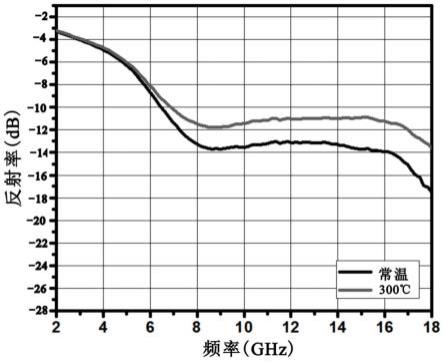
1.本发明涉及吸波材料技术领域,特别是涉及一种耐高温吸波涂层及其制备方法。
背景技术:2.随着微波技术的发展,系统对微波吸收材料的耐高温性能要求越来越高。然而传统吸波涂层存在耐温性能差,在高温下易出现涂层开裂以及吸波性能下降的缺点,无法满足高温需求。
3.因此,急需提供一种在高温下不易出现涂层开裂,且具有优异的吸波性能的吸波涂层。
技术实现要素:4.针对现有技术中存在的一个或者多个技术问题,本发明提供了一种耐高温吸波涂层及其制备方法及其制备方法,本发明的制备法简单可控,制得的吸波涂层具有优异的耐高温性能、吸波性能和力学性能,可满足高温需求。
5.本发明在第一方面提供了一种耐高温吸波涂层的制备方法,包括:
6.s1.将铁钴合金粉体、酚醛树脂胶液、有机溶剂和硅烷偶联剂充分混合,得到混合浆料;
7.s2.在研磨的条件下,向所述混合浆料加入有机溶剂,调节所述混合浆料的粘度,得到吸波涂料;
8.s3.将所述吸波涂料喷涂于基体的表面,得到所述耐高温吸波涂层。
9.优选地,在步骤s1中,将所述铁钴合金粉体和所述酚醛树脂胶液混合后,并于搅拌条件下加入所述有机溶剂和所述硅烷偶联剂,得到所述混合浆料。
10.优选地,在步骤s1中,所述铁钴合金粉体、所述酚醛树脂胶液、所述有机溶剂和所述硅烷偶联剂的质量比为(70~90):(17~55):(20~30):(0.02~0.08)。
11.优选地,在步骤s1中,所述铁钴合金粉体的粒径为10~40μm。
12.优选地,在步骤s1中,所述所述酚醛树脂胶液由酚醛树脂和有机溶剂混合得到;所述酚醛树脂胶液的固含量为50~70%。
13.优选地,在步骤s2中,在研磨的条件下,向所述混合浆料加入有机溶剂,调节所述混合浆料的粘度至10~30pa
·
s,得到所述吸波涂料。
14.优选地,在步骤s1中,所述硅烷偶联剂为γ-缩水甘油醚氧丙基三甲氧基硅烷;和/或
15.在步骤s1和步骤s2中,所述有机溶剂为乙酸乙酯、正丁醇和丙酮中的一种。
16.优选地,在步骤s3中,将所述吸波涂料放入喷罐中,用喷枪在所述基体的表面喷涂50~150次,得到所述耐高温吸波涂层;喷涂时,设置喷枪的口径为1~2mm,喷涂的压强为0.2~0.8mpa,喷涂的距离为10~50cm。
17.优选地,在步骤s3中,所述基体为合金基体;和/或所述耐高温吸波涂层的厚度为
0.5~2mm。
18.本发明在第二方面提供了一种耐高温吸波涂层,采用第一方面所述的制备方法制备得到。
19.本发明与现有技术相比至少具有如下有益效果:
20.本发明吸波浆料以具有耐高温性能铁钴合金粉体为吸收剂,酚醛树脂为基体材料、硅烷偶联剂为原料,制得铁钴合金粉体和酚醛树脂均匀分散的混合浆料,并通过调控混合浆料的粘度,得到可直接喷涂于结构件表面的吸波涂料,形成的吸波涂层具有优异的耐高温性能、吸波性能和力学性能。
附图说明
21.为了更清楚地说明本发明实施例的技术方案,下面将对实施例描述中所需要使用的附图作简单地介绍,显而易见地,下面描述中的附图是本发明的一些实施例,对于本领域普通技术人员来讲,在不付出创造性劳动的前提下,还可以根据这些附图获得其他的附图。
22.图1是本发明实施例1提供的半固化耐高温吸波薄膜的反射率-频率曲线图;
23.图2是本发明实施例2提供的半固化耐高温吸波薄膜的反射率-频率曲线图;
24.图3是本发明实施例3提供的半固化耐高温吸波薄膜的反射率-频率曲线图;
25.图4是本发明对比例1提供的吸波薄膜的反射率-频率曲线图;
26.图5是本发明对比例5提供的吸波薄膜的反射率-频率曲线图。
具体实施方式
27.为使本发明实施例的目的、技术方案和优点更加清楚,下面将结合本发明实施例中的技术方案进行清楚、完整地描述,显然,所描述的实施例是本发明一部分实施例,而不是全部的实施例,基于本发明中的实施例,本领域普通技术人员在没有做出创造性劳动的前提下所获得的所有其他实施例,都属于本发明保护的范围。
28.本发明在第一方面提供了一种耐高温吸波涂层的制备方法,包括:
29.s1.将铁钴合金粉体、酚醛树脂胶液、有机溶剂和硅烷偶联剂充分混合,得到混合浆料;本发明吸波浆料以铁钴合金粉体为吸收剂,酚醛树脂为基体材料,两者均为耐高温材料,两者复合后,可以保证制得的吸波涂层具有优异的耐高温性能、吸波性能和力学性能。
30.s2.在研磨的条件下,向所述混合浆料加入有机溶剂,调节所述混合浆料的粘度,得到吸波涂料;本发明在研磨的条件下,向混合浆料中加入有机溶剂调节混合浆料的粘度,以得到适合喷涂的吸波涂料。
31.s3.将所述吸波涂料喷涂于基体的表面,得到所述耐高温吸波涂层。
32.本发明吸波浆料以具有耐高温性能铁钴合金粉体为吸收剂,酚醛树脂为基体材料、硅烷偶联剂为原料,制得铁钴合金粉体和酚醛树脂均匀分散的混合浆料,并通过调控混合浆料的粘度,得到可直接喷涂于结构件表面的吸波涂料,形成的吸波涂层具有优异的耐高温性能、吸波性能和力学性能。
33.根据一些优选的实施方式,在步骤s1中,将所述铁钴合金粉体和所述酚醛树脂胶液混合后,并于搅拌条件下加入所述有机溶剂和所述硅烷偶联剂,得到所述混合浆料。
34.根据一些优选的实施方式,在步骤s1中,所述铁钴合金粉体、所述酚醛树脂胶液、
所述有机溶剂和所述硅烷偶联剂的质量比为(70~90):(17~55):(20~30):(0.02~0.08);本发明将铁钴合金粉体、酚醛树脂胶液、有机溶剂和硅烷偶联剂的用量控制在上述范围,即得到铁钴合金粉体和酚醛树脂均匀分散的混合浆料,确保制得的吸波涂层同时具有优异的力学性能、耐温性能和吸波性能,可直接喷涂于结构件表面。
35.根据一些优选的实施方式,在步骤s1中,所述铁钴合金粉体的粒径为10~40μm;本发明将铁钴合金粉体的粒径控制上述范围,可确保铁钴合金粉体均匀分散在酚醛树脂胶液中。
36.根据一些优选的实施方式,在步骤s1中,所述所述酚醛树脂胶液由酚醛树脂和有机溶剂混合得到;所述酚醛树脂胶液的固含量为50~70%;
37.根据一些优选的实施方式,在步骤s2中,在研磨的条件下,向所述混合浆料加入有机溶剂,调节所述混合浆料的粘度至10~30pa
·
s,得到所述吸波涂料;本发明通过加入有机溶剂调控混合浆料的粘度,对于有机溶剂具体用量不做限定,满足将吸波涂料的粘度控制在目标范围即可;将吸波涂料的粘度控制在上述范围,可得到的浆料适合喷涂,喷涂后的涂层具有优异的力学性能,不易开裂;与结构件表面具有较强的粘附力,不易出现脱落。
38.根据一些优选的实施方式,在步骤s1中,所述硅烷偶联剂为γ-缩水甘油醚氧丙基三甲氧基硅烷(kh560);和/或
39.在步骤s1和步骤s2中,所述有机溶剂为乙酸乙酯、正丁醇和丙酮中的一种;在步骤s1中,有机溶剂的作用主要是为了使铁钴合金粉体、酚醛树脂胶液和硅烷偶联剂充分分散,得到分散均匀的混合浆料;在步骤s2中,有机溶剂的作用则是为了调节混合浆料的粘度,以得到满足喷涂要求的吸波涂料。
40.根据一些优选的实施方式,在步骤s3中,将所述吸波涂料放入喷罐中,用喷枪在所述基体的表面喷涂50~150次,得到所述耐高温吸波涂层;喷涂时,设置喷枪的口径为1~2mm,喷涂的压强为0.2~0.8mpa,喷涂的距离为10~50cm。本发明喷涂过程中,喷涂的次数、设置喷枪的口径,喷涂的压强,喷涂的距离可根据实际需要进行调整,一般将喷涂的次数、设置喷枪的口径,喷涂的压强,喷涂的距离相关参数限制在上述范围即可满足大部分需求。
41.根据一些优选的实施方式,在步骤s3中,所述基体为合金基体;和/或所述耐高温吸波涂层的厚度为0.5~2mm。本发明吸波涂层的厚度可根据实际需求和应用场景进行选择,配合相应喷涂参数即可得到上述厚度的吸波涂层。
42.在一些具体的实施例中,制备所述耐高温吸波涂层包括:s1.将所述铁钴合金粉体和所述酚醛树脂胶液混合后,于400~700r/min的转速下,搅拌10~20min,并于搅拌条件下加入所述有机溶剂和所述硅烷偶联剂,得到所述混合浆料;所述铁钴合金粉体、所述酚醛树脂胶液、所述有机溶剂和所述硅烷偶联剂的质量比为(70~90):(17~55):(20~30):(0.02~0.08);s2.将混合浆料放入三辊研磨机中,于50~70r/min的转速下,研磨1~3h,并在研磨的条件下,向所述混合浆料加入有机溶剂,调节所述混合浆料的粘度至10~30pa
·
s,得到所述吸波涂料;s3.将所述吸波涂料放入喷罐中,用喷枪在所述基体的表面喷涂50~150次,得到所述耐高温吸波涂层;喷涂时,设置喷枪的口径为1~2mm,喷涂的压强为0.2~0.8mpa,喷涂的距离为10~50cm。
43.本发明在第二方面提供了一种耐高温吸波涂层,采用上述第一方面所述的制备方法制备得到。
44.本发明制备的吸波涂料可直接喷涂于结构件表面,形成的吸波涂层具有优异的耐温性能和吸波性能,且涂层不易开裂;在2~18ghz频段内,在300℃下反射率相比于常温下反射率的上升值均不超过5db。
45.为了更加清楚地说明本发明的技术方案及优点,下面结合实施例对本发明作进一步说明。
46.需要说明的是,本发明中的材料和试剂均可以是在市面上直接购买得到或自行合成得到,对具体型号不做限制。
47.吸波性能测试标准:参照gjb2038a-2011执行。
48.实施例1
49.s1.将700g粒径为30um的铁钴合金粉体缓慢加入到550g固含量为60%的酚醛树脂中,用搅拌机于400r/min的转速下,搅拌时间10min,并在搅拌条件下加入200g的乙酸乙酯和0.2g的kh560,形成混合浆料;
50.s2.将混合浆料放入三辊研磨机中,在50r/min的转速下,研磨2小时,研磨时,进行研磨;并在研磨条件下加入乙酸乙酯,至粘度为30pa
·
s,形成吸波涂料;
51.s3.称取500g吸波涂料放入喷罐中,用喷枪在金属件表面喷涂100遍,得到厚度为1.5mm的耐高温吸波涂层;喷涂时,设置喷枪口径为1mm,压强为0.6mpa,行枪距离为20cm;
52.该耐高温吸波涂料可直接喷涂于结构件表面,得到的吸波涂层具有优异的耐温性能和吸波性能,且涂层不易开裂;如图1所示,在2~18ghz频段内,在300℃下反射率相比于常温下反射率的上升值均不超过3db。
53.实施例2
54.s1.将800g粒径为30um的铁钴合金粉体缓慢加入到400g固含量为60%的酚醛树脂中,用搅拌机于500r/min的转速下,搅拌时间10min,并在搅拌条件下加入300g的乙酸乙酯和0.6g的kh560,形成混合浆料;
55.s2.将混合浆料放入三辊研磨机中,在70r/min的转速下,研磨2小时,研磨时,进行研磨;并在研磨条件下加入乙酸乙酯,至粘度为30pa
·
s,形成吸波涂料;
56.s3.称取500g吸波涂料放入喷罐中,用喷枪在金属件表面喷涂100遍,得到厚度为1.5mm的耐高温吸波涂层;喷涂时,设置喷枪口径为2mm,压强为0.8mpa,行枪距离为50cm;
57.该耐高温吸波涂料可直接喷涂于结构件表面,得到的吸波涂层具有优异的耐温性能和吸波性能,且涂层不易开裂;如图2所示,在2~18ghz频段内,在300℃下反射率相比于常温下反射率的上升值均不超过3db。
58.实施例3
59.s1.将900g粒径为30um的铁钴合金粉体缓慢加入到170g固含量为60%的酚醛树脂中,用搅拌机于500r/min的转速下,搅拌时间10min,并在搅拌条件下加入250g的乙酸乙酯和0.4g的kh560,形成混合浆料;
60.s2.将混合浆料放入三辊研磨机中,在70r/min的转速下,研磨2小时,研磨时,进行研磨;并在研磨条件下加入乙酸乙酯,至粘度为10pa
·
s,形成吸波涂料;
61.s3.称取500g吸波涂料放入喷罐中,用喷枪在金属件表面喷涂100遍,得到厚度为1.5mm的耐高温吸波涂层;喷涂时,设置喷枪口径为2mm,压强为0.8mpa,行枪距离为50cm;
62.该耐高温吸波涂料可直接喷涂于结构件表面,制得的吸波涂层,具有优异的耐温
性能和吸波性能,且涂层不易开裂;如图3所示,在2~18ghz频段内,在300℃下反射率相比于常温下反射率的上升值均不超过5db。
63.对比例1
64.s1.将500g粒径为30um的铁钴合金粉体缓慢加入到550g固含量为60%的酚醛树脂中,用搅拌机于700r/min的转速下,搅拌时间20min,并在搅拌条件下加入100g的乙酸乙酯和0.6g的kh560,形成混合浆料。
65.s2.将混合浆料放入三辊研磨机中,在50r/min的转速下,研磨2小时,研磨时,进行研磨;并在研磨条件下加入乙酸乙酯,至粘度为30pa
·
s,形成吸波涂料。
66.s3.称取500g吸波涂料放入喷罐中,用喷枪在金属件表面喷涂100遍,得到厚度为0.6mm的耐高温吸波涂层;喷涂时,设置喷枪口径为1.5mm,压强为0.7mpa,行枪距离为50cm;
67.该耐高温吸波涂料可直接喷涂于结构件表面,如图4所示,在2~18ghz频段内,在300℃下反射率相比于常温下反射率的上升值虽不超过3db,但吸波性能差。
68.对比例2
69.对比例2与实施例1基本相同,其区别之处在于:在步骤s1中,将800g粒径为30um的铁钴合金粉体、400g固含量为60%的酚醛树脂、300g的乙酸乙酯和0.6g的kh560,用搅拌机于400r/min的转速下,搅拌时间10min,形成混合浆料。
70.形成的吸波涂料分散不均匀,喷涂效果差,无法得到耐高温吸波涂层。
71.对比例3
72.对比例3与实施例1基本相同,其区别之处在于:在步骤s1中,将800g粒径为30um的铁钴合金粉体、400g固含量为60%的酚醛树脂和300g的乙酸乙酯,用搅拌机于400r/min的转速下,搅拌时间10min,形成混合浆料。
73.因未加入偶联剂形成的吸波涂料分散不均匀,无法进行喷涂得到耐高温吸波涂层。
74.对比例4
75.对比例4与实施例1基本相同,其区别之处在于:无步骤s2。
76.形成的混合浆料粘度太大,无法进行喷涂得到耐高温吸波涂层。
77.对比例5
78.对比例5与实施例1基本相同,其区别之处在于:在步骤s1中,将铁钴合金粉体换成羰基铁粉。
79.对比例5制得的吸波薄膜在常温具有一定的吸波性能,但高温吸波性能较差。
80.对比例6
81.对比例6与实施例1基本相同,其区别之处在于:在步骤s1中,将铁钴合金粉体换成铁氧体。
82.对比例6制得的吸波薄膜在常温具有一定的吸波性能,但高温吸波性能较差。
83.最后应说明的是:以上实施例仅用以说明本发明的技术方案,而非对其限制;尽管参照前述实施例对本发明进行了详细的说明,本领域的普通技术人员应当理解:其依然可以对前述各实施例所记载的技术方案进行修改,或者对其中部分技术特征进行等同替换;而这些修改或者替换,并不使相应技术方案的本质脱离本发明各实施例技术方案的精神和范围。