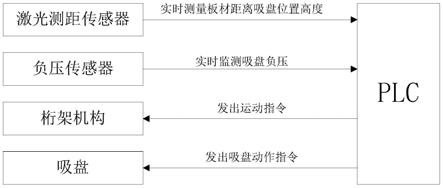
1.本发明涉及自动控制系统的控制方法,更具体地说是一种板材上料控制方法,能够广泛地应用于机械加工行业,实现平板的上料的自动控制。
背景技术:2.在数控、冲压等加工生产过程中,机床上下料工作重复性很高,其虽然简单,但由于繁复乏味而使得很多操作工人不再愿意从事这类工作。因此,实现工件上下料的自动控制技术越来越得到关注,相关技术的应用也越来越广。
3.数控机床、工业机器人机械手以及各类机电一体化设备的配合应用更加速了数控加工领域的发展。为提高上下料的稳定性,可以将自动化解决方案导入机床上下料的设备中,利用工业机器人搭配多款自动化产品形成专业的机床上下料方案,以便精确完成上下料与残屑清理,提高生产的自动化程度、提高作业灵活度和效率,但是,相关技术和设备成本高,无法得到普遍应用。同时,在不同的应用场合中,由于堆叠产品高度不同、厚度不同,传统的固定模式的上下料机构并不能满足其上下料的实际需求。现代工业应用中小批量、多品种的要求比较越来越多,因此,迫切需要一种简易、经济,针对不同厚度和不同高度产品具有较强的自适应能力的上料机构控制系统。
技术实现要素:4.本发明是为避免上述现有技术所存在的不足,提供一种板材上料自适应控制方法,以其简易和经济的形式,针对不同厚度和不同高度产品较强的自适应能力满足上料自动控制的需求。
5.本发明为实现发明目的采用如下技术方案:
6.本发明板材上料自适应方法,其特征是:
7.所述板材上料是采用吸盘通过负压吸附的形式进行板材取料和转运;
8.设置自适应控制系统包括:激光测距传感器、负压传感器、plc控制器,以及带动吸盘升降和水平转运的运动执行机构;
9.所述激光测距传感器用于实时检测吸盘距板材上表面的高度值,获得高度检测信号;
10.所述负压传感器用于实时监测吸盘负压,获得负压检测信号;
11.所述plc控制器根据所述高度检测信号和负压检测信号控制运动执行机构执行相应的动作,实现板材上料的自适应控制。
12.本发明板材上料自适应控制方法,其特征是:
13.所述运动执行机构由伺服电机进行驱动。
14.本发明板材上料自适应控制方法,其特征是:
15.设定三个高度值,分别是初始高度h2、第一高度h和第二高度h1,并且:h2>h>h1;
16.设定两个下降阶段,分别是以第一速度v1控制吸盘下降的第一下降阶段和以第二
速度v2控制吸盘下降的第二下降阶段,并且:v1>v2;
17.所述初始高度h2是指:在运动执行机构开始下降之间,吸盘距板材上表面的高度;
18.所述第一高度h是指:在由运动执行机构带动吸盘下降的过程中,当吸盘下降到吸盘距板材上表面的高度为第一高度h时,启动吸盘开始负压工作;
19.所述第二高度h1是指:在由运动执行机构带动吸盘下降的过程中,当吸盘下降到吸盘距板材上表面的高度为第二高度h1时,停止运动执行机构带动吸盘继续下降的动作;
20.所述第一速度v1是指:在由运动执行机构带动吸盘下降的过程中,当吸盘处在初始高度h2和第一高度h之间时,运动执行机构以第一速度v1带动吸盘下降,为第一下降阶段;
21.所述第二速度v2是指:在由运动执行机构带动吸盘下降的过程中,当吸盘处在第一高度h和第二高度h1的阶段中,运动执行机构以第二速度v2带动吸盘下降,为第二下降阶段。
22.本发明板材上料自适应控制方法,其特征是:
23.根据设定的三个高度值和两个下降阶段按如下步骤进行控制:
24.步骤1、将安装在运动执行机构下端的吸盘设置在初始高度h2上,由所述运动执行机构带动吸盘沿桁架横梁横移到上料工位上方;
25.步骤2、进入第一下降阶段,由plc控制器控制运动执行机构带动吸盘按第一速度v1下降,直至由激光测距传感器检测获得吸盘距板材上表面的高度为第一高度h,完成第一下降阶段;
26.步骤3、进入第二下降阶段,由plc控制器控制运动执行机构带动吸盘按第二速度v2继续下降,直至由激光测距传感器检测获得吸盘距板材上表面的高度为第二高度h1,由plc控制器控制运动执行机构停止下行,完成第二下降阶段;
27.步骤4、由负压传感器检测获得负压检测信号不低于设定压力值时,判断吸盘取料成功,随及由plc控制器控制运动执行机构带动吸盘连同板材上升,并通过水平转运到达后续指定工位,实现板材上料;
28.步骤5、返回步骤1执行下一板材上料的自适应控制,上料工位上的板材托盘无需升高。
29.与已有技术相比,本发明有益效果体现在:
30.1、本发明以抓取工件上表面为参考面,通过将激光测距以及负压监测实时获得板材上表面与吸盘的距离,从而控制吸盘工作吸取板材件,不需要设置上料工位板材托盘的升降功能,大大简化了上料工作的结构设置,有效克服了现有技术中因板材厚度不一、堆叠高度不同的问题,以其自适应能力满足了不同场合中板材上料自动控制的需求。
31.2、本发明以不同的速度完成两个不同的下降过程控制,在快速下降的同时,避免吸盘与板材之间发生撞击,保证系统工作稳定可靠。
32.3、本发明通过负压监测反馈吸取动作是否完成,从而进行后续提料送料工作,以此形成闭环控制,大大提高了系统工作效率,减少人工投入,降低人工成本,增强对生产系统的管理与控制。
33.4、本发明对工件要求宽松,能够适应多种厚度工件,适应不同料堆厚度。
34.5、本发明结构简单,控制便捷,精度高,能够适用于不同环境中板材上下料情形。
附图说明
35.图1为本发明方法中所设置的控制系统框图;
36.图2为本发明方法应用于材料上料中上料工位示意;
37.图中标号:1桁架机构,2运动执行机构,3吸盘,4激光测距传感器,5堆叠板材。
具体实施方式
38.本实施例中板材上料是采用吸盘通过负压吸附的形式进行板材取料和转运。
39.参见图1和图2,为实现自适应控制,设置自适应控制系统包括:激光测距传感器4、负压传感器、plc控制器,以及带动吸盘升降和水平转运的运动执行机构2,运动执行机构2设置在桁架机构1上,由伺服电机进行驱动。
40.激光测距传感器4用于实时检测吸盘3距堆叠板材5的板材上表面的高度值,获得高度检测信号;
41.负压传感器针对吸盘3的负压腔进行设置,用于实时监测吸盘负压,获得负压检测信号;
42.plc控制器根据高度检测信号和负压检测信号控制运动执行机构执行相应的动作,实现板材上料的自适应控制。
43.本实施例中板材上料自适应控制方法进行如下参数设定:
44.设定三个高度值,分别是初始高度h2、第一高度h和第二高度h1,并且:h2>h>h1。
45.设定两个下降阶段,分别是以第一速度v1控制吸盘下降的第一下降阶段和以第二速度v2控制吸盘下降的第二下降阶段,并且:v1>v2,其中:
46.初始高度h2是指:在运动执行机构开始下降之间,吸盘距板材上表面的高度;
47.第一高度h是指:在由运动执行机构带动吸盘下降的过程中,当吸盘下降到吸盘距板材上表面的高度为第一高度h时,启动吸盘开始负压工作;
48.第二高度h1是指:在由运动执行机构带动吸盘下降的过程中,当吸盘下降到吸盘距板材上表面的高度为第二高度h1时,停止运动执行机构带动吸盘继续下降的动作;
49.第一速度v1是指:在由运动执行机构带动吸盘下降的过程中,当吸盘处在初始高度h2和第一高度h之间时,也包括吸盘处在初始高度h2上时,以及吸盘处在第一高度h上时,运动执行机构以第一速度v1带动吸盘下降,为第一下降阶段;
50.第二速度v2是指:在由运动执行机构带动吸盘下降的过程中,当吸盘处在第一高度h和第二高度h1的阶段中,运动执行机构以第二速度v2带动吸盘下降,为第二下降阶段。
51.本实施例中根据设定的三个高度值和两个下降阶段按如下步骤进行控制:
52.步骤1、将安装在运动执行机构下端的吸盘设置在初始高度h2上,由运动执行机构带动吸盘沿桁架横梁横移到上料工位上方。
53.步骤2、进入第一下降阶段,由plc控制器控制运动执行机构带动吸盘按第一速度v1下降,直至由激光测距传感器检测获得吸盘距板材上表面的高度为第一高度h,完成第一下降阶段。
54.步骤3、进入第二下降阶段,由plc控制器控制运动执行机构带动吸盘按第二速度v2继续下降,直至由激光测距传感器检测获得吸盘距板材上表面的高度为第二高度h1,由plc控制器控制运动执行机构停止下行,完成第二下降阶段。
55.步骤4、由负压传感器检测获得负压检测信号不低于设定压力值时,判断吸盘取料成功,随及由plc控制器控制运动执行机构带动吸盘连同板材上升,并通过水平转运到达后续指定工位,实现板材上料。
56.步骤5、返回步骤1执行下一板材上料的自适应控制,上料工位上的板材托盘无需升高。
57.具体实施中,相关参数可以设置为:
58.h2=100cm,h=30cm,h1=5cm,v1=50cm/s,v2=10cm/s。
59.本发明利用负压传感器是对吸盘负压进行检测,由伺服电机驱动运动执行机构执行进行升降和水平转运,由plc控制器依据设定的参数和算法实现循环闭环控制,分阶段执行不同的下降速度,使得取料系统稳定可靠;能够广泛适用于板材厚度不统一,板材堆叠高度不统一,上料位上中板材托盘无法升降的各种场合,以自适应的形式实现板材上料自动控制,动作过程快捷、稳定、可靠,能有效提高生产效率并降低生产成本。