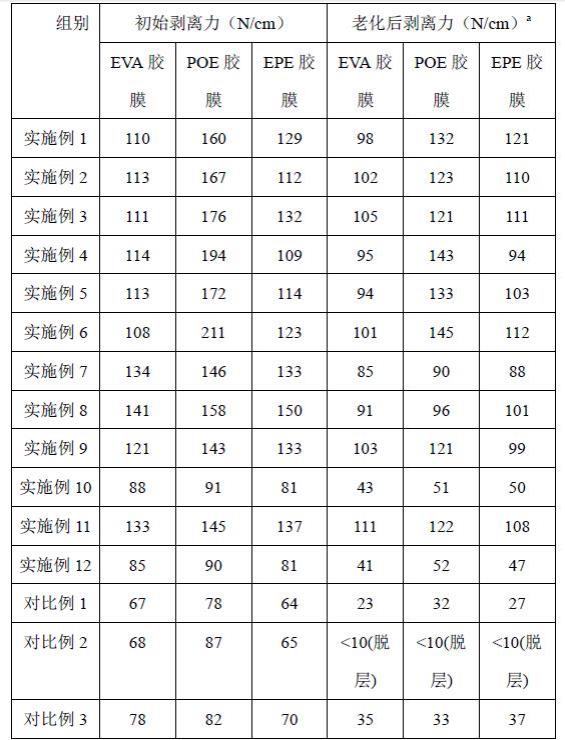
1.本发明涉及树脂技术领域,尤其涉及一种改性树脂材料及其制备方法和应用。
背景技术:2.光伏组件通常分为五层结构,自上而下分别是玻璃、胶膜、电池片、胶膜、玻璃(或背板)。如果组件上下两侧全部使用玻璃,则为双玻组件;如果上侧使用玻璃,下侧使用背板,则为单玻组件。光伏组件上的背板为多层结构的聚合物材料,该多层结构自上而下分别为涂层、基材、涂层三层结构(简称为cpc结构)或者涂层、基材、胶粘剂、聚合物膜(或基材)四层结构(简称为kpf结构或ppf结构)或者涂层、基材两层结构(简称为pc结构)。现有技术中存在的技术难题就是背板与胶膜粘接力的问题。
3.为了使背板能牢固的贴合到胶膜上,常规的解决方案是通过在背板涂层里增加聚酯树脂、环氧树脂、偶联剂等物质。然而,这些物质的添加分别有其各自的缺点,比如聚酯树脂因为分子结构中含有酯键,不耐水解,在长期的湿热老化中,容易发生化学键的断裂,而使涂层原有的力学强度下降,进而导致背板与胶膜的剥离力下降。环氧树脂最大的缺点是容易硬化黄变,时间久了,涂层内聚力增加,使背板在胶膜上的剥离力下降。而偶联剂多为小分子物质,具有很好的初粘效果,但由于容易发生迁移,会导致后期的剥离力严重下降。
4.cn112831296a公开了一种可使用于玻璃、金属粘接的胶水及其制备方法,所述胶水由主体树脂、辅助树脂、溶解介质、功能性助剂组成。该发明以羟基改性丙稀酸树脂为主体、聚酯树脂为辅,同时加入增粘树脂,结合异氰酸酯封闭型固化剂反应,所制备的胶水解决了行业现用胶水在热转工艺条件下易产生黄变的缺点,并且提升了产品的一体性、材料适用范围、初粘性、抗粘性等,在热转印行业具有潜在的应用价值。但是,该发明中的增粘树脂为达玛、松香、萜稀中的一种,制成的胶水用于光伏组件材料制备时,背板与胶膜之间的剥离力不够,且耐湿热老化性能有待进一步提高。
5.cn108192551a公开了一种透明、高粘接性的硅烷改性胶粘剂及其制备方法。该硅烷改性胶粘剂包括以下重量份的原料组分:硅烷改性聚合物100份、活性稀释剂10-30份、增塑剂20-50份、气相白炭黑5-25份、除水剂2-4份、增粘剂1-5份、稳定剂0.1-2份、催化剂0.1-2.5份;所述硅烷改性聚合物由硅烷改性聚醚a和含有烷氧基硅烷的聚丙烯酸酯类共聚物组成。该发明的硅烷改性胶粘剂透明性好且具有较高的力学强度和弹性,粘接性能稳定优异,在高温高湿等特殊粘接场合下,依然具有稳定可靠的粘接性能和优良的耐老化黄变性能。但是,该胶黏剂用于光伏组件材料制备时,背板与胶膜之间的剥离力不够,且耐湿热老化性能同样有待进一步提高。
技术实现要素:6.针对现有技术的不足,本发明的目的在于提供一种改性树脂材料及其制备方法和用途,改性树脂材料用于光伏组件制备时,解决了光伏背板在光伏胶膜上剥离力低的问题,可以显著增强背板与胶膜之间的剥离力,并且可使背板与胶膜之间的剥离力耐受长期的湿
热老化而没有下降或下降很小或有小幅提升。
7.本发明的目的之一在于提供一种改性树脂材料,为达此目的,本发明采用以下技术方案:一种改性树脂材料,按重量份计,包含如下组分:主体树脂
ꢀꢀꢀꢀꢀꢀꢀꢀꢀꢀ
10-60份增粘树脂
ꢀꢀꢀꢀꢀꢀꢀꢀꢀꢀ
0.005-3份固化剂
ꢀꢀꢀꢀꢀꢀꢀꢀꢀꢀꢀꢀ
5-20份助剂
ꢀꢀꢀꢀꢀꢀꢀꢀꢀꢀꢀꢀꢀꢀ
0-50份溶剂
ꢀꢀꢀꢀꢀꢀꢀꢀꢀꢀꢀꢀꢀꢀ
20-70份;其中,所述增粘树脂为硅烷改性聚合物。
8.本发明的改性树脂材料,通过硅烷改性聚合物的加入,作为增粘树脂,与其他组分之间配合,解决了光伏背板在光伏胶膜上剥离力低的问题,可以显著增强背板与胶膜之间的剥离力,并且可使背板与胶膜之间的剥离力耐受长期的湿热老化而没有下降或下降很小或有小幅提升。
9.具体的,一种改性树脂材料按重量份计,包含如下组分:主体树脂的重量份为10-60份,例如为10份、11份、12份、13份、14份、15份、16份、17份、18份、19份、20份、21份、22份、23份、24份、25份、26份、27份、28份、29份、30份、31份、32份、33份、34份、35份、36份、37份、38份、39份、40份、41份、42份、43份、44份、45份、46份、47份、48份、49份、50份、51份、52份、53份、54份、55份、56份、57份、58份、59份、60份等。
10.增粘树脂的重量份为0.005-3份,例如为0.005份、0.01份、0.02份、0.03份、0.04份、0.05份、0.06份、0.07份、0.08份、0.09份、0.1份、0.2份、0.3份、0.4份、0.5份、0.6份、0.7份、0.8份、0.9份、1份、1.1份、1.2份、1.3份、1.4份、1.5份、1.6份、1.7份、1.8份、1.9份、2份、2.1份、2.2份、2.3份、2.4份、2.5份、2.6份、2.7份、2.8份、2.9份、3份等。
11.固化剂的重量份为5-20份,例如为5份、6份、7份、8份、9份、10份、11份、12份、13份、14份、15份、16份、17份、18份、19份、20份等。
12.助剂的重量份为0-50份,例如为0、1份、5份、10份、15份、20份、25份、30份、35份、40份、45份或50份等。
13.溶剂的重量份为20-70份,例如为20份、25份、30份、35份、40份、45份、50份、55份、60份、65份或70份等。
14.本发明中,所述硅烷改性聚合物包含硅烷改性聚醚、硅烷改性聚烯烃、硅烷改性聚氨酯、硅烷改性聚酯中的任意一种或至少两种的混合物,包括但不限于市售品、自主合成品。
15.本发明中,所述硅烷改性聚合物的数均分子量为1000-10000,例如为1000、2000、3000、4000、5000、6000、7000、8000、9000、10000等,优选为1000-5000,更优选为2000-4000。
16.本发明中,所述硅烷改性聚合物为端基硅烷改性或侧基硅烷改性聚合物材料得到,可以为分子链的一端硅烷化改性,也可以为分子链的两端硅烷化改性。
17.所述聚合物材料由碳元素、氧元素和氢元素中的两种或三种组成。
18.所述聚合物材料包含聚乙二醇、聚丙二醇、聚四氢呋喃醚二醇、聚乙烯、聚丙烯、聚丁二烯、聚异戊二烯、聚1-丁烯、聚乙烯-1-辛烯共聚物、聚乙烯-1-丁烯共聚物、三元乙丙橡
胶、丁基橡胶、羟基封端聚丁二烯、羟基封端聚氨酯预聚体、异氰酸酯基封端的聚氨酯预聚体、聚碳酸酯二醇、聚己二酸乙二醇酯、聚己二酸丁二醇酯、聚己二酸己二醇酯、聚癸二酸乙二醇酯、聚癸二酸丁二醇酯中的任意一种或至少两种的混合物。
19.本发明中,所述硅烷改性的方法选自(1)至(7)中的任意一种;(1)直接利用聚合物材料两端的羟基或异氰酸酯基与硅烷偶联剂分子反应;(2)先对聚合物材料两端或侧链羟基化,再利用硅烷偶联剂进行硅烷化;(3)先对聚合物材料子两端或侧链环氧化,再利用硅烷偶联剂进行硅烷化;(4)先对聚合物材料两端或侧链羧基化,再利用硅烷偶联剂进行硅烷化;(5)先对聚合物材料两端或侧链氨基化,再利用硅烷偶联剂进行硅烷化;(6)先对聚合物材料两端或侧链修饰异氰酸酯基团,再利用硅烷偶联剂进行硅烷化;(7)聚合物分子链中或侧链上有双键时,利用聚合物材料分子链中的双键和硅烷偶联剂反应进行硅烷化。
20.上述硅烷改性方法,可经由一步化学反应、两步化学反应或三步化学反应完成。
21.本发明中,所述主体树脂包含丙烯酸树脂、氟碳树脂、聚氨酯树脂、聚酯树脂、环氧树脂中的任意一种或至少两种的混合物。优选为丙烯酸树脂和/或氟碳树脂。
22.本发明中,所述聚酯树脂包括分子链中重复出现酯键-coo-的聚合物树脂。
23.本发明中,所述环氧树脂包括分子链两端含有环氧基团的聚合物树脂。
24.本发明中,所述固化剂包括二官能度异氰酸酯、三官能度异氰酸酯和封闭型异氰酸酯中的任意一种或至少两种的混合物。
25.本发明中,所述溶剂包含乙酸乙酯、乙酸丁酯、丙二醇甲醚醋酸酯、n,n-二甲基甲酰胺、n,n-二甲基乙酰胺中的任意一种或至少两种的混合物。
26.本发明中,所述助剂包含无机填料、消光粉、颜料、流平剂、分散剂、耐水解剂、催化剂中的任意一种或至少两种的混合物。
27.本发明中,按助剂重量份为0-50份计,包含0-40份的无机填料、0-5份的消光粉、0-5份的颜料、0-1份的流平剂、0-1份的分散剂、0-1份的耐水解剂、0-1份的催化剂。
28.例如,无机填料的重量份为0、1份、5份、10份、15份、20份、25份、30份、35份或40份等,无机填料包含钛白粉、硫酸钡、碳酸钙、氧化铝、氢氧化铝、炭黑、白炭黑中的任意一种或至少两种的混合物。
29.消光粉的重量份为0、1份、2份、3份、4份、5份等,消光粉包含起消光作用的二氧化硅类物质。
30.颜料的重量份为0-5份,例如为0、1份、2份、3份、4份、5份等。
31.流平剂的重量份为0-1份,例如为0、0.1份、0.2份、0.3份、0.4份、0.5份、0.6份、0.7份、0.8份、0.9份或1份等。流平剂包含有机硅流平剂、含氟流平剂、丙烯酸流平剂中的任意一种或至少两种的混合物。
32.分散剂的重量份为0-1份,例如为0、0.1份、0.2份、0.3份、0.4份、0.5份、0.6份、0.7份、0.8份、0.9份或1份等,分散剂包含无机分散剂、有机分散剂、高分子类分散剂中的任意一种或至少两种的混合物。
33.耐水解剂的重量份为0-1份,例如为0、0.1份、0.2份、0.3份、0.4份、0.5份、0.6份、
0.7份、0.8份、0.9份或1份等,耐水解剂包含碳化二亚胺类、环氧类、酸酐类中的任意一种或至少两种的混合物。
34.催化剂的重量份为0-1份,例如为0、0.1份、0.2份、0.3份、0.4份、0.5份、0.6份、0.7份、0.8份、0.9份或1份等,催化剂包含锡类催化剂和/或叔胺类催化剂。
35.本发明的目的之二在于提供一种目的之一所述的改性树脂材料的制备方法,包括如下步骤:按配比将主体树脂、增粘树脂、固化剂、助剂加入溶剂中混合,得到所述改性树脂材料。
36.本发明的目的之三在于提供一种目的之一所述的改性树脂材料的应用,将所述改性树脂材料用于光伏组件中背板涂层的制备。
37.与现有技术相比,本发明的有益效果为:本发明的改性树脂材料,用于光伏组件制备时,解决了光伏背板在光伏胶膜上剥离力低的问题,可以显著增强背板与胶膜之间的剥离力,并且可使背板与胶膜之间的剥离力耐受长期的湿热老化而没有下降或下降很小或有小幅提升。具体的,改性树脂材料与eva胶膜的初始剥离力为60-200 n/cm,老化后的剥离力为40-150 n/cm;改性树脂材料与poe胶膜的初始剥离力为60-200 n/cm,老化后的剥离力为40-150 n/cm;改性树脂材料与epe胶膜的初始剥离力为60-200 n/cm,老化后的剥离力为40-150 n/cm。
具体实施方式
38.下面通过具体实施方式来进一步说明本发明的技术方案。
39.如无具体说明,本发明的各种原料均可市售购得,或根据本领域的常规方法制备得到。
40.实施例1硅烷化改性聚醚用于背板涂层里的增粘(1)硅烷化改性聚醚的合成将端羟基聚丙二醇(分子量4000)在120℃真空烘箱内除水处理2小时,然后在氮气保护下降至室温,加入3-异氰酸酯基丙基三甲氧基硅烷,微量的二月桂酸二丁基锡作为催化剂,升温至60-80℃,反应4小时,得到硅烷化改性的聚醚。
41.(2)背板涂层的制备按照以下配方调配背板涂层用的涂液:物料重量份丙烯酸树脂(常州都亚,ba2240)15钛白粉18二氧化硅粉料0.5炭黑0丙烯酸流平剂(信诺
®
we-d811cr)0.05迪高760w分散剂0.1耐水解剂hymax
®
210(朗亿新材)0.05聚酯树脂(伊斯曼,tx1001)1环氧树脂(南亚,128e)1
硅烷化改性聚醚0.5醋酸丁酯58hdi三聚体(万华化学,ht100)3.5二月桂酸二丁基锡0.02将上述涂液涂覆到电晕处理的pet(双星,288um厚度,1140mm宽度,半透)表面,在170℃烘箱内烘60s,在50℃条件下熟化60h。涂层干燥后的厚度控制在4
±
0.5μm范围内。
42.实施例2硅烷化改性聚烯烃在背板涂层里的增粘(1)硅烷化改性聚烯烃的合成将端羟基聚烯烃(羟基含量0.85mmol/g)在120℃真空烘箱内除水处理2小时,然后在氮气保护下降至室温,加入异佛尔酮二异氰酸酯及微量的二月桂酸二丁基锡作为催化剂,升温至60-80℃,反应2小时;然后将温度降低至室温,加入3-氨基丙基三甲氧基硅烷得到硅烷化改性的聚烯烃。
43.(2)背板涂层的制备按照以下配方调配背板涂层用的涂液:物料重量份丙烯酸树脂(南通方鑫化工,fx-9027)18钛白粉15二氧化硅粉料0.5炭黑0迪高流平剂4100.05byk-lpc22092分散剂0.1耐水解剂hymax
®
213(朗亿新材)0.05聚酯树脂(万青化学,dc191)1环氧树脂(南亚,128e)1硅烷化改性聚烯烃0.3醋酸丁酯58hdi三聚体(万华化学,ht100)3.5二月桂酸二丁基锡0.02将上述涂液涂覆到电晕处理的pet(恒力,290um厚,1140mm宽,半透)表面,在160℃烘箱内烘干2min,然后在50℃烘箱熟化60h。涂层干燥后的厚度控制在4
±
0.5μm范围内。
44.实施例3硅烷改性聚氨酯在背板涂层里的增粘(1)硅烷化改性聚氨酯的合成将自合成的端羟基聚氨酯(分子量5000)在120℃真空烘箱内除水处理2小时,然后在氮气保护下降至室温,加入3-异氰酸酯基丙基三甲氧基硅烷,微量的二月桂酸二丁基锡作为催化剂,升温至60-80℃,反应4小时,得到硅烷化改性的聚氨酯。
45.(2)背板涂层的制备按照以下配方调配背板涂层用的涂液:
物料重量份丙烯酸树脂(睿科化学,rkz5001)15钛白粉18二氧化硅粉料0.5碳黑0氟硅流平剂(信诺
®
we-8776cr)0.05disperbyk-184分散剂0.1抗水解稳定剂s-70000.05聚酯树脂(杜邦,lw9020nc010)1环氧树脂(南亚,128e)1硅烷化改性聚氨酯1.0醋酸丁酯58ipdi三聚体(科思创,ba4470)3.5二月桂酸二丁基锡0.02将上述涂液涂覆到电晕处理的pet(裕兴,290um厚,1140mm宽,半透)表面,在170℃烘箱内烘干1min,然后在50℃烘箱熟化60h。涂层干燥后的厚度控制在4
±
0.5μm范围内。
46.实施例4 硅烷改性聚酯在背板涂层里的增粘(1)硅烷化改性聚酯的合成将聚己二酸丁二醇酯(分子量3000)在120℃真空烘箱内除水处理2小时,然后在氮气保护下降至室温,加入异佛尔酮二异氰酸酯及微量的二月桂酸二丁基锡作为催化剂,升温至60-80℃,反应2小时;然后将温度降低至室温,加入3-氨基丙基三甲氧基硅烷得到硅烷化改性的聚酯。
47.(2)背板涂层的制备按照以下配方调配背板涂层用的涂液:物料重量份丙烯酸树脂(南通方鑫化工,fx-9066)15钛白粉18二氧化硅粉料0.5炭黑0有机硅流平剂(信诺
®
we-d511n)0.05分散剂(科宁新材料,kmt-310)0.1耐水解剂(朗亿新材,hymax
®
220)0.05聚酯树脂(巴斯夫,b4406g2)1环氧树脂(南亚,128e)1硅烷化改性聚酯0.5丙二醇甲醚醋酸酯58hdi三聚体(万华化学,ht100)3.5二月桂酸二丁基锡0.02将上述涂液涂覆到电晕处理的pet(裕兴,290um厚,1140mm宽,半透)表面,在170℃
烘箱内烘干1min,然后在50℃烘箱熟化60h。涂层干燥后的厚度控制在4
±
0.5μm范围内。
48.实施例5 商用硅烷改性聚醚在背板涂层里的增粘(1)硅烷化改性聚醚(外购)硅烷化改性聚醚购自日本钟渊化学工业株式会社,牌号:s303h。
49.(2)背板涂层的制备按照以下配方调配背板涂层用的涂液:物料重量份丙烯酸树脂(常州都亚ba2240)15碳酸钙18二氧化硅粉料0.5炭黑0.05氟碳流平剂(科宁新材料,kmt-1023)0.05分散剂(科宁新材料,kmt-3002)0.1耐水解剂(朗亿新材,hymax
®
1212)0.05聚酯树脂(巴斯夫b4300g3)1环氧树脂(南亚,128e)1s303h(日本钟渊化学,外购)0.8丙二醇甲醚醋酸酯58hdi三聚体(万华化学,ht100)3.5二月桂酸二丁基锡0.02将上述涂液涂覆到电晕处理的pet(裕兴,290um厚,1140mm宽,半透)表面,在170℃烘箱内烘干1min,然后在50℃烘箱熟化60h。涂层干燥后的厚度控制在4
±
0.5μm范围内。
50.实施例6 商用硅烷改性聚烯烃在背板涂层里的增粘(1)硅烷化改性聚烯烃(外购)硅烷化改性聚烯烃购自赢创特种化学(上海)有限公司,牌号:vestoplast 206。
51.(2)背板涂层的制备按照以下配方调配背板涂层用的涂液:物料重量比丙烯酸树脂(常州都亚ba2240)15碳酸钙18二氧化硅粉料0.5炭黑0氟碳流平剂(科宁新材料,kmt-1023)0.05分散剂(科宁新材料,kmt-3002)0.1耐水解剂(朗亿新材,hymax
®
1212)0.05聚酯树脂(巴斯夫b4300g3)1环氧树脂(南亚,128e)1vestoplast206(德国赢创,外购)0.6醋酸丁酯58
hdi三聚体(万华化学,ht100)3.5二月桂酸二丁基锡0.02将上述涂液涂覆到电晕处理的pet(裕兴,290um厚,1140mm宽,半透)表面,在170℃烘箱内烘干1min,然后在50℃烘箱熟化60h。涂层干燥后的厚度控制在4
±
0.5μm范围内。
52.实施例7 增粘树脂的量增加至2份(1)硅烷化改性聚烯烃的合成按照实施例2的方法合成硅烷化改性的聚烯烃。
53.(2)背板涂层的制备按照以下配方调配背板涂层用的涂液:物料重量份丙烯酸树脂(南通方鑫化工,fx-9027)18钛白粉15二氧化硅粉料0.5炭黑0迪高流平剂4100.05byk-lpc22092分散剂0.1耐水解剂hymax
®
213(朗亿新材)0.05聚酯树脂(万青化学,dc191)1环氧树脂(南亚,128e)1硅烷化改性聚烯烃2醋酸丁酯58hdi三聚体(万华化学,ht100)3.5二月桂酸二丁基锡0.02将上述涂液涂覆到电晕处理的pet(恒力,290um厚,1140mm宽,半透)表面,在160℃烘箱内烘干2min,然后在50℃烘箱熟化60h。涂层干燥后的厚度控制在4
±
0.5μm范围内。
54.实施例8 增粘树脂的量增加至3份(1)硅烷化改性聚醚(外购)硅烷化改性聚醚购自日本钟渊化学工业株式会社,牌号:s303h。
55.(2)背板涂层的制备按照以下配方调配背板涂层用的涂液:物料重量份丙烯酸树脂(常州都亚ba2240)15碳酸钙18二氧化硅粉料0.5炭黑0氟碳流平剂(科宁新材料,kmt-1023)0.05分散剂(科宁新材料,kmt-3002)0.1耐水解剂(朗亿新材,hymax
®
1212)0.05聚酯树脂(巴斯夫b4300g3)1
环氧树脂(南亚,128e)1s303h(日本钟渊化学,外购)3丙二醇甲醚醋酸酯58hdi三聚体(万华化学,ht100)3.5二月桂酸二丁基锡0.02将上述涂液涂覆到电晕处理的pet(裕兴,290um厚,1140mm宽,半透)表面,在170℃烘箱内烘干1min,然后在50℃烘箱熟化60h。涂层干燥后的厚度控制在4
±
0.5μm范围内。
56.实施例9 不加助剂(1)硅烷化改性聚烯烃的合成按照实施例2的方法合成硅烷化改性的聚烯烃。
57.(2)背板涂层的制备按照以下配方调配背板涂层用的涂液:物料重量份丙烯酸树脂(南通方鑫化工,fx-9027)18钛白粉15二氧化硅粉料0.5炭黑0迪高流平剂4100.05byk-lpc22092分散剂0.1耐水解剂hymax
®
213(朗亿新材)0.05聚酯树脂(万青化学,dc191)0环氧树脂(南亚,128e)0硅烷化改性聚烯烃0.3醋酸丁酯58hdi三聚体(万华化学,ht100)3.5二月桂酸二丁基锡0.02将上述涂液涂覆到电晕处理的pet(恒力,290um厚,1140mm宽,半透)表面,在160℃烘箱内烘干2min,然后在50℃烘箱熟化60h。涂层干燥后的厚度控制在4
±
0.5μm范围内。
58.实施例10将分子量增加至12000(1)硅烷化改性聚醚的合成按照实施例1的方法,将端羟基聚丙二醇(分子量12000)在120℃真空烘箱内除水处理2小时,然后在氮气保护下降至室温,加入3-异氰酸酯基丙基三甲氧基硅烷,微量的二月桂酸二丁基锡作为催化剂,升温至60-80℃,反应4小时,得到硅烷化改性的聚醚。
59.(2)背板涂层的制备按照以下配方调配背板涂层用的涂液:物料重量份丙烯酸树脂(常州都亚ba2240)15钛白粉18二氧化硅粉料0.5
炭黑0丙烯酸流平剂(信诺
®
we-d811cr)0.05迪高760w分散剂0.1耐水解剂hymax
®
210(朗亿新材)0.05聚酯树脂(伊斯曼,tx1001)1环氧树脂(南亚,128e)1硅烷化改性聚醚0.5醋酸丁酯58hdi三聚体(万华化学,ht100)3.5二月桂酸二丁基锡0.02将上述涂液涂覆到电晕处理的pet(双星,288um厚度,1140mm宽度,半透)表面,在170℃烘箱内烘60s,在50℃条件下熟化60h。涂层干燥后的厚度控制在4
±
0.5μm范围内。
60.实施例11将丙烯酸树脂换成氟碳树脂(1)硅烷化改性聚烯烃的合成按照实施例2的方法合成硅烷改性聚烯烃。
61.(2)背板涂层的制备按照以下配方调配背板涂层用的涂液:物料重量份氟碳树脂(长兴,eterflon-41011)18钛白粉15二氧化硅粉料0.5炭黑0迪高流平剂4100.05byk-lpc22092分散剂0.1耐水解剂hymax
®
213(朗亿新材)0.05聚酯树脂(万青化学,dc191)1环氧树脂(南亚,128e)1硅烷化改性聚烯烃0.3醋酸丁酯58hdi三聚体(万华化学,ht100)3.5二月桂酸二丁基锡0.02将上述涂液涂覆到电晕处理的pet(恒力,290um厚,1140mm宽,半透)表面,在160℃烘箱内烘干2min,然后在50℃烘箱熟化60h。涂层干燥后的厚度控制在4
±
0.5μm范围内。
62.(3)剥离力测试按照国标gb/t2790-1995测试背板涂层分别与eva胶膜、poe胶膜、epe胶膜之间的剥离力及dh85 2000h后的剥离力。
63.实施例12 低分子量硅烷改性聚醚在背板里的情况(1)硅烷化改性聚醚的合成按照实施例1的方法,将端羟基聚丙二醇(分子量650)在120℃真空烘箱内除水处
理2小时,然后在氮气保护下降至室温,加入3-异氰酸酯基丙基三甲氧基硅烷,微量的二月桂酸二丁基锡作为催化剂,升温至60-80℃,反应4小时,得到硅烷化改性的聚醚。
64.(2)背板涂层的制备按照以下配方调配背板涂层用的涂液:物料重量份丙烯酸树脂(常州都亚ba2240)15钛白粉18二氧化硅粉料0.5炭黑0丙烯酸流平剂(信诺
®
we-d811cr)0.05迪高760w分散剂0.1耐水解剂hymax
®
210(朗亿新材)0.05聚酯树脂(伊斯曼,tx1001)1环氧树脂(南亚,128e)1硅烷化改性聚醚0.5醋酸丁酯58hdi三聚体(万华化学,ht100)3.5二月桂酸二丁基锡0.02将上述涂液涂覆到电晕处理的pet(双星,288um厚度,1140mm宽度,半透)表面,在170℃烘箱内烘60s,在50℃条件下熟化60h。涂层干燥后的厚度控制在4
±
0.5μm范围内。
65.对比例1 不使用硅烷改性聚合物在背板里的情况(1)硅烷化改性聚烯烃的合成将端羟基聚烯烃(羟基含量0.85mmol/g)在120℃真空烘箱内除水处理2小时,然后在氮气保护下降至室温,加入异佛尔酮二异氰酸酯及微量的二月桂酸二丁基锡作为催化剂,升温至60-80℃,反应2小时;然后将温度降低至室温,加入3-氨基丙基三甲氧基硅烷得到硅烷化改性的聚烯烃。
66.(2)背板涂层的制备按照以下配方调配背板涂层用的涂液:物料重量份丙烯酸树脂(南通方鑫化工,fx-9027)18钛白粉15二氧化硅粉料0.5炭黑0迪高流平剂4100.05byk-lpc22092分散剂0.1耐水解剂hymax
®
213(朗亿新材)0.05聚酯树脂(万青化学,dc191)1环氧树脂(南亚,128e)1硅烷化改性聚烯烃0
醋酸丁酯58hdi三聚体(万华化学,ht100)3.5二月桂酸二丁基锡0.02将上述涂液涂覆到电晕处理的pet(恒力,290um厚,1140mm宽,半透)表面,在160℃烘箱内烘干2min,然后在50℃烘箱熟化60h。涂层干燥后的厚度控制在4
±
0.5μm范围内。
67.对比例2 使用硅烷偶联剂代替硅烷改性聚合物在背板里(1)背板涂层的制备按照以下配方调配背板涂层用的涂液:物料重量份丙烯酸树脂(南通方鑫化工,fx-9027)18钛白粉15二氧化硅粉料0.5炭黑0迪高流平剂4100.05byk-lpc22092分散剂0.1耐水解剂hymax
®
213(朗亿新材)0.05聚酯树脂(万青化学,dc191)1环氧树脂(南亚,128e)1硅烷偶联剂(3-甲基丙烯酰氧基丙基三甲氧基硅烷)0.3醋酸丁酯58hdi三聚体(万华化学,ht100)3.5二月桂酸二丁基锡0.02将上述涂液涂覆到电晕处理的pet(恒力,290um厚,1140mm宽,半透)表面,在160℃烘箱内烘干2min,然后在50℃烘箱熟化60h。涂层干燥后的厚度控制在4
±
0.5μm范围内。
68.对比例3 增粘树脂的用量增加至5份(1)硅烷化改性聚烯烃的合成按照实施例2的方法,合成硅烷改性聚烯烃。
69.(2)背板涂层的制备按照以下配方调配背板涂层用的涂液:物料重量份丙烯酸树脂(南通方鑫化工,fx-9027)18钛白粉15二氧化硅粉料0.5炭黑0迪高流平剂4100.05byk-lpc22092分散剂0.1耐水解剂hymax
®
213(朗亿新材)0.05聚酯树脂(万青化学,dc191)1环氧树脂(南亚,128e)1
硅烷化改性聚烯烃5醋酸丁酯58hdi三聚体(万华化学,ht100)3.5二月桂酸二丁基锡0.02将上述涂液涂覆到电晕处理的pet(恒力,290um厚,1140mm宽,半透)表面,在160℃烘箱内烘干2min,然后在50℃烘箱熟化60h。涂层干燥后的厚度控制在4
±
0.5μm范围内。
70.剥离力测试将实施例1-12与对比例1-3制得的涂层按照国标gb/t2790-1995测试背板涂层分别与eva胶膜、poe胶膜、epe胶膜之间的剥离力及dh85 2000h后的剥离力,结果如表1所示。
71.表1 老化前后剥离力
注:a 老化条件85℃,85%湿度,2000小时。
72.由表1数据可以看出,相比对比例1,从实施例1-实施例6的实验数据可以看出,涂层中加入少量增粘树脂(硅烷改性聚合物)后,背板涂层与不同胶膜的初始剥离力均有大幅度提升,而且经过湿热老化后,背板涂层与胶膜的剥离力保持率高,几乎无衰减。
73.实施例7、8中,分别增加了增粘树脂的量至2份、3份,背板涂层与胶膜剥离力在老化前有提升,老化后一定的下降,但仍高于80n/cm。
74.对比例3,将增粘树脂的量增加至5份,增粘树脂超过一定用量后,涂层背板与胶膜在老化前后的剥离力变差,老化后,无法满足使用要求,即老化后剥离力≥40n/cm。
75.实施例9中,将同样起增粘作用的聚酯树脂和环氧树脂去除,但仍旧保留硅烷改性聚合物,背板涂层与胶膜之间老化前后的剥离力仍旧没有显著变化,说明硅烷改性聚合物在背板涂层的增粘性能上起决定性作用。
76.而在对比例2中,通过将硅烷改性聚合物用其它硅烷偶联剂取代后,背板涂层与胶膜的初始剥离力大幅度下降,而且老化后的剥离力≤10n/cm,出现脱层,无法满足使用需求。
77.在实施例10中,将硅烷改性聚合物的分子量增加至12000,及在实施例12中,将硅烷改性聚合物的分子量降低至650,背板涂层与胶膜老化前后的剥离力均有所下降,但均满足了使用需求。这说明,将硅烷改性聚合物控制在一定的范围内的必要性。
78.在实施例11中,将丙烯酸树脂,变为氟碳树脂,背板涂层与胶膜老化前后的剥离力并未显著变化,这说明该增粘树脂在不同涂层里具有普遍的增粘效果。
79.本发明通过上述实施例来说明本发明的详细工艺设备和工艺流程,但本发明并不局限于上述详细工艺设备和工艺流程,即不意味着本发明必须依赖上述详细工艺设备和工艺流程才能实施。所属技术领域的技术人员应该明了,对本发明的任何改进,对本发明产品各原料的等效替换及辅助成分的添加、具体方式的选择等,均落在本发明的保护范围和公开范围之内。
80.以上详细描述了本发明的优选实施方式,但是,本发明并不限于上述实施方式中的具体细节,在本发明的技术构思范围内,可以对本发明的技术方案进行多种简单变型,这些简单变型均属于本发明的保护范围。
81.另外需要说明的是,在上述具体实施方式中所描述的各个具体技术特征,在不矛盾的情况下,可以通过任何合适的方式进行组合,为了避免不必要的重复,本发明对各种可能的组合方式不再另行说明。
82.此外,本发明的各种不同的实施方式之间也可以进行任意组合,只要其不违背本发明的思想,其同样应当视为本发明所公开的内容。