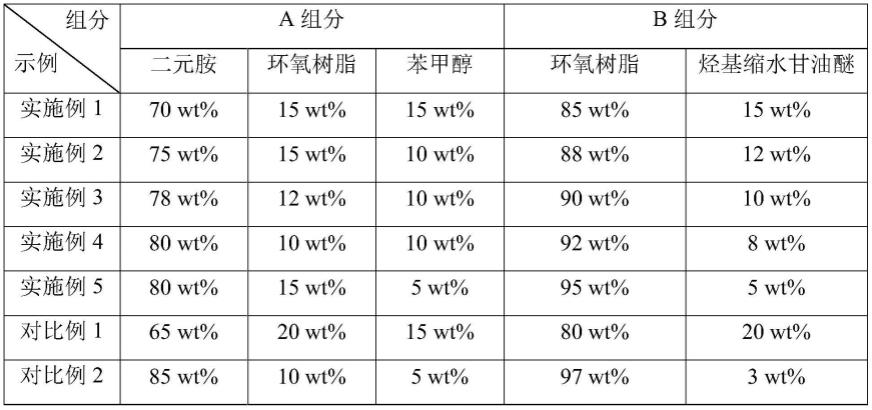
1.本技术涉及超耐磨涂料领域,尤其是涉及一种无溶剂环氧超耐磨涂料及其制备方法。
背景技术:2.环氧涂料是一种高分子聚合物涂料,具有高机械性能、低固化收缩率、优异的耐化学性、与其他基材粘合性好等优点,因而被广泛应用于设备、建筑、地坪等领域。
3.不过环氧涂料的耐磨性不够好,比如应用于耐磨性能要求很高的户外地坪时,其耐磨性能难以满足应用需求,因此通常会在环氧涂料面漆上再涂覆一层超耐磨涂层以保证地坪的耐磨性能,目前一般是在已经固化的环氧面漆上涂覆一层聚氨酯涂料,聚氨酯涂料耐磨性能优异,能够很好地满足对于耐磨性能要求很高的应用场景。
4.不过聚氨酯涂料与环氧涂料的层间附着力不佳,在将聚氨酯超耐磨涂料涂覆到环氧面漆上之前,需要将环氧漆膜打磨粗糙,从而通过增加聚氨酯漆膜与环氧漆膜之间的接触面积以提高层间附着力,但是当遇到大面积的施工工程时,会大大增加工程量并延长工期。
技术实现要素:5.为了改善采用聚氨酯涂料作为与环氧面漆结合的耐磨层时会大大增加工程量并延长工期的问题,本技术提供一种无溶剂环氧超耐磨涂料及其制备方法。
6.第一方面,本技术提供一种无溶剂环氧超耐磨涂料,采用如下的技术方案:一种无溶剂环氧超耐磨涂料,其特征在于,由a组分、b组分和c组分组成,其中,a组分由以下组分组成:含有饱和环己烷的二元胺
ꢀꢀꢀꢀ
70~80wt%,a组分用环氧树脂
ꢀꢀꢀꢀꢀꢀꢀꢀꢀꢀꢀ
10~15wt%,苯甲醇
ꢀꢀꢀꢀꢀꢀꢀꢀꢀꢀꢀꢀꢀꢀꢀꢀꢀꢀꢀꢀ
5~15wt%;b组分由以下组分组成:b组分用环氧树脂
ꢀꢀꢀꢀꢀꢀꢀꢀꢀꢀꢀ
85~95wt%,烃基缩水甘油醚
ꢀꢀꢀꢀꢀꢀꢀꢀꢀꢀꢀꢀ
5~15wt%;c组分为耐磨填料;所述a组分、b组分和c组分的重量配比为a组分:b组分:c组分=(1~1.1):3:(1.8~2.2),所述耐磨填料的粒径大于涂料涂覆形成的漆膜的厚度。
7.通过采用上述技术方案,a组分作为固化剂组分,含有饱和环己烷结构的二元胺作为固化剂与环氧树脂的固化产物有优异的耐化性和理化机械性能,但纯的含有饱和环己烷结构的二元胺的活性过高,吸水性很强,因此加入少量环氧树脂以降低二元胺中伯胺的数量,苯甲醇用于改善柔韧性;b组分是环氧组分,和a组分固化剂反应可形成三维网状结构的坚韧漆膜;c组分是硬度特高的骨料,a与b反应形成的坚韧漆膜会将c组分固定住,c的粒径
大于漆膜的厚度,在实际应用时c组分耐磨填料承担了大部分的受力,结合a、b组分形成的坚韧漆膜,使整体的漆膜体现出优异的耐磨性能和硬度。
8.本技术制得的环氧超耐磨涂料与环氧面漆属于相似体系,与环氧面漆的层间附着力好,漆膜不易分离脱落,在施工时不需要再对环氧面漆进行打磨,大大减少了工程量,缩短了工期,另外,聚氨酯涂料往往施工时间很短,很快就会干燥凝固,施工难度大,而本技术环氧超耐磨涂料的可施工时间长,降低了施工难度。
9.本技术为环氧涂料,生产成本比聚氨酯涂料低很多,实用性高,相比于聚氨酯涂料的生产,工艺更简单,工业化生产难度低;另外,工业上将溶剂含量小于4%的体系成为无溶剂体系,本技术环氧超耐磨涂料溶剂含量低于4%,为无溶剂体系,voc排放量低,环保性好。
10.优选的,a组分由78wt%的含有饱和环己烷的二元胺、12wt%的a组分用环氧树脂和10wt%的苯甲醇组成,b组分由90wt%的b组分用环氧树脂和10wt%的烃基缩水甘油醚组成,所述a组分、b组分和c组分的重量配比为a组分:b组分:c组分=1:3:2。
11.经试验,采用上述配比制得的无溶剂环氧超耐磨涂料的性能更好。
12.优选的,所述含有饱和环己烷的二元胺为异佛尔酮二胺、1,3-环己烷二胺,1,4-环己烷二甲胺,1,2-环己二胺,1,3-环己二甲胺中的一种或几种的组合。
13.优选的,所述含有饱和环己烷的二元胺为异佛尔酮二胺。
14.经试验,异佛尔酮二胺具有类似金刚烷的结构,硬度更高,对于提高漆膜耐磨性能的效果更好。
15.优选的,所述耐磨填料为金刚砂粉、刚玉粉、陶瓷微珠中的一种或几种的组合。
16.通过采用上述技术方案,上述几种填料的硬度高,具有优异的耐磨性能。
17.优选的,所述耐磨填料为陶瓷微珠。
18.通过采用上述技术方案,陶瓷微珠硬度高且呈球状,粒径分布范围窄,使漆膜表面更均匀平整,应用效果更好。
19.优选的,所述耐磨填料的粒径为涂料涂覆形成的漆膜厚度的1.1~1.2倍。
20.经试验,当耐磨填料的粒径小于漆膜厚度的1.1倍时,当漆膜遇到外界的摩擦时,漆膜与外界作用物体之间的作用力会直接作用到漆膜上,进而使漆膜受到较大的磨损,当耐磨填料的粒径大于漆膜厚度1.2倍时,耐磨填料凸出于漆膜表面的部位较多,不便于漆膜表面的日常清理,并且耐磨填料与漆膜之间的牢固性也会受到影响,在受到外力时,耐磨填料容易从漆膜上脱落。
21.优选的,所述烃基缩水甘油醚为烷基缩水甘油醚、丁基缩水甘油醚、苯基缩水甘油醚、苄基缩水甘油醚、烯丙基缩水甘油醚中的一种或几种的组合。
22.优选的,所述烃基缩水甘油醚为c12-14烷基缩水甘油醚。
23.通过采用上述技术方案,c12-14烷基缩水甘油醚分子链更长,能够提供优异的柔韧性能。
24.优选的,所述a组分用环氧树脂为双酚a型环氧树脂和/或双酚f型环氧树脂,所述b组分用环氧树脂为双酚a型环氧树脂和/或双酚f型环氧树脂。
25.优选的,所述a组分用环氧树脂为e-44、e-51、e-54的一种或几种的组合,所述b组分用环氧树脂为e-44、e-51、e-54的一种或几种的组合。
26.优选的,所述a组分用环氧树脂为e-51,所述b组分用环氧树脂为e-51。
27.通过采用上述技术方案,e-51环氧值更高,交联密度更大,有利于提高漆膜的耐磨性能。
28.第二方面,本技术提供一种无溶剂环氧超耐磨涂料的制备方法,采用如下的技术方案:一种无溶剂环氧超耐磨涂料的制备方法,包括以下步骤:将a组分用环氧树脂搅拌滴加至含有饱和环己烷的二元胺中,控制1小时滴加完毕,滴加完毕后控制温度在60~80℃保温2小时,然后加入苯甲醇,搅拌分散均匀,降温至40℃过滤,滤液为a组分;将b组分用环氧树脂和烃基缩水甘油醚混合于一起,控制转速400~600转/分钟,搅拌30~60分钟,得到b组分;将a组分与b组分搅拌混合均匀,然后再加入c组分,搅拌分散均匀,得到无溶剂环氧超耐磨涂料。
29.通过采用上述技术方案,相比于常规的聚氨酯涂料的生产,本技术工艺更简单,工业化生产难度低,降低了生产成本,实用性高。
30.综上所述,本技术包括以下至少一种有益技术效果:1、本技术制得的环氧超耐磨涂料与环氧面漆属于相似体系,与环氧面漆的层间附着力好,漆膜不易分离脱落,在施工时不需要再对环氧面漆进行打磨,大大减少了工程量,缩短了工期,另外,聚氨酯涂料施工时间很短,很快就会干燥凝固,施工难度大,而本技术环氧超耐磨涂料的可施工时间长,降低了施工难度。
31.2、本技术在体系中添加耐磨填料结合a、b组分形成的坚韧漆膜,a、b组分固化形成的三维网状结构与耐磨填料协同作用使整体的漆膜体现出优异的耐磨性能和硬度,应用时通过耐磨填料承担大部分外界对漆膜施加的力,降低了漆膜的磨损。
32.3、本技术为环氧涂料,生产成本比聚氨酯涂料低,实用性高,相比于聚氨酯涂料的生产,工艺更简单,工业化生产难度低,另外,本技术环氧超耐磨涂料溶剂含量低于4%,为无溶剂体系,voc排放量低,环保性好。
具体实施方式
33.为了更方便理解本技术的技术方案,以下结合表格和实施例对本技术作进一步详细说明,但不作为本技术限定的保护范围。
34.实施例1a组分的制备:取70wt%的1,3-环己烷二胺、15wt%的e-44环氧树脂、15wt%的苯甲醇,将e-44环氧树脂搅拌滴加至1,3-环己烷二胺中,控制1小时滴加完毕,滴加完毕后控制温度在60~80℃保温2小时,然后加入苯甲醇,搅拌分散15分钟,降温至40℃过滤,滤液为a组分;b组分的制备:取85wt%的e-44环氧树脂和15wt%的丁基缩水甘油醚,将e-44环氧树脂和丁基缩水甘油醚混合于一起,控制转速500转/分钟,搅拌30分钟,得到b组分;涂料的制备:将a组分与b组分搅拌混合均匀,然后再加入c组分,c组分为粒径在180~200目之间的金刚砂粉,a组分、b组分、c组分的重量比为a组分:b组分:c组分=1:3:1.8,搅拌分散均匀,得到无溶剂环氧超耐磨涂料。
35.实施例2与实施例1的区别在于:a组分由75wt%的1,4-环己烷二甲胺、15wt%的e-54环氧树脂、10wt%的苯甲醇组成,b组分由88wt%的e-44环氧树脂和12wt%的苯基缩水甘油醚组成。
36.实施例3与实施例1的区别在于:a组分由78wt%的异佛尔酮二胺、12wt%的e-51环氧树脂、10wt%的苯甲醇组成,b组分由90wt%的e-51环氧树脂和10wt%的c12-14烷基缩水甘油醚组成。
37.实施例4与实施例1的区别在于:a组分由80wt%的1,2-环己二胺、10wt%的e-54环氧树脂、10wt%的苯甲醇组成,b组分由92wt%的e-54环氧树脂和8wt%的苄基缩水甘油醚的组成。
38.实施例5与实施例1的区别在于:a组分由80wt%的1,3-环己二甲胺、15wt%的e-54环氧树脂、5wt%的苯甲醇组成,b组分由95wt%的e-51环氧树脂和5wt%的烯丙基缩水甘油醚的组成。
39.对比例1与实施例1的区别在于:a组分由65wt%的1,3-环己烷二胺、20wt%的e-44环氧树脂、15wt%的苯甲醇组成,b组分由95wt%的e-44环氧树脂和5wt%的丁基缩水甘油醚的组成。
40.对比例2与实施例1的区别在于:a组分由80wt%的1,3-环己烷二胺、15wt%的e-44环氧树脂、5wt%的苯甲醇组成,b组分由97wt%的e-44环氧树脂和3wt%的丁基缩水甘油醚的组成。
41.表1:实施例1~5及对比例1~2无溶剂环氧超耐磨涂料中a组分和b组分的组分配比。
42.性能检测试验采用实施例1~5及对比例1~2中制得的无溶剂环氧超耐磨涂料涂覆成漆膜,待漆膜完全凝固后进行以下性能检测试验,检测数据见表2。
43.附着力:检测方法参照gb/t 9286-1998,检测标准≤1级。
44.漆膜硬度:检测方法参照gb/t 6739-2006,检测标准≥h。
45.耐磨性:检测方法参照gb/t 1768-2006,检测标准≤0.03g。
46.检测附着力时,涂覆基材上预先涂覆有环氧面漆。
47.检测耐磨性时,漆膜厚度控制在约为70微米,实施例1~5及对比例1~2中耐磨填料的粒径为180~200目,按照公式:目数
×
孔径(微米数)=15000为标准,实施例1~5及对比例1~2中耐磨填料的粒径约为75~83.3微米,基于工业误差的允许范围内,可视为该粒径范围的耐磨填料的粒径约为漆膜厚度的1.1~1.2倍,下述实施例及对比例的测试标准及粒径换算同此。
48.表2:实施例1~5及对比例1~2中无溶剂环氧超耐磨涂料漆膜的测试数据。
49.根据实施例1~5及表2中的数据可以看出,本技术制得的无溶剂环氧超耐磨涂料形成的漆膜具有优异的附着力、漆膜硬度及耐磨性,与环氧面漆之间的附着力能够达到0级,其中以实施例3制得的无溶剂环氧超耐磨涂料性能更好,漆膜硬度可达6h,耐磨性仅为0.024g。
50.结合对比例1可以看出,当a组分中二元胺的含量减少,b组分中环氧树脂的含量减少时,漆膜的硬度和耐磨性都会降低,这是因为a组分中二元胺的减少和b组分中环氧树脂的减少都会降低体系的交联密度降低,从而影响漆膜的硬度和耐磨性,且试验中发现a组分的粘度会增大,施工性不佳。
51.结合对比例2可以看出,当a组分中二元胺的含量增加,b组分中环氧树脂的含量增加时,虽然漆膜的附着力、漆膜硬度及耐磨性均符合应用标准,但是在试验过程中发现,b组分的粘度会增大,施工性不佳,并且后续的检测中还发现,对比例2中的漆膜在点滴法(gb/t 9274-1988:丙法)试验中漆膜会出现气泡的情况,原因是a组分中二元胺的增加使体系中胺氢量增大,造成耐水性变差。
52.实施例6与实施例1的区别在于,将1,3-环己烷二胺替换为异佛尔酮二胺。
53.实施例7与实施例3的区别在于,将异佛尔酮二胺替换为1,4-环己烷二甲胺。
54.对实施例6~7中制得的无溶剂环氧超耐磨涂料涂覆成的漆膜进行上述性能检测
试验,检测数据见表3。
55.表3:实施例1、3、6~7中无溶剂环氧超耐磨涂料漆膜的测试数据。
56.结合实施例1、3、6~7及表3的数据可以看出,二元胺采用异佛尔酮二胺时,对于漆膜的硬度有提升作用,原因是异佛尔酮二胺具有类似金刚烷的结构,硬度更高,也有利于提高漆膜的耐磨性。
57.实施例8与实施例3的区别在于:a组分、b组分、c组分的重量比为a组分:b组分:c组分=1:3:1.9。
58.实施例9与实施例3的区别在于:a组分、b组分、c组分的重量比为a组分:b组分:c组分=1:3:2。
59.实施例10与实施例3的区别在于:a组分、b组分、c组分的重量比为a组分:b组分:c组分=1:3:2.1。
60.实施例11与实施例3的区别在于:a组分、b组分、c组分的重量比为a组分:b组分:c组分=1.1:3:2.2。
61.对比例3与实施例3的区别在于:a组分、b组分、c组分的重量比为a组分:b组分:c组分=1:3:2.3。
62.对比例4与实施例3的区别在于:a组分、b组分、c组分的重量比为a组分:b组分:c组分=1:3:1.7。
63.对实施例8~11及对比例3~4中制得的无溶剂环氧超耐磨涂料涂覆成的漆膜进行上述性能检测试验,检测数据见表4。
64.表4:实施例3、8~11及对比例3~4中无溶剂环氧超耐磨涂料漆膜的测试数据。
65.结合实施例3、8~11、对比例3~4及表4的数据可以看出,随着c组分占比的增加,漆膜的耐磨性逐渐提高,但同时也会对漆膜的附着力造成影响。对比例11中虽然漆膜的耐磨性能更好,但是附着力相对于实施例8~9较低。对比例3中漆膜的附着力仅为2级,达不到应用标准,原因是耐磨填料的占比过高,导致漆膜粘性降低。对比例4中漆膜的耐磨性不符合应用标准,原因是耐磨填料的占比过低,应用时来自外界的压力和摩擦力会较多分散到漆膜上,使漆膜产生较大磨损。因此,综合考虑以实施例9中制得的无溶剂环氧超耐磨涂料为更优。
66.实施例12与实施例9的区别在于:c组分为粒径在180~200目之间的刚玉粉。
67.实施例13与实施例9的区别在于:c组分为粒径在180~200目之间的陶瓷微珠。
68.对实施例12~13中制得的无溶剂环氧超耐磨涂料涂覆成的漆膜进行上述性能检测试验,检测数据见表5。
69.表5:实施例9、12~13中无溶剂环氧超耐磨涂料漆膜的测试数据。12~13中无溶剂环氧超耐磨涂料漆膜的测试数据。
70.结合实施例9、12~13及表5的数据可以看出,采用陶瓷微珠作为耐磨填料时,漆膜的耐磨性更好,硬度更高,原因是陶瓷微珠硬度更高且呈球状,粒径分布范围窄,在分散至漆膜表面时整体更均匀平整,凸出的耐磨填料粒子高度基本上持平,对于外界的压力和摩擦力能够更好地分散承担。试验还发现,采用高温烧结后的陶瓷微珠应用效果更好,漆膜的耐磨性和硬度更高。
71.实施例14
与实施例13的区别在于:陶瓷微珠的粒径为160~170目。
72.实施例15与实施例13的区别在于:陶瓷微珠的粒径为200~210目。
73.对实施例14~15中制得的无溶剂环氧超耐磨涂料涂覆成的漆膜进行上述性能检测试验,检测数据见表6。
74.按照上述换算公式进行换算,实施例14中耐磨填料的粒径约为88.2~93.8微米,实施例15中耐磨填料的粒径约为71.4~75微米,基于工业误差的允许范围内,可视为实施例14中耐磨填料的粒径约为漆膜厚度的1.26~1.34倍,实施例15中耐磨填料的粒径约为漆膜厚度的1.02~1.07倍。
75.表6:实施例13~15中无溶剂环氧超耐磨涂料漆膜的测试数据。
76.结合实施例13~15及表6的数据可以看出,实施例13中漆膜的附着力、漆膜硬度及耐磨性更优。实施例14中漆膜的附着力为1级,原因是耐磨填料的粒径过大,其自身体积与漆膜接触面积的占比更小,耐磨填料凸出于漆膜的高度过高,因此在受力时,耐磨填料容易松动出现脱落,从而造成漆膜的附着力变差。实施例15中漆膜的耐磨性为0.018g,相比于实施例13有所降低,原因是耐磨填料的粒径较小,基本上与漆膜的厚度持平,在漆膜受到外力时,耐磨填料承担的压力和摩擦力较少,漆膜承担的压力和摩擦力增加,因此漆膜磨损会更严重。
77.综上,本技术制得的无溶剂环氧超耐磨涂料形成的漆膜具有优异的附着力、漆膜硬度及耐磨性,附着力可达0级,与环氧面漆的附着能力好,不易分离,且应用时更容易施工,漆膜硬度可达7h,耐磨性仅为0.013g,耐磨性能好。
78.本具体实施例仅仅是对本技术的解释,其并不是对本技术的限制,本领域技术人员在阅读完本说明书后可以根据需要对本实施例做出没有创造性贡献的修改,但只要在本技术的权利要求范围内都受到专利法的保护。