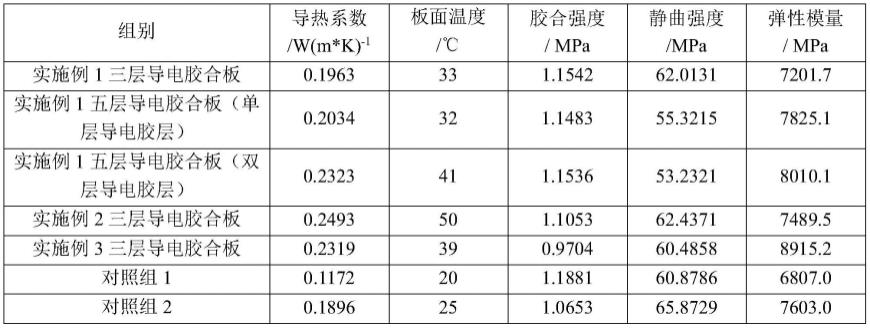
1.本发明涉及胶粘剂技术领域,具体为一种石墨基的导电胶粘剂,及该种导电胶粘剂的制备方法;本发明同时还涉及该种石墨基的导电胶粘剂的应用,具体是利用该种导电胶粘剂制备得到的电热胶合板,及该种电热胶合板的制备方法。
背景技术:2.木基电热功能材料是以木质材料作为基体,与碳基材料、金属材料等导电物质复合而制成的一种新型电热材料。制备木基电热功能材料的方法较多,在木质单板表面涂布导电胶粘剂以制备导电胶合板,将木质纤维、木质刨花与导电胶粘剂混合以制备导电纤维板或导电刨花板等都是存有记载的现有技术。在这类技术方案中,导电胶粘剂的综合性能,例如制造成本、分散性、胶层电阻率,对制备得到的导电人造板的性能有决定性的影响。
3.现有技术中有较多的关于导电胶粘剂的配方、制备方法的记载,添加导电金属粉末是最传统的一种技术方案。例如中国专利数据库中,公开号为cn103881609a,名称为“导电胶粘剂的制备方法及用该方法获得的导电胶粘剂”的发明专利申请中记载了向环氧树脂胶粘剂中添加导电金属粉末,例如金属银粉,并通过添加气相二氧化硅作为导电金属粉末的附着基体以促进扩散从而制备得到导电胶粘剂的技术方案。
4.但是,出于导电金属粉末自身在胶粘剂中的分散效果不佳,导电金属粉末的使用成本相对较高,并且以它作为发热基础材料制得的胶粘剂导电性能不理想等原因,现有技术进一步提出了碳基发热胶粘剂的产品与制备方法。例如中国专利数据库中,公开号为cn108753213a,名称为“一种导电胶粘剂及其制备方法和应用方法”的发明专利申请,以及公开号为cn114736631a,名称为“一种导电胶粘剂的制备方法”的发明专利申请。前者记载了向丙烯酸酯树脂胶粘剂中添加单壁碳纳米管、导电填料等从而制备得到导电胶粘剂的技术方案,其中导电填料是镍粉、银纳米线、铜粉和铝粉中的一种或几种。后者记载了将多壁碳纳米管溶液和石墨烯溶液加入溶于有机溶剂的胶粘剂中从而制备得到导电胶层的技术方案。
5.除了单壁碳纳米管、多壁碳纳米管、石墨烯、碳纤维和镀镍膨胀石墨也是较为常见的两种碳基导电材料。公开号为cn111621253a,名称为“一种基于石墨的高强导热环氧树脂胶粘剂及其制备方法”的发明专利申请中记载了向环氧树脂胶粘剂中添加改性石墨、复合玻璃纤维等从而制备得到导电胶粘剂的技术方案,其中改性石墨是通过剥离法制得的石墨的烯纳米片。公开号为cn107312484a,名称为“一种环氧树脂型导电胶粘剂及其制备方法”的发明专利申请中记载了向脂肪族环氧树脂中添加导电颗粒等从而制备得到导电胶粘剂的技术方案,其中导电颗粒是改性碳纤维材料,具体是将碳纤维与苯胺单体充分混合兵加入十二烷基苯磺酸溶液得到混合溶液,再向混合溶液中滴加过硫酸铵与十二烷基苯磺酸的混合物,最后将反应得到的产物过滤、洗涤、干燥、粉碎后制得。公开号为cn105694797a,名称为“一种复合导电胶粘剂的制备方法”的发明专利申请中记载了以45份胶粘剂基体、15份镀镍活化膨胀石墨、15份固化剂和2份辅料的配方,制备得到的导电胶粘剂能够用于电极片
和磁体晶体的粘接。
6.上述碳基发热胶粘剂的导电性能优于金属基导电胶粘剂,但是单壁碳纳米管、多壁碳纳米管、石墨烯、碳纤维和膨胀石墨均存在价格高、分散性差的缺点,膨胀石墨需要化学镀镍进行预先的活化处理,并且活化后的膨胀石墨的质量分数达到23%,极大的提高了胶粘剂的使用成本。
7.另一个方面,人造板不属于高附加值的产品,它的主要原材料(木质材料和胶粘剂)中,胶粘剂的价格决定了人造板的成品价格。以上述单壁碳纳米管、多壁碳纳米管、石墨烯和碳纤维的一种或多种混合作为导电基体的导电胶粘剂,由于分散性较差,往往需要使用相对大量的基体,提高了导电胶粘剂的价格,进而使得成品导电人造板的价格大大超出了市场对于人造板产品的预期价格。因此,上述方法制备得到的导电人造板始终未被推而广之。
8.基于成本因素的考虑,使用添加有石墨颗粒的胶粘剂粘结木质材料制备人造板的技术方案是较为实际的。例如公开号为cn1994696,名称为“电磁屏蔽功能胶合板的制造方法”的发明专利申请中记载了将石墨粉混于脲醛树脂或酚醛树脂胶粘剂中得到导电胶粘剂,并利用该种导电胶粘剂粘结单板从而制备得到导电胶合板的技术方案。然而,该发明专利申请的主要技术目的是使胶合板具备电磁波屏蔽的功能,徜若从导电性能角度考量,众所周知,石墨粉的价格虽低,但导电效率也相对较低、导电性能相对较差。
9.综上,现有技术中缺少一种导电性能相对较好且价格相对较低的导电胶粘剂。
技术实现要素:10.本发明的目的在于克服上述技术问题,从而提供一种石墨基导电胶粘剂,本发明同时还提供了该种石墨基导电胶粘剂的制备方法,以及应用。
11.为实现上述第一个技术目的,本发明的第一个实施例提供了一种石墨基导电胶粘剂,包括树脂胶粘剂、石墨,该种导电胶粘剂还包括膨胀石墨,所述膨胀石墨与所述石墨组成混合导电填料;所述石墨的添加量占所述石墨基导电胶粘剂的质量分数不低于12.5%,所述膨胀石墨的添加量占所述混合填料的质量分数为0.5~3.5%。
12.作为优选,所述石墨的添加量占所述石墨基导电胶粘剂的质量分数为13~15%,所述膨胀石墨的添加量占所述混合导电填料的质量分数为1~2%。
13.作为优选,所述石墨呈颗粒状,粒径为300~340目。
14.作为优选,所述膨胀石墨呈颗粒状,粒径为75~85目。
15.作为优选,所述树脂胶粘剂为脲醛树脂胶粘剂或酚醛树脂胶粘剂。
16.为实现上述第二个技术目的,本发明的第二个实施例提供了用于制备上述石墨基导电胶粘剂的方法,常温条件下,向所述树脂胶粘剂中添加由所述石墨和所述膨胀石墨组成的混合物,之后以350~450r/min的转速机械搅拌8~12min。
17.为实现上述第三个技术目的,本发明的第三个实施例提供了一种利用上述石墨基导电胶粘剂的导电胶合板,包括多层层叠的单板,所述单板两两之间通过胶层粘结,其中,至少一个所述胶层为导电胶层,且所述导电胶层由所述石墨基导电胶粘剂形成,所述导电胶层的两端铺设有导电胶带。
18.作为优选,所述石墨基导电胶粘剂的施胶量为110~130g/
㎡
。
19.作为优选,多个所述胶层中的至少一个为导电胶层,其余胶层为普通胶层;所述普通胶层由非导电胶粘剂以120~150g/
㎡
的涂布量涂布形成。
20.为实现上述第四个技术目的,本发明的第四个实施例提供了一种用于制备上述导电胶合板的方法,其特征在于,
21.首先,对至少一层第一单板单面施胶,涂布所述石墨基导电胶粘剂以在所述第一单板的表面形成导电胶层;随后,在所述导电胶层的两端铺设所述导电胶带;
22.再后,先对第二单板单面施胶,涂布非导电胶粘剂以在所述第二单板的表面形成普通胶层,再将所述第一单板、所述第二单板相互层叠组坯得到所述导电组坯材料;
23.最后,对所述导电组坯材料实施热压得到所述导电胶合板。
24.综上所述,与现有技术相比,本发明的有益效果是:
25.1、本技术技术方案仅添加极少量的膨胀石墨便能够极大的改善石墨基导电胶粘剂的导电性能,同时石墨基导电胶粘剂每千克的制造成本仅增加2元左右。
26.2、本技术技术方案的另一个有益效果是施胶量的降低。适当量的石墨颗粒的存在,能够填充单板的胶合界面从而降低界面的粗糙度,进而用于填平胶合界面的石墨基导电胶粘剂的量也相应减少,所以石墨基导电胶粘剂的施胶量与普通胶合板施胶量相比是减少的。虽然石墨基导电胶粘剂的施胶量降低了,但导电胶合板的胶合强度不仅没有受到影响,反而还提高了它的整体刚性。并且由于施胶量的降低,从而能够进一步降低本技术技术方案的胶粘剂的使用成本。
附图说明
27.为了更清楚地说明本技术实施例或现有技术中的技术方案,下面将对实施例或现有技术描述中所需要使用的附图作简单地介绍,显而易见地,下面描述中的附图仅是本技术的一些实施例,对于本领域技术人员来讲,在不付出创造性劳动性的前提下,还可以根据这些附图获得其他的附图。
28.图1为本技术实施例1的三层导电胶合板的结构示意图。
29.图2a为石墨单一成分导电胶层的导电网络示意图。
30.图2b为本技术实施例1的石墨基导电胶粘剂的导电网络示意图。
31.图3为本技术实施例1的五层导电胶合板(单层导电胶层)的结构示意图。
32.图4为本技术实施例1的五层导电胶合板(双层导电胶层)的结构示意图。
33.图5a为石墨单一成分导电胶层的导电胶层的sem图。
34.图5b为本技术实施例5的导电胶层的sem图。
35.图5c为本技术实施例7的导电胶层的sem图。
36.图5d为本技术实施例9的导电胶层的sem图。
37.图6a为石墨单一成分导电胶粘剂制备得到三层导电胶合板的板面温度红外分布。
38.图6b为本技术实施例5的三层导电胶合板的板面温度红外分布。
39.图6c为本技术实施例7的三层导电胶合板的板面温度红外分布。
40.图6d为本技术实施例9的三层导电胶合板的板面温度红外分布。
41.图中:100、第一单板,200、第二单板,a、导电胶层,b、普通胶层。
具体实施方式
42.为了使本技术领域的人员更好地理解本技术中的技术方案,下面将结合本技术实施例中的附图,对本技术实施例中的技术方案进行清楚、完整地描述,显然,所描述的实施例仅是本技术一部分实施例,而不是全部的实施例。基于本技术中的实施例,本领域普通技术人员在没有做出创造性劳动的前提下所获得的所有其他实施例,都应当属于本技术保护的范围。
43.本技术公开了一种石墨基导电胶粘剂,包括树脂胶粘剂、石墨、膨胀石墨,其中,石墨占石墨基导电胶粘剂的质量分数不低于12.5%,膨胀石墨的添加量占混合填料的质量分数为0.5~3.5%。
44.石墨、膨胀石墨是导电胶粘剂的导电基体的常规选择。石墨是一种传统廉价的碳基材料,来源广泛,但石墨的导电效率相对较低、导电性能相对较差。膨胀石墨是天然石墨鳞片经插层、水洗、干燥、高温膨化得到,膨胀石墨由大量的纳米石墨微片构成,具有优秀的导电(热)性能,由于膨胀石墨的价格较为昂贵,因此常见用于制造模制品(例如公开号为cn104245304b的发明专利中公开的技术方案)、导热性压敏胶粘剂(例如公开号为cn102741372a的发明专利申请中公开的技术方案)等具有相对较高附加值的导热产品的制备。本领域的技术人员过往也曾尝试将石墨与膨胀石墨组成的混合导电填料加入一些胶粘剂,意图以膨胀石墨替换部分石墨从而得到一种具有相对较高导电性能且价格相对低廉的石墨基导电胶粘剂。公开号为cn109148047b,名称为“一种聚苯乙烯泡沫小球表面涂炭的阻值调试方法”的中国发明专利记载了石墨与膨胀石墨共用的技术方案,该技术方案的涂料由25~40%的乙炔炭黑、3~7%的超导炭黑、6~18%的膨胀石墨、6~18%的纳米石墨组成,余量为其它非导电助剂。其中给出了以1:1的比例使用膨胀石墨和纳米石墨。
45.在该技术的启示下,人们首先以1:1的比例向木工胶粘剂中添加膨胀石墨和石墨。结果显示,(1)膨胀石墨的质量分数超过3%之后胶粘剂失去流动性;(2)向木工胶粘剂中添加3%的质量分数的石墨和3%的质量分数的膨胀石墨虽然能够顺利完成涂布并形成有效的导电胶层,但是利用它粘结的胶合板在通电后几乎不能形成电流,胶合板也没有升温的现象。
46.在一般思维方式的引导下,人们增加石墨的质量分数,将石墨的质量分数增加至15%,为了能够形成连续的胶层而将膨胀石墨的添加量降低至2.5%;同时以仅添加15%石墨的木工胶粘剂作为参照。结果显示,由仅添加15%石墨的木工胶粘剂粘结的胶合板在连通12v稳定电压后能够形成电流,通电30分钟后胶合板表面温度能够达到25℃。但是添加有15%石墨和2.5%膨胀石墨的木工胶粘剂粘结的胶合板能够形成电流,但在通电30分钟后胶合板表面温度仅达到22℃。实验结果显然表明,通过以原始膨胀石墨替换部分纳米石墨的技术方案不仅不能起到降低成本、提高导电性能的效果,原始膨胀石墨的添加反而影响了纳米石墨本身的导电性能。
47.以上这些过往的研究、实验默认了膨胀石墨与石墨的共同作用仅体现在两种不同的导电模式的叠加,即膨胀石墨的多孔结构可穿插在石墨形成的二维导电网络中,形成三维连通的立体导电网络。但显然实验的结果并不按照上述前提发展。最终,人们得出结论,当石墨形成的二维导电网络与膨胀石墨形成的三维导电网络重叠后,二者之间存在某种相互干涉,使得同时添加在胶粘剂中得到的导电胶粘剂的导电性能低于单独添加石墨成分的
情形,在石墨中添加膨胀石墨不仅提高了成本反而还降低了导电性能。
48.反观本技术的技术中,发明人克服了以上技术偏见以及常规的思维惯性,创造性的发现:当满足(1)石墨导电颗粒的数量达到阈值,(2)膨胀石墨导电颗粒的数量恰好能够连通平面导电网络两个条件的情况下,极小的膨胀石墨的添加量能够极大的改善石墨或石墨基导电胶粘剂的性能。
49.具体来说,导电胶粘剂中的石墨导电颗粒的数量达到阈值,即占导电胶粘剂12.5%的质量分数(虽然根据胶粘剂种类不同,这一数值略有差异,但大致可以确定是12.5%或略高),石墨的片层相互搭界,石墨晶体内碳原子之间能够形成稳定连通的二维平面导电网络。此时,如果导电胶粘剂中同时还存在数量合适的膨胀石墨导电颗粒,即膨胀石墨导电颗粒的数量恰好能够在垂直方向上连通那些由石墨导电颗粒形成的平面导电网络,膨胀石墨的石墨微片以石墨的片层为基础不断向空间伸长,连通了相邻的两个由石墨形成的平面导网络,从而逐渐形成三维导电网络。发明人创造性的发现所述的“数量合适”、“恰好能够在垂直方向上连通平面导电网络”的数量是指膨胀石墨的添加量占混合导电填料0.5~3.5%的质量分数,换言之,在混合导电填料中石墨与膨胀石墨的添加比例是(99.5:0.5)~(96.5:3.5)。在此情况下,该三维导电网络的主体平面网状结构由石墨晶体内碳原子形成,膨胀石墨的数量极少不足以独立构成三维导电网络,但其中的石墨微片作为桥梁连通相邻的两个由石墨构成的平面导电网状结构,最终构成一个以石墨形成的平面导电网状结构为面、通过膨胀石墨连通的三维导电网络。与现有技术过往的研究具有本质的区别,本技术的技术方案是以石墨为基础,利用膨胀石墨架桥形成三维导电网络,而非意图在石墨形成的平面导电网络中加入由膨胀石墨形成的三维导电网络。从结果来看,本技术的技术方案也达到了意想不到的技术效果,与石墨导电胶粘剂相比较,占混合导电填料0.5~3.5%质量分数的膨胀石墨的添加(膨胀石墨占石墨基导电胶粘剂的质量分数由石墨的实际添加量换算获得),几乎没有增加本技术的石墨基导电胶粘剂的制造成本,但导电性能却有了飞跃式的提高。显然,本实施例的创造性在于,在3%的极限添加量的原始膨胀石墨无法起到导电作用的前提下,12.5%以上的石墨与极少量的膨胀石墨混后能够赋予木工胶粘剂的相对较好的导电性能。
50.另一个方面,根据发明人的创造性发现,我们可以反推理解过往研究与实验的失败原因。(1)石墨的添加量过低时,石墨导电颗粒数量不足以形成二维平面导电网络;(2)石墨的添加量超过阈值但膨胀石墨的添加量过高时,用于连通平面导电网络之外的多余膨胀石墨与胶层形成新的界面,破坏了胶层的整体性,使两种导电颗粒之间的结合面减小,反而无法构建高效的三维导电网络通路,降低了发热元件(石墨基导电胶粘剂胶层)的发热功率。
51.以下通过一些实施例以更细致的数据进一步阐述本技术的技术方案。
52.实施例1
53.一种石墨基导电胶粘剂包括树脂胶粘剂、石墨、膨胀石墨。树脂胶粘剂是市售获得的脲醛树脂胶粘剂。石墨呈粉末状,粒径为300~340目,该粒径范围内的石墨颗粒均可使用,不需要进一步筛选,石墨颗粒和膨胀石墨颗粒的添加量占石墨基导电胶粘剂13%的质量分数,其中石墨颗粒与膨胀石墨颗粒的添加量之比为99:1,膨胀石墨呈粉末状,粒径为75~85目,该粒径范围内的膨胀石墨颗粒均可使用,不需要进一步筛选。
54.以制备1000g本实施例的石墨基导电胶粘剂为例。首先,称取128.7g石墨颗粒、1.3g膨胀石墨颗粒混合组成石墨/膨胀石墨导电填料,并按比例称取870.0g脲醛树脂胶粘剂。随后,在常温条件下,将上述石墨/膨胀石墨导电填料加入脲醛树脂胶粘剂中,以400r/min的转速机械搅拌10min从而得到本实施例的石墨基导电胶粘剂。搅拌速度在350~450r/min范围内,搅拌时间在8~12min范围内均可,同时本领域技术人员可以知晓,选择较高的搅拌速度时应当适当减少搅拌时间,反之则应当适当增加搅拌时间。
55.以制备三层导电胶合板为例。首先,取3片规格为300mm
×
300mm
×
2mm的杨木单板,其中1片记为第一单板100,其余2片记为第二单板200,在第一单板100的表面涂布石墨基导电胶粘剂,涂布量为125g/
㎡
形成导电胶层a;在其中1片第二单板200的表面涂布非导电胶粘剂,涂布量为145g/
㎡
形成普通胶层b,本实施例中选用与石墨基导电胶粘剂的基础胶粘剂相同的脲醛树脂胶粘剂。随后,在导电胶层a的两端铺设有导电胶带。最后,由上至下依次层叠第二、第一、第二单板200,100,200,并在120℃、1.25mpa的工艺条件下热压6min后得到本实施例的三层导电胶合板。参照图1所示,本实施例的三层导电胶合板包括三层层叠的单板200,100,200,三层单板相互之间通过胶层粘结,其中一个胶层为导电胶层a,且该导电胶层a由石墨基导电胶粘剂形成,导电胶层a的两端铺设有导电胶带。
56.参照图2a所示,由本实施例的石墨基导电胶粘剂构成的导电胶层中,石墨基导电胶粘剂中的石墨导电颗粒的数量达到阈值,石墨的片层相互搭界,石墨晶体内碳原子之间能够形成稳定连通的二维平面导电网络,并且相邻石墨的片层之间仍有间隙。参照图2b所示,以99:1的质量比加入膨胀石墨导电颗粒后,膨胀石墨的石墨微片以石墨的片层为基础不断向空间伸长,连通了相邻的两个由石墨形成的平面导网络,并架桥连接水平方向的石墨片层,填补了石墨片层之间的间隙,从而逐渐形成三维导电网络。
57.根据胶合理论,胶合板胶合界面的强度与胶粘剂在木材表面的浸润程度有关。由于木材单板表面粗糙,因此普通胶层施胶后,有部分胶粘剂渗入木材内部填充不平整沟槽,然后再胶接,因此需要的施胶量更大。而导电胶层中存在大量微米级石墨颗粒,在热压时可填充单板表面不平整的沟槽,继而进一步产生胶接,因此可节省施胶量。现有技术中,人们普遍认为石墨成分的添加会影响胶粘剂的胶合强度。这是因为现有技术中,为了达到需要的导热性能应当添加相对较大量的石墨颗粒,大量的石墨颗粒的存在影响了胶层的连续性,继而影响了导电胶粘剂的胶合性能。而在本实施例中,达到需要的导电性能仅需要极少的石墨颗粒与膨胀石墨颗粒,石墨颗粒与膨胀石墨颗粒足以预先填平单板胶合界面的沟槽,但又不影响胶粘剂的连续性与成膜性能,能够在提高导电性能的同时以相对较小的施胶量满足标准规定与使用所需的胶合性能。由于施胶量的减小,所以基本上可以抵消因膨胀石墨的添加而微小增加的胶粘剂成本。
58.另一个意想不到的技术效果是导电胶合板的材料刚性的提高。发明人认为,这是由于石墨的填充作用使导电胶合板的整体刚性有所提高。以上实验数据请参见表1的弹性模量。
59.以制备五层导电胶合板为例。首先,取5片规格为300mm
×
300mm
×
2mm的杨木单板,其中1片记为第一单板100,其余4片记为第二单板200,在第一单板100的表面涂布石墨基导电胶粘剂,涂布量为125g/
㎡
形成导电胶层a;在其中3片第二单板200的表面涂布非导电胶粘剂,涂布量为145g/
㎡
形成普通胶层b。随后,在导电胶层a的两端铺设有导电胶带。最后,
由上至下依次层叠未施胶的第二单板200、第一单板100、施胶的3片第二单板200,并在120℃、1.30mpa的工艺条件下热压6min后得到本实施例的五层导电胶合板。参照图3所示,本实施例的五层导电胶合板包括五层层叠的单板200,100,200,200,200,单板相互之间通过胶层粘结,其中一个胶层为导电胶层a,且该导电胶层a由石墨基导电胶粘剂形成,导电胶层a的两端铺设有导电胶带。
60.以制备五层导电胶合板为例。首先,取五片杨木单板,其中2片记为第一单板100,其余3片记为第二单板200,在2片第一单板100的表面涂布石墨基导电胶粘剂,涂布量为125g/
㎡
形成导电胶层a;在其中2片第二单板200的表面涂布非导电胶粘剂,涂布量为145g/
㎡
形成普通胶层b。随后,在导电胶层a的两端铺设有导电胶带。最后,由上至下依次层叠未施胶的第二单板200、第一单板100、施胶的第二单板200、第一单板100、施胶的第二单板200,并在120℃、1.30mpa的工艺条件下热压6min后得到本实施例的五层导电胶合板。参照图4所示,本实施例的五层导电胶合板包括五层层叠的单板200,100,200,100,200,单板相互之间通过胶层粘结,其中两层胶层为导电胶层a,且该导电胶层a由石墨基导电胶粘剂形成,两层导电胶层a的两端均铺设有导电胶带。
61.实施例2
62.实施例2与实施例1的区别在于,1000g石墨基导电胶粘剂中包括870.0g脲醛树脂胶粘剂、127.4g石墨颗粒、2.6g膨胀石墨颗粒,换言之,石墨颗粒与膨胀石墨颗粒的添加量之比为98:2。
63.按照实施例1的方法制备三层导电胶粘剂,在第一单板100表面涂布本实施例配方制得的石墨基导电胶粘剂,涂布量为120g/平方米。
64.实施例3
65.实施例3与实施例1的区别在于,1000g石墨基导电胶粘剂中包括870.0g脲醛树脂胶粘剂、126.1g石墨颗粒、3.9g膨胀石墨颗粒,换言之,石墨颗粒与膨胀石墨颗粒的添加量之比为97:3。
66.按照实施例1的方法制备三层导电胶粘剂,在第一单板100表面涂布本实施例配方制得的石墨基导电胶粘剂,涂布量为120g/平方米。
67.表1中示出了实施例1至3的各导电胶合板的材料性能。采用tp720温度巡检仪测试各导电胶合板的表面温度变化情况,不同导电胶合板各选3块,每块导电胶合板上选取5个测温点分别布置热电偶,施加12v电压,通电30min记录导电胶合板板面温度,结果取平均值。采用tc3000e导热系数测定仪,测定导电胶层的导热系数,样品直径为50mm、厚度为5mm,取样测定三次,结果取平均值。采用by302x2/2万能实验压机,参照gb/t17657-2013《人造板及饰面人造板理化性能试验方法》测试导电胶合板的胶合强度、静曲强度和弹性模量。对照组1为普通三层胶合板,使用与石墨基导电胶粘剂的基础胶粘剂相同的脲醛树脂胶粘剂,涂布量125g/
㎡
。对照组2的导电胶粘剂使用石墨单一成分的导电胶粘剂,其中树脂胶粘剂为脲醛树脂胶粘剂,石墨的质量分数为15%。
68.表1.实施例1至3的各导电胶合板的材料性能
[0069][0070]
实施例4
[0071]
实施例4与实施例1的区别在于,1000g石墨基导电胶粘剂中包括850.0g脲醛树脂胶粘剂、149.25g石墨颗粒、0.75g膨胀石墨颗粒,换言之,石墨颗粒与膨胀石墨颗粒的添加量之比为99.5:0.5。
[0072]
按照实施例1的方法制备三层导电胶粘剂,在第一单板100表面涂布本实施例配方制得的石墨基导电胶粘剂,涂布量为120g/平方米。
[0073]
实施例5
[0074]
实施例5与实施例4的区别在于,1000g石墨基导电胶粘剂中包括850.0g脲醛树脂胶粘剂、148.5g石墨颗粒、1.5g膨胀石墨颗粒,换言之,石墨颗粒与膨胀石墨颗粒的添加量之比为99:1。
[0075]
参照图5a所示,导电胶层中石墨的片层之间相互搭接,但其中仍存在孔隙无法形成连续平整的界面。参照图5b所示,当添加约1wt%(相对于混合导电填料的质量分数)的膨胀石墨后,具有高径厚比的膨胀石墨使得导电颗粒之间更为致密的搭接,胶层表面趋于平整。图5b中,由于含量较少不能观察到膨胀石墨颗粒。
[0076]
参照图6a、6b所示,显然,膨胀石墨的加入在提高导电胶合板发热性能的同时,还提高了表面温度均匀性。
[0077]
实施例6
[0078]
实施例6与实施例4的区别在于,1000g石墨基导电胶粘剂中包括850.0g脲醛树脂胶粘剂、147.75g石墨颗粒、2.25g膨胀石墨颗粒,换言之,石墨颗粒与膨胀石墨颗粒的添加量之比为98.5:1.5。
[0079]
实施例7
[0080]
实施例7与实施例1的区别在于,1000g石墨基导电胶粘剂中包括850.0g脲醛树脂胶粘剂、147.0g石墨颗粒、3.0g膨胀石墨颗粒,换言之,石墨颗粒与膨胀石墨颗粒的添加量之比为98:2,。
[0081]
以制备三层导电胶合板为例,实施例7与实施例1的区别在于,第一单板100表面石墨基导电胶粘剂的涂布量为120g/
㎡
,第二单板200表面非导电胶粘剂的涂布量为140g/
㎡
。
[0082]
参照图5c所示,当膨胀石墨的添加量达到2wt%(相对于混合导电填料的质量分数)时,可以明显观察到膨胀石墨颗粒,此时石墨微片不断向空间伸长,逐渐形成三维导电网络,导电网络形成的导电效率急剧提升,导电胶合板的升温速率明显加快。
[0083]
将图6c与图6b、6d相比较,膨胀石墨添加量为2wt%(相对于混合导电填料的质量
分数)时发热效果最为明显且温度分布最为均匀。
[0084]
以制备五层导电胶合板为例,实施例7与实施例1的区别在于,第一单板100表面石墨基导电胶粘剂的涂布量为120g/
㎡
,第二单板200表面非导电胶粘剂的涂布量为140g/
㎡
。
[0085]
以制备五层导电胶合板为例,实施例7与实施例1的区别在于,2片第一单板100表面石墨基导电胶粘剂的涂布量为110g/
㎡
,第二单板200表面非导电胶粘剂的涂布量为140g/
㎡
。
[0086]
实施例8
[0087]
实施例8与实施例4的区别在于,1000g石墨基导电胶粘剂中包括850.0g脲醛树脂胶粘剂、146.25g石墨颗粒、3.75g膨胀石墨颗粒,换言之,石墨颗粒与膨胀石墨颗粒的添加量之比为97.5:2.5。
[0088]
实施例9
[0089]
实施例9与实施例4的区别在于,1000g石墨基导电胶粘剂中包括850.0g脲醛树脂胶粘剂、145.5g石墨颗粒、4.5g膨胀石墨颗粒,换言之,石墨颗粒与膨胀石墨颗粒的添加量之比为97:3。
[0090]
参照图5d所示,当膨胀石墨增至3wt%(相对于混合导电填料的质量分数)时,可以观察到大量的膨胀石墨微片。并且已经能够观察到过多的导电粒子破坏了导电胶层的整体性的现象,此时,两种导电颗粒之间的结合面减小,反而无法构建高效的网络通道,降低了导电胶层的发热功率。但膨胀石墨的添加量为3wt%(相对于混合导电填料的质量分数)时的导电胶层的导电性能仍优于石墨单一成分的导电胶层。
[0091]
将图6d与图6b、6c相比较,膨胀石墨添加量为3wt%(相对于混合导电填料的质量分数)时温度分布的均匀性劣于添加量为2wt%(相对于混合导电填料的质量分数)的情形,但仍优于添加量为1wt%(相对于混合导电填料的质量分数)的情形。这是由于电热层在平行于电热层方向上导热性能的差异所导致。
[0092]
实施例10
[0093]
实施例10与实施例4的区别在于,1000g石墨基导电胶粘剂中包括850.0g脲醛树脂胶粘剂、144.75g石墨颗粒、5.25g膨胀石墨颗粒,换言之,石墨颗粒与膨胀石墨颗粒的添加量之比为96.5:3.5。
[0094]
表2中示出了实施例4至10的各导电胶合板的材料性能。
[0095]
表2.实施例4至10的各导电胶合板的材料性能
[0096][0097]
实施例11
[0098]
实施例11与实施例1的区别在于,1000g石墨基导电胶粘剂中包括830.0g脲醛树脂胶粘剂、168.3g石墨颗粒、1.7g膨胀石墨颗粒,换言之,石墨颗粒与膨胀石墨颗粒的添加量之比为99:1。
[0099]
按照实施例1的方法制备三层导电胶粘剂,在第一单板100表面涂布本实施例配方制得的石墨基导电胶粘剂,涂布量为115g/平方米,第二单板200表面非导电胶粘剂的涂布量为135g/
㎡
。
[0100]
实施例12
[0101]
实施例12与实施例11的区别在于,1000g石墨基导电胶粘剂中包括830.0g脲醛树脂胶粘剂、166.6g石墨颗粒、3.4g膨胀石墨颗粒,换言之,石墨颗粒与膨胀石墨颗粒的添加量之比为98:2。
[0102]
实施例13
[0103]
实施例13与实施例11的区别在于,1000g石墨基导电胶粘剂中包括830.0g脲醛树脂胶粘剂、164.9g石墨颗粒、5.1g膨胀石墨颗粒,换言之,石墨颗粒与膨胀石墨颗粒的添加量之比为97:3。
[0104]
表3中示出了实施例11至13的三层导电胶合板的材料性能。
[0105]
表3.实施例11至13的各导电胶合板的材料性能
[0106][0107]
实施例14
[0108]
实施例14与实施例1的区别在于,树脂胶粘剂为酚醛树脂胶粘剂,1000g石墨基导电胶粘剂中包括860.0g酚醛树脂胶粘剂、138.6g石墨颗粒、1.4g膨胀石墨颗粒,换言之,石
墨颗粒与膨胀石墨颗粒的添加量之比为99:1、0.141%。
[0109]
按照实施例1的方法制备三层导电胶粘剂,在第一单板100表面涂布本实施例配方制得的石墨基导电胶粘剂,涂布量为110g/平方米,第二单板200表面非导电胶粘剂的涂布量为130g/
㎡
。
[0110]
实施例15
[0111]
实施例15与实施例14的区别在于,1000g石墨基导电胶粘剂中包括860.0g酚醛树脂胶粘剂、137.2g石墨颗粒、2.8g膨胀石墨颗粒,换言之,石墨颗粒与膨胀石墨颗粒的添加量之比为98:2。
[0112]
按照实施例1的方法制备三层导电胶粘剂,在第一单板100表面涂布本实施例配方制得的石墨基导电胶粘剂,涂布量为120g/平方米,第二单板200表面非导电胶粘剂的涂布量为140g/
㎡
。
[0113]
实施例16
[0114]
实施例16与实施例14的区别在于,1000g石墨基导电胶粘剂中包括860.0g酚醛树脂胶粘剂、135.8g石墨颗粒、4.2g膨胀石墨颗粒,换言之,石墨颗粒与膨胀石墨颗粒的添加量之比为97:3。
[0115]
按照实施例1的方法制备三层导电胶粘剂,在第一单板100表面涂布本实施例配方制得的石墨基导电胶粘剂,涂布量为130g/平方米,第二单板200表面非导电胶粘剂的涂布量为140g/
㎡
。
[0116]
表4中示出了实施例14至16的三层导电胶合板的材料性能。
[0117]
表4.实施例14至16的各导电胶合板的材料性能
[0118][0119]
实施例17
[0120]
实施例17与实施例1的区别在于,树脂胶粘剂为酚醛树脂胶粘剂,1000g石墨基导电胶粘剂中包括840.0g酚醛树脂胶粘剂、158.4g石墨颗粒、1.6g膨胀石墨颗粒,换言之,石墨颗粒与膨胀石墨颗粒的添加量之比为99:1。
[0121]
按照实施例1的方法制备三层导电胶粘剂,在第一单板100表面涂布本实施例配方制得的石墨基导电胶粘剂,涂布量为110g/平方米,第二单板200表面非导电胶粘剂的涂布量为130g/
㎡
。
[0122]
实施例18
[0123]
实施例18与实施例1的区别在于,树脂胶粘剂为酚醛树脂胶粘剂,1000g石墨基导电胶粘剂中包括840.0g酚醛树脂胶粘剂、156.8g石墨颗粒、3.2g膨胀石墨,换言之,石墨颗粒与膨胀石墨颗粒的添加量之比为98:2,石墨颗粒与膨胀石墨颗粒的添加量占石墨基导电胶粘剂的质量分数分别是16%、0.327%。
[0124]
按照实施例1的方法制备三层导电胶粘剂,在第一单板100表面涂布本实施例配方
制得的石墨基导电胶粘剂,涂布量为120g/平方米,第二单板200表面非导电胶粘剂的涂布量为140g/
㎡
。
[0125]
实施例19
[0126]
实施例19与实施例1的区别在于,树脂胶粘剂为酚醛树脂胶粘剂,1000g石墨基导电胶粘剂中包括840.0g酚醛树脂胶粘剂、155.2g石墨颗粒、4.8g膨胀石墨,换言之,石墨颗粒与膨胀石墨颗粒的添加量之比为97:30.495%。
[0127]
按照实施例1的方法制备三层导电胶粘剂,在第一单板100表面涂布本实施例配方制得的石墨基导电胶粘剂,涂布量为130g/平方米,第二单板200表面非导电胶粘剂的涂布量为140g/
㎡
。
[0128]
表5中示出了实施例17至19的三层导电胶合板的材料性能。为了能够更好的体现实施例17至19的三层导电胶合板的胶合性能,表5中的对照组3、4中均改为酚醛树脂胶粘剂胶粘制得的胶合板。
[0129]
表5实施例17至19的各导电胶合板的材料性能
[0130][0131]
以上描述是为了进行图示说明而不是为了进行限制。通过阅读上述描述,在所提供的示例之外的许多实施方式和许多应用对本领域技术人员来说都将是显而易见的。因此,本教导的范围不应该参照上述描述来确定,而是应该参照所附权利要求以及这些权利要求所拥有的等价物的全部范围来确定。出于全面之目的,所有文章和参考包括专利申请和公告的公开都通过参考结合在本文中。在前述权利要求中省略这里公开的主题的任何方面并不是为了放弃该主体内容,也不应该认为申请人没有将该主题考虑为所公开的申请主题的一部分。