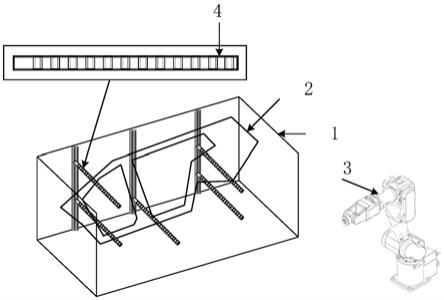
1.本发明涉及视觉检测技术应用领域,具体涉及一种适用于卡槽式料架的自动上件方法。
背景技术:2.汽车制造产业链中,白车身上用的零部件是从各个零部件供应商或主机厂自身的冲压车间制成,然后通过一些储运器具运输至焊装车间进行下一步的白车身生产制造。其中,储运器具类别中最常用的便是零件储运料架,而卡槽式料架则是最常使用的料架。卡槽式料架的核心组件为卡槽条、金属悬臂及框架,卡槽条通常由橡胶、尼龙等软性材料通过注塑制成,上面有特征形状的卡槽用以支撑并约束零件位置。零件多沿纵深方向独立侧立储放在料架中,零件装箱时需要将零件的各部分准确放置在卡槽内。目前对于卡槽式料架的上料通常是人工完成,若要实现自动化上料过程可采用1)高精度料架(精度高于
±
1mm)、高精度工位定位工装、配合机器人固定运行轨迹来实现,但是这种方法成本昂贵,且使用过程中维护检修较为困难,难以大规模推广使用;或者,还可以采用机器视觉的方式,这种方式对于料架制造精度要求不高,且能容纳使用过程中卡槽条形变带来的影响,但是在生产线上实现,存在以下难度:
3.1)料架制造精度低,使用过程中存在变形,为保证零件正确上件,需要视觉定位精度达到mm级;
4.2)不同类型料架的卡槽定位位置差异较大,需要视觉检测设备对每个卡槽条进行空间定位方能准确引导机器人进行轨迹规划,才能保证正常上料;
5.3)需要在生产线要求节拍内完成上料。
技术实现要素:6.为了解决上述技术问题,本发明提供一种适用于卡槽式料架的自动上件方法,其能利用视觉传感器定位同一卡槽式料架上多个卡槽条上的卡槽位置,实时调整机器人的运动位姿,实现自动上件。
7.为此,本发明的技术方案如下:
8.一种适用于卡槽式料架的自动上件方法,所述卡槽式料架上平行设置有多个卡槽条,每个卡槽条垂直于长度方向上设有多个尺寸相同的卡槽,不同卡槽条上由内向外相同排序的卡槽用于放置同一个工件;
9.该自动上件方法包括如下步骤:
10.1)视觉传感器分别获取各个卡槽条的图像,计算获取各个卡槽条上代表各个卡槽位置的特征点在基准坐标系下的三维坐标,记为第m个卡槽条上由内向外第i个卡槽;m取值为[1,卡槽条总数]中的自然数;i取值为[1,单个卡槽条上设有的卡槽总数]中的自然数;
[0011]
2)调用人工示教得到的相同卡槽式料架最内侧卡槽位置上件时所对应的机器人
工作位姿进行工作,获取待安装位置机器人末端在基准坐标系下的位姿;按照预定上件步骤,机器人将工件放置在最内侧卡槽上,i=1;
[0012]
3)获取所有卡槽条代表i+1位置卡槽的特征点的基准三维坐标计算和之间的旋转平移关系继而获取此位置所对应待安装位置机器人末端相对于前一待安装位置机器人末端的旋转平移关系,以此调整机器人运动轨迹,使其到达待安装位置,按照预定上件步骤,机器人将工件放置在i+1位置卡槽处;
[0013]
4)以i=i+1,判断其是否大于单个卡槽上设有的卡槽总数,若否,则重复进行步骤3);若是,则此卡槽式料架上件完成。
[0014]
进一步,步骤2)替换为:先计算新的卡槽式料架最内侧卡槽位置相较人工示教相同卡槽式料架最内侧卡槽位置的旋转平移关系,进而获取对应待安装位置机器人末端在基准坐标系下的位姿;按照预定上件步骤,机器人将工件放置在最内侧卡槽上,i=1。
[0015]
更进一步,步骤1)获取各个卡槽条图像的视觉传感器为单目视觉传感器、双目视觉传感器、结构光传感器或者多目视觉系统。
[0016]
更进一步,步骤1)计算获取各个卡槽条上代表各个卡槽位置的特征点在基准坐标系下的三维坐标时,先获取单个卡槽条上代表首、尾位置卡槽的特征点在基准坐标系下的三维坐标,再结合卡槽条加工时卡槽位置的线性关系获取代表各个卡槽位置的特征点在基准坐标系下的三维坐标。
[0017]
更进一步,步骤2)人工示教时,机器人携带零件至距放下零件位置5~20cm处停止,此位置记为待安装位置,再按照预定的上件步骤把零件放置卡槽内。
[0018]
更进一步,所述卡槽为弧形、梯形、y字形或矩形。
[0019]
更进一步,所述卡槽条为一体式注塑成型的。
[0020]
该自动上件方法结合卡槽条特征快速、准确的定位各个卡槽位置,结合同一工件上件时不同卡槽条上卡槽位置相较前一位置的旋转、平移关系推算机器人末端在待安装位置相较前一次安装的旋转、平移关系,按照预定轨迹上件,实现卡槽式料架的自动上件,能大幅度降低人工成本投入。
附图说明
[0021]
图1为本发明提供的自动上件方法实际应用环境示意图。
具体实施方式
[0022]
以下结合附图和具体实施方式对本发明的技术方案进行详细描述。
[0023]
一种适用于卡槽式料架的自动上件方法,卡槽式料架1上平行设置有多个卡槽条4,每个卡槽条4垂直于长度方向上设有多个尺寸相同的卡槽,不同卡槽条4上由内向外相同排序的卡槽用于放置同一个工件2;
[0024]
该自动上件方法包括如下步骤:
[0025]
1)视觉传感器分别获取各个卡槽条4的图像,计算获取各个卡槽条上代表各个卡槽位置的特征点在基准坐标系下的三维坐标,记为第m个卡槽条上由内向外第i个卡槽;m取值为[1,卡槽条总数]中的自然数;i取值为[1,单个卡槽上设有的卡槽总数]中的自
然数;采集图像时可以使用单目视觉传感器、双目视觉传感器、结构光传感器或者多目视觉系统;只要能按照要求获取基坐标系卡槽条及单个卡槽位置即可;基坐标系可以是机器人坐标系,也可以是基于空间中固定位置建立的坐标系;各卡槽截面可以为弧形、梯形、y字形或矩形,无需严格限制,只要通过视觉传感器能获取其位置关系,即可使用该方法;
[0026]
2)调用人工示教得到的相同卡槽式料架1最内侧卡槽位置上件时所对应的机器人工作位姿进行工作,获取待安装位置机器人末端在基准坐标系下的位姿;按照预定上件步骤,机器人将工件放置在最内侧卡槽上,i=1;
[0027]
3)获取所有卡槽条代表i+1位置卡槽的特征点的基准三维坐标计算和之间的旋转平移关系继而获取此位置所对应待安装位置机器人末端相对于前一待安装位置机器人末端的旋转平移关系,以此调整机器人3运动轨迹,使其到达待安装位置,按照预定上件步骤,机器人将工件放置在i+1位置卡槽处;
[0028]
4)以i=i+1,判断其是否大于单个卡槽上设有的卡槽总数,若否,则重复进行步骤3);若是,则此卡槽式料架上件完成。
[0029]
具体实施时,步骤1)计算获取各个卡槽条上代表各个卡槽位置的特征点在基准坐标系下的三维坐标时,先获取单个卡槽条上代表首、尾位置卡槽的特征点在基准坐标系下的三维坐标,再结合卡槽条加工时卡槽位置的线性关系获取代表各个卡槽位置的特征点在基准坐标系下的三维坐标。具体使用中,因为卡槽条多为一体式注塑成型,使用过程中形变基本同步,故而其在长期使用过程中各个卡槽位置的线性关系不变。
[0030]
为了让本方法也适用于卡槽式料架更换时位置重复精度不高的情形,步骤2)替换为:先计算新的卡槽式料架最内侧卡槽位置相较人工示教相同卡槽式料架最内侧卡槽位置的旋转平移关系,进而获取对应待安装位置机器人末端在基准坐标系下的位姿;按照预定上件步骤,机器人将工件放置在最内侧卡槽上,i=1。当然,代表各个卡槽位置的特征点在基准坐标系下的三维坐标还可以通过其他方式获得,譬如通过视觉传感器系统分别依据图像获取各个点坐标。
[0031]
具体实施时,步骤2)人工示教时,机器人携带零件至距放下零件位置5~20cm处停止,此位置记为待安装位置,再按照预定的上件步骤把零件放置卡槽内。
[0032]
该自动上件方法结合卡槽条特征快速、准确的定位各个卡槽位置,结合同一工件上件时不同卡槽条上卡槽位置相较前一位置的旋转、平移关系推算机器人末端在待安装位置相较前一次安装的旋转、平移关系,按照预定轨迹上件,实现卡槽式料架的自动上件,能大幅度降低人工成本投入。
[0033]
前面对本发明具体示例性实施方案所呈现的描述是出于说明和描述的目的。前面的描述并不想要成为毫无遗漏的,也不是想要把本发明限制为所公开的精确形式,显然,根据上述教导很多改变和变化都是可能的。选择示例性实施方案并进行描述是为了解释本发明的特定原理及其实际应用,从而使得本领域的其它技术人员能够实现并利用本发明的各种示例性实施方案及其不同选择形式和修改形式。本发明的范围旨在由所附权利要求书及其等价形式所限定。