贴合型复合膜1、发光型涂层2、保护涂层3和保护膜4。
28.本发明提供的热贴合胶带采用蓄光型发光形式,即胶带通过表面蓄光涂层在日间进行光照的吸收在黑暗的情况下可以自发光,不需要其他能源损失较为环保。另外该胶带采用热贴合的装配形式,即在使用过程中通过加热时胶带底层熔融与基材贴合,具有较好的一致性及永久性。
29.本发明提供的热贴合胶带,热贴合型复合膜1为pp与pe多层复合膜;所述复合膜厚度为50-100微米,软化点为170-190摄氏度。发光型涂层2为蓄光型水性涂层,干膜厚度20-40微米;发光型涂层2蓄光性能为大于6h。
30.本发明提供的热贴合胶带,保护涂层3为水性丙烯酸树脂合成,其干膜厚度15-25微米,为高耐磨,耐指划涂层,其硬度大于1h。保护膜4为耐高温静电吸附膜,其软化点大于150摄氏度。
31.本发明提供的热贴合胶带,发光型涂层2包含如下组分:主体树脂、润湿剂、水、消泡剂、流平剂、增稠剂以及发光颜料;所述的主体树脂为水基型丙烯酸酯和聚氨酯的物理混
合物,两者之间可以互溶但不会发生化学反应;所述的发光颜料为稀土激活碱土金属发光材料,粒径为20-40微米;各组分按重量份数配比如下:
32.丙烯酸酯
ꢀꢀꢀꢀꢀ
10-15份;
33.聚氨酯
ꢀꢀꢀꢀꢀꢀꢀ
16-20份;
34.发光颜料
ꢀꢀꢀꢀꢀ
15-20份。
35.其中最优配比方案为丙烯酸酯15份,聚氨酯16份,发光颜料18份,若丙烯酸酯树脂超出15份,涂层成膜后偏硬,若少于10份则会影响涂层的耐候性能。聚氨酯可以有效改善涂层的整体柔韧性,过少则无法达到该效果,过多则会降低涂层呢过的耐磨。发光材料决定了涂层的发光时效及亮度,过少则发光时效降低,过多则会影响涂层的物性。
36.本发明提供的热贴合胶带,流平剂可选择改性丙烯酸共聚物,增稠剂可选择改型聚丙烯酸类增稠剂及缔合型聚氨酯类增稠剂的混合物。
37.由于发光材料具有较好的蓄光性能,即在光照条件下积蓄光能在黑暗条件下释放光。在涂层中加入一定量的发光材料在不影响涂层本身的光泽度,色彩饱满度以及耐候、耐磨、耐污等性能的同时,通过对发光材料的添加比例及发光材料的粒径的调整;例如采用大于300目粒径的发光材料通过分次加入至质量含量18%的比例,使涂层具有较长的发光。在保证涂装多样化个性化的同时,在夜间起到安全警示作用。
38.本发明还提供一种发光型水性涂层的制备方法,包括如下步骤:
39.s1)将主体树脂加入到反应釜中搅拌,加入离子水润湿剂、消泡剂、流平剂混合,加入发光材料进行搅拌,加入增稠剂增稠,边搅拌边加入,过滤形成发光型涂层;
40.s2)在热贴合复合膜上涂布所述发光型涂层,热固后涂布保护涂层;
41.s3)加热烘干后保护涂层面与保护膜贴合。
42.本发明在保证汽车用涂层的物性要求的同时,具有蓄光自发光功能,在光照条件下具有装饰作用,在黑暗条件下具有安全警示作用。涂层采用水基型树脂voc低,安全环保。水性亲水涂料具有便于运输、易于储存、使用方便等特点。
43.下面给出一个具体实施例:
44.分别将丙烯酸树脂10kg、聚氨酯树脂20kg加入到反应釜中,搅拌混料,搅拌转速为600转/min,搅拌混料5min。
45.加入去离子水10kg、流平剂1.5kg、消泡剂0.5kg、润湿剂剂2kg搅拌20min
46.将发光材料5kg加入反应釜搅拌速度提升到1000转/min继续分散时间为10min。
47.将搅拌速度调制1200转/min,加入增稠剂2kg调整粘度至800cps。
48.最后用200目过滤布过滤,分装,制得涂料成品约为100kg。
49.虽然本发明已以较佳实施例揭示如上,然其并非用以限定本发明,任何本领域技术人员,在不脱离本发明的精神和范围内,当可作些许的修改和完善,因此本发明的保护范围当以权利要求书所界定的为准。