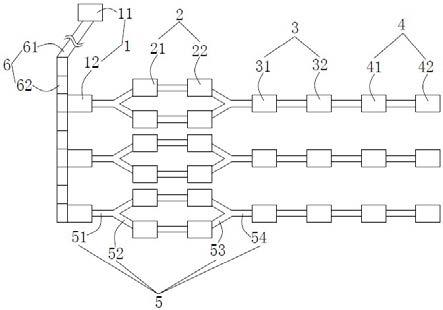
1.本发明涉及一种小剂量瓶装液体制剂的批量自动化生产线,属于制药生产设备的技术领域。
背景技术:2.小剂量的瓶装液体制剂在制备过程中,需要配制药液,并对包装的瓶体进行拆包装、洗烘灌封,将配制好的药液灌入瓶体并封口后,对其进行灭菌、光检和贴标包装。现有技术中,自动化生产线的整个生产制备过程需要多个工序的生产设备相互配合,在相邻工序之间设置用于传输瓶体的传输装置,以实现对瓶体在相邻工序之间的转运,进而完成对瓶装液体制剂的制备。在需要扩大生产规模时,则相应设置多条生产线并行生产制备。
3.但在实际生产中,由于各个工序的生产设备的加工效率各异,各个工序在固定时间内出料的物料量不同,这就导致部分工序需要停机等待在前工序的出料,使这部分工序的设备间歇运作,影响了整条生产线的生产效率。当采用多条生产线并行时,每条生产线上均配备有间歇运作的生产设备,既无益于生产效率的提高,又导致设备成本、占地面积的增加,不利于节约生产成本。同时,由于生产的是小剂量的瓶装液体制剂,这类制剂的瓶体规格小,在各个工序间输送时,极易出现倒瓶、爆瓶的现象,需要人工全程辅助扶瓶或清理爆瓶。
技术实现要素:4.本发明的目的在于克服现有技术的不足,提供一种生产效率高、倒瓶爆瓶现象少的小剂量瓶装液体制剂的批量自动化生产线。
5.本发明的目的是通过以下技术方案来实现的:一种小剂量瓶装液体制剂的批量自动化生产线,包括依次连接的瓶体上料段、洗烘灌封段、灭菌灯检段和贴标包装段,且各段之间设置有用于转运物料的传输装置,所述传输装置上设置有防倒瓶组件。
6.瓶体上料段,包括拆箱工位和多个拆包工位,所述拆箱工位和多个所述拆包工位之间连接有第一传送带,所述第一传送带上设置有多线分配组件,物料经通过第一传送带分配给多个拆包工位。
7.洗烘灌封段,包括清洗烘干工位和灌封工位,所述清洗烘干工位和灌封工位的数量一致且一一对应,所述清洗烘干工位的数量多于拆包工位的数量,所述清洗烘干工位和拆包工位之间的传输装置包括第一总线段和第一分线段,所述第一总线段与拆包工位连接,所述第一分线段与清洗烘干工位连接。
8.灭菌灯检段,包括灭菌工位和灯检工位,所述灭菌工位和灯检工位的数量一致且一一对应,所述灭菌工位的数量少于灌封工位的数量,所述灭菌工位和灌封工位之间内的传输装置包括第二分线段和第二总线段,所述第二分线段与灌封工位连接,所述第二总线段与灭菌工位连接。
9.贴标包装段,包括贴标工位和包装工位,所述贴标工位和包装工位的数量与灯检
工位一致。
10.进一步的,所述第一传送带包括输送段和分配段,所述输送段与拆箱工位连接,所述分配段与拆包工位连接,多个所述拆包工位的端部均匀分布于分配段的一侧。
11.进一步的,所述分配段由多段相对独立运行的传送段拼接组成,所述多线分配组件固定连接于分配段上,且所述多线分配组件的数量与传送段数量一致。
12.进一步的,所述多线分配组件包括固定连接于传送段边沿的滑动架,所述滑动架上开设有滑槽,所述滑槽内滑动连接有安装座,所述滑动架内开设有与滑槽连通的空腔,所述空腔内滑动连接有理线杆,所述理线杆和安装座上分别连接有驱动其移动的驱动机构,所述理线杆的移动距离始终是安装座移动距离的一半。
13.进一步的,所述防倒瓶组件包括进料防倒机构和换线防倒机构,所述进料防倒机构分布于传输装置的各段,所述换线防倒机构位于传输装置上相邻段之间或各工位与传输装置之间的衔接处。进一步的,所述进料防倒机构包括防倒链,所述防倒链由多个防倒单体串联组成,相邻的所述防倒单体之间铰接,所述防倒链上固定连接有导向件,所述导向件滑动连接于传输装置上各段的边沿。
14.进一步的,所述换线防倒机构包括第一导向带和第二导向带,所述第一导向带和第二导向带的一端均连接于传输装置的边沿,另一端沿传输装置的传输方向延伸,所述第二导向带远离传输装置边沿的一端位于第一导向带的导向范围内,所述第一导向带和第二导向带均为弹性带体。
15.进一步的,所述灌封工位包括瓶盖上料组件,所述瓶盖上料组件包括送盖管道和下料机构,所述送盖管道沿其输送方向斜向下倾斜,所述下料机构包括固定连接于送盖管道的端部的挡料件,所述送盖管道的底壁与挡料件相邻的位置开设有挂盖口,所述挡料件上开设有第一过料口和第二过料口,所述第二过料口的开口尺寸大于第一过料口,所述第二过料口位于第一过料口与挂盖口之间。
16.进一步的,所述下料机构还包括压盖板,所述压盖板固定连接于送盖管道与挡料件相邻的顶部,所述压盖板与挡料件之间留有容瓶盖通过的间隙。
17.进一步的,所述包装工位包括泡罩包装部、装盒部和装箱部,所述泡罩包装部与装盒部之间设置有泡罩板进料组件,所述泡罩板进料组件包括送料输送带、转运机构和分料平台,所述送料输送带位于泡罩包装部和分料平台之间,所述转运机构将送料输送带上的物料分两列转运至分料平台上;所述分料平台上滑动连接有分料件,所述分料平台的两侧分别设置有传料机构,两个所述传料机构上均设置有推料机构,两个所述推料机构之间设置有进料输送带,所述进料输送带上固定连接有多个分隔板,多个所述分隔板将进料输送带均匀分隔为多个进料区。
18.本发明的有益效果是:1)通过在整条生产线的不同工序段设置不同数量的加工工位,即根据各个环节加工设备的加工效率,在相应环节配备相应数量的加工设备,再将传输装置连接在不同加工工序之间,利用传输装置的分线和合线实现对所加工物料的分流和整合,以实现前后工序的加工速率的匹配,使整条生产线实现连续、稳定的加工生产,有利于提高生产效率、降低生产成本。同时,通过在传输装置上设置防倒瓶组件,能够有效减少瓶体在输送过程中,尤
其在首批瓶体进料或瓶体在传输装置的转弯、换线处所发生的倒瓶、爆瓶现象。
19.2)通过在拆箱工位与拆包工位之间的传送带上设置多线分配组件,使拆箱工位拆出的瓶包被分配至各个拆包工位,以供应各个拆包工位及后续生产线的瓶体供应。由多个拆包工位及其后续工序的相关工位形成多条并列的产线,在生产线的实际运行中,当多条并列产线中的某一工位设备出现问题或故障时,其对应的整条产线均会出现卡顿、停机的情况,导致某条产线与其他并列产线运行不同步的情况。为了适应各个拆包工位对应的产线运行情况变化,保持对各拆包工位的及时供料,本发明的第一传送带设置多段相对独立运行的传送段,并在各传送段上配备多线分配组件,通过调节多线分配组件中监测物料传输的监测位点位置,以控制相邻传送段上物料间的距离,从而实现对各拆包工位的及时补料,避免因某一条产线的卡顿而影响其他产线的瓶包上料。
20.3)通过在灌封工位处设置瓶盖上料组件,并通过设计挡料件上的过料口,使得瓶盖在上料时,仅开口朝下、能够被瓶体挂盖带走的瓶盖会被挡料件拦截,而开口方向相反的瓶盖则会从挡料件处滑落,有效避免了开口朝向相反的瓶盖卡在挡料件处形成堵塞、影响设备正常运行的情况发生,有利于提高灌封工位设备运行的稳定性,进而提高整条产线的连续运行稳定性。
21.4)通过在包装工位处设置泡罩板进料组件,将加工好的泡罩板分两条线输送,以快速实现每个进料区内放入两板泡罩板的进料,也避免了单线输送时,泡罩板在推料处因来不及推料而发生挤压变形,有利于保持泡罩板的包装完好并提高输送泡罩板的效率及包装工序的加工效率。
附图说明
22.图1为本发明生产线的运行流程图。
23.图2为本发明第一传送带上分配段的结构示意图。
24.图3为本发明第一传送带上分配段的俯视图。
25.图4为图3中的a部放大图。
26.图5为本发明多线分配组件中滑动架的内部结构示意图。
27.图6为本发明多线分配组件中滑动架的内部结构侧视图。
28.图7为本发明传输装置上设置进料防倒机构的俯视图。
29.图8为本发明传输装置上设置进料防倒机构的侧视图。
30.图9为本发明传输装置上两条相互平行传输段衔接处设置换线防倒机构的俯视图。
31.图10为本发明传输装置上两条相互垂直传输段衔接处设置换线防倒机构的俯视图。
32.图11为本发明传输装置上两条同传输段衔接处设置换线防倒机构的俯视图。
33.图12为本发明传输装置上换线防倒机构中安装架的剖视图。
34.图13为本发明灌封工位的瓶盖上料组件的结构示意图。
35.图14为图13中的b部放大图。
36.图15为本发明灌封工位的瓶盖上料组件的正视图。
37.图16为本发明灌封工位的瓶盖上料组件的侧视图。
38.图17为本发明包装工位的泡罩板进料组件的俯视图。
39.图18为本发明包装工位的泡罩板进料组件的侧视图。
40.图中,1、瓶体上料段;11、拆箱工位;12、拆包工位;2、洗烘灌封段;21、清洗烘干工位;22、灌封工位;221、送盖管道;2211、挂盖口;222、挡料件;2221、第一过料口;2222、第二过料口;2223、长挡部;2224、短挡部;2225、连接片;223、压盖板;2231、压盖部;224、瓶盖;225、瓶体;3、灭菌灯检段;31、灭菌工位;32、灯检工位;4、贴标包装段;41、贴标工位;42、包装工位;421、泡罩包装部;422、装盒部;423、装箱部;424、送料输送带;425、转运机构;426、分料平台;427、分料件;428、传料机构;4281、传料输送带;4282、限位侧板;4283、限位顶板;429、推料机构;4291、推料件;4292、挡件;430、进料输送带;4301、分隔板;4302、进料区;5、传输装置;51、第一总线段;52、第一分线段;53、第二分线段;54、第二总线段;6、第一传送带;61、输送段;62、分配段;7、多线分配组件;71、滑动架;711、滑槽;712、定位槽;72、安装座;73、理线杆;74、驱动机构;741、第一螺杆;742、第二螺杆;743、传动皮带;744、第一皮带轮;745、第二皮带轮;75、进线孔;8、进料防倒机构;81、防倒链;82、导向件;83、导向槽;84、移除机构;841、移除槽;842、推板;843、升降杆;844、驱动件;9、换线防倒机构;91、第一导向带;92、第二导向带;93、安装架;931、防滑凸起;94、安装块;95、压力传感器。
具体实施方式
41.下面将结合实施例,对本发明的技术方案进行清楚、完整地描述,显然,所描述的实施例仅仅是本发明一部分实施例,而不是全部的实施例。基于本发明中的实施例,本领域技术人员在没有付出创造性劳动的前提下所获得的所有其他实施例,都属于本发明保护的范围。
42.如图1所示,本发明提供一种技术方案:一种小剂量瓶装液体制剂的批量自动化生产线,包括依次连接的瓶体上料段1、洗烘灌封段2、灭菌灯检段3和贴标包装段4,在各段之间设置有用于转运物料的传输装置5,物料通过传输装置5在各段加工装置间传输并完成生产加工。
43.其中,本实施例的瓶体上料段1用于瓶体225的上料,即购进的瓶体225经过拆箱和拆包后沿产线输送至后续的工位。瓶体上料段1包括拆箱工位11和三个拆包工位12,拆箱工位11用于对包装有多组瓶包的瓶箱进行拆装,将多组瓶包从箱子中取出,在拆箱工位11和三拆包工位12之间连接有用于输送瓶包的第一传送带6,瓶包沿第一传送带6向多个拆包工位12输送。第一传送带6包括输送段61和分配段62,输送段61的前端与拆箱工位11连接,后端与分配段62连接,分配段62的后端则与拆包工位12连接,拆箱工位11拆出的瓶包沿输送段61
‑
分配段62输送至拆包工位12,三个拆包工位12的端部均匀分布于分配段62的一侧。
44.如图2和图3所示,为了确保瓶包在各拆包工位12处的及时进料,本实施例分配段62由九段相对独立运行的传送段拼接组成,即每段传送段有独立的驱动机构74,可控制各段传送段的运行和停止。在分配段62上固定连接有多线分配组件7,且多线分配组件7的数量与传送段数量一致,即一个多线分配组件7对应一段独立的传送段,该多线分配组件7安装于这段传送段的边沿。本实施例的多线分配组件7包括沿传送带长度方向延伸的滑动架71,该滑动架71的长度接近一段传送段的长度。在滑动架71上开设有滑槽711,滑槽711内滑动连接有安装座72(参见图4),该安装座72用于安装固定对物料输送情况进行监测的位置
传感器。这里采用的位置传感器为市售的接近式传感器,可以是电磁式、光电式、电涡流式、电容式、干簧管或霍尔式等,本实施例采用的位置传感器为漫反射光电,该位置传感器与相应传送段的驱动机构74连接,以控制该传送段的运行或停止。
45.如图5和图6所示,在滑动架71上开设有容位置传感器上连接的线束通过的进线孔75,在滑动架71内开设有与滑槽711连通的空腔,传感器上连接的线束通过该进线孔75穿入滑动架71的空腔内。在空腔内设置有用于对位置传感器上所连接的线束进行理线的理线杆73,该理线杆73滑动连接于空腔内,且空腔内设置有分别驱动理线杆73和安装座72移动的驱动机构74,该驱动机构74能够控制理线杆73的移动距离始终是安装座72移动距离的一半。本实施例采用的驱动机构74包括平行于滑槽711延伸方向的第一螺杆741和第二螺杆742,第一螺杆741用于驱动安装座72移动,第二螺杆742用于驱动理线杆73移动。其中,第一螺杆741的左端与滑动架71转动连接,右端则伸出滑动架71,在安装座72上开设有与第一螺杆741相配合的螺纹孔,这里的相配合是指第一螺杆741上的外螺纹与螺纹孔内的内螺纹相互旋合,安装座72的两侧分别与滑槽711的内侧壁抵接,即滑槽711能够限制安装座72的转动,这样当第一螺杆741转动时,安装座72沿第一螺杆741的长度方向发生移动。同样的,在理线杆73上也相应开设有与第二螺杆742相配合的螺纹孔,且在滑动件的顶部内壁开设有与第二螺杆742平行的定位槽712,通过定位槽712限制理线杆73的转动。
46.如图5和图6所示,为了控制理线杆73的移动距离始终是安装座72移动距离的一半,在第一螺杆741和第二螺杆742上分别固定连接有第一皮带轮744和第二皮带轮745,第一皮带轮744和第二皮带轮745外周套设有传动皮带743,且第二皮带轮745的周长是第一皮带轮744的两倍。这样第一皮带轮744转动两周,通过传动皮带743与之连接的第二皮带轮745相应转动一周,使第一螺杆741的转动圈数是第二螺杆742的两倍,则安装座72的移动距离也相应是理线杆73的两倍,使绕在理线杆73上的线束始终保持伸展状态。在需要对位置传感器的监测位点进行调整时,可直接转动第一螺杆741伸出滑动架71的部分,使安装座72沿滑槽711移动即可。
47.如图1所示,洗烘灌封段2包括清洗烘干工位21和灌封工位22,清洗烘干工位21和灌封工位22的数量一致且一一对应,即一个清洗烘干工位21对应一个灌封工位22,前后两个工位之间通过传输装置5连接。同时,清洗烘干工位21的数量多于拆包工位12的数量,清洗烘干工位21和拆包工位12的数量均为六个,清洗烘干工位21和拆包工位12之间的传输装置5包括第一总线段51和第一分线段52,第一总线段51与拆包工位12连接,即第一总线段51有三条,分别与三个拆包工位12连接,每个第一总线段51分出两个第一分线段52,六个第一分线段52分别与六个清洗烘干工位21连接。
48.为了减少瓶体225在传输装置5上输送期间的倒瓶现象,在传输装置5上设置有防倒瓶组件,本实施例的防倒瓶组件包括进料防倒机构8和换线防倒机构9,进料防倒机构8用于减少最先进入传输装置5的首批瓶体225的倒瓶,换线防倒机构9用于减少则用于减少瓶体225在传输装置5在分流或转弯或换线处的倒瓶。如图7和图8所示,进料防倒机构8包括防倒链81,防倒链81由多个防倒单体串联组成,本实施例的防倒单体为圆柱形,相邻的防倒单体之间通过连接片实现铰接。该进料防倒机构8分布于传输装置5的各段,即防倒链81通过放置在进瓶的传输装置5上对瓶体225进行防倒瓶,经由多个防倒单体串联成的防倒链81长度大于传输装置5的宽度,使防倒单体转动后弯曲折叠的防倒链81依然能够覆盖整个传输
装置5的宽度。
49.如图7和图8所示,为了保持防倒链81在覆盖整个传输装置5宽度的状态下稳定移动,在防倒链81上固定连接有导向件82,导向件82滑动连接于传输装置5上各段的边沿,即导向件82的一端与防倒链81固定连接,另一端滑动连接于传输装置5两侧边的防护板上设置的导向槽83内,使该导向件82沿导向槽83滑动。为了不影响物料从传输装置5到下一工位衔接处的进料,本实施例的进料防倒机构8还固定连接有用于移除防倒链81的移除槽841,该移除槽841位于各工位前端与传输装置5连接处。移除槽841能够容纳导向件82的端部在其内滑动,且移除槽841的开口小于其内部宽度,即移除槽841上方开口小于导向件82端部的宽度,使导向件82的端部在移除过程中保持在移动槽内。为了避免在移除防倒链81时将传输带上的瓶体225蹭倒,本实施例的移除槽841朝向传输带的传输方向斜向上倾斜,即向图中的右上方倾斜。在移除槽841内滑动连接有推动导向件82沿移除槽841滑动的推板842,通过推板842推动导向件82沿移除槽841向右上方滑动,将防倒链81从传输带上移除。
50.如图7和图8所示,为了方便导向件82进入移除槽841,该移除槽841的一端抵接在导向槽83的端部(移除槽841端部的开口与其内部宽度一致),使导向件82沿导向槽83滚动到端部时,直接进入移除槽841内。在移除槽841内设置有用于推动导向件82沿移除槽841滑动的推板842,该推板842位于移除槽841的下端,当导向件82进入移除槽841内时,导向件82正好位于推板842上方。推板842上连接有驱动推板842沿移除槽841向右上方滑动的结构,这里对驱动相关结构的启闭控制可通过控制系统实现,如在推板842上或推板842的下方安装压力传感器,当导向件82移动至推板842上时,通过该压力传感器向控制系统发出信号,控制系统向驱动相关结构发出启动的命令。本实施例的驱动相关结构包括沿水平方向延伸升降杆843,在升降杆843上开设有凹槽,推板842滑动连接于该凹槽内,升降杆843上连接有驱动升降杆843升降的驱动件844,该驱动件844包括沿竖直方向延伸的丝杆和驱动丝杆转动的电机,在升降杆843上开设有与丝杆相配合的螺纹孔,升降杆843通过该螺纹孔套设于丝杆上,当电机带动丝杆转动时,升降杆843沿丝杆上升或下降,推板842在升降杆843的带动下沿移除槽841滑动,推板842本身也相对升降杆843左右滑动。
51.如图9和图10所示,换线防倒机构9位于传输装置5上相邻段之间或各工位与传输装置5之间的衔接处,传输装置5上的相邻段包括传输装置5的分流或转弯或换线处。本实施例的换线防倒机构9包括第一导向带91和第二导向带92,第一导向带91和第二导向带92的前端均连接于传输装置5的边沿,后端沿传输装置5的传输方向延伸,且第二导向带92的后端位于第一导向带91的导向范围内,所述第一导向带91和第二导向带92均为弹性带体,即第一导向带91和第二导向带92均会与输送中的瓶体225相抵触,第一导向带91和第二导向带92在瓶体225的抵触下发生弹性形变同时为瓶体225提供反向的支撑,防止瓶体225在转向或偏移的过程中发生倾倒。其中,第二导向带92的弹性效果要优于第一导向带91,即第二导向带92更易发生弹性变形,这样瓶体225在输送中先与第二导向带92抵接,第二导向带92在药瓶的挤压下发生形变,向远离药瓶的传送带边沿形变和移动。由于第二导向带92的后端位于第一导向带91的导向范围内,其与第一导向带91抵触,第一导向带91也相应发生形变并产生弹力,第二导向带92可在其自身形变的回复力和第一导向带91的支持力双重作用下复又向瓶体225方向移动,即第二导向带92在瓶体225与第一导向带91之间产生抖动,从而对相邻的药瓶产生缓冲力和支持力,减少药瓶之间的间隙,也相应减少药瓶在输送中的
倒瓶现象。
52.图9为传输装置5的换线处的换线防倒机构9,即前后两段传输装置5相互平行且相对错位,使瓶体225需要沿传输方向发生一定的偏移,此处的第一导向带91和第二导向带92均朝向传输装置5中央弯曲。在第一导向带91的后方设置有压力传感器95,瓶体225在输送过程中,前端的传输装置5为运行状态,后端的传输装置5为停滞状态,当输送的瓶体225与第一导向带91抵触,使第一导向带91发生形变至与压力传感器95抵触时,该压力传感器95控制后端的传输装置5启动运行预设的时间后停止,重复上述动作,使前端传输装置5上的瓶体225逐步转移至后端的传输装置5上。图10为传输装置5的转弯处的换线防倒机构9,即前后两段传输装置5互相垂直,物料的传输方向需要改变的位置,此处的第一导向带91和第二导向带92均朝向传输装置5转角的外侧弯曲。第一导向带91的后方同样设置有压力传感器95,瓶体225在输送过程中,前后端的传输装置5均处于运行状态,当后端传输装置5连接的工位出现故障或其他情况,导致瓶体225堵塞时,堆积的瓶体225将第一导向带91压向压力传感器95,第一导向带91发生形变至与压力传感器95抵触时,该压力传感器95控制前端的传输装置5停止运行,避免瓶体225因堵塞而发生挤压爆瓶。
53.如图11和图12所示,在传输装置5与各工位的衔接处或者两段传输装置5之间的衔接处,瓶体225通过时会产生轻微晃动或震颤的位置,也可设置有换线防倒机构9。为进一步提高其对瓶体225的防倒稳定作用,此处的换线防倒机构9还包括安装架93,第二导向带92的前端滑动连接于该安装架93上,即安装架93内开设有滑槽711,第二导向带92上固定连接有安装块94,该安装块94位于该滑槽711内并可相对该滑槽711滑动,滑槽711的内壁设置有阻碍安装块94滑动的防滑凸起931,这样第二导向带92会在瓶体225的推动下沿安装架93向传输装置5的传输方向发生滑动,利用防滑凸起931对安装块94的阻碍,能够为第二导向带92进一步提供支撑,安装块94沿滑槽711的移动也能减小第二导向带92在沿传输方向上发生的形变,进而促进第二导向带92为瓶体225提供更稳定的支撑和缓冲作用。
54.如图13和图14所示,本实施例的灌封工位22包括瓶盖224上料组件,该瓶盖224上料组件包括送盖管道221和下料机构,送盖管道221沿其输送方向斜向下倾斜,下料机构包括固定连接于送盖管道221的端部的挡料件222,送盖管道221的底壁与挡料件222相邻的位置开设有挂盖口2211,瓶体225移动至挂盖口2211处时,将斜向下倾斜的瓶盖224挂在瓶体225的瓶口处并带走。
55.如图15和图16所示,为了避免有个别瓶盖224的朝向不一致、无法被瓶体225带走而卡料的情况出现,在挡料件222上开设有第一过料口2221和第二过料口2222,第二过料口2222的开口尺寸大于第一过料口2221,使得瓶盖224上料时,第一过料口2221的宽度大于瓶盖224开口侧的较小直径且小于瓶盖224顶部的台阶部直径,第二过料口2222的宽度大于瓶盖224顶部一侧的台阶部的直径,且第二过料口2222位于第一过料口2221与挂盖口2211之间。这样正常上料的瓶盖224(台阶部在上,开口朝下)的台阶部会抵在第一过料口2221处被拦截,而不同向的瓶盖224(台阶部在下、开口部在上)则会直接通过挡料件222的过料口下落,避免了不同向的瓶盖224卡在挡料件222处无法下落也无法被瓶体225带走的情况发生。本实施例的挡料件222由两个l型挡片组成,l型挡片顶端外侧固定连接有连接片2225,用于将l型挡片固定连接在送盖管道221的两侧,由两个l型挡片的长挡部2223之间形成第一过料口2221,两个l型挡片的短挡部2224之间形成第二过料口2222。
56.如图15和图16所示,下料机构还包括压盖板223,压盖板223固定连接于送盖管道221下端的顶部,即压盖板223的本体平行于送盖管道221的延伸方向,压盖板223的端部倾斜形成沿水平方向延伸的压盖部2231,在压盖板223与挡料件222之间留有容瓶盖224通过的间隙,使瓶盖224能够被瓶体225从此间隙处带走。
57.如图1所示,灭菌灯检段3包括灭菌工位31和灯检工位32,灭菌工位31和灯检工位32的数量一致且一一对应,即一个灭菌工位31对应一个灯检工位32,灭菌工位31的数量少于灌封工位22的数量,灭菌工位31和灌封工位22的数量均为三个,灭菌工位31和灌封工位22之间内的传输装置5包括第二分线段53和第二总线段54,第二分线段53与灌封工位22连接,即第二分线段53有六条,分别与六个灌封工位22连接,每两个第二分线段53合为一个第二总线段54,三个第二总线段54分别与三个灭菌工位31连接。
58.如图1所示,贴标包装段4包括贴标工位41和包装工位42,贴标工位41和包装工位42的数量与灯检工位32一致,即贴标工位41和包装工位42的数量均为三个,两者及贴标工位41与灯检工位32之间通过传输装置5连接。本实施例的包装工位42包括泡罩包装部421、装盒部422和装箱部423,当所生产产品每盒中需要包装两板或两板以上的泡罩板时,由泡罩包装部421向装盒部422输送泡罩板的速率就需要减慢,否则易造成泡罩板在推料处因来不及进料而发生挤压变形,影响产品外观。为提高生产效率、确保产品质量,本实施例的泡罩包装部421与装盒部422之间设置有泡罩板进料组件。
59.如图17和图18所示,泡罩板进料组件包括送料输送带424、转运机构425和分料平台426,送料输送带424连接于泡罩包装部421和分料平台426之间,转运机构425将送料输送带424上的物料分两列转运至分料平台426上。本实施例的转运组件为带有两列吸料盘转运板,吸料盘固定连接于转运板的下方,且个吸料盘均连接有气路管道(图中未示出)。当物料呈两列沿送料输送带424传输时,可直接利用转运板上的吸料盘从送料输送带424上吸料转运至分料平台426上。当物料呈多列沿送料输送带424传输时,可待转运板从送料输送带424上吸走两排物料后,将转运板在向分料平台426移动的过程中转动90
°
,将两排物料转为两列放置在分料平台426上。在转运平台上连接有驱动其升降、转动和移动的相关机构,此为现有技术,在此不作赘述。
60.如图17和图18所示,分料平台426上滑动连接有分料件427,本实施例的分料件427包括两个推件,两个推件由分料平台426的中央向两侧边作往复运动。本实施例的推件为推杆结构,在两个推件的端部固定连接有连接件,通过连接件使设置于分料平台426下方的驱动气缸带动推件在分料平台426上作往复运动。在分料平台426的两侧分别设置有传料机构428,两个推件将分料平台426上的物料分别推向分料平台426的两侧,使分料平台426上的物料分别进入两个传料机构428内。本实施例的传料机构428包括传料输送带4281,利用传料输送带4281对推到传料组件上的物料进行输送,为提高输送的稳定性,在传料输送带4281上设置有限位侧板4282和限位顶板4283,由两个限位侧板4282和限位顶板4283之间形成输送物料的传料通道,且靠近分料平台426的限位侧板4282在与分料平台426相邻的位置开设有传料口,使物料通过传料口被推入传料通道内。
61.如图17和图18所示,在两个传料机构428上均设置有推料机构429,两个推料机构429之间设置有进料输送带430,在进料输送带430上固定连接有多个分隔板4301,多个分隔板4301将进料输送带430均匀分隔为多个进料区4302,推料机构429用于将传料机构428上
输送的物料推入进料输送带430上的进料内。本实施例的推料机构429包括推料件4291和挡件4292,其中,挡件4292位于传料组件上的传料通道的延伸方向上,用于将传输的物料拦截下,推料件4291则位于限位挡件4292和挡料件222之间,即物料移动至限位挡件4292的端部被拦截时,由推料件4291将被拦截的物料推向进料输送带430。为了避免两个传料机构428上的物料在推料件4291的推动下同时向进料输送带430移动而发生碰撞,两个推料件4291交错设置于两个传料机构428上,即两个推料件4291对应进料输送带430上的不同进料区4302。由两个传料组件上各推一个泡罩板进入进料区4302内,使一个进料区4302内放置两盒泡罩板,以提高泡罩板的进料速度、减少泡罩板在输送中的挤压变形。
62.本实施例在使用时,工作人员只需将购入的整箱瓶体225运送至拆箱工位11处,将配制好的药液输送至灌封工位22处即可,拆箱工位11对整箱瓶体225进行分拆,将箱体内的瓶包取出并沿第一传送带6向拆包工位12输送。瓶包经过第一传送带6的输送段61移动分配段62上,分配段62上均匀分布有三个拆包工位12的进料位点。分配段62上多线分配组件7对瓶包的输送进行控制,保持每段传段带上有一个瓶包,当该段传送段上的位置传感器检测到有瓶包输送至该检测位点时,发出信号使该段传送段停止,直至其相邻的下一传送段上瓶包被输送走,则该段传送段启动将其上的瓶包传送至下一传送段上的检测位点处,以实现对各个拆包工位12的及时上料。当某条产线运行情况发生变化时,可转动相应传送段的第一螺杆741,调整检测位点的位置以改变相邻瓶包之间的距离。同时,用于检测的位置传感器发生移动时,滑动架71内的理线杆73也相应发生滑动,使该位置传感器上连接的线束保持伸展状态,避免束线因不规则卷缩而发生强力牵拉的意外情况,有利于提高设备运行的稳定性。
63.瓶包经过拆包工位12加工后成为一个个的瓶体225沿传输装置5输送,经过第一总线段51和第一分线段52后,由三线输送分流为六线输送,被输送至清洗烘干工位21,对瓶体225进行清洗烘干后继续沿传输装置5运输至灌封工位22处,配置好的药液被灌入瓶体225内,然后盖上瓶盖224封口。用于对瓶体225封口的瓶盖224沿送盖管道221输送至其末端的下料机构处,正常瓶盖224(台阶部在上、开口朝下)沿送盖管道221输送至挡料件222处被拦截,当瓶体225移动至瓶盖224下方时,瓶体225的瓶口通过挂盖口2211卡入瓶盖224内(参见图13),通过瓶体225将瓶盖224略微向上推抵,使瓶盖224挂在瓶口上且瓶盖224的台阶部从挡料件222与压料板之间的间隙通过,然后经过压盖板223的压盖后向轧盖装置传输,完成瓶盖224的上料。当有开口朝上、台阶部在下的瓶盖224输送到下料机构处时,该瓶盖224会直接从挡料件222处滑落,不会造成卡料,后续的正常瓶盖224则继续下滑至挡料件222处,等待瓶体225经过戴盖。
64.瓶体225与瓶盖224封装后沿传输装置5输送,经过第二分线段53和第二总线段54后,由六线输送合为三线输送,被输送至灭菌工位31,对封装好的瓶装药液进行灭菌,灭菌完成后输送至灯检工位32进行检验。通过检验的产品则继续由贴标工位41贴标后继续沿传输装置5向包装工位42输送,瓶装药液经泡罩包装部421包装后形成泡罩板,泡罩板呈四列沿送料输送带424向分料平台426的方向移动,泡罩板移动至送料输送带424的端部时,转运板下降,将两排泡罩板用吸料盘吸住后上升,然后转运板向分料平台426移动,移动过程中转动90
°
,使两排泡罩板转为两列放置在分料平台426上。分料平台426上的推件位于分料平台426的中央,转运板将泡罩板放置在分料平台426上两个推件的两侧,然后两个推件分别
向分料平台426的两侧推泡罩板,将泡罩板推至传料输送带4281上,传料输送带4281将泡罩板沿传料通道输送至挡料件222处,由推料件4291将泡罩板推入进料输送带430的进料区4302内。然后每个进料区4302的两板泡罩板被装入一个药盒内,药盒在经过装箱部423的装箱后得到成品。在上述各段传输装置5上均由进料防倒机构8和换线防倒机构9对瓶体225进行防倒支撑,有效减少瓶体225在输送过程中,尤其在首批瓶体225进料或瓶体225在传输装置5的转弯、换线处所发生的倒瓶、爆瓶现象,快速、高效地完成小剂量瓶装液体的自动化生产。
65.以上所述仅是本发明的优选实施方式,应当理解本发明并非局限于本文所披露的形式,不应看作是对其他实施例的排除,而可用于各种其他组合、修改和环境,并能够在本文所述构想范围内,通过上述教导或相关领域的技术或知识进行改动。而本领域人员所进行的改动和变化不脱离本发明的精神和范围,则都应在本发明所附权利要求的保护范围内。