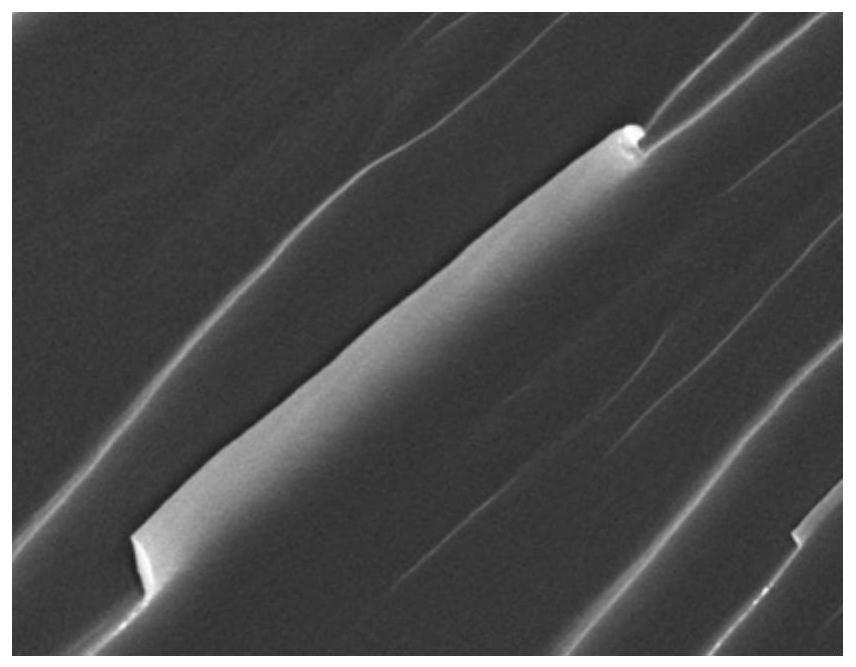
1.本发明涉及环氧树脂胶黏剂领域,尤其涉及一种二氧化硅杂化环氧树脂胶黏剂的制备方法。
背景技术:2.环氧树脂具有良好的综合性能,在胶黏剂领域应用非常广泛。然而未经改性的环氧树脂存在脆性大、耐热性差等缺点,一般需要通过加入橡胶增韧剂、热塑性树脂等改性剂增韧,增加室温粘接性能,但以模量、耐热性能等降低为代价。
3.为了提高耐热性,通常利用sio2等无机纳米粒子对环氧树脂进行直接共混改性的方法,但此方法对中高温剪切强度提高不明显。这主要是因为采用直接共混方法,无机纳米颗粒在环氧树脂中分散不均匀,容易发生团聚,改性效果受到影响。另外共混工艺制备的无机纳米颗粒难以和环氧基体形成有效的无机有机互穿网络(ipn)结构。
技术实现要素:4.本发明是要解决现有环氧树脂胶黏剂制备方法存在常温剪切强度和中高温剪切强度难以兼顾的问题,提供一种二氧化硅/环氧树脂无机有机杂化胶黏剂的制备方法。
5.本发明二氧化硅/环氧树脂无机有机杂化胶黏剂的制备方法,包括以下步骤:
6.步骤一、先将共溶剂加入到反应瓶中,然后加入硅酸酯和硅烷偶联剂,搅拌均匀,随后加入催化剂二月桂酸二丁基锡,开始加热,待反应物升温至55~60℃时,开始滴加酸水溶液,控制滴加速度使酸水溶液在20~30min内滴加完成,然后在55~60℃的温度下保温反应3~4h,之后再加入环氧树脂,混合均匀后在60~80℃真空旋蒸15~20min,最后在80~90℃真空旋蒸20~30min,制得sio2杂化环氧树脂;
7.步骤二、将步骤一得到的sio2杂化环氧树脂和等当量的胺类固化剂混合均匀,得到sio2杂化环氧树脂胶黏剂。
8.进一步的,步骤一中所述硅烷偶联剂为γ-(2,3环氧丙氧)丙基三甲氧基硅烷、γ-甲基丙烯酰氧基丙基三甲氧基硅烷中的一种或两种的混合物。
9.进一步的,步骤一中所述的硅酸酯为正硅酸乙酯、正硅酸丁酯、硅酸四异丙酯中的一种或其中几种的混合物。
10.进一步的,步骤一中所述的酸水溶液为盐酸水溶液、醋酸水溶液中的一种或两种的混合物。
11.进一步的,步骤一中所述的共溶剂为乙醇、异丙醇、乙酸乙酯或四氢呋喃。
12.进一步的,步骤一中所述的硅酸酯与硅烷偶联剂的摩尔比为(1~3):3。
13.进一步的,步骤一中所述的共溶剂与硅酸酯的摩尔比为(1~3):1。
14.进一步的,步骤一中所述的催化剂的用量占硅酸酯与硅烷偶联剂总质量的0.5%~0.7%。
15.进一步的,步骤一中所述的酸水溶液的浓度为0.45mol/l,所述酸水溶液的加入量
占硅酸酯与硅烷偶联剂总质量的22%~25%。
16.进一步的,步骤一中按照制得的sio2杂化环氧树脂中sio2的质量分数为0.5%~5%的量,计算加入环氧树脂的质量。
17.进一步的,步骤一中所述的环氧树脂为双酚a型环氧树脂e-51、双酚a型环氧树脂e-44、双酚a型环氧树脂e-20、双酚s型环氧树脂、酚醛环氧树脂f-51、4,4
’‑
二氨基二苯甲烷环氧树脂的一种或其中几种的混合物。
18.进一步的,步骤二所述的胺类固化剂为脂肪族胺类固化剂、芳香族胺类固化剂、聚酰胺、聚醚胺中的一种或其中几种的混合物。
19.本发明的有益效果:
20.本发明方法中硅烷偶联剂对合成的硅溶胶进行表面改性。硅酸酯在水解后生成表面含羟基的二氧化硅无机网络,硅烷偶联剂与二氧化硅网络结构的表面羟基发生脱水缩合,起到了表面改性的作用,防止二氧化硅溶胶发生过度水解,进一步生长和团聚,从而提高了纳米粒子的分散度。使用偶联剂的另一个目的是通过偶联剂的架桥作用,由于偶联剂中含有环氧基、丙烯基等基团,能通过对二氧化硅溶胶的表面改性,使sio2表面连接有机结构,与环氧树脂发生化学键合和物理氢键,从而改善二氧化硅无机网络结构与有机相环氧树脂之间的相容性,提高纳米粒子在环氧树脂中的分散程度。将无机组份与有机组分紧密结合起来,发挥协同作用,来改善有机组分的性能。
21.本发明方法克服了现有共混sio2纳米粒子杂化环氧胶存在的纳米粒子分散不均匀的工艺缺陷,提高环氧胶粘接性能。本发明方法显著改善了sio2无机网络和环氧有机网络相容性,形成的ipn结构显著提高了环氧胶综合性能。在提高环氧树脂胶黏剂耐热性的同时,室温粘接性能也得到提高。
22.本发明采用溶胶凝胶法制备sio2杂化环氧树脂,制备的杂化环氧树脂室温、中高温剪切强度较未改性的环氧树脂都有较大的提升。室温剪切强度最高可达到40.02mpa,同时具有较好的中高温胶接性能和耐热性能。
附图说明
23.图1为纯环氧树脂固化物断裂面的sem图;
24.图2为实施例1sio2杂化环氧树脂固化物断裂面的sem图;
25.图3为实施例1sio2杂化环氧树脂固化物750℃热失重残留物sem照片。
具体实施方式
26.本发明技术方案不局限于以下所列举具体实施方式,还包括各具体实施方式间的任意组合。
27.具体实施方式一:本实施方式二氧化硅/环氧树脂无机有机杂化胶黏剂的制备方法,包括以下步骤:
28.步骤一、先将共溶剂加入到反应瓶中,然后加入硅酸酯和硅烷偶联剂,搅拌均匀,随后加入催化剂二月桂酸二丁基锡,开始加热,待反应物升温至55~60℃时,开始滴加酸水溶液,控制滴加速度使酸水溶液在20~30min内滴加完成,然后在55~60℃的温度下保温反应3~4h,之后再加入环氧树脂,混合均匀后在60~80℃真空旋蒸15~20min,最后在80~90
℃真空旋蒸20~30min,制得sio2杂化环氧树脂;
29.步骤二、将步骤一得到的sio2杂化环氧树脂和等当量的胺类固化剂混合均匀,得到sio2杂化环氧树脂胶黏剂。
30.硅酸酯之间,以及硅酸酯与偶联剂之间的反应都是以水解反应为前提,硅酸酯和偶联剂与h2o发生亲核反应,生成硅羟基(si-oh)结构,硅羟基进行缩合反应形成溶胶,缩聚反应又会重新生成h2o。h2o的加入量将影响水解缩合生成sio2无机网络反应的进行,当h2o加入量对于缩合反应的影响程度大于或者小于水解反应时,都不利于缩合反应的进行,影响sio2无机网络的形成。
31.本实施方式的反应体系中硅酸酯和偶联剂中的烷氧基并不会全部水解,两者发生缩聚反应时,烷氧基会对反应产生一定的阻碍作用,所以硅酸酯并不会完全参与到反应中去,反而会影响到最终sio2无机网络状态和稳定性。当硅酸酯用量过少时,相应偶联剂的则会过量,也会影响最终sio2无机网络的形成。
32.杂化树脂的制备要将共溶剂、水等小分子脱除,脱溶剂的温度也会影响sio2无机网络和环氧有机网络的相容性,当脱溶剂温度过低,溶剂不能够完全脱除,体系中存在小分子,影响无机网络的形成,或者无机网络形成不完全;当脱溶剂温度较高时,水解缩合反应过快,形成的sio2容易发生团聚形成宏观粒子,体系粘度不断增加,这使得纳米sio2在环氧树脂中的分散变得困难。
33.本发明二氧化硅/环氧树脂无机有机杂化胶黏剂固化后能形成无机有机杂化ipn结构,因而具有较佳的室温和高温胶接强度。
34.具体实施方式二:本实施方式与具体实施方式一不同的是:步骤一中所述硅烷偶联剂为γ-(2,3环氧丙氧)丙基三甲氧基硅烷、γ-甲基丙烯酰氧基丙基三甲氧基硅烷中的一种或两种的混合物。其它与具体实施方式一相同。
35.采用硅烷偶联剂改性无机填料表面,不同的偶联剂中含有氨基、环氧基、丙烯基等结构,偶联剂一端连接无机相,一端连接有机相,有效避免无机颗粒的团聚并可以使无机组分和基体树脂相容性更好。需要考虑硅烷偶联剂中有机基团与环氧树脂的相容程度和反应情况。其中有机基团为氨基的偶联剂会使环氧基发生开环反应,对于环氧树脂体系影响较大,且改性后的sio2无机网络无法在环氧树脂中均匀分散,呈现浑浊状态。其中有机基团为环氧基、丙烯基的偶联剂改性后的sio2无机网络在环氧树脂中均匀分散,sio2无机网络和环氧有机网络相容性较好。
36.具体实施方式三:本实施方式与具体实施方式一或二不同的是:步骤一中所述的硅酸酯为正硅酸乙酯、正硅酸丁酯、硅酸四异丙酯中的一种或其中几种的混合物。其它与具体实施方式一或二相同。
37.具体实施方式四:本实施方式与具体实施方式一至三之一不同的是:步骤一中所述的酸水溶液为盐酸水溶液、醋酸水溶液中的一种或两种的混合物。其它与具体实施方式一至三之一相同。
38.具体实施方式五:本实施方式与具体实施方式一至四之一不同的是:步骤一中所述的共溶剂为乙醇、异丙醇、乙酸乙酯或四氢呋喃。其它与具体实施方式一至四之一相同。
39.水、硅酸酯、偶联剂以及环氧树脂之间的相容性不好,因此溶胶-凝胶法制备硅杂化环氧树脂的过程中,需要加入合适的共溶剂,使有机相与无机前驱体具有良好的相容性。
除此之外,共溶剂对硅酸酯的水解缩聚反应以及硅溶胶的产率、粒径等都有影响,随着无机结构的增长,其在共溶剂中分散均匀,有助于sio2网络结构的形成,从而可以使改性树脂更好的体现出杂化材料的优良性能。当选用不当的共溶剂时,sio2无机网络与环氧树脂发生了分相,或是变为浑浊状态。
40.具体实施方式六:本实施方式与具体实施方式一至五之一不同的是:步骤一中所述的硅酸酯与硅烷偶联剂的摩尔比为(1~3):3。其它与具体实施方式一至五之一相同。
41.具体实施方式七:本实施方式与具体实施方式一至六之一不同的是:步骤一中所述的共溶剂与硅酸酯的摩尔比为(1~3):1。其它与具体实施方式一至六之一相同。
42.共溶剂的加入量很重要,使有机相与无机相之间的相容性更好,进而可以增大反应的程度。但当溶剂用量过多,各反应物之间发生反应的机会就会减小,但若溶剂用量过少,反应物无法充分溶解混合均匀,也就无法得到充分的反应,也会影响最终产物中的sio2无机网络。
43.具体实施方式八:本实施方式与具体实施方式一至七之一不同的是:步骤一中所述的催化剂的用量占硅酸酯与硅烷偶联剂总质量的0.5%~0.7%。其它与具体实施方式一至七之一相同。
44.催化剂用量同时影响水解和缩合反应速率,进而会影响最终生成sio2的形态。催化剂用量过大会使得缩合反应程度过快,体系中的sio2发生团聚,影响sio2无机网络和环氧有机网络相容性,形成宏观粒子,最终使得sio2杂化环氧树脂产物为浑浊状态。
45.具体实施方式九:本实施方式与具体实施方式一至八之一不同的是:步骤一中所述的酸水溶液的浓度为0.45mol/l,所述酸水溶液的加入量占硅酸酯与硅烷偶联剂总质量的22%~25%。其它与具体实施方式一至八之一相同。
46.具体实施方式十:本实施方式与具体实施方式一至九之一不同的是:步骤一中按照制得的sio2杂化环氧树脂中sio2的质量分数为0.5%~5%的量,计算加入环氧树脂的质量。其它与具体实施方式一至九之一相同。
47.具体实施方式十一:本实施方式与具体实施方式一至十之一不同的是:步骤一中所述的环氧树脂为双酚a型环氧树脂e-51、双酚a型环氧树脂e-44、双酚a型环氧树脂e-20、双酚s型环氧树脂、酚醛环氧树脂f-51、4,4
’‑
二氨基二苯甲烷环氧树脂的一种或其中几种的混合物。其它与具体实施方式一至十之一相同。
48.具体实施方式十二:本实施方式与具体实施方式一至十一之一不同的是:步骤二所述的胺类固化剂为脂肪族胺类固化剂、芳香族胺类固化剂、聚酰胺、聚醚胺中的一种或其中几种的混合物。其它与具体实施方式一至十一之一相同。
49.下面对本发明的实施例做详细说明,以下实施例在以本发明技术方案为前提下进行实施,给出了详细的实施方案和具体的操作过程,但本发明的保护范围不限于下述的实施例。
50.实施例一:
51.本实施例二氧化硅/环氧树脂无机有机杂化胶黏剂的制备方法,包括以下步骤:
52.一、先将0.61g异丙醇加入反应瓶中,然后加入2.08g的正硅酸乙酯与7.08g的kh-560,搅拌均匀,随后加入0.06g的催化剂二月桂酸二丁基锡dbtdl,开始加热,待反应物升温至60℃时,开始逐滴滴加2.2g 0.45mol/l的盐酸水溶液,30min内滴加完成,然后在60℃保
温反应4h,之后加入214g e-51环氧树脂,混合均匀后在75℃真空旋蒸15min,最后在90℃真空旋蒸30min,冷却至室温,制得sio2含量为1%的杂化环氧树脂。
53.二、按重量份数将77份的sio2杂化环氧树脂合23份的聚醚胺d230混合均匀,得到sio2杂化环氧树脂胶黏剂。
54.本实施例步骤一中所述的真空旋蒸的真空度均为0~-0.1mpa。
55.测试本实施例的sio2杂化环氧树脂胶黏剂的剪切强度,粘接试片为铝合金试片,固化压力为0.03~0.1mpa,固化温度为60℃/2h+100℃/2h+150℃/2h,按gb/t7124-2008标准进行室温、80℃、120℃条件下的剪切强度测试,测试结果分别为40.02mpa、30.21mpa、9.64mpa。采用相同工艺,测定环氧树脂e-51与聚醚胺d230体系在室温、80℃、120℃条件下的剪切强度分别为31.45mpa,20.46mpa、6.15mpa。
56.纯环氧树脂、本实施例的sio2杂化环氧树脂固化物断裂面sem图分别如图1和图2所示,从图中可以观察到,纯环氧树脂固化物断裂面光滑,存在着条状锐利裂纹,呈现出明显的脆性破坏特征;sio2杂化环氧固化物断裂面呈均相结构,表现出明显的韧性断裂特征,没有观察到无机粒子析出,这说明杂化树脂中有机网络与无机网络之间相容性较好。
57.本实施例sio2杂化环氧树脂固化物750℃热失重残留物sem照片如图3所示,可以看到无机组份以连续而紧密的网状结构形式存在,而非团聚或粉末状态的sio2无机相,这种形态也说明了二氧化硅杂化环氧树脂在固化过程中,无机、有机两个网络之间形成共连续结构,形成了ipn结构。
58.实施例二:
59.本实施例二氧化硅/环氧树脂无机有机杂化胶黏剂的制备方法,包括以下步骤:
60.一、先将0.61g异丙醇加入反应瓶中,然后加入2.08g的正硅酸乙酯与7.08g的kh-560,搅拌均匀,随后加入0.06g的催化剂二月桂酸二丁基锡dbtdl,开始加热,待反应物升温至55℃时,逐滴滴加2.2g 0.45mol/l的盐酸水溶液,30min内滴加完成,然后在55℃保温反应4h,之后再加入214g e-51环氧树脂,混合均匀后在80℃真空旋蒸15min,最后在90℃真空旋蒸30min,冷却至室温,制得sio2含量为1%的杂化环氧树脂。
61.二、按重量份数将85份的sio2杂化环氧树脂合15份的间苯二甲胺混合均匀,得到sio2杂化环氧树脂胶黏剂。
62.本实例步骤一中所述的真空旋蒸的真空度均为0~-0.1mpa。
63.测试本实施例的sio2杂化环氧树脂胶黏剂的剪切强度,粘接试片为铝合金试片,固化压力为0.03~0.1mpa,固化温度为70℃/2h+100℃/2h+120℃/2h,按gb/t7124-2008标准进行室温、80℃、120℃条件下的剪切强度测试,测试结果分别为30.89mpa、28.86mpa、27.85mpa。采用相同工艺,测定环氧树脂e-51与间苯二甲胺体系在室温、80℃、120℃条件下的剪切强度分别为25.45mpa,27.00mpa、20.04mpa。
64.实施例三:
65.本实施例二氧化硅/环氧树脂无机有机杂化胶黏剂的制备方法,包括以下步骤:
66.一、先将0.61g异丙醇加入反应瓶中,然后加入2.08g的正硅酸乙酯与7.08g的kh-560,搅拌均匀,随后加入0.06g的催化剂二月桂酸二丁基锡dbtdl,开始加热,待反应物升温至60℃时,逐滴滴加2.2g 0.45mol/l的盐酸水溶液,30min内滴加完成,然后在60℃保温反应3h,之后再加入214g e-51环氧树脂,混合均匀后在75℃真空旋蒸20min,最后在90℃真空
旋蒸30min,冷却至室温,制得sio2含量为1%的杂化环氧树脂。
67.二、按重量份数将89份的sio2杂化环氧树脂合11份的三乙烯四胺混合均匀,得到sio2杂化环氧树脂胶黏剂。
68.本实例步骤一中所述的真空旋蒸的真空度均为0~-0.1mpa。
69.测试本实施例的sio2杂化环氧树脂胶黏剂的剪切强度,粘接试片为铝合金试片,固化压力为0.03~0.1mpa,固化温度为55℃/2h+90℃/2h+120℃/2h,按gb/t7124-2008标准进行室温、80℃、120℃条件下的剪切强度测试,测试结果分别为18.33mpa、18.62mpa、19.74mpa。采用相同工艺,测定环氧树脂e-51与三乙烯四胺体系在室温、80℃、120℃条件下的剪切强度分别为16.27mpa,14.86mpa、17.43mpa。
70.实施例四:
71.本实施例二氧化硅/环氧树脂无机有机杂化胶黏剂的制备方法,包括以下步骤:
72.一、先将0.61g异丙醇加入反应瓶中,然后加入2.08g的正硅酸乙酯与7.08g的kh-560,搅拌均匀,随后加入0.06g的催化剂dbtdl,开始加热,待反应物升温至60℃时,逐滴滴加2.2g 0.45mol/l的盐酸水溶液,30min内滴加完成,然后在60℃保温反应4h,之后再加入438g e-51环氧树脂,混合均匀后在80℃真空旋蒸15min,最后在90℃真空旋蒸25min,冷却至室温,制得sio2含量为0.5%的杂化环氧树脂。
73.二、按重量份数将77份的sio2杂化环氧树脂合23份的聚醚胺d230混合均匀,得到sio2杂化环氧树脂胶黏剂。
74.本实例步骤一中所述的真空旋蒸的真空度均为0~-0.1mpa。
75.测试本实施例的sio2杂化环氧树脂胶黏剂的剪切强度,粘接试片为铝合金试片,固化压力为0.03~0.1mpa,固化温度为60℃/2h+100℃/2h+150℃/2h,按gb/t7124-2008标准进行室温、80℃、120℃条件下的剪切强度测试,测试结果分别为35.85mpa、31.61mpa、8.21mpa。采用相同工艺,测定环氧树脂e-51与聚醚胺d230体系在室温、80℃、120℃条件下的剪切强度分别为31.45mpa,20.46mpa、6.15mpa。
76.实施例五:
77.本实施例二氧化硅/环氧树脂无机有机杂化胶黏剂的制备方法,包括以下步骤:
78.一、先将0.61g异丙醇加入反应瓶中,然后加入2.08g的正硅酸乙酯与7.08g的kh-560,搅拌均匀,随后加入0.06g的催化剂dbtdl,开始加热,待反应物升温至60℃时,逐滴滴加2.1g 0.45mol/l的盐酸水溶液,30min内滴加完成,然后在60℃保温反应4h,之后再加入107g e-51环氧树脂,混合均匀后在75℃真空旋蒸20min,最后在90℃真空旋蒸30min,冷却至室温,制得sio2含量为2%的杂化环氧树脂。
79.二、按重量份数将77份的sio2杂化环氧树脂合23份的聚醚胺d230混合均匀,得到sio2杂化环氧树脂胶黏剂。
80.本实例步骤一中所述的真空旋蒸的真空度均为0~-0.1mpa。
81.测试本实施例的sio2杂化环氧树脂胶黏剂的剪切强度,粘接试片为铝合金试片,固化压力为0.03~0.1mpa,固化温度为60℃/2h+100℃/2h+150℃/2h,按gb/t7124-2008标准进行室温、80℃、120℃条件下的剪切强度测试,测试结果分别为33.60mpa、30.45mpa、8.54mpa。采用相同工艺,测定环氧树脂e-51与聚醚胺d230体系在室温、80℃、120℃条件下的剪切强度分别为31.45mpa,20.46mpa、6.15mpa。