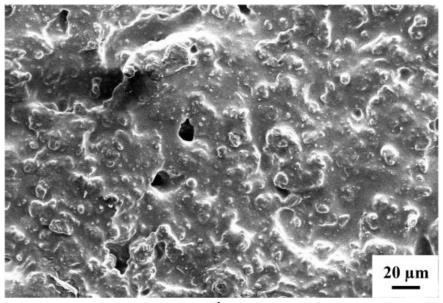
1.本发明涉及超疏水材料技术领域,尤其涉及一种导热超疏水涂料及其制备方法与应用。
背景技术:2.天气潮湿或者有水附着在裸露的高压输电线路上时经常会发生电晕放电现象,不仅会造成巨大的电力损耗,而且对附近居民的正常生活产生较大困扰。目前,电力工程中用于抑制电晕放电的方法主要是改变输电线及变电站本身的结构与性质,具体措施包括:增加分裂导线的直径与数目、提高塔杆高度以及使用球形部件将导线空心化等。然而,这些举措往往投入大且维护难度高。相比之下,在导线上涂覆具有疏水功能的涂料的方式则具有施工便捷、成本较低、维护简单等优点,应用前景广阔。
3.超疏水涂料形成的涂层的水接触角大于150
°
且滚动角小于10
°
,水滴在涂层表面容易自发滚落并带走表面的污秽。凭借此特性,超疏水涂料在玻璃的自清洁、建筑物外表的防腐蚀、织物的防污防水、工业含油废水的油水分离以及输电线防覆冰等领域中均展现出巨大的应用价值。将超疏水涂料应用于输电线路,能够修补导线表面的破损、皱皮处以及因环境产生的毛刺与划痕,这样不仅改变导线的曲率半径并降低导线周围的局部场强,而且还可以避免水滴附着以减少起晕点,从而抑制电晕噪声现象的发生。
4.目前少数科研工作者开展了疏水涂料在输电线路的应用研究。例如,吴执等人研究了水滴形态对输电线路电晕放电特性的影响,并提出在导线上涂覆室温硫化硅橡胶(rtv)、液体硅橡胶(lsr)或持久性就地成型防污闪复合涂料(prtv)来改善导线在雨天的电晕放电问题(吴执.水滴形态对输电线路导线电晕放电特性的影响[d].重庆:重庆大学,2014)。但上述机硅涂料的水接触角均低于120
°
,且有机硅的低表面能使得涂层在铝导线表面的粘附性差,较难实现长期的牢固附着。此外,用于高压线缆的涂料需要具有导热性,能够及时将电流传输过程中产生的热量传递出去。然而,目前国内外鲜少出现关于同时具有超疏水性和导热性的涂料的报道。虽然有学者采用碳纳米管作为导热填料来制备导热超疏水涂料,但这类填料的价格较昂贵,不适宜大面积推广和应用。因此,开发一种成本低并能牢固附着在金属表面的导热超疏水涂料显得尤为重要。
技术实现要素:[0005]
本发明的首要目的在于克服现有技术的缺点与不足,提供一种导热超疏水涂料。
[0006]
本发明的另一目的在于提供上述导热超疏水涂料的制备方法。
[0007]
本发明的再一目的在于提供上述导热超疏水涂料的应用。
[0008]
本发明的目的通过下述技术方案实现:一种导热超疏水涂料的制备方法,包括以步骤:
[0009]
(1)将二氧化硅分散于氨水溶液中,得到二氧化硅悬浮液,将其与含氟硅烷偶联剂的醇溶液反应,离心,洗涤,干燥,得到氟化二氧化硅颗粒;
[0010]
优选地,步骤(1)所述二氧化硅为气相二氧化硅。
[0011]
优选地,步骤(1)所述二氧化硅的尺寸为30-50nm。
[0012]
优选地,步骤(1)所述含氟硅烷偶联剂为1h,1h,2h,2h-十七氟癸基三甲氧基硅烷、1h,1h,2h,2h-十七氟癸基三乙氧基硅烷和全氟辛基三乙氧基硅烷中的至少一种。
[0013]
优选地,步骤(1)和(2)所述含氟硅烷偶联剂的醇溶液采用的溶剂为乙醇。
[0014]
优选地,步骤(1)所述含氟硅烷偶联剂与二氧化硅按照2-4ml:3-6g配比。
[0015]
优选地,步骤(1)所述反应为搅拌24-28h。
[0016]
优选地,步骤(1)所述离心为6000-10000rpm离心5-10min。
[0017]
优选地,步骤(1)所述干燥为50-60℃下真空干燥1-3h。
[0018]
优选地,步骤(1)所述洗涤采用乙醇。
[0019]
(2)将氮化硼与氢氧化钠溶液混合,反应,离心,洗涤,干燥,得到羟基化氮化硼,将其分散于含氟硅烷偶联剂的醇溶液中,再次反应,离心,再次洗涤,再次干燥,得到氟化氮化硼粉末;
[0020]
优选地,步骤(2)所述氮化硼为六方氮化硼。
[0021]
优选地,步骤(2)所述氮化硼的尺寸为40-60μm。
[0022]
优选地,步骤(2)所述氢氧化钠溶液的浓度为2-5mol/l。
[0023]
优选地,步骤(2)所述氮化硼与含氟硅烷偶联剂按照3-4g:1-2ml配比。
[0024]
优选地,步骤(2)所述反应为100-120℃反应20-24h。
[0025]
优选地,步骤(2)所述再次反应的时间为5-8h。
[0026]
优选地,步骤(2)所述离心均为2000-3000rpm离心30-40min。
[0027]
优选地,步骤(2)所述洗涤采用去离子水。
[0028]
优选地,步骤(2)所述再次洗涤采用乙醇。
[0029]
优选地,步骤(2)所述干燥为60-65℃下真空干燥2-4h。
[0030]
优选地,步骤(2)所述干燥为50-60℃真空干燥1-3h。
[0031]
(3)将乙烯基硅油、抑制剂、铂催化剂和含氢硅油于有机溶剂中混合,加入步骤(1)所述氟化二氧化硅颗粒、步骤(2)所述氟化氮化硼粉末,分散均匀,得到导热超疏水涂料。
[0032]
优选地,步骤(3)所述乙烯基硅油中的乙烯基含量为0.05-0.22%。
[0033]
优选地,步骤(3)所述含氢硅油中的含氢量为1.4-1.6%。
[0034]
优选地,步骤(3)所述铂催化剂为karstedt催化剂,铂的含量为2000ppm。
[0035]
优选地,步骤(3)所述抑制剂为炔醇类抑制剂。
[0036]
优选地,步骤(3)所述抑制剂、铂催化剂和含氢硅油采用所述有机溶剂预先制备成溶液,三者的浓度依次为1wt%、1wt%、0.33wt%,三者的溶液以及乙烯基硅油按照质量比1-2:4-5:4-5:4-8配比。
[0037]
优选地,步骤(3)所述氟化二氧化硅颗粒、氟化氮化硼粉末与乙烯基硅油的质量比为2-4:1-2:3-8。
[0038]
优选地,步骤(3)所述有机溶剂为正己烷、四氢呋喃、乙酸乙酯、和甲苯中的至少一种。
[0039]
优选地,步骤(3)所述分散均匀为搅拌5-10min,继续超声分散20-30min。
[0040]
一种导热超疏水涂料,通过上述制备方法制备得到。
[0041]
上述导热超疏水涂料在抑制高压线缆的电晕噪声中的应用。
[0042]
与现有技术相比,本发明具有以下有益效果:
[0043]
(1)本发明的涂料具有超疏水性,通过以下两方面实现:其一,乙烯基硅油和含氢硅油均属于非极性物质,通过硅氢加成反应生成的交联有机硅网络赋予涂层低表面能,并能束缚导热填料的脱落;其二,微米级尺寸的氮化硼和纳米级尺寸的二氧化硅经过氟化处理后呈非极性,能够较均匀地分散在非极性的乙烯基硅油和含氢硅油中,在涂层固化后共同构建表面的微纳粗糙结构;;且氮化硼为片状结构,自身具有良好的成膜性,并且能够包覆或锚定二氧化硅颗粒,提升粗糙结构的强度。涂料的导热性主要由导热填料氟化氮化硼所提供,片状的氟化氮化硼在涂层中均匀分散,形成了连续交错的导热网络,从而有利于热量的快速传递。以乙烯基硅油和含氢硅油为基体材料制备的涂料形成的涂层之所以能够在金属表现出良好的粘附力,主要是因为含氢硅油和乙烯基硅油具有良好的分子运动能力,能够渗透进入金属表面的微结构中,这样涂层固化后与金属表面的微结构之间形成了“锚固”连接,同时赋予涂层优良的耐候性;并且等离子体处理基材,使表面带有极性基团,能够提升涂层的附着力。本发明所制备的导热超疏水涂料形成的涂层接触角达到150
°
以上,滚动角小于10
°
,且热扩散系数达到1.1w/(m
·
k),并且具有良好的粘附力,且经过横切与剥离测试后,其水接触角变化不大,仍具有超疏水性。
[0044]
(2)本发明导热超疏水涂料所用原料成本低廉、容易获得。本发明导热超疏水涂料的制备方法具有反应条件温和、不产生副产物、单体转化率高等优点。制备的涂料可采用一步喷涂的方法,操作简便,无需特定的仪器设备。
附图说明
[0045]
图1为实施例1中二氧化硅与氟化二氧化硅的红外谱图。
[0046]
图2为实施例1中氮化硼、羟基化氮化硼与氟化氮化硼的红外谱图。
[0047]
图3为实施例1制备的导热超疏水涂层的扫描电镜图(图像放大倍数为200倍)。
具体实施方式
[0048]
下面将结合本发明实施例中的附图,对本发明实施例中的技术方案进行清楚、完整地描述,显然,所描述的实施例仅仅是本发明一部分实施例,而不是全部的实施例。基于本发明中的实施例,本领域普通技术人员在没有作出创造性劳动前提下所获得的所有其他实施例,都属于本发明保护的范围。
[0049]
实施例1
[0050]
将4ml氨水加入到16ml去离子水中并混合均匀,然后加入3g气相二氧化硅颗粒(40nm),在室温下搅拌5min后再置于超声清洗仪(fb11201,fisherbrand,美国)中分散10min,得到二氧化硅悬浮液;将4ml 1h,1h,2h,2h-十七氟癸基三甲氧基硅烷加入80ml无水乙醇中并搅拌10min,得到含氟硅烷偶联剂的乙醇溶液;将二氧化硅悬浮液加入乙醇混合液中并持续搅拌24h。产物经6000rpm离心10min后,用乙醇洗涤并在50℃下真空干燥3h,得到氟化二氧化硅颗粒;
[0051]
将2g六方氮化硼粉末(50μm)加入30ml浓度为2mol/l的氢氧化钠溶液中并充分搅拌,加热至120℃反应20h。产物经2000rpm离心35min后,用去离子水洗涤并在60℃下真空干
燥2h,即得羟基化氮化硼粉末;进一步地,将0.5ml1h,1h,2h,2h-十七氟癸基三甲氧基硅烷加入80ml无水乙醇中并搅拌下5min,加入羟基化氮化硼粉末,在搅拌条件下于室温反应6h;产物经2000r/min的转速离心35min,乙醇洗涤,60℃真空干燥2h,即得氟化氮化硼粉末。
[0052]
将含氢硅油(含氢量为1.5%)、抑制剂1-乙炔基环己醇和karstedt催化剂用正己烷稀释,得到0.33wt%的含氢硅油溶液、1wt%的抑制剂溶液和1wt%的karstedt催化剂溶液。接着,将0.8g乙烯基硅油(乙烯基含量为0.05%)、0.18g抑制剂溶液、0.75gkarstedt催化剂溶液与0.766g含氢硅油溶液依次加入30ml正己烷中并搅拌6min;再将0.2g氟化氮化硼与0.4g氟化二氧化硅颗粒先后加入并搅拌5min,继续超声分散20min使其分散均匀,得到导热超疏水涂料;同时,用无水乙醇润洗马口铁片(25mm
×
25mm
×
0.28mm),干燥后放入等低温离子体发射仪(plasmaflecto 10,plasman technology,德国)中清洗300s。最后设置喷枪压力为0.6mpa,喷枪与基底的喷涂距离为15cm,喷枪的移动速度为1cm/s,并往复移动1次将涂料喷涂于马口铁片上,在80℃下固化1h使溶剂充分挥发,制得导热超疏水涂层。
[0053]
图1为本实施例中二氧化硅经过氟硅烷改性前后的红外对比谱图。从图1可以看出,未改性的二氧化硅在947.7cm-1
与3418.4cm-1
处出现较强的吸收峰,这归属于原生sio2的-si-oh基团;在1116.6cm-1
与800cm-1
处出现了si-o-si的吸收峰;1618.6cm-1
处的吸收峰为水;改性后的在1198.7cm-1
处出现吸收峰,归属于c-f的伸缩振动,表明sio2表面有-cf2、-cf3的存在,证实了氟硅烷的成功接枝。
[0054]
图2为本实施例中氮化硼、羟基化氮化硼与氟化氮化硼的红外对比谱图。从图2可以看出,氮化硼、羟基化氮化硼以及氟化氮化硼均在814与1372处有吸收峰,分别对应于b-n的面外弯曲振动、b-n的面内拉伸振动;羟基化氮化硼在3415处出现-oh的伸缩振动;氟化氮化硼在1195处出现c-f的伸缩振动,验证了氟化改性的成功。以上结果证实了sio2与bn疏水改性的成功,疏水基团的存在使得涂层具有较优良的疏水性。
[0055]
图3为本实施例导热超疏水涂层放大200倍的扫描电镜图。从图3可以看出,涂层的表面较为粗糙,可以观察到许多细小的凸起,具有“颗粒感”;且微米尺度下的氮化硼被有机硅包覆,实现牢固地附着;大量的疏水化二氧化硅被氮化硼片层黏连锚定,共同构筑微纳粗糙结构。
[0056]
为了评价所制得的涂层的超疏水性,用光学接触角测量仪(dsa100,kruss,德国)测量涂层的表面润湿性。在室温下用5μl水作为探针液进行视频捕捉,从至少三个不同的位置获得接触角数据并计算平均值。本实例所制得的涂层的水滴静态接触角为153
°
,滚动角为9
°
,具有超疏水性能。
[0057]
为了评价超疏水涂层的导热性,利用闪光法导热系数仪(lfa 447 nanoflash,netzsch,德国)测量涂层的面内热扩散系数。本实施例所制备的超疏水涂层的导热性优良,其面内热扩散系数为1w/(m
·
k)。
[0058]
为了评价超疏水涂层的粘附性,根据iso2409-2013标准,对本实施例制备的涂层进行横切与剥离试验。具体地,利用刀片在涂层表面划刻“#”型方格,每道划痕间距2cm;接着将压敏胶带贴附在涂层表面,并用50g的砝码按压5s;之后将胶带揭下,观察涂层的剥离受损情况;根据剥落面积将涂层的粘附性定义为0-5级,0级表明涂层有极好的粘附性,5级则表面涂层的粘附性极差。从表1可以看出,本实施例所制备的超疏水涂层的粘附力达到1级,且经过横切与剥离测试后,其水接触角变化不大,仍具有超疏水性。
[0059]
实施例2
[0060]
将6ml氨水加入到25ml去离子水中并混合均匀,然后加入4g气相二氧化硅颗粒(50nm),在室温下搅拌10min后再置于超声清洗仪(fb11201,fisherbrand,美国)中分散10min,得到二氧化硅悬浮液;将3ml1h,1h,2h,2h-十七氟癸基三乙氧基硅烷加入100ml无水乙醇中并搅拌10min,得到含氟硅烷偶联剂的乙醇溶液;将二氧化硅悬浮液加入乙醇混合液中并持续搅拌24h。产物经10000rpm离心5min后,用乙醇洗涤并在60℃下真空干燥1h,得到氟化二氧化硅颗粒;
[0061]
将4g六方氮化硼粉末(60μm)加入30ml浓度为5mol/l的氢氧化钠溶液中并充分搅拌,加热至120℃反应20h。产物经2000rpm离心35min后,用去离子水洗涤并在60℃下真空干燥2h,即得羟基化氮化硼粉末;进一步地,将1ml1h,1h,2h,2h-十七氟癸基三乙氧基硅烷加入100ml无水乙醇中并搅拌下10min,加入羟基化氮化硼粉末,在搅拌条件下于室温反应8h;产物经3000r/min的转速将离心30min、乙醇洗涤,60℃真空干燥2h,即得氟化氮化硼粉末。
[0062]
将含氢硅油(含氢量1.6%)、抑制剂2-甲基-3-丁炔-2-醇和karstedt催化剂用四氢呋喃稀释,得到0.33wt%的含氢硅油溶液、1wt%的抑制剂溶液和1wt%的karstedt催化剂溶液。接着,将0.8g乙烯基硅油(乙烯基含量0.22%)、0.18g抑制剂溶液、0.75gkarstedt催化剂溶液与0.766g含氢硅油溶液依次加入30ml四氢呋喃中并搅拌8min;再将0.25g氟化氮化硼与0.5g氟化二氧化硅颗粒先后加入并搅拌10min,继续超声分散30min使其分散均匀,得到导热超疏水涂料;同时,用无水乙醇润洗马口铁片(25mm
×
25mm
×
0.28mm),干燥后放入等低温离子体发射仪(plasmaflecto 10,plasman technology,德国)中清洗300s。最后设置喷枪压力为0.7mpa,喷枪与基底的喷涂距离为20cm,喷枪的移动速度为2cm/s,并往复移动2次将导热超疏水涂料喷涂于马口铁片上,在80℃下固化1h使溶剂充分挥发,制得导热超疏水涂层。
[0063]
本实施例中二氧化硅与氮化硼改性前后的红外对比谱图以及涂层的扫描电镜图基本同图1、图2与图3,表明氟硅烷成功地接枝到了二氧化硅与氮化硼的表面,且涂层具备较粗糙的微观结构,这将赋予涂层优良的超疏水特性。
[0064]
为了评价所制得的涂层的超疏水性,用光学接触角测量仪(dsa100,kruss,德国)测量涂层的表面润湿性。在室温下用5μl水作为探针液进行视频捕捉,从至少三个不同的位置获得接触角数据并计算平均值。本实例所制得的涂层的水滴静态接触角为159
°
,滚动角为8
°
,具有超疏水性能。
[0065]
为了评价超疏水涂层的导热性,利用闪光法导热系数仪(lfa 447 nanoflash,netzsch,德国)测量涂层的面内热扩散系数。本实施例所制备的超疏水涂层的导热性优良,其面内热扩散系数为1.1w/(m
·
k)。
[0066]
为了评价超疏水涂层的粘附性,根据iso2409-2013标准,对本实施例制备的涂层进行横切与剥离试验。具体地,利用刀片在涂层表面划刻“#”型方格,每道划痕间距2cm;接着将压敏胶带贴附在涂层表面,并用50g的砝码按压5s;之后将胶带揭下,观察涂层的剥离受损情况;根据剥落面积将涂层的粘附性定义为0-5级,0级表明涂层有极好的粘附性,5级则表面涂层的粘附性极差。表1列出了本实施例超疏水涂层的粘附力等级以及剥离测试后的水接触角。本实施例所制备的有机硅/氮化硼/二氧化硅杂化超疏水涂层的粘附力达到1级,且经过横切与剥离测试后,其水接触角变化不大,仍具有超疏水性。
[0067]
实施例3
[0068]
将4ml氨水加入到16ml去离子水中并混合均匀,然后加入3g气相二氧化硅颗粒(40nm),在室温下搅拌10min后再置于超声清洗仪(fb11201,fisherbrand,美国)中分散10min,得到二氧化硅悬浮液;将3ml1h,1h,2h,2h-十七氟癸基三甲氧基硅烷加入85ml无水乙醇中并搅拌10min,得到含氟硅烷偶联剂的乙醇溶液;将二氧化硅悬浮液加入乙醇混合液中并持续搅拌24h。产物经9000rpm离心5min后,用乙醇洗涤并在50℃下真空干燥3h,得到氟化二氧化硅颗粒;
[0069]
将3g六方氮化硼粉末(40μm)加入30ml浓度为5mol/l的氢氧化钠溶液中并充分搅拌,加热至100℃反应24h。产物经2000rpm离心35min后,用去离子水洗涤并在65℃下真空干燥1h,即得羟基化氮化硼粉末;进一步地,将1ml1h,1h,2h,2h-十七氟癸基三甲氧基硅烷加入80ml无水乙醇中并搅拌下10min,加入羟基化氮化硼粉末,在搅拌条件下于室温反应6h;产物经2000r/min的转速将离心35min、乙醇洗涤,50℃真空干燥2h,即得氟化氮化硼粉末。
[0070]
将含氢硅油(含氢量1.4%)、抑制剂3-辛基-1-丁炔-3-醇和karstedt催化剂用正己烷稀释,得到0.33wt%的含氢硅油溶液、1wt%的抑制剂溶液和1wt%的karstedt催化剂溶液。接着,将1.2g乙烯基硅油(乙烯基含量0.1%)、0.2g抑制剂溶液、0.8gkarstedt催化剂溶液与0.85g含氢硅油溶液依次加入35ml正己烷中并搅拌10min;再将0.25g氟化氮化硼与0.5g氟化二氧化硅颗粒先后加入并搅拌10min,继续超声分散30min使其分散均匀,得到导热超疏水涂料;同时,用无水乙醇润洗马口铁片(25mm
×
25mm
×
0.28mm),干燥后放入等低温离子体发射仪(plasmaflecto 10,plasman technology,德国)中清洗300s。最后设置喷枪压力为0.7mpa,喷枪与基底的喷涂距离为20cm,喷枪的移动速度为2cm/s,并往复移动3次将导热超疏水涂料喷涂于马口铁片上,在70℃下固化2h使溶剂充分挥发,制得导热超疏水涂层。
[0071]
本实施例中二氧化硅与氮化硼改性前后的红外对比谱图以及涂层的扫描电镜图基本同图1、图2与图3,表明氟硅烷成功地接枝到了二氧化硅与氮化硼的表面,且涂层具备较粗糙的微观结构,这将赋予涂层优良的超疏水特性。
[0072]
为了评价所制得的涂层的超疏水性,用光学接触角测量仪(dsa100,kruss,德国)测量涂层的表面润湿性。在室温下用5μl水作为探针液进行视频捕捉,从至少三个不同的位置获得接触角数据并计算平均值。本实例所制得的有涂层的水滴静态接触角为155
°
,滚动角为9
°
,具有超疏水性能。
[0073]
为了评价超疏水涂层的导热性,利用闪光法导热系数仪(lfa 447 nanoflash,netzsch,德国)测量涂层的面内热扩散系数。由表1可知,本实施例所制备的超疏水涂层的导热性优良,其面内热扩散系数为1.0w/(m
·
k)。
[0074]
为了评价超疏水涂层的粘附性,根据iso2409-2013标准,对本实施例制备的涂层进行横切与剥离试验。具体地,利用刀片在涂层表面划刻“#”型方格,每道划痕间距2cm;接着将压敏胶带贴附在涂层表面,并用50g的砝码按压5s;之后将胶带揭下,观察涂层的剥离受损情况;根据剥落面积将涂层的粘附性定义为0-5级,0级表明涂层有极好的粘附性,5级则表面涂层的粘附性极差。表1列出了本实施例超疏水涂层的粘附力等级以及剥离测试后的水接触角。本实施例所制备的超疏水涂层的粘附力达到1级,且经过横切与剥离测试后,其水接触角变化不大,仍具有超疏水性。
[0075]
实施例4
[0076]
将5ml氨水加入到20ml去离子水中并混合均匀,然后加入3g气相二氧化硅颗粒(30nm),在室温下搅拌10min后再置于超声清洗仪(fb11201,fisherbrand,美国)中分散10min,得到二氧化硅悬浮液;将2ml1h,1h,2h,2h-十七氟癸基三乙氧基硅烷加入80ml无水乙醇中并搅拌10min,得到含氟硅烷偶联剂的乙醇溶液;将二氧化硅悬浮液加入乙醇混合液中并持续搅拌24h。产物经8000rpm离心10min后,用乙醇洗涤并在60℃下真空干燥2h,得到氟化二氧化硅颗粒;
[0077]
将4g六方氮化硼粉末(60μm)加入40ml浓度为2mol/l的氢氧化钠溶液中并充分搅拌,加热至120℃反应22h。产物经3000rpm离心30min后,用去离子水洗涤并在65℃下真空干燥1h,即得羟基化氮化硼粉末;进一步地,将1ml1h,1h,2h,2h-十七氟癸基三乙氧基硅烷加入80ml无水乙醇中并搅拌下10min,加入羟基化氮化硼粉末,在搅拌条件下于室温反应8h;产物经3000r/min的转速将离心30min、乙醇洗涤和60℃真空干燥2h,即得氟化氮化硼粉末。
[0078]
将含氢硅油(含氢量1.55%)、抑制剂3-苯基-1-丁炔-3-醇和karstedt催化剂用四氢呋喃稀释,得到0.33wt%的含氢硅油溶液、1wt%的抑制剂溶液和1wt%的karstedt催化剂溶液。接着,将1g乙烯基硅油(乙烯基含量0.12%)、0.18g抑制剂溶液、0.75gkarstedt催化剂溶液与0.766g含氢硅油溶液依次加入30ml四氢呋喃中并搅拌10min;再将0.25g氟化氮化硼与0.5g氟化二氧化硅颗粒先后加入并搅拌10min,继续超声分散30min使其分散均匀,得到导热超疏水涂料;同时,用无水乙醇润洗马口铁片(25mm
×
25mm
×
0.28mm),干燥后放入等低温离子体发射仪(plasmaflecto 10,plasman technology,德国)中清洗300s。最后设置喷枪压力为0.6mpa,喷枪与基底的喷涂距离为15cm,喷枪的移动速度为2cm/s,并往复移动3次将导热超疏水涂料喷涂于马口铁片上,在70℃下固化2h使溶剂充分挥发,制得导热超疏水涂层。
[0079]
本实施例中二氧化硅与氮化硼改性前后的红外对比谱图以及涂层的扫描电镜图基本同图1、图2与图3,表明氟硅烷成功地接枝到了二氧化硅与氮化硼的表面,且涂层具备较粗糙的微观结构,这将赋予涂层优良的超疏水特性。
[0080]
为了评价所制得的涂层的超疏水性,用光学接触角测量仪(dsa100,kruss,德国)测量涂层的表面润湿性。在室温下用5μl水作为探针液进行视频捕捉,从至少三个不同的位置获得接触角数据并计算平均值。从表1可以看出,本实例所制得的涂层的水滴静态接触角为160
°
,滚动角为8
°
,具有超疏水性能。
[0081]
为了评价超疏水涂层的导热性,利用闪光法导热系数仪(lfa 447 nanoflash,netzsch,德国)测量涂层的面内热扩散系数。本实施例所制备的超疏水涂层的导热性优良,其面内热扩散系数为0.9w/(m
·
k)。
[0082]
为了评价超疏水涂层的粘附性,根据iso2409-2013标准,对本实施例制备的涂层进行横切与剥离试验。具体地,利用刀片在涂层表面划刻“#”型方格,每道划痕间距2cm;接着将压敏胶带贴附在涂层表面,并用50g的砝码按压5s;之后将胶带揭下,观察涂层的剥离受损情况;根据剥落面积将涂层的粘附性定义为0-5级,0级表明涂层有极好的粘附性,5级则表面涂层的粘附性极差。表1列出了本实施例超疏水涂层的粘附力等级以及剥离测试后的水接触角。本实施例所制备的超疏水涂层的粘附力达到1级,且经过横切与剥离测试后,其水接触角变化不大,仍具有超疏水性。
[0083]
表1
[0084][0085]
综上,本发明所制备的导热超疏水涂料形成的涂层接触角达到150
°
以上,滚动角小于10
°
,且热扩散系数达到1.1w/(m
·
k),并且具有良好的粘附力,经过横切与剥离测试后,其水接触角变化不大,仍具有超疏水性。
[0086]
最后所应当说明的是,以上实施例仅用以说明本发明的技术方案而非对本发明保护范围的限制,尽管参照较佳实施例对本发明作了详细说明,本领域的普通技术人员应当理解,可以对本发明的技术方案进行修改或者等同替换,而不脱离本发明技术方案的实质和范围。