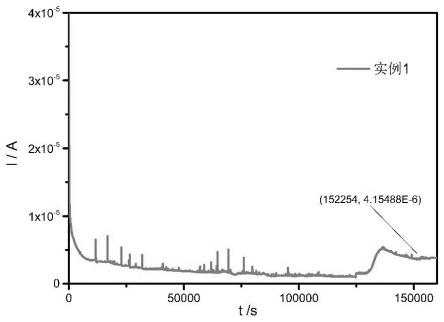
1.本发明属于管线钢表面改性技术领域,具体涉及一种输氢管道用复合抗氢渗透涂层及其制备方法。
背景技术:2.全球能源需求呈不断增长的趋势,过度使用化石燃料不仅耗尽了现有的不可再生资源,而且还造成了较为严重的环境问题。可再生能源如太阳能、风能、潮汐/波浪和核能等替代化石能源受到了一定的关注,但由于其间歇性及不可预测性,它们的实际应用依然存在着局限性。氢能作为最清洁的能源之一,以其高能量转换效率和环保特性,正成为替代不可再生能源的首选。氢能的储运是氢能产业发展中的重要环节,输氢管道的安全运行面临着严酷的挑战,其中氢脆导致的管线钢失效问题引起了广泛的关注。氢脆指的是氢进入到金属中与基体发生的交互作用,从而导致材料的力学性能受损进而产生鼓泡、开裂等现象。
3.管线钢是输氢管道的常用材料,常见的有x42、x52、x56、x70、x80等。在其表面覆盖具有延缓氢渗透作用的涂层是解决钢氢脆问题的重要手段之一。延缓氢渗透的涂层设计主要从两个方面考虑,一方面是制备孔隙率低、致密度高的涂层,阻隔氢气的进入;另一方面,制造多重氢陷阱捕获氢原子,从而降低材料中可以扩散的自由氢的浓度。
4.目前常见的抗氢渗透涂层大多为金属氧化物涂层、硅化物涂层、铝化物涂层等;制备工艺也有一定的差别,比如化学/物理气相沉积法、等离子喷涂法、溶胶凝胶法及微弧氧化法等。制备工艺及条件较为复杂、成本较高,无法满足在大规模、长距离管线钢使用的要求;另外,这类无机陶瓷涂层脆性较大,容易发生开裂,这在现实应用中存在一定的局限性。管线钢涂层的实际应用不仅应在抗氢渗透性能上考虑,还应兼顾防腐性能,这对涂层的成分和结构设计提出了更高的要求。因此,发明一种管线钢用新型复合抗氢渗透涂层对延长管线钢的使用寿命,扩大工业化应用等方面至关重要。
技术实现要素:5.针对上述已有技术存在的不足,本发明提供一种输氢管道用新型复合抗氢渗透涂层及其制备方法,该涂层制备工艺简单,成本低廉。
6.本发明是通过以下技术方案实现的。
7.一种输氢管道用复合抗氢渗透涂层,所述涂层包括:底层和设置在底层上的表面层,所述底层为二硫化钼涂层,所述表面层为改性含氟涂层。
8.进一步地,所述改性含氟涂层为经过改性的聚四氟乙烯涂层、聚偏二氟乙烯涂层、氟硅涂层中的一种或多种。
9.进一步地,所述底层中二硫化钼固含量为38%-60%。
10.进一步地,所述底层厚度为20-80μm,表面层厚度为60-150μm,复合抗氢渗透涂层总厚度为80-230μm。
11.进一步地,所述输氢管道为管线钢。
12.一种输氢管道用复合抗氢渗透涂层的制备方法,包括:(1)底层的制备:将二硫化钼粉末和分散剂混合均匀,超声混合搅拌20-60min,得到组分a;向组分a中加入粘结剂,在600-1200r/min转速下搅拌均匀后真空加热至55-80℃,保温60-300min,得到组分b;将组分b融入稀释剂中并加入固化剂,在800-1500r/min转速下搅拌均匀后得到二氧化钼涂料;在输氢管道基体表面喷涂所述二氧化钼涂料,喷涂后在160-250度保温20-90min;(2)表面层的制备:将含氟涂料采用氧化石墨烯改性,氧化石墨烯添加量为0.1%-5%,转速为800-1500r/min分散10-60min,得到改性含氟涂料;在步骤(1)制备的底层完全干燥后,在底层表面喷涂所述改性含氟涂料,最后烘烤形成稳定的表面层。
13.进一步地,所述步骤(1)二硫化钼粉末的直径为100-800nm;所述二硫化钼粉末和分散剂重量比为1:10-20,粘结剂加入量为组分a重量的30-60%,稀释剂加入量与组分b质量比为1-3:1,固化剂加入量为粘结剂重量的10-30%。
14.进一步地,所述分散剂为含0.1-5%硅烷偶联剂的丙酮或乙醇溶液中的一种,所述粘结剂为热固性聚氨酯,所述稀释剂为水,所述固化剂为异氰酸酯。
15.进一步地,所述步骤(1)在输氢管道基体表面喷涂二氧化钼涂料之前,采用从粗到细的砂纸进行打磨除去表面锈迹和氧化膜并进行除油及干燥处理。
16.进一步地,所述底层和表面层的制备过程,喷涂工艺均为将涂料装入高压无气喷涂设备,通过10-20mpa的高压进行喷涂。
17.进一步地,所述步骤(2)含氟涂料为聚四氟乙烯、聚偏二氟乙烯、氟硅中的一种或多种。
18.进一步地,所述步骤(2)表面层的制备过程中,烘烤工艺是在马弗炉中进行,温度150-300℃之间,保温20-90min后取出放置于室温。
19.本发明的有益技术效果,本发明提供的一种输氢管道用复合抗氢渗透涂层为无机和有机复合涂层,其中,二硫化钼作为新型的片层材料,具备特殊的晶体结构,具备较强的抗氢渗透性能,在500℃以下能够稳定存在不与氢气反应,具备作为新型阻氢层的潜力。
20.聚四氟乙烯涂层、聚偏二氟乙烯涂层、氟硅涂层等常用在建筑物的防护或金属的防腐领域。氧化石墨烯同样也作为二维材料,很容易与氢结合,当氢原子距离石墨烯很近时,只需要0.18ev的能量就能够形成c-h键,对氢有很强的捕获能力;同时,氧化石墨烯中的π键形成密集的电子云分布,对隧穿粒子有较强的斥力,其对氢原子的隧穿有很高的能垒。也就是说氧化石墨烯显著的增加了氢的渗透难度,延长了氢渗透的路径,可显著的提升涂层的阻氢性能;另一方面,氧化石墨烯显著提升了复合涂层的防腐性能,这在管道中的实际工况下也是必要的。
21.本发明综合了各层的优势,在氢能产业的发展过程中,可有效的延长输氢管道的使用寿命,在能源应用中可有效地解决氢渗透带来的浪费和污染,提高了管道运行的安全性。
附图说明
22.图1是实例1的电化学氢渗透曲线;图2是实例2的电化学氢渗透曲线;
图3是实例3的电化学氢渗透曲线;图4是对比例1电化学氢渗透性能测试前后sem图。
具体实施方式
23.下面结合附图和具体实施方式对本发明进行详细说明。
24.实施例1选用x80管线钢基材,尺寸30mm*30mm*1mm,表面依次用600#、800#、1000#、1200#砂纸打磨,依次在去离子水、乙醇、丙酮中超声清洗去除表面氧化膜和锈蚀,自然风干后放置备用。
25.按重量比为1:10的比例称取二硫化钼粉末和含1%硅烷偶联剂的丙酮溶液混合均匀,超声混合搅拌30min,得到组分a;加入组分a一半重量的热固性聚氨酯作为粘结剂,在1000r/min转速下搅拌均匀后真空加热至65℃,保温200min,得到组分b。将组分b融入同等质量的水中并加入粘结剂重量20%的异氰酸酯,在1500r/min转速下搅拌均匀后得到二硫化钼涂料。在x80基体表面喷涂二硫化钼涂料,喷涂后在250℃保温60min。取出冷却至室温,厚度为60μm。喷涂工艺为将二硫化钼涂料装入高压无气喷涂设备,通过10mpa的高压进行喷涂。其中,二硫化钼粉末的直径为100nm,底层中二硫化钼固含量为45%;将质量占比为1%的氧化石墨烯分散在聚偏二氟乙烯的浆料中,在1500r/min转速下搅拌30min得到改性的聚偏二氟乙烯的浆料。
26.在底层完全干燥后,喷涂改性聚偏二氟乙烯的浆料,在230℃马弗炉中烘烤30min,得到表面层厚度为100μm。其中,喷涂工艺为将改性聚偏二氟乙烯的浆料装入高压无气喷涂设备,通过10mpa的高压进行喷涂。
27.实施例2选用x80管线钢基材,尺寸30mm*30mm*1mm,表面依次用600#、800#、1000#、1200#砂纸打磨,依次在去离子水、乙醇、丙酮中超声清洗去除表面氧化膜和锈蚀,自然风干后放置备用。
28.按重量比为1:20的比例称取二硫化钼粉末和含3%硅烷偶联剂的丙酮溶液混合均匀,超声混合搅拌20min,得到组分a;加入组分a 重量40%的热固性聚氨酯作为粘结剂,在800r/min转速下搅拌均匀后真空加热至70℃,保温100min,得到组分b。将组分b按质量比为2:1融入水中并加入粘结剂重量20%的异氰酸酯,在1000r/min转速下搅拌均匀后得到二硫化钼涂料。采用喷涂的方式在x80基体表面制备,喷涂后在160度保温60min。取出冷却至室温,制备的底层厚度为70μm。喷涂工艺为将二硫化钼涂料装入高压无气喷涂设备,通过18mpa的高压进行喷涂。其中,二硫化钼粉末的直径为300nm,底层中二硫化钼固含量为52%。
29.将质量占比为0.5%的氧化石墨烯分散在聚偏二氟乙烯的浆料中,在1200r/min转速下搅拌60min得到改性的聚偏二氟乙烯的浆料。
30.在底层完全干燥后,喷涂改性聚偏二氟乙烯的浆料,在200℃马弗炉中烘烤30min,得到表面层厚度为95μm。其中,喷涂工艺为将改性聚偏二氟乙烯的浆料装入高压无气喷涂设备,通过18mpa的高压进行喷涂。
31.实施例3选用x80管线钢基材,尺寸30mm*30mm*1mm,表面依次用600#、800#、1000#、1200#砂
纸打磨,依次在去离子水、乙醇、丙酮中超声清洗去除表面氧化膜和锈蚀,自然风干后放置备用。
32.按重量比为1:10的比例称取二硫化钼粉末和含1%硅烷偶联剂的乙醇溶液混合均匀,超声混合搅拌40min,得到组分a;加入组分a重量的30%的热固性聚氨酯作为粘结剂,在1200r/min转速下搅拌均匀后真空加热至70℃,保温150min,得到组分b。将组分b按质量比为3:1融入水中并加入粘结剂重量的10%异氰酸酯,在1000r/min转速下搅拌均匀后得到二硫化钼涂料。采用喷涂的方式在x80基体表面制备,喷涂后在210度保温60min。取出冷却至室温,厚度为65μm。喷涂工艺为将二硫化钼涂料装入高压无气喷涂设备,通过15mpa的高压进行喷涂。其中,二硫化钼粉末的直径为500nm,底层中二硫化钼固含量为40%。
33.将质量占比为3%的氧化石墨烯分散在氟硅的浆料中,在950r/min转速下搅拌20min得到改性的氟硅的浆料。
34.在底层完全干燥后,喷涂改性氟硅的浆料,在150℃马弗炉中烘烤50min,得到表面层厚度为90μm。其中,喷涂工艺为将改性氟硅的浆料装入高压无气喷涂设备,通过15mpa的高压进行喷涂。
35.实施例4选用x80管线钢基材,尺寸30mm*30mm*1mm,表面依次用600#、800#、1000#、1200#砂纸打磨,依次在去离子水、乙醇、丙酮中超声清洗去除表面氧化膜和锈蚀,自然风干后放置备用。
36.按重量比为1:15的比例称取二硫化钼粉末和含1%硅烷偶联剂的乙醇溶液,将其混合均匀,超声混合搅拌60min,得到组分a;加入组分a重量60%的热固性聚氨酯作为粘结剂,在1200r/min转速下搅拌均匀后真空加热至80℃,保温200min,得到组分b。将组分b融入同等质量的水中并加入粘结剂重量的30%的异氰酸酯,在1000r/min转速下搅拌均匀后得到二硫化钼涂料。采用喷涂的方式在x80基体表面制备,喷涂后在170度保温60min。取出冷却至室温,厚度为80μm。喷涂工艺为将二硫化钼涂料装入高压无气喷涂设备,通过20mpa的高压进行喷涂。其中,二硫化钼粉末的直径为700nm,底层中二硫化钼固含量为47%。
37.将质量占比为0.1%的氧化石墨烯分散在聚四氟乙烯的浆料中,在950r/min转速下搅拌20min得到改性的聚四氟乙烯的浆料。
38.在底层完全干燥后,喷涂改性聚四氟乙烯的浆料,在170℃马弗炉中烘烤80min,得到表面层厚度为85μm。其中,喷涂工艺为将改性聚四氟乙烯的浆料装入高压无气喷涂设备,通过20mpa的高压进行喷涂。
39.对比例1采用实施例2的方法制备一种管线钢用新型复合抗氢渗透涂层,区别是不制备含氟涂层。
40.对比例2采用实施例4的方法制备一种管线钢用新型复合抗氢渗透涂层,区别是不在聚四氟乙烯的浆料中加入0.1%的氧化石墨烯。
41.对实施例1-4和对比例1-2的氢渗透评价通过电化学氢渗透方法测试, 先在无涂层一侧镀镍,电流密度为5-50ma/cm2,时间为1-20min,镀镍液采用瓦特型镀镍溶液,采用双面电解池,利用pt电极作为阳极池和阴极池的辅助电极,pt电极片有效面积1-10cm2,利用
hg/hgo作为阳极池的参比电极,阳极池中加入的电解液为0.2mol/l naoh溶液,阴极池加入的促进剂为硫脲1-3g/l;设置阳极池电压相对于参比电极为0.15-0.2v,通入氮气0.5h-1h,待背景电流稳定后向阴极池恒电流充氢,充氢电流为10-100ma/cm2。
42.氢渗透系数采用如下公式计算:式中d为表观氢渗透系数,l为测试样品厚度,t
l
为氢渗透电流it=0.63i∞的时间电化学氢渗透系数对比如表1所示。
43.表1 实施例与对比例电化学氢渗透系数对比 按照gb/t 5210—2006标准,利用数显拉开法测试仪bgd500对实施例1-4和对比例1-2进行附着力测试,利用漆膜柔韧性测试仪bgd 560柔韧性,利用漆膜冲击器bgd304抗冲击性测试。实施例中附着力均在5-10mpa之间,冲击强度为50kg.cm左右,柔韧性均在1mm。
44.采用百若plw-50 50kn氢环境电液伺服疲劳试验机进行常温下满拉伸及疲劳试验,设定应力幅值为500mpa,预充氢24h后开始测试,记录断裂时的循环周次。
45.表2 试验断裂时的循环周次以上所述的仅是本发明的较佳实施例,并不局限发明。应当指出对于本领域的普通技术人员来说,在本发明所提供的技术启示下,还可以做出其它等同改进,均可以实现本发明的目的,都应视为本发明的保护范围。