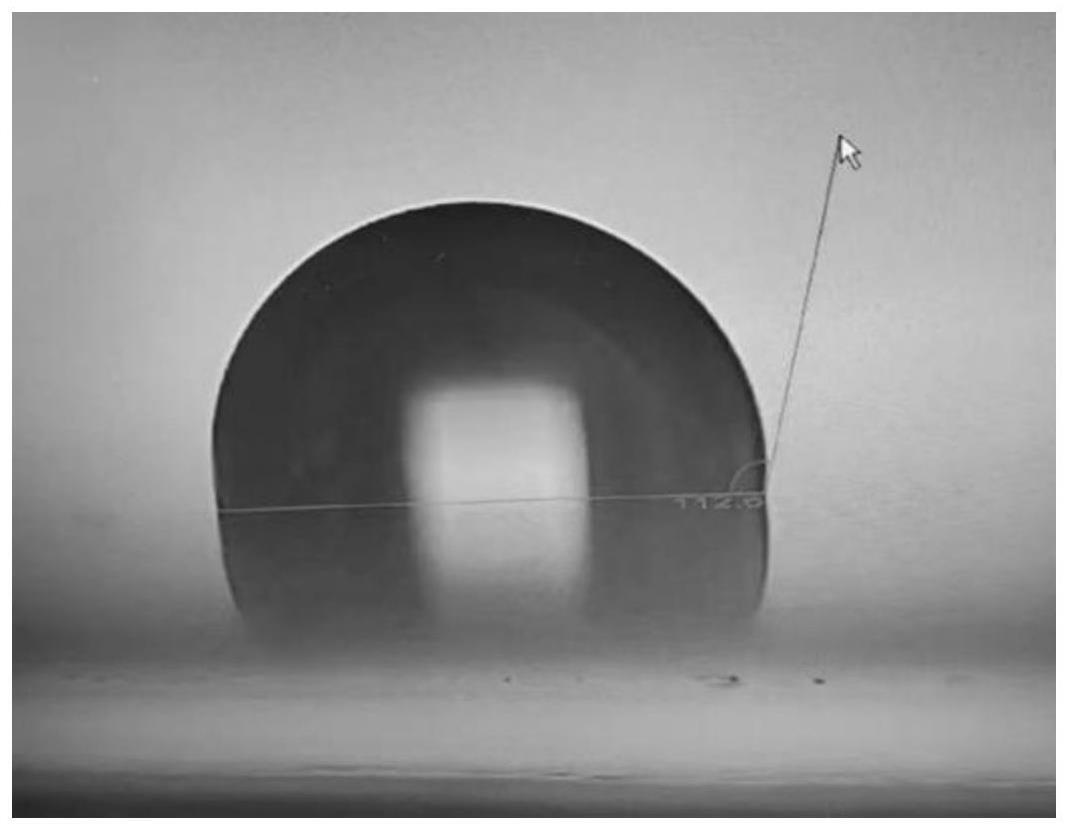
1.本发明涉及高分子涂料技术领域,更具体地,涉及一种反复脱模用铝合金模板涂料及其制备方法和应用。
背景技术:2.在使用过程中,铝合金模板与混凝土长期直接接触或铝合金模板多次循环使用都容易造成铝合金模板表面发生腐蚀,铝合金模板的表面质量和模板强度均会出现下降,同时由于铝合金模板与凝固的混凝土粘接牢固,在脱模过程中铝合金模板容易因受力而发生变形,这会影响铝模板的循环使用,因此在现有的混凝土工程中,铝合金模板常采用现场刷涂脱模剂的施工方式;但在实际操作过程中,脱模剂质量的参差不齐、未正确选用和使用脱模剂,都会导致铝合金模板拆模时沾掉混凝土表皮,造成混凝土脱皮麻面、气泡密而多等现象。
3.在铝合金模板表面镀膜可以避免使用脱模剂产生的缺陷,如中国专利cn109486324b公开了一种镀膜铝合金模板及其镀膜工艺,所述镀膜铝合金模板包括铝合金模板基材和涂层;所述镀膜铝合金模板即将铝合金模板基材进行表面抛丸、清洗和干燥,经过涂料喷涂和固化所得;所述涂料由以下重量百分比原料制得:丙烯酸树脂30%~45%、氨基树脂漆14%~22%、高耐候颜料15%~40%、稀释溶剂10%~15%、高分子分散剂0.5%~1.5%、防沉剂0.5%~0.8%和高速流平剂0.8%~1.2%;同时该发明改进现有的镀膜工艺,在抛丸、清洗和干燥后的铝合金模板基材表面喷涂丙烯酸树脂、氨基树脂漆和高耐候颜料等表面处理材料,树脂固化后制得具有重复使用次数高、混凝土成型效果好和易脱模的镀膜铝合金模板。但是该涂料的固化温度太高,为145~185℃,其对比例证明了,如果固化温度降低至105℃,将会导致涂层的附着能力差、涂层松散;且该涂层的施工复杂,限制了其应用。
技术实现要素:4.针对以上现有技术的不足,本发明的目的之一是提供一种反复脱模用铝合金模板涂料,该涂料对铝合金模板具有极佳的附着力,且具有极低的表面张力,耐冲击;将所述涂料涂刷至铝合金模板表面,固化温度低,固化后形成的涂层对铝合金模板的附着力好,不易脱落;且具有极低的表面张力使其不易粘附混凝土,易于脱模;形成的涂层耐冲击性好,可提高重复脱模的次数。
5.本发明的上述目的是通过以下技术方案实现的:
6.一种反复脱模用铝合金模板涂料,包括以下重量份数的各组分:丙烯酸树脂25~30份、二氧化硅胶体的乙醇分散液8~12份、feve树脂15~25份、填料35~65份、聚二甲基硅氧烷0.1~0.5份、三乙醇胺0.01~0.2份、烯丙基磺酸钠2~5份、有机氟硅烷5~7份、溶剂11~20份、消泡剂0.1~0.5份。
7.feve树脂为三氟氯乙烯单体与环己基乙烯醚、羟丁基乙烯基醚、烷基乙烯基醚的
共聚物,三氟氯乙烯单体与乙烯基醚单体交替连接,三氟氯乙烯单体把乙烯基醚单体从两侧包围,该树脂具有较低的表面张力和优异的耐候性和防腐性能。二氧化硅胶体的乙醇分散液在涂料干燥固化过程汇总絮凝沉淀为纳米级填料,可以降低涂料的表面能,提高疏水性。本发明采用低表面能的feve树脂作为成膜物质,使其固化成膜后具有极低的表面张力,同时对铝合金模板具有极佳的附着力,同时还可以耐酸、碱、盐等化学物质侵蚀。利用聚二甲基硅氧烷、三乙醇胺、烯丙基磺酸钠和有机氟硅烷对填料进行表面活化,使其具有更低的表面张力和更好的润湿性,从而可以更均匀的分散于树脂基料中,起到降低涂层表面张力的作用。涂层固化后,涂膜表面及其内部物质结构疏水疏油,使铝合金模板不易与混凝土粘结。而且填料具有较高的硬度,可以有效抵抗混凝土浇筑过程中对模板的摩擦、碰撞、冲击等机械损伤,保持表面脱模功能的长期有效性。本发明在低表面能的树脂与活化后的填料的共同作用下,制备出硬度高、耐冲击、不易粘结混凝土的涂层,避免混凝土浇筑和熟化过程中的破坏和腐蚀。
8.优选的,所述填料包括玻璃微珠、聚丙烯微粒、硫酸钡、纳米二氧化硅、高岭土和氧化铝粉末。其中,氧化铝粉末和玻璃微珠主要起耐磨作用,提高涂层的耐磨性;其它填料的主要作用是进行大分子有机物的填充,使得体系的疏水性好。
9.更优选的,所述氧化铝粉末和玻璃微珠的粒径为150~300目,所述聚丙烯微粒、硫酸钡、纳米二氧化硅和高岭土的粒径为80~3000目。
10.更优选的,所述玻璃微珠、聚丙烯微粒、硫酸钡、纳米二氧化硅、高岭土和氧化铝粉末的质量比为(5~6):(13~23):(6~9):(1~5):(6~9):(3~10)。
11.优选的,所述溶剂包括丙二醇甲醚乙酸酯、乙酸乙酯和乙二醇丁醚,三者质量比为(5~6):(3~5):(3~5)。
12.本发明的另一目的在于提供所述反复脱模用铝合金模板涂料的制备方法,包括以下步骤:
13.s1.按比例将丙烯酸树脂、二氧化硅胶体的乙醇分散液和feve树脂混合,搅拌均匀;
14.s2.按比例将填料、聚二甲基硅氧烷、三乙醇胺、烯丙基磺酸钠、有机氟硅烷和溶剂在60~80℃条件下搅拌30~60min;
15.s3.将步骤s1和s2得到的物料进行混合,再加入消泡剂,搅拌均匀即得到所述反复脱模用铝合金模板涂料。
16.优选的,步骤s1中,搅拌的条件为:在1000~1200rpm/min转速下搅拌10~30min。
17.本发明的再一目的在于提供所述的反复脱模用铝合金模板涂料在铝合金模板中的应用,使用方法如下:将所述涂料均匀涂覆于经过预处理的铝合金模板表面,在60~140℃下烘烤0.5~2h,使涂层固化后干膜厚度为30~60μm。
18.本发明的涂料涂覆在铝合金模板后的固化温度低,且施工便捷。固化后形成的涂层对铝合金模板的附着力好,不易脱落;且极低的表面张力使其不易粘附混凝土,易于脱模;形成的涂层耐冲击性好,可提高重复脱模的次数。
19.与现有技术相比,本发明的有益之处在于:
20.(1)本发明采用低表面能的feve树脂作为成膜物质,使其固化成膜后具有极低的表面张力,同时对铝合金模板具有极佳的附着力,同时可以耐酸、碱、盐等化学物质侵蚀。利
用聚二甲基硅氧烷、三乙醇胺、烯丙基磺酸钠和有机氟硅烷对填料进行表面活化,使其具有更低的表面张力和更好的润湿性,从而可以更均匀的分散于树脂基料中,起到降低涂层表面张力的作用。涂层固化后,涂膜表面及其内部物质结构疏水疏油,使铝合金模板不易与混凝土粘结。而且填料具有较高的硬度,可以有效抵抗混凝土浇筑过程中对模板的摩擦、碰撞、冲击等机械损伤,保持表面脱模功能的长期有效性。本发明利用低表面能的树脂与活化后的填料构建硬度高、耐冲击、不易粘结混凝土的涂层,避免混凝土浇筑和熟化过程中的破坏和腐蚀。
21.(2)本发明的涂料固化温度低,固化后的涂层对铝合金模板的附着力好,不易脱落,且具有极低的表面张力、耐酸碱、耐冲击,易脱模,可提高重复脱模的次数。
附图说明
22.图1为实施例1的涂料固化成膜后的水接触角示意图;
23.图2为实施例2的涂料固化成膜后的水接触角示意图;
24.图3为实施例3的涂料固化成膜后的水接触角示意图;
25.图4为对比例1的涂料固化成膜后的水接触角示意图;
26.图5为对比例2的涂料固化成膜后的水接触角示意图。
具体实施方式
27.下面将对本发明的技术方案进行清楚、完整地描述,显然,所描述的实施例仅仅是本发明一部分实施例,而不是全部的实施例。基于本发明中的实施例,本领域普通技术人员在没有做出创造性劳动条件下所获得的所有其它实施例,都属于本发明保护的范围。
28.以下实施例及对比例中,如无特殊说明,份数均代表重量份数。
29.feve树脂为三氟氯乙烯单体与环己基乙烯醚、羟丁基乙烯基醚、烷基乙烯基醚的共聚物,重均分子量为7000~12000。所述氧化铝粉末和玻璃微珠的粒径为150~300目,所述聚丙烯微粒、硫酸钡、纳米二氧化硅和高岭土的粒径为80~3000目。二氧化硅胶体的乙醇分散液的质量浓度为13%。
30.实施例1
31.本实施例提供一种反复脱模用铝合金模板涂料的制备方法,包括以下步骤:
32.s1.向搅拌机中加入丙烯酸树脂26份、二氧化硅胶体的乙醇分散液9份和feve树脂19份,在1000rpm/min的转速下搅拌20min;
33.s2.向反应釜中加入丙二醇甲醚乙酸酯5份、乙酸乙酯5份和乙二醇丁醚3份,再加入玻璃微珠5份、聚丙烯微粒18份、硫酸钡6份、纳米二氧化硅1.5份、高岭土6份、氧化铝粉末8份,聚二甲基硅氧烷0.3份、三乙醇胺0.1份、烯丙基磺酸钠3份、有机氟硅烷5份,然后在70℃下搅拌50min,搅拌速度为300rpm/min;
34.s3.将步骤s1和s2得到的物料进行混合,再加入不含有机硅的乙烯基聚合物消泡剂0.5份,在500rpm/min转速下搅拌15min,即得到所述反复脱模用铝合金模板涂料。
35.实施例2
36.本实施例提供一种反复脱模用铝合金模板涂料的制备方法,包括以下步骤:
37.s1.向搅拌机中加入丙烯酸树脂25份、二氧化硅胶体的乙醇分散液8份和feve树脂
25份,在1000rpm/min的转速下搅拌20min;
38.s2.向反应釜中加入丙二醇甲醚乙酸酯6份、乙酸乙酯4份和乙二醇丁醚3份,再加入玻璃微珠6份、聚丙烯微粒13份、硫酸钡9份、纳米二氧化硅5份、高岭土9份、氧化铝粉末10份,聚二甲基硅氧烷0.5份、三乙醇胺0.2份、烯丙基磺酸钠5份、有机氟硅烷7份,然后在60℃下搅拌30min,搅拌速度为500rpm/min;
39.s3.将步骤s1和s2得到的物料进行混合,再加入不含有机硅的乙烯基聚合物消泡剂0.5份,在500rpm/min转速下搅拌15min,即得到所述反复脱模用铝合金模板涂料。
40.实施例3
41.本实施例提供一种反复脱模用铝合金模板涂料的制备方法,包括以下步骤:
42.s1.向搅拌机中加入丙烯酸树脂30份、二氧化硅胶体的乙醇分散液8份和feve树脂15份,在1000rpm/min的转速下搅拌20min;
43.s2.向反应釜中加入丙二醇甲醚乙酸酯6份、乙酸乙酯3份和乙二醇丁醚4份,再加入玻璃微珠5份、聚丙烯微粒23份、硫酸钡6份、纳米二氧化硅2份、高岭土6份、氧化铝粉末3份,聚二甲基硅氧烷0.1份、三乙醇胺0.1份、烯丙基磺酸钠2份、有机氟硅烷5份,然后在80℃下搅拌60min,搅拌速度为200rpm/min;
44.s3.将步骤s1和s2得到的物料进行混合,再加入不含有机硅的乙烯基聚合物消泡剂0.1份,在500rpm/min转速下搅拌15min,即得到所述反复脱模用铝合金模板涂料。
45.实施例4
46.本实施例提供实施例1~3制备的反复脱模用铝合金模板涂料的使用方法,步骤如下:
47.对铝合金模板进行预处理,将涂料与hdi固化剂按质量比10:1进行混合,然后采用喷涂、滚涂或刷涂等方式将其均匀涂覆于铝合金模板表面,在80℃下烘烤1h,使涂层固化后干膜厚度为30~60μm。
48.对比例1
49.对比例1的反复脱模用铝合金模板涂料的制备方法与实施例1基本相同,区别之处仅在于,本对比例的步骤s1如下:向搅拌机中加入丙烯酸树脂45份和二氧化硅胶体的乙醇分散液9份,在1000rpm/min的转速下搅拌20min。即与实施例1相比,本对比例的涂料中不含feve树脂。
50.对比例2
51.本对比例提供一种反复脱模用铝合金模板涂料的制备方法,包括以下步骤:
52.s1.向搅拌机中加入丙烯酸树脂26份、二氧化硅胶体的乙醇分散液9份和feve树脂19份,在1000rpm/min的转速下搅拌20min;
53.s2.向反应釜中加入丙二醇甲醚乙酸酯5份、乙酸乙酯5份和乙二醇丁醚3份,再加入硫酸钡29份、纳米二氧化硅1.5份、高岭土6份、氧化铝粉末8份,聚二甲基硅氧烷0.3份、三乙醇胺0.1份、烯丙基磺酸钠3份、有机氟硅烷5份,然后在70℃下搅拌50min,搅拌速度为300rpm/min;
54.s3.将步骤s1和s2得到的物料进行混合,再加入不含有机硅的乙烯基聚合物消泡剂0.5份,在500rpm/min转速下搅拌15min,即得到所述反复脱模用铝合金模板涂料。
55.即与实施例1相比,本对比例的涂料中不含玻璃微珠和聚丙烯微粒,相应增加硫酸
钡的用量。
56.试验例
57.采用实施例4的使用方法将实施例1~3制备的涂料涂覆于铝合金模板上,然后测试涂层的各项性能,测试结果见表1。
58.其中,附着力根据gb/t 9286-1998《色漆和清漆漆膜的划格试验》的方法进行测试;
59.盐雾测试方法如下:采用5%的nacl水溶液作为喷雾用溶液进行中性盐雾试验。试验温度为30℃,试验时间为500h,溶液ph值调节在中性范围(6.5-7.2)。试验结束后,将样品取出清洗后进行观察。
60.耐冲击测试根据gb/t 1732-2020《漆膜耐冲击测定法》的方法进行测试;
61.反复脱模,每次模板表面混凝土粘附量不大于5g/m2,则代表顺利脱模;
62.表1测试结果
[0063][0064]
从表1的测试结果可知,本发明实施例1~3制备的涂料固化后的涂层对铝合金模板具有极佳的附着力,不易发生涂层脱落。此外,本发明的涂层的耐腐蚀性能优异,盐雾测试未出现腐蚀现象,可避免模板基材受到侵蚀。
[0065]
本发明采用低表面能的树脂,并对填料进行表面活化,使得涂层的表面张力低、疏水,水接触角大,使得混凝土不易粘附在涂层表面,利于脱模。
[0066]
实施例1~3的涂层反复脱模的次数最高可达到98次,说明本发明的涂料固化后的涂层可反复脱模,且不粘附混凝土。同时,涂层洗刷1000次后表面张力的变化值较小,说明表层磨损后,内部结构仍具有较好的疏水疏油效果;表明本发明的涂料固化后,涂膜的表面及其内部物质结构均疏水疏油。
[0067]
与实施例1相比,对比例1的涂料不含fave树脂,涂层表面张力较高,疏水疏油性能变差,导致混凝土无法顺利从模板上脱下来。对比例2的填料中缺少玻璃微珠和聚丙烯微粒,由于填料的结构和表面活化程度发生变化,导致水接触角减小,洗刷1000次后涂层表面
张力明显增大,同时由于耐磨性降低和涂层内部填料颗粒表面能的不同导致脱模次数显著减少。
[0068]
综上,将本发明的涂料应用于铝合金模板表面,固化温度低,固化后形成的涂层对铝合金模板的附着力好,不易脱落;且具有极低的表面张力使其不易粘附混凝土,易于脱模;形成的涂层耐冲击性、耐磨性能好,且磨损后涂层表面张力变化值小,可提高重复脱模的次数。
[0069]
尽管已经示出和描述了本发明的实施例,对于本领域的普通技术人员而言,可以理解在不脱离本发明的原理和精神的情况下可以对这些实施例进行多种变化、修改、替换和变型,本发明的范围由所附权利要求及其等同物限定。