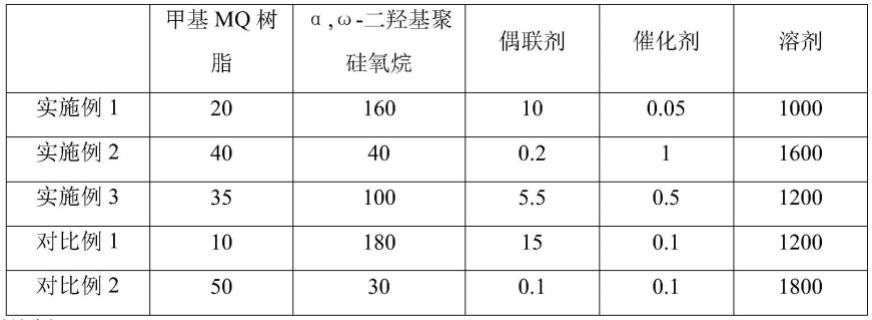
1.本技术涉及硅橡胶表面处理技术的领域,尤其是涉及一种硅橡胶表面处理剂及其制备方法。
背景技术:2.硅胶材料是一种常用的化工制品,其具有耐高温、易清洗、使用寿命长、环保无毒等特性而受到广泛的关注和应用,同时其具有良好的电绝缘性能、耐低温性能、耐候性、导热性和抗辐射性,其凭借着优秀的性质占据大量市场,在生活中各个领域均具有广泛的应用。硅胶制品在运用中为了增强其与所接触机体之间的连接力,通常需要在表面贴附胶带,以满足其粘接要求。但是硅胶为非极性材料,其表面比较细腻光滑,具有很低的表面活性和生理惰性,普通胶带在硅胶制品表面的粘附力很弱,难以满足正常的粘接需求,所以在粘接前需要使用硅胶表面处理剂进行表面处理。
3.硅胶表面处理剂专用于硅橡胶材料的表面处理,能有效改善硅橡胶材质的表面极性,大大提高粘接性能。公开号为cn113462349a的中国专利申请公开了一种硅胶与3m双面胶粘合处理剂及其制备方法,其中的处理剂包括有机硅压敏胶30-60份,硅树脂10-20份,偶联剂5-10份,溶剂40-70份,以有机硅压敏胶作为基材来达到与硅胶的粘合性,并通过加入偶联剂促进有机硅压敏胶的固化进而在硅胶表面形成一层粘合层,以满足与3m双面胶的粘合。上述现有技术中,使用有机硅压敏胶作为基材,经过其处理的硅胶制品表面会具有一定的粘附性,使得处理剂处理后的硅胶制品的存放管理带来了很大的不便,增加了处理剂处理后硅胶制品的存放管理成本。
技术实现要素:4.为了降低硅胶表面处理剂处理后硅胶制品的表面粘性,提升存放和实施过程的便捷性,本技术提供一种硅橡胶表面处理剂及其制备方法,第一方面,本技术提供一种硅橡胶表面处理剂,采用如下的技术方案:一种硅橡胶表面处理剂,包括以下重量份的原材料:甲基mq树脂20~40份;α,ω-二羟基聚硅氧烷40~160份;偶联剂0.2~10份;催化剂0.05~1份;以及溶剂1000~1600份。
5.通过采用上述技术方案,利用甲基mq树脂补强α,ω-二羟基聚硅氧烷,并通过添加偶联剂引入部分端羟基形成处理剂的基料。以α,ω-二羟基聚硅氧烷作为基料,再结合羟基树脂的补强性和羟基官能团反应,替换现有技术中直接使用压敏胶作为主胶的方法,使固化后的基料既能够达到胶料自身的强度,还可以大大降低直接现有技术中因直接使用压敏胶带来的表面粘性,使得经过硅橡胶表面处理剂处理过的硅胶基材便于储存放置,降低存
放管理成本。
6.可选的,所述偶联剂包括胺类偶联剂和异氰酸酯偶联剂;所述胺类偶联剂和异氰酸酯类偶联剂的质量比为1:1。
7.进一步优选,所述胺类偶联剂为双(3-三甲氧基甲硅烷基丙基)胺;所述异氰酸酯类偶联剂为(3-异氰基丙基)三乙氧基硅烷。
8.通过采用上述技术方案,所用的胺类偶联剂其结构上每个氨基都连接有双硅烷基和硅烷结构,其中的胺类基团可以作为异氰酸酯类偶联剂的引发剂而引发异氰酸酯类偶联剂中的异氰酸酯和水反应,后续胺类偶联剂自身再与基料聚合物产生肽键类化学键合,达到扩链的作用,并同时释放出甲硅基部分,与硅胶表面集团形成强固的键合力。(3-异氰基丙基)三乙氧基硅烷其上含有异氰酸酯和乙氧基两种不同活性基团,在胺类偶联剂的催化作用下,异氰酸酯结构和水分子反应生成不稳定的氨基甲酸,然后由氨基甲酸分解出胺,进一步继续催化反应;而反应同时另一端的活性基团乙氧基可以偶联有机分子和无机填料,增强其粘基性。通过两种催化剂的配合释放活性基团,不仅使分子扩链提升力学性能,还可使得两种偶联剂中活性基团完全释放,进一步提升基料的粘基性的同时,还可以有效缩短固化成型所需的时间。两种相互催化偶联反应的偶联剂配合使用,在溶剂挥发过程,空气中的水分配合钛酸酯类催化剂形成正促进催化效果,使处理剂快速固化在硅橡胶表面形成多活性基团薄膜。
9.可选的,所述α,ω-二羟基聚硅氧烷的羟基含量为0.5~3.0%。
10.进一步优选,所述α,ω-二羟基聚硅氧烷包括a类α,ω-二羟基聚硅氧烷和b类α,ω
ꢀ‑
二羟基聚硅氧烷,所述a类α,ω-二羟基聚硅氧烷为粘度为1000~50000mpa
·
s的α,ω-二羟基聚硅氧烷,所述b类α,ω-二羟基聚硅氧烷为分子量为60w~90w的α,ω-二羟基聚硅氧烷。
11.进一步优选,所述a类α,ω-二羟基聚硅氧烷的占比为20~80wt%,余量为b类α,ω
ꢀ‑
二羟基聚硅氧烷。
12.通过采用上述技术方案,α,ω-二羟基聚硅氧烷是一种低粘性大分子材料,使用其代替压敏胶作为硅橡胶表面处理剂的基料,再结合甲基mq树脂补强和羟基官能团反应,可以有效提升制得的处理剂的强度并大大降低处理剂的表面粘性,进而提升生产工艺的便捷性,并且便于经处理剂处理后硅橡胶制品的存放管理。通过两种不同分子量和粘度的α,ω-二羟基聚硅氧烷配合使用,可以有效提升制得的处理剂胶料的粘度和强度,提升对硅橡胶的处理效果。
13.可选的,所述溶剂包括异构十二烷和白电油中的至少一种。
14.进一步优选,所述溶剂包括异构十二烷和白电油,异构十二烷和白电油的质量比为1: (1.25~1.5)。
15.通过采用上述技术方案,异构十二烷和白电油作为处理剂的溶剂使用,可以有效降低制得的硅橡胶处理剂的刺激性气味和毒害性,并且由于白电油具有极高的挥发性,可以加快硅橡胶表面处理剂的挥发速度,有效提升固化时间。异构十二烷和白电油作为溶剂对丙烯酸等双面胶的溶解破坏性小,可以有效降低对硅橡胶粘接胶的损坏,提升粘接强度,防止产品出现点腐蚀和危害性,使产品能应用于更高要求的场景。
16.可选的,所述催化剂为酞酸酯类催化剂。
17.进一步优选,所述催化剂为钛酸四丁酯、钛酸异丁酯、钛酸异丙酯中的任意一种。
18.通过采用上述技术方案,通过酞酸酯类催化剂催化基料反应,使基料快速成型并让活性基团迅速在硅橡胶表面或者无机基材表面形成强力键合,使得双面胶或者其它基材在硅橡胶制品表面具有良好的粘接效果。
19.可选的,所述甲基mq树脂为缩合型甲基mq树脂,m/q比值为0.5~1.2,分子量为 2000~7000,羟基含量为3.0~5.0%。
20.第二方面,本技术提供一种硅橡胶表面处理剂的制备方法,采用如下的技术方案:一种硅橡胶表面处理剂的制备方法,包括以下步骤:s1、将甲基mq树脂和α,ω-二羟基聚硅氧烷在50~60℃下混合均匀;s2、升温至65~120℃,加入偶联剂搅拌混合反应1~3h;s3、降温至室温,加入溶剂,搅拌混合均匀,然后加入催化剂,混合均匀后,抽真空,过滤,得到硅橡胶表面处理剂。
21.可选的,步骤s2包括:升温至65~70℃,加入胺类偶联剂搅拌反应1~1.5h,然后继续升温至110~120℃加入异氰酸酯类偶联剂,继续搅拌反应1.5~2h。
22.通过采用上述技术方案,在制备过程中,以α,ω-二羟基聚硅氧烷为基料,再以少量的羟基树脂填充补强,替换传统直接使用压敏胶为主胶系列的方法,使固化后的基料既能达到胶料自身强度还能大大降低直接使用压敏胶带来的表面粘性,使处理过后的硅胶基材便于储存放置,提升工艺简单化和可操作化。
23.综上所述,本技术包括以下至少一种有益技术效果:1.本技术技术方案中,以α,ω-二羟基聚硅氧烷为基料,再以少量的羟基树脂填充补强,替换传统直接使用压敏胶为主胶系列的方法,使固化后的基料既能达到胶料自身强度还能大大降低直接使用压敏胶带来的表面粘性,使处理过后的硅胶基材便于储存放置,提升工艺简单化和可操作化。
24.2.本技术技术方案中,两种相互催化偶联反应的偶联剂配合使用,胺类偶联剂中的胺可作为异氰酸酯反应的引发剂,使异氰酸酯偶联剂和水反应的同时,释放出自身的活性基团。而异氰酸酯和水反应生成不稳定的氨基甲酸,然后由氨基甲酸分解释放胺,进一步继续催化反应,同时释放出活性基团,这不仅加快了反应中期的分子扩链反应,还能保证两种偶联剂中活性基团完全释放,缩短了固化成型所需时间的同时,还可以达到硅胶与双面胶或其他基材良好的粘接效果。
25.3.使用异构十二烷混合白电油混配做溶剂,替换掉苯类溶剂使用,一方面是降低刺激性气味和苯环类溶剂带来的毒性,也优化了其他溶剂对丙烯酸一类双面胶的溶解性,防止产品出现点腐蚀和危害性,使产品能更好的应用于医疗基材方面等更高要求的应用场景。
具体实施方式
26.以下结合具体实施例对本技术作进一步详细说明。
27.实施例1一种硅橡胶表面处理剂,组分配比参见表1,具体制备方法如下:s1、按配比取甲基mq树脂和α,ω-二羟基聚硅氧烷加入反应釜,加热至60℃搅拌反
应 30min;甲基mq树脂的分子量为2000~7000,m/q比值为0.5,羟基含量为3.0%;α,ω-二羟基聚硅氧烷的羟基含量为0.5%,分子量为60w~70w;s2、反应釜升温至70℃,加入双(3-三甲氧基甲硅烷基丙基)胺,搅拌反应1h;s3、反应釜降温至室温,加入异构十二烷并搅拌混合均匀后加入钛酸四丁酯催化剂,搅拌混合均匀;s4、混合物抽真空、过滤,然后出料分装,得到硅橡胶表面处理剂。
28.实施例2一种硅橡胶表面处理剂,组分配比参见表1,具体制备方法与实施例1保持一致。
29.实施例3一种硅橡胶表面处理剂,组分配比参见表1,具体制备方法与实施例1保持一致。
30.对比例1一种硅橡胶表面处理剂,组分配比参见表1,具体制备方法与实施例1保持一致。
31.对比例2一种硅橡胶表面处理剂,组分配比参见表1,具体制备方法与实施例1保持一致。
32.表1:实施例1~3及对比例1~2组分配比(单位:g)对比例3以公开号为cn113462349a、发明名称为“一种硅胶与3m双面胶粘合处理剂及制备方法”的中国发明专利中记载的方法制备硅橡胶表面处理剂,作为对比例1。组分配比为:529有机硅压敏胶60g,mq硅树脂20g,550偶联剂5g,560偶联剂10g,白电油70g。
33.对比例4一种硅橡胶表处理剂,与实施例1的区别在于,选用二甲苯代替异构十二烷作为溶剂,其余均与实施例1保持一致。
34.性能检测对实施例1~3及对比例1~4中制得的硅橡胶表面处理剂样品进行性能检测,检测结果见下表 2。检测项目如下:1、粘结性能:取两块硅胶片,表面清理干净,将硅橡胶表面处理剂样品涂覆与清理干净的硅胶片表面并静置使其完全固化,然后将3m双面胶贴于两块经过处理的硅胶片表面之间,压紧、压牢后放置24h,然后使用180
°
剥离力测试机测试剥离力。
35.2、表面粘性:取两块硅胶片,表面清理干净,将硅橡胶表面处理剂样品涂覆与清理干净的硅胶片表面并静置使其完全固化,然后将两块硅胶片经过处理的一面相对贴合,通
过观察两块硅胶片是否可以稳定粘接来判断是否具有粘性。
36.表2:实施例1~3级对比例1~4性能检测结果通过表2中的数据可以看出,本技术技术方案提供的硅橡胶表面处理剂处理后的硅胶表面无粘性,经过其处理的硅胶方便保存,没有相互粘接的风险;并且经其处理后的硅胶表面具有很好的粘结性能,3m双面胶在其上可以很好粘接。另外,与对比例4相比,本技术技术方案中提供的硅橡胶表面处理剂对双面胶的无破坏效果,不会导致双面胶的强度降低。
37.进一步,对实施例1~3和对比例2中的硅橡胶表面处理剂样品的固化时长进行检测,以验证其固化性能。检测方法如下:取5块硅胶片,表面清理干净,依次编号为样品1、样品2、样品3、样品4和样品5,每块硅胶片表面均匀涂覆硅橡胶表面处理剂,样品1~5依次静置2min、5min、10min、20min和30min,静置结束后在硅胶片经硅橡胶表面处理剂处理的一侧贴附3m双面胶并压紧压实后立即使用180
°
剥离力测试机测试剥离力。测试结果见下表3。
38.表3:实施例1~3及对比例3固化性能检测结果通过表3中的数据可以下可能出,本技术技术方案中的硅橡胶表面处理剂在10min后已经完全固化,经处理后的硅胶表面达到稳定的粘接效果;而对比例3中公开的硅橡胶表面处理剂,其固化时间超过20min,静置30min才能完全固化。经过对比,本技术技术方案中制得的硅橡胶表面处理剂,具有更快的固化速率,对硅胶表面的处理效率更高。
39.以下实施例在实施例3的基础上对硅橡胶表面处理剂的性能进一步探究。
40.实施例4
一种硅橡胶表面处理剂,与实施例3的区别在于,选用分子量为80w~90w的α,ω-二羟基聚硅氧烷,其余均与实施例3保持一致。
41.实施例5一种硅橡胶表面处理剂,与实施例3的区别在于,α,ω-二羟基聚硅氧烷包括a类和b类, a类是粘度为1000pa
·
s的α,ω-二羟基聚硅氧烷,占比为20wt%,b类是分子量为 60w~70w的α,ω-二羟基聚硅氧烷,占比为80wt%,其余均与实施例3保持一致。
42.实施例6一种硅橡胶表面处理剂,与实施例5的区别在于,a类α,ω-二羟基聚硅氧烷的粘度为 50000pa
·
s,其余均与实施例5保持一致。
43.实施例7一种硅橡胶表面处理剂,与实施例5的区别在于,a类α,ω-二羟基聚硅氧烷的粘度为 25000pa
·
s,其余均与实施例5保持一致。
44.实施例8一种硅橡胶表面处理剂,与实施例5的区别在于,a类α,ω-二羟基聚硅氧烷的重量百分比为80%,b类α,ω-二羟基聚硅氧烷的重量百分比为20%,其余均与实施例5保持一致。
45.实施例9一种硅橡胶表面处理剂,与实施例5的区别在于,a类α,ω-二羟基聚硅氧烷的重量百分比为50%,b类α,ω-二羟基聚硅氧烷的重量百分比为50%,其余均与实施例5保持一致。
46.实施例10一种硅橡胶表面处理剂,与实施例5的区别在于,a类α,ω-二羟基聚硅氧烷的重量百分比为90%,b类α,ω-二羟基聚硅氧烷的重量百分比为10%,其余均与实施例5保持一致。
47.对实施例4~10制得的硅橡胶表面处理剂的样品进行粘接性能检测,检测结果见下表 4。
48.表4:实施例4~10性能检测结果实施例4~10性能检测结果通过表1中的数据可以看出,两种不同规格的α,ω-二羟基聚硅氧烷配合使用,制
成的硅胶表面处理剂具有更好硅胶表面处理效果,双面胶在硅胶表面具有更强的粘接强度。
49.以下实施例在实施例7的基础上,对偶联剂对硅橡胶表面处理剂的固化性能做进一步的探究。
50.实施例11一种硅橡胶表面处理剂,与实施例7的区别在于,偶联剂为(3-异氰基丙基)三乙氧基硅烷,其余均与实施例7保持一致。
51.实施例12一种硅橡胶表面处理剂,与实施例7的区别在于,偶联剂包括质量比为1:1的双(3-三甲氧基甲硅烷基丙基)胺和双(3-异氰基丙基)三乙氧基硅烷,其它组分与实施例7相同,具体制备方法如下:s1、按配比取甲基mq树脂和α,ω-二羟基聚硅氧烷加入反应釜,加热至60℃搅拌反应 30min;s2、反应釜升温至70℃,加入双(3-三甲氧基甲硅烷基丙基)胺,搅拌反应1h;s3、反应釜继续升温至120℃,加入(3-异氰基丙基)三乙氧基硅烷,搅拌反应2h;s4、反应釜降温至室温,加入异构十二烷并搅拌混合均匀后加入钛酸四丁酯催化剂,搅拌混合均匀;s5、混合物抽真空、过滤,然后出料分装,得到硅橡胶表面处理剂。
52.实施例13一种硅橡胶表面处理剂,与实施例12的区别在于,双(3-三甲氧基甲硅烷基丙基)胺和双(3
‑ꢀ
异氰基丙基)三乙氧基硅烷的质量比为1:2,其余均与实施例12保持一致。
53.实施例14一种硅橡胶表面处理剂,与实施例12的区别在于,双(3-三甲氧基甲硅烷基丙基)胺和双(3
‑ꢀ
异氰基丙基)三乙氧基硅烷的质量比为2:1,其余均与实施例12保持一致。
54.参照前文的固化性能检测方法,对实施例11~14中的硅橡胶表面处理剂样品进行固化性能检测,检测结果见下表5。
55.表5:实施例11~14固化性能检测结果通过表5中的数据可以看出,胺类偶联剂和异氰酸酯偶联剂的配合使用,明显的提升了硅橡胶表面处理剂的固化速率。两种偶联剂配合使用以后,胺类偶联剂中的胺可作为异氰酸酯反应的引发剂,使异氰酸酯偶联剂和水反应的同时,释放出自身的活性基团。而异
氰酸酯和水反应生成不稳定的氨基甲酸,然后由氨基甲酸分解释放胺,进一步继续催化反应,同时释放出活性基团,这不仅加快了反应中期的分子扩链反应,还能保证两种偶联剂中活性基团完全释放,缩短了固化成型所需时间。从表中的数据看,硅橡胶表面处理剂涂覆在硅橡胶表面后,在2~5min内即可达到较好的固化效果,后续继续静置的过程中,粘接性能的变化幅度趋于放缓,说明硅橡胶表面处理剂在2~5min内已经基本完全固化。
56.进一步对实施例11~14中硅橡胶表面处理剂处理后的硅胶表面的粘接性能进行检测,检测结果见下表6。
57.表6:实施例11~14粘接性能检测结果 剥离力(gf/25mm)硅胶表面状态实施例111911硅胶完全撕破实施例122017硅胶完全撕破实施例121968硅胶完全撕破实施例141944硅胶完全撕破从表6中的数据可以看出,胺类偶联剂和异氰酸酯偶联剂的配合使用不仅可以加快硅橡胶表面处理剂的固化速率,还可以进一步提升处理后硅胶表面的粘接性能。并且,当胺类偶联剂和异氰酸酯偶联剂的按照1:1的质量比配合使用时,其效果最佳,处理后的硅胶表面粘接性能最优,双面胶粘合后剥离力可以达到2000gf/25mm以上,具有极佳的硅胶表面处理效果。
58.实施例15一种硅橡胶表面处理剂,与实施例12的区别在于,溶剂包括异构十二烷和白电油,异构十二烷和白电油的质量比为1:1.25,其余均与实施例12保持一致。
59.实施例16一种硅橡胶表面处理剂,与实施例15的区别在于,异构十二烷和白电油的质量比为1:1.5,其余均与实施例15保持一致。
60.实施例17一种硅橡胶表面处理剂,与实施例15的区别在于,异构十二烷和白电油的质量比为1:1,其余均与实施例15保持一致。
61.实施例18一种硅橡胶表面处理剂,与实施例3的区别在于,甲基mq树脂的分子量为3000~5000, m/q比值为1.2,羟基含量为5.0%,其余均与实施例3保持一致。
62.实施例19一种硅橡胶表面处理剂,与实施例18的区别在于,甲基mq树脂的分子量为3000~5000, m/q比值为1.0,羟基含量为4.0%,其余均与实施例3保持一致。
63.对实施例15~19中的硅橡胶表面处理剂样品进行性能检测,检测结果见下表7 表7:实施例15~19性能检测结果 剥离力(gf/25mm)硅胶表面状态实施例152126硅胶完全撕破实施例162119硅胶完全撕破实施例172043硅胶完全撕破
实施例181869硅胶完全撕破实施例191826硅胶完全撕破以上均为本技术的较佳实施例,并非依此限制本技术的保护范围,故:凡依本技术的结构、形状、原理所做的等效变化,均应涵盖于本技术的保护范围之内。