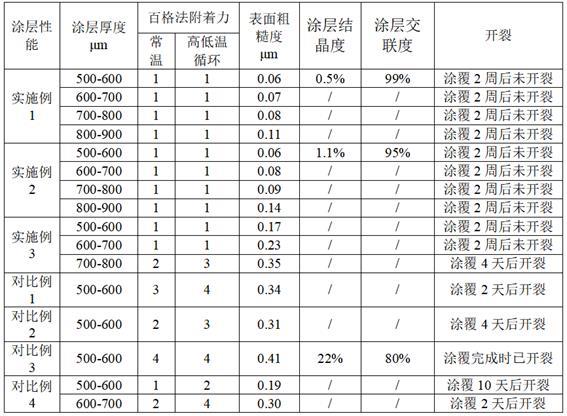
1.本发明属于聚苯硫醚复合涂层的技术领域,尤其涉及一种聚苯硫醚厚涂层及其制备方法。
背景技术:2.近年来随着轨道交通和车辆的电动化,对于许多设备防腐和抗静电性能提出了新的挑战和要求。在一些应用场景,例如长期运行温度175℃,或者是涂层要承受液体中固体颗粒的不断冲刷,氟塑料涂层往往使用效果较差。
3.聚苯硫醚简称pps,是分子主链中带有苯硫基的热塑性树脂,是热塑性高分子材料中稳定性最高的树脂之一,具有优良的绝缘性、耐温性、硬度、耐化学腐蚀性、耐磨性、尺寸稳定性、阻燃性、均衡的物理机械性能和较好的加工性能,被广泛应用于电子电器、化学工程、航空航天、汽车运输等领域。聚苯硫醚涂层具有优异的耐化学性、耐高温性,对于碳钢、铸铁、铝、铍、陶瓷、玻璃钢等的表面都有优良的粘接性能,可以作为耐高温防腐涂层,用于化工设备防腐、海洋防腐等领域,但要更好地实现上述性能,需要将聚苯硫醚涂层厚膜化。
4.但以聚苯硫醚为主成分的粉末涂料存在一个明显的缺陷,涂层固化时易发生收缩,由此产生内应力,导致涂层表面出现针孔、凹凸不平、流坠、气泡、龟裂、脱落等缺陷,从而降低涂层的防腐性能,尤其是在涂层较厚时,pps的氧化交联从表面开始逐渐向内层扩展,如果每次喷涂过厚,会造成涂层氧化交联不彻底,涂层无法完全塑化,使涂层黏结力下降,因此以上问题更为明显。
5.硕士论文(q235-a钢表面高分子聚苯硫醚及sio2复合涂层的制备与性能研究,蒋海平)选用sio2及高分子材料 pps 在q235-a 钢表面制备了pps/sio2复合涂层,以改善 q235-a 钢表面的pps 涂层的拉伸性能、冲击性能及耐磨损等力学性能,底层涂料最佳配方为:93%pps、5%sio2、2%助剂,涂层的典型固化条件为:底层:300-320℃,8-10min;中间层:340-350℃,10-l5min;面层:350-360℃,15-20min。利用上述各层涂料配方和固化条件,可以获得厚度为0.5-0.6mm 结合强度和摩擦性能优良的涂层。
6.硕士论文(氟树脂和聚苯硫醚复合涂层制备及性能研究,马长江)用聚全氟乙丙烯和聚苯硫醚树脂共混改性,以二氧化钛为填料,经磷化处理,采用流化床浸涂方法、通过多次涂覆工艺制备了厚度为0.5~0.6mm的涂层,耐热耐腐蚀涂层的主要技术指标和性能为:结合强度:18.9mpa;厚度:0.5~0.6mm;耐热性能:长期使用温度高达200℃;耐蚀性能:具有优异的耐蚀性能和耐热性能,可以耐强酸、强碱和有机溶剂的侵蚀。
7.专利(cn114702898a)本发明公开了一种金属表面耐磨耐腐蚀的聚苯硫醚涂层及其制备方法,该聚苯硫醚涂层,按重量百分比计,原料组成包括:多孔聚苯硫醚粉末45-80%;导热耐磨填料10-35%;含氟树脂10-20%;所述多孔聚苯硫醚粉末的平均孔径为600-1200nm;所述含氟树脂的d50=130-500nm,通过多次喷涂可以制备得到厚度为在300-1000μm的聚苯硫醚涂层。
8.专利(cn114845818a)本发明提供通过对基材进行一次涂装就能够形成厚度500μm
以上的皮膜的皮膜形成方法,其通过对熔点以上且250-400℃、mfr为10-100g/10min、平均粒径处于20-500μm的聚苯硫醚树脂粉体进行加热,通过对基材进行一次涂装而形成膜厚500μm以上的皮膜,所得到的皮膜的表面粗糙度ra为0.30μm以下。
9.可见,目前聚苯硫醚厚涂层只能通过多次涂覆的方式或采用特定参数的聚苯硫醚制备得到。但多次涂覆工艺繁杂,且易受多次喷涂质量和熔融流平工艺的影响,较难制备得到性能优良的涂层;而采用特定的聚苯硫醚树脂进行一次涂装,因原料受限,没有普适性。因此,需要提供一种原料限制较小、经一次涂覆即可制备得到具有良好性能的聚苯硫醚涂层的方法。
技术实现要素:10.本发明针对现有技术存在的问题,提供了一种聚苯硫醚厚涂层及其制备方法。本发明利用经氧气吸附的多孔pps粉末作为原料,采用一次涂覆即可实现0.5mm以上聚苯硫醚涂层的制备,制备工艺简单,且涂层韧性佳,不发生开裂,是一种具有大规模工业化生产前景的新型涂层材料,可用于工业防腐、换热器、绝缘轴承等领域。
11.为实现上述目的,本发明采用的技术方案如下:第一方面,本发明提供了一种聚苯硫醚厚涂层,其采用经氧气吸附的多孔pps粉末作为原料,经一次涂覆、加热熔融流平制备得到。
12.在一项优选的实施方案中,所述聚苯硫醚厚涂层厚度≥500μm,表面粗糙度ra≤0.25μm。
13.在一项优选的实施方案中,所述聚苯硫醚厚涂层厚度≥800μm,表面粗糙度ra≤0.25μm。
14.在一项优选的实施方案中,所述多孔pps粉末平均孔径为0.01-2μm,比表面积为1-300m2/g,常见的多孔pps粉末的平均孔径和比表面积满足以上要求。
15.在一项优选的实施方案中,所述多孔pps粉末平均孔径为0.01-1μm,比表面积为5-300m2/g。
16.在一项优选的实施方案中,所述经氧气吸附的多孔pps粉末通过将多孔pps粉末置于高压氧气中吸附氧气至平衡得到。
17.在一项优选的实施方案中,先对多孔pps粉末进行真空脱附,再在高压氧气中吸附氧气。
18.在一项优选的实施方案中,所述真空脱附条件为在-0.001mpa至-0.1mpa条件下脱气1-6h,所述高压氧气吸附条件为0.1-100mpa,吸附时间1-24h。
19.pps在空气中加热时发生交联,交联的结果,pps由线性结构转变为立体网状结构,规整性下降、结晶度降低,交联后的树脂强度、韧性和耐热性大大提高,改变了原来结晶pps的脆性。聚苯硫醚涂层喷涂过厚时,会造成涂层氧化交联不彻底,涂层无法完全塑化,使涂层黏结力下降,现有技术中除用加热对pps进行交联处理外,常采用加入交联促进剂、氧化剂或硫化剂对pps进行化学交联处理。由于在高温下氧气亦可起到交联剂的作用,本发明通过采用经氧气吸附的多孔pps粉末作为原料,由于多孔pps粉末吸附了足够的氧气,在加热熔融流平过程中可以有效的对聚苯硫醚树脂进行交联,降低其结晶度以及涂层固化时的收缩,从而制备得到厚度≥500μm,表面粗糙度ra≤0.25μm的聚苯硫醚厚涂层,涂层韧性佳,不
发生开裂,并且对金属的附着力佳。
20.在一项优选的实施方案中,还包括助剂,所述助剂选自无机填料、氟树脂、交联促进剂、氧化剂或硫化剂。通过以上原料,可以进一步改善聚苯硫醚涂层的固化交联效果,或降低涂层的收缩程度。
21.第二方面,本技术还提供了上述聚苯硫醚厚涂层的制备方法,包括如下步骤:1)制备经氧气吸附的多孔pps粉末:先对多孔pps粉末进行真空脱附,再将多孔pps粉末置于高压氧气中吸附氧气至平衡,将制备得到的经氧气吸附的多孔pps粉末样品保持在此氧气高压状态,备用;2)聚苯硫醚涂层制备:将金属基材或工件预热,采用步骤1)得到的经氧气吸附的多孔pps粉末,或步骤1)得到的经氧气吸附的多孔pps粉末与助剂的混合物,涂装制膜,加热熔融流平、冷却,即完成所述聚苯硫醚厚涂层的制备。
22.在一项优选的实施方案中,步骤2)中预热条件为300-400℃预热0.5-2小时,加热熔融流平条件为300-400℃加热1-3小时;步骤2)的冷却方式选自自然冷却或程序降温。
23.在一项优选的实施方案中,所述金属基材或工件选自不锈钢、铝合金、碳钢、铜、钛合金中的一种或多种。
24.在一项优选的实施方案中,步骤2)中采用静电喷涂法涂装制膜,设定压缩空气气压0.5-0.7mpa,静电喷涂电压60-80kv,电流30-45ua,喷涂距离15-25cm,静电喷涂至基材表面至全部被粉体覆盖。
25.在一项优选的实施方案中,步骤2)的冷却方式选自自然冷却或程序降温。
26.第三方面,本发明提供了上述聚苯硫醚厚涂层在耐高温防腐涂层中的应用。
27.相对于现有技术,本发明具有以下有益效果:1. 本发明利用氧气吸附的多孔pps粉末作为原料,采用一次涂覆即可实现0.5mm以上聚苯硫醚涂层的制备,制备工艺简单,是一种具有大规模工业化生产前景的新型涂层材料,可作为耐高温防腐涂层,用于工业防腐、换热器、绝缘轴承等领域。
28.2. 本发明制备的聚苯硫醚厚涂层的厚度≥500μm,表面粗糙度ra≤0.25μm,涂层韧性佳,不发生开裂,并且对金属的附着力佳。
具体实施方式
29.值得说明的是,本发明中使用的原料均为普通市售产品,对其来源不做具体限定。
30.实施例1聚苯硫醚厚涂层的制备1)制备经氧气吸附的多孔pps粉末:先对多孔pps粉末(平均孔径为0.05μm,比表面积为39.18m2/g)在-0.01mpa条件下脱气2h进行真空脱附,再将多孔pps粉末置于1.5mpa高压氧气中吸附氧气20h至平衡,将制备得到的经氧气吸附的多孔pps粉末样品保持在此氧气高压状态,备用;2)聚苯硫醚涂层:将不锈钢工件在300-400℃预热1小时,将步骤1)得到的经氧气吸附的多孔pps粉末装入静电喷涂粉罐,设定压缩空气气压0.6mpa,静电喷涂电压70kv,电流40ua,喷涂距离20cm,静电喷涂至基材表面至全部被粉体覆盖,继续340℃加热2小时,冷却至室温后,即在工件内壁形成聚苯硫醚厚涂层。分别制备500μm-600μm、600μm-700μm、700
μm-800μm、800μm-900μm的聚苯硫醚厚涂层。
31.实施例2除多孔pps粉末平均孔径为0.5μm,比表面积为11.18m2/g,高压氧气为5mpa以外,其他同实施例1。
32.实施例3除多孔pps粉末平均孔径为2μm,比表面积为4.98m2/g,高压氧气为10mpa,分别制备500-600μm、600μm-700μm、700μm-800μm的聚苯硫醚厚涂层以外,其他同实施例1。
33.对比例1除多孔pps粉末平均孔径为5μm,比表面积为0.8m2/g,制备500-600μm的聚苯硫醚厚涂层以外,其他同实施例3。
34.对比例2除多孔pps粉末平均孔径为5μm,比表面积为0.8m2/g,高压氧气为30mpa,制备500-600μm的聚苯硫醚厚涂层以外,其他同实施例3。
35.对比例3除不对多孔pps粉末进行氧气吸附处理、制备500-600μm的聚苯硫醚厚涂层以外,其他同实施例1。
36.对比例4除不对多孔pps粉末进行真空脱附处理、制备500-600μm、600μm-700μm的聚苯硫醚厚涂层以外,其他同实施例1。
37.试验例对实施例1-3、对比例1-3分别制备的涂层样品进行检测试验,结果见表1:膜厚:用st9332涂层测厚仪测定。
38.涂层附着力:包括常温附着力和高低温循环(高低温循环温度:低温-20℃,高温180℃,循环10次)后附着力,参照标准gb-t1720-1979漆膜附着力测定法测定。
39.粗糙度:使用mitutoyo公司制造的表面粗糙度测定机sj-210对涂装膜的表面粗糙度ra进行测定。
40.涂层结晶度:通过非等温结晶曲线计算得到,非等温结晶曲线由差示扫描量热法(dsc)获得,具体操作参照gbt19466-2004。
41.涂层交联度:取一定m0质量的涂层,用液氮粉碎,然后放入200℃的α-氯萘中溶解,搅拌2小时,然后趁热过滤,将滤渣取下后真空干燥除去溶剂,称重,记为m,交联度计算公式为,。
42.表1
由上表可知实施例1-3均可获得厚度≥500μm,表面粗糙度ra≤0.25μm的厚涂层,并且涂层韧性佳,不发生开裂,对金属的附着力佳。由于在高压下,材料的吸附性能主要受到材料孔径和比表面积的影响,较大比表面积和较小孔径往往对应着更高的高压气体吸附量,实施例1-2相比实施例3,以及实施例3相比对比例1-2中的多孔pps粉末孔径更小,更有利于吸附氧气,以改善聚苯硫醚涂层的固化,制备得到更厚的性能优异的涂层。并且,由对比例1-2可以看出,增大高压氧气的压强,亦有利于提高高压气体吸附量,改善固化。
43.比较实施例1和对比例3,可以看出,采用未经氧气吸附处理的多孔pps粉末,不能制备得到性能优异的聚苯硫醚厚涂层。对比实施例1和对比例4可以看出,在高压氧气吸附之前,对多孔pps粉末进行真空脱附处理有利于提高多孔pps粉末对氧气的吸附量,从而改善聚苯硫醚涂层的固化,制备得到更厚的性能优异的涂层。
44.比较实施例1-2与对比例3的结晶度和交联度,可以看出经过氧气吸附处理后可以有效降低涂层的结晶度、提高涂层交联度。
45.最后应当说明的是,以上内容仅用以说明本发明的技术方案,而非对本发明保护范围的限制,本领域的普通技术人员对本发明的技术方案进行的简单修改或者等同替换,均不脱离本发明技术方案的实质和范围。