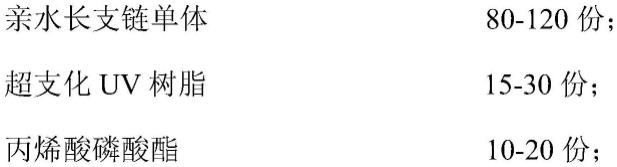
1.本发明涉及涂料技术领域,尤其涉及一种防污抗藻涂料及其制备方法。
背景技术:2.长期浸泡在水中,如海水中使用的船舶、管道、水下通道、展览视窗、鱼缸、泳池等设施或设备,表面易滋生海藻、贝壳造成水生生物污损,并导致腐蚀加剧、管路堵塞、视觉遮挡等问题。
3.水生生物污损的形成主要是以下过程:
4.1)设备表面浸没在海水后的数分钟内就会被蛋白质、多糖和糖蛋白等大分子所粘附,形成基膜,这是第一阶段;
5.2)随后细菌在基膜上附着繁殖,形成生物膜;因为浮游细菌是通过范德华力和静电相互作用等弱作用力在基膜上附着的,因此这过程一开始是可逆的,但随着细菌开始分泌胞外代谢物,细菌的附着变得牢固,这是第二阶段,可在数小时内完成;
6.3)在第三阶段,由于生物膜为硅藻孢子等多细胞的小型污损生物提供了良好的生存条件,使设备表面在几天内覆盖有黏液层;
7.4)最后,藤壶、贻贝、苔藓虫、盘管虫和大型藻类等种类繁多的大型污损生物附着生长,此过程可在一两个月内完成,可覆盖设备表面数年之久。
8.上述过程并不是一成不变的,几个过程之间没有必然的先后性;污损生物的附着生长很大程度上受温度、酸碱度、盐度、水流速度和基底种类的影响。
9.现有的防污抗藻涂层方案主要有:生物毒杀型、污损脱附型等方案。
10.其中生物毒杀型,按基料树脂可分为,a)基料不可溶(抗藻剂向表面析出向水体溶解扩散,扩散速率不可控);b)基料可溶解(抗藻剂随基料表层被溶解逐步释放,时效短);c)自抛光基料(侧链可水解形成亲水层,易被冲刷清洁,掺配部分可溶树脂,控制延长释放抗藻剂时效),自抛光基料掺配部分可溶树脂和抗藻剂,是目前最有效的方案之一,但依赖水体动态冲刷,对于静态抗藻,降解速率远慢于可溶解树脂,可溶解树脂接触水体即可可控脱落,降解为小分子,不必依赖水体动态冲刷。
11.污损脱附型,即硅系、氟系低表面能抗污涂层,不易附着,且易清洗脱落,但也依赖水体动态冲刷。
12.以上防污抗藻方案中,生物毒杀型对水生生物有或多或少的伤害;污损脱附型在静态水体中防污效果较差。
13.有鉴于此,提供一种对水生生物伤害小,同时在静态水体中防污抗藻效果好的防污抗藻涂料是目前亟需解决的技术问题。
技术实现要素:14.本发明要解决的技术问题是:为了解决现有技术中的防污抗藻方案无法同时兼顾对水生生物伤害小且在静态水体中防污抗藻效果好的问题,本发明提供一种防污抗藻涂料
及其制备方法,该防污抗藻涂料以超支化树脂为交联核心搭配适量比例的亲水长支链单体组成水凝胶,可有效提高涂层硬度、附着力、耐水性;涂料中还加入反应型磷酸酯和反应型胺类单体协同抗藻,从而获得了对水生生物低伤害又能在静态水体中高效抗藻的优异性能,解决了现有技术中防污抗藻方案无法同时兼顾对水生生物伤害小且在静态水体中防污抗藻效果好的问题。
15.本发明解决其技术问题所采用的技术方案是:
16.一种防污抗藻涂料,按照重量份数计,包括如下组分:
[0017][0018]
可选地,所述亲水长支链单体选自丙烯酸聚乙二醇酯、丙烯酸聚丙二醇酯、丙烯酸聚乙烯醇酯中的至少一种。
[0019]
可选地,所述丙烯酸聚乙二醇酯选自sr550、sr551中的至少一种;所述丙烯酸聚丙二醇酯包括y57146;所述丙烯酸聚乙烯醇酯包括pegdac。
[0020]
可选地,所述超支化uv树脂为丙烯酸酯类树脂。
[0021]
可选地,所述丙烯酸酯类树脂的官能度不小于12。
[0022]
可选地,所述含胺基聚合物选自聚醚胺、聚氧乙烯胺、聚乙烯亚胺中的至少一种。
[0023]
可选地,所述光引发剂选自α-羟基酮类、苯乙酮类中的至少一种。
[0024]
可选地,所述α-羟基酮类光引发剂选自184、1173中的至少一种;所述苯乙酮类光引发剂包括bdk。
[0025]
可选地,所述溶剂选自酯类溶剂、醚类溶剂、苯类溶剂中的至少一种。
[0026]
本发明的另一目的在于提供一种如上所述的防污抗藻涂料的制备方法,包括如下步骤:
[0027]
s1:将甲基丙烯酸缩水甘油酯、含胺基聚合物和溶剂混合,加热至80℃,搅拌反应2-3h,得到第一反应混合液;
[0028]
s2:将所述第一反应混合液冷却至20-50℃,加入亲水长支链单体、超支化uv树脂、丙烯酸磷酸酯,搅拌反应10-30min,得到第二反应混合物;
[0029]
s3:将所述第二反应混合物冷却至25℃以下,移至黄光灯环境,加入光引发剂,搅拌反应10-30min,得到防污抗藻涂料。
[0030]
本发明的有益效果是:
[0031]
本发明提供的防污抗藻涂料,通过特定配方设计的uv固化型水凝胶涂层,以超支化树脂为交联核心,搭配适量比例的亲水长支链单体,组成水凝胶类防污抗藻涂料;该水凝胶类防污抗藻涂料通过树脂分子取向的弹性回复和结合水的渗透压产生的排斥力抗污,再加入特定比例的反应型磷酸酯和反应型胺类单体协同抗藻,防污抗藻过程对水生生物的伤害小,同时不必依赖水体的动态冲刷,加强静态水体抗污效果。
具体实施方式
[0032]
现在对本发明作进一步详细的说明。下面描述的实施例是示例性的,旨在用于解释本发明,而不能理解为对本发明的限制,基于本发明的实施例,本领域普通技术人员在没有作出创造性劳动的前提下所获得的所有其他实施例,都属于本发明保护的范围。
[0033]
为解决现有技术中水凝胶类防污抗藻涂层附着力较差的问题,本发明提供一种防污抗藻涂料,按照重量份数计,该防污抗藻涂层包括如下组分:
[0034][0035][0036]
本发明提供的防污抗藻涂料,通过特定配方设计的uv固化型水凝胶涂层,以超支化树脂为交联核心,搭配适量比例的亲水长支链单体,组成水凝胶类防污抗藻涂料;该水凝胶类防污抗藻涂料通过树脂分子取向的弹性回复和结合水的渗透压产生的排斥力抗污,再加入特定比例的反应型磷酸酯和反应型胺类单体协同抗藻,防污抗藻过程对水生生物的伤害小,同时不必依赖水体的动态冲刷,加强静态水体抗污效果。
[0037]
为保证防污抗藻涂料的综合性能,本发明优选丙烯酸磷酯与含胺基聚合物的质量比范围为(1-2):(2-1),一方面避免丙烯酸磷酸酯含量过少防污抗藻性能较差,丙烯酸磷酸酯含量过多导致涂层硬度下降,水煮易发白;另一方面避免含胺基聚合物含量过少防污抗藻性能较差,含胺基聚合物含量过高导致防污抗藻过程对水生生物的伤害大;同时避免丙烯酸磷酸酯与含胺基聚合物含量同时过多时,导致产生絮状沉淀,影响综合效果。
[0038]
该防污抗藻涂料可有效提高涂层硬度、附着力、耐水性;当微生物向涂层靠近时,首先是涂层表面的亲水长支链的排斥作用进行物理防污抗藻,然后是涂层表面短支链上的磷酸酯、胺基等基团杀灭微生物,从而使得制备的防污抗藻涂料在对水生生物低伤害、能高效抗藻的基础上,具有较好的力学性能,在塑料表面具有优异的附着力,避免将该防污抗藻涂料涂覆于塑料表面后,若长期泡在水中出现发雾、涂层被溶胀脱落、被鱼类撞击脱落等问题。
[0039]
为保证防污抗藻涂层的物理防污抗藻能力,本发明优选亲水长支链单体的分子量不小于200,优选亲水长支链单体选自丙烯酸聚乙二醇酯、丙烯酸聚丙二醇酯、丙烯酸聚乙烯醇酯中的至少一种;并进一步优选丙烯酸聚乙二醇酯选自沙多玛sr550、沙多玛sr551中的至少一种;丙烯酸聚丙二醇酯可选用上海源叶y57146;丙烯酸聚乙烯醇酯可选用西安齐岳pegdac。
[0040]
本发明优选超支化uv树脂为丙烯酸酯类树脂,并进一步优选丙烯酸酯类树脂的官能度不小于12。
[0041]
具体的,优选该丙烯酸酯类树脂可选用型号包括但不限于戴马斯bdt1015、戴马斯bdt1018。
[0042]
本发明中丙烯酸磷酸酯可选型号包括但不限于沙多玛sr9051,长兴em39,日本化药pm-2。
[0043]
本发明优选含胺基聚合物选自聚醚胺、聚氧乙烯胺、聚乙烯亚胺中的至少一种,其中聚醚胺可选用的型号包括但不限于上海阿拉丁聚醚胺d-2000,cas no.:9046-10-0;聚氧乙烯胺可选用的型号包括但不限于上海阿拉丁聚氧乙烯二胺,cas no.:24991-53-5;聚乙烯亚胺可选用的型号包括但不限于上海攻碧克gbk-pei9。
[0044]
本发明中的光引发剂选自α-羟基酮类、苯乙酮类中的至少一种,其中α-羟基酮类可选用的型号包括但不限于igm的引发剂184、引发剂1173;苯乙酮类可选用的型号包括但不限于igm的引发剂bdk。
[0045]
本发明中的溶剂选自酯类溶剂、醚类溶剂、苯类溶剂中的至少一种,如乙酸乙酯、乙酸丁酯、丙二醇单甲醚、甲苯等。
[0046]
本发明的另一目的在于提供一种如上所述的防污抗藻涂料的制备方法,该制备方法包括如下步骤:
[0047]
s1:将甲基丙烯酸缩水甘油酯、含胺基聚合物和溶剂混合,加热至80℃,搅拌反应2-3h,在含胺基聚合支链接枝少量丙烯酸酯,得到第一反应混合液;
[0048]
s2:将第一反应混合液冷却至20-50℃,加入亲水长支链单体、超支化uv树脂、丙烯酸磷酸酯,搅拌反应10-30min,得到第二反应混合物;
[0049]
s3:将第二反应混合物冷却至25℃以下,移至黄光灯环境,加入光引发剂,搅拌反应10-30min,得到防污抗藻涂料。
[0050]
本发明提供的防污抗藻涂料的制备方法,制备过程简单,通过特定配方设计的uv固化型水凝胶涂层,以超支化树脂为交联核心,搭配适量比例的亲水长支链单体,组成水凝胶类防污抗藻涂料;该水凝胶类防污抗藻涂料通过树脂分子取向的弹性回复和结合水的渗透压产生的排斥力抗污,再加入特定比例的反应型磷酸酯和反应型胺类单体协同抗藻,防污抗藻过程对水生生物的伤害小,同时不必依赖水体的动态冲刷,加强静态水体抗污效果。
[0051]
为使本发明的上述目的、特征和优点能够更为明显易懂,下面对本发明的具体实施例做详细的说明。
[0052]
第一组实施例
[0053]
实施例1-1
[0054]
s1:按照重量份数计,将2份甲基丙烯酸缩水甘油酯(gma)、15份的聚醚胺d-2000和1000份的乙酸丁酯混合,加热至80℃,搅拌反应2h,在含胺基聚合支链接枝少量丙烯酸酯,
得到第一反应混合液;
[0055]
s2:将第一反应混合液冷却至20℃,加入100份的亲水长支链单体sr550、20份的超支化uv树脂bdt1015、15份的丙烯酸磷酸酯sr9051,搅拌反应10min,得到第二反应混合物;
[0056]
s3:将第二反应混合物冷却至25℃以下,移至黄光灯环境,加入8份的光引发剂184,搅拌反应10min,得到防污抗藻涂料。
[0057]
实施例1-2
[0058]
s1:按照重量份数计,将2份甲基丙烯酸缩水甘油酯(gma)、15份的聚氧乙烯二胺和1000份的丙二醇单甲醚混合,加热至80℃,搅拌反应2.5h,在含胺基聚合支链接枝少量丙烯酸酯,得到第一反应混合液;
[0059]
s2:将第一反应混合液冷却至30℃,加入100份的亲水长支链单体y57146、20份的超支化uv树脂bdt1018、15份的丙烯酸磷酸酯sr9051,搅拌反应20min,得到第二反应混合物;
[0060]
s3:将第二反应混合物冷却至25℃以下,移至黄光灯环境,加入8份的光引发剂bdk,搅拌反应20min,得到防污抗藻涂料。
[0061]
实施例1-3
[0062]
s1:按照重量份数计,将2份甲基丙烯酸缩水甘油酯(gma)、15份的gbk-pei9和1000份的甲苯混合,加热至80℃,搅拌反应3h,在含胺基聚合支链接枝少量丙烯酸酯,得到第一反应混合液;
[0063]
s2:将第一反应混合液冷却至50℃,加入100份的亲水长支链单体pegdac、20份的超支化uv树脂bdt1018、15份的丙烯酸磷酸酯sr9051,搅拌反应30min,得到第二反应混合物;
[0064]
s3:将第二反应混合物冷却至25℃以下,移至黄光灯环境,加入8份的光引发剂bdk,搅拌反应30min,得到防污抗藻涂料。
[0065]
实施例1-4
[0066]
s1:按照重量份数计,将1份甲基丙烯酸缩水甘油酯(gma)、10份的d-2000和1000份的乙酸乙酯混合,加热至80℃,搅拌反应2.5h,在含胺基聚合支链接枝少量丙烯酸酯,得到第一反应混合液;
[0067]
s2:将第一反应混合液冷却至30℃,加入100份的亲水长支链单体sr550、15份的超支化uv树脂bdt1015、10份的丙烯酸磷酸酯sr9051,搅拌反应20min,得到第二反应混合物;
[0068]
s3:将第二反应混合物冷却至25℃以下,移至黄光灯环境,加入5份的光引发剂184,搅拌反应20min,得到防污抗藻涂料。
[0069]
实施例1-5
[0070]
s1:按照重量份数计,将3份甲基丙烯酸缩水甘油酯(gma)、20份的d-2000和1000份的乙酸丁酯混合,加热至80℃,搅拌反应2.5h,在含胺基聚合支链接枝少量丙烯酸酯,得到第一反应混合液;
[0071]
s2:将第一反应混合液冷却至30℃,加入100份的亲水长支链单体sr550、30份的超支化uv树脂bdt1015、20份的丙烯酸磷酸酯sr9051,搅拌反应20min,得到第二反应混合物;
[0072]
s3:将第二反应混合物冷却至25℃以下,移至黄光灯环境,加入10份的光引发剂184,搅拌反应20min,得到防污抗藻涂料。
[0073]
实施例1-1~1-5中的原料组成参见表1所示:
[0074]
表1
[0075][0076][0077]
对上述各实施例制备的防污抗藻涂料进行性能测试,测试结果参见表2所示:
[0078]
表2
[0079]
测试项目实施例1-1实施例1-2实施例1-3实施例1-4实施例1-5透过率91.3%91.5%90.8%90.8%91.1%雾度0.5%0.5%0.6%0.5%0.3%铅笔硬度hhhhh百格附着力5b5b5b5b5b水煮后雾度0.8%0.7%0.7%0.6%0.7%水煮后附着力5b5b5b5b5b抗藻性能0级0级0级0级0级
[0080]
第二组实施例
[0081]
实施例2-1
[0082]
s1:按照重量份数计,将2份甲基丙烯酸缩水甘油酯(gma)、10份的d-2000、5份的聚氧乙烯二胺、5份的gbk-pei9、500份的乙酸丁酯和500份的乙酸乙酯混合,加热至80℃,搅拌反应2.5h,在含胺基聚合支链接枝少量丙烯酸酯,得到第一反应混合液;
[0083]
s2:将第一反应混合液冷却至30℃,加入50份的亲水长支链单体sr550、50份的y57146、10份的超支化uv树脂bdt1015、10份的超支化uv树脂bdt1018、15份的丙烯酸磷酸酯sr9051,搅拌反应20min,得到第二反应混合物;
[0084]
s3:将第二反应混合物冷却至25℃以下,移至黄光灯环境,加入8份的光引发剂184,搅拌反应20min,得到防污抗藻涂料。
[0085]
实施例2-2
[0086]
s1:按照重量份数计,将2份甲基丙烯酸缩水甘油酯(gma)、5份的d-2000、10份的聚
氧乙烯二胺、5份的gbk-pei9、500份的乙酸丁酯和500份的丙二醇单甲醚混合,加热至80℃,搅拌反应2.5h,在含胺基聚合支链接枝少量丙烯酸酯,得到第一反应混合液;
[0087]
s2:将第一反应混合液冷却至30℃,加入50份的亲水长支链单体y57146、50份的pegdac、10份的超支化uv树脂bdt1015、10份的超支化uv树脂bdt1018、15份的丙烯酸磷酸酯sr9051,搅拌反应20min,得到第二反应混合物;
[0088]
s3:将第二反应混合物冷却至25℃以下,移至黄光灯环境,加入8份的光引发剂bdk,搅拌反应20min,得到防污抗藻涂料。
[0089]
实施例2-3
[0090]
s1:按照重量份数计,将2份甲基丙烯酸缩水甘油酯(gma)、5份的d-2000、5份的聚氧乙烯二胺、10份的gbk-pei9、500份的丙二醇单甲醚和500份的甲苯混合,加热至80℃,搅拌反应2.5h,在含胺基聚合支链接枝少量丙烯酸酯,得到第一反应混合液;
[0091]
s2:将第一反应混合液冷却至30℃,加入50份的亲水长支链单体sr550、50份的pegdac、10份的超支化uv树脂bdt1015、10份的超支化uv树脂bdt1018、15份的丙烯酸磷酸酯sr9051,搅拌反应20min,得到第二反应混合物;
[0092]
s3:将第二反应混合物冷却至25℃以下,移至黄光灯环境,加入8份的光引发剂184,搅拌反应20min,得到防污抗藻涂料。
[0093]
实施例2-4
[0094]
s1:按照重量份数计,将1份甲基丙烯酸缩水甘油酯(gma)、10份的d-2000、10份的gbk-pei9、500份的乙酸乙酯、300份的乙酸丁酯、100份的丙二醇单甲醚和100份的甲苯混合,加热至80℃,搅拌反应2.5h,在含胺基聚合支链接枝少量丙烯酸酯,得到第一反应混合液;
[0095]
s2:将第一反应混合液冷却至30℃,加入50份的亲水长支链单体sr550、25份的y57146、25份的pegdac、10份的超支化uv树脂bdt1015、20份的超支化uv树脂bdt1018、10份的丙烯酸磷酸酯sr9051,搅拌反应20min,得到第二反应混合物;
[0096]
s3:将第二反应混合物冷却至25℃以下,移至黄光灯环境,加入5份的光引发剂184,搅拌反应20min,得到防污抗藻涂料。
[0097]
实施例2-5
[0098]
s1:按照重量份数计,将3份甲基丙烯酸缩水甘油酯(gma)、10份的d-2000、5份的聚氧乙烯二胺、500份的乙酸乙酯、300份的乙酸丁酯、100份的丙二醇单甲醚和100份的甲苯混合,加热至80℃,搅拌反应2.5h,在含胺基聚合支链接枝少量丙烯酸酯,得到第一反应混合液;
[0099]
s2:将第一反应混合液冷却至30℃,加入25份的亲水长支链单体sr550、50份的y57146、25份的pegdac、20份的超支化uv树脂bdt1015、10份的超支化uv树脂bdt1018、20份的丙烯酸磷酸酯sr9051,搅拌反应20min,得到第二反应混合物;
[0100]
s3:将第二反应混合物冷却至25℃以下,移至黄光灯环境,加入10份的光引发剂184,搅拌反应20min,得到防污抗藻涂料。
[0101]
实施例2-1~2-5中的原料组成参见表3所示:
[0102]
表3
[0103][0104][0105]
对上述各实施例制备的防污抗藻涂料进行性能测试,测试结果参见表4所示:
[0106]
表4
[0107]
测试项目实施例2-1实施例2-2实施例2-3实施例2-4实施例2-5透过率91.1%91.3%90.9%90.6%90.5%雾度0.5%0.5%0.3%0.7%0.8%铅笔硬度hhhhh百格附着力5b5b5b5b5b水煮后雾度0.8%0.8%0.7%0.9%0.9%水煮后附着力5b5b5b5b5b抗藻性能0级0级0级0级0级
[0108]
对比例1
[0109]
s1:按照重量份数计,将2份甲基丙烯酸缩水甘油酯(gma)、15份的d-2000、1000份的乙酸丁酯混合,加热至80℃,搅拌反应2.5h,在含胺基聚合支链接枝少量丙烯酸酯,得到第一反应混合液;
[0110]
s2:将第一反应混合液冷却至30℃,加入100份的亲水长支链单体sr550、15份的丙烯酸磷酸酯sr9051,搅拌反应20min,得到第二反应混合物;
[0111]
s3:将第二反应混合物冷却至25℃以下,移至黄光灯环境,加入8份的光引发剂184,搅拌反应20min,得到防污抗藻涂料。
[0112]
对比例2
[0113]
s1:按照重量份数计,将2份甲基丙烯酸缩水甘油酯(gma)、15份的d-2000、1000份的乙酸丁酯混合,加热至80℃,搅拌反应2.5h,在含胺基聚合支链接枝少量丙烯酸酯,得到第一反应混合液;
[0114]
s2:将第一反应混合液冷却至30℃,加入100份的亲水长支链单体sr550、5份的超支化uv树脂bdt1015、15份的丙烯酸磷酸酯sr9051,搅拌反应20min,得到第二反应混合物;
[0115]
s3:将第二反应混合物冷却至25℃以下,移至黄光灯环境,加入8份的光引发剂184,搅拌反应20min,得到防污抗藻涂料。
[0116]
对比例3
[0117]
s1:按照重量份数计,将2份甲基丙烯酸缩水甘油酯(gma)、15份的d-2000、1000份的乙酸丁酯混合,加热至80℃,搅拌反应2.5h,在含胺基聚合支链接枝少量丙烯酸酯,得到第一反应混合液;
[0118]
s2:将第一反应混合液冷却至30℃,加入100份的亲水长支链单体sr550、50份的超支化uv树脂bdt1018、15份的丙烯酸磷酸酯sr9051,搅拌反应20min,得到第二反应混合物;
[0119]
s3:将第二反应混合物冷却至25℃以下,移至黄光灯环境,加入8份的光引发剂184,搅拌反应20min,得到防污抗藻涂料。
[0120]
对比例4
[0121]
s1:按照重量份数计,将2份甲基丙烯酸缩水甘油酯(gma)、15份的d-2000、500份的乙酸乙酯、300份的乙酸丁酯、100份的丙二醇单甲醚和100份的甲苯混合,加热至80℃,搅拌反应2.5h,在含胺基聚合支链接枝少量丙烯酸酯,得到第一反应混合液;
[0122]
s2:将第一反应混合液冷却至30℃,加入100份的亲水长支链单体sr550、15份的超支化uv树脂bdt1015,搅拌反应20min,得到第二反应混合物;
[0123]
s3:将第二反应混合物冷却至25℃以下,移至黄光灯环境,加入5份的光引发剂184,搅拌反应20min,得到防污抗藻涂料。
[0124]
对比例5
[0125]
s1:按照重量份数计,将500份的乙酸乙酯、300份的乙酸丁酯、100份的丙二醇单甲醚和100份的甲苯混合,加热至80℃,搅拌反应2.5h,在含胺基聚合支链接枝少量丙烯酸酯,得到第一反应混合液;
[0126]
s2:将第一反应混合液冷却至30℃,加入100份的亲水长支链单体sr550、15份的超支化uv树脂bdt1015、10份的丙烯酸磷酸酯sr9051,搅拌反应20min,得到第二反应混合物;
[0127]
s3:将第二反应混合物冷却至25℃以下,移至黄光灯环境,加入10份的光引发剂184,搅拌反应20min,得到防污抗藻涂料
[0128]
对比例1-5中的原料组成参见表5所示:
[0129]
表5
[0130][0131][0132]
对上述各对比例制备的防污抗藻涂料进行性能测试,测试结果参见表6所示:
[0133]
表6
[0134]
测试项目对比例1对比例2对比例3对比例4对比例5透过率91.8%91.3%90.8%90.6%90.5%雾度0.3%0.5%0.6%0.7%0.8%铅笔硬度6b3b3hhh百格附着力0b2b5b5b5b水煮后雾度0.1%36%0.7%0.9%0.9%水煮后附着力0b0b5b5b5b抗藻性能3级0级3级2级2级
[0135]
上述各实施例以及对比例均按照如下方法进行性能测试:
[0136]
将各实施例和对比例制备的涂料,淋涂在3mmpmma板材上,板材尺寸200
×
100mm,70℃干燥5分钟,然后经uv固化,uv灯使用的是h型汞灯,能量300-400mj/m2。
[0137]
对制备的涂层按照如下方法或标准进行性能测试:
[0138]
透过率:astm d1003;
[0139]
雾度:astm d1003;
[0140]
铅笔硬度:astm d3363;
[0141]
百格附着力:astm d3359;
[0142]
水煮测试:100℃水煮30min;
[0143]
抗藻性能:gb t 24127-2009。
[0144]
从上述数据看出,各实施例制备的防污抗藻涂料均具有较好的抗藻性能、优异的力学性能以及优异的附着力以及耐水煮性能,短期以及长期抗藻效果均较好,综合性能优异,可满足市场使用。
[0145]
对比例1提供的技术方案中未添加超支化树脂,制备的涂层附着力极差,水煮后涂层几乎被全部溶解,短期抗藻通过,长期抗藻效果很差。
[0146]
对比例2提供的技术方案中超支化树脂添加过少,铅笔硬度、附着力与对比例1相比有改善,但仍不足,且水煮后发白,抗藻性能通过,但长期使用后不透明。
[0147]
对比例3提供的技术方案中超支化树脂添加过量,硬度、耐水均提高,但抗藻性能下降。
[0148]
对比例4、5提供的技术方案中未添加磷酸酯和含胺基聚合物,抗藻性能均有衰减。
[0149]
以上述依据本发明的理想实施例为启示,通过上述的说明内容,相关工作人员完全可以在不偏离本项发明技术思想的范围内,进行多样的变更以及修改。本项发明的技术性范围并不局限于说明书上的内容,必须要根据权利要求范围来确定其技术性范围。