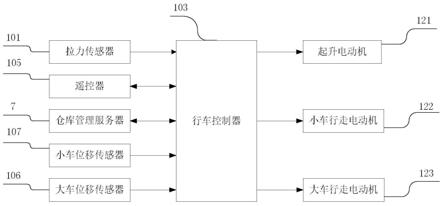
[0001]
本发明涉及一种钢板转运自动检测系统及检测方法,可用于行车起吊板材发货过程中的货物清点检测。
背景技术:[0002]
大型钢铁厂一般按照客户指定尺寸或者标准尺寸制造板材,按照同一客户定制板材或统一规格存放在一起,仓库管理系统提前统计好板材的库位、规格、数量。在板材发货时主要采用桥门式起重机(俗称行车),通过电磁吸盘起吊板材转运到运输货车上。为避免发错需清点发货板材的规格和数量,传统上采用对照发货单依靠人工比对的方法,先进技术是在行车起吊时扫描板材上的二维码进行确认。
[0003]
现有技术中采用对照发货单依靠人工比对的方法,效率低,人员在现场检查危险性大,通过简单观察容易发错货物;采用在行车起吊时扫描板材上的二维码进行确认的方法,因板材放置一定时间及转运过程碰撞容易造成二维码无法辨识,且利用电磁吸盘一次可起吊多块板材,如果大型板材在上小型板材在下不易找到二维码,造成无法扫描二维码,仍需要人工清点。
技术实现要素:[0004]
发明目的:本发明目的是提出一种钢板转运自动检测系统及检测方法,解决现有技术中板材转运检测不方便、效率低的问题。
[0005]
技术方案:一种钢板转运自动检测系统,包括:
[0006]
拉力传感器,安装在吊钩与行车连接点之间,用于测量吊钩单股钢丝绳的拉力,并将所测量的拉力发送给行车控制器;
[0007]
位移传感器组,包括用于测量起吊时大车位置的大车位移传感器,以及用于测量起吊时小车位置的小车位移传感器,并将所测量的大车、小车位置发送至行车控制器;
[0008]
行车控制器,用于根据拉力传感器测量的拉力计算当前吊运的钢材净重量,并根据位移传感器组测量的大车、小车位置确定吊钩所在库位,通过将当前吊运的钢材净重量与事先存储的仓库库位板材的各规格进行比较,计算出实际转运板材的规格及数量;
[0009]
仓库管理服务器,与行车控制器通信连接,用于向行车控制器提供仓库内板材存放的规格、重量、库位管理信息。
[0010]
进一步地,所述行车控制器包括第一获取单元,用于获取拉力传感器测得的吊钩单股钢丝绳的拉力f;
[0011]
第二获取单元,用于获取钢丝绳的倍率n和吊具重量t
0
;
[0012]
第一计算单元,用于根据下式计算当前吊运的钢材净重量:δt=f
×
n-t
0
。
[0013]
进一步地,所述行车控制器包括:第二获取单元,用于读取仓库管理服务器中预先存储的库存板材管理信息,得到吊钩所在库位将起吊板材的规格及数量;
[0014]
第二计算单元,用于根据库位将起吊板材的规格及数量进行排列组合,计算每种
组合下的起吊重量并与当前吊运的钢材净重量δt进行比较,得出最接近δt的板材规格及数量的组合,输出各个规格及对应的数量。
[0015]
基于上述钢板转运自动检测系统的检测方法,包括以下步骤:
[0016]
(1)当行车在转运人员操纵下到达指定库位时,行车通过其小车、大车位置及预先存储的仓库库位板材信息,自动判断将起吊板材的规格及数量;
[0017]
(2)在大车或小车行驶过程中,根据吊运净重量及该库位存放板材的规格及数量,自动计算当前吊运的板材规格及数量;
[0018]
(3)根据吊运净重量从当前值降为0,判断此次吊运结束,记录本次吊运的板材规格及数量,并与上次吊运板材规格及数量进行累加;
[0019]
(4)将累加的已吊运板材规格及数量与发货单对比,如果已完成发货单上的任务,则结束自动检测过程,形成出货报告,如果未完成,则重复执行上述(1)、(2)、(3)步骤。
[0020]
进一步地,所述步骤(1)中行车通过其小车、大车位置及预先存储的仓库库位板材信息,自动判断将起吊板材的规格及数量包括:
[0021]
利用大车位移传感器测量起吊时大车位置,利用小车位移传感器测量起吊时小车位置,根据所测量的大车、小车位置确定吊钩所在库位;
[0022]
从仓库管理服务器中预先存储的板材管理信息中获取吊钩所在库位将起吊板材的规格及数量。
[0023]
进一步地,所述步骤(2)中根据吊运净重量及该库位存放板材的规格及数量,自动计算当前吊运的板材规格及数量包括:
[0024]
利用安装在吊钩与行车连接点之间的拉力传感器测量吊钩单股钢丝绳的拉力f,根据下式得到当前吊运的钢材净重量:δt=f
×
n-t
0
,其中n为钢丝绳的倍率,t
0
为吊具重量;
[0025]
根据吊钩所在库位将起吊板材的规格及数量,计算不同组合下的起吊重量,并与当前吊运的钢材净重量δt进行比较,得出最接近δt的板材规格及数量的组合,即为当前吊运的板材规格及数量。
[0026]
有益效果:本发明通过在行车上增加大车位移传感器、小车位移传感器,查询出吊钩所在库位,利用仓库管理服务器提供该库位库存板材的规格及数量,通过行车上安装的拉力传感器测量起吊净重量,根据与仓库管理服务器中预先存储的各个板材的规格、重量等参数对比,自动计算当前起吊净重量下板材的数量、规格,实现板材发货转运的自动检测。仓库管理服务器是当前普遍使用的设备,本发明通过适当的应用和几个传感器、行车控制器的设置,能够在板材出库吊运过程中自动识别发货物料的规格及数量,并自动与发货单进行比对,实现自动化出货检测。且检测元件不受二维码破坏、光线不足等影响,检测效率高,不需要单独的检测人员,使用简单,易于推广。
附图说明
[0027]
图1为本发明实施例的板材转运自动检测系统结构框图;
[0028]
图2为本发明实施例的板材转运自动检测系统的控制系统示意图;
[0029]
图3为本发明实施例的板材转运自动检测方法的流程图。
具体实施方式
[0030]
下面结合附图对本发明的技术方案作进一步说明。下述实施方式中的构成要素包含本领域技术人员可置换且容易置换的构成要素、或者实质上相同的构成要素。或者能够将以下记载的构成要素适当组合。另外,在以下的实施方式的说明中,对同一构成标注同一标记,对不同的构成标注不同的标记。
[0031]
参照图1对本实施例的板材转运自动检测系统的安装结构进行说明。图1是本实施方式的板材转运自动检测系统构成示意图。图中:1,行车;2,仓库;3,运输车;4,起吊板材;5,电磁吸盘;6,吊具钢丝绳;101,拉力传感器;102,吊钩;103,行车控制器;104,司机室;105,遥控器;106,大车位移传感器;107,小车位移传感器。
[0032]
行车1架设在板材仓库1的轨道上,行车控制器103安装在司机室104内,遥控器105行车控制器103进行通信、控制行车运行。
[0033]
吊钩102通过卷扬钢丝绳与行车相连,通过吊具钢丝绳6与电磁吸盘5相连。吊具包括吊具钢丝绳、电磁吸盘、吊钩等,为行车产品以外、为起吊板材使用的辅助装置。
[0034]
起吊板材时,吊钩102起升电磁吸盘5,电磁吸盘产生磁力,吸引起吊板材4。下落板材时,吊钩102释放电磁吸盘5,板材在运输车5落地后,电磁吸盘磁力消失,释放板材。
[0035]
小车位移传感器107用于通过测量小车位移,继而确定吊钩沿行车导轨垂直方向(y轴)的位置。
[0036]
大车位移传感器106用于通过测量大车位移,继而确定吊钩沿行车导轨平行方向(x轴)的位置。
[0037]
本实施例中,小车位移传感器采用拉线传感器,传感器安装在行车司机室104附近的固定支架上,传感器引出拉线固定在与吊钩一起运动的支架上。当吊钩沿行车导轨垂直方向(y轴)运动时,传感器根据吊钩位置输出对应的电信号,根据电信号可以计算得到吊钩对应的y轴位置。例如,给定型号位移传感器0-5v的电信号对应0-100米,如果输出的电信号是2.5v,则对应的运动位置在50米。
[0038]
本实施例中,大车位移传感器采用拉线传感器,传感器安装在行车司机室104附近的固定支架上,传感器引出拉线固定在仓库行车导轨的一端。当吊钩沿行车导轨平行方向(x轴)运动时,传感器根据吊钩位置输出对应的电信号,根据电信号可以计算得到吊钩对应的x轴位置。
[0039]
本实施例中,大车位移传感器106、小车位移传感器107都采用电流型传感器,输出电流4∽20ma,大车位移传感器106测量范围0∽120m,小车位移传感器107测量范围0∽30m,传感器接入行车控制器103的模拟量输入口。
[0040]
拉力传感器101一端连接在行车固定耳板上,另一端通过钢丝绳索套与吊钩相连,在吊钩起落过程中,能够测量钢丝绳拉力。
[0041]
本实施例中,拉力传感器101采用电流型传感器,输出电流4∽20ma,测量范围0∽2500kg,传感器接入行车控制器103的模拟量输入口。
[0042]
行车控制器带有处理器、通信接口、输入输出接口及软件系统,负责检测系统的信号处理、计算、逻辑及测试结果的判定和存储。
[0043]
参照图2对本发明实施例的检测系统的控制系统进行说明。图2是根据本发明实施例的板材转运自动检测控制系统框图。
[0044]
拉力传感器101作为输入变量,连接到行车控制器103的输入端口,经过行车控制器103进行ad转换及数据处理,获知起吊重量。
[0045]
大车位移传感器106、小车位移传感器107作为输入变量,连接到行车控制器103的输入端口,经过行车控制器103进行ad转换及数据处理,形成吊钩的x轴、y轴位置。
[0046]
仓库管理服务器7通过以太网与行车控制器103相连,为行车控制器103输送发货单信息、库位信息、库位对应的板材规格及数量信息。同时,行车控制器103把板材出库的结果传送给仓库管理服务器7。
[0047]
遥控器105通过总线与行车控制器103相连,用于控制行车的运行。
[0048]
行车控制器103控制起升电动机121的正转、反转,实现吊钩的起升或下落。
[0049]
行车控制器103控制小车电动机122的正转、反转,实现吊钩的沿行车导轨垂直方向运动。
[0050]
行车控制器103控制大车电动机123的正转、反转,实现吊钩的沿行车导轨平行方向运动。
[0051]
需要说明的是,在本实施例中,遥控器105采用总线与行车控制器103相连,若采用无线通信、或者开关量连接,能够达到同样控制效果。
[0052]
下面结合图3对本发明实施例的控制策略进行说明。图3是根据本发明实施例的板材转运自动检测方法控制程序主流程图。在本实施例中,该程序主要在行车控制器103中完成。主要包括以下步骤:
[0053]
s162,行车控制器103读取大车位移传感器106、小车位移传感器107的长度检测信号,计算当前吊钩所处库位。
[0054]
s163,行车控制器103根据当前库位,从仓库管理服务器7中获得当前库位对应的板材规格及数量。
[0055]
s164,行车控制器103读取拉力传感器101的拉力值,根据钢丝绳倍率计算当前总起重量t:
[0056]
t=f
×
n
[0057]
其中,t为总起重量,f为单股钢丝绳拉力,n为钢丝绳倍率,即穿过吊钩动滑轮的钢丝绳股数。
[0058]
s165,判断当前起重量t是否大于吊具重量t
0
,如果t>t
0
,说明当前行车已经吊运板材,执行步骤s166;如果t≤t
0
,说明当前行车没有吊运板材,执行步骤s174。
[0059]
s166,判断大车或小车是否正在行走,如果大车或小车处静止状态,该t
0
可能为起吊过程量,不是本次起吊的全部重量,执行步骤s162;如果大车或小车正在行走,该t
0
为本次起吊的全部重量,执行步骤s167。
[0060]
s167,计算当前吊运的净重量δt:
[0061]
δt=t-t
0
[0062]
其中,t为总起重量,δt为本次吊运净重量,t
0
为电磁吸盘、钢丝绳、吊钩等吊具重量。当前吊运的净重量δt是在大车或小车运动中起重量相对稳定值,起升过程起重量从0∽δt及下落过程起重量从δt∽0的重量不计入净重量δt。
[0063]
s168,根据模糊算法,查询当前库位所有板材的重量以及他们的组合,与当前净重量δt相比较,如果这些重量与数量的组合与当前净重量δt相等,执行步骤s169;如果这些
重量与数量的组合与当前净重量δt不相等,系统无法自动识别,执行步骤s171。
[0064]
s169,判断对应各板材重量和数量是否为唯一值,如果这些重量与数量的组合有多种可能性,系统无法自动识别,执行步骤s171;如果这些重量与数量的组合只有一种,执行步骤s170。
[0065]
s170,记录当前各板材规格及数量,作为下一步判断的依据,执行步骤s172。
[0066]
s171,系统无法自动识别,发出警示,需要人工介入。
[0067]
s172,根据净重量是否从δt减小到0,判断是否操纵行车把板材放置到运输车上。如果净重量没有从δt减小到0,说明板材还在空中转运中,执行步骤s162;如果净重量没有从δt减小到0,说明板材已经放置到转运车上,执行步骤s173。
[0068]
s173,本次吊运统计的板材规格和数量有效,累加并存储已转运各板材规格及数量。
[0069]
s174,根据步骤s173的结果,判断与发货单对比各板材规格、数量是否完整,如果吊运完成,符合发货单,本次发货自动检测结束;如果不符合发货单对比各板材规格、数量,返回执行步骤s162。
[0070]
以上实施例仅用以说明本发明的技术方案而非对其限制,尽管参照上述实施例对本发明进行了详细的说明,所属领域的普通技术人员应当理解:依然可以对本发明的具体实施方式进行修改或者等同替换,而未脱离本发明精神和范围的任何修改或者等同替换,其均应涵盖在本发明的权利要求保护范围之内。